炉温测试板制作及曲线测试规范
炉温曲线的管理规范

炉温曲线的管理规范炉温曲线的管理规范1.目的:为了能正确测量炉温曲线,提高产品的焊接质量,并保存曲线文档,以便后续生产需要进行调用。
2.测温板的申请:新品在DVT2阶段,申请1块空PCB板和2套物料。
3.测温板制做和曲线设定:新品的测温板和曲线设定都由试产工程师完成。
3.1测温板的制做:3.1.1测温板选取测温点:(1)测温点数量必须制作3-5个测温点。
(2)结合重要元器件的温度特性。
(3)元件的分布状况。
3.1.2焊接测温点:(1)焊接材料:必须用高温焊锡丝,不能用普通焊锡丝。
(2)焊接点:焊点应完全把热电偶的测温点裹住,而不要让它一部分曝露在外面;在保证测温点裹住的前提下应尽量使焊接点小。
3.1.3红胶固定:(1) 固定点数量:至少必须制作2个固定点。
(2) 固定点位置:第一个固定点在离测温点的0.5CM处,第二个固定点在离测温点2CM 处。
3.1.4高温胶带固定:(1) 热电偶测试线必须整齐,不能胡乱堆叠。
(2)用高温胶把热电偶测试线整齐固定在测温板上。
4.测温板的管理:由技术组长统一保管;如有坏板,请反馈给量产工程师。
5.测试方法和要求:请参考测量回温曲线作业指导书。
6.炉温曲线的判断和保存:请参考各产品的作业指导书-----焊前检验2。
6.1如测量出来的炉温曲线符合各产品的作业指导书要求,请存档d:/TEST/产品名称+日期,并在当班后用邮件的方式发给江苹苹统一保存;如江苹苹第二天早上没有收到邮件,要求当班技术员在第二天早会后补发。
6.2如测量出来的炉温曲线不符合各产品的作业指导书要求,请重新测量: a. 如再一次测量出来的炉温曲线符合各产品的作业指导书要求,同5.1。
b.如再一次不符合各产品的作业指导书要求,判断测温板是否坏了,用另一块平台的测温板再测量一次。
如果NG,请反馈给量产工程师,由量产工程师制做测温板并调整曲线设定。
注意事项:1. PROFILE曲线以保证产品品质为第一前提。
波峰焊炉温曲线测试板制作指导书
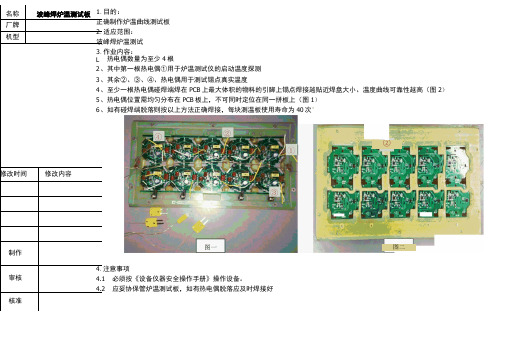
目的:
适应范围:
作业内容:
热电偶数量为至少4根
其中第一根热电偶①用于炉温测试仪的启动温度探测
其余②、③、④、热电偶用于测试锡点真实温度
至少一根热电偶碰焊端焊在PCB上最大体积的物料的引脚上锡点焊接越贴近焊盘大小、温度曲线可靠性越高(图2)热电偶位置需均匀分布在PCB板上,不可同时定位在同一拼板上(图1)
如有碰焊端脱落则按以上方法正确焊接,每块测温板使用寿命为40次°
必须按《设备仪器安全操作手册》操作设备。
应妥协保管炉温测试板,如有热电偶脱落应及时焊接好②
图二。
炉温测试板制作及曲线测试规范
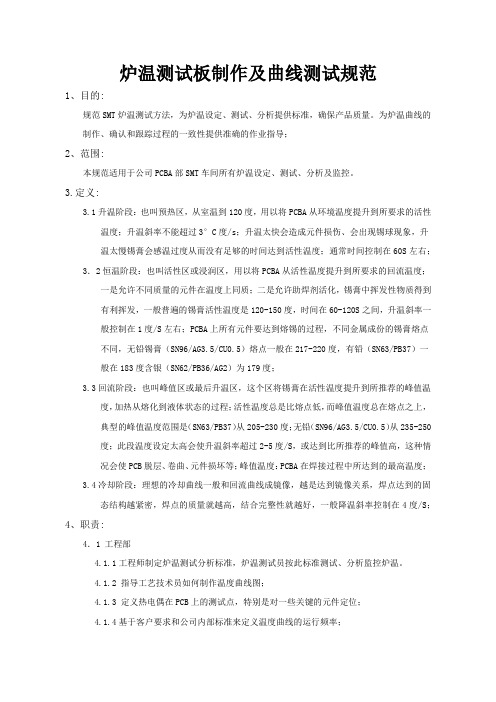
炉温测试板制作及曲线测试规范1、目的:规范SMT炉温测试方法,为炉温设定、测试、分析提供标准,确保产品质量。
为炉温曲线的制作、确认和跟踪过程的一致性提供准确的作业指导;2、范围:本规范适用于公司PCBA部SMT车间所有炉温设定、测试、分析及监控。
3.定义:3.1升温阶段:也叫预热区,从室温到120度,用以将PCBA从环境温度提升到所要求的活性温度;升温斜率不能超过3°C度/s;升温太快会造成元件损伤、会出现锡球现象,升温太慢锡膏会感温过度从而没有足够的时间达到活性温度;通常时间控制在60S左右;3.2恒温阶段:也叫活性区或浸润区,用以将PCBA从活性温度提升到所要求的回流温度;一是允许不同质量的元件在温度上同质;二是允许助焊剂活化,锡膏中挥发性物质得到有利挥发,一般普遍的锡膏活性温度是120-150度,时间在60-120S之间,升温斜率一般控制在1度/S左右;PCBA上所有元件要达到熔锡的过程,不同金属成份的锡膏熔点不同,无铅锡膏(SN96/AG3.5/CU0.5)熔点一般在217-220度,有铅(SN63/PB37)一般在183度含银(SN62/PB36/AG2)为179度;3.3回流阶段:也叫峰值区或最后升温区,这个区将锡膏在活性温度提升到所推荐的峰值温度,加热从熔化到液体状态的过程;活性温度总是比熔点低,而峰值温度总在熔点之上,典型的峰值温度范围是(SN63/PB37)从205-230度;无铅(SN96/AG3.5/CU0.5)从235-250度;此段温度设定太高会使升温斜率超过2-5度/S,或达到比所推荐的峰值高,这种情况会使PCB脱层、卷曲、元件损坏等;峰值温度:PCBA在焊接过程中所达到的最高温度;3.4冷却阶段:理想的冷却曲线一般和回流曲线成镜像,越是达到镜像关系,焊点达到的固态结构越紧密,焊点的质量就越高,结合完整性就越好,一般降温斜率控制在4度/S;4、职责:4.1 工程部4.1.1工程师制定炉温测试分析标准,炉温测试员按此标准测试、分析监控炉温。
炉温测试板制作及测试标准

1.目的为制作炉温测试板和测试炉温提供正确的方法和依据,使精密电子部炉温板制作及测试作业标准化,确保炉温符合产品品质要求。
2.适用范围适用公司精密电子部回流炉测温板制作及炉温测试作业。
3.定义无4.权责4.1 精密电子工程部4.1.1负责本规范文件制定及完善,并严格按此规范进行操作。
4.1.2负责根据生产需求制作对应机型的测试板及炉温测试。
4.1.3负责炉温测板的报废评估及炉温曲线优化,保证产品质量。
5.程序5.1测试点的位置选取原则5.1.1测试点位置选取,测试板要求选取PCB上5个测试点,需注意第一通道需超出PCB 2.5CM 左右。
5.1.2结合PCB板元件的温度特性,一般选取的点需要覆盖大中小执容量的元件。
5.2测试点选取类型5.2.1胶水板测试点选取:PCB两端的透镜上各选取1点,PCB两端的透镜引脚边各1点,PCB中间位置选取1点。
※修订履历※变更日期变更版本变更内容5.2.2锡膏板测试点选取:插座引脚PAD上选取1点,PCB中间LED PAD上选取1点,另外3点选取在PCB三个角上离PCB板边20MM左右位置的LED PAD上。
5.3测温点的制作方法5.3.1用少量的高温锡线将测温线头焊接在元件引脚与PAD间接触的区域,焊点应完全把热电偶测温点包裹住(或用胶水),不允许一部分曝露在外面。
在保证测温点裹住的情前提下,尽量使测试点体积小不可过大。
5.3.2为了防止测温线松动,用高温胶把热电偶测试线整齐固定在测温板上,热电偶测试必须整齐,不能打结或缠绕。
5.4测温板的报废处理判定方法5.4.1测温板外观判定,若测温板上的油墨变色或掉落等现象,测温板测需要做报废处理。
5.4.2测试板首次使用需在测试板上标示使用日期,若出现两组以上高温与首次测试值差异大于7℃时,测温板则需要做报废处理。
6.测试的频率6.1更换机种、载板治具时必测6.2连续生产(相同产品)每天测一次6.3新产品必测6.4炉后测试出现异常时必测6.5当炉温有异常时要重新测量7.测试作业流程7.1根据所测试生产工艺选择所需的测试板(如图1-图2)图1:无铅锡膏测试用测试板图2:热固胶用测试板(需加当前过炉的载板治具)7.2打开炉温测试软件,点击开始测试炉温曲线。
波峰焊炉温曲线测试规
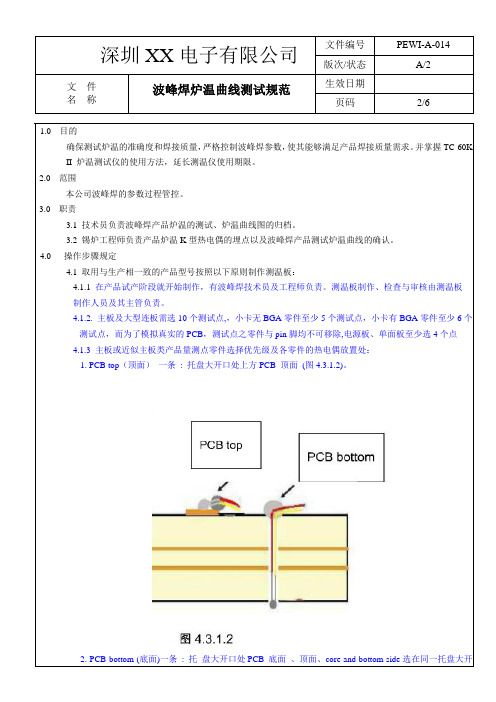
文件名称波峰焊炉温曲线测试规范生效日期页码3/6口处,并以少量红胶固定于PCB上(图4.3.1.2)。
测温端点皆不可以被定位红胶黏着覆盖。
(图4.3.1.2)。
3. 电解电容通孔一条: 选择电容负脚,测温点放置在负极通孔内部,且不可露出板面,如无则选择,则选择通孔零件的地脚。
4. Dwell time(触锡时间):靠近PC板中央托盘大开孔处钻孔(孔径约1.0mm),测温点需突出底面板面约1~1.5mm。
5. 选择最靠近托开孔的2颗BGA各一条, 量测点放置在距离托开孔较近处,需选择信号焊盘埋设。
6. DIMM区域一条: 于托架大开孔区(建议优先选取DIMM的位置)顶面选一连接大铜箔的贴片焊盘,可将零件移除用高温锡丝将测温端点焊于焊盘上。
(图4.3.1.2.7)7. 电解电容电解电容本体表面一条,测温端点以高温锡丝焊接于电解电容上方表面并以少量红胶(<0.4MM见方)进行固定,若板上无电解电容时则可不测。
(图4.3.1.2.8).8. 选择托开孔上方或最靠近托开孔的顶面SMT 区域,如QFP或SOP零件,需选择其一,使用高温锡丝将测温端点焊接于一支信号焊盘与零件脚中间,参考图4.2.1.2.2。
文件名称波峰焊炉温曲线测试规范生效日期页码5/64.5 用鼠标点击桌面“O-DA TAPRO”,输入效验码6个8,分别输入产品信息。
(客户、产品型号,线别、温区数量及温度、链条速度等等)4.6 将数据下载线与TC-60K II连接,点击“下载”等待下载完后关闭电源开关,提取产品温度曲线,并打印存档。
(保存在电脑指定位置,便于追溯)4.7 根据5.0项的要求分析产品温度曲线是否在标准范围内,如果产品参数测试不合格,依据标准参数重新设置波峰焊产品参数,待温度稳定后按4.10-4.12步骤重新设置测试,直到产品参数测试合格后方可以过炉生产。
4.8 产品在波峰焊接中如果出现有空焊、连锡不良时,应重新制定产品曲线参数。
炉温测试板制作及测试作业规范

FS FS/M-SMT-E-009A REV.0-2016.01.08保密级别:内部公开炉温测试板制作及测试作业规范1.0目的为制作炉温测试板和测试炉温提供正确的方法和依据,使SMT炉温板制作及测试作业标准化,确保炉温符合产品品质要求。
2.0范围适用公司SMT回流炉测温板制作及炉温测试作业。
3.0权责3.1SMT工程部3.1.1负责本规范文件制定及完善,并严格按此规范进行操作。
3.1.2负责根据生产需求制作对应机型的测试板及炉温测试。
3.1.3负责炉温测板的报废评估及炉温曲线优化,保证产品质量。
3.3品质部3.3.1负责监督炉温测试板的制作确认及使用寿命监控。
3.3.2负责监督每日炉温测试及温度曲线确认检查。
4.0程序4.1测试点的位置选取原则4.1.1测试点位置选取,手机主板要求选取6个测试点,需注意感温线的接线端正负不可接反。
4.1.2结合PCB板元件的温度特性,一般选取的点需要覆盖大中小执容量的元件。
4.1.3依照PCB板元件组件的分布,选点需平均分配覆盖PC板面区域。
4.2测试点选取类型4.2.1BGA类元件正中央底(如图1“●”标示),从PCB板背面打孔把探头埋入BGA底部。
4.2.2QFN类元件元件正中央接地焊盘(如图2“●”标示)从PCB板背面打孔把探头埋入元件底部或四边的引脚焊盘。
4.3.3USB、耳机、卡座和屏蔽盖类大热容量元件容易冷焊的元件都需要测试点,如下图“●”标示。
屏蔽盖CHIP类元件4.3测温线的制作4.3.1采用镍铬-镍铝热电偶感温线。
4.3.2每根感温线的长度为20-30cm,最长不超过30cm.4.3.3测温线测点端接头分开后,必须用点焊机熔接成一个结点,不允许用扭绞方式,测试点不能出现交叉的现象。
如下图示4.3.4测试线另一端连接测温头,镍铬端(有条细红线缠绕)接测温头的正极,另一根接测温头的负极(如图示)4.4测温点的制作方法4.4.1BGA元件从元件的背面打孔,将感温线穿过孔,将测温线穿过钻孔把探头埋在BGA元件底部,然后用红胶对BGA元件四边进行固定,并封堵钻孔。
测温板制作规范

1.目的制定测温板制作标准规范,供相关人员进行学习或作为制作测温板的依据.。
2.范围2.1 自动化所有测温板。
2.2 自动化工程技术人员。
3.定义3.1 自动化部门。
3.2 适用于本公司自动化回流焊温度测量管控.4.职责自动化技术员负责产品profile测量,测温板的制作/维护,曲线的管理,profile标准的制定,profile的检查,优化和审批。
生产部:负责反馈不良状況给技术人员,以便及时改善炉溫。
质管部:负责定期监控炉温设置状况,保证制程稳定。
5.回流焊测温板制作5.1测温板的申请与制作要求:5.1.1测温板由产线向仓库申请、工程制作测温板。
5.1.2客户有要求按客户要求制作;在客户没有特别要求的情况下可选用导热胶,红胶或高温锡丝作为测温点固定材料。
5.1.3测温线的种类为:Type K Ni-Cr合金vs.Ni-Al合金-200℃~1250℃,直径≤0.254mm。
5.1.4测温点制作,焊接大小为测温点高度≤2.5mm,长宽≤5mm。
5.1.5引脚类元件测温点必须平贴PCB板,与元件引脚相连,如下图一5.1.6若有BGA类元器件测温点必须紧贴在所取得的焊点上,如下图二5.1.7测温点的标志位置需与profile图显位置一致。
5.1.8测温点做好后,要等导热胶或红胶完全烘干后才能使用,且在烘干过程中不可碰到测温板和测温线,避免测温线头与测温点之间松脱,影响导热效果.5.1.9测温线不可断裂,不可将两根导线扭在一起。
如下图:5.1.10导线与插头连接,将导线依据板子尺寸大小选择长度,拨去绝缘皮约6mm用丝刀固定连接到插头上,红色连接到负极,黄色连接到正极,不可接反,如下图所示:5.1.11高温胶带应该固定热电偶绝缘外皮部分,不应该盖住热电偶探头5.1.12红胶用于填充孔和绑定热电偶线,但不可过多(直径≤ 5mm)以至于影响温度测量的准确性。
5.1.13保证测量空气的热电偶探头距离PCBA边缘2.5cm 左右,PCBA和温度记录仪之间至少保持20cm 的距离。
波峰焊炉温曲线设定规范

工程管理波峰焊炉温曲线设定规范PAGE4 OF5 REV A6.5.4.1使用有铅系列焊锡(Sn63/Pb37)炉温Profile 的如下:Solder peak temperature : 220- 245℃Preheat completed temperature: 80-120℃ Preheat Time (Temperature from80℃ to 120℃): 50-100 sec Soak Time (Temperature above 183℃): 2-9 sec6.5.5 炉温稳定性曲线测试:对各线波峰焊用标准测试样板及标准Profile 测量波峰焊炉的炉温, 测出的Profile 与 标准Profile (如附件二所示)进行比较, Solder peak temperature deviation < 5℃ Preheat completed temperature deviation < 5℃Solder Time (Temperature abov e 183℃) deviation < 2 sec如果偏差值在以上范围内﹐证明此炉稳定, 可量产用﹔若不符合标准, 及时通知设备工程师确认6.5.6 若对波峰焊炉有重大的维修, 维修后则重复6.5.5 6.6标准测试样板炉温曲线Profile 量测规定:6.6.1 每周一次用标准测试样板对各波峰焊炉以标准炉温参数测量.6.6.2 测定完成后将炉温曲线打印出来, 经由主管确认符合规格后置于对应的波峰焊炉上即可正常生产6.6.3所有的炉温曲线图应保存在规定的文件夹和计算机指定的地方存盘以利备查, 炉温曲线 6.7备注:Preheat Solder soakSolder peak TempPreheat completed Temp。
- 1、下载文档前请自行甄别文档内容的完整性,平台不提供额外的编辑、内容补充、找答案等附加服务。
- 2、"仅部分预览"的文档,不可在线预览部分如存在完整性等问题,可反馈申请退款(可完整预览的文档不适用该条件!)。
- 3、如文档侵犯您的权益,请联系客服反馈,我们会尽快为您处理(人工客服工作时间:9:00-18:30)。
炉温测试板制作及曲线测试规范
1、目的:
规范SMT炉温测试方法,为炉温设定、测试、分析提供标准,确保产品质量。
为炉温曲线的制作、确认和跟踪过程的一致性提供准确的作业指导;
2、范围:
本规范适用于公司PCBA部SMT车间所有炉温设定、测试、分析及监控。
3.定义:
3.1升温阶段:也叫预热区,从室温到120度,用以将PCBA从环境温度提升到所要求的活性
温度;升温斜率不能超过3°C度/s;升温太快会造成元件损伤、会出现锡球现象,升
温太慢锡膏会感温过度从而没有足够的时间达到活性温度;通常时间控制在60S左右;
3.2恒温阶段:也叫活性区或浸润区,用以将PCBA从活性温度提升到所要求的回流温度;
一是允许不同质量的元件在温度上同质;二是允许助焊剂活化,锡膏中挥发性物质得到
有利挥发,一般普遍的锡膏活性温度是120-150度,时间在60-120S之间,升温斜率一
般控制在1度/S左右;PCBA上所有元件要达到熔锡的过程,不同金属成份的锡膏熔点
不同,无铅锡膏(SN96/AG3.5/CU0.5)熔点一般在217-220度,有铅(SN63/PB37)一
般在183度含银(SN62/PB36/AG2)为179度;
3.3回流阶段:也叫峰值区或最后升温区,这个区将锡膏在活性温度提升到所推荐的峰值温
度,加热从熔化到液体状态的过程;活性温度总是比熔点低,而峰值温度总在熔点之上,
典型的峰值温度范围是(SN63/PB37)从205-230度;无铅(SN96/AG3.5/CU0.5)从235-250
度;此段温度设定太高会使升温斜率超过2-5度/S,或达到比所推荐的峰值高,这种情
况会使PCB脱层、卷曲、元件损坏等;峰值温度:PCBA在焊接过程中所达到的最高温度;
3.4冷却阶段:理想的冷却曲线一般和回流曲线成镜像,越是达到镜像关系,焊点达到的固
态结构越紧密,焊点的质量就越高,结合完整性就越好,一般降温斜率控制在4度/S;
4、职责:
4.1 工程部
4.1.1工程师制定炉温测试分析标准,炉温测试员按此标准测试、分析监控炉温。
4.1.2 指导工艺技术员如何制作温度曲线图;
4.1.3 定义热电偶在PCB上的测试点,特别是对一些关键的元件定位;
4.1.4基于客户要求和公司内部标准来定义温度曲线的运行频率;
4.1.5 认可和审核炉温曲线图;
4.2 品质部
4.2.1首片确认回流焊的参数设置(可根据公司标准核对),并对曲线进行认可;
4.2.2IPQC定期监控炉温设置状况,保证生产过程中品质的稳定。
4.3 制造部
4.3.1炉温测试员及时反馈不良状况给工程师,以便及时改善炉温设定。
4.3.2炉前目检人员定时确认回流焊温度设定是否有更改;
5.程序:
5.1、测试环境:15℃~30℃。
5.2、测试时间:每班一次(换线或其它异常情况例外)。
5.3、测试工具和材料准备:
5.3.1高温焊锡线(250-300℃)
5.3.2高温胶水或贴片红胶
5.3.3热电偶(耐温350℃)
5.3.4恒温电烙铁(300-350℃)
5.3.5测试电路板(使用已贴装元件的PCB板)
5.3.6炉温测试仪(误差范围:±1℃)
5.4、测试板放置方向及测试状态:
5.4.1测试板流入方向有要求:以贴装进板方向为准。
5.4.2测试板流入方向无要求:定位孔靠向回焊焊操作一侧水平垂直放入履带中间。
5.4.3 若回焊炉中央有支撑物体时,测温时空载测试。
若回焊炉中央无支撑物体时,测
温时以满载测试。
5.5.测试点的选取
5.5.1研发有指定选取测试点的板必须使用客户指定的测试点进行炉温测试.
5.5.2研发没有指定选取测试点的板,选取测试点必须遵循以下要求:
5.5.2.1至少选取三个点作为测试点,有BGA时BGA测试点不少于两点,测试BGA锡
球和BGA表面温度各一点。
有QFP时在QFP引脚焊盘上选取一点测试QFP
引脚底部温度,最后一点测试PCB表面温度或CHIP零件温度。
若PCB上有
几个QFP,优先选取较大的为测试点。
5.5.2.1.1 PCBA 为100个点以下,则测温板只需选择三个点。
此三点选取必须符
合5.5.2.1规定,且元件少的基板选点隔离越远越好。
对于SMT贴片零件
多的基板,应从BGA﹑QFP﹑PLCC﹑SOP、SOJ﹑SOT﹑DIODE﹑CHIP顺序选择
测试点。
5.5.2.1.2 PCBA为100个点以上,分以下两种状况:
A: PCBA 上有QFP ,但无BGA的PCB板,测温板只需选择四个点。
其中大IC 及小IC各一点,有电感及高端电容必须选取,选点方式越近越好。
B: PCBA 上既有QFP又有BGA 的PCB板,测温板必须选择五个点以上,选点方式应选择零件较密的中心位置的点来测试。
5.5.2.2 若有一些特殊材料,在选取测试点时,必须优先考虑在此材料焊盘上选取
测试点,以确保该材料的焊接效果.
5.5.2.3 回流焊测温引线固定的焊接点的大小必须在:L=3-5mm,W=2-4mm﹐违者需
要重新焊接,在不影响牢固性及温度的状态下,焊点大小越小越好。
5.5.2.4 固定测温引线的材料必须是:380度以上的高温锡丝,贴片红胶或高温胶
水固定,为保证其焊接的牢固性及温度的准确性,没有经试验的材料不可
以使用。
5.6.监控:
5.6.1炉温测试员每次测试出的炉温曲线经过工程师确认和核准后,炉温曲线才生效。
5.6.2 IPQC对炉温测试员每次测试出的炉温曲线进行检查,如果不符合则要求炉温测试
员必须重新调整和测试,直到合格才能正常使用。
5.7.温度的设定标准
5.7.1客户有要求时,以客户提供的曲线为准
5.7.2客户无要求时,则按如下要求设定
5.7.2.1锡膏焊接工艺
A:升温区(T1)(30~130℃)升温速率保持在2.5℃/S以下。
B:预热区(T2)最低温度130℃,最高温度170℃,要求时间维持在60秒~120秒之间。
C:回流区183℃以上,维持在45秒~90秒。
而且200℃以上的时间维持在20
秒~60秒。
D:顶峰温度为:210~240℃,时间维持在20秒~60秒。
E:有BGA、QFP、IC时,BGA内部温度210-220℃,表面温度为210~230℃。
F:降温区(顶峰温度130℃)降温速率保持在:有铅产品3℃/S以下、无铅产品2℃
/S -4℃/S之间内来设置。
G:冷却区温度设置,设定为100-125℃之间,超越无显示实际温度﹐为自动控制系统。
备注:以上标准时间及温度,除元件少(1-20点)或FR-1材质外,其余必须遵照执行。
5.7.2.1红胶固化工艺
通常加热需过100摄氏度,一般在120摄氏度以上保持90-180秒;150摄氏度保持有60-90秒,峰值温度不能超过160摄氏度;
5.8.异常处理
5.8.1当温度过高或过低和温区间的时间不符合分析标准,必须马上停止过板。
待工程
师重新设定炉温后,炉温测试员温度重新测试,OK后方可继续过板﹐对之前过的
板进行质量追踪。
5.9.注意事项
5.9.1炉温测试员在进行测试作业时,必须佩戴静电手套和无线静电环作业,需要拿板
子时,必须拿板边,不可拿板面。
5.9.2如有不明之处,请咨询工程师。
5.9.3回焊炉温度参数设定误差值为±10℃,温度设定值及实际值都可以在与回焊炉联
机之计算机上读出。
回焊炉链条速度由工程师根据不同产品设定,其回焊炉链条
速度都可于计算机上读出设定值及实际值,实际值高出回焊炉的内部已设定实际
链速为设定链速±3mm/min。
5.9.4每次新机种试产测出合格的Profile曲线之后,再连续测5次﹐检测回焊炉的
稳定性。
5.9.5如果客户提供Profile曲线,则根据Profile曲线调试炉温。
如果客户没有提供
A Profile曲线,则根据锡膏成份的要求调试炉温。
调整OK后的炉温及链条速度,
填写在「回焊炉参数设定参考表」及「炉温测试报表」中。
5.9.6当材质﹑制程有变更需要参数版本升级时﹐必须填写「温度修改履历表」。
6.附件:
6.1「回焊炉参数设定参考表」
6.2「炉温测试报表」
6.3「回流焊温度曲线监控记录表」。