材料成形工艺第二章 液态金属成形过程及控制
液态金属成形过程及控制
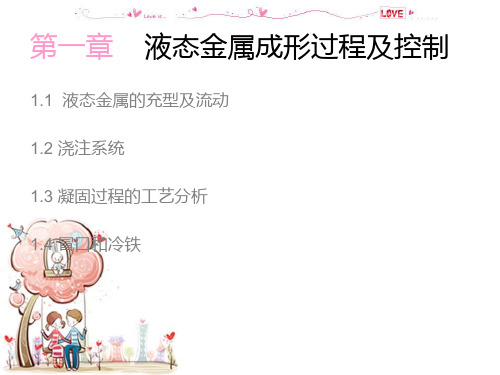
冒口。
冒口补缩原理
二、选择冒口位置的原则
1.冒口应就近设在铸件热节(hot spot)的上方或侧 旁; 2.冒口应尽量设在铸件最高、最厚的部位; 3.冒口不应设在铸件重要的、受力大的部位; 4.冒口不应选在应力集中处; 5.应尽量用一个冒口补缩几个热节或铸件; 6.冒口不应在加工面上。
金属液过滤器安放位置
泡沫陶瓷过滤器过滤机理
• • 1.“滤饼”机制 复杂的泡沫陶瓷结构,可以高效率 地机械挡渣,当金属液通过结构复 杂的泡沫陶瓷过滤器时,通过过滤 介质的机械分离作用,把大于过滤 器表面孔眼的夹杂物滤除,并使之 沉积在过滤器液态金属流入端,成 为过滤器的一个组成部分。随着夹 杂物在过滤器表面上堆积数量的增 多,逐渐形成了一层“滤饼”,使 金属液流道进一步变细,因而新增 的过滤介质表面可以滤除更为细小 的夹杂物。与此同时,介质内部也 有过滤作用,在贯穿于陶瓷体的众 多小孔中,有的呈现微小狭缝,有 的存在死角,这些变化不同的区域 都是截获夹杂物的可能位置。
第一章
液态金属成形过程及控制
1.1 液态金属的充型及流动 1.2 浇注系统 1.3 凝固过程的工艺分析 1.4 冒口和冷铁
1.1液态金属的充型及流动
• 概述:充型+凝固→铸造成形→质量 一、液态金属充型的水力学特征及在浇注系统中的流动 水力学特征: ①粘性流动←粘度→合金成分,温度,结晶 ②流动的不稳定性 ③散体材料的“多孔管流动”
铸件
1.位置(4)-阶梯式
a)多直浇道式 b)用塞球法控制式 c)控制各 组元比例式 d)带缓冲直浇道 e)带反直浇道式
2.按各单元断面积的比例
• 收缩式:A直﹥ A横﹥ A内 • 扩张式: A直﹤ A横﹤ A内 • 半扩张式: A直﹤ A横﹥ A内
第2章金属液态成形
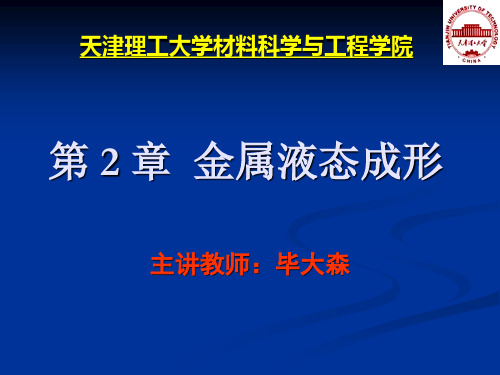
第2章 金属液态成形
固态金属按原子聚集形态分为晶体与非晶 体。
晶体——凡是原子在空间呈规则的周期性 重复排列的物质称为晶体。
单晶体——在晶体中所有原子排列位向相 同者称为单晶体
第2章 金属液态成形
(1)金属从固态熔化为液态时的变化 金属熔化时的体积增大量在3%~7%的
范围内。而金属从绝对零度到熔点温度的 固态体积膨胀量几乎都是约7%。
固态金属的结构可以看作由理想的晶体结 构加上缺陷(空穴、间隙原子、位错、晶 界等)组成。随着温度的升高,固态金属 中缺陷的数量增加,活动性增大。
第2章 金属液态成形
在力F的作用下,在X轴方向每一层原子 都相对于下一层原子产生相对运动,其平 均速度 v qF。
第2章 金属液态成形
v 值也可以写成微分形式:
v vx q F
y
作用在流体单位面积上的力用Pxy表示, 则:
F
Pxy 2
或者 F Pxy 2
第2章 金属液态成形
由上两式可得:
第2章 金属液态成形
如图是由X射线衍射结果整理而得的原子 密度分布曲线。
横坐标r为观测点至某一任意选定的原子 (参考中心)的距离,对于三维空间,它 相当于以所选原子为球心的一系列球体的 半径。
纵坐标表示当半径增减一个单位长度时, 球体(球壳)内原子个数的变化值,其中 (r)称为密度函数。
第2章 金属液态成形
第2章 金属液态成形
液态金属的粘度在温度不太高时,随温度 的升高粘度下降。
难熔化合物的粘度较高,而低熔点的共晶 成分合金的粘度低。
材料成形工艺液态金属铸造成形工艺2

第一部分 液态金属铸造成形工艺
第一部分 液态金属铸造成形工艺
第一章 液态金属铸造成形工艺基础
1
液态金属铸造成形工艺
概述
第一章 液态金属铸造成形工艺基础
☺ 铸造:使熔融的金属液流入并凝固在预先制备的铸型中, 获得特定形状和性能的毛坯或零件(铸件)的方法或技术。
铸造的基本工艺要素是:熔融金属液 预先制备的铸型
解决方案: 利用动量矩守恒原理抑 制漩涡。
具体措施:
使用池形浇口杯;
使用浇口塞提高液面。
28
第一章 液态金属铸造成形工艺基础
二、基本工艺过程及其控制
1、充型过程及其控制
1.2、液态金属在浇注系统中的流动情况
3). 金属液在直浇道中的流动情况
流动特点:
金属液在重力作用下沿 直浇道流动;
金属液在流动过程中因 势能降低有液流加速的 现象;
流体在运动状态下呈现出一种 抗拒运动的特性,称为粘性。
液态金属是有粘性的流体,其 粘度与其成分及温度相关。
在流动过程中液态金属的粘度随液态金属温度的降低而 不断增大,当液态金属中出现部分固相时,液体的粘度 急剧增加,其流速和流态也会发生显著改变。
11
第一章 液态金属铸造成形工艺基础
二、基本工艺过程及其控制
可能导致金属液的离壁
流动。
29
第一章 液态金属铸造成形工艺基础
二、基本工艺过程及其控制
1、充型过程及其控制
3). 金属液在直浇道中的流动情况
A. 直浇道的作用
将来自浇口杯的液流引入横浇道、内浇道或直接引入 型腔。
通过调整直浇道高度,可获得足够的水力学压头,保 证金属液在规定的时间内以适当的速度充满型腔。
液态金属加工中的凝固控制

液态金属加工中的凝固控制是一个重要环节,因为它对产品的质量和性能有着显著的影响。
通过控制凝固过程,可以确保金属材料得到充分凝固,形成良好的组织和性能。
下面将从三个方面详细介绍液态金属加工中的凝固控制。
一、温度控制在液态金属加工中,温度是影响凝固过程的关键因素之一。
为了确保金属材料充分凝固,需要对加工过程中的温度进行精确控制。
通常,通过使用水冷装置或热管理系统来调节和控制温度。
在加工过程中,温度的波动可能会对金属材料的组织和性能产生不利影响。
因此,需要定期检查冷却系统的运行状况,确保其正常工作。
二、速度控制液态金属加工中的速度控制也是至关重要的。
在金属凝固过程中,过快的加工速度可能会导致金属材料变形或产生裂纹。
因此,需要根据金属材料的性质和加工设备的性能,合理设置加工速度。
同时,在加工过程中还需要密切关注金属材料的流动情况,避免过热或过冷现象的发生。
三、冷却速率控制冷却速率是影响金属材料凝固速度和组织结构的重要因素之一。
通过控制冷却速率,可以调整金属材料的凝固过程,使其达到最佳的性能和组织。
在液态金属加工中,通常使用水冷或空气冷却等方式来控制冷却速率。
通过调节冷却水的流量或空气的压力,可以实现对冷却速率的有效控制。
此外,还可以通过调整模具的结构和形状来改变金属材料的凝固过程,以达到最佳的凝固效果。
总之,液态金属加工中的凝固控制是一个综合性的过程,需要从温度、速度和冷却速率等多个方面进行考虑和控制。
通过精确控制这些因素,可以确保金属材料得到充分凝固,形成良好的组织和性能,从而提高产品的质量和性能。
这需要操作人员具备丰富的经验和专业知识,以及对设备和材料的深入了解。
02 金属材料液态成形工艺技术
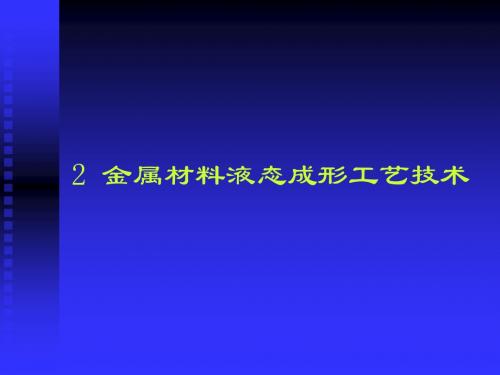
2 铸造工艺特点 适应性广:适应铸铁,碳钢,有色金属等材料; 适应性广:适应铸铁 ,碳钢, 有色金属等材料; 铸件大小, 形状和重量几乎不受限制; 铸件大小 , 形状和重量几乎不受限制 ; 壁厚 mm到 1mm到1m 。 可成形复杂零件: 适合形状复杂, 可成形复杂零件 : 适合形状复杂 , 尤其是有 复杂内腔的毛坯或零件。 复杂内腔的毛坯或零件。 成本低 缺点: 组织缺陷, 力学性能低, 质量不稳定, 缺点 : 组织缺陷 , 力学性能低 , 质量不稳定 , 工作环境较差。 因此, 铸件多数做为毛坯用。 工作环境较差 。 因此 , 铸件多数做为毛坯用 。
熔模铸造的特点和应用
( 1 ) 铸件精度高 , 表面质量好 , 属少 , 无切削工 铸件精度高, 表面质量好, 属少, 尺寸精度IT11-14, 表面粗糙度Ra12. 艺 。 尺寸精度 IT11-14, 表面粗糙度 Ra12.5-1.6µm 。 可铸造形状复杂铸件, 最小壁厚可达0 (2) 可铸造形状复杂铸件 , 最小壁厚可达 0 . 3 mm 最小铸孔直径0 mm。可一次铸出组合体。 ,最小铸孔直径0.5mm。可一次铸出组合体。 铸造合金种类不受限制, ( 3 ) 铸造合金种类不受限制 , 尤其适合高熔点和 难切削合金。 难切削合金。 生产批量不受限制,可单件或成批生产。 (4)生产批量不受限制,可单件或成批生产。 ( 5 ) 工序繁杂 , 生产周期长 , 原辅材料费用高 , 工序繁杂, 生产周期长, 原辅材料费用高, 生产成本较高,铸件限于25kg。 生产成本较高,铸件限于25kg。
木模
(5)填砂浇注 (6)脱壳、清理。 脱壳、清理。
熔 模 铸 造
熔模铸造
熔模铸件的结构工艺性
铸 孔不能太小和太深 , 一般铸孔应大于 孔不能太小和太深, mm。 2mm。 逐渐壁厚不可太薄 一般2 mm。 壁厚不可太薄, 逐渐壁厚不可太薄,一般2-8mm。 铸件壁厚尽量均匀 壁厚尽量均匀。 铸件壁厚尽量均匀。
金属液态成形教学课件.

三种凝固方式示意图
铸件质量与其凝固方式密切相关。一般,逐层凝 固时,合金的充型能力强,便于防止缩孔和缩松;糊 状凝固,则难以获得结晶紧密的铸件。
影响凝固方式的因素
• 合金的结晶温度范围 合金的结晶温度范围愈小, 凝固区愈窄,愈倾向于逐层凝 固;反之,则倾向于逐层凝固。 铸件的温度梯度 当合金成分已确定,凝固 区的宽窄,取决于其内外层的 温度梯度。铸件的温度梯度愈 大,凝固区愈窄,愈倾向于逐 层凝固。铸件的温度梯度愈小 , 凝固区愈宽,愈倾向于糊 状凝固。
合金的总收缩为上述三种收缩的总和。其中 液态收缩和凝固收缩形成铸件的缩孔和缩松,固 态收缩使铸件产生内应力、变形和裂纹。
合金的收缩量可用体收缩率和线收缩率来表示。 体收缩率:单位体积的变化量。 线收缩率:单位长度的变化量。
• 液态收缩时,合金从浇注温 度冷却到液相线温度。(体 收缩) • 凝固收缩时,合金从液相线 温度冷却到固相线温度。 (体收缩) • 固态收缩时,合金从固相线 温度冷却到室温。 (线收缩)
• 同时凝固原则适用于收缩小或壁厚均匀的薄壁铸件,采用同时凝 固原则,铸件热应力小,但在铸件中心往往产生缩松。
• 对结构复杂的铸件,既要避免产生缩孔和缩松,又要减小热应力, 防止变形和裂纹,这两种凝固原则可同时采用。
• 合理应用冒口、冷铁等工艺措施 冒口一般设置在铸件厚 壁和热节部位,尺寸应保证 比补缩部位晚凝固,并有足 够的金属液供给,形状多为 园柱形。 冷铁通常是用铸铁、钢 和铜等金属材料制成的激冷 物,与冒口配合,可扩大冒 口的有效补缩距离。
防止措施:使芯撑、冷铁表面保持干燥,无油无 锈。
1.合金的流动性
(1)慨念: 指液态金属的流 动能力,在铸造过程中即表现 为液态金属充填铸型的能力。 合金流动性的大小,通常以螺 旋形试样的长度来衡量。
金属液态成形工艺原理讲稿
金属液态成形工艺原理讲稿一、引言金属液态成形工艺是一种重要的金属加工方法,它利用金属在液态状态下的可塑性,通过施加外力,将金属材料压制成所需形状的工艺过程。
金属液态成形工艺广泛应用于航空航天、汽车制造、船舶制造等众多领域,具有高效、精确、灵活的特点。
本文将介绍金属液态成形工艺的原理和应用。
二、金属液态成形工艺的原理金属液态成形工艺主要依靠金属在液态状态下的可塑性来实现材料的变形。
在液态状态下,金属具有较高的流动性和可塑性,可以通过施加外力使金属流动,从而制造出复杂形状的金属构件。
金属液态成形工艺的主要原理包括以下几点: 1. 温度控制:金属液态成形工艺需要将金属升温到液态状态,通常通过加热设备控制金属的温度。
2. 施加外力:在金属材料处于液态状态时,需要施加适当的外力,如压力、压力冲击等,以实现对金属的形状变化和压制成型。
3. 液态流动:金属在液态状态下具有较高的流动性,可以通过控制液态金属的流动轨迹和速度,实现对金属的精确塑性变形。
4. 液态金属的熔化和凝固特性:金属在液态和固态之间的相变过程对金属液态成形工艺具有重要影响。
不同金属具有不同的熔化温度和凝固温度,需要根据具体金属材料选择合适的工艺参数。
三、金属液态成形工艺的应用金属液态成形工艺在许多领域都有广泛的应用,具有以下几个优点: 1. 高效生产:金属液态成形工艺可以实现多工位、多工序的同时进行,提高了生产效率。
2. 精确成形:金属液态成形工艺可以制造出复杂形状的金属构件,加工精度高,尺寸和形状可控性强。
3. 节约材料:金属液态成形工艺可以使金属材料得到较好的填充,减少了材料的浪费。
4. 节约能源:金属液态成形工艺可以在短时间内实现金属材料的加热和冷却,节约了能源消耗。
金属液态成形工艺在以下领域有广泛的应用: 1. 航空航天:金属液态成形工艺可以制造出高强度和轻质的航空航天零部件,提高了飞行器的性能和燃油效率。
2. 汽车制造:金属液态成形工艺可以制造出汽车发动机缸体、曲轴等零部件,提高了汽车的动力性能和燃油效率。
材料成形工艺原理第二章液态金属的结构和性质
在碰撞时,有的原子将一部分能量传给别 的原子,而本身的能量降低了。
结果是每时每刻都有一些原子的能量超过 原子的平均能量,有些原子的能量则远小于 平均能量。这种能量的不均匀性称为“能量 起伏”。
由于能量起伏,一些原子则可能越过势垒跑到原 子之间的间隙中或金属表面,而失去大量能量,在 新的位置上作微小振动(图1-3)。一旦有机会获得 能量,又可以跑到新的位置上。
接近熔点时,晶界上的原子则可能脱离原晶粒表 面,向邻近晶粒跳跃,晶粒逐渐失去固定形状。
特征:
将金属加热至熔点时,金属体积突然膨胀3~5%, 等于固态金属从热力学温度零度加热到熔点前的总 膨胀量。
金属的其它性质如电阻、粘性等发生突变,吸收 大量热能——熔化潜热,而金属的温度不升高。
这些突变现象是不能仅仅用离位原子和空穴数目 的增加加以解释的。因为空穴数目的增加不可能是 突变的。
(5) 如前所述,由于势能曲线是极不对称的,向左振动 时,动能很快就全部转化为势能,原子所能达到的最大 偏离位置较小。
向右振动,则需较大的偏离,动能才全部转化为势 能,振幅的中心位置则由Ro→R1 …。但是,这种膨胀 只改变原子的间距,并不改变原子排列的相对位置。
(6) 晶体中每个原子的振动能量不是均等的, 振动方向杂乱无章。
或
当R=R0 时,F (R0)=0,即
对应于能量的极小值,状态 稳定。原子之间倾向于保持一定 的间距,这就是在一定条件下, 金属中的原子具有一定排列的原 因。
当R=R1时,吸引力最大,即
对应能量曲线的拐点。 当R>R1时,吸引力开始减小, 势能向最大值转折。
二、金属的加热膨胀
晶体中原子并不是固定不动的,只要温度高于热力学 温度0K,每个原子皆在平衡位置附近振动,即所谓热振 动。温度升高时振动能量增加,振动频率和振幅加大。
液态成型第二章第一节,第二节分析
Pb 20 40 60 80 Sb
a)在恒温下凝固 b)在一定温度范围内凝固
合金的物理性能对流动性的影响
合金的热导率(λ),比热容(C)和密度(ρ): C、ρ较大, λ较小的合金,因其本身含有较多的热量,而热
量的散失又较慢,因此,流动性好;反之,流动性较差。
合金的表面张力: 在相同条件下,一般合金表面张力大的,流动性较差;反之,
但是,随着浇注温度的提高,合金的吸气、氧化现象严重,总 收缩量增加,反而易产生气孔、缩孔等缺陷,而且铸件结晶组 织粗大。
原则:
在保证足够流动性的前提下,应尽可能降低浇注温度。
2) 充型压头
压头(压力头): 指直接施加在液态金属表面的静压力,用液柱高度值表示
液态合金在流动方向上所受的压力越大,充型能力越好。
第2章 液态金属成型
2.1 概述 2.2 铸造成型基本理论 2.3 砂型铸造 2.4 特种铸造 2.5 现代铸造方法的发展
2.1 概述
2.1.1 液态成形的基本概念 2.1.2 铸造生产的特点 2.1.3 铸造方法
2.1.1 液态成形的基本概念
液态成形(铸造):
是熔炼金属,制造铸型,并 将熔融金属浇入到铸型的 型腔中,凝固后获得毛坯 或铸件的一种工艺方法。
合金获得优质铸件的能力,即在铸造生产中表现 出来的工艺性能。
• 合金铸造Biblioteka 能:包括液态合金的充型能力、收缩性、偏析倾 向性、氧化性和吸气性等。
2.2.1 合金的充型能力
1 基本概念 2 影响充型能力的因素及工艺措施
1 基本概念
合金的充型能力:
液态合金充满铸型型腔,获得形状完整、 轮廓清晰的健全铸件的能力。
2.1.2 铸造生产的特点
金属的液态成形
金属的液态成形
金属的液态成形是现代制造业中一种重要的工艺。
它利用金属的熔融
中性,通过注射、挤压、铸造等操作,将金属材料精确地成形。
以下
是液态成形的步骤。
第一步,准备金属材料。
在液态成形过程中,首先需要准备好金属材料。
不同的成形工艺需要不同的金属材料。
一般情况下,常见的液态
成形材料有铝、铜、镁、钢等。
第二步,加热金属材料。
将金属材料加热到其熔点以上,使其成为液态,从而为后续加工过程做好准备。
这一步中需要注意金属材料的熔
点和其他性质,避免出现烧结、氧化等现象。
第三步,选择成形工艺。
根据金属材料的特性,以及生产需求,选择
不同的成形工艺。
一般来说,液态成形工艺分为注射、挤压、铸造等。
第四步,进行液态成形操作。
在进行液态成形操作时,需要注意操作
人员的专业技能和经验水平,尤其是对于一些高难度和高风险的操作。
操作中需要注意安全,配合机械和设备运转,精确控制工艺参数和加
工速度。
第五步,进行收尾工作。
当液态成形结束后,需要对设备和金属材料
进行清洗、维修和保养等收尾工作,确保设备和材料的安全可靠,以
及生产线的正常运转。
总体来说,液态成形在现代制造业中扮演着重要的角色,是现代制造
业的重要组成部分。
液态成形工艺的精细化、自动化和智能化也正在不断提高,使其在新时代更加高效、安全、环保和持续发展。
- 1、下载文档前请自行甄别文档内容的完整性,平台不提供额外的编辑、内容补充、找答案等附加服务。
- 2、"仅部分预览"的文档,不可在线预览部分如存在完整性等问题,可反馈申请退款(可完整预览的文档不适用该条件!)。
- 3、如文档侵犯您的权益,请联系客服反馈,我们会尽快为您处理(人工客服工作时间:9:00-18:30)。
第二章 液态金属成形过程及控制
第一节 第二节 第三节 第四节 第五节
液态金属充型过程的水力学特性及流动情况 浇注系统的设计 液态金属凝固收缩过程的工艺分析 冒口设计 冷铁设计
第一节 液态金属充型过程的水力学特性及流动情况
一、液态金属充型流动过程的水力学特性 二、液态金属在浇注系统中的流动情况 三、金属熔体过滤器及浇注系统
1.液态金属在浇口杯中的流动情况
图2-3 浇口杯内液面深度和浇注高度的影响 a)合理 b)、c)不合理
1.液态金属在浇口杯中的流动情况
为了减轻和消除水平旋涡,对于重要的中、大型铸件,常用 带浇口塞的浇口杯。先用浇口塞堵住浇口杯的流出口,然后进 行浇注,当浇口杯被充填到一定高度且熔渣已浮起时,再拔起 浇口塞,使合金液开始流入直浇道。浇口塞可用耐火材料或铸 铁材料制成,其结构应能保证拔起浇口塞时不产生涡流。有时 也用一金属薄片盖住浇口杯的流出口,当浇口杯被充填到一定 的高度时,金属薄片受热熔化,浇口杯的流出口就被打开,如 图2-4所示。
1.液态金属在浇口杯中的流动在浇口杯中的流动情况
浇口杯内出现水平旋涡会带入熔渣和气体,因而应注意防 止。当金属液从各个方向流入直浇道时,各向流量不均衡,某 一流股的流向偏离直浇道中心,就会形成水平涡流。根据水力 学原理,水平涡流越靠近中心部位压力越低,液面越低,这样 浮在液面上的熔渣会沿着弯曲的液面,一边旋转,一边和空气 一同进入直浇道,就有可能形成氧化夹渣等铸造缺陷。
1.液态金属在浇口杯中的流动情况
图2-4 有拔塞、浮塞或铁隔片的浇口杯 a)拔塞式 b)浮塞式 c)铁隔片式
2.液态金属在直浇道中的流动情况
图2-5 砂型中合金液流的充满条件 a)合金液流内任一截面上各点的压力p b)合金液流内任一截面上各点的压力p
3.液态金属在横浇道中的流动情况
(1)横浇道的稳流作用 液流从直浇道落下时,速度大,不平稳, 而经过浇口窝进入横浇道后,液流转向并趋于平稳。 (2)横浇道的流量分配作用 液流充满横浇道的同时,即由横浇 道分配给各个内浇道。 (3)横浇道的挡渣作用 横浇道是浇注系统的主要挡渣单元,其 挡渣作用与熔渣特性、横浇道本身结构、各浇道的相互配置关 系有关。 (4)横浇道的结构形状 横浇道的断面形状,可有圆形、半圆形、 梯形等多种形式。
(1)横浇道的稳流作用
液流从直浇道落下时,速度大,不平稳,而经过浇口窝进入横 浇道后,液流转向并趋于平稳。横浇道是直浇道与内浇道之间 的中间浇道,液体金属在横浇道中的流动情况与这三个浇道的 断面积之比有较密切的关系。当直浇道断面积大于横浇道断面 积,而横浇道断面积又大于内浇道断面积,即收缩式浇注系统 时,从直浇道下落的液流可立即把横浇道充满;相反,对于扩 张式或半扩张式浇注系统,横浇道并不立即被充满,而是随着 型腔中合金液面的升高而逐渐地被充满。
(2)横浇道的流量分配作用
液流充满横浇道的同时,即由横浇道分配给各个内浇道。同一 横浇道上有多个等断面的内浇道时,各内浇道的流量不等。在 一般条件下,远离直浇道的流量大,接近直浇道的流量小。各 内浇道的流量主要取决于合金液柱的高度、横浇道的长度、内 浇道在横浇道上的位置以及各浇道断面积之比。当合金液柱高、 横浇道不十分长时,从直浇道流入横浇道的合金液大部分流入 距直浇道较远的内浇道。如果直浇道高度不大、横浇道很长, 则大部分液流将流入处于中间位置或靠近直浇道的内浇道。这 种流量不均匀现象同横浇道与内浇道断面积之比有关。一般情 况下,浇道截面扩张程度越大,则流量不均匀现象越明显。
一、液态金属充型流动过程的水力学特性
(1)粘性流体流动 液态金属是有粘性的流体,其粘度的大小与 它的成分有关,在流动过程中又随温度的降低而增大。 (2)不稳定流动 在充型过程中液态金属温度不断降低,而铸型 温度不断增高,两者之间的热交换呈不稳定状态。 (3)多孔管中流动 由于砂型具有一定的孔隙,可以把砂型中的 浇注系统和型腔看做是多孔的管道和容器。 (4)湍流流动 生产实践中的测试和计算证明,液态金属在浇注 系统中流动时,其雷诺数Re大于临界雷诺数Re临,属于湍流流 动。
1.液态金属在浇口杯中的流动情况
浇口杯的作用是:承接来自浇包的金属液,防止金属液飞溅和 溢出,便于浇注;减轻液流对型腔的冲击;分离熔渣和气泡, 并阻止其进入型腔;增加充型压力头。浇口杯按结构形状可分 为漏斗形和盆形两大类。漏斗形浇口杯结构简单,挡渣作用差, 由于金属液易产生绕垂直轴旋转的涡流,易于卷入气体和熔渣, 因此这种浇口杯仅适用于对挡渣要求不高的砂型铸造及金属型 铸造的小型铸件。盆形浇口杯效果较好,底部设置凸缘有利于 浇注操作,使金属液的浇注速度达到适宜的大小后再流入直浇 道。这样浇口杯内液体深度大,可阻止垂直轴旋转的水平旋涡 的形成,从而有利于分离熔渣和气泡,如图2-2所示。
二、液态金属在浇注系统中的流动情况
1.液态金属在浇口杯中的流动情况 2.液态金属在直浇道中的流动情况 3.液态金属在横浇道中的流动情况 4.液态金属在内浇道中的流动情况
二、液态金属在浇注系统中的流动情况
图2-1 铸铁件浇注系统的典型结构 1—浇口杯 2—直浇道 3—直浇道窝 4—横浇道 5—末端延长段 6—内浇道
水力模拟试验表明,影响浇口杯内水平旋涡的主要因素是 浇口杯内液面的深度,其次是浇注高度、浇注方向及浇口杯的 结构等。浇口杯内液面深度和浇注高度的影响如图2-3所示。液 面深度大时不易出现水平旋涡(见图2-3a),液面浅时易出现水平 旋涡(见图2-3b)。浇包嘴距浇口杯越高,水平旋涡越易于产生 (见图2-3c)。总之,液面浅和浇注高度大时,偏离直浇道中心的 水平流速较高,因而易出现水平旋涡。
(3)横浇道的挡渣作用
图2-6 横浇道挡渣原理图
a)
b)
(3)横浇道的挡渣作用
在横浇道中,渣的上浮速度和横浇道挡渣作用的主要因素有: 1)杂质与合金液的密度差越大,熔渣越易上浮除去。 2)渣团半径R越大,熔渣上浮速度越大,越易除去。 3)合金液在横浇道中的流动速度v横越大,液流在横浇道中的湍 流程度越大,杂质上浮所遇到的干扰越大。当v横达到一定程 度时,杂质就浮不上来而始终悬浮在液流中,此时的v横临界 速度称为悬浮速度。 4)合金液的粘度越大,则渣团上浮越慢,越难除去夹杂。