花生油生产工艺
花生油传统压榨工艺

花生油传统压榨工艺
花生油的传统压榨工艺是一种古老的生产方法,主要分为以下几个步骤:
1. 选材,首先要选择新鲜的花生作为原料。
通常选择成熟的花生果实,这样可以保证花生油的口感和香味。
2. 清洗,将选好的花生进行清洗,去除表面的杂质和土壤。
3. 烘烤,清洗后的花生果实要进行烘烤,以去除多余的水分,同时增加花生的香味。
这一步也有助于破坏花生中的抗营养因子,提高营养成分的吸收率。
4. 压榨,烘烤后的花生果实被送入压榨机进行压榨。
传统的压榨机通常是利用物理压力将花生压榨成油,而不使用化学溶剂。
这种方法可以保留花生油中的营养成分和天然香味。
5. 沉淀分离,经过压榨后的花生油中仍然会残留一些杂质和固体颗粒,需要经过沉淀和分离的过程。
这一步通常是通过静置或者离心的方法将油中的杂质和固体分离出来,得到纯净的花生油。
传统的压榨工艺在保留花生油的营养成分和天然香味方面具有
优势,但也存在生产效率低、生产成本高的缺点。
随着科技的发展,现代化的花生油生产工艺逐渐取代了传统的压榨工艺,采用更高效
的机械设备和工艺流程,但一些传统压榨工艺仍然在一些地方得到
应用,因为它们能够生产出口感和香味更加纯正的花生油。
花生油制取技术

花生油制取技术
花生油制取技术是指将花生经过一系列加工工艺,从中提取出花生油的过程。
其主要包括以下几个步骤:
1. 处理原料。
首先需要将采摘来的花生去壳、去杂质,然后进行清洗、烘干等处理,以保证提取的花生油质量。
2. 破碎。
将处理好的花生用破碎机破碎成小颗粒,方便后续的压榨。
3. 压榨。
将破碎后的花生颗粒放入压榨机中,加热、压榨,使花生油从花生中被挤出。
4. 沉淀和过滤。
将挤出的花生油放置一段时间,让沉淀物沉淀到底部,然后将上层的花生油抽离并进行过滤,以去除其中的杂质和残留物。
5. 精炼。
为了提高花生油的质量,还需要进行精炼处理。
主要包括脱酸、脱臭、漂白等步骤,使花生油的质量更加纯净。
以上就是花生油制取技术的主要步骤。
随着技术不断发展,现在还出现了一些新的提取方式,如超临界流体萃取、微波辅助萃取等,这些新技术不仅可以提高花生油的提取效率,而且还可以减少对环境的影响,具有广阔的应用前景。
- 1 -。
花生油的压榨工艺

花生油的压榨工艺
花生油的压榨工艺是指将花生经过一系列的加工处理,从而提取出花生油的过程。
下面是一般的花生油压榨工艺流程:
1. 清洗:将采摘回来的花生进行清洗,去除杂质和表面的脏物。
2. 烘干:清洗后的花生需要进行烘干,以去除花生表面的水分。
3. 筛选:经过烘干后的花生需要进行筛选,去除破碎、变质和不合格的花生。
4. 烘炒:将筛选好的花生进行烘炒,烘炒的目的是提高花生的含油率。
5. 压榨:烘炒后的花生经过压榨机械压榨,将花生油从花生中提取出来。
压榨的时候需要控制好温度和榨压的压力,以保证花生油的质量和产量。
6. 沉淀:压榨得到的花生油需要经过一段时间的静置,使得杂质和沉淀物沉淀到底部。
7. 过滤:静置后的花生油需要进行过滤,去除沉淀物和杂质,以获得纯净的花生油。
8. 脱臭和脱色:过滤后的花生油可能还存在一些异味和颜色不纯的问题,因此
需要进行脱臭和脱色处理,使得花生油具有良好的口感和外观。
9. 包装:经过脱臭和脱色处理后的花生油需要进行包装和细分,然后进行质量检测,最后出厂销售。
需要注意的是,不同的压榨工艺会有所差异,具体的工艺流程也可能会因所处的地区和工艺技术的不同而有所变化。
以上是一般的花生油压榨工艺流程,仅供参考。
花生榨油工艺流程
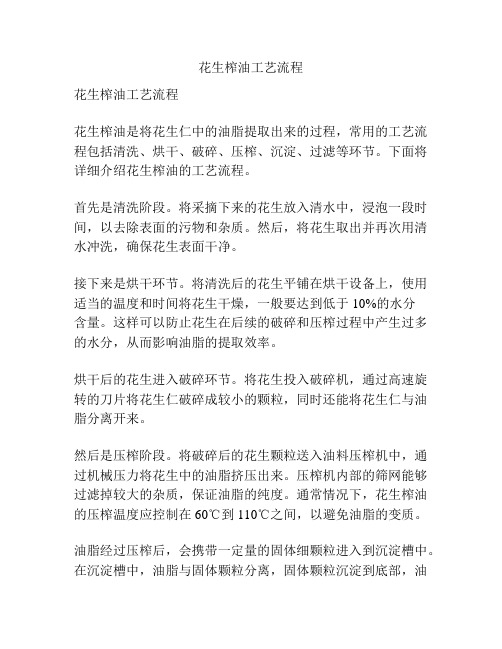
花生榨油工艺流程花生榨油工艺流程花生榨油是将花生仁中的油脂提取出来的过程,常用的工艺流程包括清洗、烘干、破碎、压榨、沉淀、过滤等环节。
下面将详细介绍花生榨油的工艺流程。
首先是清洗阶段。
将采摘下来的花生放入清水中,浸泡一段时间,以去除表面的污物和杂质。
然后,将花生取出并再次用清水冲洗,确保花生表面干净。
接下来是烘干环节。
将清洗后的花生平铺在烘干设备上,使用适当的温度和时间将花生干燥,一般要达到低于10%的水分含量。
这样可以防止花生在后续的破碎和压榨过程中产生过多的水分,从而影响油脂的提取效率。
烘干后的花生进入破碎环节。
将花生投入破碎机,通过高速旋转的刀片将花生仁破碎成较小的颗粒,同时还能将花生仁与油脂分离开来。
然后是压榨阶段。
将破碎后的花生颗粒送入油料压榨机中,通过机械压力将花生中的油脂挤压出来。
压榨机内部的筛网能够过滤掉较大的杂质,保证油脂的纯度。
通常情况下,花生榨油的压榨温度应控制在60℃到110℃之间,以避免油脂的变质。
油脂经过压榨后,会携带一定量的固体细颗粒进入到沉淀槽中。
在沉淀槽中,油脂与固体颗粒分离,固体颗粒沉淀到底部,油脂则自上而下流出。
沉淀槽的设计合理与否直接影响着油脂的质量与产量。
最后是过滤环节。
将由沉淀槽流出的油脂经过滤网过滤,去除残留的固体颗粒,使油脂更加纯净。
同时,还可对油脂进行进一步的澄清处理,提高油脂的质量。
通过以上工艺流程,即可得到高质量的花生油。
在实际生产中,还可以根据需要进行其他工艺的调整和改进,如调节压榨温度、增加油脂的萃取时间等,以提高油脂的产量和质量。
总之,花生榨油的工艺流程包括清洗、烘干、破碎、压榨、沉淀、过滤等环节。
这些工序的合理安排和操作技术的熟练掌握,能够提高花生油的产量和质量,满足市场需求。
花生油精炼方法与步骤

花生油精炼方法与步骤
花生油的精炼过程主要包括去除杂质、脱色、去味、脱臭等步骤,以下是一般的花生油精炼方法和步骤:
1.去除杂质:
目的:去除花生油中的杂质,如悬浮物、机械杂质等。
步骤:将原始的花生油通过沉淀、过滤等方式,去除其中的大颗粒和悬浮物。
2.脱色:
目的:去除花生油中的色素,提高油的透明度。
步骤:通常采用活性炭吸附的方法。
将活性炭与花生油混合,通过物理吸附将油中的色素吸附去除,然后通过过滤将活性炭分离。
3.去味:
目的:去除花生油中的异味,提高油的口感。
步骤:通过蒸馏或其他方法,将花生油中的异味成分去除。
这一步骤可以通过高温蒸馏或使用脱臭设备完成。
4.脱臭:
目的:进一步去除花生油中的异味。
步骤:通过蒸馏等方法,将油中的异味成分挥发掉。
这一步骤通常使用高温蒸馏和真空脱臭。
5.冷却和包装:
目的:冷却油品并进行最终包装。
步骤:将经过精炼的花生油进行冷却,并进行最终包装,以确保油品的新鲜度和稳定性。
注意事项:
精炼过程中要确保设备的卫生和清洁,以避免次生污染。
控制精炼过程中的温度、时间和其他工艺参数,以保证油品的品质。
使用高质量的脱色剂、去味剂和脱臭剂,以确保油品的色泽、口感和气味。
这些步骤构成了一般的花生油精炼过程,实际操作时可能还会根据具体情况进行一些微调。
土法花生油生产工艺
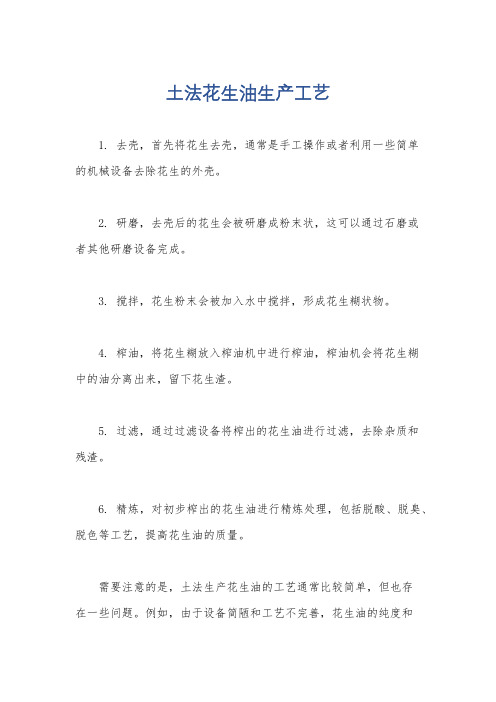
土法花生油生产工艺
1. 去壳,首先将花生去壳,通常是手工操作或者利用一些简单
的机械设备去除花生的外壳。
2. 研磨,去壳后的花生会被研磨成粉末状,这可以通过石磨或
者其他研磨设备完成。
3. 搅拌,花生粉末会被加入水中搅拌,形成花生糊状物。
4. 榨油,将花生糊放入榨油机中进行榨油,榨油机会将花生糊
中的油分离出来,留下花生渣。
5. 过滤,通过过滤设备将榨出的花生油进行过滤,去除杂质和
残渣。
6. 精炼,对初步榨出的花生油进行精炼处理,包括脱酸、脱臭、脱色等工艺,提高花生油的质量。
需要注意的是,土法生产花生油的工艺通常比较简单,但也存
在一些问题。
例如,由于设备简陋和工艺不完善,花生油的纯度和
质量可能无法得到有效保障;同时,土法生产工艺对环境的影响也可能比较大。
因此,在实际生产中,需要注意加强卫生管理、提高生产工艺的科学性,以及合理利用资源,减少对环境的影响。
优质花生油执行标准
优质花生油执行标准优质花生油执行标准通常包括以下几个方面:一、生产工艺标准优质花生油的生产工艺一般采用物理压榨法或浸出法。
物理压榨法是利用机械外力将花生仁挤压出油,具有保留花生原有营养和风味的特点。
浸出法则是利用有机溶剂将花生中的油脂溶解出来,再经过处理达到一定质量标准。
二、原辅料要求优质花生油的生产必须使用符合要求的花生原料,并且对辅料如水、食品添加剂等也有严格的规定。
一般来说,优质花生油的生产会选择新鲜、无霉变的花生仁为原料,并使用符合饮用水标准的水进行生产。
三、质量标准优质花生油的质量标准包括色泽、气味、口感、水分及挥发物、不溶性杂质、酸价、过氧化值、黄曲霉素等指标。
其中,色泽是判断油脂质量的重要指标,优质花生油应呈淡黄色或澄黄色;气味和口感则关系到产品的风味和口感,优质花生油应具有浓郁的花生香味和良好的口感;水分及挥发物、不溶性杂质等指标则关系到产品的纯净度和安全性,优质花生油中应含有较少的水分和挥发物等杂质;酸价和过氧化值则反映了油脂的新鲜度和氧化程度,优质花生油的酸价和过氧化值应符合国家标准;黄曲霉素是一种致癌物质,优质花生油的黄曲霉素含量应符合国家标准。
四、安全标准优质花生油的安全标准应符合国家相关规定,包括农药残留、重金属含量、添加剂使用等方面。
在生产过程中,要保证生产场所的卫生和安全,严格控制添加剂的使用量和使用范围,以确保产品的安全性和健康性。
五、包装标准优质花生油的包装标准包括包装材料、包装设计、标识等方面。
包装材料应符合食品包装材料的相关规定,并具有良好的密封性能和防潮性能;包装设计应美观大方,符合产品的特点和品牌形象;标识应清晰、易读、规范,包括产品名称、生产日期、保质期、厂家信息等内容。
综上所述,优质花生油执行标准包括生产工艺标准、原辅料要求、质量标准、安全标准和包装标准等方面。
这些标准的严格遵守和执行,能够保证产品的质量和安全,提高消费者的满意度和信任度。
同时,对于生产厂家来说,要不断加强技术研发和品质管理,提高产品的质量和附加值,才能在激烈的市场竞争中获得更大的发展空间。
花生油工艺流程
花生油工艺流程1 浓香花生油的预榨生产工艺流程油料-- 清理-- 分级-- 烘干/ 冷却-- 小路25%~30%热风烘炒-- 吸风降温-- 轧糁破碎/ 脱皮--大路75%~70%轧坯-- 蒸炒--压榨2 工艺说明2.1 清理:破壳-去壳-筛选-去石-磁选2.2 分级:用分级筛分离出花生中的未成熟粒、霉变粒、破碎粒等不完善粒,这部分可用于生产二级油,单独销售。
2.3 烘干/冷却:烘干设务可用热风气流干燥机。
花生烘干后水分控制在5%~6%。
然后迅速用冷空气把油粒温度降至40℃以下。
2.4 破碎/脱皮:破碎机可用齿辊式破碎机,目的是把红外衣扒掉,破碎后用风力风选器或吸风平筛将红外衣吸出,分离出的花生红皮可用作医药化工原料。
2.5 热风烘炒:将总量25%~30%的花生瓣送至热风烘炒炉,在此烘炒炉内油料被加热到180℃~200℃。
烘炒温度是浓香花生油产生香味的关键因素,温度太低,香味较淡;温度太高,油料易糊化。
2.6 降温与轧糁:为防止油料糊化和自燃,烘炒后应迅速散热降温,降温后用齿辊式破碎机轧成碎粒状。
2.7 蒸炒:立式蒸炒锅对生坯进行蒸炒。
1层~2 层装料要满,起到蒸的作用;3层~5 层装料要浅,起到排除水分的作用;出料温度108℃~112℃,水分5%~7%,为保证花生油有浓郁的香味,蒸炒锅炉的间接蒸汽压力应不小于0.6mpa。
2.8 榨油:考虑到浓香花生油生产工艺的特殊性,对榨油机主轴转速作了适当调整,主轴转速由原来的8rpm提高到10rpm,并适当放厚饼的厚度。
入榨温度135℃,入榨水分1.5%~2%,机榨饼残油9%~10%。
所得毛油经沉淀后用立式叶片过滤机过滤后送到精炼车间,机榨饼经破碎后送至浸出车间进行二次浸出。
浸出毛油经精炼后作普通油单独销售。
3 毛油精炼工序工艺流程过滤毛油-- 降温-- 加助滤剂-- 二次降温-- 沉淀48h-- 过滤-- 成品油-- 滤饼4 工艺说明4.1 一次降温:从机榨车间送来的过滤毛油温度一般在60℃~70℃,为节约能源,先用自来水(冷却水)于低速搅拌下(30rpm)散热冷却,温度降至接近室温为止。
生榨花生油的制作工艺
生榨花生油的制作工艺
生榨花生油是通过压榨花生仁制成的天然、无污染的植物油,其制作工艺可以分为以下几个步骤:
1. 花生筛选:将生产过程中的花生仁进行筛选,去除杂质和不符合要求的花生仁,保证加工质量。
2. 归并花生仁:将经过筛选的花生仁归并到一起,切成适当大小的小块,便于后续的压榨。
3. 清洗花生仁:将切好的花生仁用清水冲洗,去除表面的污垢和杂质。
4. 烘干花生仁:将清洗后的花生仁晾晒或烤干,保证花生仁的干燥程度,以便后续的压榨。
5. 压榨花生油:将干燥的花生仁放入压榨机中进行压榨,从中提取出花生油和剩余的花生渣,花生油通过过滤后即可获得。
6. 过滤花生油:将提取出的花生油通过滤纸等物质进行过滤,去除不纯物质,以便保存和食用。
7. 装瓶包装:将过滤好的花生油装入适当的瓶中,进行密封、贴标签等包装处
理,方便销售和使用。
以上就是生榨花生油的制作工艺,其制作过程简单,既保留了花生的营养成分又没有添加任何化学物质,是一种非常健康的天然植物油。
纯正花生油的产品标准号
纯正花生油的产品标准号
1. 生产工艺
纯正花生油的生产工艺主要是采用物理压榨法。
这种生产方法不涉及任何化学处理或添加,能够最大限度地保留花生原有的营养成分和天然风味。
2. 原料
纯正花生油的原料是优质花生,通常选用新鲜、无污染、非转基因的种子或果实。
3. 质量等级
纯正花生油通常被划分为一级和二级两个质量等级。
一级花生油色泽浅,气味香,滋味浓郁;二级花生油色泽稍深,气味和滋味可能稍逊于一级。
4. 品牌
纯正花生油的知名品牌有金龙鱼、福临门、鲁花等。
不同品牌的产品在质量和风味上可能略有差异,但总体来说,都符合相关的产品标准。
5. 出品商
纯正花生油的出品商应具有相应的生产资质和认证,如质量管理体系认证和食品安全管理体系认证等。
出品商应能提供产品质量检测报告和食品生产许可证等相关文件。
6. 包装规格
纯正花生油的包装规格多样,以满足不同消费者的需求。
一般来
说,包装规格常见的有5L、10L、18.9L等。
同时,包装材料应符合食品安全标准,具有良好的密封性能和抗氧化性能。
7. 执行标准
纯正花生油应符合国家相关标准,如《花生油》。
在产品标签上应标明执行标准号,以供消费者辨识产品质量。
8. 食品生产许可证编号
纯正花生油的生产企业需获得食品生产许可证,并在产品标签上注明许可证编号。
消费者可通过查询该编号了解企业的资质和产品的合法性。
- 1、下载文档前请自行甄别文档内容的完整性,平台不提供额外的编辑、内容补充、找答案等附加服务。
- 2、"仅部分预览"的文档,不可在线预览部分如存在完整性等问题,可反馈申请退款(可完整预览的文档不适用该条件!)。
- 3、如文档侵犯您的权益,请联系客服反馈,我们会尽快为您处理(人工客服工作时间:9:00-18:30)。
浓香花生油生产工艺简介
花生是高含油油料,目前尚不能采用一次浸出工艺。
浓香花生油风味独特,营养价值高,深受广大消费者的青睐。
中华人民共和国国家标准(GB8615-88)对浓香花生油的质量标准作了详细规定,本文就浓香花生油的生产工艺技术作一介绍。
1浓香花生油的生产工艺流程(预榨部分)
花生是高含油油料,目前尚不能采用一次浸出工艺。
浓香花生油风味独特,营养价值高,深受广大消费者的青睐。
中华人民共和国国家标准(GB8615-88)对浓香花生油的质量标准作了详细规定,本文就浓香花生油的生产工艺技术作一介绍。
1浓香花生油的生产工艺流程(预榨部分)
油料--清理--分级--烘干/冷却--小路25%~30%热风烘炒--吸风降温--轧糁破碎/脱皮--大路75%~70%轧坯--蒸炒--------
2 工艺说明
2.1 清理:与普通二级油所用设备相同
2.2 分级:用分级筛分离出花生中的未成熟粒、霉变粒、破碎粒等不完善粒,这部分可用于生产二级油,单独销售。
2.3 烘干/冷却:烘干设务可用热风气流干燥机。
花生烘干后水分控制在5%~6%。
然后迅速用冷空气把油粒温度降至40℃以下。
2.4 破碎/脱皮:破碎机可用齿辊式破碎机,目的是把红外衣扒掉,破碎后用风力风选器或吸风平筛将红外衣吸出,分离出的花生红皮可用作医药化工原料。
2.5 热风烘炒:将总量25%~30%的花生瓣送至燃煤热风烘炒炉,在此烘炒炉内油料被加热到180℃~200℃。
烘炒温度是浓香花生油产生香味的关键因素,温度太低,香味较淡;温度太高,油料易湖化。
2.6 降温与轧糁:为防止油料糊化和自燃,烘炒后应迅速散热降温,降温后用齿辊式破碎机轧成碎粒状。
2.7 蒸炒:"用五层立式蒸炒锅对生坯进行蒸炒。
1层~2层装料要满,起到蒸的作用;3层~5层装料要浅,起到排除水分的作用;出料温度108℃~112℃,水分5%~7%,为保证花生油有浓郁的香味,蒸炒锅炉的间接蒸汽压力应不小于0.6mpa。
2.8 榨油:本工艺使用的是200型螺旋榨油机,考虑到浓香花生油生产工艺的特殊性,对榨油机主轴转速作了适当调整,主轴转速由原来的8rpm提高到10rpm,并适当放厚饼的厚度,一般控制在10mm左右。
入榨温度135℃,入榨水分1.5%~2%,机榨饼残油9%~10%。
所得毛油经沉淀后用立式叶片过滤机过滤后送到精炼车间,机榨饼经破碎后送至浸出车间进行二次浸出。
浸出毛油经精炼后作普通油单独销售。
3 毛油精炼工序工艺流程
过滤毛油--一次降温--加助滤剂--二次降温--沉淀48h--过滤--成品油--滤饼
4 工艺说明
4.1 一次降温:从机榨车间送来的过滤毛油温度一般在60℃~70℃,为节约能源,先用自来水(冷却水)于低速搅拌下(30rpm)散热冷却,温度降至接近室温为止。
4.2 加助滤剂:加助滤剂的目的是提高最后过滤效果,加速滤饼的形成,降低成品油中磷脂、胶溶性杂质的含量;助滤剂和种类有活性炭和固体花生饼粉末;加入量为油重的0.1%左右。
4.3 二次降温:用冷冻盐水于低速搅拌下将花生油冷却到10℃~15℃,然后保温沉淀静置48h。
4.4 过滤:将沉淀48h后的毛油泵入板框压滤机进行过滤。
在滤饼形成前得到的过滤油较浑浊,应在滤饼形成后重新过滤,过滤后得到的成品油即可进行包装。
4.5 滤饼的处理:机榨车间得到的滤饼可回榨;精炼车间得到的滤饼可掺加到粕中。
5 影响浓香花生油香味的因素分析
影响农香花生油香味的因素主要有以下几个方面:
5.1 花生原料自身的影响
生产浓香花生油的油料要求籽粒饱满,未经过陈化期。
未成熟粒、破损粒、霉变粒和陈化变粒不能用于生产浓香花生油。
未成熟粒和陈化粒所产油脂酸价较高,风味较差,而霉变粒和破损粒又容易受到黄曲霉毒素的污染。
因此在生产过程中,必须将这些油料分离出来用于单独加工普通二级油。
5.2 大小路比例的影响
生坯料(大路)与热风烘炒料(小路)一般按3:1掌握。
烘炒料比例太小,花生油香味较淡;比例太大,榨油时饼难以成型,出油率降低,毛油浑浊,给后道工序的处理增加困难。
5.3 烘炒温度的影响
热风烘炒是生产浓香花生油的关键工序,花生油香味的产生与烘炒温度有直接关系。
温
度太低,香味较淡;温度太高,油料易焦糊。
一般控制烘炒温度180℃~200℃。
为防止油料湖化和自燃,烘炒后应立即散热降温。
5.4 蒸炒环节的影响
对生坯进行蒸炒是生产浓香花生油的又一重要环节。
浓香花生油出油率的高低、香味与色泽、磷脂与胶溶性成分的含量都与蒸炒有直接的关系。
要采用高水分蒸坯技术,在蒸炒锅内将油料水分调节到12%~13%;在设备耐压许可的情况下,尽量提高间接水蒸汽的压力,一般控制在0.6MPa~MPa;有条件的企业,最好使用过热水蒸汽。
在蒸炒过程中,要使磷脂及胶溶性物质充分吸水凝聚与蛋白质结合,这是保证成品油280℃加热试验合格和提高成品油透明度的关键所在。
6 生产浓香花生油应注意的几人问题
浓香花生油独特的香味与它独特的生产工艺有很在关系。
为保持其天然的色、香、味,对浓香化生油一般不进行水化、碱炼、脱色和脱臭处理。
对花生原料也十分考察,必须选用新鲜的、籽粒饱满的优质花生仁。
未成熟粒,破损粒、霉变粒、陈化粒绝对不能用于生产农香花生油。
为确保浓香花油的质量符合GB8615-88的要求,还应注意以下几个问题:
6.1 浓香花生油的酸价问题
GB8615-88对浓香花生油的酸值作了明确规定,要求酸值≤1.0mgKOH/g,因浓香花生油不能碱炼和蒸馏,必须寻找降低酸值的新途径。
具体做法是:采用特殊的加工工艺,先做空白试验,即在蒸炒前加入预定的水,若制取的浓香花生油酸值≤1.0,则在蒸炒前把水改成相同量的碱液。
加入一定量浓度的碱液,它是利用一定量的浓度碱液与料坯中游离脂肪酸起中和反应,起到降低浓香花生油中酸值的目的。
碱液浓度和加入量应视花生仁中的油的酸值高低而定。
6.2 农香花生油的280℃加热试验问题
GB615-88对浓香花生油的280℃加热试验作了明确规定,要求280℃加热试验油色不得变深,无析出物。
解决这一技术问题的关键是采用高水分蒸坯工艺,合理控制冷冻温度,沉淀时间和助滤剂的使用。
6.3生产应在密闭,避光的条件下进行,并尽量减少金属离子的侵染。
6.4下脚料,焦湖粒,过夜料不能用于生产浓香花生油。
6.5生产设备长期闲置后开机以及大修过后开机的头几个班次所产花生油应作普通花生油处理。