CNC原点设置
CNC操作

3.准备工作: 准备工作: 准备工作
机床卫生,因为数控铣床是精度要求极高的机器,所以它的卫生工作必须到位。一定要用棉布把工作 台擦干净,工件卫生,先用锉刀把工件四周的毛刺打干净,再用布擦干净,保证工件在工作台上水平.
4.摆放工作: 摆放工作: 摆放工作 一定要按程式单要求做,看清楚摆向和分中方法,认准基准角和正反面,不要乱摆一通。 5.压码仔: 按要求压码仔,一般压四个角,否则会导致撞刀等事情发生。 压码仔: 压码仔 6.打表: 打表: 打表
数控铣床(CNC)操作手册 操作手册 数控铣床
1.开机: 开机: 开机
先打开电箱电源开关,再安面板电源按钮,等显示屏显示稳定后再扭开紧急开关按钮,这时面板上和 工作等会报警,不停的闪烁,这时按下RESET。开机时注意防电,手不能带水不能碰到电源。
2.归原点: 归原点: 归原点
开机后面板上X、Y、Z轴要求原点复归,要把功能旋钮扭到回零功能。然后逐个轴作原点复归,一般 要先归Z轴再归XY,当屏幕上机械坐标值全是O时,则表示归原点已成功。
先打平表面,再打侧面,一定要保证工件水平,注意,是单边碰数的,碰那边就打那边的侧面表。
7.分中: 分中: 分中
一是要按要求分中,不要单边碰数的也去四面分中,该偏数的切记一定要偏数,但一定要减去分中棒 的半径,分中前先要把转速设好,一般是400—600转,再启动,千万不要多设一个0或者没设好就启动 。四面分中做法,先用分中棒碰工件的一边,先十个丝十个丝的碰,再一个丝一个丝的进行微调。当 微调到分中棒刚好一个丝就偏出来时为好,再选择这个边的轴,把相对坐标值清0,然后再该轴的另一 边分好后再将坐标除以2得到商,再将机床移到商值再将该轴归0,再以同样的方法分得另一轴的中心, 再把中心点的机械坐标值输入到工件坐标值中(如G54坐标)。
数控机床原点、参考点、工作零点的区别和联系
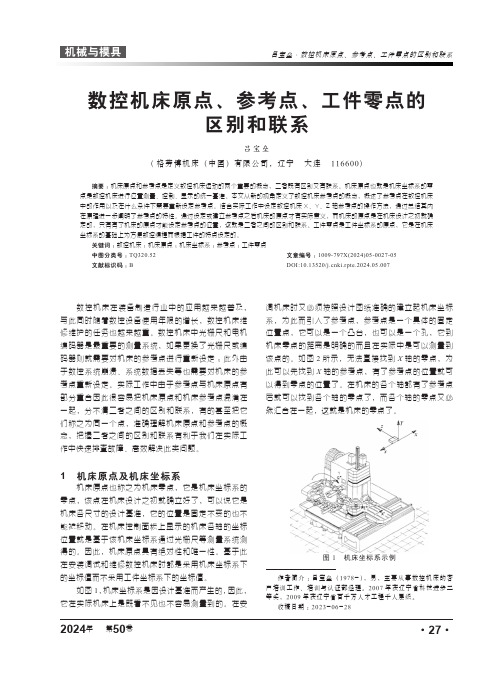
作者简介:吕宝垒(1978-),男,主要从事数控机床的客户培训工作、培训与认证部经理。
2007年获辽宁省科技进步二等奖,2009年获辽宁省百千万人才工程千人层级。
收稿日期:2023-06-28数控机床在装备制造行业中的应用越来越普及,与此同时随着数控设备使用年限的增长,数控机床维修维护的任务也越来越重。
数控机床中光栅尺和电机编码器是最重要的测量系统,如果更换了光栅尺或编码器则就需要对机床的参考点进行重新设定;此外由于数控系统崩溃、系统数据丢失等也需要对机床的参考点重新设定。
实际工作中由于参考点与机床原点有部分重合因此很容易把机床原点和机床参考点混淆在一起,分不清二者之间的区别和联系,有的甚至把它们称之为同一个点,准确理解机床原点和参考点的概念,把握二者之间的区别和联系有利于我们在实际工作中快速排查故障、高效解决此类问题。
1 机床原点及机床坐标系机床原点也称之为机床零点,它是机床坐标系的零点,该点在机床设计之初就确立好了,可以说它是机床各尺寸的设计基准,它的位置是固定不变的也不能被移动。
在机床控制面板上显示的机床各轴的坐标位置就是基于该机床坐标系通过光栅尺等测量系统测得的。
因此,机床原点具有绝对性和唯一性。
基于此在安装调试和维修数控机床时都是采用机床坐标系下的坐标值而不采用工件坐标系下的坐标值。
如图1,机床坐标系是因设计基准而产生的,因此,它在实际机床上是既看不见也不容易测量到的。
在安数控机床原点、参考点、工件零点的区别和联系吕宝垒(格劳博机床(中国)有限公司,辽宁 大连 116600)摘要:机床原点和参考点是定义数控机床运动的两个重要的概念,二者既有区别又有联系。
机床原点也就是机床坐标系的零点是数控机床进行位置测量、控制、显示的统一基准。
本文从新的视角定义了数控机床参考点的概念,概述了参考点在数控机床中的作用以及在什么条件下需要重新设定参考点。
结合实际工作中设定数控机床X、Y、Z 轴参考点的操作方法,通过总结其内在原理进一步阐明了参考点的特性。
CNC操作指引
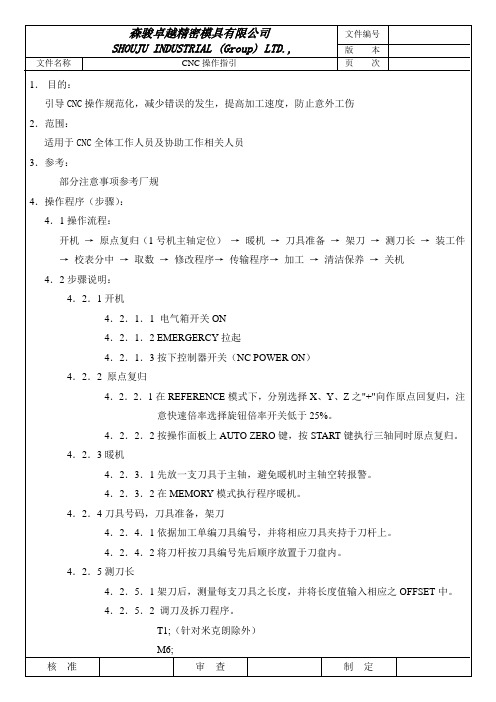
4.2.10.1手动关机:将主轴移至床台中间,按下操作面板顶部之POWER OFF,待其闪亮后松开,机台内部自动执行关机循环,约2分钟后自动切断总电源。
4.2.10.2自动关机:将操作面板之POWER OUT按下,灯亮,则程序执行到M30或M02时,自动开启关机循环,约1分钟后自动切断总电源。
4.2.7.3找出X、Y的工作原点,在HANDLE模式,将X、Y轴移至X0Y0即工作原点。
4.2.7.4定G54之X、Y值。
OFFSET→WORKX0→MEASUR→Y0→MEASUR,即可将X0Y0之机械坐标值输入至G54坐标中。
4.2.8呼叫第一支刀T1,用1个ψ6刀柄之刀具放在工件表面上,以T1刀具不能通过时往上0.01mm处设为REL坐标之Z6.(因本公司用ψ6刀杆对刀),查看第一刀之刀长补正值H1,将Z轴移至REL坐标Z0时的机械坐标值扣除H1值后输入至G54,Z之坐标补正设定完成。
4.2.9传输程序,加工
4.2.9.1手写程序加工
在EDIT模式下,输入已编写完整之程序,并提高刀具20~50mm处试运行程序,正确后在MEMORY模式下按START键运行。
4.2.9.2CAM程序加工
4.2.9.2.1调出加工程序
4.2.9.2.2根据刀具之加工顺序,修改程序之刀号,根据刀具的大小,程序之加工进给量即F值的大小修改转速S****值,根据文件在DATA SERVER中之程序号修改呼叫程序的参数。
4.2.5.2调刀及拆刀程序。
T1;(针对米克朗除外)
M6;
G65P9623 H1. D2;
M30
H刀具长度输入此补偿号
D刀具半径输入此补偿号
4.2.6子程序更改与传送
4.2.6.1在PC修改子程序F值及M99并加入G05P10000及G05 P0
项目工作页-任务2 数控机床参数设置与调试

能够识记数控机床参数的种类、数据类型、结构形式,理解其在数控机床控制中的作用。
能进行修改数控机床参数,掌握常见数控机床基本参数的设置,能对伺服初始化参数进行设置和操作。
二、任务描述通过本项工作任务实施,学习数控机床参数及作用,识记数控系统参数、机床参数、伺服参数、PLC参数、设备接口参数、螺补参数的存储形式,了解参数对数控系统与机床运行的作用及影响。
能够操作伺服初始化参数的设置。
三、工作目标1、掌握数控机床常用基本参数的设置。
2、掌握伺服始化参数的设置,分析在数控机床运行时的作用。
3、发挥团队合作精神,会修改数控机床、数控系统等参数。
四、任务准备(一)团队组成方案每4人分为一组,每组指定1人为小组长,1人为材料管理员,2人为技术员,小组长负责组织本组任务实施及结果汇报,并负责安全生产。
材料员负责材料领取分发,填写所需材料、工具的相关记录表,并负责工具的保养。
组长、材料员与技术员共同合作进行项目的实施。
(二)仪器、仪表、工具、材料准备万用表一只,螺丝刀一套。
(三)相关理论知识1、参数设定画面用于参数的设置、修改等操作,在操作时需要打开参数开关,按OFSSET键显示图示画面就可以进行修改参数开关,参数开关为1时,可以进入参数进行修改。
图参数开关画面图参数画面1)诊断画面当出现报警时,可以通过诊断画面进行故障的诊断,按上图中的诊断键,如下图所示。
图 诊断画面2、机床常用的参数名称含义1) 数控机床与轴有关的参数:参数号1020: 表示数控机床各轴的程序名称,如在系统显示画面显示的X 、Y 、Z 等,一般设置是,车床为88,90;铣床与加工中心为88,89,90参数号1022: 表示数控机床设定各轴为基本坐标系中的哪个轴,一般设置为1,2,3参数号1023: 表示数控机床各轴的伺服轴号,也可以称为轴的连接顺序,一般设置为1,2,3,设定各控制轴为对应的第几号伺服轴参数号8130:表示数控机床控制的最大轴数轴数CNC 控制的最大轴数2)数控机床与存储行程检测相关的参数:1320:各轴的存储行程限位1的正方向坐标值。
MZN M64 CNC X-Z原点设置
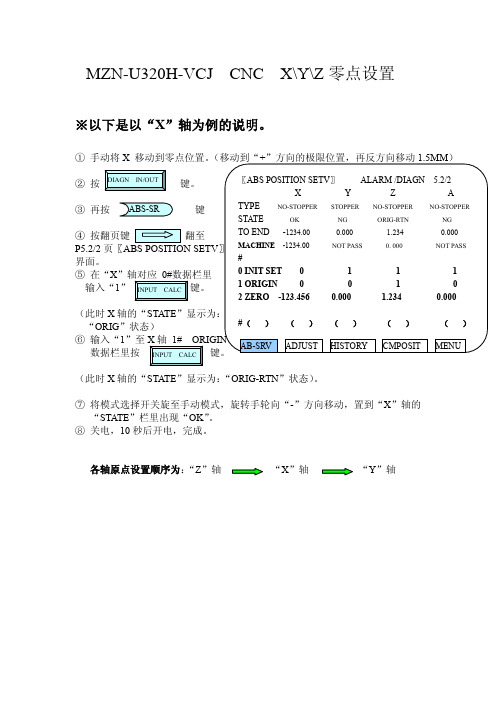
键
V
④ 按翻页键
翻至
P5.2/2 页〖ABS POSITION SETV〗 界面。
⑤ 在“X”轴对应 0#数据栏里 输入“1” INPU。T CALC 键。
TYPE NO-STOPPER
STATE
OK
TO END -1234.00
MACHINE -1234.00
#
0 INIT SET 0
1 ORIGIN 0
⑧ 关电,10 秒后开电,完成。
各轴原点设置顺序为:“Z”轴
“X”轴
“Y”轴
⑥ 输入“1”至 X 轴 1# ORIGIN 数据栏里按 INPUT CALC 键。
#( ) AB-SRV
() ADJUST
() HISTORY
() CMPOSIT
() MENU
(此时 X 轴的“STATE”显示为:“ORIG-RTN”状态)。
⑦ 将模式选择开关旋至手动模式,旋转手轮向“-”方向移动,置到“X”轴的 “STATE”栏里出现“OK”。
2 ZERO -123.456
STOPPER NG 0.000
NOT PASS
Байду номын сангаас
NO-STOPPER ORIG-RTN 1.234 0. 000
1 0 0.000
1 1 1.234
NO-STOPPER NG 0.000
NOT PASS
1 0 0.000
(此时 X 轴的“STATE”显示为: “ORIG”状态)
MZN-U320H-VCJ CNC X\Y\Z 零点设置
※以下是以“X”轴为例的说明。
① 手动将 X 移动到零点位置。(移动到“+”方向的极限位置,再反方向移动 1.5MM)
g92指令编程实例详解

g92指令编程实例详解引言:在CNC加工中,g92指令是一条常用的指令,用于设定工件坐标系原点,具有重要的作用。
本文将通过一个实例来详解g92指令的使用方法和注意事项。
一、g92指令的基本概念g92指令是一条模态指令,用于设定工件坐标系的原点。
它的一般格式为“g92 Xx Yy Zz”,其中X、Y、Z分别表示X轴、Y轴和Z 轴的坐标值。
通过设置这些坐标值,可以将工件坐标系的原点定位到任意位置。
二、g92指令的应用实例假设我们需要在一块工件上进行孔加工,该工件的尺寸为100mm×100mm,孔的位置需要相对于工件中心点进行定位。
现在,我们将通过g92指令来实现这个功能。
1. 首先,我们需要将刀具移到工件的中心位置,即X轴和Y轴坐标为50mm。
这可以通过以下代码实现:G00 X50 Y502. 接下来,我们使用g92指令将工件坐标系的原点设置为当前刀具位置,即X轴和Y轴坐标为0,Z轴坐标为当前刀具高度。
代码如下:G92 X0 Y0 Z[Z轴坐标]3. 现在,我们可以开始进行孔加工了。
假设每个孔的直径为10mm,我们需要在X轴和Y轴方向上每隔20mm加工一个孔。
代码如下:G01 X10 Y0 F100G01 X0 Y10 F100G01 X-10 Y0 F100G01 X0 Y-10 F1004. 完成孔加工后,我们需要将刀具移动到安全位置。
代码如下:G00 X0 Y0三、g92指令的注意事项1. 在使用g92指令时,需要注意刀具的位置和工件坐标系的原点位置。
刀具位置应该与工件坐标系的原点位置相对应,否则会导致加工错误。
2. 在使用g92指令时,需要确保刀具的高度正确。
可以通过测量工件上的参考点来确定刀具高度,并在g92指令中设置Z轴坐标值。
3. 在使用g92指令后,需要注意是否有其他指令影响了工件坐标系的原点位置。
如果有,需要进行相应的处理,以保证加工的准确性。
结论:通过以上实例,我们详细了解了g92指令的使用方法和注意事项。
FANUC机床CNC操作面板说明

AUTOMATIC(RIGHT/LEFT/LOADER):在自动模式下操作和编辑程序。
CO-OPE(RIGHT/LEFT/LOADER):用于在CO-OPE模式下操作左/右轴和机械手。也用语自动回机械原点。
MACHINE RESDY:按此按钮后,液压电机开始运转。如果灯亮,CNC单元和机床也准备开始工作。
LEFT MODE:按MANUAL后,按此按钮表示左打塔有效,并且在屏幕上显示的左刀塔的数据。
RIGHT MODE:按MANUAL后,按此按钮表示右打塔有效,并且在屏幕上显示的右刀塔的数据。
CHUCK CLOSE/OPEN:关闭/打开主卡盘。
MACHINE GUIDE:显示条件和操作机床及机械手。
MENU:显示上述功能按钮的内容。
软键结构
有四种软键:章节选择键、操作选择键、回菜单键、继续菜单键。按CNC操作面板上的功能按钮,在屏幕底部显示每个条款,按对应的软键显示相应的屏幕。
MESSAGE:ALART-显示NC报警信息。HISTORY-显示报警历史资料。
FANUC MW系列机床CRT/MDI面板说明
INPUT:用于输入数据、刀具补偿、参数,也用于将数据输入I/O单元。
CAN:删除
POS:显示当前点位置,绝对坐标、相对坐标及混合。
PROG:在编辑模式下,显示所有存储的程序。在设置状态,显示MDI操作数据。在自动操作时,显示当前执行的程序。
OFFSET/SETTING:用于刀具补偿数据输入、数据设置、显示几何补偿。
SYSTEM:显示NC参数、特征、梯形图。
MESSAGE:显示NC报警信息和历史资料。
fanuc原点的设定方法

fanuc原点的设定方法Fanuc原点的设定方法Fanuc原点的设定是CNC加工中非常重要的一步,它确定了工件坐标系与机床坐标系的关系,对于后续的加工操作具有决定性的影响。
下面将详细介绍Fanuc原点的设定方法。
一、Fanuc原点的概念Fanuc原点是指机床坐标系中的零点位置,也可以称之为零点坐标。
在Fanuc系统中,通常有三个原点,分别是X轴原点、Y轴原点和Z轴原点。
根据机床的不同类型和控制系统的不同,Fanuc原点的设定方法也有所区别。
二、Fanuc原点设定的准备工作在设定Fanuc原点之前,需要进行一些准备工作,以确保设定的准确性和安全性。
1. 确定机床的固定位置:机床在设定Fanuc原点时需要保持稳定的位置,确保不会发生移动或晃动。
2. 检查机床的零件状态:检查机床的各个零件是否完好,如导轨、螺杆等,确保没有松动或损坏的情况。
3. 清理机床工作台面:清理机床的工作台面,确保上面没有杂物或残留物。
三、Fanuc原点的设定方法1. 打开Fanuc控制面板:按下机床上的电源开关,打开Fanuc控制面板。
2. 进入原点设定界面:在控制面板上选择“参数设置”菜单,进入参数设置界面。
3. 选择轴向参数设定:在参数设置界面中选择“轴向参数设定”选项,进入轴向参数设定界面。
4. 选择原点设定功能:在轴向参数设定界面中选择“原点设定”功能,进入原点设定界面。
5. 选择需要设定的轴向:在原点设定界面中选择需要设定的轴向,如X轴、Y轴或Z轴。
6. 移动轴向到设定位置:根据实际需求,通过手动操作或使用机床的快速移动功能,将选定的轴向移动到设定位置。
7. 确定设定位置:当轴向移动到设定位置后,按下“确定”按钮,确认设定位置。
8. 完成设定:完成一个轴向的设定后,可以选择设定其他轴向的原点,或者退出设定界面。
四、Fanuc原点设定的注意事项在进行Fanuc原点设定时,需要注意以下几点,以确保设定的准确性和安全性。
1. 设定前确认坐标轴位置:在设定Fanuc原点之前,应该先确认坐标轴的起始位置,确保设定的位置不会超出机床的工作范围。
- 1、下载文档前请自行甄别文档内容的完整性,平台不提供额外的编辑、内容补充、找答案等附加服务。
- 2、"仅部分预览"的文档,不可在线预览部分如存在完整性等问题,可反馈申请退款(可完整预览的文档不适用该条件!)。
- 3、如文档侵犯您的权益,请联系客服反馈,我们会尽快为您处理(人工客服工作时间:9:00-18:30)。
CNC原点设置这里详细地介绍了发那克,三菱,西门子几种常用数控系统参考点的工作原理、调整和设定方法,并举例说明参考点的故障现象,解决方法。
相对位置检测系统绝对位置检测系统前言:当数控机床更换、拆卸电机或编码器后,机床会有报警信息:编码器内的机械绝对位置数据丢失了,或者机床回参考点后发现参考点和更换前发生了偏移,这就要求我们重新设定参考点,所以我们对了解参考点的工作原理十分必要。
参考点是指当执行手动参考点回归或加工程序的G28指令时机械所定位的那一点,又名原点或零点。
每台机床有一个参考点,根据需要也可以设置多个参考点,用于自动刀具交换(A TC)、自动拖盘交换(APC)等。
通过G28指令执行快速复归的点称为第一参考点(原点),通过G30指令复归的点称为第二、第三或第四参考点,也称为返回浮动参考点。
由编码器发出的栅点信号或零标志信号所确定的点称为电气原点。
机械原点是基本机械坐标系的基准点,机械零件一旦装配好,机械参考点也就建立了。
为了使电气原点和机械原点重合,将使用一个参数进行设置,这个重合的点就是机床原点。
机床配备的位置检测系统一般有相对位置检测系统和绝对位置检测系统。
相对位置检测系统由于在关机后位置数据丢失,所以在机床每次开机后都要求先回零点才可投入加工运行,一般使用挡块式零点回归。
绝对位置检测系统即使在电源切断时也能检测机械的移动量,所以机床每次开机后不需要进行原点回归。
由于在关机后位置数据不会丢失,并且绝对位置检测功能执行各种数据的核对,如检测器的回馈量相互核对、机械固有点上的绝对位置核对,因此具有很高的可信性。
当更换绝对位置检测器或绝对位置丢失时,应设定参考点,绝对位置检测系统一般使用无挡块式零点回归。
一:使用相对位置检测系统的参考点回归方式:1 发那克系统:1)工作原理:当手动或自动回机床参考点时,首先,回归轴以正方向快速移动,当挡块碰上参考点接近开关时,开始减速运行。
当挡块离开参考点接近开关时,继续以FL速度移动。
当走到相对编码器的零位时,回归电机停止,并将此零点作为机床的参考点。
2)相关参数:参数内容系统0i/16i/18i/21i 0所有轴返回参考点的方式:0. 挡块、1. 无挡块 1002.1 0076各轴返回参考点的方式:0. 挡块、1. 无挡块1005.1 0391各轴的参考计数器容量 1821 0570~************每轴的栅格偏移量 1850 0508~0511 0640 0642 7508 7509是否使用绝对脉冲编码器作为位置检测器:0. 不是、1. 是1815.5 0021 7021绝对脉冲编码器原点位置的设定:0. 没有建立、1. 建立1815.4 0022 7022位置检测使用类型:0.内装式脉冲编码器、1. 分离式编码器、直线尺 1815.1 0037 7037快速进给加减速时间常数 1620 0522快速进给速度1420 0518~0521FL速度1425 0534手动快速进给速度 1424 0559~0562伺服回路增益1825 05173)、设定方法:a、设定参数:所有轴返回参考点的方式=0;各轴返回参考点的方式=0;各轴的参考计数器容量,根据电机每转的回馈脉冲数作为参考计数器容量设定;是否使用绝对脉冲编码器作为位置检测器=0 ;绝对脉冲编码器原点位置的设定=0;位置检测使用类型=0;快速进给加减速时间常数、快速进给速度、FL速度、手动快速进给速度、伺服回路增益依实际情况进行设定。
b、机床重启,回参考点。
c、由于机床参考点与设定前不同,重新调整每轴的栅格偏移量。
4)故障举例:一台0i-B机床X轴手动回参考点时出现90号报警(返回参考点位置异常)。
a、机床再回一次参考点,观察X轴移动情况,发现刚开始时X轴不是快速移动,速度很慢;b、检测诊断号#300,<128;d、检查手动快速进给参数1424,设定正确;e、检查倍率开关ROV1、ROV2信号,发现倍率开关坏,更换后机床正常。
2 三菱系统:1)工作原理:机床电源接通后第一次回归参考点,机械快速移动,当参考点检测开关接近参考点挡块时,机械减速并停止。
然后,机械通过参考点挡块后,缓慢移动到第一个栅格点的位置,这个点就是参考点。
在回参考点前,如果设定了参考点偏移参数,机械到达第一个栅格点后继续向前移动,移动到偏移量的点,并把这个点作为参考点。
2)相关参数:参数内容系统M60 M64快速进给速度 2025慢行速度2026参考点偏移量 2027栅罩量 2028栅间隔 2029参考点回归方向20303)设定方法:a、设定参数:参考点偏移量=0栅罩量=0栅间隔=滚珠导螺快速进给速度、慢行速度、参考点回归方向依实际情况进行设定。
b、重启电源,回参考点。
C、在|报警/诊断|→|伺服|→|伺服监视(2)|,计下栅间隔和栅格量的值。
d、计算栅罩量:当栅间隔/2<栅格量时,栅罩量=栅格量-栅间隔/2当栅间隔/2>栅格量时,栅罩量=栅格量+栅间隔/2e、把计算值设定到栅罩量参数中。
f、重启电源,再次回参考点。
g、重复c、d过程,检查栅罩量设定值是否正确,否则重新设定。
h、根据需要,设定参考点偏移量。
4)故障举例:一台三菱M64系统钻削中心,Z轴回参考点时发生过行程报警。
a、检查参考点检测开关信号,当移动到参考点挡块位置时,能够从“0”变为“1”;b、检查栅罩量参数(2028),正常;检查参考点偏移量参数(2027),正常;检查参考点回归方向参数(2030),和其它同型号机床核对,发现由反方向“1”变成了同方向“0”,改正后,重启回参考点,正常。
3、西门子系统:1) 工作原理:机床回参考点时,回归轴以Vc速度快速向参考点文件块位置移动,当参考点开关碰上挡块后,开始减速并停止,然后反方向移动,退出参考点挡块位置,并以Vm速度移动,寻找到第一个零脉冲时,再以Vp速度移动Rv参考点偏移距离后停止,就把这个点作为2)相关参数:参数内容系统802D/810D/840D返回参考点方向MD34010寻找参考点开关速度(Vc) MD34020寻找零脉冲速度(Vm)MD34040寻找零脉冲方向MD34050定位速度(Vp)MD34070参考点偏移(Rv) MD34080参考点设定位置(Rk)MD341003)设定方法:a、设定参数:返回参考点方向参数、寻找零脉冲方向参数根据挡块安装方向等进行设定;寻找参考点开关速度(Vc)参数设定时,要求在该速度下碰到挡块后减速到“0”时,坐标轴能停止在挡块上,不要冲过挡块;参考点偏移(Rv)参数=0b、机床重启,回参考点。
C、由于机床参考点与设定前不同,重新调整参考点偏移(Rv)参数。
4、故障举例:一台西门子810D系统,机床每次参考点返回位置都不一致,从以下几项逐步进行排查:a、伺服模块控制信号接触不良;b、电机与机械联轴节松动;C、参数点开关或挡块松动;d、参数设置不正确;е、位置编码器供电电压不低于4.8V;f、位置编码器有故障;g、位置编码器回馈线有干扰;最后查到参考点挡块松动,拧紧螺丝后,重新试机,故障排除。
二:绝对位置检测系统:1. 发那克系统:1)工作原理:绝对位置检测系统参考点回归比较简单,只要在参考点方式下,按任意方向键,控制轴以参考点间隙初始设置方向运行,寻找到第一个栅格点后,就把这个点设置为参考点。
2)相关参数系统0i/16i/18i/21i 0所有轴返回参考点的方式:0. 挡块、1. 无挡块 1002.1 0076各轴返回参考点的方式:0. 挡块、1. 无挡块1005.1 0391各轴的参考计数器容量 1821 0570~************每轴的栅格偏移量 1850 0508~0511 0640 0642 7508 7509 是否使用绝对脉冲编码器作为位置检测器:0. 不是、1. 是 1815.5 0021 7021绝对脉冲编码器原点位置的设定:0. 没有建立、1. 建立 1815.4 0022 7022位置检测使用类型:0.内装式脉冲编码器、1. 分离式编码器、直线尺 1815.1 0037 7037快速进给加减速时间常数 1620 0522快速进给速度1420 0518~0521FL速度1425 0534手动快速进给速度 1424 0559~0562伺服回路增益1825 0517返回参考点间隙初始方向0. 正1. 负 1006 0003 7003 00663)设置方法:a、设定参数:所有轴返回参考点的方式=0;各轴返回参考点的方式=0;各轴的参考计数器容量,根据电机每转的回馈脉冲数作为参考计数器容量设定;是否使用绝对脉冲编码器作为位置检测器=0 ;绝对脉冲编码器原点位置的设定=0;位置检测使用类型=0;快速进给加减速时间常数、快速进给速度、FL速度、手动快速进给速度、伺服回路增益依实际情况进行设定;b、机床重启,手动回到参考点附近;c、是否使用绝对脉冲编码器作为位置检测器=1 ;绝对脉冲编码器原点位置的设定=1;e、机床重启;f、由于机床参考点与设定前不同,重新调整每轴的栅格偏移量。
2、三菱系统(M60、M64为例):1)、无挡块机械碰压方式:a、设定参数:#2049.=1 无檔块机械碰压方式;#2054 电流极限;b、选择“绝对位置设定”画面,选择手轮或寸动模式,(也可选择自动初期化模式);C、在“绝对位置设定”画面,选择“可碰压”;d、#0绝对位置设定=1 ,#2原点设定:以基本机械坐标为准,设定参考点的坐标值;e、移动控制轴,当控制轴碰压上机械挡块,在给定时间内达到极限电流时,控制轴停止并反方向移动。
如果b步选择手轮或寸动模式,则控制轴反方向移动移动到第一栅格点,这个点就是电气参考点;如果b步选择“自动初期化”模式,则在第a步还要设置#2005碰压速度参数和#2056接近点值,此时控制轴反方向以#2005(碰压速度)移动到#2056(接近点)值停止,再以#2055(碰压速度)向挡块移动,在给定时间内达到极限电流时,控制轴停止并以反方向移动到第一栅格点,这个点就是电气参考点;g、重启电源。
2)无挡块参考点方式调整:a、设定参数:#2049 =2 无挡块参考点调整方式;#2050 =0 正方向、=1 负方向;b、选择“绝对位置设定”画面,选择手轮或寸动模式;c、在“绝对位置设定”画面,选择“无碰压”方式;d、#0绝对位置设定=1 ,#2原点设定:以基本机械坐标为准,设定参考点的坐标值;e、把控制轴移动到参考点附近。
f、#1 =1,控制轴以#2050设置方向移动,达到第一个栅格点时停止,把这个点设定为电气参考点。
g、重启电源。
3 西门子系统(802D、810D、840D为例):1)调试;a、设置参数:MD34200=0.绝对编码器位置设定; MD34210=0.绝对编码器初始状态;b、选择“手动”模式,将控制轴移动到参考点附近;c、输入参数:MD34100,机床坐标位置;d、激活绝对编码器的调整功能:MD34210=1.绝对编码器调整状态;e、按机床复位键,使机床参数生效;f、机床回归参考点;g、机床不移动,系统自动设置参数:34090. 参考点偏移量;34210. 绝对编码器设定完毕状态,屏幕上显示位置是MD34100设定位置。