制动系统匹配设计
运用MATLAB进行汽车制动系匹配设计
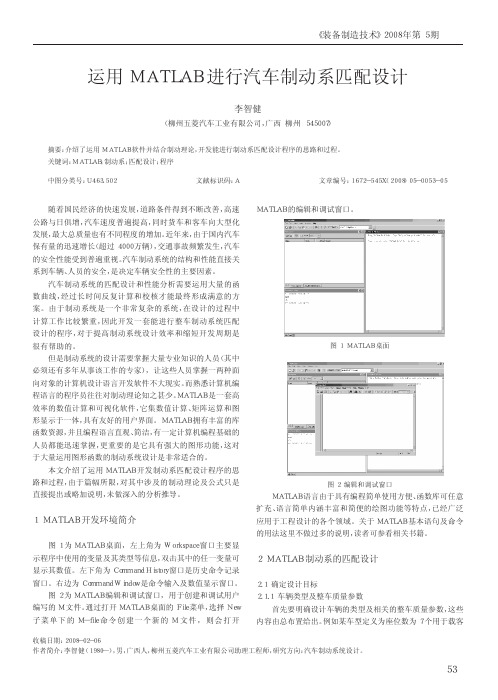
的下方,而为了提高制动效率,β 线应尽可能靠近 I线。
根据汽车理论,理想制动器制动力分配曲线方程为:
$ ! " #% F!2=
1 2
G hg
b2+
4hg L G
F!1
-
Gb hg
+2F!1
(1)
F!1—— —前制动器制动力; F!2—— —后制动器制动力; G— ——汽车重力;
b—— —汽车质心至后轴中心线距离;
明确以上整车质量参数后,计算制动系所用到质心到前、
后轴的距离等参数均可推算出来。整车质量参数的输入语句
如下:
clc
clear
M 1=1;
% 属于 M 1 类车辆填 1,否则填 0
N 1=0;
% 属于 N 1 类车辆填 1,否则填 0
O TH E R =0;
% 属于其它类车辆填 1,否则填 0
m a_k=1005;
图 2 为 M A TLA B 编辑和调试窗口,用于创建和调试用户 编写的 M 文件。通过打开 M A TLA B 桌面的 File 菜单,选择 N ew 子菜单下 的 M -file 命 令 创 建 一 个 新 的 M 文 件 , 则 会 打 开
M A TLA B 的编辑和调试窗口。
图 1 MATLAB 桌面
图 2 编辑和调试窗口 M A TLA B 语言由于具有编程简单使用方便、函数库可任意 扩充、语言简单内涵丰富和简便的绘图功能等特点,已经广泛 应用于工程设计的各个领域。关于 M A TLA B 基本语句及命令 的用法这里不做过多的说明,读者可参看相关书籍。
2 MATLAB 制动系的匹配设计
2.1 确定设计目标 2.1.1 车辆类型及整车质量参数
Pw =9.31;
制动系统匹配设计计算分解
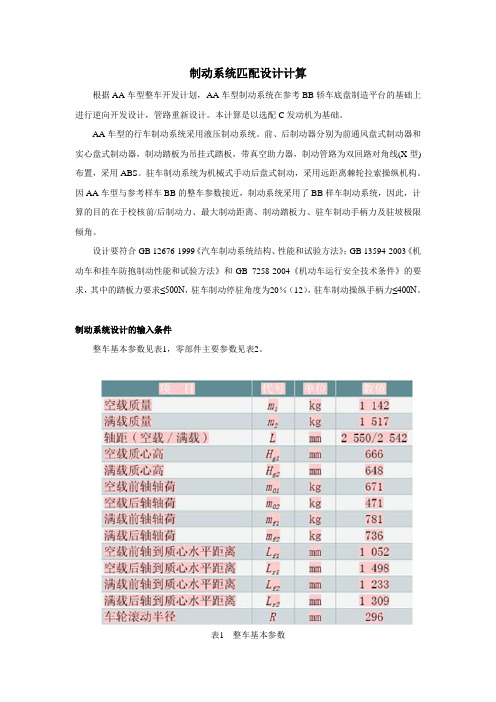
制动系统匹配设计计算根据AA车型整车开发计划,AA车型制动系统在参考BB轿车底盘制造平台的基础上进行逆向开发设计,管路重新设计。
本计算是以选配C发动机为基础。
AA车型的行车制动系统采用液压制动系统。
前、后制动器分别为前通风盘式制动器和实心盘式制动器,制动踏板为吊挂式踏板,带真空助力器,制动管路为双回路对角线(X型)布置,采用ABS。
驻车制动系统为机械式手动后盘式制动,采用远距离棘轮拉索操纵机构。
因AA车型与参考样车BB的整车参数接近,制动系统采用了BB样车制动系统,因此,计算的目的在于校核前/后制动力、最大制动距离、制动踏板力、驻车制动手柄力及驻坡极限倾角。
设计要符合GB 12676-1999《汽车制动系统结构、性能和试验方法》;GB 13594-2003《机动车和挂车防抱制动性能和试验方法》和GB 7258-2004《机动车运行安全技术条件》的要求,其中的踏板力要求≤500N,驻车制动停驻角度为20%(12),驻车制动操纵手柄力≤400N。
制动系统设计的输入条件整车基本参数见表1,零部件主要参数见表2。
表1 整车基本参数表2 零部件主要参数制动系统设计计算1.地面对前、后车轮的法向反作用力地面对前、后车轮的法向反作用力如图1所示。
图1 制动工况受力简图由图1,对后轮接地点取力矩得:式中:FZ1(N):地面对前轮的法向反作用力;G(N):汽车重力;b(m):汽车质心至后轴中心线的水平距离;m(kg):汽车质量;hg(m):汽车质心高度;L(m):轴距;(m/s2):汽车减速度。
对前轮接地点取力矩,得:式中:FZ2(N):地面对后轮的法向反作用力;a(m):汽车质心至前轴中心线的距离。
2.理想前后制动力分配在附着系数为ψ的路面上,前、后车轮同步抱死的条件是:前、后轮制动器制动力之和等于汽车的地面附着力;并且前、后轮制动器制动力Fm1、Fm2分别等于各自的附着力,即:根据式(1)、(2)及(3),消去变量ψ,得:由(1)、(2)、(3)及此时=zg,z=ψ=ψ0,可得:前轴:后轴:由此可以建立由Fu1和Fu2的关系曲线,即I曲线。
车辆不同工况下的制动匹配

• 制动过程的平顺性:制动时应柔和、平稳,解除时应迅速、彻底。避免在制动过程中出现不必要的颤动、噪声 以及制动踏板行程过大等。
02
不同工况下制动需求分析
市区行驶工况
仿真模型建立及参数设置方法
制动系统动力学模型
建立包括制动器、制动盘、制动鼓、制动蹄等在内的详细 制动系统动力学模型,模拟制动过程中的力学行为。
仿真参数设置
根据车辆类型、制动系统结构、制动器类型等,设置相应 的仿真参数,如制动器摩擦系数、制动盘/鼓尺寸、制动 蹄片材料等。
仿真环境搭建
模拟不同道路条件、车辆载荷、制动初速度等工况,为制 动系统仿真提供真实的环境条件。
维修保养周期
建议每行驶一定里程数或时间后 进行制动系统的检查与保养,具 体周期可根据车辆使用情况而定 。
项目清单
包括制动液更换、制动器摩擦片 更换、制动盘检查与更换、制动 系统管路检查等。
维修保养注意事项及操作指南
注意事项
在进行制动系统维修保养时,需确保车辆处于安全状态,避免在坡道或不稳定的 路面上进行。同时,使用合适的工具和材料,遵循制造商的维修手册进行操作。
加强团队建设和人才培养,提高团队 在车辆制动系统领域的整体实力。
拓展新能源汽车制动系统的研究和应 用领域,积极探索新的制动匹配方案 。
THANKS
感谢观看
不同工况下仿真结果分析比较
制动距离分析
比较不同工况下的制动距离,评 估制动系统在不同条件下的制动
效能。
制动稳定性分析
分析制动过程中车辆的稳定性,包 括侧滑、甩尾等现象的发生情况。
气制动匹配设计

气制动匹配设计目录一.气压制动系统介绍二.气压制动系统设计计算三.阀类零件的配置四.制动器选择五.气室匹配气制动系统介绍气压制动系统以空压机产生的压缩空气作为制动能源,驾驶员的操纵仅用于控制能源的分配,控制与执行装置均为气压式,故又称为全气压动力系统。
优点:1、制动操纵省力、制动强度大、工作介质使用后无需回收;2、气源可供其他辅助用气设备使用,并便于供给挂车制动力及操作挂车制动控制装置;3、无液压系统受热形成气泡影响制动性能的问题;缺点:1、存在空气压缩机、贮气筒、阀类、气室等装置,使其结构复杂、笨重、成本高;2、滞后性较长,因而增加了制动距离;3、制动系统排气时存在噪音;4、压缩空气中的水分、油垢、积炭容易使管路及贮气筒锈蚀、磨损、导致制动元件失效。
气制动系统组成及管路布置GB12676法规要求序号设计参数制动系统结构要求条目设计方案1充气时间发动机怠速,将储气筒存气排净,关闭所有储气筒放气阀,将发动机转速升至最大功率转速,测定升压最慢储气筒的升压时间至厂定气压65%,最长时间3min,至厂定气压,最长时间为6min。
5.5.5.1要求选取匹配的空气压缩机,限定储气筒最大容积2有效制动次数储能器充至厂定压力,空气压缩机停转,储能装置必须是在行车制动经8次全行程制动后,第9次制动时,储能装置的剩余压力仍能保证达到应急制动的制动效能。
5.5.1要求限定储气筒最小容积并选取匹配的气室3弹簧制动系弹簧压缩腔的供能回路中必须安装有单独的专用储能器或必须至少有两个独立的储能器向其供能。
4.4.3要求四回路保护阀(开启压力)利用储能来动作的行车制动系,若不利用储能的装置就达不到规定的4报警装置应急制动性能时,除安装压力表外,还必须安装报警装置。
当系统中任何部分储存的能量下降到某一值时,报警装置应能发出光信号或声信号。
4.2.13要求压力传感器当系统中任何部分储存的能量下降到某一值时,报警装置应能发出光四回路保护阀5报警装置信号或声信号。
中卡三轴载货车制动系统的匹配设计
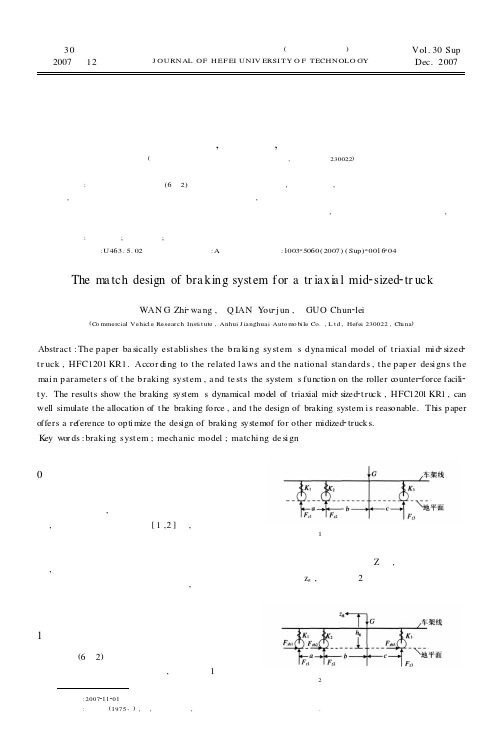
第30卷增刊 2007年12月合肥工业大学学报(自然科学版)J OURNAL OF HEF EI UNIV ERSI TY O F TECHNOLO GYVol.30Sup Dec.2007 收稿日期22作者简介汪知望(5),男,安徽岳西人,安徽江淮汽车股份有限公司助理工程师中卡三轴载货车制动系统的匹配设计汪知望, 钱友军, 郭春雷(安徽江淮汽车股份有限公司商用车研究院,安徽合肥 230022)摘 要:初步建立了中卡三轴(6×2)载货汽车的制动力学模型,在此基础上,参照相关法规及国家标准的要求,对其制动系统的主要参数及制动器进行了设计计算,并在滚筒反力式制动检验台上对车辆的制动性能进行检测。
结果表明该制动力学模型能较好地模拟制动过程中制动力的分配,整车制动系统的设计是合理的,可为其他中卡车型制动系统的优化设计提供参考。
关键词:制动系统;力学模型;匹配设计中图分类号:U463.5.02 文献标识码:A 文章编号:100325060(2007)(Sup)20016204The ma tch design of bra king system f or a tr iaxi a l mid 2sized 2tr uckWAN G Zhi 2wa ng , Q IAN Y ou 2j un , GUO Chun 2lei(C o mmercial Vehicl e Research Insti t ute ,Anhui J ianghuai Auto m o bi le Co.,L t d ,Hefei 230022,Chi na )Abstract :The paper ba sically est abli shes t he bra ki ng syst em ’s dyna mical model of t riaxial mi d 2sized 2t r uck ,HFC1201KR1.Accor di ng to t he related l aws and t he national standards ,t he paper desi gns t he mai n parameter s of t he braki ng syst em ,a nd te st s the system ’s function on the roller c ounter 2force facili 2t y.The result s show t he braking syst em ’s dynamical model of t riaxial mid 2sized 2t ruck ,HFC1201KR1,canwell simulate t he allocation of t he braking force ,and t he design of braking system i s reasonable.This paper offers a re ference to opti mize the design of braki ng systemof for other midized 2trucks.K ey w or ds :braki ng syst em ;mechanic model ;matchi ng de si gn0 引 言汽车制动系统的结构和性能直接关系到车辆、人员的安全,因此被认为是汽车的重要安全件,受到普遍重视。
制动总泵与制动系统匹配设计

制动总泵排量与制动系统匹配设计汽车制动系统在设计过程中,不但考虑制动系统元件的设计,也应考虑到制动主缸的排量与整个制动系统是否匹配,如匹配不当,将造成制动系统性能不良,易造成刹车踏板行程偏大或无刹车。
在这里根据HFJ6350B车换装自调间隙制动器(前、后均为鼓式)的设计来说明制动主缸排量与制动系统匹配设计问题。
根据有关要求,一个轮缸的工作容积为V i=π/4*d2*δ其中d为轮缸活塞直径,δ为轮缸活塞完全制动时的行程,初步设计时对于鼓式制动器取2~2.5mm。
则轮缸的总工作容积V=∑V i考虑到管路的变形(刚性油管变形可忽略不计,只考虑软管的变形量)则V0=αV 在初步设计时,取α=1.3根据以上要求,我们对HFJ6350B车原来的制动主缸排量进行了匹配计算,发现如在原车状态下直接换装自调间隙制动器,排量满足不了要求,造成制动踏板行程偏大,影响刹车性能,在试装过程中也证实了这种情况,为此有必要重新选择制动主缸。
我们初步选择了缸径为22.22、带真空助力器的制动主缸。
由此对制动主缸的排量、踏板行程、产生压力进行了计算。
下面仅列出有关排量的计算过程,其它计算过程略去:自调间隙制动器前后轮缸排量的要求前轮缸:V1=1.3*4*π/4* d12*δ=5267.1mm3后轮缸:V2=1.3*4*π/4* d22*δ=2488.8mm3拟选择制动主缸的排量制动主缸第一腔排量:V m1=π/4* d2*S1=5813.7 mm3>V1制动主缸第二腔排量:V m2=π/4* d2*S2=4069.6 mm3>V2通过初步计算,可以认定制动主缸与自调间隙制动器是匹配的,满足使用要求。
然后进行了第二次试装,试装结果证实了主缸满足制动器要求。
从而完成了HFJ6350B车换装自调间隙制动器的设计工作。
同时也找到了一种选择制动主缸排量的方法。
底盘室制动组。
基于汽车制动系统的匹配设计要点研究
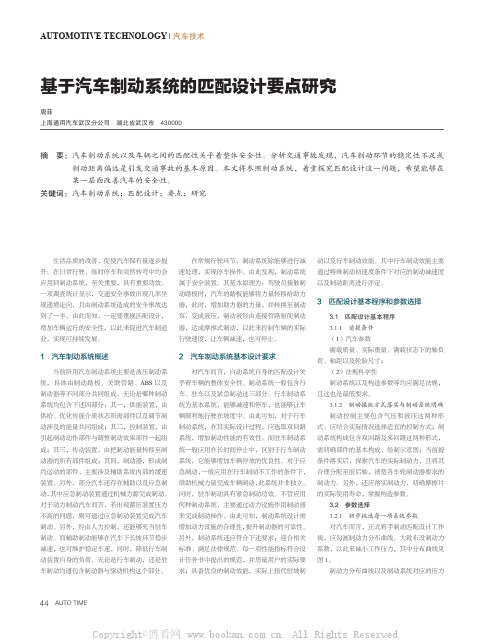
AUTOMOTIVE TECHNOLOGY | 汽车技术基于汽车制动系统的匹配设计要点研究唐菲上海通用汽车武汉分公司 湖北省武汉市 430000生活品质的改善,促使汽车保有量逐步提升。
在日常行驶、临时停车和突然转弯中均会应用到制动系统,至关重要,具有重要功效。
一项调查统计显示,交通安全事故出现几率呈现递增走向,且由制动系统造成的安全事故达到了一半。
由此而知,一定要重视匹配设计,增加车辆运行的安全性,以此来促进汽车制造业,实现可持续发展。
1 汽车制动系统概述当前所用汽车制动系统主要是液压制动系统,具体由制动踏板、关联管路、ABS以及制动器等不同部分共同组成。
无论是哪种制动系统均包含下述四部分:其一,供能装置,由供给、优化传能介质状态所需部件以及调节制动涉及的能量共同组成;其二,控制装置,由引起制动动作部件与调整制动效果部件一起组成;其三,传动装置,由把制动能量转移至制动器的所有部件组成;其四,制动器,形成制约运动的部件,主要涉及辅助系统内部的缓速装置。
另外,部分汽车还存在辅助以及应急制动,其中应急制动装置通过机械力源完成制动。
对于动力制动汽车而言,若出现蓄压装置压力不高的问题,则可通过应急制动装置完成汽车制动。
另外,经由人力控制,还能够充当驻车制动。
而辅助制动能够在汽车下长坡环节稳步减速,也可维护稳定车速,同时,降低行车制动装置自身的负荷。
无论是行车制动,还是驻车制动均通包含制动器与驱动机构这个部分。
在常规行驶环节,制动系统除能够进行减速处理,实现停车操作。
由此发现,制动系统属于安全装置。
其基本原理为:驾驶员接触制动踏板时,汽车的踏板能够将力量转移给助力器,此时,增加助力器的力量,并转换至制动泵,变成液压,制动液经由连接管路驱使制动器,达成摩擦式制动,以此来控制车辆的实际行驶速度,让车辆减速,也可停止。
2 汽车制动系统基本设计要求对汽车而言,自动系统自身的匹配设计关乎着车辆的整体安全性。
制动系统一般包含行车、驻车以及紧急制动这三部分。
制动系统匹配设计
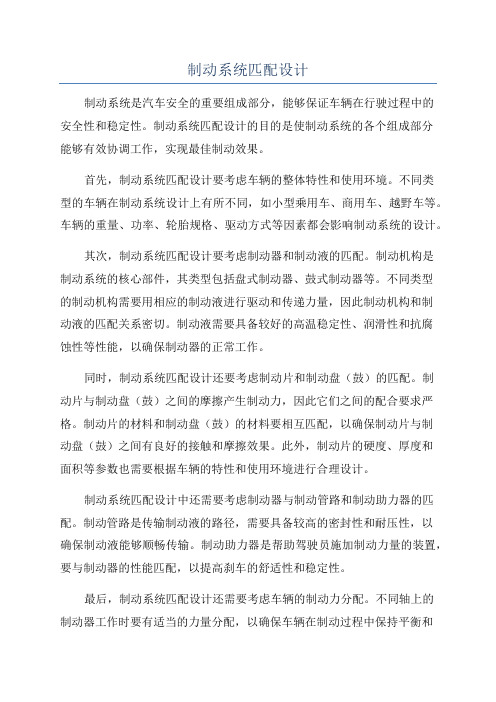
制动系统匹配设计制动系统是汽车安全的重要组成部分,能够保证车辆在行驶过程中的安全性和稳定性。
制动系统匹配设计的目的是使制动系统的各个组成部分能够有效协调工作,实现最佳制动效果。
首先,制动系统匹配设计要考虑车辆的整体特性和使用环境。
不同类型的车辆在制动系统设计上有所不同,如小型乘用车、商用车、越野车等。
车辆的重量、功率、轮胎规格、驱动方式等因素都会影响制动系统的设计。
其次,制动系统匹配设计要考虑制动器和制动液的匹配。
制动机构是制动系统的核心部件,其类型包括盘式制动器、鼓式制动器等。
不同类型的制动机构需要用相应的制动液进行驱动和传递力量,因此制动机构和制动液的匹配关系密切。
制动液需要具备较好的高温稳定性、润滑性和抗腐蚀性等性能,以确保制动器的正常工作。
同时,制动系统匹配设计还要考虑制动片和制动盘(鼓)的匹配。
制动片与制动盘(鼓)之间的摩擦产生制动力,因此它们之间的配合要求严格。
制动片的材料和制动盘(鼓)的材料要相互匹配,以确保制动片与制动盘(鼓)之间有良好的接触和摩擦效果。
此外,制动片的硬度、厚度和面积等参数也需要根据车辆的特性和使用环境进行合理设计。
制动系统匹配设计中还需要考虑制动器与制动管路和制动助力器的匹配。
制动管路是传输制动液的路径,需要具备较高的密封性和耐压性,以确保制动液能够顺畅传输。
制动助力器是帮助驾驶员施加制动力量的装置,要与制动器的性能匹配,以提高刹车的舒适性和稳定性。
最后,制动系统匹配设计还需要考虑车辆的制动力分配。
不同轴上的制动器工作时要有适当的力量分配,以确保车辆在制动过程中保持平衡和稳定。
制动力分配的主要方式有前后轮制动力分配和左右轮制动力分配两种。
综上所述,制动系统匹配设计是一个综合性的工程任务,需要综合考虑车辆的整体特性、使用环境和制动系统的各个组成部分之间的匹配关系。
只有进行合理的匹配设计,才能实现制动系统的最佳性能和安全效果。
- 1、下载文档前请自行甄别文档内容的完整性,平台不提供额外的编辑、内容补充、找答案等附加服务。
- 2、"仅部分预览"的文档,不可在线预览部分如存在完整性等问题,可反馈申请退款(可完整预览的文档不适用该条件!)。
- 3、如文档侵犯您的权益,请联系客服反馈,我们会尽快为您处理(人工客服工作时间:9:00-18:30)。
2.2.2 同步附着系数及制动器制动力分配系数的初步选择
2.
制动器制动力分配系数 前制动器制动力与汽车总的制动器制动力之比,称为制动器制动力分配系数
。由于在附着条件所限定的 范围内,地面制动力在数值上等于相应的制动周缘 力,因此������又通称为制动力分配系数。
11
2.2.2 同步附着系数及制动器制动力分配系数的初步选择
3. 制动器制动力分配系数的初步选择
根据已作出的I曲线图、法规要求、制动效率初步选择空、满载同步附着系 数,然后计算制动器制动力分配系数。 I曲线由整车参数确定,45°的平行线反映的是在某一附着系数下的前、后 地面制动力间的关系。如果选定一个同步附着系数,与这一附着系数对应的45° 的平行线与I曲线的交点,也应是I曲线与β 线的交点,过交点与原点的直线即为 无制动力调节装置时的 曲线;β 线与I曲线所包围的面积反映制动效率的高低
2.2.1 理想制动力分配曲线绘制
2. 理想的前、后制动器制动力分配曲线—I曲线 (1) 地面制动力FB:地面作用于车轮上的制动力,即地面与轮胎之间的摩擦力 ,其方向与车轮旋转方向相反。 (2) 制动器制动力Fμ :轮胎周缘克服制动器摩擦力矩所需的力,又称制动周缘 力。与地面制动力方向相反,当车轮角速度ω >0时,大小亦相等,且Fμ 仅由制 动器结构参数决定。即Fμ 及取决于制动器的结构型式、结构尺寸、摩擦副的摩 擦系数及车轮有效半径等,并与制动踏板力即制动系的液压或气压成正比。
• 同时,为提高整车性能,不同级别的车型,又会对制动性能提出高于以上标
准的要求,这些要求会在设计任务书中体现,因此,对设计任务书要求高于 法规要求的,要按设计任务书要求设计。 2
2.制动系统主要参数的选择
• 制动系统参数选择形式多样,可根据实际情况、用不同的方法确定,以最终 保证设计参数合理为准。如:轴荷、重心位置相近的车辆,可借鉴采用参考 车型数据;平台化产品,可借用部分参数,选择其它参数;选择参数后要进 行校核计算,满足要求后就可以采用;下面以无参考样车时的设计为例,简 要说明制动系统主要参数选择的一般步骤。 • 制动系统参数选择的一般步骤如下:
制动系匹配设计
1
1.制动系统匹配计算的目的与要求
• 制动系统的匹配设计主要是根据设计任务书的要求,整车配置、布置及参数 ,参考同类车型参数,选择制动器的形式、结构及参数,然后校核计算,验 证所选参数是否满足设计任务书及法规的要求,满足要求后初步确定参数。 • • 公司目前的车型均为M1类,操纵系统为液压操纵、真空助力。 因此,本匹配计算主要以上述车型及操纵系统为基础进行基础制动系统及调 节装置的匹配计算,ABS或ESP等辅助制动系统的匹配计算由配套厂家完成。 • GB12676-1999《汽车制动系结构、性能和试验方法》、GB7258-2012《机动车 运行安全技术条件》,GB13594-2003《机动车和挂车防抱制动性能和试验方 法》等对制动系的性能、要求及试验方法都作了详细的规定,因此,制动系 设计首先应满足以上法规的要求。
(2-10)
16
2.3.2 制动器型式的确定
制动器型式选择要结合总布置共同确定,盘式制动器由于其热稳定性、水稳 定性、制动稳定性好等优点,广泛用于轿车和部分客车和载货汽车的前轮。而后 轮采用鼓式制动器较容易地附加驻车制动的驱动机构,兼作驻车制动器之用。所 以,采用前盘后鼓制动器能够达到一般制动性能要求,而且成本较低。 高性能轿车前后轮均采用盘式,主要是为了保持制动力分配系数的稳定;同 时,配备ESP时,一般鼓式制动器不能满足ESP的需求,所以采用盘式制动器。
尽量高。通过作图试选,结合法规要求,初步选择制动力分配系数。
2.2.2 同步附着系数及制动器制动力分配系数的初步选择
图2 制动力分配曲线
不装制动力调节装置时,同步附着系数由式(2-5)及(2-8)推导得:
装感载比例阀时,拐点以前的制动力分配同上式。
13
2.2.3 系统工作压力的确定
管路压力越高,制动轮缸或主缸直径就越小,但对系统密封、管路尤其是制 动软管及管接头则提出了更高的要求,对软管的耐压性、强度以及接头的密封性 的要求就更加严格。因此,一般路面上制动时,管路压力不要超过10MPa,同时 ,考虑到传动效率、制动力调节装置等的影响等,选择管路压力还要适当减小。 目前开发的轿车,管路压力一般在4.5-8MPa。
(2-3)
(3) 理想的前、后制动器制动力分配 在附着系数为������的路面上,前、后车轮同步抱死的条件是:前、后轮制动器制动 力之和������ ������ = ������ ������1 + ������ ������2 等于汽车与地面附着力������∅ = ������∅1 + ������∅2 ;并且前、后轮制动 器制动力������������1 、 ������������2 分别等于各自的附着力������∅1 、 ������∅2 ,即
19
2.3.4 制动器效能因数的计算与选择
2.制动器效能因数的计算 制动器效能因数取决于制动器结构、摩擦材料的摩擦系数。各种制动器用摩擦材 料的摩擦系数的稳定值约为0.3-0.5,一般取0.35-0.4。
可以根据制动器结构和摩擦材料的摩擦系数计算效能因数。
盘式制动器的效能因数计算 钳盘式制动器:
9
2.2.2 同步附着系数及制动器制动力分配系数的初步选择
1. 同步附着系数 同步附着系数∅0 是汽车制动时前、后轮同时抱死时的路面附着系数。 同步附着系数的选择首先要满足制动稳定性的要求,然后要有高的制动效率并满 足应急制动等的要求。对制动稳定性的法规进行分析:附着系数在0.2-0.8之间时除 个别很小的区段外,均要求前轮先抱死,所以同步附着系数应≥0.8,但满足此要求 后,制动时前轴负荷较大,制动效率低,所以一般都要加装制动力调节装置。 另外,同步附着系数的选择还要结合整车的使用条件、轴荷分配、管路布置、配 置综合考虑。经常在良好的路面上使用且车速较高的车辆,为保证制动时的稳定性, 同步附着系数可选的大一点。对管路布置为II型的制动系统,要考虑单回路失效的应 急制动效能;制动系统配置ABS时要满足ABS匹配的基本要求。 对装ABS的车辆同步附着系数满足ABS匹配要求即可,一般应在0.5-1.0为宜。 装感载比例阀时,拐点后的空、满载同步附着系数应≥0.8。 10
(2-4)
7
2.2.1 理想制动力分配曲线绘制
在上述条件下 由公式(1)(2)(4)可得:
(2-5)
(2-6)
(2-7)
8
2.2.1 理想制动力分配曲线绘制
将(7)可绘成以������������1 、 ������������2 为坐标的曲线,即为理想的前后、轮制动器制动 力分配曲线,简称I曲线。 根据式(4)的第一式,按不同∅值作图,得到一组与坐标轴成45°的平行线 ,绘在I曲线图上,以便分析使用。
2.3.4 制动器效能因数的计算与选择
1. 定义 制动器效能因数是制动器在单位输入压力或力的作用下所能输出的力或力矩 ,用于比较不同结构型式的制动器的效能。可定义在制动鼓或制动盘的作用半径 上所产生的摩擦力与输入力之比,即
(2-11)
式中: Tf -制动器的摩擦力矩; r -制动鼓或制动盘的作用半径; 盘式制动器作用半径可近似为r = ������������ + ������0 /2,������������ 、������0 为扇形制动块内、外半 径。 鼓式制动器作用半径制动鼓内半径。 P -输入力,一般取加于两制动蹄的张开力(或加于两制动块的压紧力)的平均 值为输入力。
,包围面积越小,效率越高。 装感载比例阀时,制动力分配曲线如下图,可以参考同类车型、法规要求选 择拐点前的制动力分配线并确定拐点;再选择拐点后的空载(或满载)同步附着 系数,作出拐点后的空载(或满载)β 线,一般空、满载拐点后的β 线平行,所 以可作出拐点后的另一条β 线,再根据45°的平行线就可以确定满载(或空载) 的同步 附着系数,拐点后的空、满载同步附着系数应≥0.8,且要使制动效率 12
① 了解整车配置并输入与制动系统有关的整车参数及要求。
② 初步选择系统主要参数。 ③ 制动器及相关参数的选择及计算 ④ 操纵系统主要参数的选择及计算
3
2.1与匹配计算有关的整车参数及要求
序号 参数 1 2 3 4 5 6 7 整车空载/满载质量 轴距 空载/满载质心高 空载/满载质心到前 轴的水平距离 空载/满载质心到后 轴的水平距离 前后轮胎滚动半径 制动系统配置和其 他要求 L ℎgk /ℎgm ������������ /������������ ������������ /������������ ������1 /������2 代号 ������������ /������������ 单位 kg mm mm mm mm mm 通用代号ℎ������ 通用代号a 通用代号b 通用代号R 数值 备注 通用代号m
17
2.3.3 制动半径的确定
在有关的整车总布置参数和制动器的结构型式确定后,即可参考已有的同类 型、同等级汽车的同类制动器,轮辋尺寸,对制动器的结构参数进行初选。 1. 鼓式制动器制动半径 鼓式制动器制动半径就是制动鼓内半径,在输入力一定时,制动鼓直径越 大,制动力矩越大。但其直径受轮辋内径的限制,而且其直径增大也使制动鼓的 质量增加,非悬挂质量增加,不利于汽车行驶平顺性。另外,制动鼓与轮辋之间 应有一定的间隙,此间隙一般不应小于20-30mm,以利通风散热。 可以根据轮辋直径及整车布置初选制动鼓内径,轿车制动鼓内径一般比轮辋 外径小125-150mm,载货汽车和客车制动鼓内径一般比轮辋外径小80-100mm;初 选的制动鼓内径应符合QC/T309-1999《制动鼓工作直径及制动蹄片宽度尺寸系列 》的规定(部分参考样车为国外标准,与此标准不一致)。 2. 盘式制动器制动半径 盘式制动器制动半径取决于摩擦衬块的内、外半径,也即取决于制动盘直径 及轮毂法兰盘直径,制动盘直径增大可以降低制动钳的加紧力,降低摩擦衬块的 单位压力和工作温度。制动盘直径也受轮辋直径的限制。通常制动盘的直径为轮 辋直径的70%-79%。 盘式制动器制动半径可近似为r=(ri+rO)/2,ri、rO为制 动摩擦衬块内、外半径。 推荐rO/ri<1.5,以线绘制