拉延模设计规范
拉延模设计顺序标准
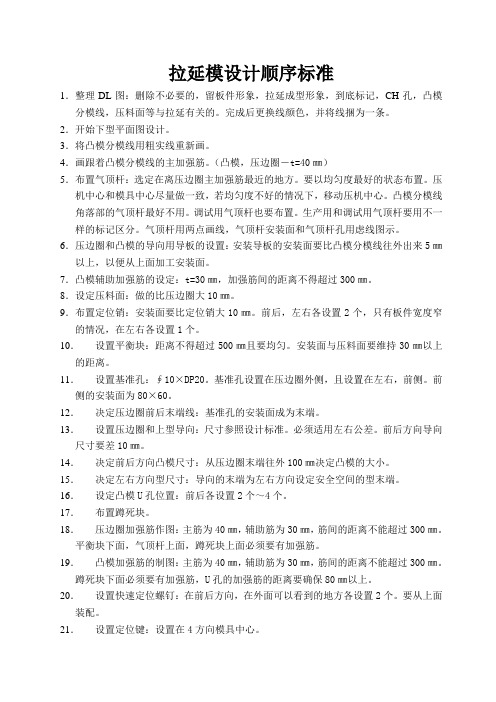
拉延模设计顺序标准1.整理DL图:删除不必要的,留板件形象,拉延成型形象,到底标记,CH孔,凸模分模线,压料面等与拉延有关的。
完成后更换线颜色,并将线捆为一条。
2.开始下型平面图设计。
3.将凸模分模线用粗实线重新画。
4.画跟着凸模分模线的主加强筋。
(凸模,压边圈-t=40㎜)5.布置气顶杆:选定在离压边圈主加强筋最近的地方。
要以均匀度最好的状态布置。
压机中心和模具中心尽量做一致,若均匀度不好的情况下,移动压机中心。
凸模分模线角落部的气顶杆最好不用。
调试用气顶杆也要布置。
生产用和调试用气顶杆要用不一样的标记区分。
气顶杆用两点画线,气顶杆安装面和气顶杆孔用虑线图示。
6.压边圈和凸模的导向用导板的设置:安装导板的安装面要比凸模分模线往外出来5㎜以上,以便从上面加工安装面。
7.凸模辅助加强筋的设定:t=30㎜,加强筋间的距离不得超过300㎜。
8.设定压料面:做的比压边圈大10㎜。
9.布置定位销:安装面要比定位销大10㎜。
前后,左右各设置2个,只有板件宽度窄的情况,在左右各设置1个。
10.设置平衡块:距离不得超过500㎜且要均匀。
安装面与压料面要维持30㎜以上的距离。
11.设置基准孔:∮10×DP20。
基准孔设置在压边圈外侧,且设置在左右,前侧。
前侧的安装面为80×60。
12.决定压边圈前后末端线:基准孔的安装面成为末端。
13.设置压边圈和上型导向:尺寸参照设计标准。
必须适用左右公差。
前后方向导向尺寸要差10㎜。
14.决定前后方向凸模尺寸:从压边圈末端往外100㎜决定凸模的大小。
15.决定左右方向型尺寸:导向的末端为左右方向设定安全空间的型末端。
16.设定凸模U孔位置:前后各设置2个~4个。
17.布置蹲死块。
18.压边圈加强筋作图:主筋为40㎜,辅助筋为30㎜,筋间的距离不能超过300㎜。
平衡块下面,气顶杆上面,蹲死块上面必须要有加强筋。
19.凸模加强筋的制图:主筋为40㎜,辅助筋为30㎜,筋间的距离不能超过300㎜。
拉延模设计手册

拉延模设计手册一、拉延模的分类拉延模分双动拉延模与单动拉延模两类1、双动拉延模是在专用的双动压力机上生产的拉延模,通常上模为凸模,下模为凹模,压边圈安装在压机的外滑块上,其结构如下图,此种结构拉延模压边力较为稳定,但由于需要专用的压机,安装较为烦琐,且结构尺寸较大,现在已经运用的越来越少。
2、单动拉延模是在单动压机上生产的拉延模,通常上模是凹模,下模是凸模,压边圈由下气垫或其它压力源(例于氮气弹簧)提供压料力,其结构如下图,由于模具通用性好,现大部分拉延模为此种结构。
工作台下模上模压边圈上模垫板内滑块外滑块下模上模工作台压边圈上滑块二、拉延模的主要零件(主要为单动拉延模)拉延模一般有上模、下模、压边圈三大部件组成(根据结构的不同要求,可能增加一此部件,例于局部的小压料板),以及安装这三大部件上的其它功能零件,主要有以下零件:1、导向零件:耐磨板、导向腿,导柱;2、限位调压零件:平衡块、到底块;3、坯料定位零件:定位具、气动定位具;4、安全装置:卸料螺钉(等向套筒,也起锁付的作有)、安全护板;5、拉延功能零件:到底印记、弹顶销、通气管、CH孔合件;6、取送料辅助零件:辅助送出料杆、打料装置。
三、单动拉延模的设计(一)模具中心的确认与顶杆的分布模具中心的确认通常依据顶杆的布置的需要设定。
一般在工艺设计时,会按钣件的中心确定一个数模中心。
顶杆的分布需尽量靠近分模线,并均匀布,通常两根顶杆之间最多空一个顶杆位,顶杆数量要尽可能多。
在模具设计时首先以数模中心与压机工作台中心重合,如顶杆分布满足上述要求,则以数模中心做为模具中心。
如无法满足上述要求,侧在需要更改的方向上移动(最大1/2顶杆间距),确认一个最优化的方案,同时以工作台的中心做为模具的中心。
(注:在试模压力机与工作压力机顶杆孔不致时,需设置试模顶杆,并在优先保证生产顶杆的要求下,优化顶杆部置)模具中心与数模中心重合如厂家要求使用顶杆以外的压力源,例于氮气弹簧等,则一般直接以数模中心做为模具中心,压力源沿分模线均匀分布,并需确认压力源的大小是否足够。
拉延模设计

5.上模座
(一)模面 如同压板模面,将素材线往外偏20mm得到模面。 (二)肋条 根据分模线、平衡块来布主肋、副肋。 (三)漏水孔与窥视孔 漏水孔作用为:清洗模具时,使上模能方便的排水。如左下图所 示。窥视孔为当采用箱跟导引时,为了方便测量箱跟导引与耐磨板间 的间隙,在耐磨板上方开个孔以方便测量。该孔尺寸为40X50。
外部工艺补充——压料面
压料面是指板料在凹模圆角以外的法兰部分,工件本体部分或工 艺补充部分组成,其应是平面或曲率较小的曲面,不允许有大的起伏 或拐点在拉延成型过程中,压料面的材料被逐渐拉入凹模型腔内,转 化为覆盖件形状。压料面与凸模形状保持一定几何关系,保证在拉延 过程中板料处于张紧状态,并能平稳地包拢凸模,防止起皱破裂。
3.模仁
(一)2D面 如同压板,模仁的2D面也需要逃料,其尺寸为: ①=50mm,②=10mm。
(二)肋条 分模线内偏10mm布主肋,再布副肋,并保证型面肉厚有60mm。
(三)定位元件 当模仁采用组合式时,模仁需要准确的定位在模座上。一般采用 键定位。键一般设置 3处,键的长度为60mm,宽度视模仁大小而定。 (四)锁付 模仁的锁付有正锁和反锁两种。中小模仁锁付用正锁,大模仁用 反锁。正锁为螺栓锁付承面在模仁外侧,螺纹孔打在下模座上,螺栓 由下模座的正面锁入。反锁则相反,锁付承面在模仁内侧,螺纹孔打 在模仁的锁付面上,螺栓由下模座的底面锁入。采用正锁时,应注意 锁付承面的打螺丝空间,承面不能太小,一般为分模线往外偏70mm 左右。 (五)起吊、翻转 模仁设计时应考虑到起吊与翻转的操作。一般起吊孔可以在螺 栓锁付承面上打出。翻转可在模仁侧壁上补上四个平台,以打翻转螺 丝孔,或在模仁侧壁上装铸入螺母,翻转应在同一水平面上。
2.对覆盖件的要求
拉延模

拉延模具检测规范
为了提高模具制造质量,特制定本规范:
1.满足装配的技术要求。
2.拉延模外观整洁、装配合理,凸模、压边圈下平面对凹模上平面的平
行度误差不大于0.2/300(mm)。
3. 拉延模凸模
3.1 拉延模凸模表面光顺无波纹,表面粗糙度Ra0.8μm ,装饰棱线清晰、美观。
3.2 导板的安装面与冲压方向平行。
3.3 在凸出的筋和棱角处火焰淬火。
4. 压边圈
4.1 拉延模压边圈压料面表面粗糙度Ra0.8μm 。
4.2 拉延模压边圈导向与拉延模凸模的导向间隙为0.05mm~0.10mm。
4.3 拉延模压边圈的内轮廓与拉延模凸模的外轮廓的间隙为 1.5mm~3mm。
(根据模具的大小或分模线的型面位置)
4.4 拉延模压边圈的下限位墩与拉延模凸模的限位的间隙小于0.05mm。
5. 凹模
5.1 凹模型腔形状与凸模吻合,并保持均匀料厚间隙,表面粗糙度Ra0.8μm ,凹模圆角和突出部分表面火焰淬火。
5.2 压料面形状与压边圈吻合,并保持均匀料厚间隙,表面粗糙度Ra0.8μm。
5.3 凹模导板与压边圈导向间隙为0.05mm~0.10mm。
5.4 凹模导板的安装面与冲压方向平行。
5.5 凹模型面限位与压边圈的上限位的间隙小于0.05mm。
6. 凸模与凹模的排气孔布置均匀,不能在棱线及凸楞上钻孔,孔经小于6mm。
7. 板料定位全部采用角板定位。
(特殊情况可采用销式定位)。
003--拉延模几大要素的设计原则
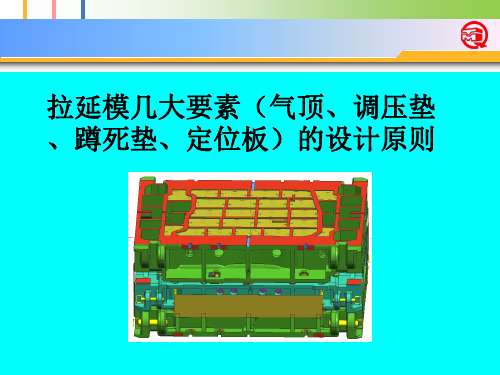
结束
拉延模几大要素(气顶、调压垫 、蹲死垫、定位板)的设计原则
一、拉延模的定义
定义:拉延模就是使平面板料拉伸成具有一定形状 的空心零件的模具
拉延模
平面坯料
空心零件
二、拉延的运动过程
三、拉延模的分类
拉延模分为单动拉延、双动拉延和三动拉延,由于三动拉
延涉及较少,这里只简单介绍前两种。
单动拉延分以下两种
顿死垫
顿死垫—用于压边圈与下模具之 间,在模具死点状态顿死成型的 垫块。 调压垫布置及有关事项:
如果产品范围大于拉延分模线, 则拉延时需要墩死。如果产品范 围在拉延分模线内则不需要墩死 ,二者之间留2mm间隙。 墩死垫尽量布置在调压垫正下方 ,尽可能靠近分模线。墩死垫下 方也要有筋,这样,当墩死时调 压垫墩死垫从上到下均为刚性接 触,增强了模具强度。如果制件 压料面过大,调压垫距离分模线 较远,则保证掉压垫下方的墩死 垫之外,在掉压垫与分模线之间 ,靠近分模线处再相应增加几处 墩死垫,使拉延充分墩死,充分 成型。
注:St:压边圈行程 ST:气垫行程 A:工作台厚 D:=(A+B)-L L:气顶杆长 H、H’:气顶承接面距工作台距离
调压垫
调压垫—用于压边圈与上模控
制二者之间局部压力的垫块。 调压垫布置及有关事项:
调压垫应延分模线均匀分布, 间隔400mm左右。调压垫下 方应有立筋,增加强度。 为了调压效果更好,制件四角 调压时,尽量在角部布置两个 调压垫,避免只在角上放一个 调压垫。 调压垫Z向应均分在压料面上下 两侧 ,使压料面高于调压垫安 装面,如果制件起伏较大,无 法保证安装面低于压料面,则 调压垫安装面与压料面之间留 至少30mm的距离 ,以保证加 工压料面时,球刀不与调压垫 安装面干涉。
汽车覆盖件拉延模设计方法

•
8.确定模具尺寸、导腿尺寸、导板尺寸位置
• 确定模具尺寸 (1)调入模板,调整闭合高(根据工艺卡),模具长宽 (2)确定模具吊耳、起重棒、翻转套大小及位置 • 确定导腿尺寸 (1)导腿长度至少占整体宽度2/5 (2)确定导腿刃入量,保证导腿导板在上模触料之前刃入40mm (3)导腿处导板保证同一高度且同时刃入 • 凸模导板尺寸及位置 (1)导板的安装位置约在凸模长度方向的1/6处 (2)导板导向面的宽度约为凸模长度的1/5-1/4 (3)导板高度〉压边圈行程+60~100mm (4)导板安装面要凸出分模线3~5mm便于加工 ( 5 ) 导板上端面与压边圈距离最好设计为40mm,因钳工调试时 不放墩死垫,容易发生异常。
9.布筋、挖夹持孔、减重孔、流水孔、出气 孔 • 布筋
(1)受力处必须布筋支撑,如调压垫、墩死垫 上下模底面筋要与机床的T槽错开,分模线以内上模本体、凸模、下 模座的筋要对应,导板后面最好有筋支撑 (2)两筋间隔最大350MM,一般控制在300MM以内 (3)为保证铸造清砂,底空不易过深过窄,底空型腔深度最好小于2.5 倍的底空宽度 (4)受力筋上尽量少挖减重孔 (5)尽量避免十字筋 • 夹持孔及减重孔的尺寸及形状,根据模具结构尺寸的不同而不同,但 其底边与模具底面间距至少100MM-150MM • 流水孔一般为直径Φ40的圆孔,设在模具型腔底部,并要保证每个型 腔的液体能流到模具外侧。 • 凸凹模的随型筋上挖Φ50的出气孔,不要存在封闭的型腔 凸凹模的型面上挖Φ4或Φ6的出气孔,打在凸凹模的凹形处
10.满足设计任务书及客户要求
• • • • • • • • • 活动件防护装置 在下模装防护板 压板槽、上模快卡、下模快速定位的要求 键槽及通键、加工基准孔的要求 起重形式的要求 气顶接柱上加钢垫、气顶躲空的要求 气路及电路位置的要求 模具防反、防侧向力的要求 客户及任务书对标准件的要求 客户的其他要求(如铸字、叉车过孔等)
拉延模设计
拉延模设计一:准备工作拉延模DL图内容:1层分模线2层板料线3层工艺面4层CH修模孔5层B/H到底标记导入冲压机床放入200层。
二:缝补工艺面。
三:压边圈(1)分型面设计1.板料线,拉伸外扩20. C拆分体工艺面实体放入20层,标注压边圈。
涂颜色。
2.7投影分模线到地面关联去掉,保留分模线,Ctrl+3光顺分模线,大小调整数,然后点光顺,如果没有光顺,先Alt+D打断然后光顺。
光顺后放入201层,拉伸分模线,单边偏执外扩3mm。
求差。
(2)空刀设计分模线向下偏置50,单边偏置13.分模先不能偏置就打断。
(3)长宽确定,不加工面。
拉伸地面,双侧偏置60+30. 然后分型面,D大致偏置-20,C拆分实体,然后求和。
(4)平衡块,定位具,基准孔。
设计平衡块间距350-450,左右2个,平衡块坐面低于分型面。
定位具6个,左右各1个,两边各2个,定位具沉入分型面,跟板料线对齐。
基准孔在定位具后边各一个。
Y正方向1个。
(5)高度的确定,行程有50以上接触,55行程100的导板正好。
条件1型面差+3045-70用75的导板。
70-95用100的导板,95-120用125导板,120-145用150的导板。
导板长度+100就是压边圈高度。
条件2行程+5070-105用100的导板。
105-130用125的导板,大于130用150导板。
导板长度+100就是压边圈高度。
(6)顶杆设计分模线外两侧,均匀排布。
可以Y向移动。
不可以X向移动,坐面60.厚度10.垫块厚度20. (7)导引设计导板宽度板料线1/8。
位置在分模线1/6处。
两边放1个,长边放2个。
.导板面到分模线5-10.先40厚的长方体。
C拆分10,20,10. 3块。
1.导板面:上面9倒10mm斜角。
下面偏置15,倒20圆角。
2.背托面:上面偏置5-10,下面拉伸40,向里偏置10。
3.导入导板。
涂颜色。
拉伸导板面,左40右40上30.倒圆角25.(8)淘沙减重处理5偏置底面轮廓线40。
2.拉延模设计规范
目录1 拉延模的类型....................................................22 下平面图标注内容................................................43 上平面图 ....................................................174 剖视图........................................................255 尺寸标注与标准件选用规范........................................266 铸件结构.....................................................267 拉延筋 ......................................................298 拉延凸模轮廓的确定............................................319 拉延件坯料尺寸的确定...........................................3210 拉延工艺缺口...................................................3311 拉延模的材料....................................................3512 拉延件对拉延模的特殊要求........................................361 拉延模的类型拉延模送料面线的高度及结构形式,是根据冲压设备情况由用户提出的。
拉延模的闭合高度一般取650-1000mm。
送料面线的高度一般取500-700mm,必须保证压边圈有足够的强度,使操作者能够方便的进行上下料操作,所以送料面高度取在闭合高度中心偏上100-200mm。
拉延模制作规范
1)把压边圈放在下模上锁紧(放到底),模仁涂红丹,导板(耐磨板)涂红丹,要求薄而均匀。
2)把下模反转放在上模上,上机台合模、
3)先合导板,要求接触率80%以上,均匀接触。同组立时导板研配。
4)模仁部分的研配
要求压机不加压,上模模仁水平面部分红丹接触率为90%以上,均匀接触。基准面接触率为100%,斜面放铅丝确认间隙。
B.顶杆压力设定——根据图面设定压力,与设计协商(经过计算)
3.素材摆放位置确认
素材放在压边圈上,根据模仁形状初步设定素材位置,并划线作为标记
4.管理面间隙确认
A.先压出阻条痕迹(没有阻条怎么办?)
B.素材管理面位置涂红丹
C.采用分段拉延的方法确认管理面间隙、观察素材走料状况
5.板件成型下死点前10mm观察并确认板件的褶皱发生与破裂发生,参照板件褶皱与破裂发生的简单对策
5)钻行程螺栓孔。
6)以上完毕后,在行程螺栓的位置把压边圈锁紧固定。
6、组好后,准备加工
7、如果模仁、压边圈,上模有镶块的情况。
1)将磨好的钢块与机能无关的棱角倒角C2.
2)清理钢料,将钢块与安装面和背托面进行研磨,用红丹检测,85%以上的接触率要均匀,间隙MAX0.03。
3)有定位键的要先配好定位键。
10.扣除料厚后,抛光。
11.再次试模,确认成形极限。平衡块高度,模具高度确认
12.试模完成
13.如果是镶块的拉延模具,就要送出热处理
1),热处理前做如图处理
2),热处理回来后,做平面度研磨。组立。
3),合模确认各部位间隙。
4),再次试模确认。
C研磨抛光后要预留刀花0.02-0.04以保证精度,特别是基准面及板件搭接面。
2)R角研磨抛光
模具培训:拉延模几大要素的设计原则
定位板的定位方向安装面留出
3mm间隙,待试料后确定最终 位置。
结束
1.内导向拉延模—压边圈的导向形式在分模线以里的拉延模
三、拉延模的分类
2.外导向拉延模—压边圈的导向形式在分模线以外的拉延模
三、拉延模的分类
双动拉延
三、拉延模的分类
另外,根据工作内容的不同及成型的需要,拉延模中还会增加不同的内 容,例如增加切角,破裂刀等,根据料厚的不同,还会采用镶块结构
切角拉延局部
定位板
▪ 定位板—用于放入制件时使其与
下模型面相对位置固定贴紧的部 件。
▪ 定位板的布置及有关事项: 定位板一般设置于下模、下圈或
下芯上。
拉延模需要四面布置定位板,数
量视模具大小确定,长方件车门 等一侧2处,细长件柱类1处。 定位板间距大于制件定位方向 2/3以上。
对于自动线模具,一般XY方向
若St+H’+D>ST应加接柱, 使St+H+D≤ST,则H=ST-StD
注:St:压边圈行程 ST:气垫行程 A:工作台厚 D:=(A+B)-L L:气顶杆长 H、H’:气顶承接面距工作台距离
调压垫
▪ 调压垫—用于压边圈与上模控
制二者之间局部压力的垫块。
▪ 调压垫布置及有关事项:
调压垫应延分模线均匀分布,
拉延模几大要素(气顶、调压垫 、蹲死垫、定位板)的设计原则
一、拉延模的定义
定义:拉延模就是使平面板料拉伸成具有一定形状 的空心零件的模具
拉延模
平面坯料
空心零件
二、拉延的运动过程
三、拉延模的Leabharlann 类▪ 拉延模分为单动拉延、双动拉延和三动拉延,由于三动拉
- 1、下载文档前请自行甄别文档内容的完整性,平台不提供额外的编辑、内容补充、找答案等附加服务。
- 2、"仅部分预览"的文档,不可在线预览部分如存在完整性等问题,可反馈申请退款(可完整预览的文档不适用该条件!)。
- 3、如文档侵犯您的权益,请联系客服反馈,我们会尽快为您处理(人工客服工作时间:9:00-18:30)。
拉延模设计规范
模具大小分类:
注:为导板宽度
5
模具端头设计
上下模导向型式尺寸
导柱规格
d di D D1 D2 H1 H2 A ?50 50 40 70 60 125 75 70 140 ?60 60 50 :80 70 135 : 90 90 160 ?80 80 60 100 90 155
120 120 190 ?100
100
80
120
110
不套导 柱
150 150
210
h
■ 1・
严1
1
1 J'
常
— 工
I 1
町
1
1B 1
10 d . A A rj o 十 p — 1
II
I 1 —1 + “ ,1 ■
L ---- ■ ? ----- 11
|i
—1—
模具端头主要型式和尺寸如下:
A
<1>
<2> <3>
模具锁附及压板槽结构压板槽结构如下:
4
60r ir'
般
模
结
自动装模、
用结构
装
用
构
注:1.H值见筋厚规定
9 Or In
模具长度L 压板槽单边数量
L W 1600 2
1600VL W 2500 3
L>2500 4
压板槽设置数量:
5
限位柱
模具类别 特大型 大型 中型 小型
限位柱直径D
80 P 70 60 60 限位柱处方形 平
台尺寸A
100
90
80
80
注:1.每套模具在四角设置4处
材科:45
5 安全平面
每套模具必须设置4处安全平面(空间不允许时可仅设2处),且设置在明显处
安全平面尺寸:
注:1.中型模具空间有限时可设成120X120或120X150
2.上下模安全平面在闭合状态下相距110。
5 连模板
连模板使用范例及安装凸台尺寸如下:
.
扳
模具类别特大型大型中型小型连模板尺寸80X80 80X80 60X60 60X60 I
--------
T
型号 A B T L
「50 30 50 10 结构决定
70 40 70 12 结构决定
注:连模板长度应在存放状态下计算
5 平衡块
材料:45, HRC28-32
规格代号 A 模具类型
50 50 小型,且长度W
1200mm
60 60 ①.小型,(1200mm w长度w 1500mm ②.中型
80 80 大型,特大型
0A
5 起重装置标准一吊耳
吊棒单个承重
(T)
使用范围
© 50 3.5 中型
© 55 4.
2
大型,但宽
< 1500mm
© 60 5.0 特大型
ca
o
90
注:起重孔内必须镶钢管,保证同
轴度#58
j J
X! !
1 、
\
1
i
50, 55吊棒的吊耳
5
起重装置标准一插销式起重棒
吊棒 规格
D1 D2 D3 D4 D5 D6 D7 L L1 40 ;40
50 20 :22
35 32 :30 160 210 50 50 60 24 26 39 36 40 220 270 55 55 65 26 28 44 41 45 220 270 60 :60 70 28 :30 49 46 :50 250 300 70 70 80 32 34 56 51 60 250 300 80
80
90
36
38
62
56
70
300
350
材料:45,锻件,调质HRC2&32。
L
C4
飞土
5
起重装置标准一铸入式起重棒
D d D1 L L1 A B C
E
F
G R r 单个承 重(T )
42 90
110 140 80 15 75 20 10 10 32 4 1 0.7 50 110 130 175 100 :20 90 20 15 15 40 5 2 1.2 60 120 160 205 120 :20 110 20 15 25 50 5 2 2.5 70 130 180 230 140 25 115 25 20 25 55 5 2 5.0 80 130 210 250 160 25 125 25 20 35 65 5 2 7.0 90 140
240
270 180 ;25
135
25
25
35
75
5
2
10.0
吊棒 使用模具范围
D=42 小型,且长度w 1200mm
D=50
小型,且1200mm :长度w 1600mm
材料:45,锻件,调质HRC2&32
R
铸入式起重棒镶入处结构:
1-2 通用设计标准
注:
1. 铸件逃孔制作标准
2. 除制作必要外,外围铸孔尽量不要制作;
3. 铸件不加工处均倒角C10,吊索滑动部分均倒R20; 加工
面外缘处倒角C2-C3;
4. 铸孔标准上列为参考值,实际制作考虑模具强度;
5. 铸件筋条间最大距离w 300mm
1-2 通用设计标准
5
1. 仅导板导向时:
注: 1.防呆仅设置于模具F侧右下侧导板;
2.仅导柱导向时,设置于模具F侧右下侧导柱
2 .导柱兼导板导向时:
模具防呆标准
5 定位具设置
注:1•前后定位具分两种:一种为不带塑料滚轮的普通定位具,用于内装件的拉延模毛坯定位;另一种为带塑料滚轮的定位具,用于外观件的拉延模毛坯定位。
2. 一般零件采用四面定位,每侧各设两处定位,窄长零件前后各设两处定位,左右各设一处定位。
5 耐磨板组立标准防护板凸台1 •耐磨板组立范例如下:
2•防护板凸台
⑴.防护板凸台一律为30X30mr的方凸台,高10mm不需加工;
(2).防护板凸台每间距350m叶400mrr设置一处。
M >0 p
5 凹模与压边圈的设计
1 •凹模与压边圈一般情况下仅用导板导向;当工件拉延困难需在拉延模上设置预切边结构时,应增加导柱导向;
2.凹模与压边圈的导向宽度尽量大于模具宽度的1/2,最小不小于200mm;
3 •凹模上定位具避让孔80X70,平衡块位置要有筋条;
4. 压边圈与凸模为内导时,凹模上安全区与压料圈对应;压边圈与凸模为外导时,凹模上安全区
与凸模(下模座)对应;
5. 凹模主筋条沿分模线布置:
6. 压边圈一般从侧面掏空,压边圈上平衡块位置要有筋条;
7. 当下模座为吊耳起吊型式时,压边圈的吊棒不能在下模吊耳的正上方;
8. 压边圈的限位结构:
小型模具下模座高度取120mm中型模具(长度大于1600)下模座高度取150mm大型模具(长度大于2500)下模座高度取180mm压边圈最矮处高度(非加工面)取170mm 凹上模座最
5 凹模与压边圈的设计矮处高度取130mm
5 压边圈与凸模(下模座)的导向1.一般情况下,采用内导结构:
H下实平賣芟
2. 当凸模细长,强度较差时,采用外导型式;
3. 当行程较大机床闭合高度不足时,采用外导型式;
5 顶杆平衡块到底垫块平衡块
1 •生产顶杆原则上全数设置,仅在与内导板干涉时取消;
2. 试模顶杆依情况设定;
3. 平衡块间距350mmr450mm
4. 平衡块正下方必须设置到底垫块;可视模具大小在其它位置适当增加到底垫块;
5. 压边圈上平衡块位置要有筋条;
6. 下模座上到底垫块位置要有筋条;
7. 压边圈与下模座分模处及平衡块处结构如下:
5 顶杆平衡块到底垫块平衡块
5 顶杆平衡块到底垫块平衡块
当机床顶杆初始顶出高度不够高时,压边圈顶杆凸台铸高,型式如下图,若仍无法满足要求,则追加二级顶杆。
XAM。