粒度是磨料微粉最重要的技术指标之一
磨料粒度文档

磨料粒度简介磨料粒度是指磨料颗粒的大小和均匀程度,是磨料的重要物理特性之一。
磨料粒度对磨粒的磨削性能、表面质量和加工效率具有显著影响。
磨料粒度的评估指标主要包括磨料颗粒大小和颗粒分布均匀性。
本文将详细介绍磨料粒度的定义、测试方法以及对磨削性能和加工效率的影响。
磨料粒度的定义磨料粒度是指磨料颗粒的尺寸大小。
常见的磨料粒度指标有粒径和粒度分布。
粒径粒径是磨料颗粒的平均直径或尺寸。
常用的粒径单位有微米(μm)和目数(Mesh)。
微米是国际通用的长度单位,1微米等于千分之一毫米,常用来表示磨料粒径的绝对大小。
目数是用来表示筛网的开孔数的单位,表示每英寸线交叉点的数量。
根据不同国家和地区的标准,磨料的粒径与目数之间存在一定的对应关系。
粒度分布粒度分布是指磨料颗粒在不同粒径范围内的分布情况。
常见的粒度分布曲线有累积曲线和归一化曲线。
累积曲线表示磨料中颗粒尺寸小于等于某一粒径的百分比。
归一化曲线表示磨料中颗粒尺寸在某一范围内的百分比。
磨料粒度的测试方法磨料粒度的测试方法通常包括筛分法、显微镜法和激光粒度分析法。
筛分法筛分法是最常用的磨料粒度测试方法之一,通过将磨料样品放在不同孔径的筛网上进行振动筛分,根据筛网上通过孔的磨料颗粒数量和质量来确定磨料的粒径分布情况。
显微镜法显微镜法是一种直接观察和测量磨料颗粒尺寸的方法,需要使用显微镜放大观察磨料颗粒,然后通过测量显微镜视野中磨料颗粒的尺寸来确定磨料的粒径。
激光粒度分析法激光粒度分析法是使用激光散射原理来测量磨料粒子的尺寸分布的方法。
通过激光束照射样品,然后测量散射光的强度和角度,从而计算出磨料颗粒的尺寸分布。
磨料粒度对磨削性能的影响磨料粒度对磨削性能具有显著的影响,主要体现在以下几个方面:磨削质量磨料粒度对磨削表面的质量和光洁度有很大影响。
当磨料粒度过大时,磨粒切削能力较低,磨削表面粗糙度大,表面质量较差。
当磨料粒度过小时,磨粒的密度增大,磨削表面的粗糙度也会增加。
磨料的粒度

磨料的粒度磨料的粒度是指磨料颗粒的粗细程度,磨料的粒度规格用粒度号来表示。
*粒度号用目或粒度表示,是1英寸*1英寸的面积内有多少个颗粒数(是指磨料颗粒的大小相当于1平方英寸的多少分之一)。
例:1000,表示砂粒大小是25.4微米。
磨料的国家标准把粒度规格分为两类:一类是用于固结磨具、研磨、抛光的磨料粒度规格,其粒度号以"F"打头,称为"F粒度号磨料";另一类是用于涂附磨料的磨粒粒度规格,其粒度号以"P"打头,称为"P粒度号磨料".(1)F粒度号规格普通磨料粒度按颗粒尺寸大小,分为39个粒度号,其筛比为1.1892,即粗磨粒F4、F5、F6、F7、F8、F10、F12、F14、F16、F20、F22、F24、F30、F36、F40、F46、F54、F60、F70、F80、F90、F100、F120、F150、F180、F220、微粉F230、F240、F280、F320、F360、F400、F500、F600、F800、F1000、F1200、F1500、F2000.根据磨料生产工艺,磨料粒度在F4~F220部分的称为"粗磨粒"、其磨粒尺寸在63µm以上,多用筛分法生产;磨料粒度在F230~F2000范围内,磨粒尺寸小于63µm的称为"微粉",多用于水选法生产。
F4~F220粗磨粒磨料粒度组成、F230~F2000微粉磨料粒度组成(光电沉降粒度)及F230~F2000微粉磨料粒度组成参见GB-T 2481-2009标准。
(2)P粒度号规格在涂附磨具中使用P粒度号磨料(P为popular的第一个字母)。
国标规定磨料有28个粒度号,即粗磨料P12、P16、P20、P24、P36、P40、P50、P60、P80、P100、P120、P150、P180、P220、细磨料P240、P280、P320、P360、P400、P500、P600、P800、P1000、P1200、P1500、P2000、P2500.P12~P220磨料较粗,其筛比为1.892.P240~P2500磨料为粒度较系及分为磨料,所用筛分比为1.120→1.589→1.196.P12~P220磨料粒度组成与P240~P250磨料粒度组成参见GB-T 9258-2000标准。
碳黑
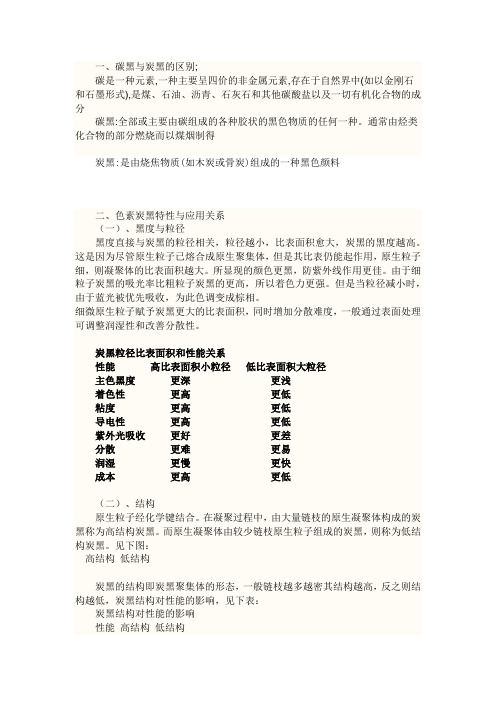
一、碳黑与炭黑的区别;碳是一种元素,一种主要呈四价的非金属元素,存在于自然界中(如以金刚石和石墨形式),是煤、石油、沥青、石灰石和其他碳酸盐以及一切有机化合物的成分碳黑:全部或主要由碳组成的各种胶状的黑色物质的任何一种。
通常由烃类化合物的部分燃烧而以煤烟制得炭黑:是由烧焦物质(如木炭或骨炭)组成的一种黑色颜料二、色素炭黑特性与应用关系·(一)、黑度与粒径黑度直接与炭黑的粒径相关,粒径越小,比表面积愈大,炭黑的黑度越高。
这是因为尽管原生粒子已熔合成原生聚集体,但是其比表仍能起作用,原生粒子细,则凝聚体的比表面积越大。
所显现的颜色更黑,防紫外线作用更佳。
由于细粒子炭黑的吸光率比粗粒子炭黑的更高,所以着色力更强。
但是当粒径减小时,由于蓝光被优先吸收,为此色调变成棕相。
细微原生粒子赋予炭黑更大的比表面积,同时增加分散难度,一般通过表面处理可调整润湿性和改善分散性。
炭黑粒径比表面积和性能关系性能高比表面积小粒径低比表面积大粒径主色黑度更深更浅着色性更高更低粘度更高更低导电性更高更低紫外光吸收更好更差分散更难更易润湿更慢更快成本更高更低(二)、结构原生粒子经化学键结合。
在凝聚过程中,由大量链枝的原生凝聚体构成的炭黑称为高结构炭黑。
而原生凝聚体由较少链枝原生粒子组成的炭黑,则称为低结构炭黑。
见下图:高结构低结构炭黑的结构即炭黑聚集体的形态,一般链枝越多越密其结构越高,反之则结构越低,炭黑结构对性能的影响,见下表:炭黑结构对性能的影响性能高结构低结构分散更易更难导电性更高更低润湿更慢更快粘度更高更低主色黑度更低更高填充量更低更高光泽更低更高着色力更低更高(三)、表面化学性炭黑的生产方法不同其表面化学性能各异。
炭黑表面具有不同的含氧官能团(如羧基、内脂基、酚基、羰基等)。
一般含氧官能团高的炭黑,挥发份高,其色调可调性能好,其流动度也较高。
炭黑样品加热至825±25oC后以百份重量损失表示炭黑挥发份。
金刚石微粉粒度的主要技术指标

金刚石微粉粒度的主要技术指标
金刚石微粉是一种重要的超硬材料,广泛应用于磨削、切削、抛光和轴承等领域。
其粒度是评价其质量和性能的重要指标之一。
以下是金刚石微粉粒度的主要技术指标:
1.平均粒径(D50值):表示一组粉末中50%的颗粒直径小于该值,是衡量粉末粒度大小的重要参数。
2.最大粒径(Dmax值):表示一组粉末中最大颗粒的直径大小。
3.最小粒径(Dmin值):表示一组粉末中最小颗粒的直径大小。
4.粒度分布:通过对粉末粒径的测量,可以得到粒度分布曲线,从而了解粉末的粒径分布情况。
5.比表面积(BET值):表示单位质量的粉末所占据的表面积大小,也是衡量粉末颗粒大小的重要参数之一。
6.颗粒形态:金刚石微粉颗粒形态多样,有球形、棱柱形、六角柱形等,不同形态的颗粒对材料的性能也会产生不同的影响。
综上所述,以上几个参数是金刚石微粉粒度的主要技术指标,可以用于评价其质量和性能,也是选择合适的金刚石微粉的重要参考。
- 1 -。
微粉粒度分布标准us

微粉粒度分布标准us
微粉是指颗粒尺寸在1微米至100微米之间的固体颗粒,其粒度分布对于许多
工业领域的产品质量和性能具有重要影响。
微粉的粒度分布标准us是指微粉颗粒
在不同尺寸范围内的分布情况,它对于微粉的加工、应用和性能评价具有重要意义。
首先,微粉的粒度分布对于产品的性能和品质具有直接影响。
在许多行业中,
微粉被广泛应用于涂料、塑料、橡胶、油墨、陶瓷等制品的生产中。
微粉的粒度分布均匀与否,直接关系到产品的光泽度、透明度、强度、导电性等性能指标。
因此,制定微粉粒度分布标准us对于保证产品质量和性能具有重要意义。
其次,微粉的粒度分布标准us对于微粉的加工具有指导作用。
在微粉的生产
加工过程中,粒度分布的不均匀会导致生产工艺的不稳定,甚至影响产品的使用效果。
通过制定粒度分布标准us,可以为生产加工提供参考依据,帮助企业优化生
产工艺,提高生产效率,降低生产成本。
另外,微粉的粒度分布标准us还对于微粉的性能评价具有重要意义。
通过粒
度分布标准us的制定,可以对微粉的粒度分布进行客观、准确的评价,为用户提
供可靠的产品质量信息。
这对于用户选择合适的微粉产品,保证产品的使用效果具有积极的促进作用。
综上所述,微粉粒度分布标准us对于微粉产品的质量、加工和性能评价具有
重要意义。
通过制定科学合理的粒度分布标准us,可以促进微粉产品的质量提升,推动行业的健康发展。
因此,各行业应重视微粉粒度分布标准us的制定与执行,
为产品的质量和性能提供有力保障。
金相试样机械抛光质量影响因素及解决措施
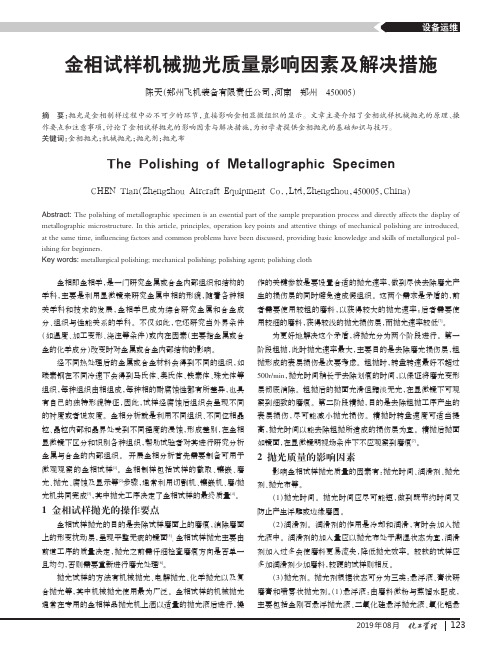
2019年08月金相试样机械抛光质量影响因素及解决措施陈天(郑州飞机装备有限责任公司,河南郑州450005)摘要:抛光是金相制样过程中必不可少的环节,直接影响金相显微组织的显示。
文章主要介绍了金相试样机械抛光的原理、操作要点和注意事项,讨论了金相试样抛光的影响因素与解决措施,为初学者提供金相抛光的基础知识与技巧。
关键词:金相抛光;机械抛光;抛光剂;抛光布The Polishing of Metallographic SpecimenCHEN Tian (Zhengzhou Aircraft Equipment Co.,Ltd,Zhengzhou,450005,China)Abstract:The polishing of metallographic specimen is an essential part of the sample preparation process and directly affects the display of metallographic microstructure.In this article,principles,operation key points and attentive things of mechanical polishing are introduced,at the same time,influencing factors and common problems have been discussed,providing basic knowledge and skills of metallurgical pol⁃ishing for beginners.Key words:metallurgical polishing;mechanical polishing;polishing agent;polishing cloth金相即金相学,是一门研究金属或合金内部组织和结构的学科,主要是利用显微镜来研究金属中相的形貌,随着各种相关学科和技术的发展,金相学已成为综合研究金属和合金成分、组织与性能关系的学科。
金刚石微粉粒度标准

金刚石微粉粒度标准引言近年来,金刚石微粉在各个行业中的应用越来越广泛,如硬质合金、切削工具、磨料材料等领域。
在生产和应用金刚石微粉时,人们普遍关注的一个重要参数就是其粒度。
粒度的不同决定了金刚石微粉在不同领域的应用效果。
因此,为了规范金刚石微粉的质量和使用,制定金刚石微粉粒度标准是非常必要的。
粒度测量方法金刚石微粉的粒度是指金刚石微粉中颗粒粒径的大小。
常用的粒度测量方法有:1.筛分法:利用标准筛分装置将金刚石微粉按粒径从大到小进行分类。
筛网的孔径决定了分割粒径的上下限。
2.液体分散法:利用相对粒度明显不同的流体将金刚石微粉分散,然后通过测量不同粒度颗粒在液体中的沉降速度或浮力大小来精确测定颗粒粒径。
3.显微照相法:利用显微镜观察金刚石微粉颗粒的实际大小,并根据观察结果进行频率统计。
粒度标准根据金刚石微粉的不同应用领域和生产工艺要求,制定了不同的粒度标准。
以下是常见的金刚石微粉粒度标准:粗尺码区•D3:均匀尺码为3mm的金刚石微粉。
•D5:均匀尺码为5mm的金刚石微粉。
•D10:均匀尺码为10mm的金刚石微粉。
中尺码区•D15:均匀尺码为15mm的金刚石微粉。
•D20:均匀尺码为20mm的金刚石微粉。
•D30:均匀尺码为30mm的金刚石微粉。
细尺码区•D40:均匀尺码为40mm的金刚石微粉。
•D50:均匀尺码为50mm的金刚石微粉。
•D60:均匀尺码为60mm的金刚石微粉。
以上标准仅为示例,实际应用中可以根据具体需求进行调整和制定。
粒度控制为了确保金刚石微粉的质量和稳定性,粒度控制是非常重要的。
以下是一些常见的粒度控制方法:1.定期对金刚石微粉进行粒度分析,掌握其分布情况。
2.制定合理的生产工艺和操作规范,确保金刚石微粉在生产过程中的粒度变化控制在合理的范围内。
3.选择合适的筛网孔径,确保筛分过程的准确性和可靠性。
4.优化液体分散方法,提高测量精度。
5.根据粒度分布数据,进行有效的数据统计和分析,为粒度控制提供参考依据。
cmp 磨料 指标

CMP(化学机械抛光)的磨料指标主要包括以下几个方面:
1. 化学成分:CMP抛光液中包含去离子水、磨料、pH值调节剂、氧化剂、抑制剂和表面活性剂等化学成分。
这些成分的种类和比例对于抛光效果至关重要。
2. 磨料:磨料是CMP抛光液中的重要组成部分,一般包括纳米级SiO2、Al2O3粒子等。
磨料的粒度、形状和分布对抛光速率、表面粗糙度和抛光均匀性都有显着影响。
3. 质量分数:即磨料在CMP抛光液中的比例,是衡量磨料含量的一项重要指标。
4. 粒径:磨料的粒径大小直接影响到抛光速率和表面粗糙度。
较小的粒径可以获得更光滑的表面,但同时也需要更多的抛光液和更长的抛光时间。
5. 分散度:指磨料在CMP抛光液中的分散程度。
良好的分散度可以提高抛光效率和表面质量。
6. 形貌:磨料的形状和结构也会影响其抛光效果。
不同形貌的磨料可能在不同的抛光条件下表现出不同的优势。
这些指标对于CMP抛光液的性能至关重要,因此需要密切关注并控制这些指标,以确保获得最佳的抛光效果。
- 1、下载文档前请自行甄别文档内容的完整性,平台不提供额外的编辑、内容补充、找答案等附加服务。
- 2、"仅部分预览"的文档,不可在线预览部分如存在完整性等问题,可反馈申请退款(可完整预览的文档不适用该条件!)。
- 3、如文档侵犯您的权益,请联系客服反馈,我们会尽快为您处理(人工客服工作时间:9:00-18:30)。
粒度是磨料微粉最重要的技术指标之一。
然而由于它的抽象性和实际测试存在的困难,许多用户甚至部分制造商对“粒度”的理解都比较模糊,这实际上成了我国磨料技术水平提高的一大障碍。
为此对“粒度”的基本概念作一通俗{TodayHot}介绍。
“粒度”是指一个粉体样品颗粒大小的总体描述。
详细的要用粒度分布来表示,在实用中一般只取几个关键参数,例如磨料JIS标准中的D50、D94、D3。
由于实际的微粉颗粒是不规则的,而且同一样品中各颗粒之间也不一致,所谓颗粒的大小,用不同方法就会得出不同的结果。
因此任何一个粉体产品的粒度标准,都必须注明所用测量仪器的原理。
有的标准允许用几种原理的仪器,这时标准数据也是不同的。
下面对几种国内常用的中国国家(W)标准和日本JIS标准作具体说明。
国家标准:俗称W标准,因在粒度号前冠以字母W而得名,W是汉语“微粉”中“微”字的拼音(WEI)的字头。
实际上该标准已于1998年废止,但现在还在技术设备比较落后的磨料制造商和广大用户中流行。
W标准是建立在用显微镜刻度尺测量颗粒大小的方法上的。
这种方法规定用颗粒的最大宽度代表颗粒的大小。
该标准以大致为公比对颗粒大小(又称“粒径”)分档,例如40、28、20、14、10等等(单位为“μm”),又把一个粉体样品中的颗粒按上述分档法为基本粒、混合粒、细粒、粗粒和最大粒。
以粒度W14{HotTag}为例。
基本粒:10-14μm
混合粒:7-14μm
细粒:<7μm
粗粒:14-28μm
最粗粒:28-40μm
基本粒是磨料中最有用的部分,希望比例越高越好,国标要求在50%以上。
混合粒则占磨料的主要部分,比例当然也是越高越好,国标要求在80%以上。
W 标准粒径的定义
日本标准推荐的仪器有两种原理:一是电气抵抗法(即电阻法或称库尔特法),二是沉降管法。
两种方法由于原理不同,标准值也不同,例如,JIS#1500,电阻法D50值为8.0±0.6μm,而沉降管法的D50为10.51μm。
沉降管法速度慢,人工参与多,实际上很少被采用。
现在人们通常说的JIS标准指的都是用电阻法的。
日本标准采用“最大粒、D3、D50和D94”等4个参数表述一个牌号微粉的粒度,这里,最大粒的概念是很清楚的,D3、D50和D94则表示从最大粒径开始算到这些粒径值的颗粒(以重量计)含量分别为3%、50%和94%。
仍以JIS#1500为例:
最大粒<23μm
D3 <20μm
D50 =8.0±0.6μm
D94 >4.5μm
JIS微粉粒度标准图示
D3=10.99μm D50=8.00μm D94=6.1μm
日本标准与中国W标准的主要区别有二点:
其一,日本标准规定使用粒度仪器(电阻法或沉降管法)测量微粉的粒度(分布),而中国W标准则用显微镜目视法测量颗粒大小,后者精度较低,受人为因素影响大。
其二,日本标准对粒度号的区分比较细,从#240(D50=57μm)到#8000 (D50 = 1.2μm)共分18个号,而中国W标准从W63(D50≈50μm)到W3.5(D50≈2.5μm)共分10个号,前者差不多比后者多一倍,因此有人说按W标准一个粒度号的微粉,按日本标准可以分成两个粒度号。
以上两点就是人们认为日本标准的微粉粒度较集中的原因。
找W标准的粒度号与JIS标准的对应关系时,大体上只要将“W”后的数字乘以0.7作为
D50值,再在JIS粒度表中找D50值最相近的粒度号就可。
例如W10的D50约为7μm,相当于JIS#1500(D50μm)。