论地铁车站渗漏水原因及治理措施
地铁漏水原因分析及补漏措施
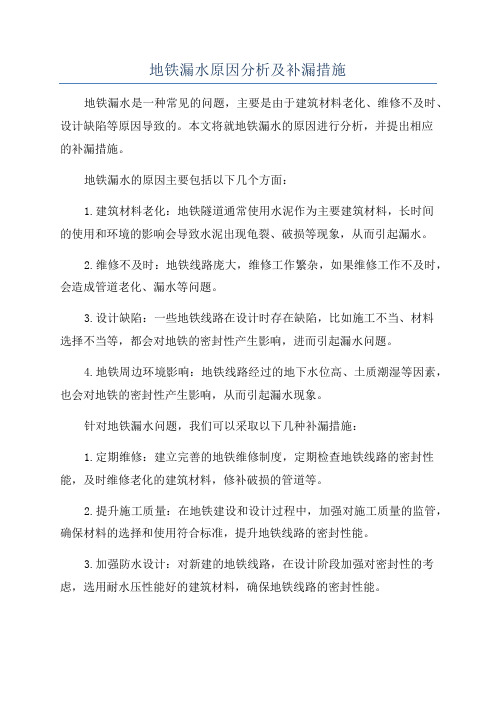
地铁漏水原因分析及补漏措施地铁漏水是一种常见的问题,主要是由于建筑材料老化、维修不及时、设计缺陷等原因导致的。
本文将就地铁漏水的原因进行分析,并提出相应的补漏措施。
地铁漏水的原因主要包括以下几个方面:1.建筑材料老化:地铁隧道通常使用水泥作为主要建筑材料,长时间的使用和环境的影响会导致水泥出现龟裂、破损等现象,从而引起漏水。
2.维修不及时:地铁线路庞大,维修工作繁杂,如果维修工作不及时,会造成管道老化、漏水等问题。
3.设计缺陷:一些地铁线路在设计时存在缺陷,比如施工不当、材料选择不当等,都会对地铁的密封性产生影响,进而引起漏水问题。
4.地铁周边环境影响:地铁线路经过的地下水位高、土质潮湿等因素,也会对地铁的密封性产生影响,从而引起漏水现象。
针对地铁漏水问题,我们可以采取以下几种补漏措施:1.定期维修:建立完善的地铁维修制度,定期检查地铁线路的密封性能,及时维修老化的建筑材料,修补破损的管道等。
2.提升施工质量:在地铁建设和设计过程中,加强对施工质量的监管,确保材料的选择和使用符合标准,提升地铁线路的密封性能。
3.加强防水设计:对新建的地铁线路,在设计阶段加强对密封性的考虑,选用耐水压性能好的建筑材料,确保地铁线路的密封性能。
4.增强排水系统:对地铁周边的排水系统进行升级改造,确保地下水位的正常排放,减少对地铁线路密封性的影响。
5.加强检测监测:建立健全的地铁漏水检测系统,定期对地铁线路进行漏水检测,及时发现问题并进行修补。
综上所述,地铁漏水问题的出现往往是多种因素共同作用的结果,需要综合考虑建筑材料的老化、维修工作的及时性、设计的合理性和周边环境的因素等。
只有在加强维修、提升施工质量、加强防水设计、增强排水系统以及加强检测监测等多个方面同时进行整治,才能有效地解决地铁漏水问题,确保地铁线路的安全运营。
城市地铁施工渗漏水原因与防水措施分析

城市地铁施工渗漏水原因与防水措施分析随着城市的发展,地铁建设变得越来越普遍。
在地铁施工过程中,渗漏水问题成为一种常见的现象。
渗漏水可能会对地铁线路和周围的建筑物造成损害,因此需要采取措施来解决这个问题。
本文将分析渗漏水的原因,并提出一些防水措施。
渗漏水的原因主要包括以下几个方面:1. 地铁施工过程中出现的缺陷:地铁施工包括地铁车站、隧道、轨道等建设,如果在施工过程中没有完全解决接缝、弯曲等地方的缺陷,就容易产生渗漏水的问题。
2. 地下水位高:一些地区的地下水位较高,而且地铁施工通常会打断地下水流动的路径,导致地下水无法排出,从而造成堆积和渗漏。
3. 地质条件差:一些地区的地质条件较差,例如黏土或软岩等,这些地质条件容易导致水渗透。
为了解决地铁施工渗漏水问题,可以采取以下防水措施:1. 加强施工过程中的质量控制:在施工过程中,应严格控制质量,确保所有接缝和连接部位都严密可靠,以防止水渗漏。
2. 排水系统的设计和建设:在地铁施工中,应当设计和建设一个完善的排水系统,确保地下水能够畅通排出,从而减少水渗漏的可能性。
3. 针对地质条件进行不同的处理:根据地质条件的不同,可采取不同的防水措施。
在黏土层下面的隧道施工中,可以采用防渗混凝土结构或挡墙来防止地下水渗透。
4. 定期检查和维护:地铁施工完成后,应定期检查地铁线路和周围的建筑物,及时发现和修复任何渗漏问题,以防止水渗漏进一步扩大。
地铁施工中的渗漏水问题可能会对地铁线路和周围建筑物造成损害,因此需要采取防水措施来解决这个问题。
在施工过程中加强质量控制、设计和建设排水系统、针对不同的地质条件采取不同的防水措施,以及定期检查和维护都是有效的解决方法。
通过这些措施,可以减少地铁施工渗漏水的可能性,确保地铁运行的安全和顺畅。
城市地铁施工渗漏水原因与防水措施分析

城市地铁施工渗漏水原因与防水措施分析随着城市化进程不断加快,地铁成为城市公共交通建设的重要组成部分。
在地铁施工中,渗漏水问题经常会成为一个困扰工程师和设计师的难题。
渗漏水不仅会影响地铁隧道的使用安全,还会对周边环境造成严重影响。
对地铁施工渗漏水原因进行深入分析,并采取科学有效的防水措施显得尤为重要。
1. 地质条件不利地下地质条件是影响地铁施工渗漏水问题的主要原因之一。
如果地铁隧道施工所处地层为含水层、软土、粉土等地质条件不利的地段,就容易导致地铁隧道渗漏水问题。
尤其是在岩层较松散的地质条件下,地铁隧道的施工就会面临严峻的地质灾害风险,容易发生渗漏水问题。
2. 地铁隧道设计和施工技术不合理地铁隧道设计和施工技术是影响地铁施工渗漏水问题的另一重要原因。
如果在地铁隧道设计和施工过程中,选择不合理的材料、运用不当的工艺、或者忽视了环境因素的影响,都会导致地铁隧道施工过程中出现渗漏水问题。
如果在地铁隧道施工中未能采取有效的排水措施,就会出现地铁隧道内渗漏水情况。
3. 管道破损在地铁隧道的施工过程中,如果管道施工材料不合格、管道连接松动或管道设计不合理等原因,都会导致地铁隧道管道渗漏水的问题。
4. 设备故障地铁隧道施工中使用的设备如果存在故障,也会引发地铁隧道渗漏水问题。
隧道掘进机等设备若存在泄露或运行不畅等问题,都会导致地铁隧道渗漏水现象。
5. 周边环境改变地铁施工所处的周边环境发生改变,也可能引发地铁隧道渗漏水问题。
周边地下水位升高、周边土地开挖等因素都可能对地铁隧道施工造成不利影响,导致渗漏水问题的发生。
1. 合理选用材料地铁隧道施工中,选用合理的防水材料是防水措施中的重要一环。
地铁隧道施工中地下室外墙面常用的防水材料有沥青防水膜、聚合物改性沥青防水卷材等,需要根据地质条件和施工环境确定合适的防水材料,以有效预防渗漏水问题。
2. 优化设计施工工艺在地铁隧道设计和施工中,应选择合适的工艺和施工方法,并充分考虑地质条件和周边环境的影响,以减少渗漏水问题的发生。
闲置重启的轨道交通地铁工程地下车站渗漏水的治理

闲置重启的轨道交通地铁工程地下车站渗漏水的治理地铁工程中的地下车站渗漏水是一个常见的问题,对于轨道交通的正常运营和乘客的安全都造成了一定的影响。
为了解决这个问题,需要对渗漏水进行全面的治理和修复工作。
本文将从渗漏水的原因分析、治理方法和经验总结等方面对地铁工程中地下车站渗漏水进行探讨。
地下车站渗漏水的原因主要可以从以下几个方面进行分析。
地铁车站通常位于地下,深入地下土层中,地下水的水平面高度会对车站的地下空间形成压力,从而引起渗漏水现象。
施工过程中可能存在施工不规范、施工材料质量不过关等问题,导致地下车站墙体、地面等部位出现破损、开裂,从而引发渗漏水。
地下车站周边地下管线的设置和维护也会对渗漏水产生影响。
确切地确定渗漏水的原因对于治理工作至关重要。
地铁工程中地下车站渗漏水的治理方法可以采取多种手段。
对渗漏水的具体原因进行调查和分析,找出存在的问题和隐患。
对已经出现渗漏水的部位进行修复,修复的过程中可以采用适当的封堵材料进行处理,如水泥、沥青、聚合物等。
在施工阶段,应严格控制施工质量,以避免施工过程中出现不规范、不合格等问题。
对于地下车站周边管线的设置和维护也非常重要,必要时可以对管线进行改造和维修,以减少渗漏水的可能。
在实施治理方法过程中,需要注重以下几个方面的问题。
治理工作应该科学合理,不仅要解决当前的渗漏水问题,还要考虑到长期的使用和维护。
对于已经出现渗漏水的地下车站,需要及时采取措施进行修复和处理,以避免进一步扩大和加重渗漏水的程度。
渗漏水治理过程中需要注重安全措施的落实,确保操作人员和乘客的安全。
在实际操作中,可以参考一些成功的经验和案例。
可以进行现场勘察和数据收集,对渗漏水的程度和范围进行精确的测量和记录。
可以借鉴其他地铁工程的治理经验,学习和运用先进的渗漏水治理技术和设备。
需要加强对施工质量和维护管理的监督和检查,及时发现和解决存在的问题。
城市地铁施工渗漏水原因与防水措施分析

城市地铁施工渗漏水原因与防水措施分析城市地铁的建设是现代城市化进程中不可或缺的一环,但是在地铁施工中经常会出现渗漏水问题,这不仅会给周围的环境造成危害,也会对地铁运营造成一定的影响。
因此,在地铁建设中采取防水措施是非常必要的。
下面分析城市地铁施工渗漏水的原因及防水措施。
一、渗漏水的原因1.地下含水层水位高在城市中,地下水位往往比较高,对于深度较浅的地铁站点,其地下水位往往高于地铁车站地面,导致车站跑道或侧壁渗漏情况严重。
2.土壤条件复杂城市地铁建设往往需要穿越各种土质地层,有些土层含水量大,对防水材料的要求较高。
3.地铁施工质量不过关地铁工程施工质量差也是造成渗漏水的主要原因之一,如未按照规范要求进行洞口处理、未进行地下水的封堵等。
4.地铁车站在洼地在城市中,地势比较低的区域往往更容易积水,如果地铁车站就建在这些低洼地区,就难免会受到来自周围环境的渗漏水的影响。
二、防水措施1.选用合适的防水材料选用符合国家及地方标准的防水材料和施工工艺,例如乙烯丙烯橡胶防水材料、有机硅防水材料等,以确保防水效果。
2.地铁车站排水系统的改善对于设计较差的排水系统,可采用新的排水设施或增加排水设备来改善雨水的排水能力。
3.如实施地下隧道排水适当的排水措施是防止地下级的积水,降低地下水位的关键手段之一。
在地铁隧道工程中,要注意隧道两侧的水池,引导积水到出口处排放,从而减少积水对隧道环境的污染。
4.做好地铁车站干燥排水在当初建设时,在防水施工的同时,应该同时考虑车站的干燥排水方法。
尽量使用建筑材料少受潮的技术,对于假山、花台等地形旅游设施,注重排水设计,避免积水。
总之,防水工程施工是城市地铁建设中十分重要的工作。
地铁渗漏水问题影响到地铁的使用效果,因而应该本着防患于未然的态度,采取一系列的预防措施,以确保人们能够安心地乘坐地铁。
地铁车站结构渗漏的原因分析及防治

地铁车站结构渗漏的原因分析及防治地铁作为城市中重要的交通工具,为人们出行提供了便利,然而在地铁车站结构中,常常会发生渗漏的情况。
地铁车站结构渗漏严重影响了车站设施的使用寿命和乘客的出行体验,因此对地铁车站结构渗漏的原因进行分析,以及如何进行防治成为了亟待解决的问题。
1.设计施工问题地铁车站涉及到复杂的结构设计和施工工艺,若在设计和施工中存在问题,可能会导致车站结构渗漏。
例如地铁车站地下结构设计、材料选取和施工工艺不合理等都会导致车站结构渗漏的发生。
2.构筑物老化随着时间的推移,地铁车站的构筑物会因为受到风吹雨淋、水土侵蚀等自然环境的影响而逐渐老化,从而出现渗漏问题。
特别是在地铁车站结构中存在裂缝或者破损的地方,更容易导致渗漏的发生。
3.地下水位变化城市地铁车站通常位于地下深处,地下水位的变化会对地铁车站结构的渗漏产生直接影响。
当地下水位上升时,会对地铁车站结构施加水压力,导致渗漏的发生。
4.排水系统问题地铁车站内部通常设置有排水系统,但是如果这些排水系统出现堵塞或者设计不当,就会导致地铁车站结构的渗漏。
由于车站周边区域的排水系统问题,也会影响地铁车站结构渗漏。
二、地铁车站结构渗漏的防治措施1.加强设计和施工质量管理在地铁车站结构的设计和施工过程中,需要严格按照国家相关标准和规范进行操作,确保结构的合理性和施工质量。
2.定期检测和维护对地铁车站结构进行定期检测和维护是非常关键的,及时发现问题并及时处理,可以最大限度的减少渗漏问题的发生。
3.强化防水工程在地铁车站结构的施工中增加防水材料的使用,并加强防水工程的设计和施工过程,以保证结构的防水性能。
4.完善排水系统对地铁车站结构内部的排水系统进行优化和改善,保证其畅通,以及加强对周边区域的排水系统的管理和维护。
5.科学合理利用地下水资源在地铁车站的建设和运营中,需要科学合理利用地下水资源,避免因地下水位的不合理使用而导致渗漏问题的发生。
6.加强安全意识地铁车站的管理者和员工需要加强对车站结构渗漏问题的认识和了解,加强相关知识培训,从而提高车站结构渗漏问题的应对能力。
闲置重启的轨道交通地铁工程地下车站渗漏水的治理

闲置重启的轨道交通地铁工程地下车站渗漏水的治理地铁工程地下车站是城市轨道交通系统的重要组成部分,对于城市交通的发展和便捷性起着至关重要的作用。
随着地铁线路的日益延伸和使用年限的增加,一些地铁工程地下车站出现了一些问题,其中最为突出的就是地下车站的渗漏水问题。
渗漏水问题不仅影响了地铁工程设施的正常使用,还可能对安全造成影响,因此对地下车站渗漏水问题进行治理是一项紧迫的任务。
一、渗漏水问题的原因分析1.地下水位高地下车站位于地下,周围环境中地下水位的高低直接影响着车站的渗漏情况。
当地下水位偏高时,会导致地下车站内外水压梯度明显,容易导致墙壁出现渗漏现象。
2.建筑结构老化随着地铁工程使用年限的增加,车站建筑结构、密封材料等可能会出现老化、损坏的情况,从而造成渗漏问题。
3.地下施工质量差在地铁工程的建设过程中,如果地下车站施工质量不达标,例如防水材料施工不当等,也容易导致渗漏问题的出现。
二、治理方案1.维护地下排水系统地下车站的排水系统是防止渗漏水问题的关键。
对排水管道进行定期清理、排查漏点,保持通畅是预防渗漏水问题的重要措施。
2.修复建筑结构对于老化、损坏的建筑结构,需要及时进行维修和加固,重点处理车站墙面、地板等与外界接触的部位,以减少渗漏水的侵蚀。
3.加强防水材料的使用地下车站在建设和维护过程中需要加强对防水材料的使用和管理,确保其性能稳定,杜绝因防水材料问题导致的渗漏现象。
4.加大监测力度利用现代化的监测技术,对地下车站的渗漏情况进行实时监测和分析,及时发现渗漏问题,采取相应的治理措施。
5.加强维护管理定期对地下车站进行维护保养工作,包括对设施设备的检查和维修,以确保地下车站的正常使用。
三、渗漏水问题治理的意义1.保障地铁工程的安全运行渗漏水问题的存在会对地下车站的设施和结构造成侵蚀,可能导致设施结构的损坏,进而危及地铁工程的安全运行,因此对渗漏水问题进行治理,是保障地铁工程安全运行的重要举措。
地铁车站渗漏原因分析及防治措施
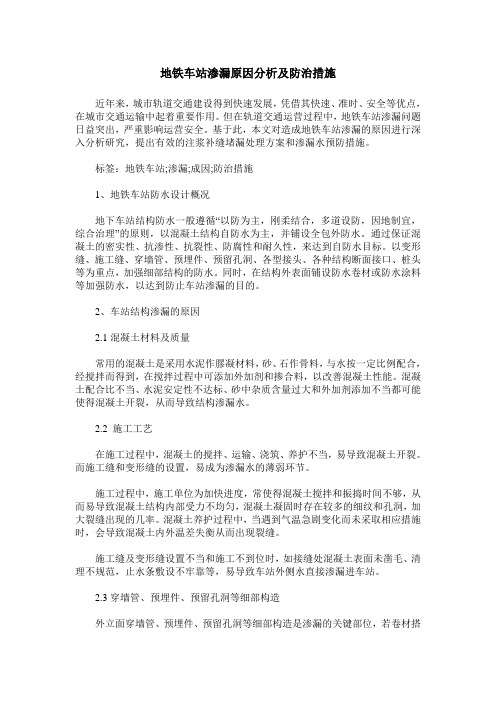
地铁车站渗漏原因分析及防治措施近年来,城市轨道交通建设得到快速发展,凭借其快速、准时、安全等优点,在城市交通运输中起着重要作用。
但在轨道交通运营过程中,地铁车站渗漏问题日益突出,严重影响运营安全。
基于此,本文对造成地铁车站渗漏的原因进行深入分析研究,提出有效的注浆补缝堵漏处理方案和渗漏水预防措施。
标签:地铁车站;渗漏;成因;防治措施1、地铁车站防水设计概况地下车站结构防水一般遵循“以防为主,刚柔结合,多道设防,因地制宜,综合治理”的原则,以混凝土结构自防水为主,并铺设全包外防水。
通过保证混凝土的密实性、抗渗性、抗裂性、防腐性和耐久性,来达到自防水目标。
以变形缝、施工缝、穿墙管、预埋件、预留孔洞、各型接头、各种结构断面接口、桩头等为重点,加强细部结构的防水。
同时,在结构外表面铺设防水卷材或防水涂料等加强防水,以达到防止车站渗漏的目的。
2、车站结构渗漏的原因2.1混凝土材料及质量常用的混凝土是采用水泥作膠凝材料,砂、石作骨料,与水按一定比例配合,经搅拌而得到,在搅拌过程中可添加外加剂和掺合料,以改善混凝土性能。
混凝土配合比不当、水泥安定性不达标、砂中杂质含量过大和外加剂添加不当都可能使得混凝土开裂,从而导致结构渗漏水。
2.2 施工工艺在施工过程中,混凝土的搅拌、运输、浇筑、养护不当,易导致混凝土开裂。
而施工缝和变形缝的设置,易成为渗漏水的薄弱环节。
施工过程中,施工单位为加快进度,常使得混凝土搅拌和振捣时间不够,从而易导致混凝土结构内部受力不均匀,混凝土凝固时存在较多的细纹和孔洞,加大裂缝出现的几率。
混凝土养护过程中,当遇到气温急剧变化而未采取相应措施时,会导致混凝土内外温差失衡从而出现裂缝。
施工缝及变形缝设置不当和施工不到位时,如接缝处混凝土表面未凿毛、清理不规范,止水条敷设不牢靠等,易导致车站外侧水直接渗漏进车站。
2.3穿墙管、预埋件、预留孔洞等细部构造外立面穿墙管、预埋件、预留孔洞等细部构造是渗漏的关键部位,若卷材搭接和卷边处理不到位、预留孔洞周边混凝土不密实牢固,易导致渗漏。
- 1、下载文档前请自行甄别文档内容的完整性,平台不提供额外的编辑、内容补充、找答案等附加服务。
- 2、"仅部分预览"的文档,不可在线预览部分如存在完整性等问题,可反馈申请退款(可完整预览的文档不适用该条件!)。
- 3、如文档侵犯您的权益,请联系客服反馈,我们会尽快为您处理(人工客服工作时间:9:00-18:30)。
论地铁车站渗漏水原因及治理措施
摘要:本文笔者结合某工程实例,针对地铁车站施工中渗漏水产生的原因,采取了合理的治理措施,从而保证地铁车站的防水效果。
关键词: 地铁车站;渗漏水;原因;治理措施
前言
随着城市的不断发展,城市人口也不断增加,城市的交通出行问题也面临着巨大的考验。
地铁工程渗漏水是现今国内较常见的一种工程缺陷,尤其是南方多雨及地下水位较高的地区,它不仅与地下工程周边地质水文环境、结构埋深、防水设计方案、防水材料等有关,还与结构混凝土性能、施工方案、施工工艺等有关。
因此,做好地铁的渗漏水问题即是亟待解决的问题也是造福人民生活的一个重要指标。
1 工程概况某地铁车站全长163.7m,标准断面宽17.9m,开挖深度15.8m,基坑内设三道钢支撑。
基坑采用钢筋混凝土灌注桩与旋喷桩咬合结构。
地质情况:①填土层,埋深0~1.55m;②新近沉积层主要为粉土、粉细砂、中粗砂、圆砾、砂砾,埋深1.55~8.70m;③一般第四纪沉积层主要为粉质黏土埋深8.7~19.6m。
2 地铁车站施工渗漏水原因开挖施工至地面以下7m时,基坑侧壁钻孔桩桩间均出现渗漏水现象,渗漏水在同一平面上呈不连续分布,漏水点大小各异,经采用量筒测算,水量在1.5~52.0m3/h不等。
车站基坑两端头区间隧道与车站接口处洞门四周渗漏水严重。
经研究勘察,现场漏水原因分析:①地下水位高,砂层、卵砾石层透水性好,基坑周边水源补给充足。
②设计时可能考虑到对古建筑的影响,在本站未设降水井,只设有深层减压降水井,减压降水深度为地面以下17.85m,而基坑开挖深度为16.90m,减压井不能对中层的潜水及地表水起到降水作用。
③盾构提前过站造成端头墙围护桩断开,形成不连续的止水帷幕。
④本工程的围护结构为钻孔桩加旋喷桩,先施工钻孔桩,再施工旋喷桩,两次成桩施工造成桩体间存在间隙,且在地下水丰富和不均匀地质条件下,施工的旋喷桩密实度差异较大,同时旋喷桩施工时的提升速度不均易造成水泥浆断层,受水流冲刷,空隙较大时夹带泥土、砂石从漏水点涌出。
3 地铁车站渗漏水治理措施施工中根据渗漏水的特点总结了以下几个方面:大面积漏水、集中性漏水、较小漏水点或渗水等情况,根据以上渗漏的原因采取不同措施治理渗漏水,堵水施工遵循“堵排结合,以堵为主”的治水原则,同时考虑内外因素,不同漏水情况采取不同治水措施,外部因素以截流为主,内部因素以堵排为主,内外排水措施相互结合才能达到治水的目的。
3.1 预注浆措施地面以下7~12m已开挖部分,基坑墙壁出现大面积渗漏水,漏水点普遍集中在桩间,漏水中含泥沙量大,漏水点孔径为5~30cm,漏水量每孔约15~45m3/h。
暂停大面积土方开挖,对该砂卵石地层实施超前注浆堵水方案: (1)对已开挖的工作面喷射混凝土封闭,混凝土强度达到设计强度的70%时采用风钻在桩间打孔,注浆管的布设间距为横向1.2m,竖向1.5m,孔径为φ40,注浆管为φ32,壁厚δ=3.25mm的钢花管,漏浆孔在钢管前端1.5m设置,间距
为15cm,孔径为8mm,梅花形布置,管头制成锥形,注浆管从钻孔桩与旋喷桩之间斜向打入,打设深度应穿过旋喷桩,插入注浆管分1.5m和2.5m两种,长管作为深层预注浆,短管为二次补偿注浆,插入角度为水平向下15°,注浆管外漏15~20cm。
(2)注浆设备采用KBY50/70型双液注浆机,注浆连接管路为φ30的橡胶软管。
(3)先注入1:0.8~1:1水泥浆,注浆压力为0.1~0.3MPa,注浆过程中因回填的浆液与土体间隙饱和产生较大压力,当压力达到0.3MPa时,停止注水泥浆,二次补偿注水泥—水玻璃双液浆,经现场原状土注浆试验确定配合比:水泥采用P.O32.5普通硅酸盐水泥,水玻璃模数2.2~2.8,浓度不低于35Beˊ,同时加入缓凝剂NaH2PO4,掺量≤3%,水泥浆与水玻璃体积比为1:1,凝结时间控制在8~10分。
二次补偿注浆压力为0.3~0.6MPa,注浆时要注意观察压力和流量变化,压力逐渐上升,流量逐渐减少,当注浆压力达到设计终压时,再稳3分,可结束本孔注浆。
二
3.2 集中堵水措施(1)基坑侧壁集中堵水处理漏水情况:预注浆之后进行基坑开挖,桩间仍有渗漏水,原因是周边有潜水,水位分布在开挖面以上约1.5m,用压力仪器测试水压在0.03~0.07MPa之间,这种漏水情况较为集中,在距离万泉河和圆明园湖泊较近的地方漏水明显较大,以点状分布为主,集中性漏水还集中在地下12~15m,经统计,漏点分布范围为每100m2约有15个点,漏水量每孔约为5.5~25.0m3/h。
堵水措施:堵水施工时有针对性地先在原漏水点处采用YT-28风钻打孔预埋注浆管,四周用水泥砂浆封堵,拌合砂浆时加适量速凝剂加快凝固时间。
漏水孔径>150mm的先采用草袋堵塞,再用砂浆封堵,插入注浆管角度为水平向下15°,外侧露出管头20~30cm。
将桩间水通过注浆管引流出来,然后对基坑侧壁挂网喷射混凝土封闭,喷射混凝土时注意防止堵塞注浆管,在喷射混凝土达到设计强度后进行注浆施工,浆液选用水泥—水玻璃双液浆,材料选用、配合比、注浆压力同上。
(2)区间洞口处集中堵水漏水情况:基坑端头墙洞口处桩体断开,形成不连续止水帷幕,洞口周边漏水严重。
堵水措施:在洞口外轮廓环向打设两排小导管,第一排导管距离洞口外轮廓200mm,一、二层小导管间距为300mm,导管环向间距为1000mm。
注浆材料选用1:1的水泥浆与水玻璃配合成1:1(体积比)的水泥—水玻璃双液浆,注浆扩散半径为0.25m。
管片下部采用钢格栅+网片+连接钢筋+小导管注浆联合支护。
注浆顺序为先内侧后外侧,同一层环向注浆管采用间隔注浆。
3.3 较小漏水点及渗水堵漏措施较小漏水点及渗水对施工影响不大,但也应该在施工时加以处理,防止以少积多,这种渗漏水主要在地下15.00~16.85m这一区域,漏水量每处约0.3~3.0m3/h。
施工时先用水对漏水点进行清洗,再用速凝型水不漏粉剂封堵漏水点和渗水面。
水不漏粉剂与水按照1:0.3配制并搅拌均匀,调制好的配料凝固时间约为3分,漏水点堵漏时将配料揉成团状,填塞漏点并将表面抹平压实封闭,渗水面堵水时用抹子均匀地涂抹一层配料,厚度为2~4mm,反复碾压整平,直到不再有渗水为止,如第一层不能达到堵漏效果时再涂抹第二层。
3.4 引、排水措施漏水情况:该站基坑四周水源相通,通过预注浆堵水和集中堵水后,大面积漏水基本得到解决,局部有压水无法根除,具体为每100m2有5~8个漏水点,分布在基底以上6m范围。
引排措施:①在开挖至底层(深度为16.85m)时,土层为黏土,上部渗漏水与黏土形成泥浆,影响施工,为保证基坑大面积无水作业,在基坑四周开挖一条断面为30cm(宽)×20cm(深)的盲沟,
每隔40~50m设一集水坑,盲沟沿东西走向设3‰的下坡,盲沟和集水坑内铺满透水性良好的碎石,同时在盲沟内埋置一根φ80的排水盲管,确保排水畅通,水流通过盲沟排至坑内集水坑,再使用抽水机或泥浆泵集中排出基坑外。
②侧壁漏水点通过在基坑侧壁开孔插入塑料软管引流,管外壁空隙用水不漏封堵,塑料软管直径为10mm,有压水流通过塑料软管排至两侧排水盲沟。
③为防止基坑侧壁渗漏水流入基坑内,在侧壁铺设一层塑料薄膜,并将引水软管连同塑料薄膜埋放至盲沟内,侧壁有流水时可通过水管或沿塑料薄膜流入排水盲沟,再排除基坑外,达到引、排水的效果。
4 效果分析本工程针对基坑渗漏水不同部位和不同情况采取不同的堵水措施,先堵大面积,再集中处理分散漏水点,最后对有压水进行引、排,整个过程对附近水源采取截流措施,效果如下: (1)采用长、短管进行深层注浆和二次补偿注浆,注入水泥浆每孔0.6~4.7m3,注水泥—水玻璃双液浆每孔0.3~1.2m3,注浆后基坑侧壁无大面积漏水。
(2)集中性漏水点采取先引水,再进行单管注水泥—水玻璃双液浆,注浆量为 1.7~2.6m3,注浆后90%以上漏水点无漏水现象。
(3)个别有压漏水点通过导管、盲沟引流排水,防止了渗漏水进入基坑。
(4)基坑周边建筑物无裂缝、坍塌,地面沉降变化终值为49mm,围护结构斜率变化为8mm,均在可控范围,基坑四周各种管线安全可靠。
(5)结构及防水层施工基本达到无水作业。
结束语
综上所述,地铁车站工程的施工条件复杂、难度较大,渗漏水问题是困扰着地铁车站工程施工人员的难题。
因此,应引起高度重视,不能掉以轻心,必须已预防为主,一旦发生渗漏水问题,必须详细了解现场实际地质情况,并采取有针对性的治理措施,这样才能提高地铁车站工程的整体质量。