FC倒装芯片装配技术介绍
fc封装工艺

FC封装工艺是一种先进的电子封装技术,其主要应用于高密度、高速、高可靠性的电路设计及制造中。
以下是FC 封装工艺的主要步骤和特点:底部金属化处理:在基板上涂覆金属化膜层,以增强基板的导电性。
触点制备:在基板上制造小孔,以便连接电路和封装。
铜箔层叠:在基板上铺设一层铜箔,并在其上涂覆一层绝缘涂层。
光刻蚀刻:通过光刻技术在涂有光刻胶的铜箔上形成电路图形。
去底填料:去除光刻胶并清洗铜箔表面,以便进行后续处理。
芯片倒装:将芯片倒装焊在基板上,通过焊料实现芯片与基板的连接。
填充底部填充料:将底部填充料倒入芯片与基板之间,以保护焊点并提高封装可靠性。
固化处理:将封装件放入固化炉中进行底部填充料的固化。
测试与检验:对封装件进行电气性能测试和外观检验,确保其符合要求。
声表面波器件工艺原理-9倒装焊工艺原理

九,声表器件倒装焊工艺原理序:倒装芯片(FC)技术,是在芯片的焊接区金属上制作凸焊点,然后将芯片倒扣在外壳基座上,以实现机械性能和电性能的连接,由于FC是通过凸焊点直接与底座相连,因此与其它互连技术相比,FC具有最高的封装密度、最小的封装尺寸(线焊可焊的最小陶瓷外壳为3×3mm,而FC可以作到芯片级)、最好的高频性能(电感小)、最小的高度、最轻的重量,以及产品高可靠、生产高工效等。
倒装焊工艺:主要由UBM的形成、凸点的制作、倒装焊接三部分组成。
(一)UBM的形成:当凸焊点材料与芯片上的焊接区金属不能很好浸润粘附时(或接触电阻大,或热匹配差,或两种材料间易形成会导致键合强度降低的金属间化合物),需要在凸焊点与芯片压焊块之间置入一层既能与芯片焊接区金属良好粘附、又能与凸焊点良好浸润、还能有效阻挡两者之间相互反应扩散的金属膜(UBM),因我们无法找到可同时满足上述要求的材料,所以通常UBM由多层金属膜组成。
(说明:与凸点连接的还有底座上相应的焊接点,由于在底座制作时该部位已镀有多层金属,能满足要求,固在此不于讨论。
)1,对UBM的各层要求及材料选择:1)粘附层:要求与铝膜及钝化层间的粘附性好,低阻接触,热膨涨系数接近,热应力小。
常选用材料有:Cr、Ti、Ti-W、Al、V等,因它们与Al浸润性很好,固该层可较薄。
2)扩散阻挡层:能有效阻挡凸焊点材料与铝间的相互扩散,以免形成不利的金属间化合物,特别是金凸焊点,在高温下与铝可生成Al2Au、AlAu、AlAu2、Al2Au5等脆性金属间化合物及在接触处相互扩散形成空洞,导致键合强度降低甚至失效。
该层常用材料有:Ti、Ni、Cu、Pd、Pt、Ti-W等。
(当用软焊料如PbSn作凸点时,由于其回流时会吃掉浸润层,直接与阻挡层接触;此时阻挡层应足够厚,且与凸点相浸润,不反应产生有害物)3)浸润层:要求一方面能和凸焊点材料良好浸润,可焊性好,且不会形成不利于键合的金属间化合物;另一方面还能保护粘附层和阻挡层金属不被氧化、粘污。
FC装配技术
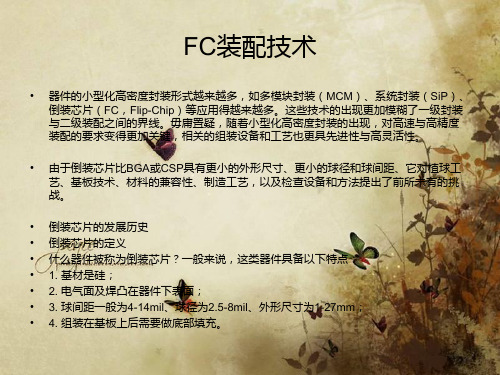
• •
• • • • •
对贴装精度及稳定性的要求 对于球间距小到0.1mm的器件,需要怎样的贴装精度才能达到较高的良率? 基板的翘曲变形,阻焊膜窗口的尺寸和位置偏差,以及机器的精度等,都会 影响到最终的贴装精度。关于基板设计和制造的情况对于贴装的影响,我们 在此不作讨论,这芯片装配工艺对贴装设备的要求里我们只是来讨论机器的 贴装精度。为了回答上面的问题,我们来建立一个简单的假设模型: 1.假设倒装芯片的焊凸为球形,基板上对应的焊盘为圆形,且具有相同的直 径; 2.假设无基板翘曲变形及制造缺陷方面的影响; 3.不考虑Theta和冲击的影响; 4.在回流焊接过程中,器件具有自对中性,焊球与润湿面50%的接触在焊接 过程中可以被“拉正” 那么,基于以上的假设,直径μ的焊25m球如果其对应的圆形焊盘的直径为 50μm时,左右位置偏差(X轴)或 前后位置偏差(Y轴)在焊盘尺寸的50%, 焊球都始终在焊盘上(图9)。对于焊球直径为25μm的倒装芯片,工艺能力 Cpk要达到1.33的话,要求机器的最小精度必须达到12μm@3sigma。
• •
•
•
倒装芯片的装配工艺流程介绍 相对于其它的IC器件,如BGA、CSP等,倒装芯片装配工艺有其特殊性,该 工艺引入了助焊剂工艺和底部填充工艺。因为助焊剂残留物(对可靠性的影 响)及桥连的危险,将倒装芯片贴装于锡膏上不是一种可采用的装配方法。 业内推出了无需清洁的助焊剂,芯片浸蘸助焊剂工艺成为广泛使用的助焊技 术。目前主要的替代方法是使用免洗助焊剂,将器件浸蘸在助焊剂薄膜里让 器件焊球蘸取一定量的助焊剂,再将器件贴装在基板上,然后回流焊接;或 者将助焊剂预先施加在基板上,再贴装器件与回流焊接。助焊剂在回流之前 起到固定器件的作用,回流过程中起到润湿焊接表面增强可焊性的作用。 倒装芯片焊接完成后,需谄骷撞亢突逯涮畛湟恢纸海ㄒ话阄费跏 黪ゲ牧希5撞刻畛浞治凇懊噶鞫怼钡牧鞫院头橇鞫裕∟ofollow)底部填充。 上述倒装芯片组装工艺是针对C4器件(器件焊凸材料为SnPb、SnAg、SnCu 或SnAgCu)而言。另外一种工艺是利用各向异性导电胶(ACF)来装配倒 装芯片。预先在基板上施加异性导电胶,贴片头用较高压力将器件贴装在基 板上,同时对器件加热,使导电胶固化。该工艺要求贴片机具有非常高的精 度,同时贴片头具有大压力及加热功能。 对于非C4器件(其焊凸材料为Au 或其它)的装配,趋向采用此工艺。这里,我们主要讨论C4工艺,下表列出 的是倒装芯片植球(Bumping)和在基板上连接的几种方式。
倒装封装(FC)方案(一)

倒装封装(FC)方案背景与目标随着中国半导体产业的快速发展,传统封装技术已无法满足市场对高性能、高可靠性产品的需求。
倒装封装(FC)技术作为第三代封装技术,具有高密度、高性能、低成本等优势,成为产业结构改革的重要方向。
本方案旨在推广倒装封装技术在中国的应用,促进半导体产业的发展。
工作原理倒装封装(FC)技术是一种基于芯片底部连接的封装方法。
通过在芯片底部制作凸点,实现与基板的连接。
该技术可实现更高的I/O密度、更短的连接距离和更好的电性能。
此外,FC技术还具有高可靠性和低成本的优点。
实施计划步骤1.技术研究与开发(R&D): 首先,进行必要的技术研究与开发,包括凸点制作、芯片与基板连接技术、底部填充材料等关键技术。
2.设备采购与调试: 根据技术要求,采购相应的生产设备,并进行调试与验证,确保设备的稳定性和可靠性。
3.小批量试产: 在技术验证通过后,进行小批量试产,进一步验证生产流程和产品性能。
4.大规模量产: 在小批量试产成功后,进行大规模量产,以满足市场需求。
5.持续改进与优化: 根据市场反馈和生产数据,不断优化生产工艺和流程,提高产品质量和生产效率。
适用范围倒装封装技术适用于多种领域,如移动通信、汽车电子、云计算等。
特别是对于高性能、高可靠性、低成本的产品需求,倒装封装具有显著优势。
创新要点1.凸点制作技术创新: 开发适用于倒装封装的凸点制作技术,实现高密度、高性能的连接。
2.材料选择与优化: 选择合适的底部填充材料和其他相关材料,确保产品的可靠性和性能。
3.生产流程优化: 通过工艺研究和设备调试,实现生产流程的优化,提高生产效率和产品质量。
4.市场推广与应用拓展: 加强与客户的沟通和合作,将倒装封装技术推广到更多领域和应用场景。
预期效果预计通过本方案的实施,可以带来以下预期效果:1.提高半导体产业的技术水平和竞争力;2.促进中国半导体产业的结构改革和升级;3.满足市场对高性能、高可靠性产品的需求;4.提高企业的生产效率和产品质量;5.增强中国半导体产业的国际竞争力。
FC简介

B. 压力烘箱原理视图:
C. Underfill 点胶模拟(Glass die):
Underfill 点胶视图
14
Thanks!
点胶机:Protec
Normal & Pressure烘箱
Nozzle Epoxy PCB
点胶前
Underfill
点胶后
SAT扫描
13
倒装芯片封测流程
Underfill (底部填充-CUF):
A. 毛细作用及原理视图:指液体在细管状 物体内侧,由于内聚力与附着力的差异、 克服地心引力而上升的现象;
倒装芯片封测流程
Pre-bake
基板预烘烤 锡膏印刷 表面贴装
UF Pre-bake Plasma UF
UF预烘烤 离子清洗 UF点胶 UF胶固化
Chip mount 上板&S/M Pre-bake FCA Reflow
SMT
Printing
UF
上Carrier 基板预烘烤 芯片倒装 回流炉 去Flux清洗 Fail
UF Cure
SAT 清洗 烘烤 3/O QA
Pass 3rd 检验 QA 3rd 检验 下Carrier
SAT抽检 抽检基板清洗 抽检基板除湿
FCA
Deflux
下板
倒装芯片封测流程
Surface Mount Technology (表面元件贴装):
通过锡膏印刷的方式进行元件贴装,将电容、电阻、电感等元器件贴焊于基板上.
Die attach
Process simulation
倒装芯片封测流程
Flipchip Attach (芯片倒装):
芯片倒装Process 产品贴装之后通过X-ray确认芯片贴装效果,含芯片偏移/虚焊/桥接 /Bump空洞等确认项.
倒装封装(FC)方案(二)

倒装封装(FC)方案一、实施背景随着中国制造业的持续发展,对于先进封装技术的需求日益增强。
倒装封装(FC)作为一种具有高密度、高可靠性、高性能的封装技术,已在中国半导体产业中占据了重要地位。
然而,面对国际竞争的挑战和国内产业结构的转型需求,中国需要进一步优化倒装封装的产业结构,提高自主创新能力,以实现产业升级。
二、工作原理倒装封装(FC)是一种将芯片直接放置在具有高导热性能的基板上,通过引脚与基板相连的封装方式。
其工作原理主要依赖于芯片与基板间的热膨胀系数(CTE)匹配,以及焊接点的可靠性。
通过选择与芯片和基板都具有良好相容性的材料,实现芯片与基板的可靠连接,同时优化引脚布局,提高电学性能。
三、实施计划步骤1.技术研发:加大研发投入,集中力量突破关键技术难题,开发具有自主知识产权的倒装封装技术和设备。
2.产学研合作:推动企业与高校、研究机构的深度合作,共同建设技术研发平台,共享资源,提高技术成果转化效率。
3.产业结构调整:优化上下游企业的布局,培育一批具有国际竞争力的倒装封装产业链主导企业,引导产业集聚,形成产业生态。
4.市场推广:鼓励企业拓展市场,推广倒装封装产品在各领域的应用,特别是在5G、物联网、人工智能等新兴产业的推广。
四、适用范围倒装封装技术适用于各种需要高可靠性、高密度、高性能封装的领域,如消费电子、通信设备、航空航天、汽车电子等。
特别是在需要高导热性能和微型化封装的领域中,倒装封装具有显著的优势。
五、创新要点1.材料创新:研发新型高导热性能材料,提高芯片与基板的热传导性能。
2.工艺创新:优化倒装封装的生产工艺,提高生产效率,降低成本。
3.设计创新:根据实际应用需求,设计更先进的倒装封装结构,提高封装的电学性能和机械可靠性。
4.系统集成创新:将倒装封装技术与其它先进技术相结合,如MEMS、3D封装等,开发出更先进的系统集成产品。
六、预期效果1.提高产业竞争力:通过技术创新和产业结构调整,提高中国倒装封装产业的国际竞争力。
封装工艺中倒装(FC)工艺和材料介绍
Temperature vs. Viscosity, Flow Rate
3
2.5
2
1.5
80-100°C is
1
recommended
0.5
0
60
80
100
120
PCB Prebake UF plasma clean
Underfill Underfill cure
Reduces underfill viscosity
By substrate topography
Flux residue
By moisture contamination
By cleaning residue
Major defects in Flipchip and UF
▶ Moisture Void
Major defects in Flipchip and UF
▷ Substrate type ▷ Plasma condition: Power (watt) & Time ▷ Heat block temperature ▷ Dispensing pattern
Causes
Countermeasures
Because of weak interaction
Why use flip chip?
Smallest Size Highest Performance Greatest I/O Flexibility Most Rugged Lowest Cost
Process flow of Super FC
FOL 2 (Memory)
Wafer Backgrind 2 Wafer Mount 2 Wafer Saw 2
半导体fc工艺
半导体fc工艺哎呀,半导体FC工艺,这玩意儿听起来就挺高大上的,不过别急,我今儿个就给你聊聊这个,保证让你听得明明白白,还能乐呵乐呵的。
话说,这半导体工艺啊,就像做蛋糕一样,得一层一层来。
FC工艺呢,就是其中的一个步骤,全名叫“Flip Chip”工艺,直译过来就是“翻转芯片”。
这名字听起来是不是有点搞笑?芯片还能翻转?别急,听我慢慢道来。
首先,这FC工艺,其实就是把芯片的底部金属焊盘翻转过来,直接和电路板连接的一种技术。
这就好比你把一张纸翻过来,然后在背面写上字一样。
不过,这芯片可比纸复杂多了,它上面密密麻麻的都是电路,一不小心,那可就全乱套了。
我记得有一次,我在实验室里,亲眼目睹了这FC工艺的全过程。
那是个阳光明媚的下午,实验室里静悄悄的,只有机器运转的声音。
我看着那些工程师,他们一个个都穿着白大褂,戴着手套,眼睛盯着显微镜,手里拿着那些比米粒还小的芯片,小心翼翼地翻转、焊接。
那场景,简直就像是在做一场精细的手术。
我看着他们,心里不由得佩服。
这FC工艺,可不仅仅是翻转那么简单,它还得保证芯片和电路板之间的连接完美无缺。
这就好比你在纸上写字,不仅要写得好看,还不能写错一个字。
而且,这FC工艺还有个特别的地方,就是它用的是一种叫做“焊球”的东西。
这些焊球,就像是一个个小小的金色珠子,它们在高温下融化,然后迅速凝固,把芯片和电路板牢牢地粘在一起。
这个过程,就像是在做糖葫芦,只不过这糖葫芦不是给人吃的,而是给机器用的。
说到这,我突然想起了小时候,妈妈给我做的糖葫芦。
那时候,我总是站在厨房门口,看着妈妈把一颗颗山楂串起来,然后裹上糖浆。
那糖浆在锅里咕嘟咕嘟地冒着泡,散发出诱人的香味。
我那时候就想,这半导体FC工艺,是不是也有点像做糖葫芦呢?你看,这FC工艺,虽然听起来高大上,但其实它的原理和我们日常生活中的一些事情还挺相似的。
它就像是一场精细的手术,也像是在做糖葫芦。
虽然我们可能不会亲手去做,但了解它的过程,也能感受到科技的魅力和乐趣。
4第二章 互连技术FCB
2.4 倒装焊技术(FCB)2.4.1 FCB2.4.4 C42.4.5倒装焊接机简介*微组装工艺*一、FCB技术2.4.1FCB技术及特点倒装焊(FCB)是芯片与基板直接安装互连的一种方法。
在芯片连接的地方制作出突起的焊点,在后期操作中直接将芯片的焊点与基板的焊区形成连接。
WB和TAB互连法通常那是芯片面朝上安装互连、而FCB则是芯片面朝下,芯片上的焊区直接与基板上的焊区互连。
*微组装工艺*制作的凸点芯片既可以用于在厚膜陶瓷基板上进行FCB,又可以在薄膜陶瓷或Si基板上进行FCB,还可以在PCB上直接将芯片进行FCB。
使用FCB的基板一般有:陶瓷、Si基板、PCB环氧树脂基板。
Samples with Different DimensionsPCB 上不同尺寸倒装焊样品Flip Chip on Flexible substrate 在软质底板上倒装焊*微组装工艺*基板芯片表面互连线基板表面互连线凸点基板芯片表面互连线基板表面互连线*微组装工艺*二、发展历史1964倒装芯片出现;1969年,IBM公司C4技术(可控塌陷技术);至今,已广泛应用于SIP,MCM,微处理器,硬盘驱动器以及RFID等领域。
*微组装工艺*三、FCB技术的优缺点优点:FCB的互连线非常短。
互连产生的杂散电容、互连电阻和互连电感均比WB和TAB小得多,从而更适合高频、高速的电子产品应用;FCB芯片安装互连占的基板面积小.因而芯片安装密度高。
此外,FCB芯片焊区可面阵布局、更适合高I/O数的LSI、VLSI芯片使用;芯片的安装、互连是同时完成的,这就大大简化了安装互连工艺,快速、省时,适于使用先进的SMT 进行工业化大批量生产。
*微组装工艺*缺点:芯片面朝下安装互连,会给工艺操作带来一定难度,焊点检查困难(只能使用红外线和X光检查); 在芯片焊区一般要制作凸点,增加了芯片的制作工艺流程和成本;倒装焊同各材料间的匹配所产生的应力问题也需要很好地解决等。
半导体fc的封装流程
半导体fc的封装流程下载温馨提示:该文档是我店铺精心编制而成,希望大家下载以后,能够帮助大家解决实际的问题。
文档下载后可定制随意修改,请根据实际需要进行相应的调整和使用,谢谢!并且,本店铺为大家提供各种各样类型的实用资料,如教育随笔、日记赏析、句子摘抄、古诗大全、经典美文、话题作文、工作总结、词语解析、文案摘录、其他资料等等,如想了解不同资料格式和写法,敬请关注!Download tips: This document is carefully compiled by theeditor. I hope that after you download them,they can help yousolve practical problems. The document can be customized andmodified after downloading,please adjust and use it according toactual needs, thank you!In addition, our shop provides you with various types ofpractical materials,such as educational essays, diaryappreciation,sentence excerpts,ancient poems,classic articles,topic composition,work summary,word parsing,copy excerpts,other materials and so on,want to know different data formats andwriting methods,please pay attention!半导体 FC(Flip Chip,倒装芯片)的封装流程主要包括以下几个步骤:1. 芯片制备晶圆制造:通过一系列工艺步骤,在硅晶圆上制造出集成电路芯片。
- 1、下载文档前请自行甄别文档内容的完整性,平台不提供额外的编辑、内容补充、找答案等附加服务。
- 2、"仅部分预览"的文档,不可在线预览部分如存在完整性等问题,可反馈申请退款(可完整预览的文档不适用该条件!)。
- 3、如文档侵犯您的权益,请联系客服反馈,我们会尽快为您处理(人工客服工作时间:9:00-18:30)。
FC倒装芯片装配技术介绍器件的小型化高密度封装形式越来越多,如多模块封装(MCM)、系统封装(SiP)、倒装芯片(FC,Flip-Chip)等应用得越来越多。
这些技术的出现更加模糊了一级封装与二级装配之间的界线。
毋庸置疑,随着小型化高密度封装的出现,对高速与高精度装配的要求变得更加关键,相关的组装设备和工艺也更具先进性与高灵活性。
由于倒装芯片比BGA或CSP具有更小的外形尺寸、更小的球径和球间距、它对植球工艺、基板技术、材料的兼容性、制造工艺,以及检查设备和方法提出了前所未有的挑战。
倒装芯片的发展历史倒装芯片的定义什么器件被称为倒装芯片?一般来说,这类器件具备以下特点:1. 基材是硅;2. 电气面及焊凸在器件下表面;3. 球间距一般为4-14mil、球径为2.5-8mil、外形尺寸为1-27mm;4. 组装在基板上后需要做底部填充。
其实,倒装芯片之所以被称为“倒装”,是相对于传统的金属线键合连接方式(Wire Bonding)与植球后的工艺而言的。
传统的通过金属线键合与基板连接的芯片电气面朝上(图1),而倒装芯片的电气面朝下(图2),相当于将前者翻转过来,故称其为“倒装芯片”。
在圆片(Wafer)上芯片植完球后(图3),需要将其翻转,送入贴片机,便于贴装,也由于这一翻转过程,而被称为“倒装芯片”。
倒装芯片的历史及其应用倒装芯片在1964年开始出现,1969年由IBM发明了倒装芯片的C4工艺(Controlled Collapse Chip Connection,可控坍塌芯片联接)。
过去只是比较少量的特殊应用,近几年倒装芯片已经成为高性能封装的互连方法,它的应用得到比较广泛快速的发展。
目前倒装芯片主要应用在Wi- Fi、SiP、MCM、图像传感器、微处理器、硬盘驱动器、医用传感器,以及RFID等方面(图5)。
与此同时,它已经成为小型I/O应用有效的互连解决方案。
随着微型化及人们已接受SiP,倒装芯片被视为各种针脚数量低的应用的首选方法。
从整体上看,其在低端应用和高端应用中的采用,根据TechSearch International Inc对市场容量的预计,焊球凸点倒装芯片的年复合增长率(CAGR)将达到31%。
倒装芯片应用的直接驱动力来自于其优良的电气性能,以及市场对终端产品尺寸和成本的要求。
在功率及电信号的分配,降低信号噪音方面表现出色,同时又能满足高密度封装或装配的要求。
可以预见,其应用会越来越广泛。
倒装芯片的组装工艺流程一般的混合组装工艺流程在半导体后端组装工厂中,现在有两种模块组装方法。
在两次回流焊工艺中,先在单独的SMT生产线上组装SMT器件,该生产线由丝网印刷机、贴片机和第一个回流焊炉组成。
然后再通过第二条生产线处理部分组装的模块,该生产线由倒装芯片贴片机和回流焊炉组成。
底部填充工艺在专用底部填充生产线中完成,或与倒装芯片生产线结合完成。
倒装芯片的装配工艺流程介绍相对于其它的IC器件,如BGA、CSP等,倒装芯片装配工艺有其特殊性,该工艺引入了助焊剂工艺和底部填充工艺。
因为助焊剂残留物(对可靠性的影响)及桥连的危险,将倒装芯片贴装于锡膏上不是一种可采用的装配方法。
业内推出了无需清洁的助焊剂,芯片浸蘸助焊剂工艺成为广泛使用的助焊技术。
目前主要的替代方法是使用免洗助焊剂,将器件浸蘸在助焊剂薄膜里让器件焊球蘸取一定量的助焊剂,再将器件贴装在基板上,然后回流焊接;或者将助焊剂预先施加在基板上,再贴装器件与回流焊接。
助焊剂在回流之前起到固定器件的作用,回流过程中起到润湿焊接表面增强可焊性的作用。
倒装芯片焊接完成后,需要在器件底部和基板之间填充一种胶(一般为环氧树酯材料)。
底部填充分为于“毛细流动原理”的流动性和非流动性(No-follow)底部填充。
上述倒装芯片组装工艺是针对C4器件(器件焊凸材料为SnPb、SnAg、SnCu或SnAgCu)而言。
另外一种工艺是利用各向异性导电胶(ACF)来装配倒装芯片。
预先在基板上施加异性导电胶,贴片头用较高压力将器件贴装在基板上,同时对器件加热,使导电胶固化。
该工艺要求贴片机具有非常高的精度,同时贴片头具有大压力及加热功能。
对于非C4器件(其焊凸材料为Au或其它)的装配,趋向采用此工艺。
这里,我们主要讨论C4工艺,下表列出的是倒装芯片植球(Bumping)和在基板上连接的几种方式。
倒装倒装芯片几何尺寸可以用一个“小”字来形容:焊球直径小(小到0.05mm),焊球间距小(小到0.1mm),外形尺寸小(1mm2)。
要获得满意的装配良率,给贴装设备及其工艺带来了挑战,随着焊球直径的缩小,贴装精度要求越来越高.目前12μm甚至10μm的精度越来越常见。
贴片设备照像机图形处理能力也十分关键,小的球径小的球间距需要更高像素的像机来处理。
随着时间推移,高性能芯片的尺寸不断增大,焊凸(Solder Bump)数量不断提高,基板变得越来越薄,为了提高产品可靠性底部填充成为必须。
对贴装压力控制的要求考虑到倒装芯片基材是比较脆的硅,若在取料、助焊剂浸蘸过程中施以较大的压力容易将其压裂,同时细小的焊凸在此过程中也容易压变形,所以尽量使用比较低的贴装压力,一般要求在150g左右。
对于超薄形芯片,如0.3mm,有时甚至要求贴装压力控制在35g。
对贴装精度及稳定性的要求对于球间距小到0.1mm的器件,需要怎样的贴装精度才能达到较高的良率?基板的翘曲变形,阻焊膜窗口的尺寸和位置偏差,以及机器的精度等,都会影响到最终的贴装精度。
关于基板设计和制造的情况对于贴装的影响,我们在此不作讨论,这芯片装配工艺对贴装设备的要求里我们只是来讨论机器的贴装精度。
为了回答上面的问题,我们来建立一个简单的假设模型:1.假设倒装芯片的焊凸为球形,基板上对应的焊盘为圆形,且具有相同的直径;2.假设无基板翘曲变形及制造缺陷方面的影响;3.不考虑Theta和冲击的影响;4.在回流焊接过程中,器件具有自对中性,焊球与润湿面50%的接触在焊接过程中可以被“拉正”。
那么,基于以上的假设,直径25μm的焊球如果其对应的圆形焊盘的直径为50μm时,左右位置偏差(X 轴)或前后位置偏差(Y轴)在焊盘尺寸的50%,焊球都始终在焊盘上(图9)。
对于焊球直径为25μm 的倒装芯片,工艺能力Cpk要达到1.33的话,要求机器的最小精度必须达到12μm@3sigma.对照像机和影像处理技术的要求要处理细小焊球间距的倒装芯片的影像,需要百万像素的数码像机。
较高像素的数码像机有较高的放大倍率,但是,像素越高视像区域(FOV)越小,这意味着大的器件可能需要多次“拍照”。
照像机的光源一般为发光二极管,分为侧光源、前光源和轴向光源,并可以单独控制。
倒装芯片的的成像光源采用侧光、前光,或两者结合。
那么,对于给定器件如何选择像机呢?这主要依赖图像的算法。
譬如,区分一个焊球需要N个像素,则区分球间距需要2N个像素。
以环球仪器的贴片机上Magellan数码像机为例,其区分一个焊球需要4个像素,我们用来看不同的焊球间隙所要求的最大的像素应该是多大,这便于我们根据不同的器件来选择相机,假设所有的影像是实际物体尺寸的75%。
倒装芯片基准点(Fiducial)的影像处理与普通基准点相似。
倒装芯片的贴装往往除整板基准点外(Global fiducial)会使用局部基准点(Local fiducial),此时的基准点会较小(0.15—1.0mm),像机的选择参照上面的方法。
对于光源的选择需要斟酌,一般贴片头上的相机光源都是红光,在处理柔性电路板上的基准点时效果很差,甚至找不到基准点,其原因是基准点表面(铜)的颜色和基板颜色非常接近,色差不明显。
如果使用环球仪器的蓝色光源专利技术就很好的解决了此问题。
吸嘴的选择由于倒装芯片基材是硅,上表面非常平整光滑,最好选择头部是硬质塑料材料具多孔的ESD吸嘴。
如果选择头部为橡胶的吸嘴,随着橡胶的老化,在贴片过程中可能会粘连器件,造成贴片偏移或带走器件。
对助焊剂应用单元的要求助焊剂应用单元是控制助焊剂浸蘸工艺的重要部分,其工作的基本原理就是要获得设定厚度的稳定的助焊剂薄膜,以便于器件各焊球蘸取的助焊剂的量一致。
要精确稳定的控制助焊剂薄膜的厚度,同时满足高速浸蘸的要求,该助焊剂应用单元必须满足以下要求:1. 可以满足多枚器件同时浸蘸助焊剂(如同时浸蘸4或7枚)提高产量;2. 助焊剂用单元应该简单、易操作、易控制、易清洁;3. 可以处理很广泛的助焊剂或锡膏,适合浸蘸工艺的助焊剂粘度范围较宽,对于较稀和较粘的助焊剂都要能处理,而且获得的膜厚要均匀;4. 蘸取工艺可以精确控制,浸蘸的工艺参数因材料的不同而会有差异,所以浸蘸过程工艺参数必须可以单独控制,如往下的加速度、压力、停留时间、向上的加速度等。
对供料器的要求要满足批量高速高良率的生产,供料技术也相当关键。
倒装芯片的包装方式主要有这么几种:2×2或4×4英JEDEC盘、200mm或300mm圆片盘(Wafer)、还有卷带料盘(Reel)。
对应的供料器有:固定式料盘供料器(Stationary tray feeder),自动堆叠式送料器(Automated stackable feeder),圆片供料器(Wafer feeder),以及带式供料器。
所有这些供料技术必须具有精确高速供料的能力,对于圆片供料器还要求其能处理多种器件包装方式,譬如:器件包装可以是JEDEC盘、或裸片,甚至完成芯片在机器内完成翻转动作。
我们来举例说明几种供料器. Unovis的裸晶供料器(DDF Direct Die Feeder)特点:• 可用于混合电路或感应器、多芯片模组、系统封装、RFID和3D装配• 圆片盘可以竖着进料、节省空间,一台机器可以安装多台DDF• 芯片可以在DDF内完成翻转•可以安装在多种贴片平台上,如:环球仪器、西门子、安必昂、富士对板支撑及定位系统的要求有些倒装芯片是应用在柔性电路板或薄型电路板上,这时候对基板的平整支撑非常关键。
解决方案往往会用到载板和真空吸附系统,以形成一个平整的支撑及精确的定位系统,满足以下要求:1.基板Z方向的精确支撑控制,支撑高度编程调节;2.提供客户化的板支撑界面;3.完整的真空发生器;4.可应用非标准及标准载板。
回流焊接及填料固化后的检查对完成底部填充以后产品的检查有非破坏性检查和破坏性检查,非破坏性的检查有• 利用光学显微镜进行外观检查,譬如检查填料在器件侧面爬升的情况,是否形成良好的边缘圆角,器件表面是否有脏污等• 利用X射线检查仪检查焊点是否短路,开路,偏移,润湿情况,焊点内空洞等• 电气测试(导通测试),可以测试电气联结是否有问题。
对于一些采用菊花链设计的测试板,通过通断测试还可以确定焊点失效的位置• 利用超声波扫描显微镜(C-SAM)检查底部填充后其中是否有空洞、分层,流动是否完整破坏性的检查可以对焊点或底部填料进行切片,结合光学显微镜,金相显微镜或电子扫描显微镜和能谱分析仪(SEM/EDX),检查焊点的微观结构,例如,微裂纹/微孔,锡结晶,金属间化合物,焊接及润湿情况,底部填充是否有空洞、裂纹、分层、流动是否完整等。