[汽车零件]汽车零件注塑生产的应用与实践
注塑工艺在汽车零部件制造中的应用

注塑工艺在汽车零部件制造中的应用注塑工艺在汽车零部件制造中的应用汽车零部件制造是汽车工业中至关重要的一部分,注塑工艺作为一种先进而有效的制造方法,在汽车零部件制造中发挥着重要作用。
本文将从注塑工艺的定义、优势以及在汽车零部件制造中的应用等方面进行探讨。
首先,注塑工艺是一种将熔化的塑料材料注入到模具中,通过冷却和固化来制造成型的工艺。
相比传统的制造方法,注塑工艺具有以下几个优势。
首先,注塑工艺可以实现高效生产,通过自动化设备和流水线生产,大大提高了生产效率。
其次,注塑工艺可以制造出形状复杂的零部件,模具可以根据设计要求进行定制,使得产品的制造更加灵活多样化。
此外,注塑工艺还可以实现材料的节约和回收利用,减少了资源浪费和环境污染。
在汽车零部件制造中,注塑工艺的应用广泛而深入。
首先,汽车内饰件的制造离不开注塑工艺。
例如汽车座椅、仪表盘、车门内饰板等零部件,通过注塑工艺可以制造出形状精确、表面光滑的产品,提升了汽车内饰的品质和舒适性。
其次,汽车外观件的制造也离不开注塑工艺。
例如汽车前后保险杠、车灯外壳等零部件,注塑工艺可以制造出具有良好外观质量和抗撞击性能的产品,提高了汽车的安全性和美观性。
此外,注塑工艺还可以应用于汽车动力系统和悬挂系统等零部件的制造,提高了汽车的性能和可靠性。
然而,注塑工艺在汽车零部件制造中也面临一些挑战和难题。
首先,材料选择是一个重要的问题。
汽车零部件需要具备耐高温、耐磨损、耐化学腐蚀等特性,因此需要选择适合的塑料材料。
其次,模具设计和制造也是一个关键环节。
汽车零部件的形状复杂多样,模具需要具备高精度和高耐用性,因此需要投入大量的研发和制造成本。
此外,注塑工艺还需要进行合理的工艺参数设计,以确保产品的质量和性能。
总之,注塑工艺在汽车零部件制造中发挥着重要作用。
通过提高生产效率、制造形状复杂的零部件以及实现材料的节约和回收利用等优势,注塑工艺为汽车零部件的制造提供了先进而有效的方法。
汽车注塑模具基础知识
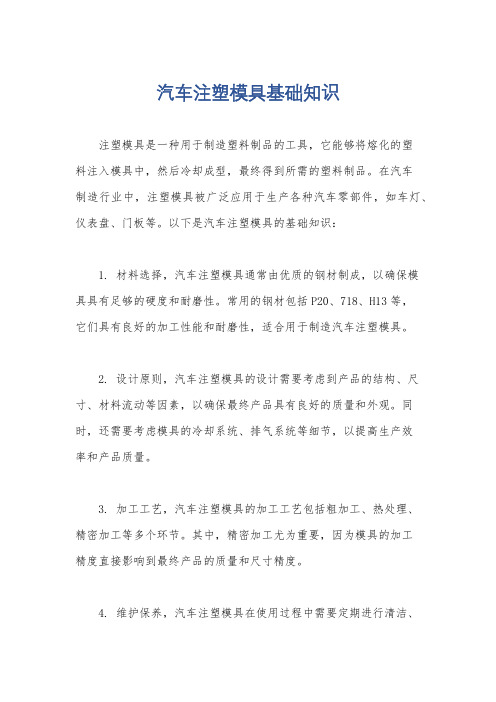
汽车注塑模具基础知识
注塑模具是一种用于制造塑料制品的工具,它能够将熔化的塑
料注入模具中,然后冷却成型,最终得到所需的塑料制品。
在汽车
制造行业中,注塑模具被广泛应用于生产各种汽车零部件,如车灯、仪表盘、门板等。
以下是汽车注塑模具的基础知识:
1. 材料选择,汽车注塑模具通常由优质的钢材制成,以确保模
具具有足够的硬度和耐磨性。
常用的钢材包括P20、718、H13等,
它们具有良好的加工性能和耐磨性,适合用于制造汽车注塑模具。
2. 设计原则,汽车注塑模具的设计需要考虑到产品的结构、尺寸、材料流动等因素,以确保最终产品具有良好的质量和外观。
同时,还需要考虑模具的冷却系统、排气系统等细节,以提高生产效
率和产品质量。
3. 加工工艺,汽车注塑模具的加工工艺包括粗加工、热处理、
精密加工等多个环节。
其中,精密加工尤为重要,因为模具的加工
精度直接影响到最终产品的质量和尺寸精度。
4. 维护保养,汽车注塑模具在使用过程中需要定期进行清洁、
润滑、修复等维护工作,以延长模具的使用寿命和保证生产的稳定性。
总的来说,汽车注塑模具是汽车制造过程中不可或缺的重要工具,它的质量和性能直接关系到汽车零部件的质量和生产效率。
因此,对汽车注塑模具的基础知识的掌握和应用是非常重要的。
注塑模具用途

注塑模具用途注塑模具是一种工业用的设备,广泛应用于制造各种塑料产品,如手机外壳、纺织品用品、家电外壳、汽车零件等。
注塑模具的主要功能是实现塑料制品的量产,样式和质量稳定,从而满足市场的需求。
注塑模具在现代工业生产中的作用越来越重要,下面详细介绍一下注塑模具的用途。
1.制造各种塑料制品注塑模具是制造塑料制品的关键设备之一,可以生产各种形状和尺寸各异的塑料制品,如塑料桶、塑料杯、塑料工具箱、塑料牙刷、塑料毛巾架等。
注塑模具提供了制造塑料制品的高效、低成本和条理性。
通过注塑模具,制造商可以在短时间内批量生产塑料制品,满足市场对产品的需求。
2.生产汽车零件汽车零件是注塑模具的重要应用领域之一。
例如汽车仪表板、前灯、后灯等关键部件,可以采用注塑模具进行生产。
通过模具运用注塑技术,可以快速地生产大量的零件,保证零件质量的统一和称量,从而提高产品的生产效率和降低了成本。
注塑方式还可以保证零件表面的平整度、硬度和透明度,使汽车外观更加美观。
3.制造电子产品注塑模具可为广泛的电子产品提供制造支持,如手机外壳、电视机外壳、音响、收音机和电脑外壳等。
通过模具制造电子产品,可以生产具备美观、高耐用性的产品,并且可以生产大量的产品,保持产品的一致性和稳定性,以满足市场对产品的高需求。
4.定制工业零件模具制造技术可在低成本、高强度、高精度的条件下大规模生产工业零件。
注塑模具可以生产各种规格和形状的金属或塑料零件,如夹具、模头、钢板、封头、瓶塞、塑料标签、电线和电缆绝缘体等。
注塑模具在工业零件制造过程中提供了高质量的制造方案,有效提高了生产效率和工业制品的质量。
总之,注塑模具是制造塑料制品的关键设备之一,在现代工业生产中用途广泛。
模具生产工艺的发展和提高,可以有效提高产品质量和生产效率,提高企业的竞争力。
随着科技的加速发展,注塑模具的应用领域还将更加广泛,对于工业制造和新产品开发都会有更大作用。
薄壁化注塑技术在汽车零件上的应用

薄壁化注塑技术在汽车零件上的应用摘要:安全、环保、节能是当下汽车工业发展中三大关键性话题,汽车轻量化是不可忽视的重要策略。
与此同时,保险杠是汽车运行中必不可少的安全件、外观件,要在细化分析的基础上从材料、结构、制造工艺等层面入手,灵活应用薄壁化技术的同时优化汽车保险杠设计,在控制保险杠重量的基础上有着较高的安全性、装饰性、功能性,持续改进汽车质量的同时实现综合效益目标。
本文基于薄壁化注塑技术在汽车零件上的应用展开论述。
关键词:薄壁化注塑技术;汽车零件;应用引言对于非金属材料,使用较成熟和较轻的技术制造薄材料(例如b .保险杠、车门板等。
),用于钢造型(例如。
b .前面板)和低密度材料的应用。
随着新能源汽车越来越普及,电池续航时间尤为重要,连续性与汽车质量密切相关,是汽车行业面临的一个问题。
在开发通过减少建模周期来提高生产效率和降低成本的技术时,压缩薄材料有助于满足性能要求、降低质量和降低成本。
1薄壁注塑成型定义薄壁注射方式,也称为薄壁模具环境,目前在薄壁模具方面定义不一致。
在行业中,塑料部件的厚度小于1mm,塑料投影面大于50cm2称为薄壁形状。
但是,对于汽车行业来说,销认为通过材料和工艺改进,传统抽壳可以打破,并且可以将制造性能视为薄壁形状。
2薄壁化材料测试标准熔体指数:以GB/ T3682. 1-2018测量塑料熔体流动速率(MFR)和熔体流动速率(MVR)。
第1部分:标准方法;密度:经GB/ T103. 1-2008测试,测量塑料非泡沫密度,第1部分:潜水网、液体刻度和滴度规定;拉伸强度:根据GB/ T1040. 2-2006进行测试,测量塑料拉伸性能第2部分:塑料和铸造模具的试验条件;弯曲强度:通过GB/ T9341-2008“塑料弯曲性能”测试;冲击强度:检查塑料的冲击强度(GB/ T1824-2008)。
3薄壁注塑成型技术对于薄壁注塑成型技术来说虽然在业界还没有对其形成一个较为统一定义,但是整体来说,成型塑件的厚度小于1mm,并且塑件的投影面积超过50平方厘米的注塑成型,都可以被称为是薄壁注塑。
汽车配备行业各种零部件生产工艺特点大全(1)

汽车配备行业各种零部件生产工艺特点大全(1)1. 钣金加工工艺- 特点:钣金加工工艺是根据汽车的外形和车身零部件的设计要求,通过对钣金材料的切割、弯曲、冲压、焊接等工艺进行加工制造的一种技术。
- 应用:钣金加工工艺广泛应用于汽车车身、车门、引擎盖等钣金零部件的制造过程中。
2. 塑料注塑工艺- 特点:塑料注塑工艺是将塑料颗粒加热熔化后通过注塑机射入模具中,经冷却固化后得到所需形状的一种制造工艺。
- 应用:塑料注塑工艺广泛应用于汽车内饰件、仪表盘、车灯外壳等塑料零部件的生产过程中。
3. 金属精密铸造工艺- 特点:金属精密铸造工艺是使用铸造机或压铸机将熔化的金属注入经过精密加工的模具中,通过冷却后得到所需的金属零部件。
- 应用:金属精密铸造工艺广泛应用于汽车发动机零部件、传动系统零部件等金属零部件的制造过程中。
4. 焊接工艺- 特点:焊接工艺是将两个或多个金属零部件通过加热、压合或填充金属等方式进行连接的一种制造工艺。
- 应用:焊接工艺广泛应用于汽车车身结构、底盘框架等零部件的制造过程中。
5. 电镀工艺- 特点:电镀工艺是通过电解溶液中的金属离子在金属表面上进行还原沉积,以增加金属零部件的耐腐蚀性和装饰性。
- 应用:电镀工艺广泛应用于汽车车身外部部件、进气格栅、车轮等金属零部件的制造过程中。
6. 热处理工艺- 特点:热处理工艺是通过对金属材料进行加热、保温和冷却等控制过程,改变其组织结构和机械性能的一种处理方法。
- 应用:热处理工艺广泛应用于汽车发动机零部件、传动系统零部件等金属零部件的制造过程中。
以上是汽车配备行业中常见的零部件生产工艺特点,不同工艺在不同的零部件制造过程中发挥着重要的作用,为汽车的性能和品质提供了保障。
浅析双色高光注塑产品的成型工艺和性能及在汽车行业中的应用

AUTO TIME115MANUFACTURING AND PROCESS | 制造与工艺时代汽车 1 引言随着当今科学技术的发展,生产制造水平的提升,以及人们对汽车外观品质、性能追求的不断提高,双色高光注塑产品被广泛的应用在汽车内外饰产品中。
这种先进的注塑成型方式,为汽车零部件的生产制造提供了全新的可能性。
双色高光注塑工艺,不仅可以实现在同一产品上呈现出两种不同感知颜色的视觉美感,还可在同一个产品上实现其中一种材料呈现外观品质,另一种材料实现内部结构性能的优势,从而使得产品在外观品质与结构性能上结合互补,表现出卓越的综合性能。
常见的双色高光注塑原材料粒子搭配有“PC-Red+PC-White”,“PMMA+ABS”,“PMMA+ TPE”,“ASA+PMMA”,“ASA+ EPDM”等。
“双色”原材料粒子的配对,取决于造型设计师对产品外观和性能的要求,但是其配对的前提是必须能够满足两种材料粒子本身性能的两个兼容性,即为粘合相容和加工相容。
其中,PMMA 与ABS 既是具有很好的相容性的两种原材料,两者的混合搭配,可以取长补短,提高的产品的硬度和光泽度[1]。
2 原材料的组成2.1 PMMA 材料聚甲基丙烯酸甲酯(polymethyl methacrylate),简称 PMMA。
属于长链高浅析双色高光注塑产品的成型工艺和性能及在汽车行业中的应用赵兴旺江铃控股有限公司 江西省南昌市 330052摘 要: 本文主要以“PMMA-Piano Black +ABS-G10 Black”两种原材料粒子的搭配为例,对双色高光注塑的汽车前后门窗框装饰盖板产品的成型工艺和性能进行分析介绍,以及浅析采用双色高光注塑工艺成型的多种产品在汽车内外饰零件中的应用。
关键词:双色高光注塑;PMMA/ABS;前后门窗框装饰盖板;汽车分子聚合物,主链为—C—C—单键结构,链性柔软。
具有高机械强度,表面高光泽度,优异的耐候性、耐划擦性、耐化学性等杰出的综合性能[2]。
注塑件包覆工艺__解释说明以及概述

注塑件包覆工艺解释说明以及概述1. 引言1.1 概述注塑件包覆工艺是一种将注塑件表面涂覆或包裹一层特定材料的加工方法,以实现增强结构强度、改善外观质量、提升耐用性和保护性能等目的。
该工艺在汽车制造、电子产品生产以及医疗器械行业等领域得到广泛应用,并且其技术特点逐渐被人们重视和认可。
1.2 文章结构本文将全面阐述注塑件包覆工艺的定义、原理、应用领域以及关键技术特点。
接着,对注塑件包覆工艺进行详细概述,包括历史背景、工艺流程简介和关键技术。
随后,通过分析主要应用案例,探讨该工艺在汽车零部件、电子产品外壳和医疗器械领域的实践与发展趋势。
最后,在结论与展望中总结当前注塑件包覆工艺的优缺点及存在问题,探讨未来发展方向和研究重点,并对其应用前景进行展望。
1.3 目的本文旨在系统性地介绍和分析注塑件包覆工艺,为相关领域的制造企业和研究人员提供有用的参考和指导。
通过对该工艺的深入探讨,能够增进对其定义、原理、应用领域和关键技术的理解,并促进业界对注塑件包覆工艺发展的思考与创新。
最终,希望推动该工艺在各个行业中的更广泛应用,并为相关产业链的发展做出贡献。
2. 注塑件包覆工艺解释说明2.1 注塑件包覆工艺定义注塑件包覆工艺是一种在已完成注塑成型的零部件表面上附着一层特殊材料的技术。
该技术利用各种粘结剂和涂料,通过不同的涂装方法,将附加材料牢固地覆盖在注塑零部件的表面上,以实现外观装饰、功能增强或保护作用。
这种工艺能够提供物理性能改善、耐磨损、防腐蚀和防UV等功能,为注塑产品赋予更高的价值。
2.2 注塑件包覆工艺原理注塑件包覆工艺基于几个基本原理来实现:- 表面处理:在进行包覆前,需要对注塑零部件表面进行清洁和处理以去除污垢和氧化物,并确保与涂层之间有足够的附着力。
- 选择合适数量和类型的粘接剂:根据需要,在注塑零部件表面应用适当类型和数量的粘接剂。
常见粘接剂包括聚氨酯、丙烯酸酯、环氧树脂等,其选择通常取决于底材和涂层材料的特性以及作用要求。
汽车模内镶件注塑成型( IMD )技术

汽车模内镶件注塑成型(IMD )技术塑料加工商们正在将可成型彩色薄膜视为一个经济、耐用、环境友好的装饰手段,它可使零件在脱模时即已完成装饰。
模内镶件注塑成型(IMD )技术,利用的就是这种可成型薄膜,可替代传统的、在零件脱模后采用的涂漆、印刷、热模锻、镀铬工艺。
该技术的首次成功应用是制成了一些小型的、相对较平的汽车内外饰零部件和手机零件。
今天,IMD技术有了更进一步的发展,可以制成更大的三维零件,例如整个仪表板、汽车保险杠、托板、汽车顶盖,甚至汽车、卡车的发动机罩。
据说,第一个实现商业化的、无需涂漆的水平车身板已经应用在Smart双座敞篷轿车上了。
IMD技术可节省再加工的费用,这对汽车工业极具诱惑力。
GE Plastics的Lexan SLX(一种聚碳酸酯共聚物)车身零件生产经理Venkata-krishnan Umamaheswaran说:“汽车上最贵的就是油漆了,涂漆生产线是汽车装配车间最大的投资,会占据车间一半的地面空间,而且一年内会产生1500多吨VOCs(挥发性有机物)。
”IMD技术的优势还包括:边角料产率低;可在同一地点完成零件的成型和装饰;回收性更好。
IMD技术可获得A级表面,且无流痕,更不会像流痕那样造成“模内驻色”。
但是如果零件本身就有很多孔,必须在脱模后进行装饰,那么IMD技术的经济效益则会大打折扣。
IMD技术的倡导者们宣称:利用最新一代的可成型薄膜制成的车身板,具有与涂漆金属板相媲美的甚至更高的抗划伤性和抗冲击性。
但是,假设汽车制造商们对涂漆生产线仍然施以巨额投资,则IMD在近期内还是无望完全取代涂漆工艺。
不过,工业观察家们相信:在美国,今后即使有投资,也很少会出现建造大型涂漆生产线的情况。
IMD技术首先将一块已经被印刷、涂覆或染色过的塑料薄板经冲切成坯料后,热成型成最终产品的形状。
修正后,把它放入注射腔内,从型腔后面注入一种与其相容的基体材料,最后得到成品。
成品的表面可以是纯色的,也可具有金属外观或木纹效果,还可印有图形符号。
- 1、下载文档前请自行甄别文档内容的完整性,平台不提供额外的编辑、内容补充、找答案等附加服务。
- 2、"仅部分预览"的文档,不可在线预览部分如存在完整性等问题,可反馈申请退款(可完整预览的文档不适用该条件!)。
- 3、如文档侵犯您的权益,请联系客服反馈,我们会尽快为您处理(人工客服工作时间:9:00-18:30)。
汽车零件注塑生产的应用与实践
1 前言
汽车用塑料量的多少已成为衡量汽车设计和制造水平高低的重要标志,目前国内汽车的材料约10%以上由塑料构成,塑料在汽车中的应用范围正在由汽车内部装饰扩展到汽车外部结构,除聚烯烃材料近来在汽车领域的应用量大增外,聚氨酯、增强复合材料等在汽车的运用也日益增加。
注塑件在汽车零部件所占的比例越来越高,注塑产业也成为汽车产业供应链上最为关键的环节。
2 车用塑件成型重点要素
由于汽车复杂零件的塑料件有与众不同的特殊性,所以其注塑成型在设计上需要充分考虑到如下因素,材料的干燥处理、玻纤增强材料对螺杆的新要求、驱动形式及合模结构等。
首当汽车保险杠、仪表板等常用的树脂材料为改性PP和改性ABS等改性树脂时,树脂材料有不同的吸湿性,为满足成型时的水份含量要求(一般要求0.2%),树脂原料在进入注塑机螺杆预塑计量之前,都要经过热风干燥或除湿干燥处理。
改性PP(PPEPDM)树脂的吸湿性较小,一般采用热风干燥机在80100℃的条件下23h即可。
改性ABS(PC/ABS)的吸湿性较强,在成型干燥前,应用除湿干燥机进行除湿干燥处理。
我们在设计汽车复杂塑料零件成型系统上充分考虑了除湿干燥系统功能运用。
目前国内汽车用塑料件基本上为无玻璃纤维增强的塑料制品,与使用含有短切玻璃纤维增强的树脂相比,成型无玻璃纤维增强塑料件所用注塑机的螺杆的材质和结构有较大的不同。
注塑机在设计时,要注意螺杆料筒的合金材质和特殊的热处理加工工艺,保证它的耐腐性和强度。
由于汽车零部件与常规产品不同,它的型腔面十分复杂,受力不等、应力分布不均,在设计中重点考虑它所需的加工能力。
注塑机的加工能力体现在合模力和注塑能力(以最大理论注射容积来表示)两方面。
注塑机在成型制品时,合模力必须大于模具型腔压力产生的开模力,否则模具分型面将会分开而成产生溢料。
确定注塑机合模力的公式如下:P合模P型腔F/100。
式中:P合模为注塑机的合模力(或称锁模力)KN;P型腔为模腔平均压力,MPa,与制品结构形状、精度要求和每模型腔数等有关,取值范围一般在25-40MPa之间;F为模具型腔,浇道和进料口的水平重叠投影面积CM3。
为保证可靠的锁模、注塑成型时的工艺锁模力必须小于注塑机的额定锁模力。
注塑机的最大理论注射容积与注塑机合模力吨位相匹配,是注塑机在出厂前以聚苯乙烯(PS)为基准树脂标称出来的注射容量。
3 车用塑料零部件优势
3.1 汽车复杂塑料零部件的优势
塑料可以一次加工成型,加工时间短,精度有保证。
塑料制品的弹性变形特性能吸收大量的碰撞能量,对强烈撞击有较大的缓冲作用,对车辆和乘员起到保护作用。
现代汽车上都采用塑化仪表板和方向盘,以增强缓冲作用。
前后保险杠、车身装饰条都采用塑料材料,以减轻车外物体对车身的冲击力。
塑料还具有吸收和衰减振动和噪声的作用,可以提高乘坐的舒适性。
塑料耐腐蚀性强,局部受损不会腐蚀。
通过添加不同的填料、增塑剂和硬化剂来制出所需性能的塑料,以适应车上不同部件的用途要求。
更方便的是塑料颜色可以通过添加剂调出不同颜色,省去喷漆的麻烦。
有些塑料件还可以电镀。
另一方面,汽车复杂零部件的注塑件特殊的外观和尺寸要求提高了汽车注塑件的开发门槛和风险。
Moldflow三维软件帮助企业在产品设计阶段分析塑件的成型可行性,通过对部品的变形及成型工艺的分析,评估并优化产品设计,同时指导了下游厂商的模具及注塑优化。
4 专用注塑机潜力大
泰瑞已推出新一代D系列汽车复杂塑料零部件专用注塑生产线。
早在2013广州CHINAPLAS国际橡塑展上已展示部份产品和技术。
现在,泰瑞提供的汽车复杂塑料零部件专用注塑生产线注重能耗及速度,不仅能缩短循环周期,相应提高产能;还能降低能耗,直接减低成本,实现节能环保、高响应速度、高重复精度等。
该生产线可生产的外装饰件主要部件有保险杠、挡泥板、车轮罩、导流板等,内装饰件的主要部件有仪表板、车门内板、副仪表板、杂物箱盖、座椅、后护板等。
锁模力从600至3000吨,射胶量从1848克至47601克,直正二板设计,比一般大型注塑机约少于30%以上长度,快速15秒调模、节省换模时间,多项专利授权技术,特快开模行程,达700mm/s,以8秒完成开锁模,自主研发计算器控制器。
一般注塑成型汽车前后保险杠、仪表板等大型汽车塑料件的成型周期为60100秒不等。
采用制作精良、冷却系统好的注塑模具以及配合取件机械手会缩短成型周期。
5 结论
全球车用塑料消耗量正逐年增加,车用塑料部件已从内饰件到外饰件、结构件到功能件、动力系统到转向制动系统等方向发展,特别是模块化制件,因此开发汽车复杂零部件塑料件专用注塑成型系统仍将具有很大的发展空间。