汽车厂制造质量管理制度
汽车制造质量管理制度
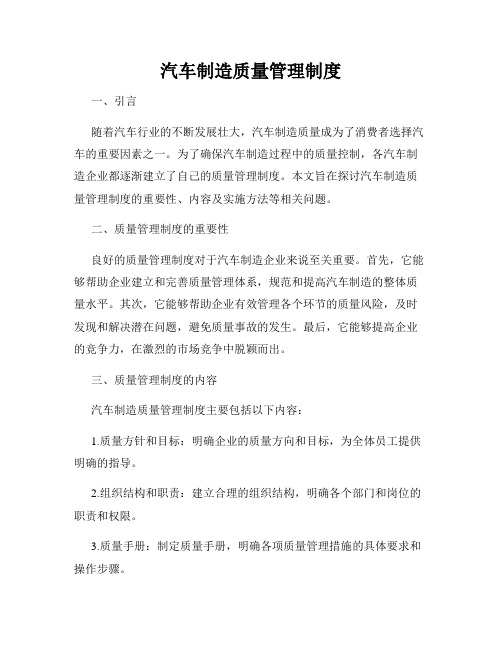
汽车制造质量管理制度一、引言随着汽车行业的不断发展壮大,汽车制造质量成为了消费者选择汽车的重要因素之一。
为了确保汽车制造过程中的质量控制,各汽车制造企业都逐渐建立了自己的质量管理制度。
本文旨在探讨汽车制造质量管理制度的重要性、内容及实施方法等相关问题。
二、质量管理制度的重要性良好的质量管理制度对于汽车制造企业来说至关重要。
首先,它能够帮助企业建立和完善质量管理体系,规范和提高汽车制造的整体质量水平。
其次,它能够帮助企业有效管理各个环节的质量风险,及时发现和解决潜在问题,避免质量事故的发生。
最后,它能够提高企业的竞争力,在激烈的市场竞争中脱颖而出。
三、质量管理制度的内容汽车制造质量管理制度主要包括以下内容:1.质量方针和目标:明确企业的质量方向和目标,为全体员工提供明确的指导。
2.组织结构和职责:建立合理的组织结构,明确各个部门和岗位的职责和权限。
3.质量手册:制定质量手册,明确各项质量管理措施的具体要求和操作步骤。
4.流程控制:建立标准化的流程控制流程,确保每个生产环节都能按照规定的要求进行操作。
5.供应商管理:建立供应商评估和管理机制,确保优质的原材料和零部件供应。
6.质量培训:组织质量培训活动,提高员工的质量意识和技能水平。
7.质量检测与控制:建立质量检测和控制体系,包括出厂检测、过程检测和产品追溯等。
8.不良品管理:建立不良品管理机制,及时发现和处理不良品,并采取相应的纠正措施。
9.持续改进:建立持续改进机制,通过不断的数据分析和评估,提出改进措施,并加以实施。
四、质量管理制度的实施方法为了确保质量管理制度的有效实施,企业可以采取以下方法:1.制定计划:制定详细的质量管理计划,明确各项任务的时间节点和责任人。
2.分工协作:各部门和岗位之间建立良好的沟通和协作机制,形成合力推进质量管理工作。
3.培训教育:开展相关的培训和教育活动,提高员工的质量管理意识和操作能力。
4.制度宣传:充分宣传质量管理制度的重要性和好处,增强员工的参与和认同感。
汽车制造企业质量管理制度
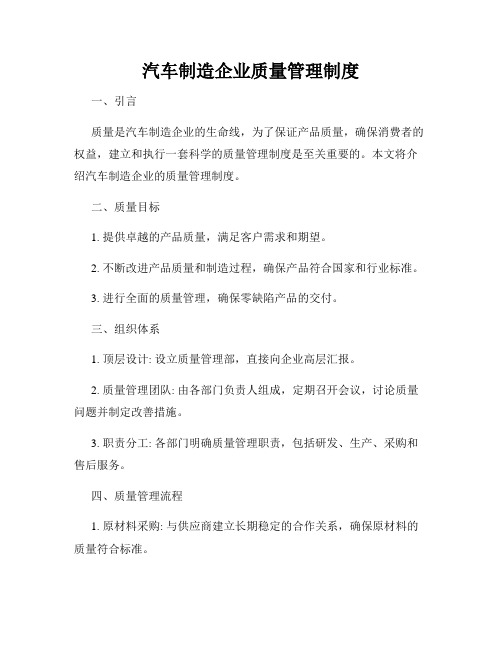
汽车制造企业质量管理制度一、引言质量是汽车制造企业的生命线,为了保证产品质量,确保消费者的权益,建立和执行一套科学的质量管理制度是至关重要的。
本文将介绍汽车制造企业的质量管理制度。
二、质量目标1. 提供卓越的产品质量,满足客户需求和期望。
2. 不断改进产品质量和制造过程,确保产品符合国家和行业标准。
3. 进行全面的质量管理,确保零缺陷产品的交付。
三、组织体系1. 顶层设计: 设立质量管理部,直接向企业高层汇报。
2. 质量管理团队: 由各部门负责人组成,定期召开会议,讨论质量问题并制定改善措施。
3. 职责分工: 各部门明确质量管理职责,包括研发、生产、采购和售后服务。
四、质量管理流程1. 原材料采购: 与供应商建立长期稳定的合作关系,确保原材料的质量符合标准。
2. 产品设计: 根据客户需求和市场趋势进行产品设计,并进行严格的验证和测试。
3. 生产制造: 制定生产作业指导书,明确每个环节的质量要求和检测方法。
4. 检测与测试: 建立全面的检测与测试流程,确保产品符合设计规范。
5. 不良品处理: 对于不良品,建立相应的处理流程,包括返修、返厂和报废等。
6. 售后服务: 建立售后服务团队,及时回应客户投诉并提供解决方案。
五、质量管理工具1. 六西格玛: 运用统计学方法分析和改善制造过程,减少缺陷率并提高产品质量。
2. PDCA循环: 制定计划、实施、检查和纠正措施,不断循环优化质量管理。
3. 5W2H法: 运用问答方式明确问题的原因和解决方案,确保质量问题得到有效解决。
4. 故障模式和影响分析(FMEA): 针对可能出现的故障进行分析,制定预防措施,降低质量风险。
六、质量监控与评估1. 内部审核: 定期进行内部质量管理体系审核,发现问题并及时改进。
2. 外部认证: 参加相关质量管理体系认证,如ISO9001国际标准认证,提升质量管理水平。
3. 客户满意度调查: 定期进行客户满意度调查,了解客户对产品和服务的评价,并及时回应问题。
车辆制造行业管理制度
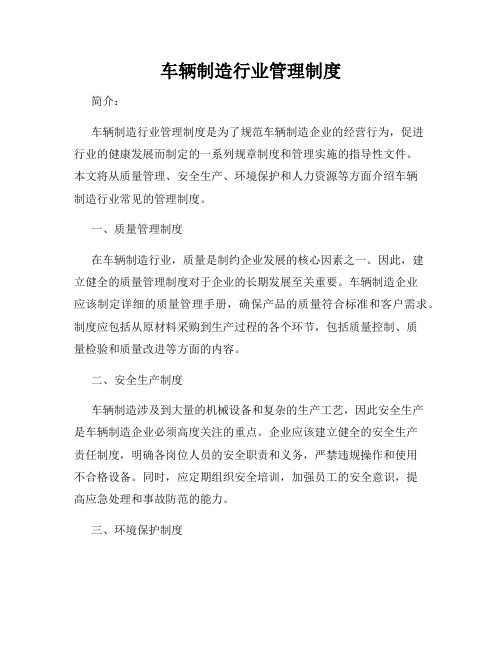
车辆制造行业管理制度简介:车辆制造行业管理制度是为了规范车辆制造企业的经营行为,促进行业的健康发展而制定的一系列规章制度和管理实施的指导性文件。
本文将从质量管理、安全生产、环境保护和人力资源等方面介绍车辆制造行业常见的管理制度。
一、质量管理制度在车辆制造行业,质量是制约企业发展的核心因素之一。
因此,建立健全的质量管理制度对于企业的长期发展至关重要。
车辆制造企业应该制定详细的质量管理手册,确保产品的质量符合标准和客户需求。
制度应包括从原材料采购到生产过程的各个环节,包括质量控制、质量检验和质量改进等方面的内容。
二、安全生产制度车辆制造涉及到大量的机械设备和复杂的生产工艺,因此安全生产是车辆制造企业必须高度关注的重点。
企业应该建立健全的安全生产责任制度,明确各岗位人员的安全职责和义务,严禁违规操作和使用不合格设备。
同时,应定期组织安全培训,加强员工的安全意识,提高应急处理和事故防范的能力。
三、环境保护制度车辆制造行业对环境的影响较大,因此企业要积极履行环境保护责任,制定环境保护制度,确保符合法律法规和标准要求。
企业应建立健全的环境管理体系,对废气、废水、废弃物等进行有效控制和处理。
此外,还应推广节能减排技术,提升资源利用效率,促进可持续发展。
四、人力资源管理制度人才是企业发展的核心资源,人力资源管理制度的健全对于车辆制造企业的长远发展至关重要。
企业应该制定详细的员工招聘、培训、绩效考核和薪酬福利制度,建立激励机制,提高员工的工作积极性和主动性。
同时,要关注员工的职业发展和福利保障,营造良好的工作环境和企业文化。
五、监督检查制度为了保证管理制度的有效实施,车辆制造企业应建立监督检查制度。
企业可以通过内部审核、第三方评估和监督抽查等方式,对质量管理、安全生产、环境保护和人力资源等方面进行全面检查,及时发现问题并采取正确的纠正和改进措施。
结论:车辆制造行业管理制度是企业健康发展的保障,能够规范企业的经营行为,提升核心竞争力。
汽车制造质量控制管理规章制度

汽车制造质量控制管理规章制度一、总则汽车制造质量控制管理规章制度(以下简称“规章制度”)是为了确保汽车制造过程中的质量控制,保障汽车品质,提高用户满意度而制定。
该规章制度适用于本公司的汽车制造环节,并严格按照国家相关法规执行。
二、质量管理责任1. 公司领导层应设立质量管理部门,并明确主管人员和质量管理人员的责任。
2. 质量管理部门应制定并贯彻执行质量管理制度,确保各制造环节符合规定要求。
3. 各部门应积极配合质量管理部门的工作,确保制造过程中的质量可控。
三、质量控制流程1. 设计阶段1.1 设计部门应对汽车设计进行全面评估和验证,确保设计方案符合国家和公司的相关规定。
1.2 设计变更需经过设计变更评估和批准,确保变更后的设计方案仍然符合相关要求。
1.3 设计部门应建立设计变更跟踪制度,及时掌握和处理设计变更。
2. 采购阶段2.1 采购部门应确保供应商具备合法资质,且供应的零部件符合质量要求。
2.2 采购部门应建立供应商评价机制,定期对供应商进行评估,并及时处理不合格供应商。
2.3 采购的零部件应提供合格证明,确保零部件符合相关要求。
3. 生产制造阶段3.1 生产制造部门应建立生产制造记录,详细记录生产过程中的各项参数和操作。
3.2 生产制造部门应设立严格的零部件入库检验制度,及时发现和处理不合格零部件。
3.3 生产制造部门应进行产品工艺过程分析,确保每个制造环节达到预期的质量要求。
4. 检测验证阶段4.1 质量管理部门应对生产车辆进行全面检测和验证,确保每辆汽车都符合质量要求。
4.2 检测记录应进行归档保存,作为质量问题追溯和解决的依据。
4.3 不合格产品应及时追踪处理,以防止不合格产品流入市场。
四、问题处理1. 质量管理部门应及时处理生产中发现的质量问题,采取措施消除质量问题的影响。
2. 质量问题发生后,相关部门应组织调查,找出问题根源,并进行整改。
3. 产品召回和质量投诉应及时受理和处理,确保用户权益不受侵害。
汽车质量管理制度范文大全
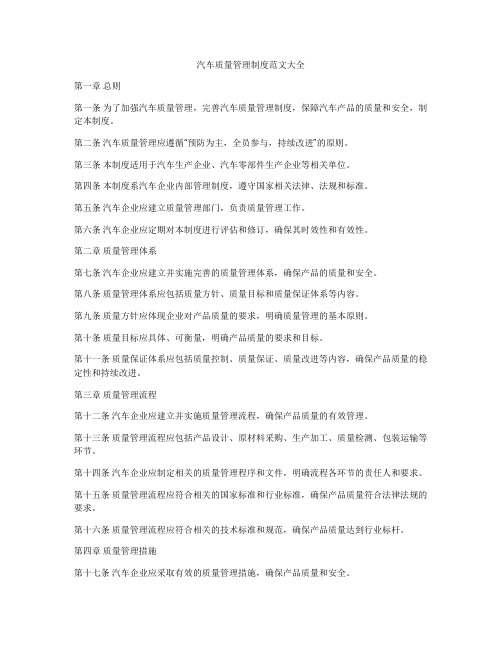
汽车质量管理制度范文大全第一章总则第一条为了加强汽车质量管理,完善汽车质量管理制度,保障汽车产品的质量和安全,制定本制度。
第二条汽车质量管理应遵循“预防为主,全员参与,持续改进”的原则。
第三条本制度适用于汽车生产企业、汽车零部件生产企业等相关单位。
第四条本制度系汽车企业内部管理制度,遵守国家相关法律、法规和标准。
第五条汽车企业应建立质量管理部门,负责质量管理工作。
第六条汽车企业应定期对本制度进行评估和修订,确保其时效性和有效性。
第二章质量管理体系第七条汽车企业应建立并实施完善的质量管理体系,确保产品的质量和安全。
第八条质量管理体系应包括质量方针、质量目标和质量保证体系等内容。
第九条质量方针应体现企业对产品质量的要求,明确质量管理的基本原则。
第十条质量目标应具体、可衡量,明确产品质量的要求和目标。
第十一条质量保证体系应包括质量控制、质量保证、质量改进等内容,确保产品质量的稳定性和持续改进。
第三章质量管理流程第十二条汽车企业应建立并实施质量管理流程,确保产品质量的有效管理。
第十三条质量管理流程应包括产品设计、原材料采购、生产加工、质量检测、包装运输等环节。
第十四条汽车企业应制定相关的质量管理程序和文件,明确流程各环节的责任人和要求。
第十五条质量管理流程应符合相关的国家标准和行业标准,确保产品质量符合法律法规的要求。
第十六条质量管理流程应符合相关的技术标准和规范,确保产品质量达到行业标杆。
第四章质量管理措施第十七条汽车企业应采取有效的质量管理措施,确保产品质量和安全。
第十八条质量控制措施应包括质量计划、质量检测、产品检验、质量记录等内容。
第十九条质量保证措施应包括质量培训、质量审核、质量分析、质量改进等内容。
第二十条质量改进措施应包括持续改进、问题解决、预防控制、纠正措施等内容。
第二十一条汽车企业应建立质量管理档案,记录质量管理的各项活动和结果。
第五章质量管理责任第二十二条汽车企业应建立并实施质量管理责任制,确保质量管理的有效执行。
汽车制造业质量管理制度
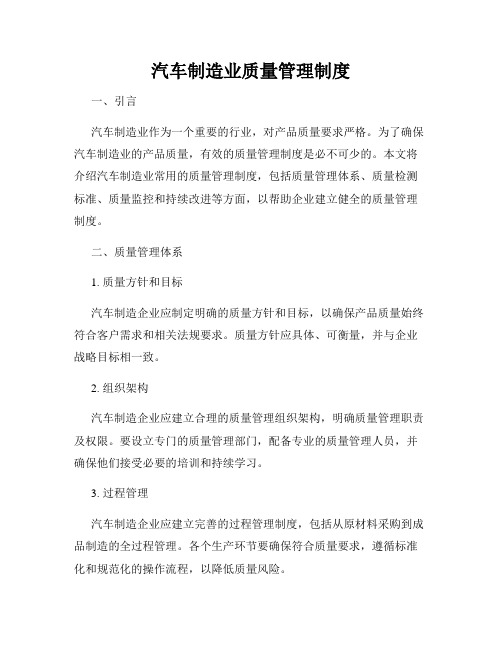
汽车制造业质量管理制度一、引言汽车制造业作为一个重要的行业,对产品质量要求严格。
为了确保汽车制造业的产品质量,有效的质量管理制度是必不可少的。
本文将介绍汽车制造业常用的质量管理制度,包括质量管理体系、质量检测标准、质量监控和持续改进等方面,以帮助企业建立健全的质量管理制度。
二、质量管理体系1. 质量方针和目标汽车制造企业应制定明确的质量方针和目标,以确保产品质量始终符合客户需求和相关法规要求。
质量方针应具体、可衡量,并与企业战略目标相一致。
2. 组织架构汽车制造企业应建立合理的质量管理组织架构,明确质量管理职责及权限。
要设立专门的质量管理部门,配备专业的质量管理人员,并确保他们接受必要的培训和持续学习。
3. 过程管理汽车制造企业应建立完善的过程管理制度,包括从原材料采购到成品制造的全过程管理。
各个生产环节要确保符合质量要求,遵循标准化和规范化的操作流程,以降低质量风险。
4. 质量审核汽车制造企业应定期进行内部质量审核,以评估质量管理体系的有效性和符合性。
同时,也要接受外部审核,如客户审核、认证机构审核等,以增加质量管理的公信力。
三、质量检测标准1. 零部件检测标准汽车制造企业应制定详细的零部件检测标准,包括材料的质量要求、工艺的要求、外观的要求等。
要确保零部件符合相应的国家和行业标准,并进行必要的测试和验证。
2. 整车质量检测标准汽车制造企业应制定整车质量检测标准,包括性能测试、安全测试、使用寿命测试等方面。
要确保整车质量符合国家和行业标准,以提高产品的可靠性和安全性。
3. 检测设备和方法汽车制造企业应配备先进的检测设备和仪器,并制定相应的检测方法和规程。
要确保检测设备的准确性和可靠性,并对检测人员进行培训,提高检测的准确度和效率。
四、质量监控1. 现场质量监控汽车制造企业应建立全面的现场质量监控机制,包括质量巡检、质量抽检、故障分析等。
要及时发现和纠正质量问题,确保产品符合质量要求。
2. 供应商质量监控汽车制造企业应对供应商进行严格的质量管理,包括供应商审查、质量评估、供应商绩效监控等。
汽车制造行业整车质量管理制度
汽车制造行业整车质量管理制度随着汽车产业的不断发展,整车质量管理在汽车制造行业中显得尤为重要。
为了确保生产的汽车质量符合国家标准和用户要求,汽车制造企业需要建立一套完善的整车质量管理制度。
本文将从质量管理体系、制度要求、质量控制和质量检验等方面,详细介绍汽车制造行业的整车质量管理制度。
一. 质量管理体系汽车制造企业通过建立质量管理体系来规范整车质量管理流程,确保产品质量的稳定性和可靠性。
质量管理体系主要包括以下几个方面:1. 质量方针和目标:制定企业的质量方针和目标,明确整车质量的管理导向和目标。
2. 组织架构:明确质量管理部门的职责和权责,建立相应的管理机构和岗位职责。
3. 责任制度:明确各部门的质量责任,建立质量管理责任制度,确保各个环节的质量责任明确。
4. 过程管理:建立生产过程管理制度,包括原材料采购、工艺流程控制、装配与调试等各个生产环节的质量控制。
5. 过程改进:建立持续改进机制,通过不断改进生产工艺和管理方法,提升整车质量水平。
二. 制度要求为了确保整车质量管理的规范性,汽车制造企业需要制定一系列的制度要求,以明确各个环节的操作规范和要求。
以下是一些常见的制度要求:1. 质量控制计划制度:明确整车质量控制的计划编制和执行要求,包括质量目标、控制点和检验标准等。
2. 质量记录管理制度:确保整车生产过程中相关的质量记录完整、准确,并能够进行追溯,以便在出现问题时进行溯源和处理。
3. 关键质量特性管理制度:建立关键质量特性的管理制度,包括关键零部件的选择、质量控制和检验要求等,以确保整车质量的可控性。
4. 不合格品管理制度:明确不合格品的处理流程和责任追究制度,包括不合格品的处置方式、责任追究和改进措施等。
三. 质量控制汽车制造企业在整车质量管理中,需要通过质量控制来确保产品的质量达到要求。
质量控制主要包括以下几个方面:1. 零部件供应商管理:建立供应商评价和审核机制,确保向企业供应的零部件质量达到要求。
整车行业汽车质量管理制度
整车行业汽车质量管理制度随着汽车产业的快速发展,整车行业的汽车质量管理制度变得尤为重要。
汽车制造商和相关利益相关者越来越关注如何提高汽车质量,以满足消费者对安全、耐用性和性能的需求。
因此,建立健全的汽车质量管理制度是整车行业的一项关键举措。
1. 质量管理体系1.1 质量方针和目标整车行业的汽车制造商应制定明确的质量方针和目标,以明确其对汽车质量的承诺和追求。
质量方针应包括对产品质量、安全性和符合法规要求的承诺。
目标应具体、可衡量,并纳入公司的战略规划和绩效评估体系中。
1.2 组织架构汽车制造商应建立一套完善的组织架构,确保质量管理职责明确、岗位设定合理。
质量部门应承担主要的质量管理职责,包括质量控制、质量改进和质量培训等。
同时,各部门应密切协作,形成质量管理的整体合力。
2. 质量控制2.1 零部件供应商管理整车行业的汽车制造商应建立供应商评估和管理体系,对供应商进行定期评估和审核,确保其提供的零部件符合质量要求。
同时,制定合格供应商名录,定期对供应商进行跟踪管理和绩效评估。
2.2 制造过程控制汽车制造商应采用先进的制造工艺和技术,确保汽车的每个生产环节都符合质量标准。
通过制定作业指导书和质量检验标准,确保每位操作工人都按照规定的程序和标准进行工作。
重点关注易出现质量问题的环节,采取有效的控制措施,防止缺陷的产生。
3. 质量改进3.1 缺陷分析和纠正措施整车行业的汽车制造商应建立缺陷分析和纠正措施的机制,对产品质量问题进行详细分析,并采取相应的纠正措施。
通过应用质量工具和方法,如贝叶斯分析、鱼骨图等,找出问题的根本原因,并采取措施避免类似问题再次发生。
3.2 持续改进质量改进是整车行业的一项重要任务。
汽车制造商应建立质量改进的长效机制,鼓励员工提出改进建议,开展质量创新活动。
通过持续改进,不断提高汽车产品的质量和性能,满足消费者的需求和期望。
4. 质量培训整车行业的汽车制造商应加强员工的质量培训,提高其质量意识和技能水平。
汽车制造公司质量管理制度
汽车制造公司质量管理制度在汽车制造业中,质量管理制度是确保产品质量稳定和持续改进的关键。
汽车制造公司应根据市场需求和行业标准,制定一套科学、系统的质量管理制度,以保证汽车的质量和安全,提高客户满意度并提升企业竞争力。
一、质量方针与目标汽车制造公司的质量方针是指导质量管理工作的总体方向和原则。
对于汽车制造公司而言,质量方针的核心是产品安全可靠、客户满意、持续改进和符合法律法规的要求。
质量方针应与公司整体战略一致,并由高层管理者承诺和推行。
质量目标是贯彻质量方针的具体指标,可以包括但不限于降低出厂次品率、提高产品合格率、减少客户投诉率等。
质量目标应设定为可实现的,具体到部门或个人,并定期进行评审和监测。
二、组织结构为实施有效的质量管理制度,汽车制造公司需建立一套完整的组织结构。
该结构应体现权责分明、信息畅通和协作高效的原则。
1. 高层管理层:负责确立质量方针与目标,并提供足够的资源支持质量管理工作。
2. 质量管理部门:负责制定、推行和监督质量管理制度,并提供培训和指导。
该部门与其他部门之间应形成有效的沟通机制。
3. 生产部门:负责实施质量管理制度,进行产品生产和质量控制。
三、质量管理制度要求1. 设计与开发阶段:在产品设计与开发阶段,汽车制造公司应采用先进的技术手段进行模拟和验证,确保产品设计符合规范和客户需求。
同时,应建立设计变更管理制度,确保任何设计变更都经过评审和验证,并及时通知相关部门。
2. 供应商管理:汽车制造公司应与供应商建立长期稳定的合作关系,并对供应商进行评估和认证。
对于关键零配件供应商,应进行更为详细的审核与管理,确保产品质量的稳定性。
3. 生产过程管理:应建立完善的生产工艺和操作规程,明确每个工序的质量标准与验收要求。
生产线上应设置充足的自动化设备和监测系统,确保产品质量的可控性和稳定性。
4. 检测与检验:汽车制造公司应建立完整的检测与检验体系,包括原材料的进货检验、在制品抽样检验、成品检验等。
汽车制造行业管理制度的质量控制
汽车制造行业管理制度的质量控制1. 引言在汽车制造行业中,质量控制是至关重要的,它不仅关乎厂商的声誉和市场竞争力,也直接关系到消费者的安全与满意度。
因此,建立一套科学、高效的管理制度对于保障汽车质量至关重要。
2. 质量控制体系2.1 质量目标设定在汽车制造行业中,企业应当设定明确的质量目标,以满足国家标准和相关法规的要求。
质量目标应当包括产品的性能、可靠性、安全性等方面的要求,并且与企业的发展战略相一致。
2.2 质量管理组织汽车制造企业应当设立质量管理部门或类似机构,负责制定、执行和监督质量控制的各项工作。
该部门应当由专业的质量管理人员组成,并且与其他相关部门密切合作,确保质量控制工作的全面推进。
2.3 质量管理流程汽车制造企业应当建立完善的质量管理流程,包括从产品设计、工艺制造、供应链管理到售后服务等各个环节。
每个环节都应当设定相应的质量控制标准,并配备相应的控制措施,以确保产品的质量稳定可靠。
3. 质量控制措施3.1 原材料质量控制在汽车制造过程中,原材料的质量直接影响到最终产品的质量。
因此,企业需要建立起严格的原材料供应商评估机制,确保所采购的原材料符合质量标准,并进行必要的检测和验收。
3.2 生产工艺质量控制汽车制造企业应当制定科学的生产工艺,并建立相应的质量控制标准和检测方法,确保生产流程的稳定性和产品的一致性。
此外,应当配备合适的设备和工具,以确保生产过程中的质量控制。
3.3 产品测试与验证在汽车制造完成之后,必须进行各项产品测试和验证,以确保产品性能和安全性符合要求。
这包括对整车、零部件和系统的各项功能和性能进行全面检测,并对不合格产品进行及时处理和追溯。
4. 质量评估与改进4.1 质量评估方法汽车制造企业应当建立完善的质量评估体系,采取有效的方法和工具,对产品和生产过程进行定期的评估和检查。
这可以包括定期的内部审核、外部认证、市场调研等,以确保质量控制工作的有效性和持续改进。
4.2 质量改进措施通过质量评估结果的分析,汽车制造企业应当及时采取相应的改进措施,以解决存在的问题和缺陷。
- 1、下载文档前请自行甄别文档内容的完整性,平台不提供额外的编辑、内容补充、找答案等附加服务。
- 2、"仅部分预览"的文档,不可在线预览部分如存在完整性等问题,可反馈申请退款(可完整预览的文档不适用该条件!)。
- 3、如文档侵犯您的权益,请联系客服反馈,我们会尽快为您处理(人工客服工作时间:9:00-18:30)。
密级:普通保存期限:长期XX汽车制造有限公司企业标准制造质量管理制度版)(第A批准审核编制—XX实施—发布——2012XX 2012XX汽车制造有限公司发布文件会签及文件修改记录表总装车间质量管理体系一、总装车间新员工培训为保证新员工尽快熟悉、适应车间生产环境、培训工艺流程,遵守公司、车间各项规章制度,在短期内达到车间岗位资质要求,特制定此培训计划。
一、培训内容及时间安排二、培训流程及要求(培训流程见附表)1.由车间统计员对新员工建立人事档案,并将人名单转交给车间安全员及质量组。
2.由车间安全员对新员工进行安全、纪律、现场培训,培训时间为2小时,培训完成后通知质量组。
3.由工艺员对新员工进行工艺流程、工艺标准、工艺纪律等培训,培训时间为2小时,培训完成后通知生产调度。
4.由生产调度根据车间实际情况将新员工分配到各段。
5.工段进行工段内二级培训,班组进行三级培训。
6.班组指派专人负责培训新员工的实际操作,并对新员工状况进行监督,实习完后出具《新员工评价表》.三、评价方法依据车间岗位资质要求对在车间培训的实习员工,根据其在实习期间的技能掌握、现场安全、质量意识、劳动纪律等方面表现进行统一考核、评价,对新员工符合岗位资质要求进行评价。
建立新员工操作评价表,由班组长或指定培训人根据新员工现场操作情况进行评价。
如综合得分在90分以上,评价为A;综合得分在70-90分,评价为B ;综合得分在70分以下,评价为C。
①、察看新员工操作与作业指导书的一致性,以及工序排布的合理性,占50分;②、考核新员工生产节拍是否能能达到要求,占20分。
③、车间工艺员跟踪装配状况是否能一次装配到位,是否按作业指导书、车间质量管理规定进行操作,做实际操作评价,占30分。
四、实习要求1、保证实习期间的安全。
2、各段记录好相应的考勤。
3、严格执行请销假制度。
(工段负责)4、严格遵守公司及车间各项规章制度。
(工段负责)5、实习人员必须认真学习实习内容,达到实习目的。
6、实习结束时车间对实习人员进行综合考评,出具考评结果。
二、总装车间信息反馈制度目的:为了完善总装的信息管理,制定此制度。
1、每周二由质量员向各工段以电子版的方式反馈上周装配质量信息,出具质量控制重点,通报上周的质量情况,在质量看板上公布各工段执行情况。
2、对于各工段汇报的质量缺陷,质量组应及时向相关部门(工段)反馈,并在相关部门回复后第一时间给予提出问题工段回复。
复修组每日上报问题需当日上午(11:00之前)反馈车间统计,车间统计汇总完成后电子版于下午(15:30之前)转交车间质量员,由质量组对多发及重大问题进行立项,立项内容由车间质量员汇总到年度总装车间质量立项表中。
人为装配问题各工段按质量组下发的时间节点完成,质量组按时间节点验收;涉及其它部门不能及时解决的问题由质量组每周向其它部门反馈并组织改进。
3、新车型的试制期间各工段有义务对各工段问题进行整理汇总,于当日汇报质量组工艺员,由工艺员总结并反馈相关部门。
4、质量组有义务对改进反馈的改进状况、0-500公里问题、过程质量问题、PDI每周问题状况、售后环节出现的问题状况、以及检验反馈的最新问题、FTT、ZCPA问题状况、每周向各工段汇报,涉及车间装配的工段立项,涉及其它部门的由工艺员协助沟通解决。
5、对于下序反馈的人为装配质量问题,质量组需在第一时间内对质量缺陷进行判定,其处理结果按《总装车间生产过程管理规定》执行。
6、对质量部下达给总装车间的各种质量任务,各工段有义务按时间节点反馈完成。
7、车间在信息反馈过程中,发生问题需由总装工艺人员制定临时措施,车间操作工执行工艺标准,管理人员监督执行。
8、在本班组内发生的质量问题必须及时上报质量组,出现重大质量问题、批量质量事故,隐瞒不报的责任人及管理人员一经发现,工段长、班组长、操作者直接免除当月工资的50%。
三、《总装车间过程质量管理规定》1、缺陷等级A类:影响整车安全及性能的关键工序、质量控制点在装配时未按作业指导书装配到位或未按作业指导书调整到位的。
漏装、漏紧、错装问题。
漆面严重坑包。
不合格品装配。
B类:各种功能件未按作业指导书装配到位\调整到位C类:漆面脏污\小划伤\内饰脏污\车内杂物D类:各项记录填写不规范2、考核标准(与其它制度不重复)A类缺陷(包含可能会发生人身安全、丧失产品主要功能,严重影响产品使用性能,降低产品寿命,对环境产生违反法规的污染以及必然会引起顾客申诉的):具体操作:下序每发现一次对操作者考核100元,车辆流入市场操作者车间内待岗;班组长考核100元。
大于5台小于10台操作者直接车间内待岗,班组长免职,工段长考核200元。
因互检失职流入下序的对互检责任人罚款100元。
对避免流入下序的其他工位操作者奖励100元。
B类缺陷(包含可能会影响产品使用性能和寿命或引起产品局部功能失效,顾客可能会提出申诉的):具体操作:下序每发现一次对责任人考核50元。
大于5台小于10台按A类缺陷处理。
一月内出现三次以上按A类缺陷处理,并对班组长考核100元。
一月内出现三次以上对工段长考核100元。
对避免流入下序的其他工位操作者奖励50元;C类缺陷(包含对产品的使用性能及寿命影响不大,顾客可能发现但不致引起顾客申诉的):具体操作:第一次不考核,由班组长培训,第二次考核30元,一月内连续出现三次者升为B类缺陷处理。
D类缺陷:第一次不考核,由班组长培训,第二次车间组织培训,一月内连续出现三次者升为C 类缺陷考核。
下序发现上序有A类、B类、C类缺陷发生的(不在自检互检范围)避免流入下序的,对操作者依据上述处罚条例额度给予考核,反馈者给予考核金额1/3的奖励。
互检人员考核金额为被考核人的1/2.四、《总装车间检验记录卡管理规定》目的:规范总装检验记录卡填写要求,提高工艺纪律过程管控,提高产品质量过程的可追溯性。
制度要求:1. 要求生产线所有员工及多能工人员熟悉自身工作内容,在总装检验记录卡上认真添写记录。
2. 操作者者名字写在操作者一栏内,对装配的配件厂家用下划线加以确认。
3. 检验记录卡暂无配套厂家的由操作者临时添加并返馈班组长、工段长;班组长、工段长反馈车间质量员,由车间质量员定期上报检验科。
4. 操作者在填写检验记录卡时要求使用黑、蓝两色签字笔或圆珠笔,禁止除上述以外的任何颜色和性质的工具。
5. 操作者在填写检验记录卡过程中字体要求字迹清晰工整,严禁签写无法辨认的连笔字。
6. 操作者填写检验记录卡涉及多项填写内容时,在对应内容分别填写,禁止跨项目填写一个名字。
7. 操作者完成全部作业并确认无误后自行填写检验记录卡,严禁提前填写和他人替签,违者每项考核5元。
8. 如遇到零配件质量或上序质量问题造成某工序无法正常操作,在工段长/班组长或工艺员同意后序装配而本工位暂不装配的情况,需在检验记录卡上注明(依据所在工段、分别填写进内饰/机舱/成车检验工位下的“其他问题描述”一栏中),如不填写,按照《总装车间过程质量管理规定》进行考核。
9. 总装车间所有员工在发现车身漆面问题时,有义务在检验记录卡上<车身油漆涂层检修记录卡>一页的车身相应位置上进行标注,并标明发现工位。
五、《不合格品管理规定》1、建立总装生产线不合格品台帐。
2、在各工段设立不合格品专用货架。
3、在生产过程中出现不合格部件后,相关操作者需立即将不合格品放置的专用货架上,并粘贴车间不合格品标识。
4、班组长组织(每天一次)由总装车间检验对不合格品开据不合格品检验单,并在显著位置粘贴标识。
发生批量问题时,反馈车间质量员,由车间质量员组织相关部门进行评审。
5在更换不合格品过程中需遵守不合格品更换流作业流程。
六、《关键工序的控制办法》关键工序与质量控制点的设置原则:a)关键工序确定原则:对最终产品的性能、寿命、可靠性及经济性等方面有直接影响的工序;b)质量控制点确定原则:工序加工质量不能通过其后的检验与试验完全确定,仅在产品使用或服务交付后才暴露出来的工序。
1、车间工艺员负责对关键工序及质量控制点操作人员定期进行培训,培训表格存档。
应根据以上的原则,以管理看板的形式明确关键工序并制定相应的技术标准和操作规程予以明确标识,悬挂在相应工位。
2、各班组长对关键工序及质量控制点进行每日抽查。
抽查内容添写在总装车间日问题汇总表格中,抽查频次不少于5%。
3、车间工艺员在工艺纪律检查时重点对其监控,发现问题处理意见同总装车间过程管理措施中A类缺陷。
七、定扭力扳手操作管理规定目的:为规范定扭力扳手的操作,使操作正确,示值准确,减少因使用不当给后序造成的重大质量事故特制定本管理规定1.扭力扳手只能用作安装紧固件(螺栓、螺母)时测量其安装力矩使用,绝不能作为拆卸工具去拧松已拧紧的紧固件。
不能敲打、磕碰或作它用。
使用时轻拿轻放,不许任意拆卸与调整。
2.使用定扭力扳手应校准合格且在有效期内的扭力扳手。
3.为了保证工作人员正确使用和测量值的准确,防止对工具、设备的损害,必须确保所施加的扭矩值在扭矩设备的范围内,在使用扭矩设备前请正确了解扳手的最大量程,不能乱用。
选择扳手的条件最好以工作值在被选用扳手的量限值20%~80%之间为宜。
4.使用时施力方向应同扳手上的箭头一致。
5.扳手报警后请勿继续用力。
6.操作中,先用风枪将螺栓拧到设定扭矩值的80%左右。
风枪应由工艺员根据扭矩设定要求选配相应规格。
7.紧固时应使用正确的接头,否则会导致施加的扭矩出现人为误差。
接头应接触紧密,有足够硬度。
8.从加载的安全考虑,在扳手手柄上尽量使用拉力(力向上)而不是推力(力向下)。
要调整操作姿势,防止操作失败时人员跌倒。
9.使用前后,扳手存放盒内,不可到处放置。
使用后,擦拭干净放入盒内。
长期不用的定力扳手使用后要注意将示值调节到最小值处,以保证其准确度及使用寿命。
否则,往往会使定力扳手提前失效或损坏。
10.使用时应严禁在尾部加套管或长柄,有专用配套附件(长柄或套管)除外。
力必须加在手柄尾端,使用时用力要均匀、缓慢。
要正确区分扳手柄被锁住了还是扳手润滑不好这两种情况,以使扳手调节到需要的扭矩值。
定力扳手锁环处于“锁住”时,不要强行转动手柄。
当锁环处于“不锁住”时,调节数值,工作值选定后,使锁环处于“锁住”后进行工作。
11.如果扳手较长时间未用过,(使用前)应先预加载几次,使内部工作机构的润滑油均匀流遍。
12.每周过程审核及工艺纪律检查专检项,如违反操作使用规程,责任人考核20-50元,班组长通报批评,如重复发生,建议车间内待岗。
八、《总装车间质量改进管理规定》目的:为了对总装质量改进项目进行有效的监督控制,规范立项及项目等级评审的相关内容,制订本流程。
适用范围:本流程适用于总装车间根据内外部顾客需求采取的纠正、改进和预防措施管理。