车间自主维护PPT
合集下载
《自主保全培训》课件

设备维护与保养
总结词
实施保养操作
详细描述
指导员工如何正确进行设备的日常保 养工作,如润滑、紧固等,确保设备 正常运行。
设备维护与保养
总结词
处理常见故障
详细描述
列举设备常见故障的表现及原因,指导员工如何排查和解决 故障,提高设备的使用寿命。
设备维护与保养
总结词
保持设备清洁
详细描述
强调设备清洁的重要性,指导员工如 何定期清洁设备,避免因污垢、积尘 导致设备性能下降。
针对不同类型故障,提供相应的修复方法和 技术,确保设备尽快恢复正常运行。
设备故障诊断与排除
总结词
预防性维护策略
详细描述
强调预防性维护的重要性,介绍通过定期检 查、更换易损件等措施,降低设备故障率的
方法。
安全操作规程
总结词
遵守安全规定
详细描述
强调遵守安全规定的重要性,介绍常见的安全规 定和操作要求。
详细描述
列举不同型号、规格的设备,比较其异同点,使员工能够根据实际情况选择合适的设备。
设备结构与原理
总结词
了解设备发展趋势
详细描述
分析设备技术的未来发展方向,使员工能够跟上技术进步的步伐。
设备维护与保养
总结词
制定维护计划
详细描述
根据设备的运行状况、使用频率 等因素,制定合理的维护计划, 包括定期检查、清洗、更换易损 件等。
02
自主保全培训内容
设备结构与原理
总结词
理解设备基本构造
详细描述
介绍设备的基本组成,包括主要部件及其功能,帮助员工了解设备的基本工作 原理。
设备结构与原理
总结词
掌握设备运行机制
详细描述
TPM全员生产维护培训课件(PPT 36张)

图文结合
故障是冰山的一角,只是问题的一小部分。
结论
故障零化的唯一办法是 “ 消除微缺陷 ”。
9
怎么做TPM?——思想转变
品质不良 故障
冰山一角
生产延迟 停机
性能下降
脱落 老化 变形 发热 松动 裂纹 噪音 泄漏 锈蚀 磨损 振动 划痕 灰尘 各种缺陷 脏污 设备 不遵守基本条件、劣化放置!
10
怎么做TPM?——思想转变
全员生产维护
Total Production Maintenance
1
现在的我们是否这样认为的……
我管生产,你管维护,设备 坏了是维修部门的事!
2
主要内容
什么是TPM? 为什么要做TPM?
TPM的好处?
怎么做TPM?
3
什么是TPM?
所谓TPM,是指全员参与的综合生产维护及全面 追求企业生产效率极限的现场改善活动。
TPM 哲学思想(三)
健康、长寿命来自于预防。
公式
预防医学=预防维护
结论
定期进行劣化测定(“健康诊断”), 有问题早发现。
11Leabharlann 怎么做TPM?——思想转变
日常 预防 预防医学 健康 诊断 早期 治疗
预防医学的3个功能:
(防止劣化) 日常维护 (加油、清扫、点检) (测定劣化) 检查 (诊断) (修复劣化) 预防修理 (事前更换)
更正思想
树立思想
TPM的基石是5S
15
怎么做TPM?——八大支柱
一套体系
TPM 全员自主维护
生产 质量 成本 交期
六大指标
安全
士气
八大支柱
个 别 改 善
自 主 保 全
初 期 管 理
故障是冰山的一角,只是问题的一小部分。
结论
故障零化的唯一办法是 “ 消除微缺陷 ”。
9
怎么做TPM?——思想转变
品质不良 故障
冰山一角
生产延迟 停机
性能下降
脱落 老化 变形 发热 松动 裂纹 噪音 泄漏 锈蚀 磨损 振动 划痕 灰尘 各种缺陷 脏污 设备 不遵守基本条件、劣化放置!
10
怎么做TPM?——思想转变
全员生产维护
Total Production Maintenance
1
现在的我们是否这样认为的……
我管生产,你管维护,设备 坏了是维修部门的事!
2
主要内容
什么是TPM? 为什么要做TPM?
TPM的好处?
怎么做TPM?
3
什么是TPM?
所谓TPM,是指全员参与的综合生产维护及全面 追求企业生产效率极限的现场改善活动。
TPM 哲学思想(三)
健康、长寿命来自于预防。
公式
预防医学=预防维护
结论
定期进行劣化测定(“健康诊断”), 有问题早发现。
11Leabharlann 怎么做TPM?——思想转变
日常 预防 预防医学 健康 诊断 早期 治疗
预防医学的3个功能:
(防止劣化) 日常维护 (加油、清扫、点检) (测定劣化) 检查 (诊断) (修复劣化) 预防修理 (事前更换)
更正思想
树立思想
TPM的基石是5S
15
怎么做TPM?——八大支柱
一套体系
TPM 全员自主维护
生产 质量 成本 交期
六大指标
安全
士气
八大支柱
个 别 改 善
自 主 保 全
初 期 管 理
一线员工自主改善培训(美的资料)PPT课件

是否与品质、强 度、性能相匹配的 材料 交货期是不是与 自身实力相适应
与工作量相比人 员配置是否过多 是否存在作业等 待 是不是有大材小 用的现象
是否充分利用了设备能力 是否有让设备空转的情况 机械的开动率还能不能提 高 精度、能力是不是超出了 需要的范围
是不是把能用的 东西扔掉了 是不是可以修理 是不是有能源泄 漏
想法
报告
许可
改善实施
指导、商量
效果确认
提案书写
事实确认/审查 标准化、横展
优秀提案审核
抽查复审、汇 总、处理
二、如何推进自主改善
2、自主改善推进流程
(5)书面提案编写与评审
个人基本情况
改
改善前情况说明
善
提
采取的改善措施
案
填
图例说明
写
范 本
实施成效
评审意见
自主改善申报表
二、如何推进自主改善
2、自主改善推进流程
一、什么是自主改善
3、自主改善与合理化建议的区别
自主改善 改了再提 结合自身工作岗位 自己力所能及的改善 着眼点:现场浪费
合理化建议 只提不改 范围不限 自己不能改提给别人改 着眼点:不限
一、什么是自主改善
4、自主改善的本质
➢ 自主改善的第一要务:一线员工的人才育成,培养员工发现问题,改善问题的思维和能力。 ➢ 自主改善的本质:引导一线员工,建立一个全员参与改善的机制,承载的是一种无处不在的
一、什么是自主改善
3、以下不属于提案改善范围
➢ 有想法,但未实施的 ➢ 仅提出缺点或问题,而欠缺具体改善内容和方法的 ➢ 组织已经实施横展的,后续提出类似提案不属于有效提案 ➢ 诉苦、报怨、不满或类似的事情
AM自主维护培训ppt课件

*
自主维护照片
透明的面板和 安全罩,有效地监控设备
*
自主维护照片
皮带罩: 之前
皮带罩: 之后
*
自主维护照片
有风扇方向指示器的色标马达
*
自主维护照片
操作员检查的路线图
*
自主维护照片
检查与润滑时间表
*
自主维护照片
良好的自主维护时间表
*
自主维护照片
良好的可视化控制
*
自主维护照片
电缆的目视标记
一旦清除了所有污染源和卫生死角,就完成了步骤2。 现在要用步骤2审核来建立里程碑。 如果能够证明团队满足所有标准,就可以鉴定为完成步骤2。
*
阶段3
阶段3: 检查与润滑
操作员执行高频率的润滑及其他基本维护任务 有色标润滑表、 检查时间表以及其他 可视化控制 设备停工期已经减少并且设备效率已经改善
设备:
异常日志
要求时间
当前状态
检查优先级
标记序号
记录异常
要求的行动
经手人
标签追踪器
*
标签追踪器
*
问题图
否
问题
污染源
不同清洁方式
1
附着在控制盘上的灰尘
2
带油渍的链条on
3
墙上的污渍
4
水管泄漏
5
漏油
6
带盖的电机
目视标记问题, 例如在同一 个图上标识出污染源和卫生死角 用符号区分各种问题类型 显示损失和问题之间的联系 添加一个对策图表并跟进—— 步骤2
*
清洁的原则
小心安全隐患 获得合适的清洁工具 保护敏感部件 从头到尾清洁 由内而外清洁 先粗略清洁,再手动清洁 使操作员最大程度参与,但需进行指导 确保进行学习 所有污垢都被清除之后,再上漆 随后立即引入定期清洁任务,以遵守标准
自主维护照片
透明的面板和 安全罩,有效地监控设备
*
自主维护照片
皮带罩: 之前
皮带罩: 之后
*
自主维护照片
有风扇方向指示器的色标马达
*
自主维护照片
操作员检查的路线图
*
自主维护照片
检查与润滑时间表
*
自主维护照片
良好的自主维护时间表
*
自主维护照片
良好的可视化控制
*
自主维护照片
电缆的目视标记
一旦清除了所有污染源和卫生死角,就完成了步骤2。 现在要用步骤2审核来建立里程碑。 如果能够证明团队满足所有标准,就可以鉴定为完成步骤2。
*
阶段3
阶段3: 检查与润滑
操作员执行高频率的润滑及其他基本维护任务 有色标润滑表、 检查时间表以及其他 可视化控制 设备停工期已经减少并且设备效率已经改善
设备:
异常日志
要求时间
当前状态
检查优先级
标记序号
记录异常
要求的行动
经手人
标签追踪器
*
标签追踪器
*
问题图
否
问题
污染源
不同清洁方式
1
附着在控制盘上的灰尘
2
带油渍的链条on
3
墙上的污渍
4
水管泄漏
5
漏油
6
带盖的电机
目视标记问题, 例如在同一 个图上标识出污染源和卫生死角 用符号区分各种问题类型 显示损失和问题之间的联系 添加一个对策图表并跟进—— 步骤2
*
清洁的原则
小心安全隐患 获得合适的清洁工具 保护敏感部件 从头到尾清洁 由内而外清洁 先粗略清洁,再手动清洁 使操作员最大程度参与,但需进行指导 确保进行学习 所有污垢都被清除之后,再上漆 随后立即引入定期清洁任务,以遵守标准
BODY TPM(自主维护)活动手册

知晓维修过程中可能发生的风险,并做好规避措施
制作特氟2h隆水现场管 实操
1h 现场 能够根据现场夹具的气路图找到相对应元件 美工刀、螺母
能够理解特氟龙水管的作用、安装位置、制作方法、安装标准
焊枪的简2h单故现场障发现、判断初级及初步处更根理换据上及述维课程修,胶让学枪员有改善夹3具h的大现致方场向及思路活动扳手1h、内现六场角等 介绍活现动扳场手焊,枪螺常丝发起故障及其现象,让独学立员地知更晓换如及何维修判胶断枪及进行初步的处理
◆ 自然劣化:由于设备自身的先天质量决定的状态变化过程。 如材料选择,结构设计等原因导致的劣化等。自然劣化一般都 有比较明显的趋势和周期性。
6
为什么要开展自主维护
在设备进入正常运行阶段,日常 设备保养维护工作非常重要, 70%的设备问题可以通过自主维 护活动得到先期预防,30%的设 备问题是必须通过专业设备维修 和技术改进措施加以预防。
全员
从最高领导者 到一线工人全 部参与
覆盖设备的全 全过程 寿命周期过程
效率化
最有效、最经 济的方法和工 具
2
什么是TPM(自主维护)
03
最大限度提高人的设备维护管理能力
技能水平
通过专业维护及自主维护工作的推广,有效提升 相关人员对设备的维护管理能力。
02 改善现场体质
技能水平
每一个作业员都必须掌握观察设备、发现问题点/缺陷的 能力,养成自己的设备自己维护的思考方式。
小组活动标准制定
全体小组成员
小组活动口号
全体小组成员
电阻式手动焊枪基础知识
全体小组成员
固定式螺母焊机基础知识
全体小组成员
胶泵基础知识
全体小组成员
焊接夹具基础知识
自主维护介绍
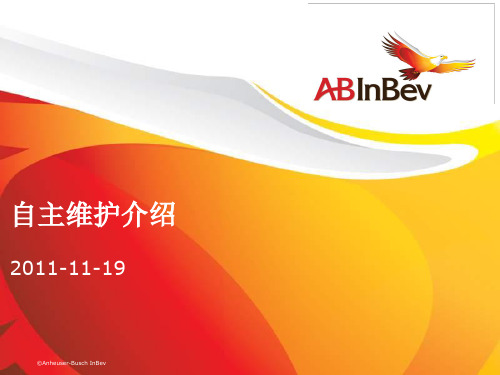
©Anheuser-Busch InBev
目的
- 通过正确的操作和对关键点的每天检查避免设备损坏 - 由操作工对设备良好的管理和维修使设备处在理想的状态 - 永久的维护设备在良好的状态所需建立的基本条件
©Anheuser-Busch InBev
What ? - BENEFITS
实行自主维护保养的益处
©Anheuser-Busch InBev
Autonomous Maintenance – Structure Definition 自主维护- 结构定义
Plant Manager 工厂经理
MCRS
TS Manager TS经理
Autonomous Maintenance Coordinator 自主维护协调员
Owner of the Autonomous Maintenance Process within the department 实施自主维护部门的所有者
Owner of the Autonomous Maintenance Process within the PLANT工厂内自主维护的所有者 Link between Area x Maintenance x People 在各部门, 维护和员工之间进行自主维护的协调工作
自主维护介绍
2011-11-19
©Anheuser-Busch InBev
Agenda
• 自主维护愿景 • 自主维护目的与益处 • 自主维护的推进 • 自主维护团队及RACI • 自主维护MCRS
©Anheuser-Busch InBev
Agenda
• 自主维护愿景 • 自主维护目的与益处 • 自主维护的推进 • 自主维护团队及RACI • 自主维护MCRS
目的
- 通过正确的操作和对关键点的每天检查避免设备损坏 - 由操作工对设备良好的管理和维修使设备处在理想的状态 - 永久的维护设备在良好的状态所需建立的基本条件
©Anheuser-Busch InBev
What ? - BENEFITS
实行自主维护保养的益处
©Anheuser-Busch InBev
Autonomous Maintenance – Structure Definition 自主维护- 结构定义
Plant Manager 工厂经理
MCRS
TS Manager TS经理
Autonomous Maintenance Coordinator 自主维护协调员
Owner of the Autonomous Maintenance Process within the department 实施自主维护部门的所有者
Owner of the Autonomous Maintenance Process within the PLANT工厂内自主维护的所有者 Link between Area x Maintenance x People 在各部门, 维护和员工之间进行自主维护的协调工作
自主维护介绍
2011-11-19
©Anheuser-Busch InBev
Agenda
• 自主维护愿景 • 自主维护目的与益处 • 自主维护的推进 • 自主维护团队及RACI • 自主维护MCRS
©Anheuser-Busch InBev
Agenda
• 自主维护愿景 • 自主维护目的与益处 • 自主维护的推进 • 自主维护团队及RACI • 自主维护MCRS
AM自主维护资料
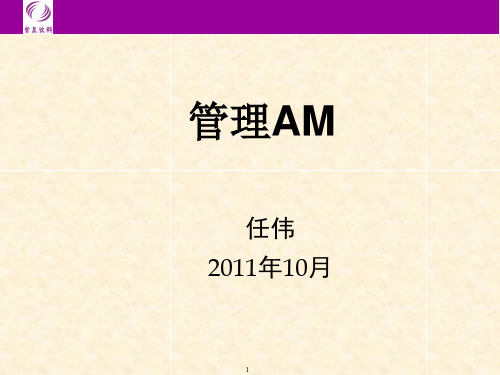
2
AM作用
1、增强设备运行稳定性,减少停机时间 2、避免浪费(藏宝图) 3、及时点检发现问题,制定维修计划避免紧急停机,降低维修成本
预防性维护比紧急维修成本更低
3
如何保持机器运行良好
预防问题 措施、监测并检查问题 协助分检出问题
•• 正确操作 •• 清洁 •• 润滑 •• 点检
• •量测和监测 • •检查 • •记录问题
4
• •自主完成小维修 • •立即汇报停机和问题 • •协助实施大型维护和 问题解决
AM实施图
自主维护团队实施看板
之后照片 成立团队 问题 地图 污染对策 (第2步) 可视化控制
藏宝图 计划 (第0步)
难以接近区 域对策 (第 2步) 清洁 时间表
点检时间表
OPLs
之前照片 问题跟进表 (第1步)
10
六、污染源地图
找到污染的源头,治病要治本
轴承油嘴、链条粉末、润滑油等
11
七、难以清洁区域及对策
针对难以清洁的区域,制定相对应的策略,使得 清洁工作变得容易,节省时间和力气。
发挥创意
12
八、清洁周期表
制作可视化图 片,明确清洁 方法、周期及 要达到的标准
编号 1 2
区域 * * * *
工具 抹布 抹布
明确责任人和要求完成期限
序号 1 2 描述 ** ** 责任人 ** ** 期限 ** **
9
五、藏宝图
与能源相关,需要我们密切关注。如设备的水、电、 汽、油的消耗或泄漏。小改善大收益。
发黑的灯 管用掉相 同的电却 无法达到 预期的加 热功率,必 须及时更 换
接 口 漏 了 , 压 缩 空 气 跑 啦 !
备
第7部分自主维护活动

自主保全7步内容
0-Step : 5S活动 1-Step : 初期清洁 2-Step : 发生源,困难点 对策 3-Step : 청소制定清洁,注油标准 4-Step : 设备总检查 5-Step : 自主检查 6-Step : 保证工艺品质 7-Step : 彻底进行自主管理
北
大
5S部门
荒
(5行)
-9/109-
1. 自主保全的概要
操作部门的做作
1. 劣化防止活动 :- 正确操作及基本条件整备 - 调整(主要是操作或准备,交替中的挑中,不良品质的防止) - 保全数据记录(防止再发,MP设计的Feed Back)
2. 劣化测定活动(5感):日常检点及定期检点的一部分 3. 劣化恢复活动: - 简单的附属品交换,异常时应急措施….等的小整备
-4/109-
1. 自主保全的概要
通过基本条件整备,排除强制劣化因素 防止故障
预防自然劣化(固有寿命)
防止强制劣化(人为劣化)
努力延长寿命
改良保全 1. 提高信赖度及安全性 2. 通过提高操作防止漏洞 3. 提高保全性及修理品质
排除因素
基本条件整备 1. 清洁:排除灰尘,污染 2. 注油:防止油污染,缺油 3. 拧紧:防止松懈、脱落
活动内容
3 Step 制订可行标准书
改善有关润滑,注油的不合理因素 * 有关注油,润滑,油,污染发生源,注油困难点对策 推进清洁检点及注油项目等肉眼管理
4 Step 总检点
总检点按科目实施理论实习 总检点按科目检点及不合理改善 推进有关检点项目的肉眼推进
活动目标
- 计划时间内完成润滑,注油 (缩短注油时间)
培
养
专
业 操
创造活跃的职场气氛
0-Step : 5S活动 1-Step : 初期清洁 2-Step : 发生源,困难点 对策 3-Step : 청소制定清洁,注油标准 4-Step : 设备总检查 5-Step : 自主检查 6-Step : 保证工艺品质 7-Step : 彻底进行自主管理
北
大
5S部门
荒
(5行)
-9/109-
1. 自主保全的概要
操作部门的做作
1. 劣化防止活动 :- 正确操作及基本条件整备 - 调整(主要是操作或准备,交替中的挑中,不良品质的防止) - 保全数据记录(防止再发,MP设计的Feed Back)
2. 劣化测定活动(5感):日常检点及定期检点的一部分 3. 劣化恢复活动: - 简单的附属品交换,异常时应急措施….等的小整备
-4/109-
1. 自主保全的概要
通过基本条件整备,排除强制劣化因素 防止故障
预防自然劣化(固有寿命)
防止强制劣化(人为劣化)
努力延长寿命
改良保全 1. 提高信赖度及安全性 2. 通过提高操作防止漏洞 3. 提高保全性及修理品质
排除因素
基本条件整备 1. 清洁:排除灰尘,污染 2. 注油:防止油污染,缺油 3. 拧紧:防止松懈、脱落
活动内容
3 Step 制订可行标准书
改善有关润滑,注油的不合理因素 * 有关注油,润滑,油,污染发生源,注油困难点对策 推进清洁检点及注油项目等肉眼管理
4 Step 总检点
总检点按科目实施理论实习 总检点按科目检点及不合理改善 推进有关检点项目的肉眼推进
活动目标
- 计划时间内完成润滑,注油 (缩短注油时间)
培
养
专
业 操
创造活跃的职场气氛
- 1、下载文档前请自行甄别文档内容的完整性,平台不提供额外的编辑、内容补充、找答案等附加服务。
- 2、"仅部分预览"的文档,不可在线预览部分如存在完整性等问题,可反馈申请退款(可完整预览的文档不适用该条件!)。
- 3、如文档侵犯您的权益,请联系客服反馈,我们会尽快为您处理(人工客服工作时间:9:00-18:30)。
关键点:1.通过清洁发现异常和功能丧失等现象,然后改进
2.污染源的对策 3.对小缺陷的发现和改进 4.建立设备的基本状态 5.对设备操作规范的澄清和坚持
13
GEA Heat Exchangers
零故障的5个阶段
第一阶段 发现造成强制劣化的所有原因,复原和提高 (改善)
建立设备的基本状态,只允许存在自然劣化的现象。也就是 减少强制劣化,对非控制的劣化现象进行复原和改善。
9
GEA Heat Exchangers
维护的基本理念
机器故障是由部件劣化引起的 劣化分强制劣化和自然劣化 消除强制劣化是计划维护的前提 不断消除薄弱点是减少自然劣化,延长设备生命周期的关键
10
GEA Heat Exchangers
故障发生的要因
应力超限 零件劣化 强度不足
11
基本条件不完备
劣化之放任
不遵守操作条件 欠缺技术(技能不足) 设计制造安装上的内在
弱点
GEA Heat Exchangers
零故障的5个基本对策
建立基本条件
设备清洁 污染源防止对策
拧 紧 防止松脱对策
加 油 明确加油部位
给油方式改善
•点 检 点检项目,点检 方法技能判定标 准 清扫点检加油 基准作成
保持操作条件
设 计 能 力 和负 荷 的 限界值设定 过 负 荷 运 转弱 点 对 策 设 备 操 作 方法 标 准 化 单 位 部 件 使用 条 件 设定和改善 施 工 基 准 设定 和 改 善 固定配管、配线 旋转部位防尘防水 环境条件整备 尘 埃 、 温 度、 湿 度 振动、冲击
➢4.自经营者至第一线从业人员全体参加。事实上,TPM是借助相关活动来 改变人的想法和行动,以使设备达到理想状态,进而改变企业体质,若只靠 企业部份人员的努力,势必无法达成。
4
Insérer texte avec "Ajouter en-tête et bas de page"
GEA Heat Exchangers
生产部门 ●运转 ●操作 ●点检 ●加油 ●调整设备、夹具 ●异常征兆发现
12
设备维修部门 ●点检 ●检查(测定)诊断 ● 修理保养●故障排除 ●故障分析
GEA Heat Exchangers
零故障的5个阶段
第一阶段 发现造成强制劣化的所有原因,复原和提高 (改善)
建立设备的基本状态,只允许存在自然劣化的现象。也就是 减少强制劣化,对非控制的劣化现象进行复原和改善。
这个时候我们需要诊断技术。
我们将采用各种不同的传感器和诊断仪器。
关键 点:
1.在劣化方式中选择参数
2.选择对这些参数的测量方法
3.衡量劣化现象的出现与物理量的关系,如尺寸的变 化,运动时的振动,当前耗电,电压、温度、磁变化等 等
17
GEA Heat Exchangers
零故障的5个阶段
第五阶段 预测维护活动的开展
000
事 故
故
人员改变
思考方式变化了
障
4-5步
行为变化了
缺
陷
实
现
车间改变 6-7步
29
GEA Heat Exchangers
维护观念的变化
TPM前
1.我开车,你维护
2.车子开坏是正常的(车子总 是要坏的)
3.再次坏了是维修工的事情 (修不好,水平低)
TPM后
1.我开车,更要维护
2.车子开坏分自然劣化与强制 劣化,而后者引起的故障和缺 陷是可以避免的
1971年前后,日本总结并在全国推广丰田公司的 全员参与和围绕效率化核心的维修管理,即 TPM。·
GEA Heat Exchangers
TPM 的定义
★TPM---全员自主维护:Total Productive Maintenance
➢1.以建立追求生产系统的最高效率化(总合的效率化)的企业经营体系为目 标。而所要建立的企业体系就是“追求生产系统效率化的极限”,产生最大的 产出,彻底追求零损失。
在开展以时间为基础的维护活动之后,我们是有可能实现设备零 故障的,然而如果我们要实现设备生命周期的最大化,就必须引 入预测维护技术。
劣 化 的 程 度
18
诊断
复原
时间
GEA Heat Exchangers
迈向零故障的历程
19
Байду номын сангаас
GEA Heat Exchangers
第二章
GEA Heat Exchangers
我们可以根据生命周期的变化和维护的频率来决定是否需 要开始纠正维护活动。
关键 点:
1.改进设计中的薄弱点 2.确保设备的防磨损和刚度强度的可靠性能 3.减少移动压力的对策
15
GEA Heat Exchangers
零故障的5个阶段
第三阶段 对自然劣化方式的摸索
维护活动将只针对自然劣化(时间性老化 )的部件开展, 设备的每一个部件都会在应力作用下随着时间的推移产生自然劣 化现象。
劣化的能力
按基准书进行作业
4总点检
培养理解设备构造,系 理解设备的机能及构造,开展深层的、系
统进行点检的能力
统全面的点检。
5– 自主点检
工序正确的操作方法, 掌握工序细节、调整方法、发生异常时的
处理异常的能力
对策,提高独立自主点检的能力
6– 标准化
经过实践后修正后,把 把暂定基准标准化,系统化,成为正式标
自主维修作业标准化
准。
7完全自主管理
构筑设备及现场管理的 1 ~ 6 步的体系化,自觉化,持续化,反复循
免疫体质
环使用PDCA进行改善
28
GEA Heat Exchangers
自主维护(AM)的总体概念
第0步 准备 第1步 第2步 第3步 第4步 第5步
体质的革新
推动
改变设备 1-3步
效果(缺陷 故障减少)
20
含义 什么是自主维护?
以生产现场操作人员为主,对于设备按照人的感官 (目视/手触/问诊/听声/嗅诊)来进行检查,
并对清扫、润滑、紧固、点检等维修技能加
以训练,使之能对小故障进行自主修理及适合 操作工做的改善,以维护设备基本状况。
“依靠我们自己维持我们的设备在良好的 状态”
21
GEA Heat Exchangers
通常引起设备故障的原因
“设备的不良70%以上来自润滑与清扫的不良”
25
GEA Heat Exchangers
清扫、润滑、紧固、点检的重要性——故障冰山理论
一粒尘土导致故障的演变过程: 尘土→划痕→存水→电化学反应→锈蚀→松动→振动→疲劳→
微裂纹→裂纹→断裂→最终故障
微缺陷
中缺陷
大缺陷
故障
不会产生 停机,暂时 不影响 功能
会产生小 停机或影 响设备功 能
已发展到 故障边缘, 置之不理 后果严重
26
GEA Heat Exchangers
为什么要AM(自主维护)
所有的损失是我们自己造成的. 故障时认为的 生产现场是损失的发源地
经常洗车可以帮 助我们发现存在
的问题
操作者了解设备性能及运行状况 便于早期发现故障 及时进行维护工作 提高操作者对设备使用的责任感 增强员工技能 提高设备运行效率
然而,我们现有的技术能力是无法很好地捕获这一现象的。
关键 点:
1.对自然劣化的时间变化趋势的追踪研究
2.劣化现象的物理分析
3.通过测定劣化的程度,掌握劣化和产品质量之间的关 系
16
GEA Heat Exchangers
零故障的5个阶段
第四阶段 对量化参数的追踪和研究
在确认劣化方式之后,接下来我们就应该找出可以测定劣化程度 的参数和物理量。
生产和维修部门沟通差,合作差 问题扯皮多,忙于推卸责任 设备故障得不到根本解决 工厂运转效率低下
23
GEA Heat Exchangers
冰山一角
故障
▶ 垃圾, 污染, 原料附着 ▶ 研磨,晃动,松动,漏油 ▶ 腐蚀,变形,伤痕,炸裂 ▶ 温度,振动,异音等
故障是冰山的一角
潜在缺陷
24
GEA Heat Exchangers
劣化复元
劣化的预知
建立修理方法
通 用 部 件 5 感 点 检和劣化部位发现
日常点检基准作 成
按故障部位进行 MTBF分析和寿命 预测 确定更换限界值 制定点检、检查、 更换基准
探讨预知异常征
解体、 清 洗、 安 装、测定、更换方 法的标准化
使用备件通用化 工具器具的改善 和专用化
经改善,使设备 的结构易于修理
TPM的自主维护(AM)和计划维护(PM)
消除强制劣化,从而在自然劣化的状态下测定 其劣化状态,当劣化已经达到某种程度以上 时, 则必须彻底使其恢复原状。
8
GEA Heat Exchangers
什么是强制劣化
强制劣化:
因错误操作,或没有遵守标准操作条件,而造成对设 备或部件的损坏。如使用不正确的工具,用力过大,松动、 漏油、缺油、灰尘、污垢等。
1950年以后,人们发现设备故障总在某部位出现, 因此在维护时主要去查找薄弱部位并对其改良。
1955年前后,人们发现设备的许多故障是周期性 出现的,于是对这类故障提出了预防维护方法。
1958年前后,工业技术不断进步,人们开始需要 不发生故障的设备。维护从设计、制作、安装开 始预防。 1958年前后,美国GE公司综合上述保全方法,提 出了一套系统的保全方案。即TPM的前身PM。
防止故障发生于未然
(最大的平均故障间隔时间,最小的平均故障修复时 维护的目的= 间)
最小的成本(人工、备件、生产等损失)
设备生命周期收益最大化
2.污染源的对策 3.对小缺陷的发现和改进 4.建立设备的基本状态 5.对设备操作规范的澄清和坚持
13
GEA Heat Exchangers
零故障的5个阶段
第一阶段 发现造成强制劣化的所有原因,复原和提高 (改善)
建立设备的基本状态,只允许存在自然劣化的现象。也就是 减少强制劣化,对非控制的劣化现象进行复原和改善。
9
GEA Heat Exchangers
维护的基本理念
机器故障是由部件劣化引起的 劣化分强制劣化和自然劣化 消除强制劣化是计划维护的前提 不断消除薄弱点是减少自然劣化,延长设备生命周期的关键
10
GEA Heat Exchangers
故障发生的要因
应力超限 零件劣化 强度不足
11
基本条件不完备
劣化之放任
不遵守操作条件 欠缺技术(技能不足) 设计制造安装上的内在
弱点
GEA Heat Exchangers
零故障的5个基本对策
建立基本条件
设备清洁 污染源防止对策
拧 紧 防止松脱对策
加 油 明确加油部位
给油方式改善
•点 检 点检项目,点检 方法技能判定标 准 清扫点检加油 基准作成
保持操作条件
设 计 能 力 和负 荷 的 限界值设定 过 负 荷 运 转弱 点 对 策 设 备 操 作 方法 标 准 化 单 位 部 件 使用 条 件 设定和改善 施 工 基 准 设定 和 改 善 固定配管、配线 旋转部位防尘防水 环境条件整备 尘 埃 、 温 度、 湿 度 振动、冲击
➢4.自经营者至第一线从业人员全体参加。事实上,TPM是借助相关活动来 改变人的想法和行动,以使设备达到理想状态,进而改变企业体质,若只靠 企业部份人员的努力,势必无法达成。
4
Insérer texte avec "Ajouter en-tête et bas de page"
GEA Heat Exchangers
生产部门 ●运转 ●操作 ●点检 ●加油 ●调整设备、夹具 ●异常征兆发现
12
设备维修部门 ●点检 ●检查(测定)诊断 ● 修理保养●故障排除 ●故障分析
GEA Heat Exchangers
零故障的5个阶段
第一阶段 发现造成强制劣化的所有原因,复原和提高 (改善)
建立设备的基本状态,只允许存在自然劣化的现象。也就是 减少强制劣化,对非控制的劣化现象进行复原和改善。
这个时候我们需要诊断技术。
我们将采用各种不同的传感器和诊断仪器。
关键 点:
1.在劣化方式中选择参数
2.选择对这些参数的测量方法
3.衡量劣化现象的出现与物理量的关系,如尺寸的变 化,运动时的振动,当前耗电,电压、温度、磁变化等 等
17
GEA Heat Exchangers
零故障的5个阶段
第五阶段 预测维护活动的开展
000
事 故
故
人员改变
思考方式变化了
障
4-5步
行为变化了
缺
陷
实
现
车间改变 6-7步
29
GEA Heat Exchangers
维护观念的变化
TPM前
1.我开车,你维护
2.车子开坏是正常的(车子总 是要坏的)
3.再次坏了是维修工的事情 (修不好,水平低)
TPM后
1.我开车,更要维护
2.车子开坏分自然劣化与强制 劣化,而后者引起的故障和缺 陷是可以避免的
1971年前后,日本总结并在全国推广丰田公司的 全员参与和围绕效率化核心的维修管理,即 TPM。·
GEA Heat Exchangers
TPM 的定义
★TPM---全员自主维护:Total Productive Maintenance
➢1.以建立追求生产系统的最高效率化(总合的效率化)的企业经营体系为目 标。而所要建立的企业体系就是“追求生产系统效率化的极限”,产生最大的 产出,彻底追求零损失。
在开展以时间为基础的维护活动之后,我们是有可能实现设备零 故障的,然而如果我们要实现设备生命周期的最大化,就必须引 入预测维护技术。
劣 化 的 程 度
18
诊断
复原
时间
GEA Heat Exchangers
迈向零故障的历程
19
Байду номын сангаас
GEA Heat Exchangers
第二章
GEA Heat Exchangers
我们可以根据生命周期的变化和维护的频率来决定是否需 要开始纠正维护活动。
关键 点:
1.改进设计中的薄弱点 2.确保设备的防磨损和刚度强度的可靠性能 3.减少移动压力的对策
15
GEA Heat Exchangers
零故障的5个阶段
第三阶段 对自然劣化方式的摸索
维护活动将只针对自然劣化(时间性老化 )的部件开展, 设备的每一个部件都会在应力作用下随着时间的推移产生自然劣 化现象。
劣化的能力
按基准书进行作业
4总点检
培养理解设备构造,系 理解设备的机能及构造,开展深层的、系
统进行点检的能力
统全面的点检。
5– 自主点检
工序正确的操作方法, 掌握工序细节、调整方法、发生异常时的
处理异常的能力
对策,提高独立自主点检的能力
6– 标准化
经过实践后修正后,把 把暂定基准标准化,系统化,成为正式标
自主维修作业标准化
准。
7完全自主管理
构筑设备及现场管理的 1 ~ 6 步的体系化,自觉化,持续化,反复循
免疫体质
环使用PDCA进行改善
28
GEA Heat Exchangers
自主维护(AM)的总体概念
第0步 准备 第1步 第2步 第3步 第4步 第5步
体质的革新
推动
改变设备 1-3步
效果(缺陷 故障减少)
20
含义 什么是自主维护?
以生产现场操作人员为主,对于设备按照人的感官 (目视/手触/问诊/听声/嗅诊)来进行检查,
并对清扫、润滑、紧固、点检等维修技能加
以训练,使之能对小故障进行自主修理及适合 操作工做的改善,以维护设备基本状况。
“依靠我们自己维持我们的设备在良好的 状态”
21
GEA Heat Exchangers
通常引起设备故障的原因
“设备的不良70%以上来自润滑与清扫的不良”
25
GEA Heat Exchangers
清扫、润滑、紧固、点检的重要性——故障冰山理论
一粒尘土导致故障的演变过程: 尘土→划痕→存水→电化学反应→锈蚀→松动→振动→疲劳→
微裂纹→裂纹→断裂→最终故障
微缺陷
中缺陷
大缺陷
故障
不会产生 停机,暂时 不影响 功能
会产生小 停机或影 响设备功 能
已发展到 故障边缘, 置之不理 后果严重
26
GEA Heat Exchangers
为什么要AM(自主维护)
所有的损失是我们自己造成的. 故障时认为的 生产现场是损失的发源地
经常洗车可以帮 助我们发现存在
的问题
操作者了解设备性能及运行状况 便于早期发现故障 及时进行维护工作 提高操作者对设备使用的责任感 增强员工技能 提高设备运行效率
然而,我们现有的技术能力是无法很好地捕获这一现象的。
关键 点:
1.对自然劣化的时间变化趋势的追踪研究
2.劣化现象的物理分析
3.通过测定劣化的程度,掌握劣化和产品质量之间的关 系
16
GEA Heat Exchangers
零故障的5个阶段
第四阶段 对量化参数的追踪和研究
在确认劣化方式之后,接下来我们就应该找出可以测定劣化程度 的参数和物理量。
生产和维修部门沟通差,合作差 问题扯皮多,忙于推卸责任 设备故障得不到根本解决 工厂运转效率低下
23
GEA Heat Exchangers
冰山一角
故障
▶ 垃圾, 污染, 原料附着 ▶ 研磨,晃动,松动,漏油 ▶ 腐蚀,变形,伤痕,炸裂 ▶ 温度,振动,异音等
故障是冰山的一角
潜在缺陷
24
GEA Heat Exchangers
劣化复元
劣化的预知
建立修理方法
通 用 部 件 5 感 点 检和劣化部位发现
日常点检基准作 成
按故障部位进行 MTBF分析和寿命 预测 确定更换限界值 制定点检、检查、 更换基准
探讨预知异常征
解体、 清 洗、 安 装、测定、更换方 法的标准化
使用备件通用化 工具器具的改善 和专用化
经改善,使设备 的结构易于修理
TPM的自主维护(AM)和计划维护(PM)
消除强制劣化,从而在自然劣化的状态下测定 其劣化状态,当劣化已经达到某种程度以上 时, 则必须彻底使其恢复原状。
8
GEA Heat Exchangers
什么是强制劣化
强制劣化:
因错误操作,或没有遵守标准操作条件,而造成对设 备或部件的损坏。如使用不正确的工具,用力过大,松动、 漏油、缺油、灰尘、污垢等。
1950年以后,人们发现设备故障总在某部位出现, 因此在维护时主要去查找薄弱部位并对其改良。
1955年前后,人们发现设备的许多故障是周期性 出现的,于是对这类故障提出了预防维护方法。
1958年前后,工业技术不断进步,人们开始需要 不发生故障的设备。维护从设计、制作、安装开 始预防。 1958年前后,美国GE公司综合上述保全方法,提 出了一套系统的保全方案。即TPM的前身PM。
防止故障发生于未然
(最大的平均故障间隔时间,最小的平均故障修复时 维护的目的= 间)
最小的成本(人工、备件、生产等损失)
设备生命周期收益最大化