模具设计规范
模具设计规范

模具设计规范一、模具工程代号:PG—顺送PB—连续开料BK—外形CP—外形及孔PC—冲孔NC—缺口加工BR—抽牙BN—押曲UB—U曲VB—V曲LB—L曲RB—R曲ZB—Z曲WB—W曲CL—卷外弯加工CB—复合弯曲DB—面押CK—窝合模HB—冲台DR—拉伸CT—分断TP—攻牙VM—折床SW—碰焊AW—烧焊PL—电镀PT—喷油HT—热处理RK—校正LV—直平RV—窝钉TB—镏披锋DG—除油PK—包装SS—丝印OT—其它二、产品图及展开图的绘制:要把客户的产品转化为设计所需的产品图。
比如:尺寸公差的调整,形状的修正等。
1.所有产品图纸尺寸需与电子图文件核对一遍。
确认产品图纸与电子图文件正确无误。
2.所有公差尺寸在图纸上用颜色笔作好标记,以便于审查、校对,且有助于自我记忆。
3.所有图形尺寸的公差调整,按其产品图纸所需加工精度要求适当调整。
例如下表:4.折弯尺寸公差调整,如尺寸公差标注在外面时,其公差需放在凸模上,母模按其尺寸调整实数做;如尺寸公差标注在内面时,其公差需放在母模上,凸模按其尺寸调整实数做。
5.设计者对图面有疑问时,应及时做好标记、并呈报上级主管共同商讨其对策。
例如:冲压件的工艺极限,图面的图形、注解及其尺寸等问题不清或有疑问等等,可向上级呈报说明其详细情况后,通过提出打合书、检讨依赖书、要望申请书等书面形式与客户联络。
其方式可采用FAX或E-mail转送、答复。
我公司优先采用FAX方式联络。
三、排样图1、首先要确定产品的毛刺方向,压延方向;产品的毛刺方向一般情况下由客户下决定:产品的压延方向当客户有特殊要求时按客户的要求来做;当客户无特别要求时,对各向同性的材质(SECC、SPCC、SPCE)来讲,应以材料的利用率为优先考虑,其产品的加工难易程度及生产稳定性面不需要考虑压延方向;对各向异性的材质(如SUS、铜材等)来讲,首先要考虑材质的纤维方向不可与折弯方向相平行,其次才考虑带料的稳定性及加工的容易程度。
模具设计规范及要点

模具设计规范及要点模具设计是制造业中非常重要的环节,它直接影响到产品的质量和生产效率。
为了确保模具设计的准确性和合理性,制定一系列的规范是非常必要的。
本文将介绍模具设计的规范及其要点。
一、模具设计规范的目的模具设计规范的目的是确保模具具备高质量和高效率的生产能力,并最大限度地减少模具使用过程中的故障和损耗。
通过遵守规范,可以提高模具的使用寿命,减少维修和更换成本,提高生产效率,降低生产成本,提升产品的质量。
二、模具设计规范的要点1.模具设计应符合产品的要求:模具设计必须根据产品的尺寸、形状、材料和数量要求来进行,确保模具可以完美地制造出符合产品要求的零件。
2.模具设计应考虑材料的选择和加工工艺:模具所选材料应具有足够的强度和硬度,以承受生产过程中的高负荷和磨损。
同时,模具的加工工艺应考虑到成本、时间和质量的平衡,确保成型过程的高效和精确。
3.模具设计应遵循安全和可靠性的原则:模具的设计应确保操作过程中的安全性,尽量减少操作人员的伤害和事故发生。
同时,模具的设计要保证其可靠性,能够稳定地工作,并且容易进行维护和修复。
4.模具设计应考虑到工装和夹具的需要:在模具设计过程中,应充分考虑到工装和夹具的配套需求,确保模具能够与其完美配合,提高生产效率和产品质量。
5.模具设计应简化结构:模具的设计应尽量简洁,避免复杂的结构,以减少制造成本和使用成本。
同时,简化结构也有利于操作和维护。
6.模具设计应具备可拆卸性:模具的设计应尽量满足零部件的可拆卸性,使得维护和更换变得容易。
这样可以减少停机时间,提高生产效率。
7.模具设计应合理确定尺寸公差:模具的设计应根据产品的尺寸要求合理确定公差,以确保模具制造出来的零件尺寸准确且符合要求。
8.模具设计应注意冷却系统的布置:模具的冷却系统设计应合理布置,以确保零件的快速冷却和缩短生产周期。
冷却系统的设计也要考虑到冷却介质的供应和排放。
9.模具设计应充分考虑排气和出渣:模具的设计应考虑到充分的排气和出渣,以防止铸件中产生气孔和杂质。
模具行位设计标准要求规范

模具行位设计标准要求规范模具行位设计标准要求规范主要包括以下几个方面:一、尺寸要求:模具行位的尺寸应符合国家标准或相关行业标准的要求。
包括行位的长度、宽度、高度、孔径等尺寸参数。
行位的尺寸应与相邻模具零件的尺寸保持一致,确保模具在装配的过程中能够正常配合、连接。
二、垂直度要求:模具行位的垂直度是指行位与模具的垂直度,也是指行位上下两个面的平行度。
行位的垂直度要求符合国家标准或相关行业标准的要求。
垂直度的要求主要是为了保证模具的精度和稳定性,使其在使用过程中不产生变形、偏斜等问题。
三、表面质量要求:行位的表面质量要求符合国家标准或相关行业标准的要求。
行位的表面应光滑、平整,不得有明显的裂纹、气孔、划痕等缺陷。
表面质量的要求主要是为了保证模具的精度和使用寿命,使其能够正常运行。
四、材料要求:模具行位的材料要求应符合国家标准或相关行业标准的要求。
行位的材料应具有一定的强度和耐磨性,能够承受模具在使用过程中的压力、冲击等力量。
材料的选择要根据具体的模具使用环境和工作条件来确定,确保模具的使用效果和寿命。
五、加工精度要求:模具行位的加工精度要求应符合国家标准或相关行业标准的要求。
行位的加工精度主要包括尺寸精度、形位公差、表面粗糙度等指标。
加工精度的要求主要是为了保证模具的精度和稳定性,使其能够满足产品的要求。
六、安装要求:模具行位的安装要求应符合国家标准或相关行业标准的要求。
行位的安装应牢固可靠,保证模具在使用过程中不会因为行位的松动而产生误差。
安装的过程中要注意行位与相邻模具零件的配合和对齐,确保模具的装配精度和稳定性。
以上是模具行位设计标准要求规范的一些主要内容,具体的标准要求还需要根据具体的模具类型、使用环境和产品要求来确定。
模具行位的设计标准要求规范能够保证模具的质量和性能,提高模具的使用效果和寿命。
同时,对于模具生产厂家和用户来说,严格按照标准进行设计和生产,有助于提高产品的竞争力和市场占有率。
模具设计规范

模具设计规范1.使用FUTABA标准模座结构组模座。
2.使用正钢或同规格标准模具零件、配件。
3.全部导销(GUIDEPIN),衬套(BUSHING)必需在尾端有凸型。
4.全部模具设计图面纸张尺寸需统一使用全开规格尺寸,并等核准后,才开始制作。
5.模具上成品部分加工时,应以成品图中尺寸公差的半值来做为加工公差,不得使用成品图上之公差来加工。
6.全部度量单位以英制为准,长度使用毫米,重量使用公斤,温度使用摄氏(C)。
7.压力以英制PSI为单位,1PSI=1磅/平方英寸=14.2 公斤/平方公分。
8.确认模厚,夹模板行程,顶出行程。
9.公母模四侧面吊模孔位置“A” 〃B〃板每一相邻两侧最少有一吊模孔,其他模板最少有一侧面有吊模孔。
10.四支导销中之任一支,必需做成偏心,即不与其他三支对称,以防止公、母模反向合模。
11.打印钢材规格及硬度於模仁底面。
12.详列材料表并标示材料与表面处理规格,并标示电热器瓦数规格与电压大小。
13.打印,编号全部模具零件。
14.模具两侧面应与装箱前以铁条固定,以免模面分开。
15.同一成品模穴超过一个穴时,应采用连续编号以便识别模穴。
16.在模座上需有一吊模孔於模具重心位置,以避免吊模时模具倾斜,并确定螺纹与深度足够负荷模重。
17.除模仁有大面积梯阶靠破外,均应装置模面锁定块(PARTINGLINELOCKS),18.肋片深度超过5mm时,需於肋底部加逸气销或以镶件制作,以利塑料充填。
19.以销子做平面靠破时,应将销子顶端加长伸入钢材内,避免销子顶面压损或变形。
20.成品重要处,应稍预留尺寸,避免加工尺寸过大而导致补焊。
21.模仁未经许可不准补焊。
22.在特别状况下以补焊修补模具时,应选用模具同材料做焊条,以免材质不同影响成品之外观及留下痕迹。
23.各项装配组立均应的确掌握公差,不得有敲击之痕迹留下。
24.全部的模板除分模面外,其余角落应倒角。
25.使用电热器之模具,均需附电路图以便生产单位正确接线。
模具设计规范

模具设计规范1.目的:为达成冲模设计、加工准确、通用,快速之目的,确保模具及样品品质,提高生产效率。
2.范围:适用于在厂内自行开发产品及客户委托设计的模具设计.3.定义:3.1冲压模具:利用其生产五金等冲压产品,适用于冲压机生产用的模具。
4.权责:权责内容详见模具设计流程图(请参考附件一)5.作业流程:5.1模具设计流程图(请参考附件一)6.作业说明:档名前加模具编号,如XXXXX—L01A,共用模用B表示,则在第一套完整图号后加互换产品之展开图,料带图..。
互换之零件等,编号为XXXXXB-L01A。
.XXXXXB-03等;复制模用N表示,若有多套,分别用N1,N2,N3.。
标件图为最后一张即第y张。
<图号>,<档名>统一。
建议:整套模具只能有一个总图,总图用XXXXX-ALL命名,所有图档都在总图里完成,确认无误后存出,尽量保持总图为最新版本。
注:除客户要求外,模具模号一般以产品料号为准.6.2.注:模板素材尺寸公差为+0。
3~+0。
5注:一般五金配件以伍全公司目录为标准.*1。
下模入子刀口到边距离>/=4。
0;建议下模入子比脱板入子单边大1。
0导料板>0。
5,脱板入子不用避位。
*2。
端子类刀口用两段式(8+17),上8.0用WC,下用SKD11,冲子用WC,刀口直线位1。
5斜1。
0度落屑对于特别小的冲子,刀口可直线位0.0斜0。
2度落屑.*3。
脱板入子挂肩均统一为4。
0。
*4。
入子大小不得小余4*5(过小不便于加垫片或敲出)。
*5。
零件之间滑动要求时,一定要放单边间隙,一般为0。
01。
*6. 敲击孔模座统一钻Φ5。
0,垫板钻Φ3。
5,特殊情况允许钻或割Φ2。
1。
*7.对于铁壳或铜壳,刀口做整体式,冲子刀口材料用SKD11/SKH9/ASP23HRC62,脱板刀口入子,及夹板入子浮升块用SKD11;成形冲子入子均用SKD11/SKH9/ASP23。
6.4.作图规范6.4.1.颜色:除虚线.中心线等特殊线为便在打印时以区别其粗细外,其余线均以随图层决定颜色,标注线之文字与指引线用绿颜色.当正式出图时,除标注.虚线.中心线等特殊线外,其余全部随图层色,图档设变时,将设变部位用其它颜色区分开来.6.4.2.图层:6.4.3.标注模板之销孔,导柱孔,入子框口,以3位小数标示磨床加工之尺寸,以3位小数标表铣床加工,落料孔,脱背板过孔,挂台,让位,其它非重要尺寸,以1位小数标示。
模压模具设计规范

模压模具设计规范模压模具是在模压工艺中起到关键作用的工具,其设计质量直接影响产品质量和生产效率。
因此,制定合理的模压模具设计规范对于提高生产效率、降低成本具有重要意义。
一、模具材料选择模具的材料选择直接关系到模具的使用寿命和稳定性。
通常情况下,模具材料应具有高硬度、高强度、耐磨损、耐腐蚀的特性。
常用的模具材料有工具钢、硬质合金等,根据具体使用需求选择合适的材料。
二、模具结构设计1.结构合理性:模具结构设计应考虑到产品成型过程中的力学特性,确保产品成型过程中不产生变形、裂纹等质量问题。
2.冷却系统设计:良好的冷却系统能够有效降低成型周期,提高生产效率。
因此,在模具设计中应合理设置冷却系统,保证模具温度均匀。
3.排气系统设计:排气系统设计不合理会导致气泡等缺陷的生成,影响产品表面质量。
因此,应合理设计排气系统,确保模具内气体顺利排出。
三、模具加工精度1.加工精度要求:模具加工精度对于产品尺寸精度和表面质量有重要影响,因此在加工过程中应严格执行设计要求。
2.使用高精度设备:选择高精度的加工设备对于保证模具加工精度至关重要,同时还应定期校准设备,保证加工准确度。
四、模具使用与维护1.模具使用注意事项:在使用过程中应根据具体产品材料和成型工艺要求选择合适的模具,并严格按照使用说明操作,避免造成不必要的损坏。
2.定期维护保养:定期对模具进行清洁、润滑和检查,发现问题及时修复,延长模具使用寿命。
五、模具质量检测1.工艺检测:在模具加工完成后,进行工艺检测,保证模具尺寸偏差在允许范围内。
2.使用寿命检测:定期对模具进行寿命检测,根据情况进行修复或更换,避免因模具使用寿命过期导致的质量问题。
综上所述,模压模具设计规范对于保证产品质量、提高生产效率至关重要。
只有严格遵循规范要求,不断优化模具设计和加工过程,才能更好地满足客户要求,提升企业竞争力。
模具设计规范
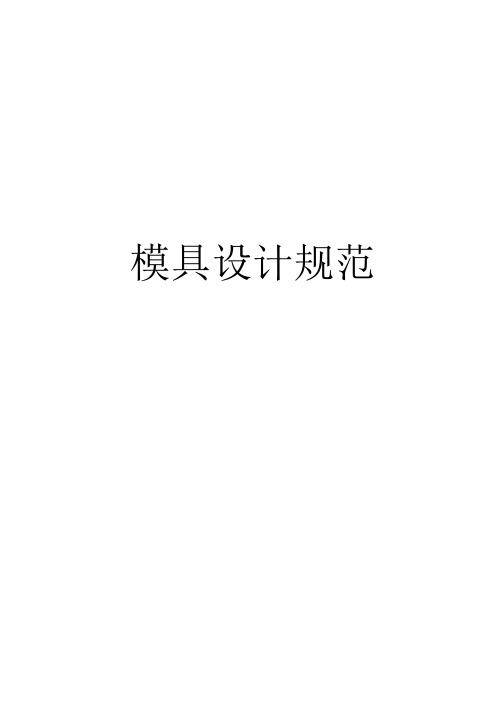
3
5 5
3.5
5 6
φ 3、φ 2.5、φ 2
φ 4、φ 5、φ 6、φ 7 φ 8 、 φ 9 、 φ 10 、 φ 12 、 φ 16 、 φ 20
d
d1+0.5
h
2.方式二:对于非DMG客户的模具顶杆止转及定位采用以下方式:
2.2
为了减少顶杆的加工量,并防止顶杆安装方向错误,特修订我公司顶杆 的杯头止转形式。改为杯头单面止转。设计尺寸见图2。 对于外单模具,若客户另有要求,按客户标准执行。无要求,则按新标 准执行。
模具设计规范
前言
• 为了满足设计及制造的要求, 指导设计工作,现将设计及制 造中应注意的问题加以整理。 待设计标准系统化后再行纳入。
•
海尔模具标准化办公室
一、冷却系统设计
1.1、模板冷却设计要求
* 三板模:要求水口板加冷却水路。 * 热流道模具:要求热流道板加冷却水 路。每个热嘴必须单独冷却。 * 对于模具长度超过1000MM的情况下, 底针板,底板必须加单独的冷却回路, 以保证针板与后模板温度一致。
*三板模倒锥形拉料杆:
三板模倒锥形拉料杆的作用主要是通过倒 扣力拉断点浇口.其设计参照:《标准件库》
*分流道拉料杆:
图5 分流道拉料杆设计
设计要点: (1)对于较长的分流道系统,应设计分流道拉 料杆.其主要作用是顶出分流道. (2) 分流道拉料杆的头部设有冷料井 , 深度 3MM 左右 , 目的为了分流道料把顶出过 程中起到导向作用,使料把顶出平衡.
以上两种形式在没有海尔模具的标准,对于没有特殊设计标准的模具均采用上述方式加工。
3.2、搭接流道设计
对于锥形流道加工在模具的两个零件上的情况,应考虑脱模, 将流道设计成如图3.1形式。一般C>0.2MM.
模具设计规范

模具设计规范随着制造工业的不断发展,模具在各个领域中的应用越来越广泛,模具设计的重要性也日益突显。
模具是产业中的重要生产工具,需遵守一定的设计规范。
本文将从模具设计规范的定义、需求和实现等方面进行阐述,以期能够更好地理解和应用模具设计规范。
一、模具设计规范的定义模具设计规范是指模具设计中遵守的标准、规程或约束条件,其主要目的是确保模具的可靠性、稳定性和高效性。
采用规范的模具设计可以有效地降低设计成本、提高生产效率和产品质量,同时还能提高准确度和安全性。
模具设计规范通常包括形状、尺寸、材料选用、加工等方面的规定,还包括模具安装、使用和维护方面的规范。
二、模具设计规范的需求1、提高模具制作效率模具是生产中不可缺少的工具,具有复杂的结构和制作工艺,设计的合理性直接影响制作工艺难度和制作周期。
制定规范可以使模具的制作效率得到提升,缩短制作周期,满足产量需求,降低制造成本。
2、保证模具质量模具制作质量直接决定了制品质量及生产效率,制定规范可以避免一些质量问题的出现,保障产品的准确度、一致性和稳定性,避免浪费资源,他们同时还可以避免模具在使用过程中出现损坏和断裂等情况,确保生产的顺利进行。
3、减少损耗模具使用过程中的损耗必不可免,但合理的规范可以让损耗最小化。
规范要求制定时明确材质、尺寸、结构等要素,能够避免无用设计,并较好地保护模具。
4、避免安全隐患模具在生产过程中承载较多的力与压力,这也增加了模具的使用风险。
制定规范可以让模具承受更大的负荷,使其在使用过程中更加安全可靠,避免意外事故的发生。
三、模具设计规范的实现1、规范标准针对不同行业,制定不同的模具设计规范标准,以保证满足每个行业的特定工艺和产量需求。
2、材料选择模具的材料需要有较好的抗腐蚀、抗磨损性能,并且具备良好的强度和硬度,可以承受生产过程中较大的压力。
同时,还要考虑材料的价格,选择性价比较高的材料。
3、设计细节需要注意的地方有很多,如模具的结构设计、表面处理、零件尺寸、空间利用等等。
- 1、下载文档前请自行甄别文档内容的完整性,平台不提供额外的编辑、内容补充、找答案等附加服务。
- 2、"仅部分预览"的文档,不可在线预览部分如存在完整性等问题,可反馈申请退款(可完整预览的文档不适用该条件!)。
- 3、如文档侵犯您的权益,请联系客服反馈,我们会尽快为您处理(人工客服工作时间:9:00-18:30)。
打印整套模具图纸 传图给CNC编程组
材料的订购
给主管审批
申查整套模具图纸
新产品检讨资料的制作
首次接到项目部的新产品3D图,根据客户提供的信息,对产品进行全方面的评估和修正。把开模所涉及的问 题点制作成如下图PPT文件格式的资料传达给客户,来进行商讨。(PPT档文件有现成模版可直接取用)
合议进胶点
合议分型线
990*1400 A=190 B=190 C=160
930*1400 A=190 B=190 C=160 1100*1550 A=190 B=190 C=160 1100*1550 A=190 B=190 C=160 1100*1640 A=200 B=190 C=160 1100*1640 A=200 B=190 C=160
非管控尺寸面
掏胶面
涂色面为玻璃面
涂色面为卡扣面
产品的刻字 日期章
客户的产品通常都要求有刻字内容:如产品的款型、料号、成型材料、产品类型(U、D、L、R)、回收 标志、还有穴号。日期章是大部分产品所必需有的。 产品的刻字内容我们优先考虑放在产品正面所能放置的面 上,若正面没有合适的位置才会考虑放在产品的侧面或者产品 的背面。刻字为减胶做一0.2mm深的沉台,刻凸字。如图样
模具设计人员工作规范
徐晓阳 编制
中粮地产腾讯工业厂
收到客户3D图 检讨资料为PPT档文件
项目部下发《新产品开模通知书》
检讨资料的制作
产品信息的说明 进胶点位置 分型线及产品出模斜度 顶出结构及横向抽芯结构 产品开模结构问题点分析 模胚的选择
发送给客户确认
设计2D结构图
模穴排位 浇注系统的设计 冷却系统的设计 顶出系统的设计 横向抽芯结构 其它模具辅助件的设计 产品分型线的设计 产品的出模斜度 产品的公差要求 排气系统
550*850 A=110 B=140 C=115 720*1320 A=175 B=190 C=140
720*1160 A=110 B=180 C=120 830*1120 A=175 B=180 C=140 830*1210 A=175 B=180 C=140
36寸整体中框
39寸整体中框 40寸整体中框 42寸整体中框 46寸整体中框
模胚及内模散件加工图
3D结构图设计完成之后,接下来的工序就要把所有的3D散件转为2D图。随后要出下面的图纸
【1】模仁内部的散件图:如前后模、行位镶件镶针、前后模镶件镶针、顶出件及模仁内部装配图; 【2】模胚散件图:如行位座、铲基、压条、耐磨板、导轨、契紧块、法兰等; 【3】模胚各板块的详细加工图:面板、分流板、垫板、AB板、方铁、顶针板和底板。
32寸上下中框 32寸左右中框 40寸上下中框 40寸左右中框 580*730 A=130 B=160 C=130 690*1250 A=175 B=190 C=140
42寸上下中框
42寸左右中框 46寸上下中框 46寸左右中框 26寸整体中框 29寸整体中框 32寸整体中框
720*1320 A=175 B=190 C=140
UG图层的规范
模具设计者需按右表规范图 层,便于后续改模和查图者都能 清楚各个部件所在,减少设计时 间,防止错误的发生。 注意:CAD中的零件图层要 和UG中零件的图层一一对应,零 件的命名是在图层的基础上:
前模+3
后模+4
90-95层
-Байду номын сангаас--------------
直顶、顶针
客户原版最新开模图纸(初次试模前只保留最新的一个就行) 模具最新开模图纸 有出模斜度(不管改过多少次模 此层始终保持最新的模 具产品) 客户设变图纸(一般没有出模斜度)顺序排列 若为几个产品出一套模的 此层可放置第二、三、四个产品 客户设变图纸(一般没有出模斜度)顺序排列(跟在该图后面) 放临时部件 特殊情况下可放置和相近图层同样的部件
27寸产品(缩水率) 1.0018 1.0016 1.0055
模穴排位前的准备工作
产品要镜向处理
找产品的最大外形中心线或容易取数的基准线
模胚选择参考类型
27寸上下中框 27寸左右中框
模胚的选用
一套模的完成时间往往是比较短的,这就要求在前期设计上的时间 能够尽量的压缩,来缓解模具制作上的时间。我们公司所生产的模具占的 99%都属于非标准型的模胚,且模胚规格大都超出了模胚厂的最大规格。 所以绘制模胚图是2D设计中的一个难点。 在之前的设计工作中,我们不段的积累实践经验,在每套新款型产品 的开模,都力图给它设计一套最佳的模胚规格以后续的不断使用。 右侧参考表中列举了大部分常用的尺寸规格(还在不段的完善中)。 若新开模产品有和之相同尺寸款型的,都可以直接调用其中的2D图纸,只 需少许修改。这样能给设计工作节省至少60%以上的设计时间: 2D结构图 模胚详细加工图 材料表 行位镶件运水螺丝图
分 类
充分检讨型模材料,硬度,精度,构造等是否与定制者之规格相符? 成形机之射出量,射出压力,合模压力是否充分? 模具是否能正确安装于指定使用的成形机上。 如螺丝位置,定位环,喷嘴半径R,注嘴孔径,顶出用孔位置及大小,型模大小及厚度等是否适当? 分模线位置是否适当? 是否会粘前模? 选用之顶出方法对成形品是否适当?顶针、扁顶、司筒、直顶、其它等。 顶针、司筒(尽量大些、顶在骨上)使用数量及位置是否适当? 顶辊孔数量要求是否OK? 司筒有无碰顶辊孔? 行位下边有顶针时,顶针板有无加行程开关? 运水大小,数量,位置是否适当? 运水孔有无撞顶针等? 有无按要求设计流道系统? 多腔模具是否入水均匀? 模图有无画反?(塑胶产品图有无作镜像) 塑胶产品在模具上有无明确基准位? 有无必要的技术要求? 尺寸标注是否足够,清晰,有无字母数字线条重叠现象? 三视图位置关系是否能对应,图面是否简洁明了? 唧咀、螺丝、顶针、运水、弹弓、撑头、定位块等位置是否正确? 胶位是否有太薄或太厚处,是否跟客户沟通进行修改? 有无修正塑胶产品图,使之有合理出模角度及擦位角度? 考虑塑胶产品公差是否有利于下次修正(一般是要有利于加胶)?
散件图如:行位座、铲基、压条、契紧块、导轨、耐磨板和法兰等
48寸整体中框
模胚的选用
新开模的有些产品, 公司要考虑它的成本、量产数量等,至此会用一些废旧的模胚二次利用。
1〉中框类模具
2〉线夹类模具
可利用唯冠(C系列)和其它客户已宣布报废的模具
可利用比亚迪(L系列)和其它客户已宣布报废的模具
2D标题框
产品的日期章我们优先考虑放在产品正面所能放置的面上, 若正面没有合适的位置才会考虑放在产品的背面或者产品的侧 面。刻字为减胶做一0.3mm深的沉台。如图样
产品的公差要求
产品的公差要求是产品在装配时所能承受的范围值。生产出来外观再好的产品如果尺寸不符合公差的范 围值也等于报废产品。 为了能使产品符合 公差值且又不会给模具 制作上增加加工量,我 们在前期设计工作上对 主要的管控尺寸进行预 放余量:能减胶的不要 加胶能追加工的不要烧 焊 右图为每个中框 产品所必有的几个主 要管控尺寸
产品图,侧壁高度不平。
产品分型面的设计直接影响着 加工难度和成型产品好坏。具体可 以从以下几点分析:
加工设备的工作量 FIT时的工作量 成型产品的品质和美观程度 成型产品的装配效果
原始设计方法
改进了设计方法
降低了分型面取消了擦穿凸位
此类型的产品通过降低分型 面完全避免的进胶点处沉台的出 现,给加工师傅带来了极大的方 便,成型产品更加不会出现披峰。
瑞议机种缩水率
大于31.5寸产品(缩水率) 1.0035 1.004 1.0035 1.006
1.004 1.004 1.004 1.006
21.5寸产品(缩水率) 分体中框LR ( PPO+PS+25%GF) 分体中框UD ( PPO+PS+25%GF) 长胶条 1.0018 1.0016 1.005
2D排位 选择合适模胚尺寸(寻找之前可套用的模胚) 准备适合该套模具的标准件方便以后直接取用
2D结构图的设计
模穴排位
浇注系统的设计
冷却系统的设计
顶出系统的设计
横向抽芯结构(即行位) 其它模具辅助件的设计
模穴排位前的准备工作 --- 缩水率
一般产品的缩水率
小于等于31.5寸产品(缩水率) 全中框(PC+10%GF) 分体中框LR (PC+10%GF) 分体中框UD (PC+10%GF) 线夹(PC)
<150 0.5
150 <料长<400 1.00
400 <料长<600 1.50
600 <料长<1000 2.00
模仁料的高度方向根据实际情况放1~2mm
热流道设计
排位结束后,且也订购了模仁大料,还有一项任务就是把设计好的产品进胶点位置图和长度,整理后另 存一份dwg格式文件通过邮件经过审查后发送给热流道公司进行热流道系统设计。这期间也大概需要1天~1.5 天的时间。 常用的热流道公司有豪润讷、鑫昊、马斯特等几家。由于厂家不同,所设计的热流道系统或多或少会有 些差异,用图时特别注意以下几点:
参考值
CELL玻璃位 OPEN区 侧壁卡扣位 其它位置 单边预留0.1mm 单边预留0.1~0.15mm 卡面预留0.05mm 参考客户电子图档
外加工
3D结构图构建已接近尾声,此时所订购的模仁大料和热流道图都已回来。模具的实际加工就要开始了。 首先要打印出做好的模仁加工图外发加工:如下 前后模仁螺丝运水加工图 前后模仁镶件镶针穿丝孔加工图 后模仁顶针孔加工图
2D出图标题框标准填法 根据图纸的大小,标题框可做相应的比例放大缩小 加工处填写区
开模信息区
修改模纪录区
模仁料的申购
排位结束后,接下来的工作就要3D分模了,这大约需要1天~1.5天的时间。为了加快进度,可根据以上 的排位并结合产品结构的实际情况,填写申购单订购模仁大料,因为这也需要大概1天~1.5天的时间,正好弥 补之时间空缺。