聚合型受阻酚抗氧剂CPL的合成工艺优化
一种受阻酚类抗氧剂的合成研究
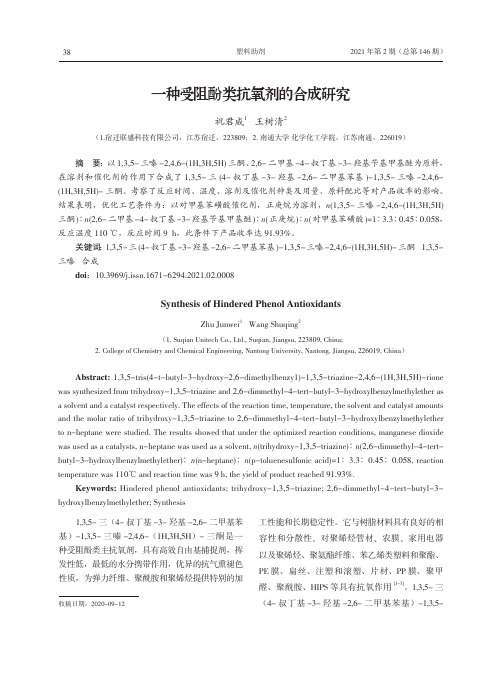
日立 L-7420 高效液相色谱仪,日本日立公司;
物的相容性较好,而另外两种催化剂溶解性稍差一 些。所以选择对甲基苯磺酸为催化剂。 2.2 催化剂用量对产品收率的影响
催化剂类型
产品收率/%
浓硫酸
91.87
对甲苯磺酸
88.92
甲基磺酸
85.24
由表 1 看出,采用对甲基苯磺酸为催化剂时,
三嗪 -2,4,6-(1H,3H,5H)- 三酮。
产品的收率最高,这是由于对甲基苯磺酸,与反应
1 实验
1.1 实验试剂及仪器 1,3,5- 三嗪 -2,4,6-(1H,3H,5H)三酮,化学纯,
溶剂
产品收率/%
石油醚
87.85
正己烷
80.91
正庚烷
91.87
由表 3 看出,正己烷的沸点低,反应温度低, 不利于反应的进行,正庚烷为溶剂时,产品的收率 最高,所以选择正庚烷为溶剂。 2.4 溶剂用量对产品收率的影响
在反应器中加入 1,3,5- 三嗪 -2,4,6-(1H,3H,5H) 三酮 12.9 g(0.1 mol)、2,6- 二甲基 -4- 叔丁基 -3羟 基 苄 基 甲 基 醚 73.3 g(0.33 mol), 反 应 温 度 110℃,反应时间 9 h,催化剂 10g,考察溶剂的用 量对产品收率的影响。结果见表 4。
在反应器中加入正庚烷45 g,1,3,5-三嗪 -2,4,6(1H,3H,5H)三酮 12.9 g(0.1mol)、2,6- 二甲基 -4叔丁基 -3- 羟基苄基甲基醚 73.3 g(0.33 mol), 反应温度 110 ℃,反应时间 9 h,改变催化剂用量, 考察催化剂的用量对产品收率的影响。结果见表 2。
聚合型受阻酚抗氧剂的制备工艺研究

抗 氧剂广 泛 用于橡 胶 、 塑料 、 维 、 纤 粘合 剂 , 防止 材料 的老 化 , 长材料 使 用寿命 , 延 另外还 用 于抑制 燃 料油 粘度 和 酸度 的增加 及食 品 防腐 等[ 。抗 氧剂 主要 有胺 类 、 1 ] 酚类 、 硫磷类 化 合物 及有 机 金属 盐类 等 。其 中胺 含 类抗 氧剂 因毒性 大主要 用 于橡 胶 , 用 过程 中易变 色 , 烃 类 油配 伍 不 好 , 使 与 目前 的研 究 方 向是 毒 性小 的胺 类 复 合型 防老剂 及 聚合 型胺 类抗 氧剂 。其 它类 型 中大 多毒 性低 , 类抗 氧剂 是 所有抗 氧 剂 中最好 的一 种 , 以 酚 可 分 为单 酚 、 酚类 抗 氧剂 , 双 有不 污染 、 毒或 无毒 特 点 , 低 同时 也具 有 很 好 的抗 氧 化 能 力 , 后 酚类 抗 氧剂 的发 今 展 方 向是提 高 自身 的相对 分子 质量 ] 。通用 型 的酚类 抗 氧 剂 的最 佳 分子 量 在 8 0 10 03, 聚 合 型受 阻 0 ~ 0[ 而 ] 酚抗 氧剂 相对 分子 质量 大 于 8 0 能溶 于 芳 香族 化 合 物 、 类 、 水 乙醇 、 丙 醇 等溶 剂 , 溶 于水 及各 种 水 0, 醚 无 异 不 溶液, 主要用 作天 然橡 胶 和合 成橡胶 、 聚酰胺 、 聚氨酯 或 聚 酯纤 维 、 料 的 防老 剂 。本 品无 毒 , 用 于食 品包 塑 可 装 材料 。聚 合型 受阻 酚抗 氧剂 的合 成 可 以用对 甲酚 与双 环 戊 二烯 进 行缩 合 反 应 制 得 的石 油 树脂 为原 料 , 再 与 异丁 烯进 行烷 基化 制得 ] 。本 文 以该 石油 树脂 及异 丁 烯 为原 料 考查 各 种 工 艺条 件 对合 成 聚 合 型 酚类 抗
受阻酚类抗氧剂的制备方法[发明专利]
![受阻酚类抗氧剂的制备方法[发明专利]](https://img.taocdn.com/s3/m/64f22ee54a7302768e9939e8.png)
专利名称:受阻酚类抗氧剂的制备方法专利类型:发明专利
发明人:孙春光,汤翠祥,范小鹏,常贻文申请号:CN201611236053.9
申请日:20161228
公开号:CN106674002A
公开日:
20170517
专利内容由知识产权出版社提供
摘要:本发明一种高效受阻酚类抗氧剂的制备方法,将3‑甲基‑5‑叔丁基‑4羟基苯基丙酸甲酯或3‑(3,5‑二叔丁基‑4羟基苯基)丙酸甲酯和相应的醇或胺在搅拌下混合均匀升温减压脱轻,后加入催化剂,升温减压进行酯交换反应;反应完成后将反应液打入刮板蒸发器或短程蒸馏设备中进行闪蒸,蒸出未反应完的3‑甲基‑5‑叔丁基‑4羟基苯基丙酸甲酯或3‑(3,5‑二叔丁基‑4羟基苯基)丙酸甲酯,后降温加入酸,保温中和后热过滤滤去催化剂,后进行结晶,烘干得到目标产物抗氧剂。
本发明对比将传统方法,操作简便,降低回收345酯或35甲酯的物料损耗、能耗,解决传统回收过程中三废问题,同时提高目标抗氧剂的收率及产品品质。
申请人:天津利安隆新材料股份有限公司
地址:300480 天津市汉沽区天津经济技术开发区汉沽现代产业区黄山路6号
国籍:CN
代理机构:天津市北洋有限责任专利代理事务所
代理人:王丽
更多信息请下载全文后查看。
新型受阻酚类抗氧剂的合成与性能研究
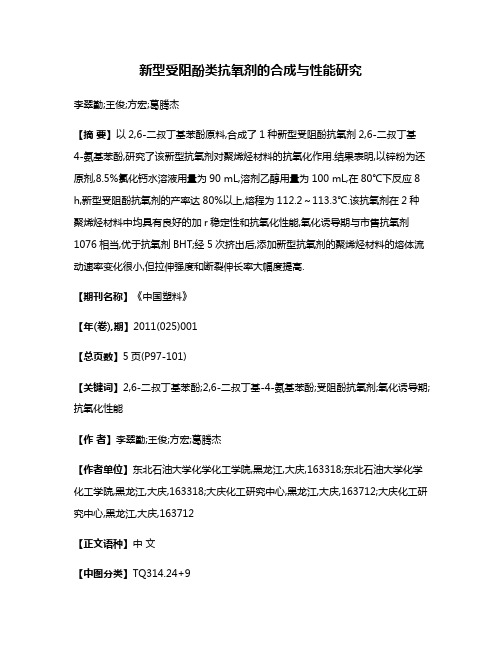
新型受阻酚类抗氧剂的合成与性能研究李翠勤;王俊;方宏;葛腾杰【摘要】以2,6-二叔丁基苯酚原料,合成了1种新型受阻酚抗氧剂2,6-二叔丁基4-氨基苯酚,研究了该新型抗氧剂对聚烯烃材料的抗氧化作用.结果表明,以锌粉为还原剂,8.5%氯化钙水溶液用量为90 mL,溶剂乙醇用量为100 mL,在80℃下反应8 h,新型受阻酚抗氧剂的产率达80%以上,熔程为112.2~113.3℃.该抗氧剂在2种聚烯烃材料中均具有良好的加r稳定性和抗氧化性能,氧化诱导期与市售抗氧剂1076相当,优于抗氧剂BHT;经5次挤出后,添加新型抗氧剂的聚烯烃材料的熔体流动速率变化很小,但拉伸强度和断裂伸长率大幅度提高.【期刊名称】《中国塑料》【年(卷),期】2011(025)001【总页数】5页(P97-101)【关键词】2,6-二叔丁基苯酚;2,6-二叔丁基-4-氨基苯酚;受阻酚抗氧剂;氧化诱导期;抗氧化性能【作者】李翠勤;王俊;方宏;葛腾杰【作者单位】东北石油大学化学化工学院,黑龙江,大庆,163318;东北石油大学化学化工学院,黑龙江,大庆,163318;大庆化工研究中心,黑龙江,大庆,163712;大庆化工研究中心,黑龙江,大庆,163712【正文语种】中文【中图分类】TQ314.24+9Abstract:A novel hinderd phenolic antioxidant 2,6-di-tert-butyl-4-aminophenol was synthesized with 2,6-di-tert-butylphenol as a raw material.When zinc powder was used as a reducing agent,ethanol as a solvent was 100 mL,the amount of calcium chloride solution was 90 mL,the reaction temperature was 80℃and the reaction time was 8 h,the yield ofthe product reached 80%and its melting point was between 112.2℃and 113.3℃.When loaded in polyolefin resins,the antioxidation property of the novel one was equal to antioxidant 1076 and was superior to antioxidant BHT.After extrusion of 5 times,the melt flow rate of the two polyolefins containing the novel antioxidant changed a little,and the tensile strength and the elongation at break increased.Key words:2,6-di-tert-butylphenol;2,6-di-tert-butyl-4-aminophenol;hinderd phenolic antioxidant;oxidation induction time;oxidation resistance property自1937年世界上第一个具有受阻酚结构的抗氧剂BHT问世以来,受阻酚类抗氧剂的开发和研究倍受关注[1]。
cpl产生机理
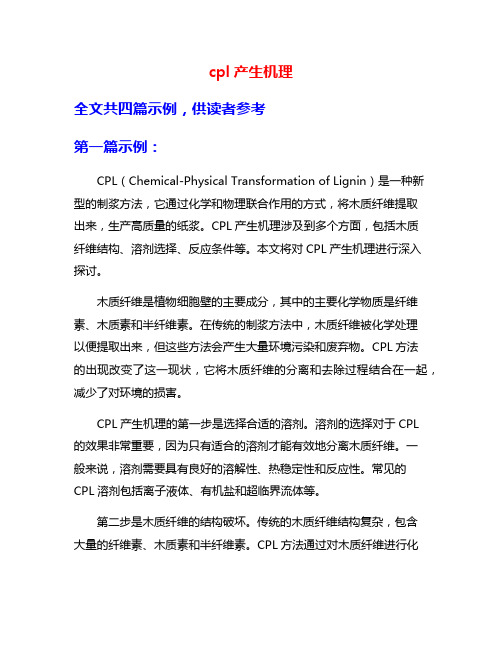
cpl产生机理全文共四篇示例,供读者参考第一篇示例:CPL(Chemical-Physical Transformation of Lignin)是一种新型的制浆方法,它通过化学和物理联合作用的方式,将木质纤维提取出来,生产高质量的纸浆。
CPL产生机理涉及到多个方面,包括木质纤维结构、溶剂选择、反应条件等。
本文将对CPL产生机理进行深入探讨。
木质纤维是植物细胞壁的主要成分,其中的主要化学物质是纤维素、木质素和半纤维素。
在传统的制浆方法中,木质纤维被化学处理以便提取出来,但这些方法会产生大量环境污染和废弃物。
CPL方法的出现改变了这一现状,它将木质纤维的分离和去除过程结合在一起,减少了对环境的损害。
CPL产生机理的第一步是选择合适的溶剂。
溶剂的选择对于CPL的效果非常重要,因为只有适合的溶剂才能有效地分离木质纤维。
一般来说,溶剂需要具有良好的溶解性、热稳定性和反应性。
常见的CPL溶剂包括离子液体、有机盐和超临界流体等。
第二步是木质纤维的结构破坏。
传统的木质纤维结构复杂,包含大量的纤维素、木质素和半纤维素。
CPL方法通过对木质纤维进行化学处理,破坏其结构,使其易于溶解和分离。
通常采用的方法包括酶解、酸碱处理和氧化等。
第三步是木质纤维的溶解。
在木质纤维结构破坏之后,溶解木质纤维是CPL的关键步骤。
溶解木质纤维需要在适当的温度、压力和pH 值下进行,以确保木质纤维完全溶解,并得到高质量的纤维。
这一步骤的成功与否直接影响着CPL的产率和质量。
最后一步是木质纤维的提取和制浆。
在木质纤维完全溶解后,需要将木质纤维从溶液中提取出来,然后进行洗涤和脱水处理,最终得到高质量的纸浆。
这一步骤需要在适当的温度和压力下进行,以确保木质纤维的提取和制浆过程顺利进行。
CPL的产生机理涉及到木质纤维结构的破坏、溶解和提取等多个环节。
通过合理选择溶剂和优化反应条件,可以提高CPL的产率和纸浆质量,实现高效、环保的木质纤维提取。
希望本文的探讨能对CPL 的研究和应用提供一定的参考价值。
一种复合液体受阻酚类抗氧剂及其制备方法

一种复合液体受阻酚类抗氧剂及其制备方法说实话一种复合液体受阻酚类抗氧剂及其制备方法这事,我一开始也是瞎摸索。
我就知道受阻酚类抗氧剂是防止材料氧化啥的挺有用,但是要搞复合的液体的,那可不容易。
我最开始就想着把各种原料一股脑混一起得了,结果那真叫一塌糊涂。
就好比做饭的时候盐、糖、酱油不分顺序乱放,最后做出来的东西根本不能吃一样。
后来我仔细研究这些原料,发现有的原料溶解特别不容易,要是直接混在一起,根本没法均匀混合。
那我就想啊,得想个办法让它们都能好好融合。
就像做沙拉的时候,要是蔬菜上有水,油醋汁就不那么容易拌匀,得把蔬菜先处理干点儿才能拌得好。
我就先针对那些不好溶的原料进行预处理,把它们弄成更细小的颗粒或者尝试加热让它们能更好地溶解在溶剂里。
再来就是比例的问题了。
我试过好多不同的比例,比如说这种原料放10份,那种原料放5份,变着花样试。
中间有很多次都失败了,做出来的抗氧剂效果特别差。
有一次我以为某个原料加多肯定好,结果反而把整个体系都破坏了,就像往一杯水里拼命加糖,最后甜得发苦还不好喝了。
经过多次摸索,我才慢慢找到了一个相对合适的比例范围。
还有反应条件,像温度和反应时间之类的。
我一开始觉得温度越高反应就越快越好呗,结果不是这样。
就跟跑步似的,不是跑得越快越久就能达到最好效果,得有个合适的节奏。
温度太高或者时间太长,不仅浪费能源,还会产生一些副反应,让最终的抗氧剂达不到预期效果。
我一次次调整温度,就那么一两度一两度地试,还有反应时间,从几个小时到几十个小时一点点琢磨。
这个制备方法啊,真不是一下两下就能搞定的。
我还不是完全确定现在这个方法就已经是最好的,也许还有其他的因素我没考虑到呢。
不过这一路摸索下来,也算是有点心得了。
要是你也想尝试做这个复合液体受阻酚类抗氧剂的话,一定要小心处理那些难溶的原料,好好琢磨比例,稳稳当当确定反应条件,不要像我刚开始一样瞎弄。
而且多记录下每次试验的结果,失败的教训啥的,这样才能慢慢找到更理想的方法。
聚乙烯接枝受阻酚抗氧剂及其制备方法和用途[发明专利]
![聚乙烯接枝受阻酚抗氧剂及其制备方法和用途[发明专利]](https://img.taocdn.com/s3/m/e381eda7fe4733687f21aa83.png)
专利名称:聚乙烯接枝受阻酚抗氧剂及其制备方法和用途专利类型:发明专利
发明人:李化毅,张银,李倩,刘卫卫,胡友良
申请号:CN201910487509.6
申请日:20190605
公开号:CN112048030A
公开日:
20201208
专利内容由知识产权出版社提供
摘要:本发明提供一种聚乙烯接枝受阻酚抗氧剂及其制备方法和用途,在聚乙烯接枝的受阻酚抗氧剂结构中引入长链烷基,大大提高了抗氧剂的分子量,可有效降低抗氧剂在加工过程和使用过程中的物理损失,增强长期抗氧能力和其耐迁移能力;所述受阻酚抗氧剂能够使高分子聚合物及其制品在使用或贮存过程中大大延长寿命,同时消除或减少因为使用抗氧剂而对人体造成的健康威胁。
本发明的受阻酚抗氧剂具有相容性好、抗氧性能高、不着色、不污染、耐洗涤、挥发性小、抗迁移能力强等优点。
申请人:中国科学院化学研究所
地址:100190 北京市海淀区中关村北一街2号
国籍:CN
代理机构:北京知元同创知识产权代理事务所(普通合伙)
更多信息请下载全文后查看。
聚合型受阻酚抗氧剂CPL的合成工艺优化

聚合型受阻酚抗氧剂CPL的合成工艺优化摘要:研究了以工业级双环戊二烯、对甲苯酚、甲基叔丁基醚为原料制备聚合型受阻酚抗氧剂CPL的合成工艺。
考察了催化剂种类和用量、反应物的物质的量配比、反应温度、反应时间等因素对合成CPL收率、熔点的影响,并提出了新的产品纯化方法。
关键词:聚合型受阻酚抗氧剂;双环戊二烯;对甲苯酚;甲基叔丁基醚聚合型受阻酚抗氧剂CPL,即对甲基苯酚一双环戊二烯一异丁基化树脂,是一种新型、高效、不变色的空间位阻聚合酚类抗氧剂,能溶于芳香族化合物,醇类、醚类等溶剂,不溶于水。
由于相对分子质量适中,具有耐热、抗抽出与树脂相容性好的特点,能应用于石油制品、食品工业、及医疗保健等,符合当前聚合型抗氧剂向高效、无毒、耐热、抗抽出、抗变色方向发展的趋势。
胡艳芳、朱新宝等以双环戊二烯酚型树脂及异丁烯为原料,考查了各种工艺条件对合成聚合型受阻酚抗氧剂的影响。
王家樑以对甲苯磺酸、磷酸、磷钼酸、磷钨酸作为催化剂,替代三氟化硼乙醚络合物以制备双环戊二烯酚型树脂,但受催化剂影响,颜色较深,副产物多。
Jonathan Simon Hill,Dong Jun对抗氧剂CPL 的合成工艺进行了优化,对反应物的物质的量比和反应温度进行了探究。
本文使用甲烷磺酸作为催化剂,使双环戊二烯与对甲苯酚先合成双环戊二烯酚型树脂,再在催化剂甲烷磺酸作用下与甲基叔丁基醚反应,生成聚合型受阻酚抗氧剂CPL,并对影响聚合型受阻酚抗氧剂CPL制备工艺的各因素及产品纯化工艺进行了研究。
1实验部分1.1 主要原料与仪器双环戊二烯、甲烷磺酸、甲基叔丁基醚、对甲酚、二甲苯、碳酸钠,均为工业级,金澳科技(湖北)有限公司;5% Pd/C,阿拉丁试剂(上海)有限公司。
WHF-O.5型高压反应釜,山东威海自控反应釜有限公司。
1.2 制备工艺1.2.1 双环戊二烯酚型树脂的制备在氮气保护下,往四口烧瓶中加入二甲苯、对甲酚,搅拌升温到140℃,常压蒸出原料中的水份。
- 1、下载文档前请自行甄别文档内容的完整性,平台不提供额外的编辑、内容补充、找答案等附加服务。
- 2、"仅部分预览"的文档,不可在线预览部分如存在完整性等问题,可反馈申请退款(可完整预览的文档不适用该条件!)。
- 3、如文档侵犯您的权益,请联系客服反馈,我们会尽快为您处理(人工客服工作时间:9:00-18:30)。
聚合型受阻酚抗氧剂CPL的合成工艺优化摘要:研究了以工业级双环戊二烯、对甲苯酚、甲基叔丁基醚为原料制备聚合型受阻酚抗氧剂CPL的合成工艺。
考察了催化剂种类和用量、反应物的物质的量配比、反应温度、反应时间等因素对合成CPL收率、熔点的影响,并提出了新的产品纯化方法。
关键词:聚合型受阻酚抗氧剂;双环戊二烯;对甲苯酚;甲基叔丁基醚聚合型受阻酚抗氧剂CPL,即对甲基苯酚一双环戊二烯一异丁基化树脂,是一种新型、高效、不变色的空间位阻聚合酚类抗氧剂,能溶于芳香族化合物,醇类、醚类等溶剂,不溶于水。
由于相对分子质量适中,具有耐热、抗抽出与树脂相容性好的特点,能应用于石油制品、食品工业、及医疗保健等,符合当前聚合型抗氧剂向高效、无毒、耐热、抗抽出、抗变色方向发展的趋势。
胡艳芳、朱新宝等以双环戊二烯酚型树脂及异丁烯为原料,考查了各种工艺条件对合成聚合型受阻酚抗氧剂的影响。
王家樑以对甲苯磺酸、磷酸、磷钼酸、磷钨酸作为催化剂,替代三氟化硼乙醚络合物以制备双环戊二烯酚型树脂,但受催化剂影响,颜色较深,副产物多。
Jonathan Simon Hill,Dong Jun对抗氧剂CPL 的合成工艺进行了优化,对反应物的物质的量比和反应温度进行了探究。
本文使用甲烷磺酸作为催化剂,使双环戊二烯与对甲苯酚先合成双环戊二烯酚型树脂,再在催化剂甲烷磺酸作用下与甲基叔丁基醚反应,生成聚合型受阻酚抗氧剂CPL,并对影响聚合型受阻酚抗氧剂CPL制备工艺的各因素及产品纯化工艺进行了研究。
1实验部分1.1 主要原料与仪器双环戊二烯、甲烷磺酸、甲基叔丁基醚、对甲酚、二甲苯、碳酸钠,均为工业级,金澳科技(湖北)有限公司;5% Pd/C,阿拉丁试剂(上海)有限公司。
WHF-O.5型高压反应釜,山东威海自控反应釜有限公司。
1.2 制备工艺1.2.1 双环戊二烯酚型树脂的制备在氮气保护下,往四口烧瓶中加入二甲苯、对甲酚,搅拌升温到140℃,常压蒸出原料中的水份。
再降温到80~90℃滴加催化剂甲烷磺酸。
搅拌均匀后,再开始滴加双环戊二烯(DCPD),滴加时间2h。
滴加完毕,升温至11O℃,继续反应7h,即可得到双环戊二烯酚型树脂。
1.2.2 聚合型受阻酚抗氧剂CPL的制备往中间产物双环戊二烯酚型树脂中再补加催化剂甲烷磺酸,通入氮气置换空气,搅拌均匀后,加热至55℃,滴加甲基叔丁基醚,滴加时间为2h,之后升温至80℃,反应4h。
反应完毕后,降至室温。
再向反应瓶中加入饱和食盐水,搅拌,静置分层除去催化剂甲基磺酸。
再依次使用5%的氢氧化钠溶液、饱和食盐水、清水将产物洗涤至中性。
1.2.3 聚合型受阻酚抗氧剂CPL的纯化将上述产物加入WHF-O.5型高压反应釜中,催化剂5%Pd/C的用量为原料质量分数的0.5%。
检测装置气密性良好后先用氮气排尽反应釜内空气,再用氢气置换釜内氮气。
在H。
压力1.5MPa,反应温度80℃条件下,反应2~4h,直到反应物料不再吸收氢气为止。
降温降压,用氮气排尽反应釜内氢气后开釜,取出物料,冷却后过滤回收催化剂。
滤液水洗三次分离有机相,减压蒸馏除去溶剂二甲苯,真空干燥,粉碎,得到白色粉末,即为聚合型受阻酚抗氧剂CPL。
2 结果与讨论2.1 双环戊二烯酚型树脂的制备2.1.1 催化剂的种类及选取催化聚合反应常采用路易斯酸及质子酸等作为催化剂。
本论文分别采用无水氯化铝、无水氯化锌、三氟化硼乙醚配合物、浓硫酸、甲烷磺酸、磷酸对缩和反应过程、中间产物进行考察(见表1)。
六种催化剂得到的产物颜色及性状均不相同。
无水氯化锌、无水氯化铝催化得到的产物为紫黑色的黏稠液体。
浓硫酸作为催化剂所得产品为黄色固体。
磷酸为催化剂时,整个反应并无多大变化。
三氟化硼乙醚配合物为催化剂的产物为紫黑色固体。
当使用甲基磺酸为催化剂时,反应进行顺利,经过后续处理即可得到性状良好的中间产品。
通过对比分析,无水氯化铝、无水氯化锌等催化剂所得产品的软化点低、颜色深、收率较低、不利于后续的异丁基化反应。
磷酸催化活性较弱,反应无法正向进行。
三氟化硼乙醚配合物作为催化剂,催化性能较强,与中间体树脂发生烷基化反应时,副产物较多。
浓硫酸催化时,虽然产品颜色较浅,软化点有所提升,但是产品性状及收率均达不到要求。
因此经过实验和比较,选取甲烷磺酸作为第一步缩合反应的催化剂,中间产品收率较高,颜色较浅,操作方便,后续反应处理也较为简单。
2.1.2 催化剂的用量对中间产品的影响使用甲烷磺酸作为催化剂,其用量以反应物的质量分数计,考察催化剂甲烷磺酸的用量对中间产品熔点的影响(见表2)。
由表2可知,当催化剂甲烷磺酸用量为1%时,中间产品的初熔点不高,产率也是最低。
随着催化剂甲烷磺酸用量的提升,中间产品的初熔点随之提升,收率也有较大改善。
但用量2%和2.5%时,中间产品的初熔点及收率变化不大。
即第一步缩合反应所用催化剂甲烷磺酸用量宜为2%。
2.1.3 反应温度对中间产品的影响双环戊二烯与对甲酚进行反应的同时往往伴随着副反应的发生,如DCPD 的阳离子自聚,DCPD的分解及分解后产物的自聚等,且温度对产品聚合度的影响也较大。
反应温度对中间产品初熔点、收率的影响见表3。
当温度较低时,反应速率较慢,且反应过程中,溶液黏稠度增加,反应不易进行,初熔点达不到中间产品的要求,收率也较低。
随着温度的增加,产品的初熔点和收率均有所增加。
温度超过110℃后,产品的熔程宽,跨度大。
这就意味着副产物增加,产品不纯,而且收率亦有所下降。
所以缩合反应的反应温度宜为110℃。
2.1.4 反应时间对中间产品的影响根据文献可知,为了消除双环戊二烯滴加过快产生的自聚影响,大部分实验中将双环戊二烯的滴加时间设置为2h。
因此在固定了催化剂的用量、反应温度和反应物的物质的量配比后,考察反应时间对中间产品的影响(见表4)。
由表4可知,随着反应时间的延长,产品收率有着较大增长,初熔点也随之增高,当反应时间为7h时,产品色泽较浅,初熔点符合要求;继续增加反应时间,收率下降,熔程拉长,中间产品颜色加深。
因此,选择反应时间为7h。
2.1.5 反应物的物质的量配比对中间产品的影响反应原料的物质的量配比是反应能否顺利进行的关键。
双环戊二烯在高温和和高浓度之下常常伴随着分解和自聚反应的进行,易导致产品的收率下降及出现不同的聚合度以致产品不纯。
反应物的物质的量配比对中间产品收率的影响见表5。
当对甲酚与DCPD的物质的量配比为4:1时,缩合反应无法进行,在催化剂和反应温度等条件固定的情况下,所得的双环戊二烯酚性树脂为红色液体,亦无法进行下一步反应。
当反应原料的物质的量配比为3:1时,所得树脂颜色较深,进行烷基化反应,得到的中间产物为极黏稠的液体。
反应物物质的量配比为3:2时,缩合反应所得树脂性状较好,颜色浅,软化点高,进行第二步烷基化反应后,中间产物初熔点符合要求,收率高。
当继续改变反应物的物质的量配比为5:4后,产品初熔点较低,且产品颜色偏黄,后续处理较困难,过量的对甲酚易造成原料的浪费。
因此,对甲酚与DCPD的物质的量配比为3:2。
2.2 烷基化反应阶段文献中报道,双环戊二烯酚型树脂与异丁烯进行烷基化反应即可得到目的产物CPL,但由于异丁烯为气体,储存、运输、使用均必须在高压条件下,因此,存在着一定的安全隐患。
在本工艺中,采用原料易得,便于储存的甲基叔丁基醚作为替代,对烷基化反应的催化剂甲烷磺酸的用量及滴加完毕后的反应时间予以研究。
2.2.1 催化剂用量对产品CPL的影响叔丁基甲醚的沸点为55.2℃,所以烷基化反应的初期温度最高也只能选取在55℃,催化剂为甲烷磺酸,用量以双环戊二烯对甲酚树脂的质量分数计。
考察在该温度下,再补加催化剂甲烷磺酸的不同用量对目的产物CPL熔点的影响见表6。
随着补加催化剂甲烷磺酸用量的增加,产品的初熔点随之升高。
补加催化剂甲烷磺酸用量为1.5%时,收率最高,且生成的树脂性状较好.颜色浅。
当补加催化剂甲烷磺酸用量继续时,产品CPL收率反而下降,产品为紫黑色固体,后续脱色困难。
因此,确定补加催化剂甲烷磺酸的用量为1.5%。
2.2.2 反应时间对产品CPL的影响采取滴加叔丁基甲醚的形式与双环戊二烯对甲酚树脂反应,补加催化剂甲烷磺酸用量为1.5%.滴加时间为2h,滴加完毕后升温至80℃继续反应。
考察了以上反应条件下,不同反应时间对产品CPI,的影响(见表7)。
当反应时间为1h时,产品CPL为紫红色黏稠液体,随着反应时间的增加,产品CPL的初熔点逐渐升高,产品收率亦有所提高。
当反应时间大于4h后,产品CPL熔点及收率均有所下降。
因此,确定反应时间定为4h。
2.3 聚合型受阻酚抗氧剂CPL的纯化目前国内合成的聚合型受阻酚抗氧剂CPL大部分都带有颜色。
但是日本开发的产品CPL,多为无色或是浅色,颜色的深浅会直接影响产品的使用范围。
因此,必须降低产品的颜色,当前解决方法主要为:一方面,在合成过程中,通过减少原料中的水分的含量和使用氮气保护以降低酚与空气的接触;另一方面,使用有效的脱色剂是必不可少的。
因此,实验考察了三种纯化方法对抗氧剂CPL 产品质量的影响:(l)直接脱色方式,分别用活性炭、活性白土脱色;(2)水蒸气蒸馏方式;(3)氢化方式,分别是水合肼还原法、锌粉十氯化铵还原法、Pd/C 催化加氢法。
结果表明:在合成树脂CPL的反应结束后,加入适量的活性炭恒温搅拌、脱色,过滤除去固体杂质,所得的产品的颜色没有明显的变化。
同样使用活性炭、活性白土进行脱色实验,发现合成树脂CPL的颜色有所降低,但是,很难达到浅色透明的程度,使用水蒸气蒸馏亦是如此。
当采取Pd/C催化加氢时,产品CPL为浅黄色半透明液体,降温降压之后,对物料予以过滤、水洗分离,待减压蒸馏去除溶剂后,干燥粉碎即可得到符合产品要求的白色粉末。
因此,产品CPL的纯化即使用Pd/C催化加氢的形式。
3 结论(l)以工业级双环戊二烯、对甲酚、叔丁基甲醚为原料合成聚合型受阻酚抗氧剂,优化了反应条件,得到了最佳的合成聚合型受阻酚抗氧剂CPL的条件。
双环戊二烯对甲酚树脂的制备:甲基磺酸为催化剂,用量为反应物总质量的2%,对甲酚与DCPD物质的量比为3:2,DCPD在80℃滴加2h,滴加完毕后110℃反应7h。
烷基化反应阶段:催化剂为甲基磺酸,其补加用量为双环戊二烯对甲酚树脂质量的1.5%,叔丁基甲醚与双环戊二烯对甲酚树脂物质的量比为3:2,叔丁基甲醚滴加温度为55℃,滴加完毕后80℃反应4h。
(2)采取Pd/C催化加氢方式对产品进行纯化处理,过滤、旋蒸去除溶剂后,干燥得到白色固体产品,初熔点105℃,平均相对分子质量在800以上。