连铸机液压系统故障诊断与维修[权威资料]
连铸机液压振动故障处理

连铸机液压振动故障处理连铸机是钢铁冶炼过程中的重要设备,直接关系到钢铁质量和生产效率。
其中,液压系统是其核心部件之一,负责提供液力传动、能量转换、动力控制等功能。
然而,在使用过程中,由于各种原因,液压系统可能会出现振动故障,给生产带来严重影响。
本文将介绍连铸机液压振动故障的主要原因和处理方法。
1. 油流不稳定连铸机液压系统中油流不稳定是常见的原因之一。
这可能由于油路管道堵塞、液压泵故障、油液过热等引起。
油路管道堵塞会导致液压泵吸入空气,增加油液压力,使系统产生压力波动和振动。
液压泵本身也会因为损坏、磨损等原因导致油流不稳定。
此外,在长时间的生产过程中,油液也会因温度过高而降低黏度,进一步加剧油流不稳定的现象。
2. 死区振动连铸机液压系统中,某些部位可能存在死区,即油液无法正常循环,会形成压力波动,引起液压振动。
这种振动被称为死区振动。
常见的死区包括转向阀处、伺服阀处、溢流阀处等。
3. 阀芯、阀座磨损在连铸机液压系统中,阀芯和阀座处于长时间摩擦和磨损状态,容易出现磨损、过度磨平等现象,影响阀门的密封性,导致泄漏和振动。
4. 液压缸问题液压缸内部可能存在气体、液压油过脏、活塞密封性差等问题,导致动力传递不稳定,产生振动。
此外,液压缸内部渗漏也会导致系统压力波动和液压振动。
1. 检查油路管道和液压泵当连铸机液压系统出现振动故障时,应首先检查油路管道和液压泵是否正常。
检查油路管道是否堵塞、是否有渗漏,清洗管道内部的积垢和异物。
如果液压泵出现故障,则需要进行修理或更换,确保油液流畅。
对于死区振动问题,可以采用增强阻尼、加强液压控制等方法消除。
比如可以在转向阀处设置节流孔,增加节流阻力,平衡压力波动。
当阀芯、阀座出现磨损、过度磨平等问题时,需要进行更换。
选择优质阀芯、阀座,确保阀门的密封性和液压系统的正常运行。
液压缸是连铸机液压系统中最为重要的部件之一,应定期检查液压缸内部的气体、油液是否过脏,及时更换液压缸密封圈。
连铸大包回转台液压系统故障原因分析与解决措施

连铸大包回转台液压系统故障原因分析与解决措施1号连铸机建投产时大包回转台事故旋转系统无法使用,影响正常生产,同时存在设备安全隐患。
对系统存在的故障进行技术分析并提出解决方案,最终实施并取得良好效果。
标签:连铸机;大包回转台;事故旋转;液压系统;故障1 引言大包回转台安装在连铸车间钢水接受跨和连铸跨之间的浇铸平台上,用于接受炼钢系统送来的盛满钢水的钢包,并将钢包转至连铸跨的浇注位置进行浇注。
当钢水浇注完后,通过设备的旋转将空钢包送回炼钢跨,同时将新的盛满钢水的钢包送到连铸跨,从而保证连铸机连续浇注生产的要求[1]。
承钢120吨连铸1#机在安装调试过程中发现事故液压回转功能无法使用,使用事故液压进行驱动时,液压马达有输出,但是大包回转台不跟随其进行转动。
2 系统工作原理及存在问题分析2.1 回转驱动装置及工作原理大包回转台回转驱动装置主要由主驱动动力源-电机、事故驱动动力源-液压源、减速机、液压离合器、制动器、开式小齿轮等组成,其示意图如图1所示。
回转驱动装置具有回转驱动、事故驱动和回转定位等三大功能。
回转驱动装置基本采用外置式,其底座焊接在回转台的固定底座上。
大包回转台旋转时,驱动动力源经过减速机驱动小齿轮转动,带动大包回转体旋转。
大包回转台回转驱动装置主驱动采用交流变频电机,事故驱动为液压马达,通过一套紧凑型减速机带动小齿轮,小齿轮驱动大齿圈及上部回转钢结构进行360°回转[2],2种驱动方式如下:(1)正常驱动模式-由变频电机驱动,大包回转台主要驱动方式。
正常電机驱动时,液压离合器与减速机输入轴脱开,电机直接驱动减速机从而驱动回转台工作。
(2)事故液压驱动模式-有液压马达驱动,用于回转台驱动电机出现故障,或者系统掉电无法继续生产时利用液压系统蓄能器储存压力油驱动液压马达工作将回转台上正在浇铸的大包转至事故位置,以确保浇铸平台人员和设备安全。
2.2 事故旋转液压系统事故旋转液压系统由2组控制阀台、液压离合器和液压马达组成,换向阀台控制大包旋转方向和提供液压马达和离合器工作需要的压力油;马达与减速器分合控制阀台部分主要控制液压马达安全工作和控制液压离合器的接合与分开。
炼钢连铸液压传动系统故障、成因及分类(1)

炼钢连铸液压传动系统故障、成因及分类(1)1 易出的故障及成因1)泄漏尽管随着加⼯技术和材料性能的不断改进,液压元件的泄漏已⼤为减少,但在钢铁企业的特定⼯作环境中液压系统泄漏故障仍占较⾼⽐例。
外泄是指向系统外部泄漏,直接表现是系统总油量的减少。
发⽣点主要在与红坯靠近的执⾏器(如液压缸)及其连接管路,由于这些部件完全暴露在铸坯的强红外辐射之下,极易造成橡胶软管⽼化破裂和油管、液压缸接头处密封失效;其次就是在连铸操作作业区和设备现场维护作业区的交叉作业区内,这⾥不但交织着各种机、电、液设备,,同时也是铸坯尾坯处理的场所,各⼯种交叉作业,若协调不好极易发⽣碰撞⽽产⽣事故,对液压系统⽽⾔就是元件的损坏和外泄漏。
内泄主要发⽣在泵体内、缸体内和阀体内。
缸体内泄主要是因为作为执⾏器的液压缸⽐较靠近铸坯或钢包,强热辐射造成活塞上密封件的⾼温⽼化,导致⾼低压两腔的窜油,使⾼压腔的压⼒降低。
其直接表现为液压缸举升和收缩缓慢、⽆⼒,严重时甚⾄⽆法完成规定动作,此时贴近缸壁可明显听到内部窜油的噪声。
由于泵和阀主要安装于专⽤的液压泵房内,所以它们的内泄主要是运动部件的磨损造成的,这是⼀个较长的缓变过程,要经历磨合期、稳定期和快速磨损期这3个阶段,前2个阶段为量变积累阶段。
第3阶段为质变阶段,此时泵、阀运⾏噪声增⼤,严重时泵出⼝压⼒下降,导致整个系统供压不⾜。
使⽤中的恒压变量泵如果内泄增⼤,使经泵壳体泄出的油量增⼤,若⽆法及时泄流,将导致壳体处油压增⾼,严重时造成液压泵损坏。
阀内泄则可能产⽣机构的误动作。
内泄是⼀种较隐蔽的故障,且从量变到质变多为突变,不易及时发现,较之外泄其危害更⼤。
1.插装阀组2.上辊压下液压缸3.排⽓测压接头4.双单向节流阀5.两位四通电磁换向阀6.两位四通电磁换向阀(带定位)7.溢流阀8.两位三通电磁球阀9.液控单向阀10.蓄能器11.两位三通电磁换向阀(带定位)12.⾼压球阀p1—送引锭杆压⼒(8MPa) p2—矫直压⼒(4~5MPa)图2 板坯连铸液压矫直系统原理图图2为板坯连铸液压矫直系统原理图。
短流程连铸连轧成套装备中常见故障及排除方法
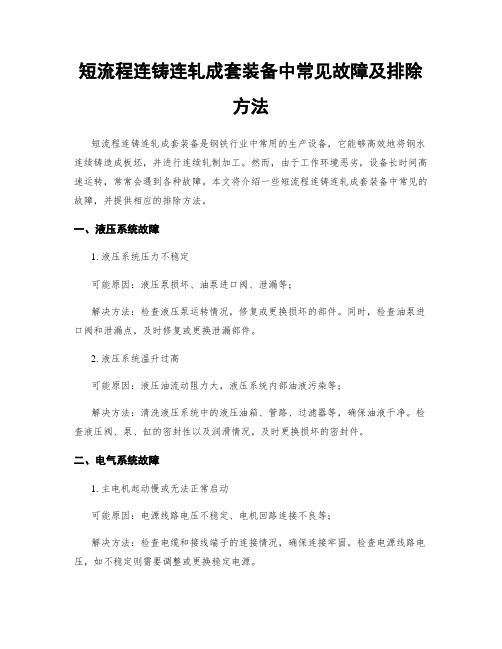
短流程连铸连轧成套装备中常见故障及排除方法短流程连铸连轧成套装备是钢铁行业中常用的生产设备,它能够高效地将钢水连续铸造成板坯,并进行连续轧制加工。
然而,由于工作环境恶劣,设备长时间高速运转,常常会遇到各种故障。
本文将介绍一些短流程连铸连轧成套装备中常见的故障,并提供相应的排除方法。
一、液压系统故障1. 液压系统压力不稳定可能原因:液压泵损坏、油泵进口阀、泄漏等;解决方法:检查液压泵运转情况,修复或更换损坏的部件。
同时,检查油泵进口阀和泄漏点,及时修复或更换泄漏部件。
2. 液压系统温升过高可能原因:液压油流动阻力大,液压系统内部油液污染等;解决方法:清洗液压系统中的液压油箱、管路、过滤器等,确保油液干净。
检查液压阀、泵、缸的密封性以及润滑情况,及时更换损坏的密封件。
二、电气系统故障1. 主电机起动慢或无法正常启动可能原因:电源线路电压不稳定、电机回路连接不良等;解决方法:检查电缆和接线端子的连接情况,确保连接牢固。
检查电源线路电压,如不稳定则需要调整或更换稳定电源。
2. 控制系统无法正常运行或操作不灵活可能原因:控制电路损坏、程序错误等;解决方法:检查控制电路中的元件,如继电器、断路器等,确保其正常运转。
检查程序设置,修复错误的程序或重新设置程序。
三、机械系统故障1. 机械传动系统噪音大或振动严重可能原因:轴承损坏、齿轮磨损等;解决方法:检查轴承,如损坏则需要更换。
检查齿轮传动装置,如磨损过大则需要修复或更换。
2. 连铸连轧机组产量下降可能原因:导轧机辊缺陷、冷却系统故障等;解决方法:检查导轧机辊,如发现缺陷则需要修复或更换。
检查冷却系统,保证冷却效果良好,如有故障则及时修复。
四、安全故障1. 磁力制动器失效可能原因:磁力制动器电磁铁损坏、接触不良等;解决方法:检查磁力制动器的电磁铁部件,如发现损坏则需要更换。
检查制动器的接线端子,确保连接良好。
2. 高温故障可能原因:设备长时间运转导致温度过高、冷却系统故障等;解决方法:检查设备运转时间,合理安排停机维护时间,及时清洁冷却系统,确保其正常运转。
连铸机械常见故障与维修措施探究

连铸机械常见故障与维修措施探究摘要:随着我国科学技术的不断进步,越来越多的科学技术研究成果被运用到生产实践中,促使我国的工业产业朝着现代化方向发展。
连铸机械是一种新型设备,其能够推动钢铁生产由人工化向机械化方向发展,提升钢铁产量与质量。
但连铸机械设备在长期使用过程中,会出现一些故障,如果未能及时做好日常检修和维护工作,会影响到连铸机械的正常运行,降低生产效率。
故此,本文主要就连铸机械设备故障及维修方案进行了简要分析。
关键词:连铸机械;故障;维修;保养引言在社会经济高速发展背景下,带动了我国工业产业的发展,对于钢铁生产的需求和要求也在不断提升。
而连铸生产工艺的运用,能够有效推动钢铁生产模式和技术的改革,提升钢铁生产率,节约能源消耗。
因此,连铸机械设备目前在我国冶金行业中得到了较为广泛的运用。
为保证连铸机械的稳定运行,做好连铸机械设备故障检修和维护工作是非常必要的。
为此,连铸技术人员不仅要熟练使用和操作连铸设备,还需要了解和掌握连铸机械设备在运行过程中经常出现的故障,并做好相应的检修和维护工作,保证连铸机械设备的良好性能,发挥连铸机械设备的生产优势,推动我国工业产业的可持续发展。
一、连铸技术的概述连铸技术是现代冶金行业中的较为常见的一种新型生产技术,是指在冶金生产中,通过将连铸设备直接将钢水浇注成型的技术【1】。
目前这项技术较为成熟,应用广泛,极大的提升了我国钢铁生产效率和质量。
而连铸技术的原理是先将钢坯熔融成钢水,然后向结晶器中持续浇筑钢水,当铸件呈现出凝固状态后,在运用设备将从结晶器中将铸件拉出来。
而在拉出来的过程中,可以通过对拉伸力度、口径等参数的调整,获得相应的铸件。
与传统冶金技术相比,连铸技术更加高效、节能,促进冶金技术的提升。
二、连铸机械常见故障及维修策略(一)大包回转台故障当大包回转台出现故障后,造成最直接的影响就是漏油,影响连铸机械的正常运行。
而连铸机械大包回转台故障主要体现在以下几个方面:一是液压油环故障。
连铸中间包液压系统故障诊断与维修
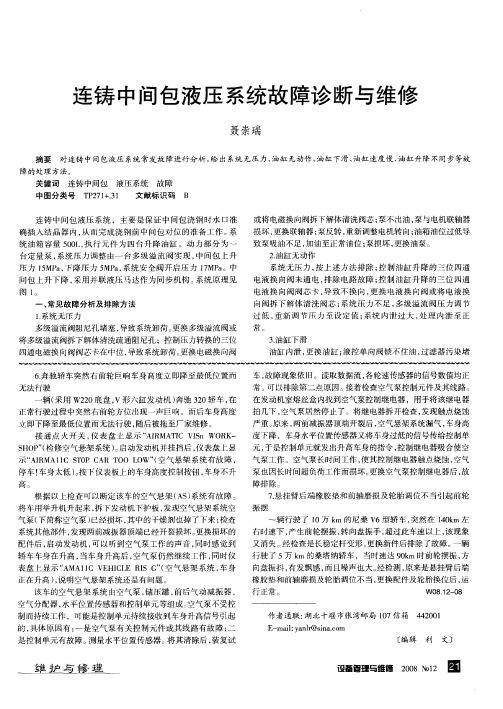
或将 电磁换 向阀拆下解体清洗阀芯; 泵不出油 , 泵与电机联轴器
损坏 , 更换联轴器 ; 泵反转 , 重新调整电机转 向; 油箱油位过低导
致 泵 吸油 不 足 , 油至 正 常 油 位 ; 损 坏 , 换 油 泵 。 加 泵 更
2’缸无动作 _ ? 由 系统 无压 力 , 上述方 法排除 ; 制油缸升 降的三位 四通 按 控 电液换 向阀未通 电, 排除 电路 故障 ; 控制 油缸升 降的三位 四通 电液换 向阀阀芯卡 , 导致不换 向 , 更换 电液换 向阀或将 电液换 向阀拆下解体 清洗阀芯 ; 系统 压力不 足 , 多级溢 流阀压力 调节 过低 , 重新 调节 压 力至 设定 值 ; 系统 内泄过 大 , 理 内泄至 正 处
连铸 中间包液压 系统 ,主要是 保证 中间包浇 钢时水 口准 确插 入结 晶器 内 , 而完成 浇钢前 中间包对位 的准备工作 。 从 系 统 油箱容 量 5 0 , 行元 件 为四台 升降油 缸 。动力部 分 为一 0 L执
台定 量 泵 , 统 压 力 调 整 由一 台 多 级 溢 流 阀 实 现 , 间 包 上 升 系 中
常。 3油 缸 下 滑 .
压力 1MP , 5 a 下降压力 5 a 系统安 全阀开启压 力 1MP 。中 MP , 7 a
间包 上升下 降 , 采用 并联液压 马达作为 同步机构 。 系统原理 见
图 1 。
一
、
常见 故 障分 析 及 排 除 方 法
1 . 无 压 力 系统 多 级 溢 流 阀 阻尼 孔 堵 塞 , 致 系统 卸 荷 。 换 多 级 溢 流 阀或 导 更
将多级溢流阀拆 下解 体清洗疏通阻尼孔 ;控制压力转换 的三位 四通电磁换 向阀阀芯 卡在 中位 , 导致 系统卸荷 。 更换 电磁换 向阀
连铸机液压系统故障诊断研究

目录第一篇绪论 (1)第一章课题背景 (1)第二章变电站综合自动化系统存在的问题及改进措施 (4)第三章变电站自动化技术现状 (9)第四章变电站综合自动化系统发展方向 (10)第一节智能电子装置(IED)的发展和光电互感器的应用 (11)第二节监控系统的发展和遥视系统的应用 (11)第三节人工智能技术的发展应用 (12)第四节通信方式的发展和工业以太网的发展应用 (12)第五节蓝牙技术的发展应用 (12)第二篇现场总线的应用现状 (13)RS-458 (13)LonWorks (13)F-NET (13)WorldFIP (13)第一章 IEC61850标准的应用现状 (14)第二章现场总线在变电站综合自动化系统应用中的不足 (14)第一节现场总线作为工控领域的专用网络 (14)第二节现场总线的拓扑结构多为总线型 (14)第三节数据通信带宽 (14)第四节总线产品众多 (14)第三章变电站综合自动化系统中现场总线应用的发展趋势 (15)第三篇现场总线的变电站自动化系统 (22)第一章系统功能 (22)第二章通讯网络 (24)第四篇硬统设计件系 (25)第一章系统总体结构 (25)第二章系统设计要点 (25)第五篇系统组态监控软件的设计 (27)第一章开发工具的选取 (27)第二章变电站对象模型分析 (27)第三章面向程序思想方法构建监控组态软件 (28)结论 (29)参考文献 (30)致谢 (31)第一篇绪论随着计算机技术、通信技术和网络技术的飞速发展和广泛应用,传统的集中、低速、专用封闭式的远动系统已向开放、高速、综合的网络化方向发展,通过局域网互联和广域网互联,实现系统信息资源共享。
变电站自动化技术也得到了较快的发展,全分散式变电站自动化系统是变电站自动化的主要发展方向[1].由于现场总线可靠性高、稳定性好、抗干扰能力强、通讯速率高、维护成本低的特点,变电站综合自动化系统已普遍采用现场总线作为系统的通讯手段,以满足自动化系统全分散、全数字化、双向、多点多站的要求。
连铸机设备液压系统常见问题和建议

连铸机设备液压系统常见问题和建议摘要:本文针对连铸机设备液压系统中的常见问题进行了分析,并提出了相应的维护与保养建议。
通过案例分析,探讨了问题的解决方案及实际效果。
关键字:连铸机设备;液压系统;常见问题;维护保养引言连铸机设备是冶金工业中重要的设备之一,其液压系统在设备运行中发挥着关键作用。
然而,在实际运行过程中,液压系统可能会出现各种问题,影响设备的正常运行。
因此,本文将分析连铸机设备液压系统的常见问题,并提出相应的维护保养建议。
1.连铸机设备液压系统常见问题1.1 液压油泄漏液压油泄漏是液压系统常见问题,原因包括接头松动和密封件损坏。
泄漏会影响系统性能,降低设备可靠性。
为了防止液压油泄漏,应定期检查接头紧固情况,更换损坏的密封件,正确安装各部件,定期检查油位和油质,遵循设备制造商的指南,以及使用液压监测设备进行在线监测。
通过这些措施,可以降低液压油泄漏风险,提高系统可靠性,保证设备正常运行。
1.2 液压泵及马达故障液压泵和马达是连铸机设备液压系统的核心部件,其故障会导致系统失效,严重影响设备的正常运行和生产效率。
故障原因包括磨损、污染、过热、过载等。
为避免故障,应定期检查液压泵和马达的工作状态,并进行必要的维护保养。
关键措施包括保持液压油清洁,监测液压系统的工作压力和温度,定期检查液压泵和马达的磨损情况并进行润滑,避免长时间空载运行,增强操作人员的培训和管理,以及对液压泵和马达进行定期维护保养。
通过这些措施,可以有效预防液压泵和马达故障,降低设备故障率,提高连铸机设备的运行效率和安全性,同时延长设备使用寿命,降低维修成本。
1.3 液压缸及活塞杆磨损液压缸和活塞杆是连铸机设备液压系统中承受较大压力的部件,长时间运行容易出现磨损,从而导致系统稳定性下降,影响生产效率。
为了延长液压缸和活塞杆的使用寿命,提高设备运行效率,应定期检查磨损情况、保持液压油清洁、采用高质量的密封件和导向环、进行润滑保养、以及加强操作人员培训和管理。
- 1、下载文档前请自行甄别文档内容的完整性,平台不提供额外的编辑、内容补充、找答案等附加服务。
- 2、"仅部分预览"的文档,不可在线预览部分如存在完整性等问题,可反馈申请退款(可完整预览的文档不适用该条件!)。
- 3、如文档侵犯您的权益,请联系客服反馈,我们会尽快为您处理(人工客服工作时间:9:00-18:30)。
连铸机液压系统故障诊断与维修本文档格式为WORD,感谢你的阅读。
摘要:本文通过主动性维修维修技术在我厂连铸机液压设备管理中的实际运用,详细论述了主动性维修技术的在板坯连铸机液压设备具体运用过程中的实施步骤、方法、控制要点,为维修行业的推广和运用主动性维修技术提供了思路。
关键词:主动性维修;液压;设备管理连铸是一种先进的生产工艺,它取代了以往的钢水模铸、脱锭、均热、开坯的组合工艺。
因此,在能源消耗、产品质量、生产效率等方面,都具有优势。
连铸机是将钢水直接加工成钢坯的成套设备,连铸机由于执行机构分散面广、传动功率大、工作环境恶劣等而广泛地采用液压系统进行传动和控制。
但其液压系统的故障诊断和维修是一项复杂的经验性工作,需要应用大量独特的专家经验和诊断策略,才能有效地解决复杂的故障诊断问题。
1连铸液压元件概述1.1液压泵液压泵是液压系统的动力元件,负责向液压系统提供合符要求的压力油源。
为了保证连铸生产的连续、稳定,一般采用进口恒压变量泵。
此类液压泵的特点是:①输出压力平稳,但结构较复杂。
②负载大,运行时间长,磨损速度快。
③装拆不方便。
1.2控制阀控制阀主要包括压力阀、方向阀与流量阀三大类。
1.2.1压力阀主要包含减压阀及溢流阀两种:减压阀的作用是将系统压力减至某一需要的出口压力;溢流阀主要起定压溢流作用,稳压,系统卸荷和安全保护作用。
1.2.2方向阀主要用以改变管道内的液体流向,以控制液压缸及马达等执行元件的运动方向。
1.2.3流量阀是通过改变阀口的过流面积来调节输出流量,从而控制执行元件的运行速度。
而针对一些大型油缸,一般都会安装有平衡阀,以保证其在启动和停止时的运行平稳(如钢水包升降装置油缸)。
控制阀的损坏主要有以下几点:1)磨损:在长期的使用过程中,控制阀的阀芯及芯套会发生磨损,使其部分或完全丧失对流体的控制能力。
2)卡阀:液压系统的工作介质即液压油中有大颗粒污染物,在通过控制阀芯时将其卡住,造成控制阀失效。
3)泄漏:密封件损坏造成的阀体漏油。
1.3执行机构执行机构主要包括液压缸与液压马达。
l)液压缸是连铸系统主要工作设备之一,其工况主要以高温高湿为主。
2)液压马达在压力油的推动下产生旋转运动,对负荷输出转速与扭矩,主要用在连铸机的钢包回转台和中间罐车上。
1.4液压辅件液压辅件包括密封件、过滤器、蓄能器、冷却器等。
1)密封件。
密封件是液压系统维持正常压力的保证因素。
液压装置的能量流与流量是一致的,且前后相通,故液压回路中任一处发生密封问题都会引起系统能量传递的偏差。
2)过滤器。
过滤器用于过滤油液中的各类污染物,保护液压系统,是重要的液压元件。
3)蓄能器。
蓄能器用于吸收压力与流量的脉动、作辅助能源和系统保压。
4)冷却器。
用于冷却系统运行中产生的热量,维持温度的平衡。
5)其他。
主要是管件、管夹、接头、仪表等。
2我厂实施主动性维修我厂连铸机建成时间不长,液压设备管理工作起步较晚,通过学习和消化的先进设备管理经验及我厂在液压设备管理工作中的具体实践,我们在液压设备管理领域采用了主动性维修模式,具体原因如下:2.1连续铸钢是我厂高效生产的重要环节,如果设备出现故障停机,将导致一整套生产线停产,损失巨大。
而液压设备作为连铸机的关键设备之一,如果发生故障会直接影响连铸生产线的正常运行。
传统的液压设备维修方式只能减少设备故障的发生,难以满足在线设备故障为“0”管理目标,引入主动性维修的维修模式十分必要。
2.2液压系统设备精密度较高,一旦磨损,修复代价极高,且修复备件很难恢复原有性能,通常使用较短时间就必须更换新元件,造成维护费用居高不下。
为保证液压设备的使用寿命及可靠性,降低设备维修费用,引入主动性维修的维修模式十分必要。
2.3随着液压技术的发展,液压元件的设计越来越趋于合理,采用主动性维修的维修模式,使液压元件寿命大幅提高已成为可能。
3液压系统故障诊断步骤3.1认真阅读说明书,查阅设备运行记录,调查情况,观察现场,熟悉液压工作原理,从整体分析各元件在系统中的性能和作用。
3.2液压系统的故障先兆包括:压力变化、流量变化、噪声、振动、泄漏等.这些现象有时不会马上影响液压系统的运转,往往预示系统将出现故障,可借助视、触、听直观得到,也可借助仪器诊断。
3.3根据液压系统的故障先兆,找出故障具体部位,根据系统原理和经验逐步缩小范围。
3.4对具体的部位进行初步检验,并进一步用仪器反复检查。
3.5确定发生故障的元件,决定修理或者更换。
4连铸机液压系统的诊断和维修4.1油箱及循环冷却装置1)调节循环冷却器水循环阀门开度,以保证油箱内油温范围+40℃一+50℃。
2)油箱内油液面应高于泵组吸油管口300mm以上,以保证有足够的空间使油内的气泡上浮。
3)定期更换循环泵滤芯,保证循环过滤器进出口压差不大于4.5bar,过滤器进口压力不大于10bar。
4.2高压泵组:1)避免高压泵吸入空气,高压泵吸入空气后会出现剧烈响动,损害极大。
2)观察每台高压泵的斜盘角度,尽量保证其角度变化范围相同,即高压泵的输出负载均衡,以避免出现“大马拉小车”的情况。
4.3蓄能器组为了达到蓄能器的最大工作效率,保证罐中氮气压力(停机状态下)为系统压力的70%左右。
4.3控制阀台1)保证减压阀调压灵敏,输出压力平稳,如出现调节反应滞后,压力波动的情况应拆的阀进行清洗或换阀。
2)溢流阀调节压力一般为所装设备工作压力的120%,可用听声或手触的方法来判断其是否泄油,如出现连续泄油的情况,需要重新调节溢流阀,调节无效的根据情况换阀或更换内部密封件。
3)换向阀的故障一般会反应到执行元件的动作异常上。
一般常见问题主要为换向阀阀芯的阻滞或卡死,在执行元件上表现为操作反应滞后或反应,此时需要对该换向阀进行拆解清洗。
4)单向阀的故障一般表现为阀芯被异物卡住,变成通路,不能起到单向止流的作用。
5)而节流阀的故障一般为管路被截断,表现为执行元件单向无动作。
4.4液压执行元件4.4.1液压缸1)泄漏也是液压缸的主要故障之一,分为內泄与外泄,內泄主要表现为油缸动作缓慢、爬行等,外泄主要表现为拉杆油封或缸体密封等处的可见漏油。
2)遇到双油缸或多油缸协同工作时,必须保证油缸的同步性,可以通过调节管路上的节流阀来控制油缸速度,已达到油缸同步的目的。
3)处于高温、高湿、高尘工作环境下的液压缸必须做防护,如为暴露在高温辐射下油缸安装隔热板,缸杆加装伸缩防尘、防高温保护套等4)同时还应该尽量避免油缸的满行程工作,因为满行程工作会使活塞杆对缸体两端的冲击力大大提高,从而损坏缸体连接件及密封。
4.4.2液压马达液压马达的损坏主要是工作部分及运动件磨损,使间隙增大,进而引起输出扭矩与转速下降、泄漏增大及振动增大。
4.5液压系统泄漏液压系统泄漏是连铸机正常工作的大敌,根据经验,将泄漏分为“渗”、“滴”、“流”、“刺”,顾名思义,不同设备对泄漏的要求也有所不同,如发现高压胶管管体渗油的就必须更换,液压硬管出现滴油或流油现象的必须焊接,一旦出现刺油现象,必须立即处理,否则会出现液压油的大量流失。
5结论液压设备从主体讲属于机械设备,它作为一种机械产品与机械技术关系密切。
液压设备是一种流体动力机械,其工作原理,工作介质及由此而来的结构与工艺特征均体现了这一点。
液压设备是一种控制机构,它与控制技术同样关系密切。
液压系统与电气,电子及计算机系统有广泛的能量与信息的交流,两者之间相互依赖,相互渗透。
液压设备在各工业部门中广泛应用,它是实现其工艺目的或相应功能的工具,这些因素必然反映至液压设备的本身。
液压设备故障诊断与监测涉及各类测试手段,它与测试技术不可分离。
由此可见,液压设备综合了机械技术、流体技术、电气、电子与计算机技术,以及与设备执行的任务相关的技术(如金属切削,塑料或成型加工,钢铁冶金,采煤等)。
从系统论的角度看,液压设备是一个系统,它具备一般系统的基本特征:整体性、层次性、动态性与目的性。
因此,系统分析方法非常适合液压系统故障的分析。
参考文献:[1] 李尧忠. 轴承清洗机液压系统的设计[J]. 液压与气动, 2009,(07)[2] 温新民. 液压系统设计中过滤元件的选型[J]. 流体传动与控制, 2010,(01)文档资料:连铸机液压系统故障诊断与维修完整下载完整阅读全文下载全文阅读免费阅读及下载阅读相关文档:对建筑工程施工项目管理的几点思考探讨城市园林绿化工程建设的全程管理问题浅析当前的园林施工管理和绿化养护管理浅谈如何提高公路工程概预算编制质量基于发行公司融资目的的优先股发行选择阐述如何有效的做好企业行政管理工作战略论企业股利分配政策的制定因素及经济影响长输管道施工技术与对策探析小议建筑工程造价预结算审核基于P2P平台的创新型公益助农金融模式探究企业材料存货预警管理现代医院经济管理创新模式探讨浅谈煤炭运销中供应链管理现状及对策浅谈中小企业“融资难”问题的成因及对策优化煤炭企业资金与结算管理体系苹果公司的经营策略分析试论企业工商管理最新最全【学术论文】【总结报告】【演讲致辞】【领导讲话】【心得体会】【党建材料】【常用范文】【分析报告】【应用文档】免费阅读下载*本文收集于因特网,所有权为原作者所有。
若侵犯了您的权益,请留言。
我将尽快处理,多谢。
*。