钢铁企业能耗大数据模型及采集
钢铁企业能耗数据模型及采集
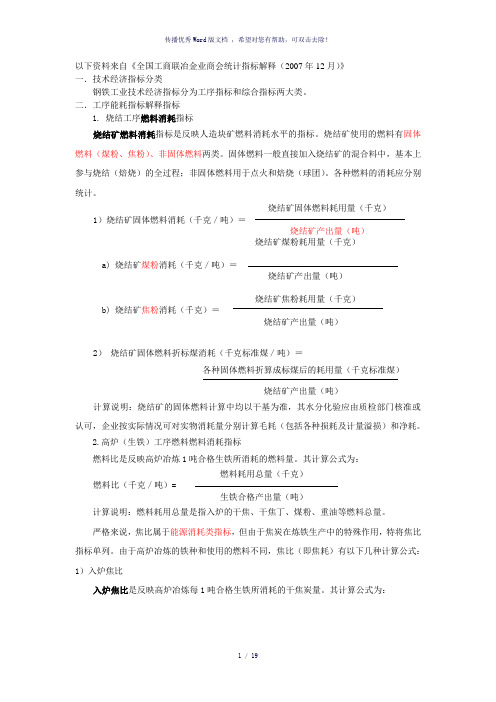
以下资料来自《全国工商联冶金业商会统计指标解释(2007年12月)》一.技术经济指标分类钢铁工业技术经济指标分为工序指标和综合指标两大类。
二.工序能耗指标解释指标1. 烧结工序燃料消耗指标烧结矿燃料消耗指标是反映人造块矿燃料消耗水平的指标。
烧结矿使用的燃料有固体燃料(煤粉、焦粉)、非固体燃料两类。
固体燃料一般直接加入烧结矿的混合料中,基本上参与烧结(焙烧)的全过程;非固体燃料用于点火和焙烧(球团)。
各种燃料的消耗应分别统计。
烧结矿固体燃料耗用量(千克)1)烧结矿固体燃料消耗(千克/吨)=烧结矿产出量(吨)烧结矿煤粉耗用量(千克)a) 烧结矿煤粉消耗(千克/吨)=烧结矿产出量(吨)烧结矿焦粉耗用量(千克)b) 烧结矿焦粉消耗(千克)=烧结矿产出量(吨)2)烧结矿固体燃料折标煤消耗(千克标准煤/吨)=各种固体燃料折算成标煤后的耗用量(千克标准煤)烧结矿产出量(吨)计算说明:烧结矿的固体燃料计算中均以干基为准,其水分化验应由质检部门核准或认可,企业按实际情况可对实物消耗量分别计算毛耗(包括各种损耗及计量溢损)和净耗。
2.高炉(生铁)工序燃料燃料消耗指标燃料比是反映高炉冶炼1吨合格生铁所消耗的燃料量。
其计算公式为:燃料耗用总量(千克)燃料比(千克/吨)=生铁合格产出量(吨)计算说明:燃料耗用总量是指入炉的干焦、干焦丁、煤粉、重油等燃料总量。
严格来说,焦比属于能源消耗类指标,但由于焦炭在炼铁生产中的特殊作用,特将焦比指标单列。
由于高炉冶炼的铁种和使用的燃料不同,焦比(即焦耗)有以下几种计算公式:1)入炉焦比入炉焦比是反映高炉冶炼每1吨合格生铁所消耗的干焦炭量。
其计算公式为:干焦耗用量(千克)入炉焦比(千克/吨)=生铁合格产出量(吨)2)综合焦比综合焦比是指高炉冶炼每1吨合格生铁所消耗的综合干焦(将各种燃料均折合成干焦计算)量。
其计算公式为:综合干焦耗用量(千克)综合焦比(千克/吨)=生铁合格产出量(吨)3)喷煤比喷煤比是反映高炉冶炼1吨合格生铁所消耗的煤量。
首钢能耗分析模型及软件的开发应用

张延平 胡雄光 蔡九菊 谢国威 胡云芝
( 钢技 术研 究 院) ( 首 东北 大 学)
摘 要 针对钢铁企业 的能流与物流耦合特点 ,开发 了能 源多级投 入产 出模 型 ,建立 了全流程 能耗分 析与
辅助决策系统 的应用软件 。该 系统根据钢铁企业产品结构 调整和设 备运行情 况 ,动态分 析 了能源结构 和能
目标 的前 提是 科学 准 确 的能耗 分析 和预 测 ,即建
织改变 ,实时计算 、分析企业生产及能耗水平 , 定 量 预测 能源 系统 的指 标变 化 ,从 而为企 业 调整 生产结 构 和保 证稳 定生 产 提供决 策依 据 。
1 研 究方法 与模型建立
投 入 产 出法是 运用 现代 数学 方法 和计 算 机手
idct sb sd n te i ai s o rd c i ajs e t n ait s rn ig T ruh n ia r ae o h su t n f pou t m x dut n o t o m ad fc ie nn . ho g li u
c c lto n n l sso i e e tp o u to iu to s,t e f r c s e u t r o d. l a u ain a d a ay i n d f r n r d c in st ai n h o e a tr s ls a e g o Ke o d i p to t u d l e e g o s mp in a ay i , e e g n g me t yW r s n u u p tmo e , n ry c n u t n l ss o n r ma a e n y
Ab ta t Ac o d n t t c u ln c a a t rsis f n r fo sr c c r i g o he o p i g h r ce t o e e g l w a d u p y h i o se l i c y n s p l c a n f te e tr is s n e e g n epr e ,a n r mul lv li p - u p t mo e s de eo e a d a p lc t n s fwa e f r y t e e n uto t u d li v l p d n n a p ia i o t r o i o e e g o s mpt n n lss f wh l p o e s n d cso ma i g s itn i e t b ihe nr cnu y i a a y i o oe r c s a d e iin— k n a ssa t s sa ls d. Th o e s se c u d y a c ly n l z t e n r sr cur a d h c a g o e e g c n u to y t m o l d n mi al a ay e h e e g y tu t e n t e h n e f n r y o s mp in
钢铁行业的大数据分析洞察市场趋势和客户需求

钢铁行业的大数据分析洞察市场趋势和客户需求近年来,大数据分析在各行各业中扮演着越来越重要的角色。
作为一种强大的工具,大数据分析在市场趋势和客户需求方面为钢铁行业提供了深刻的洞察力。
本文将探讨如何利用大数据分析来洞察钢铁市场趋势和客户需求,为行业的发展提供有力的支持。
1. 市场趋势分析大数据分析可以帮助钢铁行业洞察市场趋势,为企业制定正确的发展策略提供参考。
通过对大数据的收集和分析,钢铁企业可以获取到丰富的市场信息,包括市场容量、竞争格局、产品价格等方面的数据。
首先,钢铁行业可以通过大数据分析来预测市场需求量和趋势。
通过分析历史销售数据、行业报告以及相关经济指标等数据,企业可以得出市场的发展趋势,并准确预测出未来的市场需求。
这将有助于企业调整产能、制定合理的生产计划,以满足市场需求,提高生产效率。
其次,大数据分析可以帮助钢铁企业了解竞争格局和市场份额分配。
通过对竞争对手的销售数据、市场份额等信息进行分析,企业可以对市场竞争状况进行客观评估,并针对性地制定市场策略。
例如,企业可以通过分析竞争对手的产品定价和销售策略,制定相应的应对措施,提升自身在市场中的竞争力。
最后,大数据分析还可以帮助钢铁企业把握市场价格走势。
通过分析市场供需关系、原材料价格、产品销售数据等多方面的大数据,企业可以更好地了解市场价格的波动趋势,避免价格风险,制定合理的价格策略。
2. 客户需求分析大数据分析也可以帮助钢铁企业深入了解客户需求,提供定制化的产品和服务。
通过对客户的消费习惯、购买行为等数据进行挖掘和分析,企业可以为客户提供个性化的产品推荐和定制化的服务,提高客户满意度和忠诚度。
首先,企业可以通过大数据分析来了解客户对产品的需求和偏好。
通过分析客户的购买数据、评价和反馈以及社交媒体上的信息,企业可以了解客户对不同产品的偏好和需求,为客户提供个性化的产品推荐。
例如,通过分析客户购买历史和相关的产品评价,企业可以发现客户对某一特定型号的钢材需求较高,从而调整生产计划,加大对该型号产品的生产和销售力度。
钢铁行业大数据处理和分析系统设计与实现

钢铁行业大数据处理和分析系统设计与实现随着科技的进步和信息化的日趋深入,各个行业都迎来了大数据时代。
钢铁行业作为我国重要的基础产业之一,也面临着大量数据的处理和分析的挑战。
钢铁行业大数据处理和分析系统的设计与实现,能够帮助企业更有效地管理和利用数据,实现更高效的生产和运营。
一、系统需求分析1. 数据采集:设计一个钢铁行业大数据采集系统,能够定期自动采集各种数据源,并将其转化为结构化的数据格式。
2. 数据存储:建立一个可靠且高效的大数据存储系统,能够存储大量的数据并提供快速的数据访问。
3. 数据预处理:对采集到的数据进行清洗和预处理,包括去除重复数据、填补缺失值、处理异常值等。
4. 数据分析:设计数据分析模型和算法,能够对大量的数据进行精确的统计分析和挖掘,发现隐藏在数据中的有用信息。
5. 数据可视化:通过图表、仪表盘等方式,将数据分析结果以直观的形式展示给用户,便于用户理解和决策。
6. 数据安全:建立严格的数据安全机制,保护数据的完整性和隐私,防止未经授权的访问和篡改。
7. 系统性能:保证系统具备高并发、高可用、高稳定性的特点,能够处理海量数据,并在大数据环境下快速响应用户的查询和分析请求。
二、系统设计与实现1. 数据采集模块:设计一个数据采集模块,能够连接各种数据源,包括传感器、设备、数据库等,实现数据的自动采集和传输。
采用合适的协议和技术,确保数据的完整性和可靠性。
同时,采用分布式的架构,实现数据的横向扩展和负载均衡。
2. 数据存储模块:选择合适的存储技术,如分布式文件系统、关系型数据库、NoSQL数据库等,建立一个可靠、高效的数据存储系统。
采用数据分区和索引等技术,实现快速的数据查询和访问。
3. 数据预处理模块:设计一个数据清洗和预处理的模块,能够自动处理数据中的噪声、缺失值和异常值。
采用数据挖掘和机器学习的方法,对数据进行特征选择和降维,提高数据处理的效率和准确性。
4. 数据分析模块:选择适合钢铁行业的数据分析模型和算法,如回归分析、聚类分析、关联规则挖掘等,对大量的数据进行分析和挖掘。
大数据赋能高炉炼铁智能应用
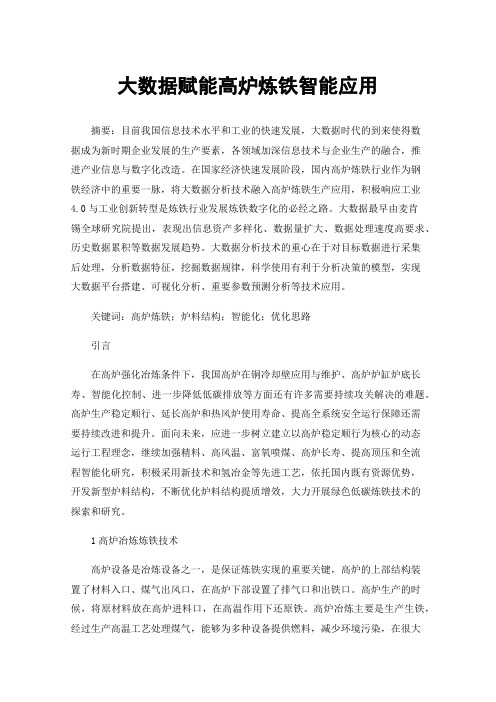
大数据赋能高炉炼铁智能应用摘要:目前我国信息技术水平和工业的快速发展,大数据时代的到来使得数据成为新时期企业发展的生产要素,各领域加深信息技术与企业生产的融合,推进产业信息与数字化改造。
在国家经济快速发展阶段,国内高炉炼铁行业作为钢铁经济中的重要一脉,将大数据分析技术融入高炉炼铁生产应用,积极响应工业4.0与工业创新转型是炼铁行业发展炼铁数字化的必经之路。
大数据最早由麦肯锡全球研究院提出,表现出信息资产多样化、数据量扩大、数据处理速度高要求、历史数据累积等数据发展趋势。
大数据分析技术的重心在于对目标数据进行采集后处理,分析数据特征,挖掘数据规律,科学使用有利于分析决策的模型,实现大数据平台搭建、可视化分析、重要参数预测分析等技术应用。
关键词:高炉炼铁;炉料结构;智能化;优化思路引言在高炉强化冶炼条件下,我国高炉在铜冷却壁应用与维护、高炉炉缸炉底长寿、智能化控制、进一步降低低碳排放等方面还有许多需要持续攻关解决的难题。
高炉生产稳定顺行、延长高炉和热风炉使用寿命、提高全系统安全运行保障还需要持续改进和提升。
面向未来,应进一步树立建立以高炉稳定顺行为核心的动态运行工程理念,继续加强精料、高风温、富氧喷煤、高炉长寿、提高顶压和全流程智能化研究,积极采用新技术和氢冶金等先进工艺,依托国内既有资源优势,开发新型炉料结构,不断优化炉料结构提质增效,大力开展绿色低碳炼铁技术的探索和研究。
1高炉冶炼炼铁技术高炉设备是冶炼设备之一,是保证炼铁实现的重要关键,高炉的上部结构装置了材料入口、煤气出风口,在高炉下部设置了排气口和出铁口。
高炉生产的时候,将原材料放在高炉进料口,在高温作用下还原铁。
高炉冶炼主要是生产生铁,经过生产高温工艺处理煤气,能够为多种设备提供燃料,减少环境污染,在很大程度上提高资源能源的利用效率。
高炉冶炼是钢铁行业发展的主要方式,钢铁生产是国民经济生产内容的一部分,新时期我国正从“制造强国”方面转型,制造业发展关系到国民经济发展,因此钢铁生产效率、生产质量直接关系到我国的经济发展速度。
基于钢铁企业大数据平台建设的理论与研究
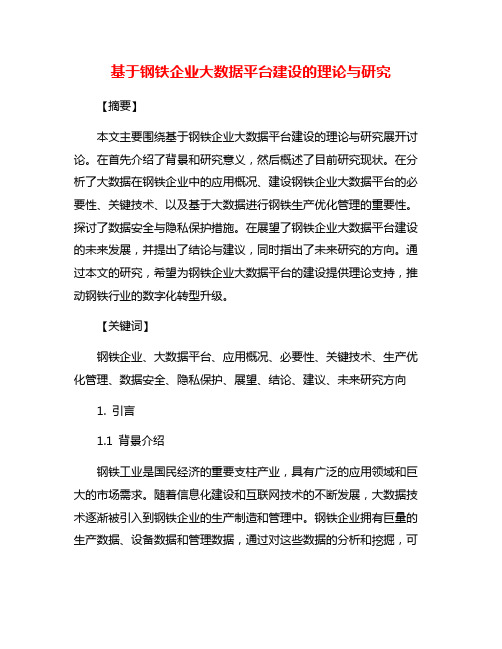
基于钢铁企业大数据平台建设的理论与研究【摘要】本文主要围绕基于钢铁企业大数据平台建设的理论与研究展开讨论。
在首先介绍了背景和研究意义,然后概述了目前研究现状。
在分析了大数据在钢铁企业中的应用概况、建设钢铁企业大数据平台的必要性、关键技术、以及基于大数据进行钢铁生产优化管理的重要性。
探讨了数据安全与隐私保护措施。
在展望了钢铁企业大数据平台建设的未来发展,并提出了结论与建议,同时指出了未来研究的方向。
通过本文的研究,希望为钢铁企业大数据平台的建设提供理论支持,推动钢铁行业的数字化转型升级。
【关键词】钢铁企业、大数据平台、应用概况、必要性、关键技术、生产优化管理、数据安全、隐私保护、展望、结论、建议、未来研究方向1. 引言1.1 背景介绍钢铁工业是国民经济的重要支柱产业,具有广泛的应用领域和巨大的市场需求。
随着信息化建设和互联网技术的不断发展,大数据技术逐渐被引入到钢铁企业的生产制造和管理中。
钢铁企业拥有巨量的生产数据、设备数据和管理数据,通过对这些数据的分析和挖掘,可以帮助企业实现生产过程优化,提高生产效率,降低成本,提升市场竞争力。
钢铁企业大数据平台的建设已经成为行业发展的趋势和需求。
通过搭建一个完善的大数据平台,钢铁企业可以实现数据的统一管理、快速查询和分析,为企业决策提供更准确、更及时的数据支持。
大数据平台还可以帮助钢铁企业实现数据共享,加强内部协同合作,提升企业整体运营效率。
随着信息时代的不断深化,钢铁企业大数据平台建设将会面临更多挑战和机遇。
加强对钢铁企业大数据平台建设理论和技术的研究,探索更有效的解决方案,助力钢铁企业实现可持续发展和转型升级,具有重要的意义和价值。
1.2 研究意义钢铁企业是我国重要的基础产业,其发展水平直接关系到国家经济发展的稳定和持续性。
随着信息技术的迅猛发展,大数据已成为企业信息化建设的重要支撑,钢铁企业亦不例外。
建设钢铁企业大数据平台具有重要的研究意义和现实价值。
钢铁行业中的大数据分析技术使用方法
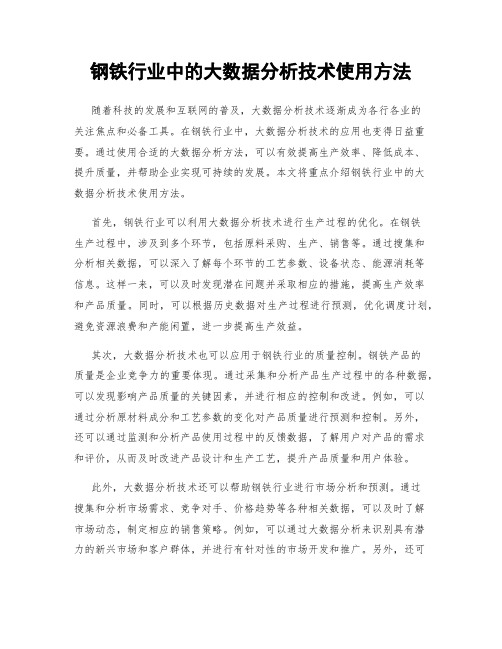
钢铁行业中的大数据分析技术使用方法随着科技的发展和互联网的普及,大数据分析技术逐渐成为各行各业的关注焦点和必备工具。
在钢铁行业中,大数据分析技术的应用也变得日益重要。
通过使用合适的大数据分析方法,可以有效提高生产效率、降低成本、提升质量,并帮助企业实现可持续的发展。
本文将重点介绍钢铁行业中的大数据分析技术使用方法。
首先,钢铁行业可以利用大数据分析技术进行生产过程的优化。
在钢铁生产过程中,涉及到多个环节,包括原料采购、生产、销售等。
通过搜集和分析相关数据,可以深入了解每个环节的工艺参数、设备状态、能源消耗等信息。
这样一来,可以及时发现潜在问题并采取相应的措施,提高生产效率和产品质量。
同时,可以根据历史数据对生产过程进行预测,优化调度计划,避免资源浪费和产能闲置,进一步提高生产效益。
其次,大数据分析技术也可以应用于钢铁行业的质量控制。
钢铁产品的质量是企业竞争力的重要体现。
通过采集和分析产品生产过程中的各种数据,可以发现影响产品质量的关键因素,并进行相应的控制和改进。
例如,可以通过分析原材料成分和工艺参数的变化对产品质量进行预测和控制。
另外,还可以通过监测和分析产品使用过程中的反馈数据,了解用户对产品的需求和评价,从而及时改进产品设计和生产工艺,提升产品质量和用户体验。
此外,大数据分析技术还可以帮助钢铁行业进行市场分析和预测。
通过搜集和分析市场需求、竞争对手、价格趋势等各种相关数据,可以及时了解市场动态,制定相应的销售策略。
例如,可以通过大数据分析来识别具有潜力的新兴市场和客户群体,并进行有针对性的市场开发和推广。
另外,还可以通过大数据分析来预测市场价格波动,规避市场风险,优化供应链管理,提高企业的竞争力和盈利能力。
钢铁行业的大数据分析技术应用不仅局限于上述几个方面,还可以涉及到能源管理、环境保护、人力资源等多个方面。
例如,在能源管理方面,可以通过大数据分析来监测和优化能源消耗,降低能耗成本,同时减少对环境的影响。
钢铁行业如何利用大数据进行质量控制

钢铁行业如何利用大数据进行质量控制钢铁行业一直以来都是现代工业发展的重要支柱,其产品广泛应用于各个领域。
然而,随着市场需求不断提高,传统的质量控制方式已经无法满足行业的要求。
为了提升产品质量和生产效率,钢铁行业开始利用大数据技术来进行质量控制。
本文将探讨钢铁行业如何利用大数据进行质量控制,以进一步推动行业的发展。
一、大数据在质量控制中的应用1. 数据采集与监测钢铁行业生产过程中会涉及大量的数据,包括原料的组成、生产线的运行参数、环境监测数据等。
通过建立自动化数据采集系统,可以实时获取并监测关键数据。
这些数据被传输到中央数据库,为后续的质量分析和控制提供基础。
2. 数据分析与建模利用大数据分析技术,钢铁行业可以对采集到的数据进行深入挖掘和分析。
通过建立数学模型和算法,可以预测钢铁生产过程中出现的质量问题,并实时调整参数,以提高产品质量。
此外,数据分析还可以用于发现隐藏在数据中的规律和趋势,为质量管理决策提供科学依据。
3. 故障诊断与预测钢铁生产线中常常会发生故障,导致质量问题和生产延误。
通过利用大数据技术,可以建立故障诊断模型,实时监测生产设备的运行状态,并预测潜在的故障。
一旦发现异常,系统会及时发出警报,并提供故障处理建议,帮助企业快速解决问题,提高生产效率和产品质量。
二、钢铁企业如何推动大数据应用1. 数据共享与合作钢铁企业在进行大数据应用时,需要与供应商、合作伙伴以及相关机构进行密切合作,共享数据资源。
可以建立数据共享平台,将各方的数据整合起来,提高数据的综合分析水平和质量控制能力。
2. 人才培养与技术支持钢铁企业在推动大数据应用时,需要培养专业的数据分析团队,并提供相关技术支持。
通过与高校和科研机构合作,可以培养出一支具备数据分析和技术研发能力的专业团队,为企业的质量控制工作提供有力支撑。
3. 先进技术的引入钢铁企业在推动大数据应用时,需要引进先进的技术和设备。
例如,利用云计算和物联网技术,可以实现数据的实时采集和处理,并提供可靠的数据存储和管理平台。
- 1、下载文档前请自行甄别文档内容的完整性,平台不提供额外的编辑、内容补充、找答案等附加服务。
- 2、"仅部分预览"的文档,不可在线预览部分如存在完整性等问题,可反馈申请退款(可完整预览的文档不适用该条件!)。
- 3、如文档侵犯您的权益,请联系客服反馈,我们会尽快为您处理(人工客服工作时间:9:00-18:30)。
以下资料来自《全国工商联冶金业商会统计指标解释(2007年12月)》一.技术经济指标分类钢铁工业技术经济指标分为工序指标和综合指标两大类。
二.工序能耗指标解释指标1. 烧结工序燃料消耗指标烧结矿燃料消耗指标是反映人造块矿燃料消耗水平的指标。
烧结矿使用的燃料有固体燃料(煤粉、焦粉)、非固体燃料两类。
固体燃料一般直接加入烧结矿的混合料中,基本上参与烧结(焙烧)的全过程;非固体燃料用于点火和焙烧(球团)。
各种燃料的消耗应分别统计。
烧结矿固体燃料耗用量(千克)1)烧结矿固体燃料消耗(千克/吨)=烧结矿产出量(吨)烧结矿煤粉耗用量(千克)a) 烧结矿煤粉消耗(千克/吨)=烧结矿产出量(吨)烧结矿焦粉耗用量(千克)b) 烧结矿焦粉消耗(千克)=烧结矿产出量(吨)2)烧结矿固体燃料折标煤消耗(千克标准煤/吨)=各种固体燃料折算成标煤后的耗用量(千克标准煤)烧结矿产出量(吨)计算说明:烧结矿的固体燃料计算中均以干基为准,其水分化验应由质检部门核准或认可,企业按实际情况可对实物消耗量分别计算毛耗(包括各种损耗及计量溢损)和净耗。
2.高炉(生铁)工序燃料燃料消耗指标燃料比是反映高炉冶炼1吨合格生铁所消耗的燃料量。
其计算公式为:燃料耗用总量(千克)燃料比(千克/吨)=生铁合格产出量(吨)计算说明:燃料耗用总量是指入炉的干焦、干焦丁、煤粉、重油等燃料总量。
严格来说,焦比属于能源消耗类指标,但由于焦炭在炼铁生产中的特殊作用,特将焦比指标单列。
由于高炉冶炼的铁种和使用的燃料不同,焦比(即焦耗)有以下几种计算公式:1)入炉焦比入炉焦比是反映高炉冶炼每1吨合格生铁所消耗的干焦炭量。
其计算公式为:干焦耗用量(千克)入炉焦比(千克/吨)=生铁合格产出量(吨)2)综合焦比综合焦比是指高炉冶炼每1吨合格生铁所消耗的综合干焦(将各种燃料均折合成干焦计算)量。
其计算公式为:综合干焦耗用量(千克)综合焦比(千克/吨)=生铁合格产出量(吨)3)喷煤比喷煤比是反映高炉冶炼1吨合格生铁所消耗的煤量。
其计算公式为:煤耗用量(千克)喷煤比(千克/吨)=生铁合格产出量(吨)4)人造块矿矿率人造块矿(烧结工序的产品)使用率,是指入炉人造块矿占入炉矿石总量的百分比。
它是反映高炉使用精料情况的指标。
其计算公式为:入炉人造块矿量(吨)人造块矿使用率(%)= 100%入炉矿实物总量(吨)计算说明:1) 人造块矿包括烧结矿、球团矿。
2) 入炉矿总量包括人造块矿和天然矿。
3.转炉炼钢炼钢,是利用不同来源的氧(如空气、氧气)来氧化炉料(主要是生铁—来自高炉)中所含杂质的复杂的金属提纯过程。
1.转炉钢金属料消耗是指每吨转炉钢所消耗的金属料量,其计算公式为:入炉金属料耗用量(千克)转炉钢金属料消耗(千克/吨)=转炉钢合格产出量(吨)计算说明:1) 转炉金属料消耗是指转炉炼钢过程所消耗的金属料量,包括转炉精炼耗用的金属料量;2) 金属料量=钢铁料量+其他原料含铁量+合金料量。
除有折合规定外,均按实物量计算。
①钢铁料量=生铁量+直接还原铁量+废钢铁量。
其中,生铁包括冷生铁、高炉铁水、还原铁;废钢铁包括各种废钢、废铁等。
凡分别管理、按类配用下列废钢铁的,在计算废钢铁消耗指标时,可按下列统一的折合标准折合计算:a.轻薄废钢,包括锈蚀的薄钢板以及相当于锈蚀薄板的其他轻薄废钢,按实物量×60%计算,其加工压块按实物量×65%计算;关于轻薄废钢,国家标准GB/T4223-1996中有明确规定;b.渣钢是指从炉渣中回收的带有渣子的钢,按实物量×70%计算;经过砸碎加工(基本上去掉杂质)的渣钢,按实物量×90%计算;c.优质钢丝(即过去所称“钢丝”)、钢丝绳、普通钢钢丝(即过去俗称“铁丝”)、铁屑以及钢锭扒皮车屑和机械加工的废钢屑(加工压块在内),按实物量×40%计算;d.钢坯切头切尾、汤道、中注管钢、桶底钢、冻包钢、重废钢等均按实物量计算。
②其他原料含铁量=铁矿石含铁量+铁鳞(包括转炉烟罩渣)含铁量。
a.铁矿石含铁量按铁矿石用量×矿石品位×80%计算;b.铁鳞含铁量按铁鳞用量×铁鳞品位×50%计算。
③合金料包括脱氧剂、发热剂及作为钢中成分加人的各种合金等。
在计算合金料消耗时,按下列统一的折合标准折合计算:a.作为脱氧剂、发热剂使用的粉状铁合金按50%折合计算;b.作为原料消耗的合金按实物量计算;c.计算硅铁、锰铁、锰硅合金的单项合金料消耗时,则要求按标准量计算、硅铁按含硅75%、锰铁按含锰6500、锰硅合金按锰+硅=82%换算成标准量。
换算时,要按不同成分的合金料进行加权平均计算出标准量。
3) 转炉金属料消耗(回炉钢水除外)应按每投一次料就算一次消耗。
生产过程中产生的废钢锭(坯)、注余冷料等一切废钢铁,应回收交库。
使用时,再办理领料手续。
就地使用时,必须办理领料手续,防止漏算消耗。
但回炉钢水允许不重复计算消耗。
注余钢水回炉应办理前炉交库、本炉领用的手续。
4) 凡使用冷料经二次熔化再进行热装炼钢的,其炼钢金属料消耗应从冷料算起,包括二次熔化的损耗。
5) 计算消耗的产品,只限于正式投产的产品。
试制阶段的新产品、科研产品,以及正式投产以前试验生产的产品,单独计算消耗指标。
6) 计算转炉钢的钢铁料、其他原料含铁、合金料消耗时,其计算公式按以上公式类推,并参照以上计算说明。
2.氧气消耗转炉炼钢工序氧气使用量(米3)转炉炼钢工序氧气能耗(米3/吨)=转炉钢合格产出量(吨)4.电炉炼钢电炉炼钢是利用电能作热源来进行冶炼的。
最常用的电炉有电弧炉和感应炉两种。
电弧炉炼钢占电炉钢产量的绝大部分。
1.电炉钢金属料消耗电炉钢金属料消耗是指每炼1吨电炉钢所消耗的金属料量。
其计算公式为:入炉金属料耗用量(千克)电炉钢金属料消耗(千克/吨)=电炉钢合格产出量(吨)计算说明:1) 特殊钢厂由于生产周期较长,有时又要冶炼原料钢。
因此,本指标的母项为电炉钢合格产出量。
电炉钢合格产出量包括用电炉冶炼的原料钢,如工艺纯铁、软钢、镍锭、脱氧剂等。
2) 电炉金属料消耗是指电炉炼钢全过程所耗用的金属料量,包括电炉精炼耗用的金属料量。
3) 金属料量=钢铁料量+其他原料含铁量+合金料量。
除有折合规定外,均按实物量计算。
①钢铁料量=生铁量+废钢铁量+直接还原铁量。
其中,生铁包括生铁块、高炉铁水;废钢铁包括各种废钢、废铁等;直接还原铁包括海绵铁(DRI)和热压块铁(HBD)。
凡分别管理、按类配用下列废钢铁的,在计算废钢铁消耗指标时,可按下列统一的折合标准折合计算:a.轻薄废钢,包括锈蚀的薄钢板以及相当于锈蚀薄板的其他轻薄废钢,按实物量×60%计算,其加工压块按实物量×65%计算;关于轻薄废钢,国家标准GB/T4223-1996中有明确规定,详见本章附表。
b.渣钢是指从炉渣中回收的带有渣子的钢,按实物量×70%计算;经过砸碎加工(基本上去掉杂质)的渣钢,按实物量×90%计算。
c.优质钢丝(即过去所称“钢丝”)、钢丝绳、普通钢钢丝(即过去俗称“铁丝”)、铁屑以及钢锭扒皮车屑和机械加工的废钢屑(加工压块在内),按实物量×40%计算。
d. 钢坯切头切尾、汤道、中注管钢、桶底钢、冻包钢、重废钢等均按实物量计算。
2.电极消耗电极耗用量(千克)电极消耗(千克/吨)=电炉钢合格产出量(吨)计算说明:电极消耗中应包括电极及接头,不包括炉外折断新电极及加工电极接头耗损。
对已经计算消耗的废电极利用不再计算;电极包括石墨电极和炭电极。
3.电力消耗电炉电力耗用量不包括炼渣炉、炉外精炼炉用电量,不包括炼钢所用的其他用电量,可扣除烘烤用电量。
其计算公式为:电炉电力耗用量(千瓦·时)电炉电力消耗(千瓦·时/吨)=电炉钢合格产出量(吨)5.钢加工生产统计指标炼钢工序生产的钢锭或连铸坯,不能直接作为其他工业生产的原材料或直接用于社会消费,因此必须对其作进一步的塑性加工或其他加工,塑性加工方法很多,有热压延加工法和冷压延加工法。
热压延加工法中的热轧法是最主要的生产方法,约有90%的钢是采用热轧法直接成材。
1.锭坯~材综合成材率锭坯~材综合成材率(投入产出法),是指产品从第一道加工工序投料(包括模铸锭和连铸坯)起直至最后一道加工工序结束止的全过程(包括各个环节生产经营周转损失)的成材率。
它反映了企业整个钢材生产过程原料的利用程度,适用于企业与企业之间、地区与地区艺间进行对比,同时也为省(市)及国家钢铁行业管理部门汇总综合成材率提供基础数据。
其计算公式为:钢加工最终钢材合格产出量(吨)锭坯、材综合成材率(%)= ×100%锭坯耗用量(吨)计算说明:1)除计算锭坯~材综合成材率外,还可计算锭坯~热压延加工钢材成材率(分大品种)。
2) 各企业生产钢材耗用原料的起点(钢锭、钢坯或钢材)和产品的止点不同,加工方法也不尽相同,为了反映各企业不同加工方法及最终钢材成材率,便于省(市)、国家逐级汇总综合成材率,各企业需要分别计算最终钢材综合成材率和分步成材率。
同时,在最终钢材综合成材率中,还应按钢材大品种分列分品种的锭坯~钢材成材率。
6.炼焦生产统计指标将各种经过洗选的炼焦煤按一定比例配合后,在炼焦炉内进行高温干馏,可以得到焦炭和荒煤气。
将荒煤气进行净化加工处理,可以得到多种煤化工产品和焦炉煤气。
1.炼焦耗洗精煤炼焦耗洗精煤是指工艺上每生产1吨焦炭(全焦干基)耗用的湿洗精煤数量(含计价水,但不包括库耗、途耗)。
其计算公式为:入炉洗精煤耗用量炼焦耗洗精煤(吨/吨)=全部焦炭合格产出量(干基)(吨)三.工序能耗1.烧结工序单位能耗烧结工序能耗中,固体燃耗约占80%,电力约占13%,点火燃耗约占6.5%,其它约为0.5%.所以说,降低固体燃耗是烧结节能工作的重点,还有提高烧结工序余热回收利用水平。
2013年上半年重点钢铁企业烧结固体燃耗为53.77kg/t,比上年升高0.05kg/t。
烧结工序单位能耗指标是反映烧结生产中能源消耗的综合指标。
其计算公式为:烧结工序净耗能量(千克标准煤)烧结工序单位能耗(千克标准煤/吨)=烧结矿产出量(吨)计算说明:1) 子项=工序耗用燃料及动力等能源总量一回收二次能源外供量一利用余热外供量一利用余能外供量。
2) 在计算人造块矿的工序单位能耗指标时,应把人造块矿生产中消耗的各种能源按规定的标准统一折算成标准煤总量。
它包括配料中用的焦粉、煤粉、点火和焙烧中用的燃油、煤气(包括为保持水分稳定所进行的烘干作业所耗的煤气)和生产中用的电力等一切动力消耗。
3) 各种能源消耗计量,均应由计量部门核准,并应有原始记录和计量磅单。
2.炼铁工序单位能耗2013年上半年全国重点钢铁企业炼铁工序能耗为399.96kgce/t, 焦比在工序能耗数据中约占70%,煤比约占20%,燃料比的变化对工序能耗的影响是起决定性的作用。