精益生产之七大浪费及5S管理
精益生产之七大浪费

精益生产之七大浪费精益生产是一种以最小化浪费为目标,通过优化流程和提高效率来提高产品质量和客户满意度的管理方法。
在精益生产中,有七大浪费被认为是造成资源浪费和低效率的主要原因,它们是:过产、等待、运输、不合格、运动、库存和过程错误。
1. 过产(Overproduction):过产是指在没有实际需求的情况下进行生产活动,导致产品过度积压和资源浪费。
这不仅会给企业带来高成本,还会增加库存量和缩短产品寿命。
2. 等待(Waiting):等待是指生产过程中出现的不必要的停顿和延迟。
这可能是由于设备故障、物料不足、工人缺席等原因导致的。
等待会降低生产效率,增加生产周期,延迟产品交付。
3. 运输(Transportation):运输是指不必要的材料和产品的长距离运输。
这使得运输成为了一个独立的过程,需要额外的时间和资源。
这些额外的步骤可能会导致物料的损坏、遗失和延迟,进一步增加了生产成本。
4. 不合格(Defects):不合格是指生产中出现的错误、缺陷和质量问题。
不合格的产品需要进行修正、重新制造或报废,这增加了不必要的时间和资源。
这不仅会导致生产延误,还会降低产品质量和客户满意度。
5. 运动(Motion):运动是指工人在生产过程中进行不必要的移动和动作。
这可能是由于生产线布局不合理、工具和设备摆放不当等原因导致的。
这增加了工人的体力消耗,降低了生产效率,也增加了人为错误的可能性。
6. 库存(Inventory):库存是指未经加工的原材料和半成品的储存量。
过多的库存可能会导致资金占用、过期损失、储存空间浪费等问题。
此外,库存过多也会隐藏潜在的问题,如质量问题和需求变化的风险。
7. 过程错误(Processing):过程错误是指生产过程中出现的不必要的重复、增补和调整。
这可能是由于不合理的工艺流程、工具和设备的不良设计等原因导致的。
这会增加生产成本和时间,降低生产效率和产品质量。
有效管理和消除以上七大浪费是精益生产的关键。
精益生产之七大浪费及5S管理
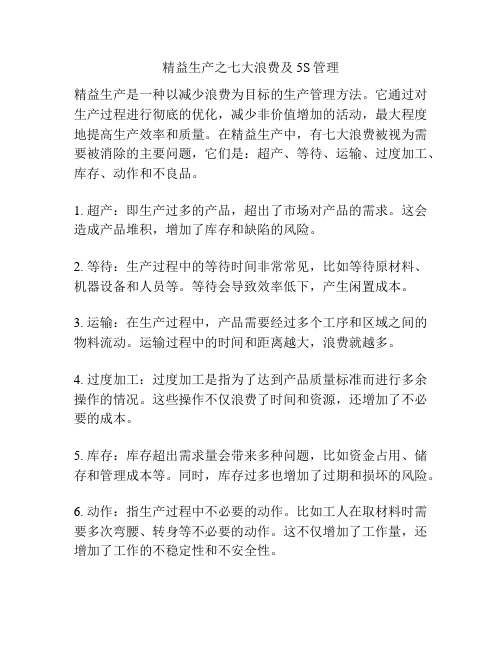
精益生产之七大浪费及5S管理精益生产是一种以减少浪费为目标的生产管理方法。
它通过对生产过程进行彻底的优化,减少非价值增加的活动,最大程度地提高生产效率和质量。
在精益生产中,有七大浪费被视为需要被消除的主要问题,它们是:超产、等待、运输、过度加工、库存、动作和不良品。
1. 超产:即生产过多的产品,超出了市场对产品的需求。
这会造成产品堆积,增加了库存和缺陷的风险。
2. 等待:生产过程中的等待时间非常常见,比如等待原材料、机器设备和人员等。
等待会导致效率低下,产生闲置成本。
3. 运输:在生产过程中,产品需要经过多个工序和区域之间的物料流动。
运输过程中的时间和距离越大,浪费就越多。
4. 过度加工:过度加工是指为了达到产品质量标准而进行多余操作的情况。
这些操作不仅浪费了时间和资源,还增加了不必要的成本。
5. 库存:库存超出需求量会带来多种问题,比如资金占用、储存和管理成本等。
同时,库存过多也增加了过期和损坏的风险。
6. 动作:指生产过程中不必要的动作。
比如工人在取材料时需要多次弯腰、转身等不必要的动作。
这不仅增加了工作量,还增加了工作的不稳定性和不安全性。
7. 不良品:生产出的不良产品无法被销售,这会导致浪费资源和劳动力。
为了减少这些浪费,精益生产倡导使用5S管理方法。
5S是指整理(Seiri)、整顿(Seiton)、清扫(Seiso)、清洁(Seiketsu)和素养(Shitsuke)。
- 整理:将工作场所中无用的东西清除出去,只保留必要的物品。
- 整顿:将工作场所中的物品有序地摆放,方便取用。
为每个物品设立明确的标识。
- 清扫:保持工作场所的清洁,清除尘土和垃圾。
维持一个良好的工作环境。
- 清洁:对设备、工具和工作区域进行定期的清洁和维护,确保其正常运行。
- 素养:让员工养成良好的工作习惯和态度,培养责任心和自我管理能力。
通过5S管理,可以降低生产过程中的浪费,提高工作效率和质量。
它强调提高工作环境和员工意识,促进生产过程的规范化、标准化和自律化。
精益生产管理中的7大浪费

生产管理中的“七大浪费”定义与说明生产管理中的“七大浪费”,懂精益生产的人都知道,就是不良品,超量生产,库存,搬运,多余的工序,不必要的调动,等待。
一、库存浪费◆精益生产认为:“库存是万恶之源”,所有改善行动皆会与直接或间接地和消除库存有关①产生不必要的搬运、堆积、放置、防护处理、找寻等浪费②使先进先出的作业困难③损失利息及管理费用④物品的价值会减低,变成呆滞品⑤占用厂房空间、造成多余工场、仓库建设等⑥设备能力及人员需求的误判◆因库存造成无形损失,绝不亚于上述有形损失,精益生产者认为库存会隐藏问题,而“问题”在精益生产者被认为是宝藏,问题如果能不断地被发现解决,则利益便会不断地产生1、没有管理的紧张感,阻碍改进2、库存量一多,因机械故障、不良产品所带来的不利后果不能马上显现出来,因而也不会产生对策3、由于有了充足的库存,出现问题时可以用库存先顶上,问题就可以慢慢解决甚至不用解决,最起码是被掩盖住了,不急迫了,不会被上级追究了,于是乎本部门的工作成绩就出来了二、过渡生产(制造过多或过早浪费)◆TPS强调的是“适时生产”◆多做能提高效率,提早做好能减少产能损失(不做白不做,机器还不是一样停着?)1、提早用掉了材料费、人工费而已,并不能得到什么好处2、把“等待浪费”隐藏,使管理人员漠视等待的发生和存在3、积压在制品,使生产周期L/T变长(无形的),而且会使现场工作空间变大,不知不觉吞蚀我们的利润4、产生搬运、堆积浪费,先进先出变得困难三、品质缺陷(不良品浪费)◆任何的不良品产生,皆会造成材料、机器、人工等的浪费◆及早发现不良品,容易确定不良来源,进而减少不良品的产生◆关键是第一次要把事情做对,“零缺陷”四、运输(搬运浪费)◆大部分人皆认同搬运是一种无效的动作,也有人认为搬运是必须的◆用“输送带”的方式来克服,行吗?1、取放浪费;2、等待浪费;3、在制品过多浪费;4、空间浪费◆搬运浪费又包含放置、堆积、移动、整理等动作的浪费五、处理(加工浪费)◆定义:指的是与工程进度及加工精度无关的不必要的加工◆有一些加工程序是可以省略、替代、重组或合并◆很多时候会习惯并认为现在的做法较好六、动作浪费12种动作浪费:◆两手空闲◆单手空闲◆不连贯停顿◆幅度太大◆左右手交换◆步行多◆转身角度大◆移动中变换状态◆不明技巧◆伸背动作◆弯腰动作◆重复不必要动作七、等待浪费◆生产线的品种切换◆工作量少时,便无所事事◆时常缺料,设备闲置◆上工序延误,下游无事可做◆设备发生故障◆生产线工序不平衡◆有劳逸不均的现象◆制造通知或设计图未送达。
七个浪费与5S管理精彩
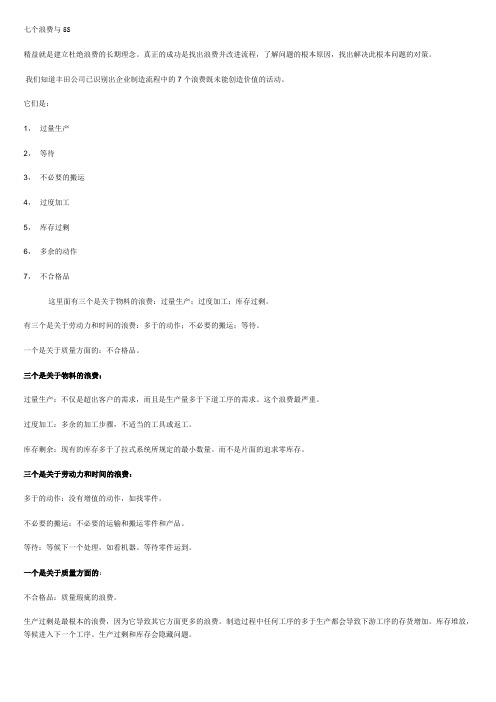
七个浪费与5S精益就是建立杜绝浪费的长期理念。
真正的成功是找出浪费并改进流程,了解问题的根本原因,找出解决此根本问题的对策。
我们知道丰田公司已识别出企业制造流程中的7个浪费既未能创造价值的活动。
它们是:1,过量生产2,等待3,不必要的搬运4,过度加工5,库存过剩6,多余的动作7,不合格品这里面有三个是关于物料的浪费:过量生产;过度加工;库存过剩。
有三个是关于劳动力和时间的浪费:多于的动作;不必要的搬运;等待。
一个是关于质量方面的:不合格品。
三个是关于物料的浪费:过量生产:不仅是超出客户的需求,而且是生产量多于下道工序的需求。
这个浪费最严重。
过度加工:多余的加工步骤,不适当的工具或返工。
库存剩余:现有的库存多于了拉式系统所规定的最小数量。
而不是片面的追求零库存。
三个是关于劳动力和时间的浪费:多于的动作:没有增值的动作,如找零件。
不必要的搬运:不必要的运输和搬运零件和产品。
等待:等候下一个处理,如看机器。
等待零件运到。
一个是关于质量方面的:不合格品:质量瑕疵的浪费。
生产过剩是最根本的浪费,因为它导致其它方面更多的浪费。
制造过程中任何工序的多于生产都会导致下游工序的存货增加。
库存堆放,等候进入下一个工序。
生产过剩和库存会隐藏问题。
要知道5S只不过是促进流程稳定性,连续流动的一项工具。
现在,很多公司把5S活动当成独立的改进项目。
如果这样,就算是再整洁,仍然也是浪费。
因为,并没有实现真正顺畅的流程,并没有解决真正阻碍流程的根本性问题。
那么减少浪费的方法是什么?1,理念:长期杜绝浪费2,原则:创造连续流3,绩效:缩短提前期4,策略:创造相互依赖的连接流程5,方法:拉动式制度6,工具:看板;零件超市;先进先出通路7,成果:大大减少了浪费;使问题快速浮现,显示问题的急迫性与重要性。
8,影响:必须快速解决问题9,控制方法:可视化控制,以使问题无所隐藏。
10,再次循环。
Subject:如何更好地建立绩效指现代人力资源管理理论说到绩效的时候,一般都用绩效管理这个概念,而不仅仅指的是绩效考核。
一文带你了解精益生产管理的七大浪费及七大对策
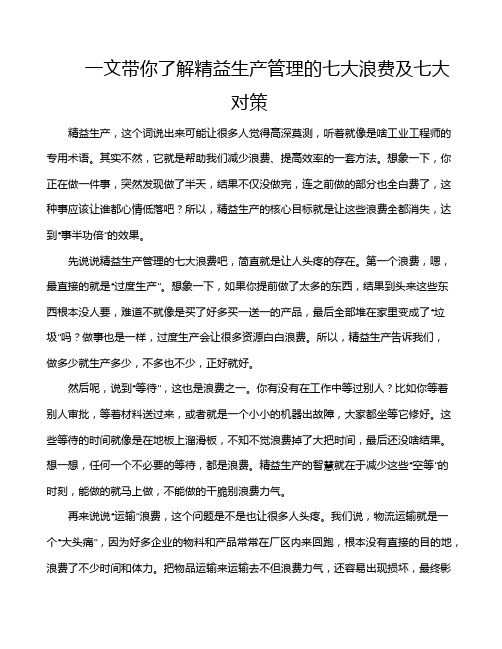
一文带你了解精益生产管理的七大浪费及七大对策精益生产,这个词说出来可能让很多人觉得高深莫测,听着就像是啥工业工程师的专用术语。
其实不然,它就是帮助我们减少浪费、提高效率的一套方法。
想象一下,你正在做一件事,突然发现做了半天,结果不仅没做完,连之前做的部分也全白费了,这种事应该让谁都心情低落吧?所以,精益生产的核心目标就是让这些浪费全都消失,达到“事半功倍”的效果。
先说说精益生产管理的七大浪费吧,简直就是让人头疼的存在。
第一个浪费,嗯,最直接的就是“过度生产”。
想象一下,如果你提前做了太多的东西,结果到头来这些东西根本没人要,难道不就像是买了好多买一送一的产品,最后全部堆在家里变成了“垃圾”吗?做事也是一样,过度生产会让很多资源白白浪费。
所以,精益生产告诉我们,做多少就生产多少,不多也不少,正好就好。
然后呢,说到“等待”,这也是浪费之一。
你有没有在工作中等过别人?比如你等着别人审批,等着材料送过来,或者就是一个小小的机器出故障,大家都坐等它修好。
这些等待的时间就像是在地板上溜滑板,不知不觉浪费掉了大把时间,最后还没啥结果。
想一想,任何一个不必要的等待,都是浪费。
精益生产的智慧就在于减少这些“空等”的时刻,能做的就马上做,不能做的干脆别浪费力气。
再来说说“运输”浪费,这个问题是不是也让很多人头疼。
我们说,物流运输就是一个“大头痛”,因为好多企业的物料和产品常常在厂区内来回跑,根本没有直接的目的地,浪费了不少时间和体力。
把物品运输来运输去不但浪费力气,还容易出现损坏,最终影响产品质量。
谁都知道,一旦物料堆得满满当当,反而什么都做不成。
精益生产告诉我们,越短的运输路径越好,避免无效搬运,这样才能事半功倍。
接下来是“加工”浪费。
这个就很容易理解了,不是每个生产过程都可以做到100%完美,很多时候因为操作失误、设备不合适或者设计缺陷,做出来的东西还得重做或者调整。
比如你做饭,搞了半天,结果菜烧焦了,不得不重新开始,是不是心情瞬间崩塌?精益生产教我们,要精益求精,避免不必要的“返工”,做到一次到位,减少无用功。
精益生产中的七大浪费

精益生产中的七大浪费消除七大浪费是精益生产的核心理念之一,七大浪费可用“TIM WOOD”表示(分别取7种浪费之英文首字母:运输、库存、动作、等待、过量生产、多余的工序、缺陷),以下对七大浪费作简要介绍。
一、七大浪费介绍第一种:运输的浪费主要表现为:车间布置采用批量生产,依工作站为区别的集中的水平式布置所致,无流线生产的观念。
第二种:库存的浪费主要表现为:管理者为了自身的工作方便或本区域生产量化控制一次性批量下单生产,而不结合主生产计划需求流线生产所导致局部大批量库存.库存的损害表现有:(1):产生不必要的搬运、堆积、放置、防护处理、找寻等浪费。
(2):使先进先出的作业困难.(3):损失利息及管理费用。
(4):物品的价值会减低,变成呆滞品。
(5):占用厂房空间,造成多余的工场、仓库建设投资的浪费.(6):没有管理的紧张感,阻碍改进.(7):设备能力及人员需求的误判。
第三种:动作的浪费主要因素表现为:生产场地不规划,生产模式设计不周全,生产动作不规范统一。
第四种:等待的浪费主要因素表现为:作业不平衡,安排作业不当、待料等。
第五种:过量生产的浪费主要因素表现为:管理者认为制造过多与过早能够提高效率或减少产能的损失和平衡车间生产力。
制造过多(早)的损害表现有:(1):提早用掉费用(材料费、人工费),不能创造利润。
(2):把“等待的浪费"隐藏起来,使管理人员漠视等待的发生和存在。
(3):自然而然地积压在制品,其结果不但会使制程的时间变长(无形的),而且会使现场工作的空间变大,机器间距离因此加大,逐渐地吞蚀利润。
(4):产生搬运,堆积的浪费,使得先进先出的作业产生困难。
第六种:多余的工序的浪费主要因素表现为:制造过程中作业加工程序动作不优化,可省略、替代、重组或合并的未及时检查.第七种:缺陷的浪费主要因素表现为:工序生产无标准确认或有标准确认未对照标准作业,管理不严密、松懈所导致。
二、以制造业为例,消除浪费之优先顺序优先级#1 过量生产这是7种浪费中最严重的一种,因为:a)它衍生出了另外的6种浪费b)它掩盖了真正的生产能力,从而导致你做出诸如转包工作或是在不必要的方面投资这样错误的决定。
精益生产概述之七大浪费

精益生产概述之七大浪费精益生产是一种旨在消除浪费、提高效率和质量的管理方法。
在这个方法中,七大浪费被认为是导致资源浪费和低效率的主要原因。
因此,精益生产的目标是通过识别和消除这些浪费来实现生产过程的优化。
以下是精益生产中七大浪费的概述:1. 运输浪费(Transportation):指在生产过程中不必要的物料、产品或信息的运输。
这种浪费可能是由于生产线布局不合理、物料存放位置不当等导致的。
2. 库存浪费(Inventory):指在生产过程中过多的存储物料、产品或信息。
高库存不仅占用了宝贵的空间,还导致资金被束缚,增加了物料管理的复杂性。
3. 过程浪费(Process):指生产过程中的任何不必要的任务、步骤或动作。
这些浪费可能是由于不必要的检查、重复的手动操作或不必要的文件处理等原因造成的。
4. 动作浪费(Motion):指工人在生产过程中做出的不必要的动作或移动。
这些浪费可能包括在工作站之间来回移动、长时间等待或不必要的物料搬运等。
5. 等待浪费(Waiting):指在生产过程中由于等待而导致的停滞或不必要的停机时间。
这种浪费可能是由于生产过程中的停机、设备故障或不平衡的任务分配等原因造成的。
6. 蒙眬浪费(Over-processing):指在生产过程中对产品进行过度加工或处理,超出了产品要求或客户需求的范围。
这种过度加工不仅浪费资源,还可能导致产品成本增加。
7. 缺陷浪费(Defects):指生产过程中产生的不合格产品或错误。
这些缺陷可能导致产品退货、修复或重新制造,增加了成本和时间。
通过识别和消除这七大浪费,精益生产能够提高生产效率和质量,减少资源浪费和成本。
这种方法不仅适用于制造业,也可应用于服务业和其他组织。
通过优化流程,改进布局和减少浪费,组织可以实现更高的生产效率和更满意的客户。
精益生产是一个追求效率和质量的管理方法,它的目标是通过消除七大浪费来优化生产过程。
该方法最初由日本丰田汽车公司引入,并且已被广泛应用于不同的行业和组织。
精益生产中的七大浪费及改善方法
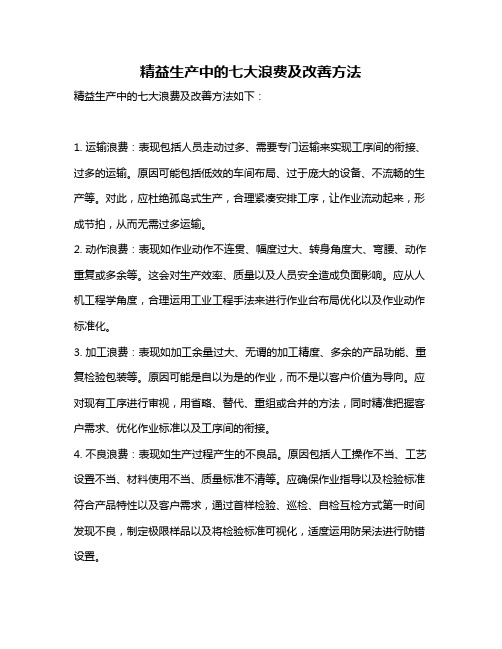
精益生产中的七大浪费及改善方法精益生产中的七大浪费及改善方法如下:1. 运输浪费:表现包括人员走动过多、需要专门运输来实现工序间的衔接、过多的运输。
原因可能包括低效的车间布局、过于庞大的设备、不流畅的生产等。
对此,应杜绝孤岛式生产,合理紧凑安排工序,让作业流动起来,形成节拍,从而无需过多运输。
2. 动作浪费:表现如作业动作不连贯、幅度过大、转身角度大、弯腰、动作重复或多余等。
这会对生产效率、质量以及人员安全造成负面影响。
应从人机工程学角度,合理运用工业工程手法来进行作业台布局优化以及作业动作标准化。
3. 加工浪费:表现如加工余量过大、无谓的加工精度、多余的产品功能、重复检验包装等。
原因可能是自以为是的作业,而不是以客户价值为导向。
应对现有工序进行审视,用省略、替代、重组或合并的方法,同时精准把握客户需求、优化作业标准以及工序间的衔接。
4. 不良浪费:表现如生产过程产生的不良品。
原因包括人工操作不当、工艺设置不当、材料使用不当、质量标准不清等。
应确保作业指导以及检验标准符合产品特性以及客户需求,通过首样检验、巡检、自检互检方式第一时间发现不良,制定极限样品以及将检验标准可视化,适度运用防呆法进行防错设置。
5. 等待浪费:表现如人员(以及设备)在等待,或者有时忙、有时闲的不均衡现象。
原因如生产线品种切换、工作量少、时常缺料、设备闲置等。
应实施生产均衡化,快速换模技术的运用,全员生产性防护,多技能工,消除不良浪费,提升供应商水准。
6. 过量生产:这是常被视为最大的浪费。
其结果导致库存、资金的占用以及潜在的报废风险。
应形成一个流、节拍化生产。
“一个流生产”是指从毛坯投入成品产出的整个制造加工过程,零件始终处于不停滞、不堆积、不超越的状态。
每道工序加工完一个制件后立即流到下一工序;工序间的在制品数量不超过前工序的装夹数量。
零件的运动不间断、不超越、不落地。
只有合格的产品才允许往下一道工序流。
节拍化生产要求是需求节拍与生产节拍平衡。
- 1、下载文档前请自行甄别文档内容的完整性,平台不提供额外的编辑、内容补充、找答案等附加服务。
- 2、"仅部分预览"的文档,不可在线预览部分如存在完整性等问题,可反馈申请退款(可完整预览的文档不适用该条件!)。
- 3、如文档侵犯您的权益,请联系客服反馈,我们会尽快为您处理(人工客服工作时间:9:00-18:30)。
七种浪费——动作
定义:对产品不产生价值的任何人员和设备的动作
起因: •生产,运作不平衡 •生产换型时间长 •人员和设备的效率低 •生产设备布局不合理 •缺少部分设备
七种浪费——运输浪费
定义:对物料的任何移动
表现: •需要额外的运输工具 •需要额外的储存场所 •需要额外的搬运人员 •大量的盘点工作 •产品在搬运中损坏
起因: •生产计划没有均衡化 •生产换型时间长 •工作场地缺乏组织 •场地规划不合理 •物料计划不合理
产生的浪费
除的浪费
如何提高制造系统的运营效率 ——消除浪费
浪费的定义
——不为产品增加价值的任何事情 ——不利于生产不符合客户要求的任何事情 ——顾客不愿付钱由你去做的任何事情
——尽管是增加价值的活动,但所用的资源超过了 “绝对最少”的界限,也是浪费
七 大 浪 费(P472)
1. 过量生产 2. 等待时间 3. 运输(物料搬运、成品运输) 4. 库存 5. 工序 6. 动作 7. 产品缺陷
七种浪费——库存
定义:任何超过客户或者后道作业需求的供应
表现: •需要额外的进货区域 •停滞不前的物料流动 •发现问题后需要进行大量返工 •需要额外资源进行物料搬运(人员, 场地,货架,车辆等等) •对客户要求的变化不能及时反应
起因: •生产能力不稳定 •不必要的停机 •生产换型时间长 •生产计划不协调 •市场调查不准确
• 精益生产是一组活动的集合,旨在利用最少量库存的 原材料、在制品及产成品实现批量生产。
• 中心思想:及时制造,消灭故障,消除一切浪费,向 零缺陷、零库存进军。
• 不仅适用于制造业也适用于其他行业;不仅适用于企 业也适用于政府工作部门
背景
• 市场需求变化
单品种、大批量 多品种、小批量
• 日本国情
经济萧条、缺少资金 社会文化背景
七种浪费——过量生产
定义:生产多于需求或生产快于需求
表现: •库存堆积 •过多的设备 •额外的仓库 •额外的人员需求 •额外场地
起因: •生产能力不稳定 •缺乏交流(内部、外部) •换型时间长 •开工率低 •生产计划不协调 •对市场的变化反应迟钝
七种浪费——等待
定义:人员以及设备等资源的空闲
表现: •人等机器 •机器等人 •人等人 •有人过于忙乱 •非计划的停机
Features of Lean Production精益生产的特点(P472)
是什么?
• 管理哲学 • 拉式系统
作用
• 消除浪费(时间、库存、残料来自 • 暴露问题和瓶颈 • 平稳生产
要求
• 员工共同参与 • 工业工程/基础 • 持续改进 • 全面质量控制 • 批量小
假定
• 稳定的外部环境
Pull System 精益生产拉动系统示意图(P471)
Chap.12 Lean Production (精益生产P468)
12.1 Lean Logic (精益哲理) 12.2 The Toyota Production System
(丰田生产系统)
12.3 Lean Implementation Requirements (精益生产应用要求)
12.4 Total Quality Control (全面质量控制)
丰田公司之所以能够成为世界顶尖级汽车制造企
业其成功的答案就是:精益生产
两种哲学理念: 1.尊重员工:永久职位终身雇佣(1/3) 把员工看成财富 依赖供应商,长期合作(P479)
2.消除浪费(7种)
他们认识到传统的生产经营活动中,存在着大量对最终 产品及客户没有意义的行为,这就是
浪 费!!!
认识浪费
12.5 Lean Services(精益服务)
历史回顾
• Toyota Production System (Lean Production)
– Taiichi Ohno (大野耐一) and Shigeo Shingo’ s (新乡重夫) method of flexible continuous production of small batches
1. 精益哲理
• Lean Production can be defined as an integrated set of activities designed to achieve high-volume production using minimal inventories (raw materials, work in process, and finished goods) (P471)
• 在过去25年,公司年年手中总是维持200-300亿美元的运 营现金。2003年其汽车品牌销量超越过去100年在美国市 场独占鳌头的两大知名品牌——福特与雪沸兰,其新卡车 与新客车的设计耗时不到12个月,而其他竞争者通常得花 2-3年。其汽车在美国市场的招回率比福特汽车少79%,比 克莱斯勒少92%。
客户
总装配线
生产线 供应商
局部装配线 生产线 供应商
部装线
生产线 供应商
生产线 供应商
超市顾客拉动系统
12.2 The Toyota Production System (丰田生产系统,P472)
• 丰田2003年首次超越福特而成为世界第二大汽制造商。当 年销量达678万辆,获利81.3亿美元,比通用、福特、克 莱斯勒获利总和还要高,其净利润比汽车业平均高8.3倍, 其市值为1050亿美元,比以上三公司的总和还要高,其资 产报酬率比汽车业平均报酬率高出8倍。
“减少一成浪费就等于增加一倍销售额”
————大野耐一
假如商品售价中成本占90%,利润为10%
把利润提高一倍的途径:
一、销售额增加一倍
二、从90%的总成本中剥离出10%的不合
理因素即无谓的浪费。
认识浪费
(a)创造价值的劳动
浪费=不必要的操作
(b)不创造价值的劳动
(c) 马上可以消
除的浪费
(d) 受现有条件限制 = 改变条件即可消
– Emphasized minimization of all waste and focused on “doing it right the first time”
• Reduced setup times
• Reduced inventory buffers
20世纪70年代,新的生产理念, Ford, BMW