热流道浇注系统
简介
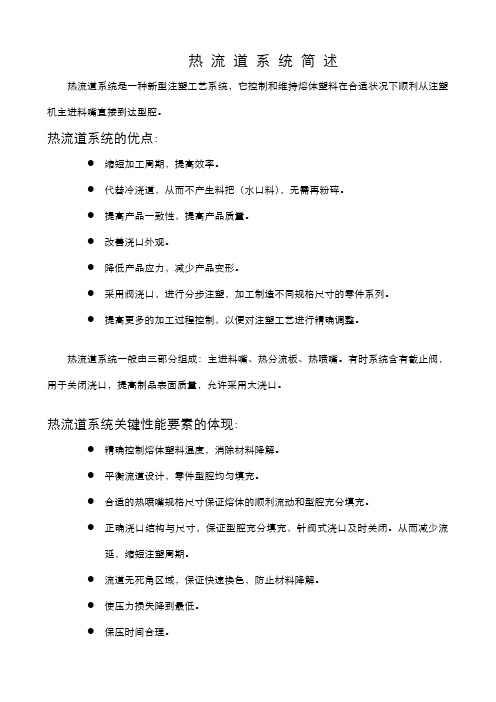
热流道系统简述
热流道系统是一种新型注塑工艺系统,它控制和维持熔体塑料在合适状况下顺利从注塑机主进料嘴直接到达型腔。
热流道系统的优点:
●缩短加工周期,提高效率。
●代替冷浇道,从而不产生料把(水口料),无需再粉碎。
●提高产品一致性,提高产品质量。
●改善浇口外观。
●降低产品应力,减少产品变形。
●采用阀浇口,进行分步注塑,加工制造不同规格尺寸的零件系列。
●提高更多的加工过程控制,以便对注塑工艺进行精确调整。
热流道系统一般由三部分组成:主进料嘴、热分流板、热喷嘴。
有时系统含有截止阀,用于关闭浇口,提高制品表面质量,允许采用大浇口。
热流道系统关键性能要素的体现:
●精确控制熔体塑料温度,消除材料降解。
●平衡流道设计,零件型腔均匀填充。
●合适的热喷嘴规格尺寸保证熔体的顺利流动和型腔充分填充。
●正确浇口结构与尺寸,保证型腔充分填充,针阀式浇口及时关闭。
从而减少流
延,缩短注塑周期。
●流道无死角区域,保证快速换色,防止材料降解。
●使压力损失降到最低。
●保压时间合理。
热流道系统浇口结构特点及应用
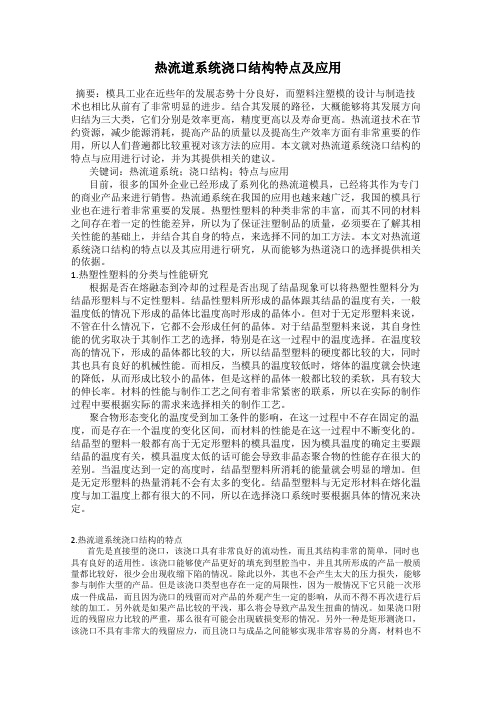
热流道系统浇口结构特点及应用摘要:模具工业在近些年的发展态势十分良好,而塑料注塑模的设计与制造技术也相比从前有了非常明显的进步。
结合其发展的路径,大概能够将其发展方向归结为三大类,它们分别是效率更高,精度更高以及寿命更高。
热流道技术在节约资源,减少能源消耗,提高产品的质量以及提高生产效率方面有非常重要的作用,所以人们普遍都比较重视对该方法的应用。
本文就对热流道系统浇口结构的特点与应用进行讨论,并为其提供相关的建议。
关键词:热流道系统;浇口结构;特点与应用目前,很多的国外企业已经形成了系列化的热流道模具,已经将其作为专门的商业产品来进行销售。
热流通系统在我国的应用也越来越广泛,我国的模具行业也在进行着非常重要的发展。
热塑性塑料的种类非常的丰富,而其不同的材料之间存在着一定的性能差异,所以为了保证注塑制品的质量,必须要在了解其相关性能的基础上,并结合其自身的特点,来选择不同的加工方法。
本文对热流道系统浇口结构的特点以及其应用进行研究,从而能够为热道浇口的选择提供相关的依据。
1.热塑性塑料的分类与性能研究根据是否在熔融态到冷却的过程是否出现了结晶现象可以将热塑性塑料分为结晶形塑料与不定性塑料。
结晶性塑料所形成的晶体跟其结晶的温度有关,一般温度低的情况下形成的晶体比温度高时形成的晶体小。
但对于无定形塑料来说,不管在什么情况下,它都不会形成任何的晶体。
对于结晶型塑料来说,其自身性能的优劣取决于其制作工艺的选择,特别是在这一过程中的温度选择。
在温度较高的情况下,形成的晶体都比较的大,所以结晶型塑料的硬度都比较的大,同时其也具有良好的机械性能。
而相反,当模具的温度较低时,熔体的温度就会快速的降低,从而形成比较小的晶体,但是这样的晶体一般都比较的柔软,具有较大的伸长率。
材料的性能与制作工艺之间有着非常紧密的联系,所以在实际的制作过程中要根据实际的需求来选择相关的制作工艺。
聚合物形态变化的温度受到加工条件的影响,在这一过程中不存在固定的温度,而是存在一个温度的变化区间,而材料的性能是在这一过程中不断变化的。
第三节浇注系统资料
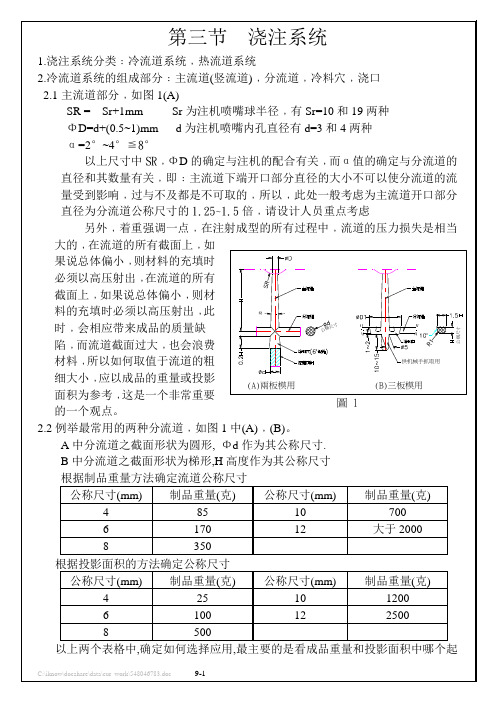
热流道系统虽然已早有运用,但设计人员在根本上对其优点的了解却远远没有跟上,下面.举例说明:
本案例为卫星接收器之面盖,使用塑料为ABS,产品主要构成是一种普普通通的壳形面盖,标准肉厚为2.5mm,外形尺寸为432*60*23.而在成品的中央外有按键存在.为保持按键的弹性,将按键的根部边接肉厚设成0.8mm,肉厚变化较大,成品的重量126克,生产量也高.
7.2.2分流板中的加热电热管应尽量设计成直管式,不可避免时,才做弯管式,因为弯管式本身的购买费用较高,而且是被安装在分流板上,下两表面,必须成双购入,不合算.
7.2.3分流板中,其头部的塑胶密封性让人注重.如何保障好这一占,见图9中Detail部分,因为分流板的端头一般是日后无须拆下,所以,在起初加工时,可以将该出口彻底烧焊塞死.
7.4垫块:
分流板在成型时都被高温加热,且内部有相当高的注射压力,这些种种的因素都会导致热流板的变形,而克服这些变形的元件就是支撑热垫块支撑垫块不但布置在中心灌嘴及热嘴的对面,更应有更大面积的垫块支撑在螺钉底部,尽可能均匀页大面积地布置支撑垫块,防止分流板变形,同时,也可以防止母模本体板底部的变形,使成型的靠插破不充分.
以上尺寸中SR﹐ΦD的确定与注机的配合有关﹐而α值的确定与分流道的直径和其数量有关﹐即﹕主流道下端开口部分直径的大小不可以使分流道的流量受到影响﹐过与不及都是不可取的﹐所以﹐此处一般考虑为主流道开口部分直径为分流道公称尺寸的1.25~1.5倍﹐请设计人员重点考虑
另外﹐着重强调一点﹐在注射成型的所有过程中﹐流道的压力损失是相当大的﹐在流道的所有截面上﹐如果说总体偏小﹐则材料的充填时必须以高压射出﹐在流道的所有截面上﹐如果说总体偏小﹐则材料的充填时必须以高压射出﹐此时﹐会相应带来成品的质量缺陷﹐而流道截面过大﹐也会浪费材料﹐所以如何取值于流道的粗细大小﹐应以成品的重量或投影面积为参考﹐这是一个非常重要的一个观点。
热流道系统介绍
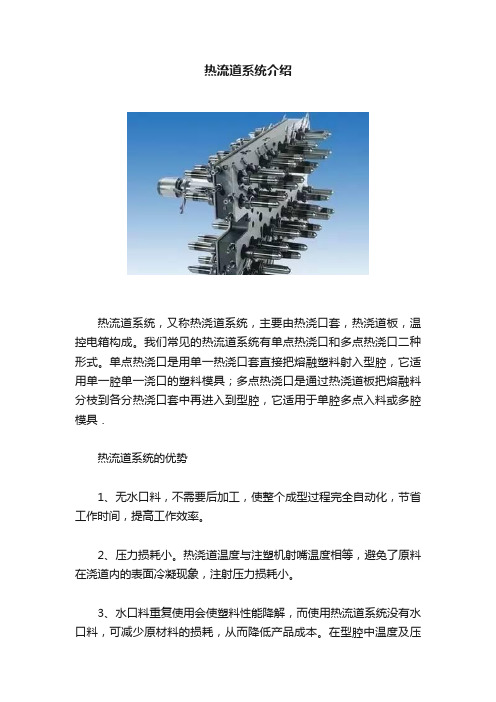
热流道系统介绍热流道系统,又称热浇道系统,主要由热浇口套,热浇道板,温控电箱构成。
我们常见的热流道系统有单点热浇口和多点热浇口二种形式。
单点热浇口是用单一热浇口套直接把熔融塑料射入型腔,它适用单一腔单一浇口的塑料模具;多点热浇口是通过热浇道板把熔融料分枝到各分热浇口套中再进入到型腔,它适用于单腔多点入料或多腔模具.热流道系统的优势1、无水口料,不需要后加工,使整个成型过程完全自动化,节省工作时间,提高工作效率。
2、压力损耗小。
热浇道温度与注塑机射嘴温度相等,避免了原料在浇道内的表面冷凝现象,注射压力损耗小。
3、水口料重复使用会使塑料性能降解,而使用热流道系统没有水口料,可减少原材料的损耗,从而降低产品成本。
在型腔中温度及压力均匀,塑件应力小,密度均匀,在较小的注射压力下,较短的成型时间内,注塑出比一般的注塑系统更好的产品。
对于透明件、薄件、大型塑件或高要求塑件更能显示其优势,而且能用较小机型生产出较大产品。
4、热喷嘴采用标准化、系列化设计,配有各种可供选择的喷嘴头,互换性好。
独特设计加工的电加热圈,可达到加热温度均匀,使用寿命长。
热流道系统配备热流道板、温控器等,设计精巧,种类多样,使用方便,质量稳定可靠。
热流道系统应用的不足之处1、整体模具闭合高度加大,因加装热浇道板等,模具整体高度有所增加。
2、热辐射难以控制,热浇道最大的毛病就是浇道的热量损耗,是一个需要解决的重大课题。
3、存在热膨胀,热胀冷缩是我们设计时要考虑的问题。
4、模具制造成本增加,热浇道系统标准配件价格较高,影响热浇道模具的普及。
热流道模具的优点热流道模具在当今世界各工业发达国家和地区均得到极为广泛的应用。
这主要因为热流道模具拥有如下显着特点:1、缩短制件成型周期因没有浇道系统冷却时间的限制,制件成型固化后便可及时顶出。
许多用热流道模具生产的薄壁零件成型周期可在5秒钟以下在纯热流道模具中因没有冷浇道,所以无生产废料。
这对于塑料价格贵的应用项目意义尤其重大。
高速注射成型的热流道系统(热恒热流道)
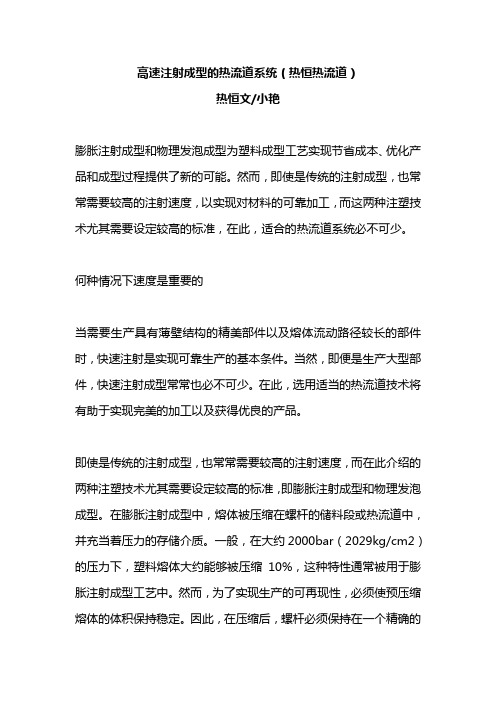
高速注射成型的热流道系统(热恒热流道)热恒文/小艳膨胀注射成型和物理发泡成型为塑料成型工艺实现节省成本、优化产品和成型过程提供了新的可能。
然而,即使是传统的注射成型,也常常需要较高的注射速度,以实现对材料的可靠加工,而这两种注塑技术尤其需要设定较高的标准,在此,适合的热流道系统必不可少。
何种情况下速度是重要的当需要生产具有薄壁结构的精美部件以及熔体流动路径较长的部件时,快速注射是实现可靠生产的基本条件。
当然,即便是生产大型部件,快速注射成型常常也必不可少。
在此,选用适当的热流道技术将有助于实现完美的加工以及获得优良的产品。
即使是传统的注射成型,也常常需要较高的注射速度,而在此介绍的两种注塑技术尤其需要设定较高的标准,即膨胀注射成型和物理发泡成型。
在膨胀注射成型中,熔体被压缩在螺杆的储料段或热流道中,并充当着压力的存储介质。
一般,在大约2000bar(2029kg/cm2)的压力下,塑料熔体大约能够被压缩10%,这种特性通常被用于膨胀注射成型工艺中。
然而,为了实现生产的可再现性,必须使预压缩熔体的体积保持稳定。
因此,在压缩后,螺杆必须保持在一个精确的位置上。
当阀式浇口喷嘴打开、大量的熔体流入到模具中时,它会承受较高的压力。
只有电机驱动的注塑机可以满足这一条件,它允许在系统界限范围内做出选择性的轴向定位,即使是在高压下也可保持该位置的稳定不变。
如果在膨胀注射成型中使用了热流道系统,那么高达2500bar(2536kg/cm2)的压力就会积聚在热流道系统中,并在定义的时间内保持不变,从而确保了所有的型腔均可获得均衡的压力。
为了成功地实现膨胀注射成型,必须确保所有的针阀能够同时平稳地开启。
一旦针阀打开,被预压在热流道中的熔体就会爆发式地膨胀,并均匀地填满型腔,从而允许非常薄的部件充满成型。
就物理发泡成型如MuCell工艺而言,需要向系统中加入物理发泡剂,该发泡剂首先是在压力的作用下溶解于塑料熔体中。
当熔体注入型腔时,压力降低,发泡剂膨胀,从而使熔体发泡。
热流道浇注系统

热流道浇注系统(hot-runner/runnerless mold)–指在浇注系统中无流道凝料–为此需要在注射模中采用绝热或加热的方法,使从注射机喷嘴到型腔入口这一段流道中的塑料一直保持熔融状态,从而在开模时只需取出塑件,而不必清理浇道凝料。
l热流道技术是应用于塑料注射模浇注流道系统的一种先进技术,是塑料注塑成型工艺发展的一个热点方向。
l它于20世纪50年代问世,经历了一段较长时间地推广以后,其市场占有率逐年上升。
l80年代中期,美国的热流道模具占注射模具总数的15%~17% ,欧洲为12%~15% ,日本约为10% 。
l但到了90年代,美国生产的塑料注射模具中热流道模具已占40%以上,在大型制品,特别是在成型盖罩、容器和外壳等类制品的生产中,注射模具占90%以上,采用热流道的达到80%。
日本的热流道模具也在逐渐普及中。
l目前,热流道加热装置在西方先进工业国已达到作为标准件出售的程度。
l现在我国热流道成型技术推广应用的程度越来越高,是今后注射模具浇注系统的一个重要发展方向。
1.热流道成型的优点①基本可实现无废料加工,节约原料;②省去除料把、修整塑件、破碎回收料等工序,因而节省人力,简化设备,缩短成型周期,提高了生产率,降低成本;③对针点浇口模具,可以避免采用三板式模具,避免采用顺序分型脱模机构,操作简化,有利于实现生产过程自动化。
④由于浇注系统的熔料在生产过程中始终处于熔融状态,浇注系统畅通,压力损失小,可以实现多点浇口、一模多腔和大型模具的低压注塑;还有利于压力传递,从而克服因补缩不足所导致的制作缩孔、凹陷等缺陷,改善应力集中产生的翘曲变形,提高了塑件质量;⑤由于没有浇注系统的凝料,而缩短了模具的开模行程,提高了设备对深腔塑件的适应能力。
2.热流道成型的缺点①模具的设计和维护较难,若没有高水平的模具和维护管理,生产中模具易产生各种故障;②成型准备时间长,模具费用高,小批量生产时效果不大;③对制件形状和使用的塑料有原则;④对于多型腔模具,采用热流道成型技术难度较高。
6.3_热流道浇注系统
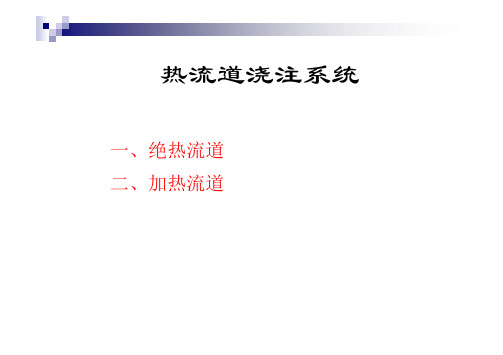
热流道浇注系统一、绝热流道二、加热流道热流道是指在浇注系统中无流道凝料,为此需要在注射模中采用绝热或加热的方法,使从注射机喷嘴到型腔入口这一段流道中的塑料一直保持熔融状态,从而在开模时只需取出塑件,而不必清理浇道凝料。
热流道技术是应用于塑料注塑模浇注流道系统的一种先进技术,是塑料注塑成型工艺发展的一个热点方向。
它于20世纪50年代问世,经历了一段较长时间地推广以后,其市场占有率逐年上升。
80年代中期,美国的热流道模具占注射模具总数的15%~17% ,欧洲为12%~15% ,日本约为10% 。
但到了90年代,美国生产的塑料注射模具中热流道模具已占40%以上,在大型制品,特别是在成型盖罩、容器和外壳等类制品的生产中,注射模具占90%以上,采用热流道的达到80%。
日本的热流道模具也在逐渐普及中。
目前,热流道加热装置在西方先进工业国已达到作为标准件出售的程度。
现在我国热流道成型技术推广应用的程度越来越高,是今后注射模具浇注系统的一个重要发展方向1.热流道成型的优点①基本可实现无废料加工,节约原料;②省去除料把、修整塑件、破碎回收料等工序,因而节省人力,简化设备,缩短成型周期,提高了生产率,降低成本;③对针点浇口模具,可以避免采用三板式模具,避免采用顺序分型脱模机构,操作简化,有利于实现生产过程自动化。
④由于浇注系统的熔料在生产过程中始终处于熔融状态,浇注系统畅通,压力损失小,可以实现多点浇口、一模多腔和大型模具的低压注塑;还有利于压力传递,从而克服因补缩不足所导致的制作缩孔、凹陷等缺陷,改善应力集中产生的翘曲变形,提高了塑件质量;⑤由于没有浇注系统的凝料,而缩短了模具的开模行程,提高了设备对深腔塑件的适应能力。
2.热流道成型的缺点①模具的设计和维护较难,若没有高水平的模具和维护管理,生产中模具易产生各种故障;②成型准备时间长,模具费用高,小批量生产时效果不大;③对制件形状和使用的塑料有原则;④对于多型腔模具,采用热流道成型技术难度较高。
塑料件模具设计--浇注系统设计

(6)轮辐式浇口
轮辐式浇口的适用范围类似 于盘形浇口,带有矩形内 孔的塑件也适用,但是它 将整个周边进料改成了几 小段直线进料。这种浇口 切除方便,流道凝料少, 型芯上部得到定位而增加 了型芯的稳定性。
31
(7)护耳式浇口
它在型腔侧面开设耳槽,熔体通过浇口冲击在 耳槽侧面上,经调整方向和速度后再进入型 腔,因此可以防止喷射现象,是一种典型的 冲击性浇口,它可减少浇口附近的内应力, 对于流动性差的塑料极为有效,浇口应设置 在塑件的厚壁处。
这种浇口的去除比较 困难,痕迹大
32
(8)点浇口
点浇口又称针点浇口或菱形浇口,是一 种截面尺寸很小的浇口,俗称小浇口。 这类浇口由于前后两端存在较大的压力 差,能较大地增大塑料熔体的剪切速率 并产生较大的剪切热,从而导致熔体的 表观粘度下降,流动性增加,有利于型 腔的充填。
33
(8)点浇口的设计形式
图a所示为直接式,直径为d的圆锥形的小端直接与塑件相 连。
图b所示为圆锥形的小端有一段直径为d、长度为l的点浇口 与塑件相连。这种形式的浇口直径d不能太小,浇口长度l 不能大长,否则脱模时浇口凝料会断裂而堵塞住浇口,影 响注射的正常进行。上述两种形式的点浇口制造方便,但 去除浇口时容易相伤塑件,浇口也容易磨损,仅适于批量 不大的塑件成型和流动性好的塑料。
非限制性浇口是整个浇口系统中截面尺寸最大的部位,它主 要对中大型筒类、壳类塑件型腔起引料和进料后的施压作用。
21
1、浇口的类型
(1)直接浇口(又称主流道形浇口)
在单型腔模中,熔体直接流入型腔,因 而压力损失小,进料速度快,成型比 较容易,对各种塑料都能适用。它传 递压力好,保压补缩作用强,模具结 构简单紧凑,制造方便。
- 1、下载文档前请自行甄别文档内容的完整性,平台不提供额外的编辑、内容补充、找答案等附加服务。
- 2、"仅部分预览"的文档,不可在线预览部分如存在完整性等问题,可反馈申请退款(可完整预览的文档不适用该条件!)。
- 3、如文档侵犯您的权益,请联系客服反馈,我们会尽快为您处理(人工客服工作时间:9:00-18:30)。
热流道浇汰系统又称无流通凝料浇注系统,需要在注射模巾采用绝热或加热的方法,使从泞射机喷嘴到型腔入口这一段流道中的塑料一直保持熔融状态,从而在开模时贝需取111制
品,r6f2需取山浇注系统的凝料。
5.3.1 热流道成型的优缺点及适用范围
热流道成型的优点如下:
(1)有利于改善制品的质量。
当大型塑料制品采用直接浇口时,浇口四周的残余应力和变形会给制品的物理性能及精度带来个良的影响,因此不得不采用多点浇u。
采均点浇口就得采蝴二板式模具结构,二板式结构对于大型模具应是尽量避免的。
而采均无流道成型既能改善制品的质坦,AVX又避免丁采用三板式横具。
(2)阅没村流道凝料减少了原料的消耗。
(3)因允需二次分型,降低了对注射机开棋行秆的要求。
(4)容易实现自动化操作,制品的后续An丁减少。
热流通成型的缺点如下:
(1)模且的设计和维护较难,若没有高水平的模具和维护管理,个产中模具扬产个各种
故障。
(2)成型难备时司长、模义费用高,小批量生产时效果不大。
(3)对制品形状和使拖的塑料有限制。
(4)对于多型腔模共,采用热流道成型的技术难度较高。
热流通成型原则L:远则于高速成型的塑料制品,若制品冷却时间长.化。
适用于热流道成型的塑料府具有如下持性:
(1)曲料对温度不敏感,在较低温度下也具有良好的流动性,成型的温度范围较宽。
(2)对压力敏感,当不施加压力时,熔休不流动,但一旦施加较低尼力时熔体就能
流动。
(3)塑料的导热性能好,可缩短注射成型周期。
比热容低,温度上升或下降迅速。
(4)塑料的热变形温度高,能将制品迅速从模具中取出。
最能满足上述要求的热塑性塑料是聚乙烯,其次是聚丙烯、聚苯乙烯和ABS。
热流道成型技术在近30午来发展很快,据报道,在美国约40%的注射模采用了热流道
成型,特别是在成型盖冕、容器和外壳等类制品的注射模中,采用热流道的达到80%。
U
木的热流道模具也在逐渐普及之中。
热流道加热装置在先进工、Lk同己达到作为标准件出售的
程度。
我国也正在开展和推广热流道成型技术。
按加热方式一般可将热流道模具分为绝热式模具和热流道模具两类。
5.3.2绝热流道模具
绝热式流道的特点是流道粗大,以致流道个心部位的塑料在连续注射时来不及凝因而保
持熔融状态,使熔体能不断地通过流道进入型腔。
绝热式流道模具可分为井式喷嘴模具和绝
热分流道模具两种。
(1)井式喷嘴模具。
井式喷嘴模具是最简单的绝热式流道模义,其结构如图5—22所
示。
布注射机喷嘴和模具入口之间设置有流道杯,均以储存塑料熔体。
制品冷却后,显然流
道朴令外层的塑料已经冷凝,但在其中心部位仍能保持熔融状态,以便于下一周期中的注射
成型。
这种模义只能做成单型腔,不且用于成型周期长和尺寸精度尚的制品。
(2)绝热分流道模具。
绝热分流道模具如图5—23所示,其结构与普通的三板式模具类似。
AVX钽电容所不同的是绝热分流道的直径很大,如同形分流道的直径常为19—32mm
这种栈具流道内的塑料容易冷凝硬化,使用时要针对塑料的种类和制品的尺寸,采取
些防止流道内塑料冷凝的措施,例如采用探针式加热器进行内部加热等。
wxq$#。