PQF连轧机轧辊断裂的形成原因分析
轧辊爆裂原因

轧辊爆裂是轧制生产中常见的一种失效形式,可能会导致严重的生产事故和经济损失。
以下是几种可能导致轧辊爆裂的原因:
1. 轧辊材质不适:轧辊材质应该具有高的强度、韧性和耐磨性。
如果材料不符合轧辊的使用要求,则会引起轧辊疲劳失效和裂纹扩展,导致轧辊爆裂。
2. 轧辊表面缺陷:轧辊表面缺陷、裂纹、凹坑等缺陷也可能导致爆裂。
这些缺陷将在轧制过程中扩展并使轧辊破裂。
3. 轧辊使用过程中温度过高:过高的轧辊表面温度会使轧辊产生变形和热疲劳裂纹,最终导致轧辊爆裂。
4. 轧辊使用寿命过长:轧辊在使用过程中会不可避免地出现疲劳损伤和磨损,长期使用可能导致轧辊的强度减小,出现裂纹和爆裂。
5. 非正常操作:轧辊在使用过程中需要严格遵循规定的操作程序和参数范围。
如果操作不当,例如过多受力或者运转速度过快,就有可能导致轧辊疲劳损伤和爆裂。
综上所述,预防轧辊爆裂需要严格控制轧辊的材质、缺陷、温度、使用寿命和操作规范,定期检测和维修轧辊以及合理调整轧制过程参数等措施。
热轧轧辊剥落或断裂的原因及预防方法探究

热轧轧辊剥落或断裂的原因及预防方法探究热轧轧辊作为热轧设备中重要的组成部分,其质量直接影响到产品质量和生产效率。
在生产中,往往会出现轧辊剥落或断裂的情况,造成了生产效率低下和安全隐患,因此研究热轧轧辊剥落或断裂的原因及预防方法具有重要的实际意义。
1. 轧辊表面损伤导致轧辊剥落或断裂在轧辊使用过程中,出现轧辊表面损伤容易导致轧辊剥落或断裂。
这种损伤包括表面裂纹、划痕、磨损、腐蚀等,这些损伤会进一步扩大,最终导致轧辊剥落或断裂。
轧辊材质好坏直接影响到轧辊的使用寿命和质量。
如果轧辊的材质不够坚固耐用,那么在热轧过程中会出现轧辊变形、疲劳、裂纹等问题,将极大影响热轧产品质量。
热轧设备的操作不规范也容易导致轧辊剥落或断裂。
例如温度控制不当、轧辊调整不到位等等,都会在热轧过程中产生不同程度的影响,最终导致轧辊剥落或断裂。
热轧工艺参数是热轧过程中必须严格控制的参数,如果热轧工艺参数不合适将会直接影响到轧辊的寿命和使用效果。
例如,轧制过程中的拉伸率、轧制力、速度等参数不合适,都将导致轧辊剥落或断裂。
1. 轧辊材质的优化优化轧辊材质可以提高轧辊的抗拉、抗压、抗疲劳等性能。
特别是在硬度和韧性之间的平衡上,选择合适的轧辊材料可大大提高轧辊的使用寿命。
2. 加强对轧辊的检测热轧轧辊在使用过程中应每隔一些周期对轧辊进行检测,及时发现轧辊损伤和裂纹等问题并进行处理,避免因轧辊的损坏而影响到生产和产品质量。
3. 热轧设备的维护针对热轧设备操作不规范等问题,应加强设备维护,保持轧辊的良好状态。
定期做好轧辊的维护与更新,及时清理轧辊附着的物质,避免附着物进一步侵蚀轧辊表面。
4. 控制热轧工艺参数对于热轧工艺参数不合适问题,应严格控制热轧温度、轧制力、速度等参数。
调整工艺参数能够有效避免轧辊的剥落或断裂。
总之,对于热轧轧辊剥落或断裂问题,合理地选择轧辊材质,加强轧辊的检测和维护,规范热轧设备操作,严格控制热轧工艺参数,是预防轧辊剥落或断裂的有效方法。
热轧轧辊剥落或断裂的原因及预防方法探究
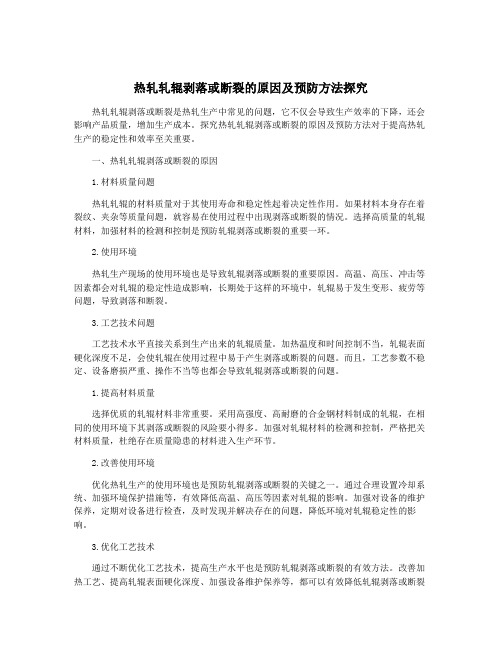
热轧轧辊剥落或断裂的原因及预防方法探究热轧轧辊剥落或断裂是热轧生产中常见的问题,它不仅会导致生产效率的下降,还会影响产品质量,增加生产成本。
探究热轧轧辊剥落或断裂的原因及预防方法对于提高热轧生产的稳定性和效率至关重要。
一、热轧轧辊剥落或断裂的原因1.材料质量问题热轧轧辊的材料质量对于其使用寿命和稳定性起着决定性作用。
如果材料本身存在着裂纹、夹杂等质量问题,就容易在使用过程中出现剥落或断裂的情况。
选择高质量的轧辊材料,加强材料的检测和控制是预防轧辊剥落或断裂的重要一环。
2.使用环境热轧生产现场的使用环境也是导致轧辊剥落或断裂的重要原因。
高温、高压、冲击等因素都会对轧辊的稳定性造成影响,长期处于这样的环境中,轧辊易于发生变形、疲劳等问题,导致剥落和断裂。
3.工艺技术问题工艺技术水平直接关系到生产出来的轧辊质量。
加热温度和时间控制不当,轧辊表面硬化深度不足,会使轧辊在使用过程中易于产生剥落或断裂的问题。
而且,工艺参数不稳定、设备磨损严重、操作不当等也都会导致轧辊剥落或断裂的问题。
1.提高材料质量选择优质的轧辊材料非常重要。
采用高强度、高耐磨的合金钢材料制成的轧辊,在相同的使用环境下其剥落或断裂的风险要小得多。
加强对轧辊材料的检测和控制,严格把关材料质量,杜绝存在质量隐患的材料进入生产环节。
2.改善使用环境优化热轧生产的使用环境也是预防轧辊剥落或断裂的关键之一。
通过合理设置冷却系统、加强环境保护措施等,有效降低高温、高压等因素对轧辊的影响。
加强对设备的维护保养,定期对设备进行检查,及时发现并解决存在的问题,降低环境对轧辊稳定性的影响。
3.优化工艺技术通过不断优化工艺技术,提高生产水平也是预防轧辊剥落或断裂的有效方法。
改善加热工艺、提高轧辊表面硬化深度、加强设备维护保养等,都可以有效降低轧辊剥落或断裂的风险。
培训操作人员,提高其技术水平,增强操作规范性,也是有效预防轧辊剥落或断裂的方法之一。
4.加强监控和管理加强对生产过程的监控和管理,及时发现并处理存在的问题也是预防轧辊剥落或断裂的关键。
轧辊断裂

轧辊断裂时轧辊损坏的一种严重形式,而且处理时间长,影响生产。
轧辊断裂的原因有两种:一种内在原因,由于轧辊本身的内在缺陷造成,如夹杂等造成断裂;另一种是外在原因,由于轧制工艺条件和使用造成,如超载等造成断裂。
具体分析:
1残余应力及热冲击断裂。
轧制开始,轧辊与高温轧件接触,在轧制过程,轧辊表面温度高,而芯部温度低,在芯部产生合成拉应力,当超过极限时,芯部产生裂纹和断辊。
避免这种断裂,轧辊使用时应预热轧辊,并保持良好的冷却条件,严禁闭水轧制,降低内外层温度梯度;普通轧辊使用前应用半年左右时效期,以降低轧辊内应力,使用后的热轧辊应及时缓冷避免再生热应力。
2疲劳裂纹扩展为断裂。
轧辊上的裂纹受弯曲应力的作用,会沿着一条较深的裂纹扩展,继续轧制裂纹会迅速扩展,达到极限,会发生断辊,预防该问题,最重要的是保证轧辊有一定的重车量,并采取必要的检测手段,并对轧辊滚压强化进行表面处理,提高轧辊疲劳强度。
3其它原因。
如夹杂、非正常组织、残余奥氏体量过高、偏析等。
预防以上问题,应采用高质量的轧辊,并对采用的轧辊提出夹杂、非正常组织、残余奥氏体、偏析等方面的量化具体要求。
4使用原因。
轧制钢类强度过高,或低温钢、黑头钢等易造成事故。
另一方面,轧制盲目加大压下量以减少道次,闭水轧制后,过快给冷却水,或冷轧薄板时,轧辊压靠力过大,扭矩大于轧制力矩,启动轧机可能扭断轴头。
故而,制定操作规程时应充分考虑各种诱因,制定明确到位,同时操作人员应严格遵守标准化操作。
(。
轧辊失效方式及其原因分析

轧辊失效方式及其原因分析轧机在轧制生产过程中,轧辊处于复杂的应力状态。
热轧机轧辊的工作环境更为恶劣:轧辊与轧件接触加热、轧辊水冷引起的周期性热应力,轧制负荷引起的接触应力、剪切应力以及残余应力等。
如轧辊的选材、设计、制作工艺等不合理,或轧制时卡钢等造成局部发热引起热冲击等,都易使轧辊失效。
轧辊失效主要有剥落、断裂、裂纹等形式。
任何一种失效形式都会直接导致轧辊使用寿命缩短。
因此有必要结合轧辊的失效形式,探究其产生的原因,找出延长轧辊使用寿命的有效途径。
1 、轧辊剥落(掉肉)轧辊剥落为首要的损坏形式,现场调查亦表明,剥落是轧辊损坏,甚至早期报废的主要原因。
轧制中局部过载和升温,使带钢焊合在轧辊表面,产生于次表层的裂纹沿径向扩展进入硬化层并多方向分枝扩展,该裂纹在逆向轧制条件下即造成剥落。
1.1 支撑辊辊面剥落支撑辊剥落大多位于轧辊两端,沿圆周方向扩展,在宽度上呈块状或大块片状剥落,剥落坑表面较平整。
支撑辊和工作辊接触可看作两平行圆柱体的接触,在纯滚动情况下,接触处的接触应力为三向压应力。
在离接触表面深度为 0.786b 处 ( b 为接触面宽度之半 ) 剪切应力最大,随着表层摩擦力的增大而移向表层。
疲劳裂纹并不是发生在剪应力最大处,而是更接近于表面,即在 Z 为 0.5b 的交变剪应力层处。
该处剪应力平行于轧辊表面,据剪应力互等定理,与表面垂直的方向同样存在大小相等的剪应力。
此力随轧辊的转动而发生大小和方向的改变,是造成接触疲劳的根源。
周期交变的剪切应力是轧辊损坏最常见的致因。
在交变剪切应力作用下,反复变形使材料局部弱化,达到疲劳极限时,出现裂纹。
另外,轧辊制造工艺造成的材质不均匀和微型缺陷的存在,亦有助于裂纹的产生。
若表面冷硬层厚度不均,芯部强度过低,过渡区组织性能变化太大,在接触应力的作用下,疲劳裂纹就可能在硬化过渡层起源并沿表面向平行方向扩展,而形成表层压碎剥落。
支撑辊剥落只是位于辊身边部两端,而非沿辊身全长,这是由支撑辊的磨损型式决定的。
辊环裂的原因

辊环槽裂及破碎的原因分析及控制措施
辊环槽裂及破碎,会给生产及准备工作造成困扰,影响企业经济效益提高,需要分析,并采取相应措施.
1破碎及槽裂原因。
1)堆钢造成辊环突然停止转动,红钢和辊环产生面接触,辊环内部受到不同的热应力,产生热裂。
2)轧制中,导卫松动,导卫和辊环间存在摩擦,辊环沿周围方向过热,在辊环表面产生热裂纹。
3)冷却效果差,辊环过热受到大的热应力,导致辊环轧槽处产生热裂纹。
4)辊环安装过紧,张应力过大使辊环发生径向裂纹。
装配过松,锥套与辊环产生滑动,造成接触面磨损,会局部应力集中而损坏。
2控制措施
1)修磨时,微裂纹要车削干净,对辊环的检验强度提高,同时对破损大,损坏严重的辊环要直接报废处理。
2)导卫上面加装螺栓和螺母,将螺栓顶在辊环前的水分配器上,在轧制中,导卫底座螺母松动时,导卫不会和辊环发生滑动接触。
3)冷却水控制,水温控制在25℃以下。
冷却水喷水方向为径向,与辊环旋转方向成15-30度,谁不会散射或呈雾状,而是直接喷入轧槽。
4)辊环安装压力规范化。
多次测试,找出规范的压力值,防止安装过松或过紧,5)制定合理的轧槽吨位,根据钢种的不同,确定合理的轧机负荷。
6)辊环要有较高的耐磨性和抗热龟裂性,以保证棒、线材良好的尺寸公差和表面光洁度;此外确保辊环的匹配的型号一致性。
轧制过程中断辊原因
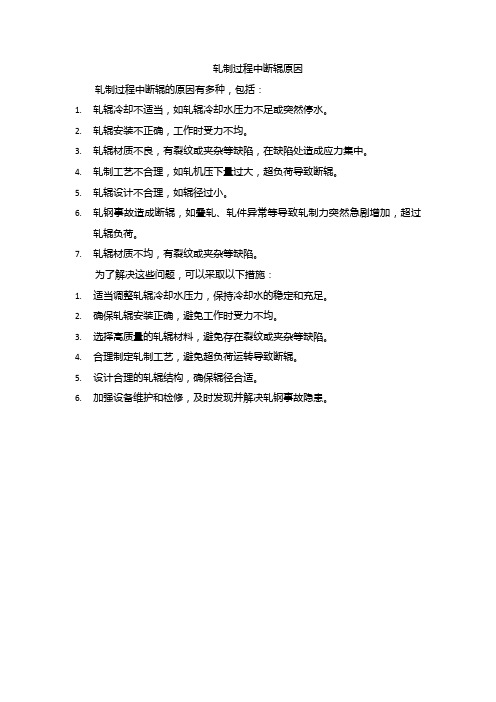
轧制过程中断辊原因
轧制过程中断辊的原因有多种,包括:
1.轧辊冷却不适当,如轧辊冷却水压力不足或突然停水。
2.轧辊安装不正确,工作时受力不均。
3.轧辊材质不良,有裂纹或夹杂等缺陷,在缺陷处造成应力集中。
4.轧制工艺不合理,如轧机压下量过大,超负荷导致断辊。
5.轧辊设计不合理,如辊径过小。
6.轧钢事故造成断辊,如叠轧、轧件异常等导致轧制力突然急剧增加,超过
轧辊负荷。
7.轧辊材质不均,有裂纹或夹杂等缺陷。
为了解决这些问题,可以采取以下措施:
1.适当调整轧辊冷却水压力,保持冷却水的稳定和充足。
2.确保轧辊安装正确,避免工作时受力不均。
3.选择高质量的轧辊材料,避免存在裂纹或夹杂等缺陷。
4.合理制定轧制工艺,避免超负荷运转导致断辊。
5.设计合理的轧辊结构,确保辊径合适。
6.加强设备维护和检修,及时发现并解决轧钢事故隐患。
轧机上断辊的原因分析
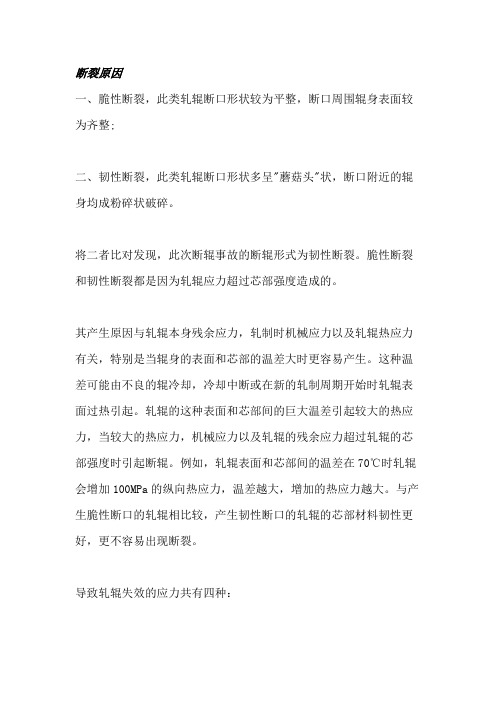
断裂原因一、脆性断裂,此类轧辊断口形状较为平整,断口周围辊身表面较为齐整;二、韧性断裂,此类轧辊断口形状多呈"蘑菇头"状,断口附近的辊身均成粉碎状破碎。
将二者比对发现,此次断辊事故的断辊形式为韧性断裂。
脆性断裂和韧性断裂都是因为轧辊应力超过芯部强度造成的。
其产生原因与轧辊本身残余应力,轧制时机械应力以及轧辊热应力有关,特别是当辊身的表面和芯部的温差大时更容易产生。
这种温差可能由不良的辊冷却,冷却中断或在新的轧制周期开始时轧辊表面过热引起。
轧辊的这种表面和芯部间的巨大温差引起较大的热应力,当较大的热应力,机械应力以及轧辊的残余应力超过轧辊的芯部强度时引起断辊。
例如,轧辊表面和芯部间的温差在70℃时轧辊会增加100MPa的纵向热应力,温差越大,增加的热应力越大。
与产生脆性断口的轧辊相比较,产生韧性断口的轧辊的芯部材料韧性更好,更不容易出现断裂。
导致轧辊失效的应力共有四种:一、制造过程中的残余应力;二、轧制过程中的机械应力;三、轧制过程中轧辊的组织应力;四、轧辊内外温差造成的热应力。
如果是因为制造残余应力过大产生断裂,断辊通常发生在轧辊初始上机使用的前几次,且为开轧的前几块轧材。
此次断裂的轧辊已经上机轧制了四次,工作层消耗了14mm,因此不应是因制造残余应力形成的断裂。
如果是因为机械应力产生的断裂,需要很大的机械应力。
经粗略计算,如此大截面的高铬铸钢轧辊若被机械应力拉断,则需要100MN 以上的拉力,对于该轧辊工作的轧机来说这是不可能的。
轧辊受力最大的部位是传动端辊颈,如果材料的力学性能指标不足,正常轧制情况下首先损坏的是传动端辊颈。
从实际轧制和断辊情况来看,不是由于机械应力造成辊身断裂。
对组织应力影响最大的就是外层组织中残余奥氏体含量。
残余奥氏体在轧制温度,轧制压力和水冷的交变作用下,发生奥氏体向马氏体或贝氏体的转变,由于奥氏体的比容小,而马氏体的比容大,因而在组织转变的过程中伴随着体积的膨胀,会致使轧辊的工作层产生更大的压应力,芯部产生更大的拉应力,芯部应力一旦超过材料的强度,必然造成轧辊断裂。
- 1、下载文档前请自行甄别文档内容的完整性,平台不提供额外的编辑、内容补充、找答案等附加服务。
- 2、"仅部分预览"的文档,不可在线预览部分如存在完整性等问题,可反馈申请退款(可完整预览的文档不适用该条件!)。
- 3、如文档侵犯您的权益,请联系客服反馈,我们会尽快为您处理(人工客服工作时间:9:00-18:30)。
第4 0卷第 1 期
2 0 1 4年 2月
包
钢
科
技
Vo 1 . 4 0, No . I
S c i e n c e a n d T e c h n o l o g y o f B a o t o u S t e e l
F e b r u a r y , 2 0 1 4
K e y w o r d s : P Q F ; o r l l s ; r o l l i n g r e d u c t i o n ; m i c r o t e n s i o n r o l l i n g m e t h o d
在内蒙古包钢 钢联 股份有限公 司无缝钢管 厂 1 5 9 m m 生产线 连 轧机组 刚 投 产不 久 , 发 现 轧 辊频 繁 断裂 , 为 有效 减少 轧辊 断裂 , 无缝 厂 对轧 辊表 面形
摘
要: 文章分析 了 P Q F 连 轧机前三架轧辊表面过早老 化磨损及轧 辊断裂 的原 因。根据现 场实际情 况 , 以轧制运
行状态 、 轧辊表面老化磨损 的情况 、 轧辊断裂 的形 态为依据 , 制定 了 P Q F连轧机微 张力轧制 法 , 减 少轧辊 老化及 断 裂, 提高轧辊寿命 。
f r a c t u r e o f r o i l s , w h i c h c o u l d ma k e t h e a g i n g a n d f r a c t u r e o f mi l s r e d u c e d a s we l l a s s e r v i c e l i f e o f r o i l s i mp ov r e d 。
P Q F连 轧机 轧辊 断裂 的形 成 原 因分 析
郭 ‘ 志 , 考 然 , 孟庆飞
( 1 . 太原科技 大学材料与工程 Nhomakorabea院, 山西 太原 0 3 0 0 2 4 ; 2 .包钢 ( 集 团) 公 司技 术质 量 部 , 内蒙古 包头 0 1 4 0 1 0 ;
3 内蒙古 包钢 钢联 股份 有 限公 司无缝钢 管厂 , 内蒙古 包头 0 1 4 0 1 0 )
mi l l i s f o r mu l a t e d b a s e d o n t h e o p e r a t i n g s t a t e o f r o l l i n g, s i t u a t i o n s o f a g i n g a n d w e a l " f o r r o l l s u r f a c e a s we l l s a or f ms or f
Gu n Z h i , - ,K AO Ra n 。
,
ME N G Q i n g— f e i 。
( 1 . S c h o o l o fMa t e r i a l s a n d E n g i n e e r i n g, T a i y u a n U n i v e r s i t y fS o ci e n c e a d n T e c h n o l o g y , T a i y u a n 0 3 ( X P - 4 , S h a n x i , C h i n a ;
关键词 : P Q F ;  ̄ L 辊; 压 下量 ; 微张力轧 制法 中 图分类号 : T G 3 3 5 . 7 文献标识码 : B 文章编号 : 1 0 0 9— 5 4 3 8 ( 2 0 1 4 ) O 1— 0 0 3 5— 0 4
Ca u s e An a l y s i s o n F r a c t u r e o f R o l l s f o r P QF C o n t i n u o u s Mi l l
f r a c t u r e o f r o l l s a r e a n a l y z e d . A c c o r d i n g t o t h e a c t u a l s i t u a t i o n s a t i f e l d , t h e mi c r o t e n s i o n r o l l i n g me t h o d f o r P Q F c o n t i n u o u s
3 . S e a m l e s s T u b e P l a n t fS o t e e l U n i o n C o .L t d .o fB a o t o u S t e e l ( G r o u p ) C o r p 。 , B a o t o u 0 1 4 0 1 0 , N e i M o gg n o l , C h i a) n
A b s t r a c t ; I n t h e p a p e r , t h e c a u s e s t h a t t h e i f r s t t h r e e r o i l s o f P Q F c o n t i n u o u s mi l l a g e a n d w e a r e a r l i e r a s w e l l a s t h e