化学镀铜沉铜工艺流程介绍
沉铜工艺培训教材
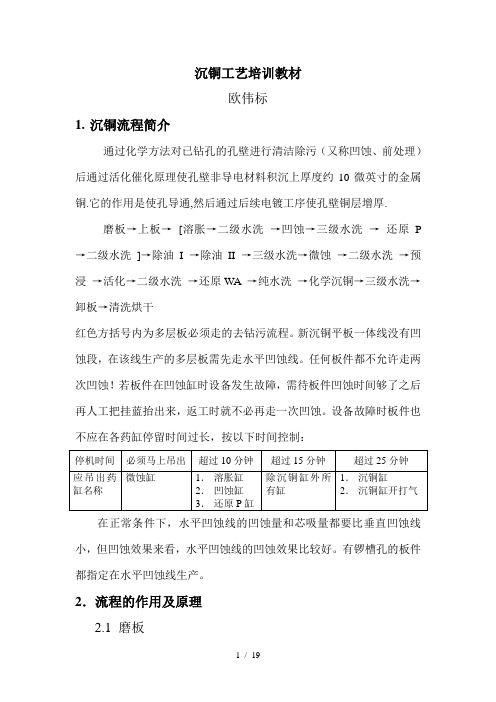
沉铜工艺培训教材欧伟标1.沉铜流程简介通过化学方法对已钻孔的孔壁进行清洁除污(又称凹蚀、前处理)后通过活化催化原理使孔壁非导电材料积沉上厚度约10微英寸的金属铜.它的作用是使孔导通,然后通过后续电镀工序使孔壁铜层增厚.磨板→上板→[溶胀→二级水洗→凹蚀→三级水洗→还原P →二级水洗]→除油I →除油II →三级水洗→微蚀→二级水洗→预浸→活化→二级水洗→还原WA →纯水洗→化学沉铜→三级水洗→卸板→清洗烘干红色方括号内为多层板必须走的去钻污流程。
新沉铜平板一体线没有凹蚀段,在该线生产的多层板需先走水平凹蚀线。
任何板件都不允许走两次凹蚀!若板件在凹蚀缸时设备发生故障,需待板件凹蚀时间够了之后再人工把挂蓝抬出来,返工时就不必再走一次凹蚀。
设备故障时板件也不应在各药缸停留时间过长,按以下时间控制:在正常条件下,水平凹蚀线的凹蚀量和芯吸量都要比垂直凹蚀线小,但凹蚀效果来看,水平凹蚀线的凹蚀效果比较好。
有锣槽孔的板件都指定在水平凹蚀线生产。
2.流程的作用及原理2.1 磨板板件进入沉铜之前要在去毛刺磨板机磨板,磨板的作用:1.磨去钻孔产生的披锋,防止披锋在后续的图形转移过程中划伤贴膜机压辊和刺破干膜造成遮孔蚀不静;2.磨去覆铜板铜箔表面的抗氧化层,并粗化铜箔表面,增加后续铜层与基铜的结合力;3.除去孔内可能存在的铜丝、板粉等杂物。
去毛刺机前两支不织布刷240#,后两支针刷320#。
蚀刻后的板件板件如果出现铜粒、轻微镀层不良、氧化等也会在去毛刺机磨板,但此类板件不能开不织布刷!。
磨板对象磨刷类型 压力 div 速度 m/min 高压水洗 bar 烘箱温度 t 1/2级 3/4级 沉铜前去毛刺240# 320# 0.9 2.8-3.0 ≥25 ≥70 平板后磨板240# 320# 0.4-0.6 3.2-3.5 ≥25 ≥70 蚀刻后磨板 关 320# 0.2-0.4 3.2-3.5 ≥25 ≥70 如果试磨后板件出现披峰, 则可在上述范围内降低速度, 增大压力或横向纵向各磨一遍重新取板试磨。
pcb化学沉铜工艺流程
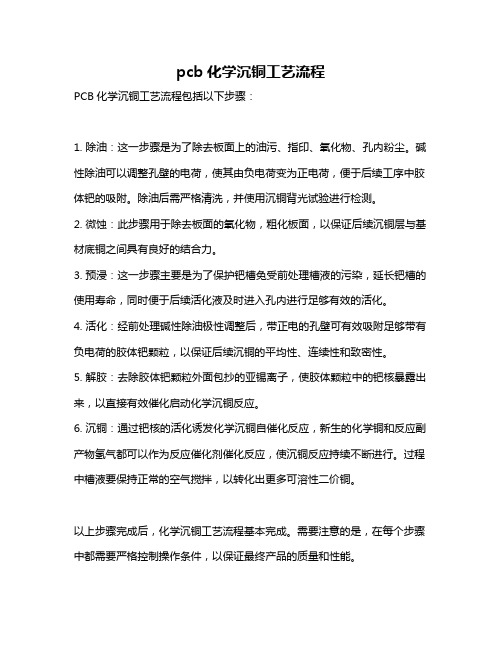
pcb化学沉铜工艺流程
PCB化学沉铜工艺流程包括以下步骤:
1. 除油:这一步骤是为了除去板面上的油污、指印、氧化物、孔内粉尘。
碱性除油可以调整孔壁的电荷,使其由负电荷变为正电荷,便于后续工序中胶体钯的吸附。
除油后需严格清洗,并使用沉铜背光试验进行检测。
2. 微蚀:此步骤用于除去板面的氧化物,粗化板面,以保证后续沉铜层与基材底铜之间具有良好的结合力。
3. 预浸:这一步骤主要是为了保护钯槽免受前处理槽液的污染,延长钯槽的使用寿命,同时便于后续活化液及时进入孔内进行足够有效的活化。
4. 活化:经前处理碱性除油极性调整后,带正电的孔壁可有效吸附足够带有负电荷的胶体钯颗粒,以保证后续沉铜的平均性、连续性和致密性。
5. 解胶:去除胶体钯颗粒外面包抄的亚锡离子,使胶体颗粒中的钯核暴露出来,以直接有效催化启动化学沉铜反应。
6. 沉铜:通过钯核的活化诱发化学沉铜自催化反应,新生的化学铜和反应副产物氢气都可以作为反应催化剂催化反应,使沉铜反应持续不断进行。
过程中槽液要保持正常的空气搅拌,以转化出更多可溶性二价铜。
以上步骤完成后,化学沉铜工艺流程基本完成。
需要注意的是,在每个步骤中都需要严格控制操作条件,以保证最终产品的质量和性能。
化学镀铜的工艺流程

化学镀铜的工艺流程化学镀铜是一种将铜溶液中的铜离子沉积到基材表面的镀铜工艺。
它用于改善材料的外观、耐蚀性和导电性。
下面是化学镀铜的工艺流程。
首先,准备工作。
准备镀铜槽、阳极、阴极以及铜离子溶液。
镀铜槽通常由聚丙烯材料制成,阳极和阴极通常都是铜材料。
铜离子溶液由硫酸铜和其他添加剂组成。
接下来,准备基材。
基材被清洁以去除表面污垢和氧化物。
清洁方法可以是机械清洗、碱性清洗、酸性清洗或电解清洗。
这是为了确保镀铜层能够牢固附着在基材上。
然后,进行预处理。
预处理步骤通常包括电解活化和表面活化。
电解活化是一种通过施加电流使基材表面发生氧化还原反应,以去除表面的氧化物和杂质的方法。
表面活化是一种使基材表面具有更好粗糙度和活性的方法,以便更好地吸收铜离子。
接下来,进行化学镀铜。
将预处理后的基材放置在镀铜槽中,确保基材与阳极和阴极相连接,并且不产生短路。
当电流通过镀铜槽时,铜离子会从溶液中沉积到基材表面,形成均匀的镀铜层。
镀铜时间可以根据需要进行调整,一般为几分钟到几小时。
镀完铜之后,进行后处理。
后处理的目的是增加镀铜层的耐蚀性和光亮度。
后处理方法可以是清洗、热处理或电化学处理。
清洗可以去除残留的溶液和杂质,而热处理可以改善镀铜层的晶体结构和力学性能。
电化学处理是通过施加电流使镀铜层发生氧化反应,以进一步提高其耐蚀性。
最后,进行质量检查。
对镀铜层进行质量检查,包括检查镀铜层的厚度、均匀性和附着力等。
这可以使用金相显微镜、非破坏性测试等方法进行。
总结起来,化学镀铜的工艺流程包括准备工作、基材准备、预处理、化学镀铜、后处理和质量检查。
通过这个工艺流程,可以获得具有良好外观和性能的镀铜层。
镀铜工艺流程

镀铜工艺流程
1. 清洗:
- 将待镀铜的基材进行清洗,去除表面的油污和杂质。
常用的清洗方法包括碱洗、酸洗和水洗。
2. 预处理:
- 在清洗后,需要进行预处理以提高基材与铜层的结合力。
预处理方法有机械预处理和化学预处理两种。
机械预处理包括打磨、抛光等,而化学预处理包括酸洗、去氧化等。
3. 光刻:
- 使用光刻技术,在基材表面涂覆一层光刻胶。
然后在光刻胶上曝光,再进行显影,形成光刻图案。
该图案将指导铜层的沉积位置。
4. 沉积:
- 将预处理过的基材浸入铜离子溶液中,通过电化学方法将铜离子还原成金属铜,并在基材表面沉积出一层铜层。
沉积时需要控制电流和时间,以获得均匀的镀层。
5. 去胶:
- 通过化学溶解或物理去除的方法,将光刻胶从基材表面去除。
这样可以暴露出铜层上的光刻图案。
6. 清洗和抛光:
- 对镀铜后的基材进行清洗和抛光,以去除可能存在的污染物
和缺陷,使铜层更加光滑和亮丽。
7. 检测和包装:
- 对镀铜后的产品进行检测,确保铜层的质量和性能符合需求。
然后进行包装,以便保护和运输。
以上是一般的镀铜工艺流程。
具体的工艺参数和操作步骤可能
因不同的材料和应用而有所差异。
在进行镀铜过程中,请务必遵守
相关的安全操作规程和环保要求,以确保生产的安全与合规。
化学沉铜工艺知识讲解-PPT
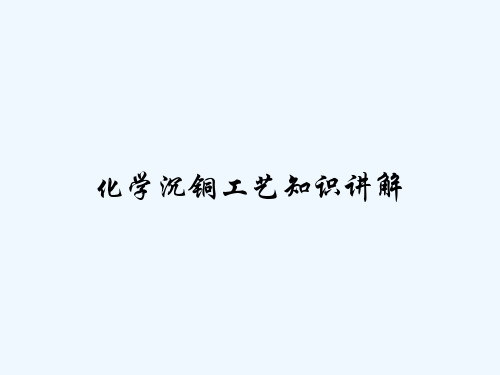
三、工艺流程简介- Plasma
2、1、2 去钻污(针对特殊板材)
去钻污主要针对得是Desmear难以去除得板材类型,包括含碳氢化合物板材、HTg板材等。
2、1、3 电镀夹膜得处理
从图可以清晰得看 出,等离子处理后得 板材可以做出三面 包夹得效果,更好得 增强了可靠性。
2、1、4 去除激光钻孔后得碳膜
三、工艺流程简介-Desmear
3、3、2 MLB 除钻污剂 214(主要成分高锰酸钾+液碱)
作用:
高锰酸钾具有强氧化性,在高温及强碱得条件下,与树脂发生化学反应 使其分解溶去。
反应原理:
4MnO4- + 有机树脂 + 4OH-
4 MnO42- + CO2 + 2H2O
附产物得生成:
KMnO4 + OH - K2MnO4 + H2O + O2
After Plating
二、工艺流程
plamsa
等离子处理
磨板
Desmear 除胶渣
Deburr 去毛刺
MLB 211膨松 Promoter 214除胶渣 Neutralizer 216 中和 Conditioner1175除油
Conditioner233调整
Electroless Copper 化学沉铜
作用:除去板子铜面上得氧化物及其它杂质。粗化铜表面,增强铜面与电解铜得齿结 能力
微蚀前
微蚀后
反应式: Cu+ S2O82- Cu2+ + 2SO42-
微蚀后铜面状况
三、工艺流程简介-沉铜工艺
微蚀中可能出现得问题: 微蚀不足:微蚀不足将导致基铜与铜镀层附着力不良、 微蚀过度:微蚀过度将导致在通孔出现反常形状(见图点A和点B)、这种情况将导致化 学铜得额外沉积并出现角裂(负凹蚀)。 槽液污染 :氯化物和有机物残渣得带入会降低蚀铜量、清洁--调整剂后需保证良好得
化学镀铜工艺流程解读

化学镀铜工艺流程解读一、背景介绍化学镀铜是一种利用化学方法在金属表面电化学镀铜的工艺。
通过镀铜可以提高金属表面的导电性、防腐性和美观性,使得金属制品在电子、电器、通信等行业得到广泛应用。
本文将对化学镀铜的工艺流程进行详细解读。
二、化学镀铜工艺流程化学镀铜的工艺流程通常包括以下几个步骤:1. 表面处理在进行化学镀铜之前,需要对金属表面进行处理,以确保金属表面的清洁和光滑度,提高镀铜层的附着力。
表面处理通常包括以下几个步骤:1.清洗:将金属制品浸泡在碱性清洗剂中,去除表面的油污和杂质。
2.酸洗:将金属制品浸泡在酸性溶液中,去除表面的氧化膜和其他氧化物。
3.中和:将金属制品浸泡在酸性溶液中,使其中和,以避免对后续步骤产生不良影响。
2. 镀铜液配制镀铜液是进行化学镀铜的关键。
镀铜液通常由铜盐、添加剂和混合溶液组成。
铜盐的选择是根据需要镀铜的金属材料来确定的。
添加剂的作用是调节镀铜液的性能,如控制镀铜速率和镀铜层的均匀性。
混合溶液则提供了电解液的基础,保持镀铜液的稳定性和酸碱平衡。
3. 镀铜过程镀铜过程是将金属制品浸泡在镀铜液中,通过电解的方式在金属表面形成一层铜镀层。
镀铜过程通常包括以下几个步骤:1.阳极准备:选择适当的铜材作为阳极,准备好铜阳极。
2.电解槽准备:将镀铜液倒入电解槽中,并将阳极和阴极安装好。
3.镀铜操作:将金属制品作为阴极放入电解槽中,通电开始镀铜过程。
通过控制电流密度和镀铜时间来控制铜镀层的厚度和均匀性。
4.检测和调整:通过周期性的检测镀铜层的厚度和质量,及时调整电流密度和镀铜时间,以确保镀铜过程和铜镀层的质量。
4. 后处理将金属制品从镀铜液中取出后,还需要进行后处理,以提高铜镀层的质量和耐腐蚀性。
后处理通常包括以下几个步骤:1.水洗:将金属制品用清水冲洗,去除残留的镀铜液。
2.烘干:将金属制品放入烘干器中,用热风或其他方式将金属制品表面的水分蒸发干净。
3.清洗:将金属制品再次浸泡在清洁溶液中,去除可能残留的污染物。
{生产工艺流程}化学镀铜工艺流程简要解读

{生产工艺流程}化学镀铜工艺流程简要解读化学镀铜是一种通过化学方法,在金属或非金属表面上沉积一层铜膜的工艺。
它通常包括以下流程:表面准备、镀前处理、镀铜、清洗、后处理和检验。
1.表面准备:在进行化学镀铜之前,首先需要对工件表面进行准备。
这一步骤的目的是去除表面的污垢和氧化物,以便能够更好地与铜液发生反应。
通常会使用化学溶剂、酸洗或表面活化剂等方法进行清洗。
2.镀前处理:在表面准备之后,工件需要进行镀前处理,以增加铜膜的附着力并提高镀层的质量。
镀前处理的方法包括磨光、电解处理和酸洗等。
磨光可以消除表面不平整,电解处理可以改善表面的电化学性质,酸洗则可以进一步清除表面的杂质和氧化物。
3.镀铜:镀铜是化学镀铜工艺的核心环节,利用电化学原理,在工件表面上沉积一层铜膜。
镀铜的过程中,需要一个含铜离子的电解液(通常为硫酸铜溶液),以及用作阳极的铜板。
工件通过电流控制被镀的时间和铜膜的厚度。
4.清洗:在完成镀铜之后,工件需要进行清洗,以除去表面残留的铜离子和电解液。
清洗一般使用水或其他合适的溶剂进行,同时还可以添加一些表面活化剂,以提高清洗效果。
5.后处理:在清洗之后,工件可以进行一些后处理步骤,以提高镀铜层的物理和化学性质。
后处理的方法包括热处理、喷漆或镀一层保护性的涂层,以增加镀铜层的耐腐蚀性和耐磨性。
6.检验:最后一步是对镀铜工件进行检验。
这一步骤是为了确保镀铜层的质量满足要求。
常见的检验方法有外观检查、厚度测量、耐蚀性测试等。
只有通过检验的工件才能进入下一个工艺环节或交付给客户使用。
总之,化学镀铜是一种常用的表面处理工艺,用于给金属或非金属表面镀上一层铜膜。
这一工艺的核心环节是镀铜,在这个过程中,需要对工件进行表面准备、镀前处理、镀铜、清洗、后处理和检验等工序。
通过这些步骤的处理,可以获得质量良好、表面光滑均匀的镀铜层,增加工件的耐腐蚀性和美观性。
镀铜工艺流程,化学镀铜工艺与电镀铜工艺的区别

镀铜工艺流程|化学镀铜工艺与电镀铜工艺的区别镀铜工艺流程镀铜工艺种类不止一种,也不是三言两语就能说清楚的,镀铜工艺特点包括了优点和缺点。
我们先来说下什么是镀铜工艺?镀铜工艺通常分为化学镀铜工艺和电镀铜工艺。
化学镀铜工艺是在有钯等催化活性物质的表面,通过甲醛等还原剂的作用,使铜离子还原析出。
化学镀铜工艺是相对于电镀铜工艺的优势主要有基体范围广泛,镀层厚度均匀,工艺设备简单,镀层性能良好等一系列优势。
电镀铜工艺,PCB制造业中,电镀铜已经应用许多年了,印制板电镀铜溶液属酸性溶液,具有高酸低铜特点,有极好的分散能力和深镀能力镀后的铜层有光泽性。
通俗的说,镀铜工艺其实是一种表面处理技术,在金属表面上镀上一薄层其它金属或合金起保护、美观的作用。
只要你需要保护的,认为有价值的,都可以给它镀上。
镀铜工艺种类1、化学镀铜工艺:是电路板制造中的一种工艺,通常也叫沉铜或孔化(PTH)是一种自身催化性氧化还原反应。
2、电镀铜工艺:用于铸模,镀镍,镀铬,镀银和镀金的打底,修复磨损部分,防止局部渗碳和提高导电性。
电镀铜工艺分为碱性镀铜和酸性镀铜二法。
电镀铜工艺也可以分为以下几个(1)氰化镀铜工艺:氰化物镀铜是应用最早和最广泛的镀铜工艺方法。
镀液主要由铜氰络合物和一定量的游离氰化物组成,呈强碱性。
(2)硫酸盐镀铜工艺:氰化物镀铜,硫酸盐镀铜工艺早期应用于塑料电镀、电铸、精饰等方面,包括装饰层和功能镀层。
在电子工业中较早的应用是印刷电路、印刷板、电子接触元件。
(3)焦磷酸盐镀铜工艺。
(4)无氰镀铜工艺:无氰镀铜工艺完全取代传统氰化镀铜工艺和光亮镀铜工艺,适用于任何金属基材:纯铜、铜合金、铁、不锈钢、锌合金压铸件、铝、铝合金工件等基材上,挂镀或滚镀均可。
镀铜工艺流程1、化学镀铜工艺步骤:膨胀→去钻污→中和→除油→微蚀→预浸→活化→加速→化学镀铜。
2、电镀铜工艺步骤:(1)氰化镀铜工艺步骤:1、浸酸→全板电镀铜→图形转移→酸性除油→二级逆流漂洗→微蚀→二级→浸酸→镀锡→二级逆流漂洗。
- 1、下载文档前请自行甄别文档内容的完整性,平台不提供额外的编辑、内容补充、找答案等附加服务。
- 2、"仅部分预览"的文档,不可在线预览部分如存在完整性等问题,可反馈申请退款(可完整预览的文档不适用该条件!)。
- 3、如文档侵犯您的权益,请联系客服反馈,我们会尽快为您处理(人工客服工作时间:9:00-18:30)。
化学镀铜/沉铜工艺流程介绍2008-1-29 来源: 中国有色网化学镀铜(Eletcroless Plating Copper)通常也叫沉铜或孔化(PTH)是一种自身催化性氧化还原反应。
首先用活化剂处理,使绝缘基材表面吸附上一层活性的粒子通常用的是金属钯粒子(钯是一种十分昂贵的金属,价格高且一直在上升,为降低成本现在国外有实用胶体铜工艺在运行),铜离子首先在这些活性的金属钯粒子上被还原,而这些被还原的金属铜晶核本身又成为铜离子的催化层,使铜的还原反应继续在这些新的铜晶核表面上进行。
化学镀铜在我们PCB制造业中得到了广泛的应用,目前最多的是用化学镀铜进行PCB的孔金属化。
PCB孔金属化工艺流程如下:钻孔→磨板去毛刺→上板→整孔清洁处理→双水洗→微蚀化学粗化→双水洗→预浸处理→胶体钯活化处理→双水洗→解胶处理(加速)→双水洗→沉铜→双水洗→下板→上板→浸酸→一次铜→水洗→下板→烘干一、镀前处理1.去毛刺钻孔后的覆铜泊板,其孔口部位不可避免的产生一些小的毛刺,这些毛刺如不去除将会影响金属化孔的质量。
最简单去毛刺的方法是用200~400号水砂纸将钻孔后的铜箔表面磨光。
机械化的去毛刺方法是采用去毛刺机。
去毛刺机的磨辊是采用含有碳化硅磨料的尼龙刷或毡。
一般的去毛刺机在去除毛刺时,在顺着板面移动方向有部分毛刺倒向孔口内壁,改进型的磨板机,具有双向转动带摆动尼龙刷辊,消除了除了这种弊病。
2 整孔清洁处理对多层PCB有整孔要求,目的是除去钻污及孔微蚀处理。
以前多用浓硫酸除钻污,而现在多用碱性高锰酸钾处理法,随后清洁调整处理。
孔金属化时,化学镀铜反应是在孔壁和整个铜箔表面上同时发生的。
如果某些部位不清洁,就会影响化学镀铜层和印制导线铜箔间的结合强度,所以在化学镀铜前必须进行基体的清洁处理。
最常用的清洗液及操作条件列于表如下:清洗液及操作条件配方组分 1 2 3碳酸钠(g/l) 40~60 ——磷酸三钠(g/l) 40~60 ——OP乳化剂(g/l) 2~3 ——氢氧化钠(g/l)— 10~15 —金属洗净剂(g/l)—— 10~15温度(℃) 50 50 40处理时间(min) 3 3 3搅拌方法空气搅拌机械移动空气搅拌机械移动空气搅拌机械移动3.覆铜箔粗化处理利用化学微蚀刻法对铜表面进行浸蚀处理(蚀刻深度为2-3微米),使铜表面产生凹凸不平的微观粗糙带活性的表面,从而保证化学镀铜层和铜箔基体之间有牢固的结合强度。
以往粗化处理主要采用过硫酸盐或酸性氯化铜水溶液进行微蚀粗化处理。
现在大多采用硫酸/双氧水(H2SO4/H202 )其蚀刻速度比较恒定,粗化效果均匀一致。
由于双氧水易分解,所以在该溶液中应加入合适的稳定剂,这样可控制双氧水的快速分解,提高蚀刻溶液的稳定性使成本进一步降低。
常用微蚀液配方如下:硫酸H2SO4 150~200克/升双氧水H202 40~80毫升/升常用稳定剂如下:稳定剂化合物添加量蚀刻铜速率双氧水H202分解率C2H5NH 2 10g/l 28% 1.4mg/l.minn-C4H9NH2 10ml/l 232% 2.7 mg/l.minn-C8H17NH2 1 ml/l 314% 1.4mg/l.minH2NCH2NH2 10g/l 2.4 mg/l.minC2H5CONH2 0.5 g/l 98% /C2H5CONH2 1 g/l 53% /不加稳定剂 0 100% 快速分解我们以不加稳定剂的蚀刻速率为100%,那么蚀刻速率大于100%的为正性加速稳定剂,小于100%的为负性减速稳定剂。
对于正性的加速稳定剂不用加热,在室温(25度C)条件下就具有较高的蚀刻速度。
而负性减速稳定剂,必须加热使用才能产生微蚀刻铜的效果。
应注意新开缸的微蚀刻液,开始蚀刻时速率较慢,可加入4g/l硫酸铜或保留25%的旧溶液。
二、活化活化的目的是为了在基材表面上吸附一层催化性的金属粒子,从而使整个基材表面顺利地进行化学镀铜反应。
常用的活化处理方法有敏化—活化法(分步活化法)和胶体溶液活化法(一步活化法)。
1.敏化-活化法(分步活化法)(1)敏化处理:常用的敏化液是氯化亚锡的水溶液。
其典型配方如下:氯化亚锡(Sncl2.2H2O)30~50g/L盐酸50~100ml/L锡粒3~5g/l配制时先将水和盐酸混合,然后加入氯化亚锡边搅拌使其溶解。
锡粒可防止Sn2+氧化。
敏化处理在室温下进行,处理时间为3~5min,水洗后进行活化处理。
(2)活化处理:常用的离子型活化液是氯化钯的溶液,其典型配方如下:氯化钯pdCl20. 5~1g/L盐酸5~10ml/L处理条件-室温,处理1~2min敏化-活化法的溶液配制和操作工艺简单,在早期的印制板孔金属化工艺中曾得到广泛应用。
这种方法有二个主要缺点:一是孔金属化的合格率低,在化学镀铜后总会发现有个别孔沉不上铜,其主要有二个方面的原因,其一是Sn+2离子对环氧玻璃的基体表面湿润性不是很强,其二是Sn+2很易氧化特别是敏化后水洗时间稍长,Sn+2被氧化为Sn+4,造成失去敏化效果,使孔金属化后个别孔沉不上铜。
二是化学镀铜层和铜箔的结合力差,其原因是在活化过程中,活化液中贵金属离子和铜箔间发生置换反应,在铜表面上形成一层松散的金属钯。
如果不去除会影响沉铜层和铜箔间的结合强度。
在多层连接以及图形电镀法工艺中,这种缺陷已经成为影响印制板质量主要矛盾,现在是用螯合离子钯分步活化法来解决这些问题.胶体钯活化法(一步活化法)(1)配方:常用的胶体钯活化液配方列于表采用胶体钯活化液能消除铜箔上形成的松散催化层,而且胶体钯活化液具有非常好的活性,明显地提高了化学镀铜层的质量,因此,在PCB的孔金属化工艺中,得到了普遍应用。
表中的配方1是酸基胶体钯,由于其盐酸含量高,使用时酸雾大且酸性太强对黑氧化处理的多层内层连接盘有浸蚀现象,在焊盘处易产生内层粉红圈。
活化液中钯含量较高,溶液费用大,所以已很少采用。
配方2是盐基胶体钯。
在盐基胶体钯活化液中加入尿素,可以和Sn2+O‖形成稳定的络合物[H2NCNH3]SC1-3,防止了活化剂产生沉淀,明显地降低了盐酸的挥发和Sn2+离子的氧化,从而提高了胶体钯活化液的稳定性。
(2)胶体钯活化液的配制方法a.酸基胶体钯活化液—称取1g氯化钯溶解于100ml盐酸和200ml纯水的混合液中,并在恒温水浴中保持30℃,边搅拌边加入氯化亚锡(SnCl2•2H2O)2.54g搅拌12min,然后再与事先配制好的氯化亚锡60g、盐酸200ml和锡酸钠7g的混合液溶解在一起,再在45℃的恒温水浴条件下保温3h,最后用水稀释至1L即可使用。
b.盐基胶体钯活化液-称取氯化钯0.25g,加入去离子水200ml,盐酸10ml,在30℃条件下搅拌,使氯化钯溶解。
然后加入3.2g氯化亚锡并适当搅拌,迅速倒入事先配制好的含有尿素50g、氯化钠250g、锡酸钠0.5g和水800mL的混合溶液中,搅拌使之全部溶解,在45℃条件下保温3h,冷至室温,用水稀释至1L。
(3)胶体钯处理工艺:采用胶体钯活化液按下述程序进行:预浸处理→胶体钯活化处理→水洗→解胶处理→水洗→化学镀铜→a.预浸处理-经过粗化处理的覆铜箔板,如果经水洗后直接浸入胶体钯活化液中进行活化处理,将会使活化液中的含水量不断增加,造成胶体钯活化液过早聚沉。
因此,在活化处理前要先在含有Sn2+的酸性溶液中进行预浸处理1~2min,取出后直接浸入胶体钯活化液中进行活化处理。
配制时应首先将盐酸与水相混合,然后再加入SnCl2•2H2O ,搅拌溶解,这样可防止SnCl2水解。
酸基胶体钯预浸液配方:氯化亚锡(SnCl2.2H2O) 70~100g/L盐酸37%(体积) 200-300ml/L盐基胶体钯预浸液配方:SnCl2.2H2O 30g/LHCl 30ml/lNaCl 200g/lO║H2N-C-NH2 50g/lb.活化处理-在室温条件下处理3~5min,在处理过程中应不断移动覆铜箔板,使活化液在孔内流动,以便在孔壁上形成均匀的催化层。
c.解胶处理-活化处理后,在基材表面吸附着以钯粒子为核心,在钯核的周围,具有碱式锡酸盐的胶体化合物。
在化学镀铜前,应将碱式锡酸盐去除,使活性的钯晶核充分暴露出来,从而使钯晶核具有非常强而均匀的活性。
经过解胶处理再进行化学镀铜,不但提高了胶体钯的活性,而且也显著提高化学镀铜层与基材间的结合强度。
常用的解胶处理液是5%的氢氧化钠水溶液或1%氟硼酸水溶液。
解胶处理在室温条件下处理1~2min,水洗后进行化学镀铜。
d.胶体铜活化液简介:明胶2g/lCuSO4.5H2O 20g/lDMAB(二甲胺基硼烷)5g/l水合肼10 g/l钯20ppmPH 7.0配制过程:首先分别将明胶和硫酸铜用温水(40度C)溶解后将明胶加入至硫酸铜的溶液中,用25%H2SO4将PH值调至2..5当温度为45度C时,将溶解后DMAB在搅拌条件下缓慢加入上述的混合溶液中,并加入去离子稀释至1升,保温40~45度C,并搅拌至反应开始(约5~10分钟)溶液的颜色由蓝再变成绿色。
放置24小时颜色变成红黑色后加入水合肼,再反应有24小时后胶体溶液的PH值为7,就可投入使用。
为了提高胶体铜的活性,通常再加入少量的钯。