采煤机选型方案分析
关于采煤机选型说明研究
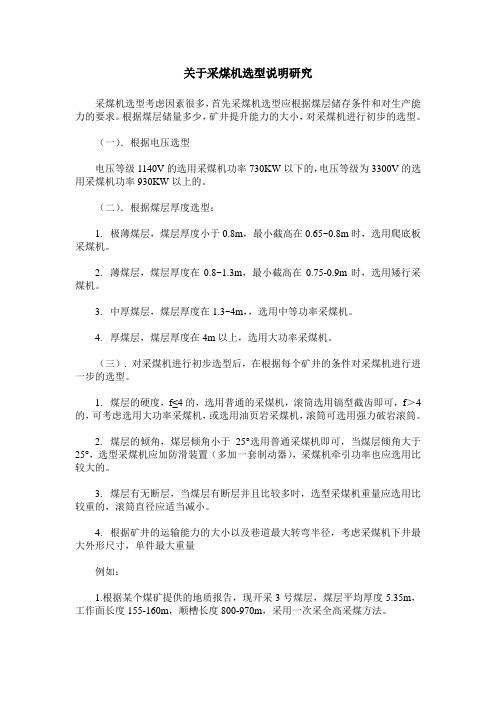
关于采煤机选型说明研究采煤机选型考虑因素很多,首先采煤机选型应根据煤层储存条件和对生产能力的要求。
根据煤层储量多少,矿井提升能力的大小,对采煤机进行初步的选型。
(一).根据电压选型电压等级1140V的选用采煤机功率730KW以下的,电压等级为3300V的选用采煤机功率930KW以上的。
(二).根据煤层厚度选型:1. 极薄煤层,煤层厚度小于0.8m,最小截高在0.65~0.8m时,选用爬底板采煤机。
2. 薄煤层,煤层厚度在0.8~1.3m,最小截高在0.75-0.9m时,选用矮行采煤机。
3. 中厚煤层,煤层厚度在1.3~4m,,选用中等功率采煤机。
4. 厚煤层,煤层厚度在4m以上,选用大功率采煤机。
(三). 对采煤机进行初步选型后,在根据每个矿井的条件对采煤机进行进一步的选型。
1. 煤层的硬度,f≤4的,选用普通的采煤机,滚筒选用镐型截齿即可,f>4的,可考虑选用大功率采煤机,或选用油页岩采煤机,滚筒可选用强力破岩滚筒。
2. 煤层的倾角,煤层倾角小于25°选用普通采煤机即可,当煤层倾角大于25°,选型采煤机应加防滑装置(多加一套制动器),采煤机牵引功率也应选用比较大的。
3. 煤层有无断层,当煤层有断层并且比较多时,选型采煤机重量应选用比较重的,滚筒直径应适当减小。
4. 根据矿井的运输能力的大小以及巷道最大转弯半径,考虑采煤机下井最大外形尺寸,单件最大重量例如:1.根据某个煤矿提供的地质报告,现开采3号煤层,煤层平均厚度5.35m,工作面长度155-160m,顺槽长度800-970m,采用一次采全高采煤方法。
2.运输条件:斜井、倾角23°、双轨、最大运送重量15吨,最大尺寸长5.5m×宽1.8m×高2.2m(含平板车高度)。
3.煤层走向倾角最大10°,工作面倾角最大15°,煤层节理较发育。
4. 采煤机截割功率计算按采煤机单位能耗计算采煤机功率为:N=60kb•B•Hg•Vmax•Hw式中:N——采煤机截割功率,kW;kb——备用系数,取1.3;Hw——采煤机割煤单位能耗,本矿取Hw=0.55kW•h/m3。
采煤机选型
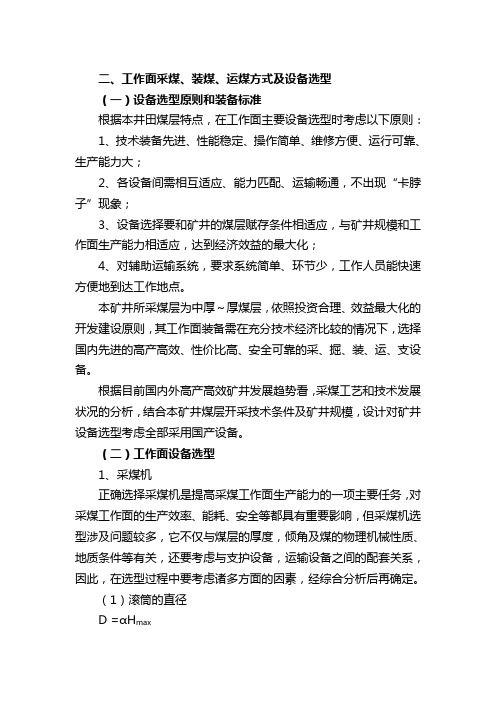
二、工作面采煤、装煤、运煤方式及设备选型(一)设备选型原则和装备标准根据本井田煤层特点,在工作面主要设备选型时考虑以下原则:1、技术装备先进、性能稳定、操作简单、维修方便、运行可靠、生产能力大;2、各设备间需相互适应、能力匹配、运输畅通,不出现“卡脖子”现象;3、设备选择要和矿井的煤层赋存条件相适应,与矿井规模和工作面生产能力相适应,达到经济效益的最大化;4、对辅助运输系统,要求系统简单、环节少,工作人员能快速方便地到达工作地点。
本矿井所采煤层为中厚~厚煤层,依照投资合理、效益最大化的开发建设原则,其工作面装备需在充分技术经济比较的情况下,选择国内先进的高产高效、性价比高、安全可靠的采、掘、装、运、支设备。
根据目前国内外高产高效矿井发展趋势看,采煤工艺和技术发展状况的分析,结合本矿井煤层开采技术条件及矿井规模,设计对矿井设备选型考虑全部采用国产设备。
(二)工作面设备选型1、采煤机正确选择采煤机是提高采煤工作面生产能力的一项主要任务,对采煤工作面的生产效率、能耗、安全等都具有重要影响,但采煤机选型涉及问题较多,它不仅与煤层的厚度,倾角及煤的物理机械性质、地质条件等有关,还要考虑与支护设备,运输设备之间的配套关系,因此,在选型过程中要考虑诸多方面的因素,经综合分析后再确定。
(1)滚筒的直径D =αH max式中:α——螺旋滚筒装煤效率;对小直径滚筒,α=0.59~0.63;对大直径滚筒,α=0.56~0.59。
H max——采高,计算时取最大采高,3号煤层取3.3m。
则:D =0.56×3.3=1.84m由于综采工作面双滚筒采煤机一般都是一次采全高,故滚筒直径D应稍大于最大采高之半,即D>1/2×H max。
目前采煤机滚筒直径已经系列化,分别为0.6m、0.65m、0.7m、0.8m、0.9m、1.0m、1.1m、1.25m、1.4m、1.6m、1.8m、2.0m、2.3m、2.6m。
采煤机选型推荐

Qm = k2 Q t/h
式中 k2——采煤机在实际工作中的连续工作系数,
一般为0.6~0.65 。
6
采煤机总体参数与选型 2. 截割高度
采煤机的实际开采高度。 采煤机的截割高度应与煤层厚度的变化范围相适应。
7
采煤机总体参数与选型
采煤机说明书中的“截割高度 ”,往往是滚筒的工作高 度 ,而不是真正的截割高度。
9
采煤机总体参数与选型
截深选择还要考虑煤层的压张效应。 当被截割煤体处于压张区内时 ,截割功率明显下降 。
一般压张深度为煤层厚度的0.4~1.0倍 。脆性煤取大值 , 韧性煤取小值。
截深为煤层厚度的1/3时 ,截割阻力比未被压张煤的 截割阻力小1/3~1/2 。为充分利用煤层压张效应 , 中厚 煤层截深一般取0.6m左右 。大功率电牵引采煤机向大截深 方向发展 ,0.9m左右 ,部分截深达1.2m。
坚固性系数f 只反映煤体破碎的难易程度 ,不能完全 反映采煤机滚筒上截齿的受力大小 ,有些国家采用截割 阻抗A表示煤体抗机械破碎的能力 。截割阻抗标志着煤 岩的力学特征 ,根据煤层厚度和截割阻抗 ,选取装机功 率。
装机功率也可按现有采煤机进行类比选取。
2
采煤机总体参数与选型
2. 根据煤层厚度选型 (1)极薄煤层 煤层厚度小于0.8m 。最小截高在 0.65~0.8m时 , 只能采用爬底板采煤机。 (2)薄煤层 煤层厚度0.8~1.3m 。最小截高在0.75~ 0.90m时 ,可选用骑槽式采煤机。 (3)中厚煤层 煤层厚度为1.3~3.5m 。选择中等功 率或大功率的采煤机。 (4)厚煤层 煤层厚度在3.5m以上 。适应于大截高 的采煤机应具有调斜功能 , 以适应大采高综采工作面地 质及开采条件的变化; 由于落煤块度较大 ,采煤机和输 送机应有大块煤破碎装置 , 以保证采煤机和输送机的正 常工作。
煤矿用采煤机及刮板机的选型

第一章 采煤机的选择机械化采煤工作面根据支护类型的不同可以分为普采和综采,本设计中采区原始数据如下表:采 区 原 始 数 据大的断层、夹矸,该工作面生产能力较高,因此我们采用综合机械化采煤生产工艺。
一、采煤机性能参数的计算与决定 1. 滚筒直径的选择双滚筒采煤机的滚筒直径应大于最大采高的一半,按经验公式双滚筒采煤机的滚筒直径D=(0.52~0.6) h max =0.6×2.3=1.38米,初步选取滚筒直径为1.4米。
2. 截深的选择滚筒截深是采煤机工作机构截入煤壁的深度,截深的确定与煤层的压张效应,截割阻抗(截齿截割单位切削厚度所对应的截割阻力)大小,煤层厚度、倾角、顶板稳定性及采煤机稳定性有关。
本设计中采煤机的工作在厚煤层中截深宜小,可取0.5米,但国内的采煤机为了制造方便截深一般为0.6米,故本设计中采煤机的截深取0.6米。
3. 滚筒转速及截割速度滚筒的转速对能耗、装载、煤尘影响很大,由公式采煤机截齿的最大切削厚度nm Vh ∙=1000m ax 可知,当采煤机一条截线上安装的截齿数m 、牵引速度v 已定时转速n 愈高,煤尘产生量愈大,截割部耗能也就愈高。
在实践中滚筒转速愈高则循环愈快,采煤机装煤效果不好。
一般认为滚筒的转速控制在30~50转/分为宜。
本设计中滚筒转速n=45转/分滚筒的转速及直径确定后采煤机的截齿截割速度也就定了,一般控制在4米/秒。
4. 采煤机的最小设计生产率采煤机的最小设计生产率用公式表示为2.024m in ⨯=WQ = 1300/24×0.2=270.83吨/小时式中:W 采煤机的日平均产量,查表可知W=39×104/300=1300吨。
5. 采煤机截割时的牵引速度及生产率1)根据采煤机的最小设计生产率Q min 决定牵引速度V 1rB H Q V ∙∙∙=60m in1≈270.83/60×2.3×0.6×1.35=2.42米/分式中Q min ---------采煤机的最小设计生产率,这里取270.83吨/小时。
(完整word版)采煤机选型计算
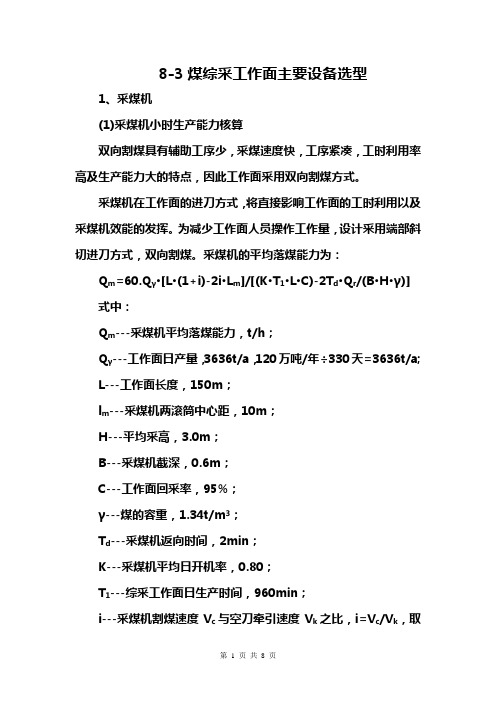
8-3煤综采工作面主要设备选型1、采煤机(1)采煤机小时生产能力核算双向割煤具有辅助工序少,采煤速度快,工序紧凑,工时利用率高及生产能力大的特点,因此工作面采用双向割煤方式。
采煤机在工作面的进刀方式,将直接影响工作面的工时利用以及采煤机效能的发挥。
为减少工作面人员操作工作量,设计采用端部斜切进刀方式,双向割煤。
采煤机的平均落煤能力为:Q m=60.Qγ·[L·(1+i)-2i·L m]/[(K·T1·L·C)-2T d·Q r/(B·H·γ)] 式中:Q m---采煤机平均落煤能力,t/h;Qγ---工作面日产量,3636t/a,120万吨/年÷330天=3636t/a;L---工作面长度,150m;l m---采煤机两滚筒中心距,10m;H---平均采高,3.0m;B---采煤机截深,0.6m;C---工作面回采率,95%;γ---煤的容重,1.34t/m3;T d---采煤机返向时间,2min;K---采煤机平均日开机率,0.80;T1---综采工作面日生产时间,960min;i---采煤机割煤速度V c与空刀牵引速度V k之比,i=V c/V k,取i=0.5则工作面采煤机平均落煤能力:Q m=60×3636×[150×(1+0.5)-2×0.5×10]/[0.8×960×150×0.95-2×2×3636/(0.6×3.0×1.34)]=453.6t/h(2)采煤机平均割煤速度综采工作面,按采煤机平均落煤能力为454t/h计算割煤速度:V c=Q m/(60·B·H·γ·C)=454/(60×0.6×3.0×1.34×0.95)=3.3m/min(3)采煤机最大割煤速度和最大生产能力采煤机最大割煤速度:V max= K c·V c采煤机最大生产能力:Q max= K c·Q m式中:V max---采煤机最大割煤速度,m/min;Q max---采煤机最大落煤量,t/h;K c---采煤机割煤不均衡系数,取1.3;则:V max=1.3×3.3=4.3m/minQ max=1.3×454=590t/h(4)采煤机装机功率按采煤机单位能耗计算采煤机功率为:N=60K b×B×H×V max×H W式中:N——采煤机功率,kWB——截深,B=0.6mH——采高,H=3.0mH W——能耗系数H W=0.8kWh/m3V max——采煤机最大割煤速度,4.3m/min。
495B1 2工作面设备选型设计讲解
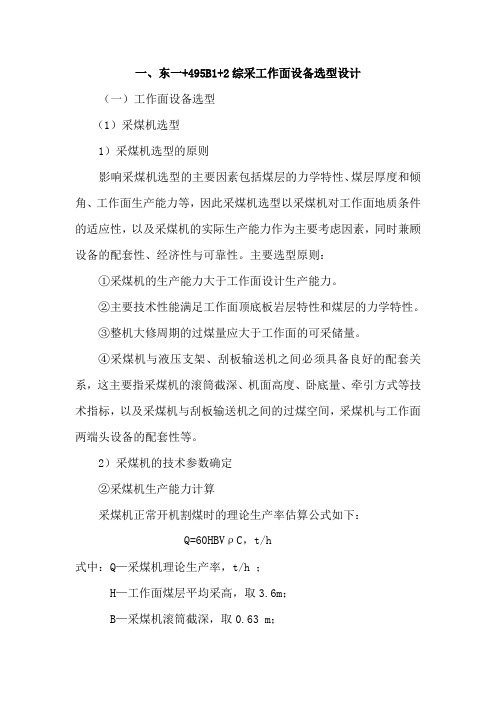
一、东一+495B1+2综采工作面设备选型设计(一)工作面设备选型(1)采煤机选型1)采煤机选型的原则影响采煤机选型的主要因素包括煤层的力学特性、煤层厚度和倾角、工作面生产能力等,因此采煤机选型以采煤机对工作面地质条件的适应性,以及采煤机的实际生产能力作为主要考虑因素,同时兼顾设备的配套性、经济性与可靠性。
主要选型原则:①采煤机的生产能力大于工作面设计生产能力。
②主要技术性能满足工作面顶底板岩层特性和煤层的力学特性。
③整机大修周期的过煤量应大于工作面的可采储量。
④采煤机与液压支架、刮板输送机之间必须具备良好的配套关系,这主要指采煤机的滚筒截深、机面高度、卧底量、牵引方式等技术指标,以及采煤机与刮板输送机之间的过煤空间,采煤机与工作面两端头设备的配套性等。
2)采煤机的技术参数确定②采煤机生产能力计算采煤机正常开机割煤时的理论生产率估算公式如下:Q=60HBVρC,t/h式中:Q—采煤机理论生产率,t/h ;H—工作面煤层平均采高,取3.6m;B—采煤机滚筒截深,取0.63 m;V—采煤机截煤时的平均牵引速度,取2m/min;ρ—煤的实体密度,取1.3t/m3;C—工作面采煤机回采率,取0.80。
Q=60×3.2×0.63×2×1.3×0.8=283t/h该工作面以放顶煤为主,采煤机割煤量以割煤高度3.6m来估算采煤机正常开机割煤时的理论生产率。
③装机功率采煤机装机功率可以采用比能法进行计算。
P=QH w,kW式中:P—装机功率,kW;Q—采煤机的理论生产率,283t/h;H w—采煤机单位能耗,取0.83kW.h/t。
P=QH w=252×0.83=234.89kW因此,选用的采煤机装机功率应不小于250kW。
配套采煤机主要性能和技术参数应满足以下要求:a、采煤机的生产能力大于250t/h;b、采煤机允许的平均截割牵引速度大于2m/min;c、采煤机应优先选用630mm截深的滚筒;d、采煤机的装机功率不低于250kW;e、采煤机牵引功率50kW以上,牵引力250kN以上;f、滚筒直径1.8m。
综合采煤机械选型设计
第一篇绪论对于采矿工程专业的学生,对于综采工作面的机械设备选型,是必须掌握的知识及能力。
具体条件及要求是:在给定的采面地质条件的基础上,根据相关的设计规范、法规,对该工作面采用综合机械化采煤方法所用的机械设备进行合理、科学的计算选型。
撰写选型设计说明书。
采煤工作面中,采煤机、刮板运输机和支护设备(液压支架或单体支柱与顶梁)等组成一个称为采煤机的有机整体来实现采煤工艺的各个工序,它们在工作能力和结构尺寸的配套关系,直接影响到采煤工艺的顺利实施和设备能力的充分发挥。
因此,为了正确地选择采煤机组各种设备的形式,不仅要看它们能否满足采煤工艺的要求,同时要注意它们之间的配套性能。
本次设计选取的原始参数为:工作面长度:300米;煤层倾角:12;煤层平均厚度:4米;顶板条件:中等稳定;A=300N/mm;f=3.5 。
第二篇综采工作面机械选型设计第一章滚筒采煤机的选用机械化采煤工作面的生产能力主要取决于采煤机的落煤、装煤能力;而落煤、装煤能力又与煤层的地质条件和机器自身的性能、参数、整体结构有关。
因此,根据地质条件正确选择采煤机械,对于充分发挥机器能力、提高工作面产量、降低能耗、安全生产有着十分主要的意义。
一、采煤机的选型通常是要符合煤层赋存条件,满足对生产能力的要求,以及与刮板输送机和液压支架的匹配要求。
需根据以下几方面确定采煤机的型号:1.根据煤层坚硬度选型本次设计煤层坚硬度系数f=3.5,A=300N/mm,属坚硬煤层;倾角12°属缓倾斜煤层,须选用大功率双滚筒式采煤机。
2.根据煤层厚度选型煤层厚度为4米,属中厚煤层,可选用的采煤机型号有MG400/920-WD、MG400/930-QWD、MG300—W、MG450/1030-WD等。
3.根据煤层倾角选型煤层倾角大于10°,须增设防滑装置。
二、生产率计算1.理论生产率 Q t =60HBv qρ=60×4×0.63×7.96×1.3=1564.6 t/hH ━是工作面平均采高m;B ━为滚筒有效截深,m;v q ━为在所给工作面条件下可能的最大工作牵引速,m/min;ρ━为煤的实体密度,取 1.3-1.4t/m3 。
综采工作面机械选型设计
综采工作面机械选型设计一、综采工作面简介综采工作面是采煤工作面的一种特殊形式,采用综合采煤机进行开采。
综采工作面具有高效、安全等特点,是现代煤矿生产中常见的采煤方式。
综采工作面机械设备的选型设计对于提高采煤效率、保障工作面安全具有至关重要的意义。
二、综采工作面机械选型设计原则在进行综采工作面机械选型设计时,需要遵循以下原则:1.适用性原则:选型的机械设备需要适应工作面的采煤工艺和工况要求,确保设备具备完成作业任务的能力。
2.可靠性原则:选型的机械设备应具有良好的可靠性和稳定性,能够保障工作面的连续、高效运行。
3.安全性原则:选型的机械设备要符合相关安全标准和规定,保障工作面作业人员的安全。
4.经济性原则:在满足工作面作业需求的基础上,选型的机械设备应具有较高的性价比,综合考虑设备的采购成本、运行成本等因素。
三、综采工作面机械选型设计过程综采工作面机械选型设计的具体过程主要包括以下几个步骤:1. 了解工作面采煤情况首先需要对待采煤矿井的地质情况、煤层赋存、采煤工艺等进行详细了解,确定工作面的采煤情况,为后续选型设计提供依据。
2. 分析机械设备需求根据工作面的采煤情况和工艺要求,分析机械设备在工作面上的具体作用和需求,确定所需设备的类型、规格、数量等参数。
3. 确定候选设备根据对工作面情况和设备需求的分析,筛选出符合工作面要求的候选机械设备,进行初步的比较和评估。
4. 进行设备比较与评估对候选设备进行详细的比较与评估,包括设备的技术参数、性能指标、价格等因素,综合考虑设备的优劣势,选择最适合工作面的设备。
5. 制定选型方案根据设备比较与评估的结果,制定最终的机械选型设计方案,确定所选设备的具体型号、配置和数量等信息。
6. 完善设计方案对选型设计方案进行细化和完善,包括制定工作面的机械设备布置方案、工作流程等,确保设备的合理配置和高效运行。
四、结语综采工作面机械选型设计是综采工作面生产的关键环节,只有合理选择适用的机械设备,才能保障工作面的高效、安全运行。
综采工作面机械选型设计
综采工作面机械选型设计随着煤炭工业的发展,综采工作面逐渐成为了煤矿生产中不可或缺的部分。
而综采工作面的机械选型设计则至关重要。
本文将从综采工作面的机械选型和设计两个方面进行讨论。
一、综采工作面机械选型1. 煤矿综采工作面的机械设备种类繁多,常见的包括煤炭采掘机、转载机、支架、风机、水泵等。
其中,综采机是综采工作面中最为重要的设备之一,选择合适的机型对于提高采煤效率及降低采矿成本等方面有着重要作用。
2. 根据不同的工作面情况,综采机的型号和数量会有所变化。
一般来说,较大的工作面会需要更多、更高效的综采设备。
此外,由于综采机在采煤时需要不断移动和调整姿态,机械的稳定性也是选型过程中需要重视的问题。
3. 选择综采机型号时,还需要考虑到不同型号之间的区别。
例如,液压传动式综采机拥有较为便捷的操控方式和较低的噪音水平,而链传动式综采机则拥有更高的采煤效率和更强的适应性。
二、综采工作面机械设计1. 综采设备设计需要考虑到开采的煤种、厚度以及周围环境等因素。
例如,对于在煤层较薄的综采工作面,支架必须更加灵活,以适应地质构造的复杂性。
2. 机械的外型和结构也是设计中需要重视的方面。
为了更好地适应复杂的工作环境,一些综采设备需要配有防尘、隔爆等装置。
此外,在风电设备的选择和设计中,合适的气动设计将会更加有效地降低由设备产生的噪音和粉尘。
3. 设计中还需要考虑到使用寿命及维护问题。
在设计过程中要充分考虑到机械使用环境和使用频率等因素,在原则上要确保最大程度地延长设备使用寿命并尽量降低设备故障率。
综合来看,综采工作面机械选型及设计是煤炭工业发展中的重要环节。
除了考虑设备的采煤效率和适应性外,还要细致地设计每一个部件,以确保设备的安全性和可靠性,为煤炭生产提供支持。
综合机械化采煤机的选型原则及选型方案
综合机械化采煤机的选型原则及选型方案摘要采煤机是综合机械化采煤工艺的主要设备之一,它的正确选择关系到采煤工作面的安全、高效、高产等方面都具有重要影响,特别是我国在对中厚、缓倾斜煤层,已达到了相当成熟的水平。
结合我矿的地质条件、采煤工艺、煤层厚度和煤层倾角的不同。
其次还要考虑与采煤机相互配套的支护设备、运输设备之间的关系,因此,作为综合机械化长壁采煤工艺的核心配套设计内容之一的采煤机选型,必须面对和处理一些特殊的复杂的情况,经综合分析后才能确定如何选择采煤机。
关键词采煤机的选型原则;影响因素;选型方案1 采煤机的选型原则作为综合机械化长壁采煤工艺的核心配套设计内容之一的采煤机在初步选型时必须考虑下列的原则:1)与采煤工作面的地质条件和采煤机的主要参数并能够满足较大的适用范围;2)与采煤工作面生产能力相匹配;3)与配套支护设备、运输设备的主要技术参数相匹配;4)与通风、提升等系统条件相适应;5)与工作面长度、采区走向长度、巷道断面尺寸等矿山技术因素相互适应;6)与采煤机技术性能良好,工作可靠性高,各种保护功能完善且使用、检修、维护方便相互适应。
2 采煤机的主要影响因素综合机械化采煤工作面采用双滚筒采煤机落煤、装煤并自开缺口,重型可弯曲刮板输送机运煤、自移式液压支架维护和管理顶板,使采煤过程全部实现机械化。
综合机械化的设备与工序密切联系、连续作业,因而产量大、效率高、安全性能好。
但是影响采煤机高产、高效、安全的主要因素有地质因素(煤层的坚硬程度、煤层倾角、煤层厚度、煤层及围岩特征、煤层的含水性和自燃情况、煤层的地质构造情况)、采煤工艺和采煤机相互配套的支护、运输设备之间的关系方面的因素。
如果能够合理的避免这些不利因素则能取得较好的经济效益和社会效益。
2.1煤层的坚硬程度煤层的坚硬程度直接影响到采煤机的选择多大功率。
当采煤工作面开采f<4的缓倾斜及急倾斜煤层时,可采用中等功率的双滚筒采煤机,对粘性煤及f=2.5~4的中硬以上煤层时,采用大功率双滚筒采煤机。
- 1、下载文档前请自行甄别文档内容的完整性,平台不提供额外的编辑、内容补充、找答案等附加服务。
- 2、"仅部分预览"的文档,不可在线预览部分如存在完整性等问题,可反馈申请退款(可完整预览的文档不适用该条件!)。
- 3、如文档侵犯您的权益,请联系客服反馈,我们会尽快为您处理(人工客服工作时间:9:00-18:30)。
采煤机选型设计方案江苏中机矿山设备有限公司2012年3月31日煤层条件1.采高满足1.2~2.4米;2.工作面长200米;3.单工作面年产90万吨;4.煤质f=3~4;采煤机采煤机各部件性能参数的计算与决定滚筒直径的选择根据目前我国采煤机生产现状及使用情况,设计选用双滚筒采煤机。
双滚筒采煤机滚筒直径应大于最大采高h max的一半,一般可按D=(0.52~0.6)h max选取,采高大时取小值,采高小时取大值。
目前双滚筒采煤机的滚筒直径也已经系列化,所以滚筒直径的选取选取和标准直径相近的数值。
对此工作面,由于其基本煤层厚度为1.2~2.4米,D=0.6×2.4=1.44(m)由于需要到达的采高为1.2-2.4,综合考虑,建议选取φ1400滚筒。
截深的选择截深的选择,受煤层厚度、倾角、顶板稳定性、截割阻抗、及液压支架的推移步距影响,设计选取截深为800mm。
滚筒转速及截割速度滚筒转速的选择,直接影响截煤比能耗、装载效果、粉尘大小等。
转速过高,不仅煤尘产生量大,且循环煤增多,转载效率降低,截煤比能耗降低。
根据实践经验,一般认为薄煤层采煤机滚筒的转速应控制在40~70转/分较为适宜。
设计取57.1转/分。
采煤机最小设计生产率采煤机最小设计生产率与采煤机有效开动率有关。
虽然综合机械化开采在我国中厚煤层一次采全高工作面的应用已经成熟,机械设备的生产加工技术也比较完善,设备可靠性也大大提高,但采煤工作面煤层潜在的变数及机械设备的检修等的各种因素均影响采煤机有效开动率,我国平均水平在40%左右。
设计取正常开动率为40%。
采煤机最小设计生产率由下式计算:4.024m in ⨯=WQ式中:Q min ——采煤机最小设计生产率,t/h ,W ——采煤工作面的日平均产量,900000÷300=3000(t ) 0.4——采煤机有效开动率。
则:)/(5.3124.02430004.024m in h t W Q =⨯=⨯=采煤机在截割时的牵引速度及生产率采煤机截割时牵引速度的高低,直接决定采煤机的生产效率及所需电机功率,由于滚筒装煤能力,运输机生产效率,支护设备推移速度等因素的影响,采煤机在截割时的牵引速度比空调时低得多,采煤机牵引速度在零到某个值范围内变化,选择截煤机时的牵引速度,要根据下述几个方面因素,综合考虑。
根据采煤机最小设计生产率Qmin 决定的牵引速度V 1γ···60min1B H Q V =m/min式中:Q min ——采煤机最小设计生产率,312.5t/h , H ——采煤机平均采高,1.9m , B ——采煤机截深,0.8m γ——煤的容重,1.4t/m3min)/(8.14.18.06.2605.312···60min 1m B H Q V =⨯⨯⨯==γ 根据截齿最大切削厚度决定的牵引速度V 2采煤机截割过程中,是滚筒以一定的转速n ,同时又以一定的牵引速度V 2沿工作面移动,切削厚度呈月牙规律变化,如果滚筒一条截线上安装的截齿数为m ,则截齿最大的切削厚度h max 在月牙中部,可用下式求出。
n 10002max ⋅=m V h mm上式中,m 一般取3,n 根据上面的计算取57.1转/分。
一般来说,h max 应小于截齿伸出齿座长度的70%,根据国产采煤机的实际情况,取45mm 。
则:1000n max 2h m V '⋅⋅⋅=m/min式中:h ’max ——截齿在齿座上伸出长度的70%,取45mm 。
则:min)/(7.71000451.5731000n max 2m h m V =⨯⨯='⋅⋅=按液压支架的推移速度决定牵引速度V 3一般讲支架的推移速度应大于采煤机的牵引速度较好,这样可保证采煤机安全生产。
截割时牵引速度V 应根据上述三方面情况综合分析后确定,其最大值应等于或大于V 1,但应小于V 2,并与V 3协调,使采煤机既能满足工作面生产能力的要求,又可避免齿座或叶片参与截割,并能保证采煤机安全生产。
综上所述,采煤机的牵引速度取V =2-4.5m/min 采煤机的牵引速度确定后,则采煤机的生产率Q 为 Q =60²H ²B ²V ²γ t/h将上述确定的直带入公式求得采煤机的生产率为 Q =60³2.6³0.8³4³1.4=699(t/h )因此可知,每小时产量为699 t/h ,远大于公司设计要求小时产量312.5 t/h 。
采煤机所需电机功率针对煤层的赋存条件、开采技术条件及选用的采煤方法,主要设备选型时既要考虑煤层厚度,又要满足工作面通风要求,结合我国薄煤层综采或高档普采工作面设备配备情况,选用性能良好、可靠性高,并适合于矿井具体条件的较先进设备,根据这一基本原则,对工作面采、装、运设备进行选型。
工作面煤的平均普氏硬度指数f=3-4,为硬煤层,可取截割阻抗为360-480N/mm 。
根据下述公式可求得采煤机截割时的比能耗H ωXB XX H A A H ωω⋅=式中:H ωX ——煤层截割比能耗,kW ²h/t , A X ——煤层最大截割阻抗,480 N/mm , A ——基准煤截割阻抗,取190 N/mm ,H ωB ——基准煤比能耗,通过插入法计算知,当牵引速度为5.5m/min 时,基准煤比能耗为0.39 kW ²h/t 。
则:)/98.039.0190480t h kW H A A H B X X ⋅=⨯=⋅=ωω 1、按采煤机单位能耗计算采煤机装机功率为: N=60 Kb•B•H•Vmin•Hw式中:N ——采煤机装机功率,kW ; Kb ——备用系数,取1.5; B ——采煤机截深,0.8m ;H ——采煤机割煤高度,2.6m;Hw——采煤机割煤单位比能耗,按潞安、晋城等矿区实测统计资料,Hw=0.65-0.85kWh/m3,结合本矿煤层的具体情况,考虑取Hw=0.98kWh/m3 Vave——采煤机平均割煤速度,取Vave=3.5m/minN=60Kb•B•H•Vave•Hw=60³1.5³0.8³2.4³3.5³0.98=558.6kW根据上述计算,按照采煤机总装机功率大于558.6kW的原则,根据我公司现有机型选型,可选用MG250/600-WDK型交流电牵引采煤机或者MG2³125/580-WD 型交流电牵引采煤机。
采煤机详细生产能力以及技术参数分别如方案一及方案二所示:采煤机实际生产能力计算方案一:MG2³125/580-WDK型交流电牵引采煤机方案一推荐采煤机的产品的特点及技术关键1、采煤机的主要特点(1)主参数先进合理装机功率580 kW,截割功率2³2³125kW,牵引力可达420kN,最高满载牵引速度可达7.6m/min,调动速度可达12m/min。
机身高度只有939 mm,特别适合采高度小而要求截割功率大的复杂地质条件工作面。
利于在该类工作面中实现高产高效。
(2)多电机横向布置采用多电机横向布置大框架总体结构,所有电机均横向布置于机身上,与纵向布置单、双电机驱动的结构相比,各部件都有独立的动力源,相互之间没有动力传递,无通轴、伞齿轮,减少了漏油环节,使传动系统工作可靠性大大提高。
大框架结构主机分三段,段与段之间用液压螺栓付联接,联接强度大,可靠性高;取消了机身底托架结构,增加了过煤空间;摇臂支撑座受到的截割反力,油缸支撑座受到的支撑反力、行走机构的牵引反力,均由行走减速箱箱体来承受,结构简单合理,可靠性高,其受力状况是传统的底托架结构无法比拟的;采用抽屉式结构,将电机、电控箱等均可从老塘侧拆出,拆装维修方便。
采用机械独立传动的弯摇臂结构,机械系统传动可靠、装煤口大。
摇臂截割电机处设有机械离合机构,确保安全性能。
采用细长柔性扭矩轴联结,对动力传动系统有保护环节。
(5)高效高强度镐型齿滚筒采用非均布叶片设计,即可消除切割力不平衡、减少机器振动又可节省功率、降低截齿消耗。
(6)电牵引系统采用“一拖一”驱动方式,具有两台变频器分别控制两台牵引电机,对工作面的适应性更强,牵引力及牵引速度大,运行可靠的特点。
电气系统上实现模块化设计,加制动电阻可用于≤20°工作面;加逆变装置可用于≤45°工作面。
(7)电气控制系统采用PLC(可编程序控制器),具有开机操作步骤提示,故障显示和记忆、温度监控保护等功能,所有显示实现汉化。
(8)可实现离机无线电遥控、端头控制站随机操作和电控箱、变频器面板上按钮控制等多种操作方式。
(9) 机器配有有效的冷却、喷雾系统。
摇臂套、电机、变频器等均有水冷。
滚筒、摇臂上设有内外喷雾。
2、采煤机的技术关键(1)机身采煤机采用多电机横向布置、大框架加模块式部件的总体结构。
摇臂与机身用简单的销轴连接。
大框架间采用高强度液压螺栓连接,左、右牵引减速箱用高强度液压螺栓与框架连接。
泵站、电控箱像抽屉一样安装在框架内,而且不承受外力,不易损坏,皆可从老塘侧拆装。
整机结构性能好,便于维修时安装、更换。
(2)摇臂采煤机摇臂回转采用小销轴结构与机身相连,与其它大部件间没有齿轮传动,回转部分的磨损与摇臂内的齿轮啮合无关。
摇臂齿轮减速都是简单的直齿传动,精度高、传动效率高。
截割电动机和摇臂主动齿轮之间,采用细长柔性扭矩轴联结,即使电动机和摇臂主动齿轮位置有少量误差,也不影响动力传递,便于安装,在受到较大的冲击载荷时对截割传动系统的齿轮和轴承起到缓冲作用,提高了可靠性。
摇臂采用弯摇臂形式,较直摇臂可以加大装煤口,提高装煤效率,增加块煤率。
摇臂上、下有冷却水套,以降低摇臂内油池的温度。
(3)高效高强度镐型齿滚筒我公司设计的滚筒的主要技术特点:截齿布置方式合理,截割平稳性好,载荷波动幅值低于10%。
在确保工作平稳的条件下,滚筒上截齿总数可达到最小,与原刀型齿滚筒相比块煤率可提高5~10%。
能确保截齿处于回转状态下工作,煤质硬度f≤4的情况下,齿耗低于7把/万吨。
设有专用装煤叶片,能有效地提高装煤效率。
在总体配套合理的情况下,滚筒装载效率高达90~95%;我公司的MG200/475-W采煤机配套的镐型齿滚筒用于永煤集团陈四楼矿150俯采工作面,装煤效果良好,高于进口镐型齿滚筒。
滚筒叶片开端设有安装喷嘴的小叶片,滚筒旋转时能形成雾环,有效地抑制工作面粉尘。
采用堆焊或喷焊高硬度耐磨材料等特殊制造工艺,在f≤4的正常使用的情况下,滚筒大修周期为过煤量100万吨以上。
(4)牵引减速箱牵引减速箱采用双浮动、四行星轮行星减速器,轴承寿命和齿轮强度的裕度大,可靠性高。