astm-a967-01e1 不锈钢部件化学钝化处理的标准规范
美标标准

评定在沸腾的氯化镁溶液中金属及其合金的抗应力腐蚀断裂的一般方法
39
ASTM G41-90(94)
测定金属在热盐环境下应力断裂敏感性的一般方法
40
ASTM G44-99
在3.5%氯化钠溶液中交替浸渍法评定金属及合金的抗应力腐蚀破裂的一般方法
41
ASTM G46-94
局部腐蚀的检测和评定
腐蚀场所或高温下使用的焊接大口径奥氏体钢管
10
ASTM A480/A480M-03
平轧不锈和抗热钢板材﹑薄板材和带材通用要求技术规范
11
ASTM A484/A484M-03
不锈和抗热钢棒﹑钢坯和锻件
12
ASTM A450/A450M-04
碳素铁素体和奥氏体合金钢管
13
ASTM A511-04
无缝不锈钢机械管件的技术规范
42
ASTM G48-03
用氯化铁溶液测定不锈钢及有关合金耐斑点腐蚀及裂隙腐蚀的试验方法
43
ASTM G78-95
海水及其它含氯化物的水文环境中铁基和镍基不锈合金的裂隙腐蚀试验
44
ASTM G85-02
改进的盐喷雾(物化)试验
纵向焊接管的超声检测
24
ASTM E309-95
用磁刨和法做管状钢产品的涡流检验
25
ASTM E340-00
金属和合金宏观腐蚀的测试方法
26
ASTM E381-98
钢制品(包括棒﹑方钢坯﹑大方坯和锻件)的宏观腐蚀测试检查和评定
27
ASTM E384-99
材料显微硬度的试验方法
28
ASTM E407-99
7
ASTM A967-01
不锈钢酸洗与钝化处理规范
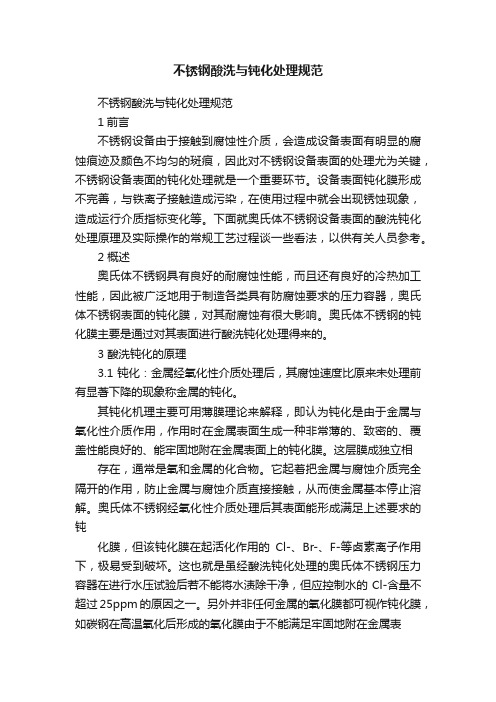
不锈钢酸洗与钝化处理规范不锈钢酸洗与钝化处理规范1前言不锈钢设备由于接触到腐蚀性介质,会造成设备表面有明显的腐蚀痕迹及颜色不均匀的斑痕,因此对不锈钢设备表面的处理尤为关键,不锈钢设备表面的钝化处理就是一个重要环节。
设备表面钝化膜形成不完善,与铁离子接触造成污染,在使用过程中就会出现锈蚀现象,造成运行介质指标变化等。
下面就奥氏体不锈钢设备表面的酸洗钝化处理原理及实际操作的常规工艺过程谈一些看法,以供有关人员参考。
2 概述奥氏体不锈钢具有良好的耐腐蚀性能,而且还有良好的冷热加工性能,因此被广泛地用于制造各类具有防腐蚀要求的压力容器,奥氏体不锈钢表面的钝化膜,对其耐腐蚀有很大影响。
奥氏体不锈钢的钝化膜主要是通过对其表面进行酸洗钝化处理得来的。
3 酸洗钝化的原理3.1钝化:金属经氧化性介质处理后,其腐蚀速度比原来未处理前有显著下降的现象称金属的钝化。
其钝化机理主要可用薄膜理论来解释,即认为钝化是由于金属与氧化性介质作用,作用时在金属表面生成一种非常薄的、致密的、覆盖性能良好的、能牢固地附在金属表面上的钝化膜。
这层膜成独立相存在,通常是氧和金属的化合物。
它起着把金属与腐蚀介质完全隔开的作用,防止金属与腐蚀介质直接接触,从而使金属基本停止溶解。
奥氏体不锈钢经氧化性介质处理后其表面能形成满足上述要求的钝化膜,但该钝化膜在起活化作用的Cl-、Br-、F-等卤素离子作用下,极易受到破坏。
这也就是虽经酸洗钝化处理的奥氏体不锈钢压力容器在进行水压试验后若不能将水渍除干净,但应控制水的Cl-含量不超过25ppm的原因之一。
另外并非任何金属的氧化膜都可视作钝化膜,如碳钢在高温氧化后形成的氧化膜由于不能满足牢固地附在金属表面的要求而不能充作钝化膜。
3.2 对于奥氏体不锈钢一般采用氧化性强的以硝酸为主剂的溶液来进行处理,为确保钝化处理的效果,在钝化前先对被钝化表面进行酸洗处理。
整个处理过程就称为酸洗钝化处理,简称酸洗钝化。
4 酸洗液、钝化液及酸洗膏配方酸洗液:20%硝酸+5%氢氟酸+75%水钝化液:5%硝酸+2%重铬酸钾十93%水酸洗钝化液(二合一):20%硝酸+10%氢氟酸+70%水酸洗钝化膏(二合一)配方:盐酸20毫升,水100毫升,硝酸30毫升,澎润土150克搅拌成糊状。
ASTM A967-2001 不锈钢零件化学钝化处理的标准规范

Designation:A967–01e1Standard Specification forChemical Passivation Treatments for Stainless Steel Parts1 This standard is issued under thefixed designation A967;the number immediately following the designation indicates the year of original adoption or,in the case of revision,the year of last revision.A number in parentheses indicates the year of last reapproval.A superscript epsilon(e)indicates an editorial change since the last revision or reapproval.e1N OTE—Paragraph3.1.1.5was deleted editorially in April2002.Paragraph10.2was corrected editorially in April2002.1.Scope1.1This specification covers several different types of chemical passivation treatments for stainless steel parts.It includes recommendations and precautions for descaling, cleaning,and passivation of stainless steel parts.It includes several alternative tests,with acceptance criteria,for confirma-tion of effectiveness of such treatments for stainless steel parts.1.2Practices for the mechanical and chemical treatments of stainless steel surfaces are discussed more thoroughly in Practice A380.1.3Several alternative chemical treatments are defined for passivation of stainless steel parts.Appendix X1gives some nonmandatory information and provides some general guide-lines regarding the selection of passivation treatment appropri-ate to particular grades of stainless steel but makes no recommendations regarding the suitability of any grade,treat-ment,and acceptance criteria for any particular application or class of applications.1.4The tests in this specification are intended to confirm the effectiveness of passivation,particularly with regard to the removal of free iron and other exogenous matter.These tests include the following practices:1.4.1Practice A—Water Immersion Test,1.4.2Practice B—High Humidity Test,1.4.3Practice C—Salt Spray Test,1.4.4Practice D—Copper Sulfate Test,1.4.5Practice E—Potassium Ferricyanide–Nitric Acid Test, and1.4.6Practice F—Free Iron Test.1.5The values stated in inch-pound units are to be regarded as the standard.The SI units given in parentheses are for information only.1.6The following precautionary caveat pertains only to the test method portions,Sections14through18of this specifica-tion:This standard does not purport to address all of the safety concerns,if any,associated with its use.It is the responsibility of the user of this standard to establish appropriate safety and health practices and determine the applicability of regulatory limitations prior to use.2.Referenced Documents2.1ASTM Standards:A380Practice for Cleaning,Descaling,and Depassivation of Stainless Steel Parts,Equipment,and Systems2B117Practice for Operating Salt Spray(Fog)Apparatus3 B254Practice for Preparation of and Electroplating on Stainless Steel42.2Federal Specification:QQ-P-35C Passivation Treatments for Corrosion-Resistant Steels53.Terminology3.1Definition of Term Specific to This Standard—It is necessary to define which of the several commonly used definitions of the term passivation will be used in this specification.(See Discussion.)3.1.1Discussion—Stainless steels are autopassivating in the sense that the protective passivefilm is formed spontaneously on exposure to air or moisture.The presence of exogenous surface contamination,including dirt,grease,free iron from contact with steel tooling,and so forth,may interfere with the formation of the passivefilm.The cleaning of these contami-nants from the stainless steel surface will facilitate the spon-taneous passivation by allowing the oxygen uniform access to the surface.The passivefilm may be augmented by chemical treatments that provide an oxidizing environment for the stainless steel surface.3.1.1.1In this specification,passivation,unless otherwise specified,is defined as the chemical treatment of a stainless steel with a mild oxidant,such as a nitric acid solution,for the purpose of the removal of free iron or other foreign matter,but which is generally not effective in removal of heat tint or oxide scale on stainless steel.In the case of stainless steels with additions of sulfur for the purpose of improved machinability,1This specification is under the jurisdiction of ASTM Committee A01on Steel, Stainless Steel,and Related Alloys and is the direct responsibility of Subcommittee A01.14on Methods of Corrosion Testing.Current edition approved Oct.10,2001.Published December2001.Originally published as A967–st previoius edition A967–99.2Annual Book of ASTM Standards,V ol01.03.3Annual Book of ASTM Standards,V ol03.02.4Annual Book of ASTM Standards,V ol02.05.5Available from Superintendent of Documents,ernment Printing Office,Washington,DC20402.1Copyright©ASTM International,100Barr Harbor Drive,PO Box C700,West Conshohocken,PA19428-2959,United States.passivation may also include the removal of sulfides from the surface of the metal for the purpose of maximizing corrosion resistance.3.1.1.2The formation of the protective passivefilm on a stainless steel,also called passivation in a more general context,will occur spontaneously in air or other oxygen-containing environment when the stainless steel surface is free of oxide scale and exogenous matter.3.1.1.3Chemical treatments,such as sodium dichromate solutions,may facilitate the more rapid formation of the passivefilm on a stainless steel surface already free of scale or foreign matter.Such treatments,also sometimes called passi-vation in common usage,are designated as post-cleaning treatments in this specification in order to distinguish them from chemical treatments capable of removing free iron from stainless steels.3.1.1.4The chemical treatments capable of removing heat tint or oxide scale from stainless steel and capable of dissolving the stainless steel itself,typically called pickling,are substan-tially more aggressive than treatments used for passivation,as defined in3.1.1.1.The surface of stainless steel that has been pickled is free of scale,free iron,and exogenous foreign matter,and does not require a separate treatment for passiva-tion as defined in3.1.1.1.The passivation process defined in 3.1.1.2will occur without further chemical treatment but may be augmented and improved by the post-cleaning treatments defined in3.1.1.3.3.1.1.5Electrochemical treatments,including electropick-ling and electropolishing capable of removing heat tint or oxide scale from stainless steel and capable of dissolving the stainless steel itself,are substantially more aggressive than treatments used for passivation,as defined in3.1.1.1.The surface of stainless steel resulting from these treatments is free of scale, free iron,and exogenous foreign matter,and does not require a separate treatment for passivation as defined in3.1.1.1.The passivation process defined in 3.1.1.2will occur without further chemical treatment,but may be augmented and im-proved by the post-cleaning treatments defined in 3.1.1.3. Statements regarding chemical treatments,unless otherwise specified,are taken to include electrochemical treatments.4.Ordering Information4.1It is the responsibility of the purchaser to specify a test practice appropriate to any particular material and application. This specification was written for the purpose of providing an alternative to United States Federal Specification QQ-P-35C. Determination of the suitability of this specification for that purpose is the responsibility of the purchaser.4.2Unless specified by the purchaser,the chemical treat-ment applied to the stainless steel parts shall be selected by the seller from among the listed passivation treatments.5.Materials and Preparation for Passivation Treatments 5.1The passivation treatments shall be of one or more of the following types.The effectiveness of a particular treatment for a particular grade of stainless steel in a particular application is demonstrated by meeting the specified testing requirements: 5.1.1Treatments in nitric acid,5.1.2Treatments in citric acid,5.1.3Other chemical treatments,including electrochemical treatments,5.1.4Neutralization,and5.1.5Post-cleaning treatments.5.2Materials:5.2.1The chemicals used for passivation treatments shall produce passivated surfaces that meet the requirements of one or more of the tests of this specification.Attention shall be given to maintaining adequate volume,concentration,purity, and temperature control appropriate to the size and amount of stainless steel to be treated.5.2.2The processor shall maintain a record with regard to concentration and temperature of the passivation solution sufficient to demonstrate that the specified passivation condi-tions were maintained for each lot of stainless steel parts processed.Such records shall be available for inspection when specified in the purchase order.The processor is not required to reveal the precise composition of proprietary chemical mix-tures but shall maintain a unique identification of the mixture that will ensure its accurate representation for subsequent use.5.2.3The processor shall be responsible for the safe dis-posal of all material generated by this process.5.3Preparation for Passivation Treatments:5.3.1The pretreatment methods and procedures used prior to the passivation treatment,including mechanical and chemi-cal methods,singly or in combination,for descaling and pickling,shall be in accordance with Practice A380.When electrochemical cleaning is required,it shall be performed in accordance with Practice B254.5.3.2The resulting pretreated surface shall be substantially free of oil,grease,rust,scale,and other foreign matter.5.3.3When thefinal pretreatment of a part includes pickling of the entire surface of the part,no further passivation treatment is required prior to testing of the surface unless specified by the purchaser.6.Treatments in Nitric Acid Solutions6.1Passivation Treatment:6.1.1Stainless steel parts shall be treated in one of the following aqueous solutions and maintained within the speci-fied temperature range for the specified time.6.1.1.1Nitric1—The solution shall contain20to25volume percent of nitric acid and2.5+0.5weight percent of sodium dichromate.The parts shall be immersed for a minimum of20 min at a temperature in the range from120to130°F(49to 54°C).6.1.1.2Nitric2—The solution shall contain20to45volume percent of nitric acid.The parts shall be immersed for a minimum of30min at a temperature in the range from70to 90°F(21to32°C).6.1.1.3Nitric3—The solution shall contain20to25volume percent nitric acid.The parts shall be immersed for a minimum of20min at a temperature in the range from120to140°F(49 to60°C).6.1.1.4Nitric4—The solution shall contain45to55volume percent of nitric acid.The parts shall be immersed for a minimum of30min at a temperature in the range from120to 130°F(49to54°C).6.1.1.5Nitric5—Other combinations of temperature,time, and concentration of nitric acid,with or without other chemi-cals,including accelerants,inhibitors,or proprietary solutions, capable of producing parts that pass the specified test require-ments.6.2Water Rinse—Immediately after removal from the pas-sivating solution the parts shall be thoroughly rinsed,using stagnant,countercurrent,or spray washes singly or in combi-nation,with or without a separate chemical treatment for neutralization(see9.1)of the passivation media,with afinal rinse being carried out using water with a maximum total solids content of200ppm.7.Treatments in Citric Acid7.1Passivation Treatment:7.1.1Stainless steel parts shall be treated in one of the following aqueous solutions and maintained within the speci-fied temperature range for the specified time.7.1.1.1Citric1—The solution shall contain4to10weight percent of citric acid.The parts shall be immersed for a minimum of4min at a temperature in the range from140to 160°F(60to71°C).7.1.1.2Citric2—The solution shall contain4to10weight percent of citric acid.The parts shall be immersed for a minimum of10min at a temperature in the range from120to 140°F(49to60°C).7.1.1.3Citric3—The solution shall contain4to10weight percent of citric acid.The parts shall be immersed for a minimum of20min at a temperature in the range from70to 120°F(21to49°C).7.1.1.4Citric4—Other combinations of temperature,time, and concentration of citric acid,with or without other chemi-cals to enhance cleaning,including accelerants,inhibitors,or proprietary solutions capable of producing parts that pass the specified test requirements.7.1.1.5Citric5—Other combinations of temperature,time, and concentrations of citric acid,with or without other chemi-cals to enhance cleaning,including accelerants,inhibitors,or proprietary solutions capable of producing parts that pass the specified test requirements.Immersion bath to be controlled ata pH of1.8–2.2.7.2Water Rinse—Immediately after removal from the pas-sivating solution,the parts shall be thoroughly rinsed,using stagnant,countercurrent,or spray washes,singly or in combi-nation,with or without a separate chemical treatment for neutralization of the passivation media(see9.2),with afinal rinse being carried out using water with a maximum total solids content of200ppm.8.Treatments in Other Chemical Solutions,IncludingElectrochemical Treatments8.1It is recognized that the purpose of removal of all exogenous matter from a stainless steel surface,including the removal of free iron,can be accomplished by different media, with potential for benefits to be gained from use of proprietary skills and art,including proprietary passivation media.Such treatments may include externally applying an electrical po-tential on the stainless steel parts,as in the case of electropol-ishing.The suitability of such passivation treatments for use in meeting the requirements of this specification shall be deter-mined by the capability of the processed parts meeting the specified test requirements.8.2Stainless steel parts shall be treated in a specified aqueous solution,with or without externally applied electrical potential,and maintained within a specified temperature range for a time sufficient for the processed parts to meet the specified test requirement.8.3Water Rinse—Immediately after removal from the pas-sivating solution,the parts shall be thoroughly rinsed,using stagnant,countercurrent,or spray washes,singly or in combi-nation,with or without a separate chemical treatment for neutralization of the passivation media(see9.2),with afinal rinse being carried out using water with a maximum total solids content of200ppm.9.Neutralization9.1The chemical reactions of the passivating media on the surface of the stainless steel shall be stopped by rinsing of the stainless steel part,with or without a separate neutralization treatment.9.2The suitability of a neutralization procedure is deter-mined by the capability of the processed parts meeting the specified test requirements.(See Note1.)N OTE1—The selection of medium and procedures for a neutralization depends of the chemistry of the passivation and on economic consider-ations.An example of a neutralizing treatment would be immersion of the part for a minimum of30min in a solution of5%NaOH at160to180°F (71to82°C),followed by a water rinse.10.Post-Cleaning Treatments10.1Although the passivefilm characteristic of stainless steel will form spontaneously in air or any other oxygen-containing environment,the processor shall,when specified, apply a chemical treatment that will accelerate the formation of the passivefilm on a chemically clean stainless steel surface. An example of a medium that serves to accelerate the forma-tion of the passivefilm but does not contribute to the removal of free iron from the stainless steel surface would be an aqueous solution of sodium dichromate.10.2When specified,within one hour after thefinal water rinse as required in6.2,7.2,or8.3,all ferritic and martensitic steel parts shall be immersed in an aqueous solution containing 4to6weight percent of sodium dichromate at a temperature in the range from140to160°F(60to71°C)for a minimum of30 min,followed by a rinse in accordance with6.2,7.2,or8.3. The parts shall then be thoroughly dried.10.3The purchaser may specify other post-cleaning treat-ments.11.Finish11.1The passivated parts shall exhibit a chemically clean surface and shall,on visual inspection,show no etching, pitting,or frosting resulting from the passivation procedures.12.Testing Agency12.1When required,the purchaser shall be permitted to perform such inspections as necessary to determine that the testing agency is capable of performing the specifiedtest.13.Lot,Frequency of Testing,and Selection of Test13.1Definition of Lot—A lot shall consist of one of the following,at the option of the processor:13.1.1The passivated parts of similar alloy and manufac-turing methods that are pretreated and passivated in a single day or within a time frame that will ensure consistent passiva-tion results;13.1.2The passivated parts of the same product of one size from one heat in one shipment;or13.1.3When few parts are involved,the passivated parts from an entire production run.13.2Unless a greater frequency of testing is specified on the purchase order,one test per lot shall be sufficient.13.3One or more of the following tests,when specified on the purchase order,shall be performed on each lot of stainless steel parts.Not all of the following tests are suitable for all grades of stainless steel.(See Note2.)13.3.1Practice A—Water Immersion Test,13.3.2Practice B—High Humidity Test,13.3.3Practice C—Salt Spray Test,13.3.4Practice D—Copper Sulfate Test,and13.3.5Practice E—Potassium Ferricyanide–Nitric Acid Test.N OTE2—Some of the tests may produce positive indications not associated with the presence of free iron on the stainless steel surface.An example would be application of Practice C on some lesser-alloyed martensitic or ferritic stainless steels.14.Practice A—Water Immersion Test14.1This test is used for the detection of free iron or any other anodic surface contaminants on stainless steel.14.2The sample representing the lot of passivated parts shall be alternately immersed in a non-rusting tank of distilled water for1h and allowed to dry in air for1h.This cycle shall be repeated a minimum of twelve times.14.3The tested sample shall not exhibit rust or staining attributable to the presence of free iron particles embedded in the surface.15.Practice B—High Humidity Test15.1This test is used for the detection of free iron or any other anodic surface contaminants on stainless steel.15.2The test shall be performed using a humidity cabinet capable of maintaining the specified test conditions.15.3The sample representing the lot of passivated parts shall be cleaned by immersion in acetone or methyl alcohol or by swabbing with a clean gauze saturated with acetone or methyl alcohol,and dried in an inert atmosphere or desiccated container.The cleaned and dried part shall be subjected to97 63%humidity at10065°F(3863°C)for a minimum of 24h.15.4The tested sample shall not exhibit rust or staining attributable to the presence of free iron particles imbedded in the surface.16.Practice C—Salt Spray Test16.1This test is used for the detection of free iron or any other anodic surface contaminants on stainless steel.16.2The sample representing the lot of passivated parts shall be tested by the salt spray test conducted in accordance with Practice B117for a minimum of2h using a5%salt solution.16.3The tested sample shall not exhibit rust or staining attributable to the presence of free iron particles imbedded in the surface.17.Practice D—Copper Sulfate Test17.1This test is recommended for the detection of free iron on the surface of austenitic stainless steels in the200and300 series,precipitation hardened stainless steels,and ferritic400 series stainless steels having a minimum of16%chromium. This test is not recommended for martensitic400series stainless steels or for ferritic400series stainless steels with less than16%chromium because these steels will give a positive indication irrespective of the presence or absence of anodic surface contaminants.This test shall not be applied to parts to be used in food processing.17.2The test solution is prepared by dissolving4g of copper sulfate pentahydrate(CuSO4·5H2O)in250mL of distilled water to which1mL of sulfuric acid(H2SO4,sp gr 1.84)has been added.Aqueous copper sulfate solutions more than two weeks old shall not be used for this test.17.3The test solution is swabbed on the surface of the sample representing the lot of passivated parts,applying additional solution as needed to keep the surface wet for a period of at least6min.At the end of this period,the surface shall be carefully rinsed and dried with care taken not to disturb copper deposits if present.17.4The tested sample shall not exhibit copper deposits.18.Practice E—Potassium Ferricyanide–Nitric Acid Test 18.1This test is recommended when detection of very small amounts of free iron is required.It is recommended for detection of free iron on austenitic200and300series stainless steels.This test is not recommended for detection of free iron on ferritic or martensitic400series stainless steels,because these steels will give a positive indication irrespective of the presence or absence of anodic surface contaminants.This test shall not be applied to parts to be used in food processing. 18.2The test solution is prepared by adding10g of chemically pure potassium ferricyanide to500mL of distilled water,adding30mL of70%nitric acid,agitating until all of the ferricyanide is dissolved,and diluting to1000mL with distilled water.The test solution shall be mixed fresh on the day of the test.18.3The test solution is swabbed on the surface of the sample representing the lot of passivated parts.The formation of a dark blue color within30s denotes the presence of metallic iron.18.4The tested sample shall not exhibit the dark blue color indicative of free iron on the surface.18.5When the test is negative,the surface shall be thor-oughly washed with warm water to removal all traces of the test solution.When the test is positive,the dark blue stain shall be removed with a solution of10%acetic acid and8%oxalic acid,followed by a thorough hot waterrinse.19.Practice F—Free Iron Test19.1This test is used for the detection of free iron on the surface of stainless steel.It is especially useful for large parts that have been uniformly cleaned but that are inconvenient for reasons of size of equipment or ease of handling of the part to place in the environments defined in Practice A(Section14)or Practice B(Section15).Unless otherwise specified by the purchaser,the number of tests and the locations of the tests shall be at the option of the processor to assure a representative testing of the part.19.2The test is performed by placing a clean cloth pad that has been thoroughly soaked with distilled or deminaralized water on the surface of the part at a part temperature of50°F (10°C)or greater for a period of not less than60minutes.The cloth shall be in contact with the steel for an area of at least20 square inches(130cm2).The pad shall be maintained wet through the test period,either by a method of retarding external evaporation,by the further addition of potable water,or by backing the pad with a sponge or similar water source.The cloth pad used shall be used for only one such test,being changed for each test so as to avoid risk of contamination. After removal of the cloth pad,the surface of the part shall be allowed to dry in air before inspection.19.3The tested part shall not exhibit rust or staining attributable to the presence of free iron particles embedded in the surface.20.Rejection and Retest20.1Any lot failing to meet the specified test requirements of the purchase order shall be rejected.A rejected lot may,at the option of the processor,be re-passivated,with or without re-pretreatment,and then be retested.The number of samples tested from a lot subject to retest shall be twice the original specified test frequency,to the limit of the number of pieces in the lot.All samples must pass the specified acceptance criterion for the specified test for the retested lot to be accepted. 21.Precision and Bias21.1No statement is made concerning either the precision or bias of Practices A,B,C,D,and E because the results state merely whether there is conformance to the criteria for success specified in the procedure.22.Certification22.1When specified in the purchase order,a report of the practice and tests used,including the record of process condi-tions when specified in accordance with 3.1.1.2,shall be supplied to the purchaser.APPENDIX(Nonmandatory Information)RMATION REGARDING PASSIV ATION TREATMENTSN OTE X1.1—The following information is based on a section of Federal Specification QQ-P-35C(Oct.28,1988)identified as information of a general or explanatory nature that may be helpful,but is not mandatory. Minor changes have been made in the text to facilitate references to the main document and to correct technical inaccuracies.X1.1Intended Use—The passivation treatments provided by this specification are intended to improve the corrosion resistance of parts made from stainless steels of all types.X1.1.1During processing operations such as forming,ma-chining,tumbling,and lapping,iron particles or other foreign particles may become smeared over or imbedded into the surface of stainless steel parts.These particles must be re-moved or they will appear as rust or stain spots.This condition may be prevented by chemically treating the parts to remove the iron particles or other foreign particles,and then allowing the passivefilm to form on the cleaned surface,with or without chemical enhancement of the formation of this oxidefilm.X1.1.2This specification is not intended for the black oxide coating of parts typically used for photographic or optical instruments.X1.2Ordering Data—Purchasers should select the pre-ferred options permitted by this specification and include the following information in the purchase order:X1.2.1Title,number,and date of this specification;X1.2.2Identification of material by type and applicable product specification;X1.2.3Test practices to be imposed(see1.4);X1.2.4Definition of lot size,if other than described in this specification;andX1.2.5Required documentation,if other than the minimum required by this specification.X1.3Grades of Stainless Steel—Different types of stainless steel are selected on a basis of properties required,for example, corrosion resistance and design criteria,and fabrication re-quirements.Table X1.1is a compilation that serves as a guide for the selection of passivation treatment for different grades, but is far from complete either in grades or in passivation treatments.X1.4Clean Water—Clean water is defined as water con-taining a maximum total solid content of200ppm.Rinsing can be accomplished by a combination of stagnant,countercurrent or spray rinses,or both,prior tofinal rinse.X1.5Chemically Clean Surface—A chemically clean sur-face is defined as a surface upon which water,when applied momentarily to the surface,will remain on that surface in an even,continuousfilm,and in addition is free of any foreign material or residualfilm deposit which would be detrimental to the quality of thepart.X1.6Test Specimens —When using test specimens instead of parts,the specimens can effectively represent the parts only if they have been exposed to the same processing steps,such as machining,grinding,heat treating,welding,and so forth,as the parts they are to represent.X1.7Carburized Surfaces —Stainless steel parts with car-burized surfaces cannot be passivated because the carbon combines with the chromium forming chromium carbides on the surface.X1.8Nitrided Surfaces —Stainless steel parts with nitrided surfaces should not be passivated because the treatment will severely corrode the nitrided case.X1.9This specification provides for the same passivation treatments as Fed.Spec.QQ-P-35C,but also includes a number of alternative passivation treatments.The effectiveness of any passivation treatment is demonstrated by the parts meeting the specified testing requirements after treatment.X1.10Martensitic Grade 440C —High-strength grades such as 440C are subject to hydrogen embrittlement or intergranular attack when exposed to acids.Cleaning by mechanical methods or other chemical methods is recom-mended.X1.11The salt spray test is typically used to evaluate austenitic stainless steels and may not be applicable to all martensitic or ferritic stainless steels.ASTM International takes no position respecting the validity of any patent rights asserted in connection with any item mentioned in this ers of this standard are expressly advised that determination of the validity of any such patent rights,and the risk of infringement of such rights,are entirely their own responsibility.This standard is subject to revision at any time by the responsible technical committee and must be reviewed every five years and if not revised,either reapproved or withdrawn.Your comments are invited either for revision of this standard or for additional standards and should be addressed to ASTM International Headquarters.Your comments will receive careful consideration at a meeting of the responsible technical committee,which you may attend.If you feel that your comments have not received a fair hearing you should make your views known to the ASTM Committee on Standards,at the address shownbelow.FIG.X1.1Recommended Nitric Acid Passivation Treatments for Different Grades of StainlessSteel。
不锈钢酸零部件膏剂酸洗钝化工艺规程
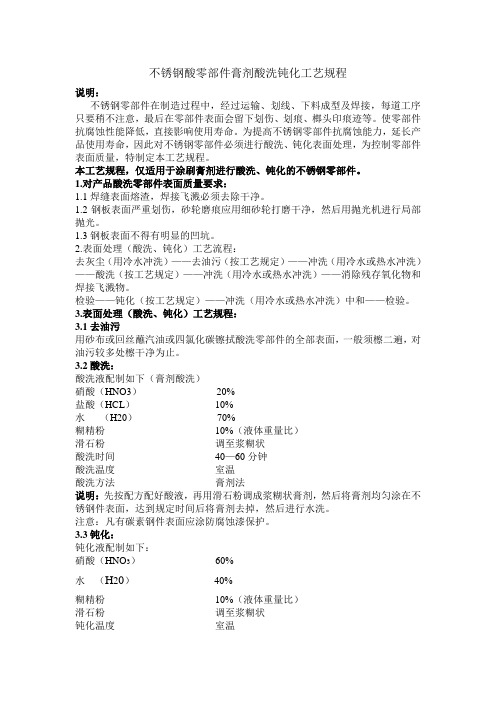
不锈钢酸零部件膏剂酸洗钝化工艺规程说明:不锈钢零部件在制造过程中,经过运输、划线、下料成型及焊接,每道工序只要稍不注意,最后在零部件表面会留下划伤、划痕、榔头印痕迹等。
使零部件抗腐蚀性能降低,直接影响使用寿命。
为提高不锈钢零部件抗腐蚀能力,延长产品使用寿命,因此对不锈钢零部件必须进行酸洗、钝化表面处理,为控制零部件表面质量,特制定本工艺规程。
本工艺规程,仅适用于涂刷膏剂进行酸洗、钝化的不锈钢零部件。
1.对产品酸洗零部件表面质量要求:1.1焊缝表面熔渣,焊接飞溅必须去除干净。
1.2钢板表面严重划伤,砂轮磨痕应用细砂轮打磨干净,然后用抛光机进行局部抛光。
1.3钢板表面不得有明显的凹坑。
2.表面处理(酸洗、钝化)工艺流程:去灰尘(用冷水冲洗)——去油污(按工艺规定)——冲洗(用冷水或热水冲洗)——酸洗(按工艺规定)——冲洗(用冷水或热水冲洗)——消除残存氧化物和焊接飞溅物。
检验——钝化(按工艺规定)——冲洗(用冷水或热水冲洗)中和——检验。
3.表面处理(酸洗、钝化)工艺规程:3.1去油污用砂布或回丝蘸汽油或四氯化碳镲拭酸洗零部件的全部表面,一般须檫二遍,对油污较多处檫干净为止。
3.2酸洗:酸洗液配制如下(膏剂酸洗)硝酸(HNO3)20%盐酸(HCL)10%水(H20)70%糊精粉10%(液体重量比)滑石粉调至浆糊状酸洗时间40—60分钟酸洗温度室温酸洗方法膏剂法说明:先按配方配好酸液,再用滑石粉调成浆糊状膏剂,然后将膏剂均匀涂在不锈钢件表面,达到规定时间后将膏剂去掉,然后进行水洗。
注意:凡有碳素钢件表面应涂防腐蚀漆保护。
3.3钝化:钝化液配制如下:硝酸(HNO3)60%水(H20)40%糊精粉10%(液体重量比)滑石粉调至浆糊状钝化温度室温钝化时间2-3小时钝化方法膏剂法说明:先按配方比例配好钝化液,再用滑石粉调成浆糊状膏剂,然后将膏剂均匀涂在不锈钢件表面,达到规定时间后将膏剂去掉,然后进行水洗。
注意:1.碳素钢表面应涂防腐蚀漆保护。
ASTM A967-2001 不锈钢零件化学钝化处理的标准规范
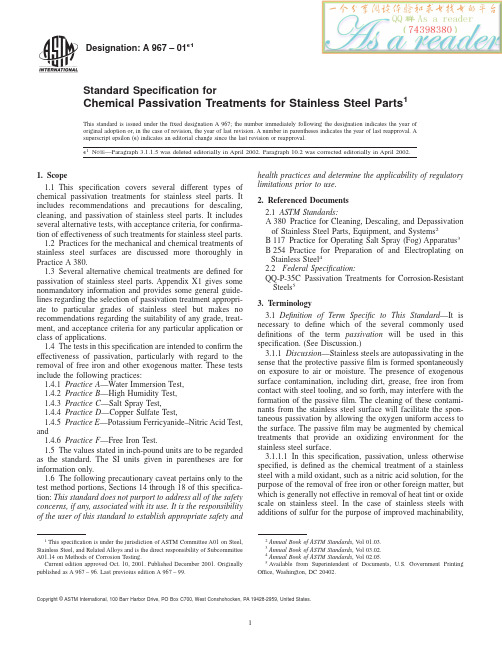
Designation:A967–01e1Standard Specification forChemical Passivation Treatments for Stainless Steel Parts1 This standard is issued under thefixed designation A967;the number immediately following the designation indicates the year of original adoption or,in the case of revision,the year of last revision.A number in parentheses indicates the year of last reapproval.A superscript epsilon(e)indicates an editorial change since the last revision or reapproval.e1N OTE—Paragraph3.1.1.5was deleted editorially in April2002.Paragraph10.2was corrected editorially in April2002.1.Scope1.1This specification covers several different types of chemical passivation treatments for stainless steel parts.It includes recommendations and precautions for descaling, cleaning,and passivation of stainless steel parts.It includes several alternative tests,with acceptance criteria,for confirma-tion of effectiveness of such treatments for stainless steel parts.1.2Practices for the mechanical and chemical treatments of stainless steel surfaces are discussed more thoroughly in Practice A380.1.3Several alternative chemical treatments are defined for passivation of stainless steel parts.Appendix X1gives some nonmandatory information and provides some general guide-lines regarding the selection of passivation treatment appropri-ate to particular grades of stainless steel but makes no recommendations regarding the suitability of any grade,treat-ment,and acceptance criteria for any particular application or class of applications.1.4The tests in this specification are intended to confirm the effectiveness of passivation,particularly with regard to the removal of free iron and other exogenous matter.These tests include the following practices:1.4.1Practice A—Water Immersion Test,1.4.2Practice B—High Humidity Test,1.4.3Practice C—Salt Spray Test,1.4.4Practice D—Copper Sulfate Test,1.4.5Practice E—Potassium Ferricyanide–Nitric Acid Test, and1.4.6Practice F—Free Iron Test.1.5The values stated in inch-pound units are to be regarded as the standard.The SI units given in parentheses are for information only.1.6The following precautionary caveat pertains only to the test method portions,Sections14through18of this specifica-tion:This standard does not purport to address all of the safety concerns,if any,associated with its use.It is the responsibility of the user of this standard to establish appropriate safety and health practices and determine the applicability of regulatory limitations prior to use.2.Referenced Documents2.1ASTM Standards:A380Practice for Cleaning,Descaling,and Depassivation of Stainless Steel Parts,Equipment,and Systems2B117Practice for Operating Salt Spray(Fog)Apparatus3 B254Practice for Preparation of and Electroplating on Stainless Steel42.2Federal Specification:QQ-P-35C Passivation Treatments for Corrosion-Resistant Steels53.Terminology3.1Definition of Term Specific to This Standard—It is necessary to define which of the several commonly used definitions of the term passivation will be used in this specification.(See Discussion.)3.1.1Discussion—Stainless steels are autopassivating in the sense that the protective passivefilm is formed spontaneously on exposure to air or moisture.The presence of exogenous surface contamination,including dirt,grease,free iron from contact with steel tooling,and so forth,may interfere with the formation of the passivefilm.The cleaning of these contami-nants from the stainless steel surface will facilitate the spon-taneous passivation by allowing the oxygen uniform access to the surface.The passivefilm may be augmented by chemical treatments that provide an oxidizing environment for the stainless steel surface.3.1.1.1In this specification,passivation,unless otherwise specified,is defined as the chemical treatment of a stainless steel with a mild oxidant,such as a nitric acid solution,for the purpose of the removal of free iron or other foreign matter,but which is generally not effective in removal of heat tint or oxide scale on stainless steel.In the case of stainless steels with additions of sulfur for the purpose of improved machinability,1This specification is under the jurisdiction of ASTM Committee A01on Steel, Stainless Steel,and Related Alloys and is the direct responsibility of Subcommittee A01.14on Methods of Corrosion Testing.Current edition approved Oct.10,2001.Published December2001.Originally published as A967–st previoius edition A967–99.2Annual Book of ASTM Standards,V ol01.03.3Annual Book of ASTM Standards,V ol03.02.4Annual Book of ASTM Standards,V ol02.05.5Available from Superintendent of Documents,ernment Printing Office,Washington,DC20402.1Copyright©ASTM International,100Barr Harbor Drive,PO Box C700,West Conshohocken,PA19428-2959,UnitedStates.passivation may also include the removal of sulfides from the surface of the metal for the purpose of maximizing corrosion resistance.3.1.1.2The formation of the protective passivefilm on a stainless steel,also called passivation in a more general context,will occur spontaneously in air or other oxygen-containing environment when the stainless steel surface is free of oxide scale and exogenous matter.3.1.1.3Chemical treatments,such as sodium dichromate solutions,may facilitate the more rapid formation of the passivefilm on a stainless steel surface already free of scale or foreign matter.Such treatments,also sometimes called passi-vation in common usage,are designated as post-cleaning treatments in this specification in order to distinguish them from chemical treatments capable of removing free iron from stainless steels.3.1.1.4The chemical treatments capable of removing heat tint or oxide scale from stainless steel and capable of dissolving the stainless steel itself,typically called pickling,are substan-tially more aggressive than treatments used for passivation,as defined in3.1.1.1.The surface of stainless steel that has been pickled is free of scale,free iron,and exogenous foreign matter,and does not require a separate treatment for passiva-tion as defined in3.1.1.1.The passivation process defined in 3.1.1.2will occur without further chemical treatment but may be augmented and improved by the post-cleaning treatments defined in3.1.1.3.3.1.1.5Electrochemical treatments,including electropick-ling and electropolishing capable of removing heat tint or oxide scale from stainless steel and capable of dissolving the stainless steel itself,are substantially more aggressive than treatments used for passivation,as defined in3.1.1.1.The surface of stainless steel resulting from these treatments is free of scale, free iron,and exogenous foreign matter,and does not require a separate treatment for passivation as defined in3.1.1.1.The passivation process defined in 3.1.1.2will occur without further chemical treatment,but may be augmented and im-proved by the post-cleaning treatments defined in 3.1.1.3. Statements regarding chemical treatments,unless otherwise specified,are taken to include electrochemical treatments.4.Ordering Information4.1It is the responsibility of the purchaser to specify a test practice appropriate to any particular material and application. This specification was written for the purpose of providing an alternative to United States Federal Specification QQ-P-35C. Determination of the suitability of this specification for that purpose is the responsibility of the purchaser.4.2Unless specified by the purchaser,the chemical treat-ment applied to the stainless steel parts shall be selected by the seller from among the listed passivation treatments.5.Materials and Preparation for Passivation Treatments 5.1The passivation treatments shall be of one or more of the following types.The effectiveness of a particular treatment for a particular grade of stainless steel in a particular application is demonstrated by meeting the specified testing requirements: 5.1.1Treatments in nitric acid,5.1.2Treatments in citric acid,5.1.3Other chemical treatments,including electrochemical treatments,5.1.4Neutralization,and5.1.5Post-cleaning treatments.5.2Materials:5.2.1The chemicals used for passivation treatments shall produce passivated surfaces that meet the requirements of one or more of the tests of this specification.Attention shall be given to maintaining adequate volume,concentration,purity, and temperature control appropriate to the size and amount of stainless steel to be treated.5.2.2The processor shall maintain a record with regard to concentration and temperature of the passivation solution sufficient to demonstrate that the specified passivation condi-tions were maintained for each lot of stainless steel parts processed.Such records shall be available for inspection when specified in the purchase order.The processor is not required to reveal the precise composition of proprietary chemical mix-tures but shall maintain a unique identification of the mixture that will ensure its accurate representation for subsequent use.5.2.3The processor shall be responsible for the safe dis-posal of all material generated by this process.5.3Preparation for Passivation Treatments:5.3.1The pretreatment methods and procedures used prior to the passivation treatment,including mechanical and chemi-cal methods,singly or in combination,for descaling and pickling,shall be in accordance with Practice A380.When electrochemical cleaning is required,it shall be performed in accordance with Practice B254.5.3.2The resulting pretreated surface shall be substantially free of oil,grease,rust,scale,and other foreign matter.5.3.3When thefinal pretreatment of a part includes pickling of the entire surface of the part,no further passivation treatment is required prior to testing of the surface unless specified by the purchaser.6.Treatments in Nitric Acid Solutions6.1Passivation Treatment:6.1.1Stainless steel parts shall be treated in one of the following aqueous solutions and maintained within the speci-fied temperature range for the specified time.6.1.1.1Nitric1—The solution shall contain20to25volume percent of nitric acid and2.5+0.5weight percent of sodium dichromate.The parts shall be immersed for a minimum of20 min at a temperature in the range from120to130°F(49to 54°C).6.1.1.2Nitric2—The solution shall contain20to45volume percent of nitric acid.The parts shall be immersed for a minimum of30min at a temperature in the range from70to 90°F(21to32°C).6.1.1.3Nitric3—The solution shall contain20to25volume percent nitric acid.The parts shall be immersed for a minimum of20min at a temperature in the range from120to140°F(49 to60°C).6.1.1.4Nitric4—The solution shall contain45to55volume percent of nitric acid.The parts shall be immersed for a minimum of30min at a temperature in the range from120to 130°F(49to54°C).6.1.1.5Nitric5—Other combinations of temperature,time, and concentration of nitric acid,with or without other chemi-cals,including accelerants,inhibitors,or proprietary solutions, capable of producing parts that pass the specified test require-ments.6.2Water Rinse—Immediately after removal from the pas-sivating solution the parts shall be thoroughly rinsed,using stagnant,countercurrent,or spray washes singly or in combi-nation,with or without a separate chemical treatment for neutralization(see9.1)of the passivation media,with afinal rinse being carried out using water with a maximum total solids content of200ppm.7.Treatments in Citric Acid7.1Passivation Treatment:7.1.1Stainless steel parts shall be treated in one of the following aqueous solutions and maintained within the speci-fied temperature range for the specified time.7.1.1.1Citric1—The solution shall contain4to10weight percent of citric acid.The parts shall be immersed for a minimum of4min at a temperature in the range from140to 160°F(60to71°C).7.1.1.2Citric2—The solution shall contain4to10weight percent of citric acid.The parts shall be immersed for a minimum of10min at a temperature in the range from120to 140°F(49to60°C).7.1.1.3Citric3—The solution shall contain4to10weight percent of citric acid.The parts shall be immersed for a minimum of20min at a temperature in the range from70to 120°F(21to49°C).7.1.1.4Citric4—Other combinations of temperature,time, and concentration of citric acid,with or without other chemi-cals to enhance cleaning,including accelerants,inhibitors,or proprietary solutions capable of producing parts that pass the specified test requirements.7.1.1.5Citric5—Other combinations of temperature,time, and concentrations of citric acid,with or without other chemi-cals to enhance cleaning,including accelerants,inhibitors,or proprietary solutions capable of producing parts that pass the specified test requirements.Immersion bath to be controlled ata pH of1.8–2.2.7.2Water Rinse—Immediately after removal from the pas-sivating solution,the parts shall be thoroughly rinsed,using stagnant,countercurrent,or spray washes,singly or in combi-nation,with or without a separate chemical treatment for neutralization of the passivation media(see9.2),with afinal rinse being carried out using water with a maximum total solids content of200ppm.8.Treatments in Other Chemical Solutions,IncludingElectrochemical Treatments8.1It is recognized that the purpose of removal of all exogenous matter from a stainless steel surface,including the removal of free iron,can be accomplished by different media, with potential for benefits to be gained from use of proprietary skills and art,including proprietary passivation media.Such treatments may include externally applying an electrical po-tential on the stainless steel parts,as in the case of electropol-ishing.The suitability of such passivation treatments for use in meeting the requirements of this specification shall be deter-mined by the capability of the processed parts meeting the specified test requirements.8.2Stainless steel parts shall be treated in a specified aqueous solution,with or without externally applied electrical potential,and maintained within a specified temperature range for a time sufficient for the processed parts to meet the specified test requirement.8.3Water Rinse—Immediately after removal from the pas-sivating solution,the parts shall be thoroughly rinsed,using stagnant,countercurrent,or spray washes,singly or in combi-nation,with or without a separate chemical treatment for neutralization of the passivation media(see9.2),with afinal rinse being carried out using water with a maximum total solids content of200ppm.9.Neutralization9.1The chemical reactions of the passivating media on the surface of the stainless steel shall be stopped by rinsing of the stainless steel part,with or without a separate neutralization treatment.9.2The suitability of a neutralization procedure is deter-mined by the capability of the processed parts meeting the specified test requirements.(See Note1.)N OTE1—The selection of medium and procedures for a neutralization depends of the chemistry of the passivation and on economic consider-ations.An example of a neutralizing treatment would be immersion of the part for a minimum of30min in a solution of5%NaOH at160to180°F (71to82°C),followed by a water rinse.10.Post-Cleaning Treatments10.1Although the passivefilm characteristic of stainless steel will form spontaneously in air or any other oxygen-containing environment,the processor shall,when specified, apply a chemical treatment that will accelerate the formation of the passivefilm on a chemically clean stainless steel surface. An example of a medium that serves to accelerate the forma-tion of the passivefilm but does not contribute to the removal of free iron from the stainless steel surface would be an aqueous solution of sodium dichromate.10.2When specified,within one hour after thefinal water rinse as required in6.2,7.2,or8.3,all ferritic and martensitic steel parts shall be immersed in an aqueous solution containing 4to6weight percent of sodium dichromate at a temperature in the range from140to160°F(60to71°C)for a minimum of30 min,followed by a rinse in accordance with6.2,7.2,or8.3. The parts shall then be thoroughly dried.10.3The purchaser may specify other post-cleaning treat-ments.11.Finish11.1The passivated parts shall exhibit a chemically clean surface and shall,on visual inspection,show no etching, pitting,or frosting resulting from the passivation procedures.12.Testing Agency12.1When required,the purchaser shall be permitted to perform such inspections as necessary to determine that the testing agency is capable of performing the specifiedtest.13.Lot,Frequency of Testing,and Selection of Test13.1Definition of Lot—A lot shall consist of one of the following,at the option of the processor:13.1.1The passivated parts of similar alloy and manufac-turing methods that are pretreated and passivated in a single day or within a time frame that will ensure consistent passiva-tion results;13.1.2The passivated parts of the same product of one size from one heat in one shipment;or13.1.3When few parts are involved,the passivated parts from an entire production run.13.2Unless a greater frequency of testing is specified on the purchase order,one test per lot shall be sufficient.13.3One or more of the following tests,when specified on the purchase order,shall be performed on each lot of stainless steel parts.Not all of the following tests are suitable for all grades of stainless steel.(See Note2.)13.3.1Practice A—Water Immersion Test,13.3.2Practice B—High Humidity Test,13.3.3Practice C—Salt Spray Test,13.3.4Practice D—Copper Sulfate Test,and13.3.5Practice E—Potassium Ferricyanide–Nitric Acid Test.N OTE2—Some of the tests may produce positive indications not associated with the presence of free iron on the stainless steel surface.An example would be application of Practice C on some lesser-alloyed martensitic or ferritic stainless steels.14.Practice A—Water Immersion Test14.1This test is used for the detection of free iron or any other anodic surface contaminants on stainless steel.14.2The sample representing the lot of passivated parts shall be alternately immersed in a non-rusting tank of distilled water for1h and allowed to dry in air for1h.This cycle shall be repeated a minimum of twelve times.14.3The tested sample shall not exhibit rust or staining attributable to the presence of free iron particles embedded in the surface.15.Practice B—High Humidity Test15.1This test is used for the detection of free iron or any other anodic surface contaminants on stainless steel.15.2The test shall be performed using a humidity cabinet capable of maintaining the specified test conditions.15.3The sample representing the lot of passivated parts shall be cleaned by immersion in acetone or methyl alcohol or by swabbing with a clean gauze saturated with acetone or methyl alcohol,and dried in an inert atmosphere or desiccated container.The cleaned and dried part shall be subjected to97 63%humidity at10065°F(3863°C)for a minimum of 24h.15.4The tested sample shall not exhibit rust or staining attributable to the presence of free iron particles imbedded in the surface.16.Practice C—Salt Spray Test16.1This test is used for the detection of free iron or any other anodic surface contaminants on stainless steel.16.2The sample representing the lot of passivated parts shall be tested by the salt spray test conducted in accordance with Practice B117for a minimum of2h using a5%salt solution.16.3The tested sample shall not exhibit rust or staining attributable to the presence of free iron particles imbedded in the surface.17.Practice D—Copper Sulfate Test17.1This test is recommended for the detection of free iron on the surface of austenitic stainless steels in the200and300 series,precipitation hardened stainless steels,and ferritic400 series stainless steels having a minimum of16%chromium. This test is not recommended for martensitic400series stainless steels or for ferritic400series stainless steels with less than16%chromium because these steels will give a positive indication irrespective of the presence or absence of anodic surface contaminants.This test shall not be applied to parts to be used in food processing.17.2The test solution is prepared by dissolving4g of copper sulfate pentahydrate(CuSO4·5H2O)in250mL of distilled water to which1mL of sulfuric acid(H2SO4,sp gr 1.84)has been added.Aqueous copper sulfate solutions more than two weeks old shall not be used for this test.17.3The test solution is swabbed on the surface of the sample representing the lot of passivated parts,applying additional solution as needed to keep the surface wet for a period of at least6min.At the end of this period,the surface shall be carefully rinsed and dried with care taken not to disturb copper deposits if present.17.4The tested sample shall not exhibit copper deposits.18.Practice E—Potassium Ferricyanide–Nitric Acid Test 18.1This test is recommended when detection of very small amounts of free iron is required.It is recommended for detection of free iron on austenitic200and300series stainless steels.This test is not recommended for detection of free iron on ferritic or martensitic400series stainless steels,because these steels will give a positive indication irrespective of the presence or absence of anodic surface contaminants.This test shall not be applied to parts to be used in food processing. 18.2The test solution is prepared by adding10g of chemically pure potassium ferricyanide to500mL of distilled water,adding30mL of70%nitric acid,agitating until all of the ferricyanide is dissolved,and diluting to1000mL with distilled water.The test solution shall be mixed fresh on the day of the test.18.3The test solution is swabbed on the surface of the sample representing the lot of passivated parts.The formation of a dark blue color within30s denotes the presence of metallic iron.18.4The tested sample shall not exhibit the dark blue color indicative of free iron on the surface.18.5When the test is negative,the surface shall be thor-oughly washed with warm water to removal all traces of the test solution.When the test is positive,the dark blue stain shall be removed with a solution of10%acetic acid and8%oxalic acid,followed by a thorough hot waterrinse.19.Practice F—Free Iron Test19.1This test is used for the detection of free iron on the surface of stainless steel.It is especially useful for large parts that have been uniformly cleaned but that are inconvenient for reasons of size of equipment or ease of handling of the part to place in the environments defined in Practice A(Section14)or Practice B(Section15).Unless otherwise specified by the purchaser,the number of tests and the locations of the tests shall be at the option of the processor to assure a representative testing of the part.19.2The test is performed by placing a clean cloth pad that has been thoroughly soaked with distilled or deminaralized water on the surface of the part at a part temperature of50°F (10°C)or greater for a period of not less than60minutes.The cloth shall be in contact with the steel for an area of at least20 square inches(130cm2).The pad shall be maintained wet through the test period,either by a method of retarding external evaporation,by the further addition of potable water,or by backing the pad with a sponge or similar water source.The cloth pad used shall be used for only one such test,being changed for each test so as to avoid risk of contamination. After removal of the cloth pad,the surface of the part shall be allowed to dry in air before inspection.19.3The tested part shall not exhibit rust or staining attributable to the presence of free iron particles embedded in the surface.20.Rejection and Retest20.1Any lot failing to meet the specified test requirements of the purchase order shall be rejected.A rejected lot may,at the option of the processor,be re-passivated,with or without re-pretreatment,and then be retested.The number of samples tested from a lot subject to retest shall be twice the original specified test frequency,to the limit of the number of pieces in the lot.All samples must pass the specified acceptance criterion for the specified test for the retested lot to be accepted. 21.Precision and Bias21.1No statement is made concerning either the precision or bias of Practices A,B,C,D,and E because the results state merely whether there is conformance to the criteria for success specified in the procedure.22.Certification22.1When specified in the purchase order,a report of the practice and tests used,including the record of process condi-tions when specified in accordance with 3.1.1.2,shall be supplied to the purchaser.APPENDIX(Nonmandatory Information)RMATION REGARDING PASSIV ATION TREATMENTSN OTE X1.1—The following information is based on a section of Federal Specification QQ-P-35C(Oct.28,1988)identified as information of a general or explanatory nature that may be helpful,but is not mandatory. Minor changes have been made in the text to facilitate references to the main document and to correct technical inaccuracies.X1.1Intended Use—The passivation treatments provided by this specification are intended to improve the corrosion resistance of parts made from stainless steels of all types.X1.1.1During processing operations such as forming,ma-chining,tumbling,and lapping,iron particles or other foreign particles may become smeared over or imbedded into the surface of stainless steel parts.These particles must be re-moved or they will appear as rust or stain spots.This condition may be prevented by chemically treating the parts to remove the iron particles or other foreign particles,and then allowing the passivefilm to form on the cleaned surface,with or without chemical enhancement of the formation of this oxidefilm.X1.1.2This specification is not intended for the black oxide coating of parts typically used for photographic or optical instruments.X1.2Ordering Data—Purchasers should select the pre-ferred options permitted by this specification and include the following information in the purchase order:X1.2.1Title,number,and date of this specification;X1.2.2Identification of material by type and applicable product specification;X1.2.3Test practices to be imposed(see1.4);X1.2.4Definition of lot size,if other than described in this specification;andX1.2.5Required documentation,if other than the minimum required by this specification.X1.3Grades of Stainless Steel—Different types of stainless steel are selected on a basis of properties required,for example, corrosion resistance and design criteria,and fabrication re-quirements.Table X1.1is a compilation that serves as a guide for the selection of passivation treatment for different grades, but is far from complete either in grades or in passivation treatments.X1.4Clean Water—Clean water is defined as water con-taining a maximum total solid content of200ppm.Rinsing can be accomplished by a combination of stagnant,countercurrent or spray rinses,or both,prior tofinal rinse.X1.5Chemically Clean Surface—A chemically clean sur-face is defined as a surface upon which water,when applied momentarily to the surface,will remain on that surface in an even,continuousfilm,and in addition is free of any foreign material or residualfilm deposit which would be detrimental to the quality of thepart.X1.6Test Specimens —When using test specimens instead of parts,the specimens can effectively represent the parts only if they have been exposed to the same processing steps,such as machining,grinding,heat treating,welding,and so forth,as the parts they are to represent.X1.7Carburized Surfaces —Stainless steel parts with car-burized surfaces cannot be passivated because the carbon combines with the chromium forming chromium carbides on the surface.X1.8Nitrided Surfaces —Stainless steel parts with nitrided surfaces should not be passivated because the treatment will severely corrode the nitrided case.X1.9This specification provides for the same passivation treatments as Fed.Spec.QQ-P-35C,but also includes a number of alternative passivation treatments.The effectiveness of any passivation treatment is demonstrated by the parts meeting the specified testing requirements after treatment.X1.10Martensitic Grade 440C —High-strength grades such as 440C are subject to hydrogen embrittlement or intergranular attack when exposed to acids.Cleaning by mechanical methods or other chemical methods is recom-mended.X1.11The salt spray test is typically used to evaluate austenitic stainless steels and may not be applicable to all martensitic or ferritic stainless steels.ASTM International takes no position respecting the validity of any patent rights asserted in connection with any item mentioned in this ers of this standard are expressly advised that determination of the validity of any such patent rights,and the risk of infringement of such rights,are entirely their own responsibility.This standard is subject to revision at any time by the responsible technical committee and must be reviewed every five years and if not revised,either reapproved or withdrawn.Your comments are invited either for revision of this standard or for additional standards and should be addressed to ASTM International Headquarters.Your comments will receive careful consideration at a meeting of the responsible technical committee,which you may attend.If you feel that your comments have not received a fair hearing you should make your views known to the ASTM Committee on Standards,at the address shownbelow.FIG.X1.1Recommended Nitric Acid Passivation Treatments for Different Grades of StainlessSteel。
不锈钢钝化操作规程

不锈钢钝化操作规程不锈钢钝化操作规程第一章总则第一条为了保证不锈钢表面的美观性和耐腐蚀性能,规范不锈钢钝化操作,制定本规程。
第二条不锈钢钝化操作应遵循安全、环保、规范、高效的原则。
第三条本规程适用于工业生产过程中的不锈钢钝化操作。
第二章术语和定义第四条不锈钢:指含铬量不低于10.5%的铁基合金。
第五条钝化:指通过化学处理,表面形成一层致密、均匀、抗腐蚀的氧化膜,提高不锈钢耐腐蚀性能。
第六条钝化剂:指用于不锈钢钝化过程中的化学药剂。
第七条原液:指未经稀释的钝化剂。
第三章设备和材料第八条钝化槽:应采用耐腐蚀材料制作,有良好的密封性能,防止钝化剂泄漏。
第九条前处理设备:应配备清洗槽、酸洗槽等设备,确保表面无污物。
第十条不锈钢钝化剂:应选择符合国家标准的产品,严禁使用过期的钝化剂。
第四章操作流程第十一条准备工作:将待钝化的不锈钢表面清洗干净,去除油污和锈蚀物。
第十二条配制钝化液:按照钝化剂的使用说明书,根据不锈钢的种类和数量,正确配比钝化液。
第十三条钝化槽处理:将准备好的钝化液倒入钝化槽中,使其表面充分浸泡。
第十四条设定时间:根据不锈钢的种类和厚度,设定合适的钝化时间。
第十五条钝化处理:将待钝化的不锈钢表面浸泡在钝化槽中,保证不锈钢表面完全与钝化液接触。
第十六条清洗处理:钝化处理完成后,将不锈钢表面用清水进行充分冲洗,去除残留的钝化液。
第十七条检验合格:经过钝化处理的不锈钢表面应均匀、致密,无色差、斑点和脱层等现象,并且经化学验收合格。
第五章安全和环保措施第十八条操作人员应穿戴好防护设备,如防护眼镜、手套、防护服等。
第十九条操作过程中应注意通风,避免钝化剂气味对人体造成危害。
第二十条不锈钢钝化液及废弃料应进行专门收集和储存,严禁直接排放到水体中。
第六章附则第二十一条针对特殊材质和工艺的不锈钢钝化操作,应编制相应的专项规程。
第二十二条违反本规程的操作行为,将依据相关安全和环保法律法规予以处理。
第二十三条本规程由不锈钢钝化操作管理人员执行,并在作业现场随时提供给操作人员。
不锈钢钝化处理标准
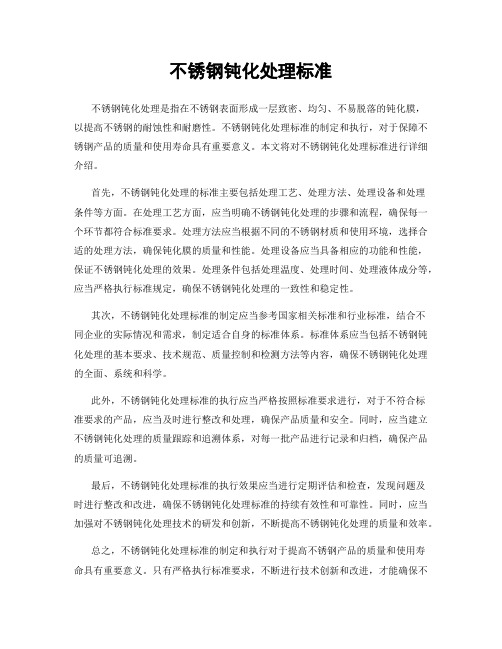
不锈钢钝化处理标准不锈钢钝化处理是指在不锈钢表面形成一层致密、均匀、不易脱落的钝化膜,以提高不锈钢的耐蚀性和耐磨性。
不锈钢钝化处理标准的制定和执行,对于保障不锈钢产品的质量和使用寿命具有重要意义。
本文将对不锈钢钝化处理标准进行详细介绍。
首先,不锈钢钝化处理的标准主要包括处理工艺、处理方法、处理设备和处理条件等方面。
在处理工艺方面,应当明确不锈钢钝化处理的步骤和流程,确保每一个环节都符合标准要求。
处理方法应当根据不同的不锈钢材质和使用环境,选择合适的处理方法,确保钝化膜的质量和性能。
处理设备应当具备相应的功能和性能,保证不锈钢钝化处理的效果。
处理条件包括处理温度、处理时间、处理液体成分等,应当严格执行标准规定,确保不锈钢钝化处理的一致性和稳定性。
其次,不锈钢钝化处理标准的制定应当参考国家相关标准和行业标准,结合不同企业的实际情况和需求,制定适合自身的标准体系。
标准体系应当包括不锈钢钝化处理的基本要求、技术规范、质量控制和检测方法等内容,确保不锈钢钝化处理的全面、系统和科学。
此外,不锈钢钝化处理标准的执行应当严格按照标准要求进行,对于不符合标准要求的产品,应当及时进行整改和处理,确保产品质量和安全。
同时,应当建立不锈钢钝化处理的质量跟踪和追溯体系,对每一批产品进行记录和归档,确保产品的质量可追溯。
最后,不锈钢钝化处理标准的执行效果应当进行定期评估和检查,发现问题及时进行整改和改进,确保不锈钢钝化处理标准的持续有效性和可靠性。
同时,应当加强对不锈钢钝化处理技术的研发和创新,不断提高不锈钢钝化处理的质量和效率。
总之,不锈钢钝化处理标准的制定和执行对于提高不锈钢产品的质量和使用寿命具有重要意义。
只有严格执行标准要求,不断进行技术创新和改进,才能确保不锈钢钝化处理的质量和效果。
希望本文对不锈钢钝化处理标准的制定和执行有所帮助。
ASTM A967

ASTM A967-01E1Standard Specification for Chemical Passivation Treatments for Stainless Steel PartsASTM International / 10-Oct-2001 / 6 pagesREPLACED by ASTM A967-051.1 This specification covers several different types of chemical passivation treatments for stainless steel parts. It includes recommendations and precautions for descaling, cleaning, and passivation of stainless steel parts. It includes several alternative tests, with acceptance criteria, for confirmation of effectiveness of such treatments for stainless steel parts.1.2 Practices for the mechanical and chemical treatments of stainless steel surfaces are discussed more thoroughly in Practice A 380.1.3 Several alternative chemical treatments are defined for passivation of stainless steel parts. gives some nonmandatory information and provides some general guidelines regarding the selection of passivation treatment appropriate to particular grades of stainless steel but makes no recommendations regarding the suitability of any grade, treatment, and acceptance criteria for any particular application or class of applications.1.4 The tests in this specification are intended to confirm the effectiveness of passivation, particularly with regard to the removal of free iron and other exogenous matter. These tests include the following practices:1.4.1 Practice A - Water Immersion Test,1.4.2 Practice B - High Humidity Test,1.4.3 Practice C - Salt Spray Test,1.4.4 Practice D - Copper Sulfate Test,1.4.5 Practice E - Potassium Ferricyanide-Nitric Acid Test, and1.4.6 Practice F - Free Iron Test.1.5 The values stated in inch-pound units are to be regarded as the standard. The SI units given in parentheses are for information only.1.6 The following precautionary caveat pertains only to the test method portions, Sections 14 through 18 of this specification: This standard does not purport to address all of the safety concerns, if any, associated with its use. It is the responsibility of the user of this standard to establish appropriate safety and health practices and determine the applicability of regulatory limitations prior to use.Keywords: chemical passivation; stainless steel; passivation treatments; water immersion, steel; high humidity, steel; 77.140.20This product replaced by:ASTM A967-05 - Standard Specification for Chemical Passivation Treatments for Stainless Steel Parts This product replaces:∙ASTM A967-99 - Standard Specification for Chemical Passivation Treatments for Stainless Steel Parts∙ASTM A967-01 - Standard Specification for Chemical Passivation Treatments for Stainless Steel Parts。
- 1、下载文档前请自行甄别文档内容的完整性,平台不提供额外的编辑、内容补充、找答案等附加服务。
- 2、"仅部分预览"的文档,不可在线预览部分如存在完整性等问题,可反馈申请退款(可完整预览的文档不适用该条件!)。
- 3、如文档侵犯您的权益,请联系客服反馈,我们会尽快为您处理(人工客服工作时间:9:00-18:30)。
洗,可在流动的水中清洗,也可进行喷洗,或者几种方法结合起来清洗。清洗时也可使用单 独的化学方法来中和(详见9.2)钝化媒介。最后的漂洗液固体含量最多为200%。
8. 包括电化学处理方法在内的其他化学溶液处理方法
8.1 众所周知去除不锈钢表面的外源物质,包括去除游离铁,可通过不同的媒介来实现,利 用合适的技艺和方法、适合的钝化媒介还可得到益处。电解时,该处理方法从外部对不锈钢 部件供电。符合该标准的此类钝化处理方法是否适用取决于反应后的部件是否符合测试的要 求。 8.2 不锈钢部件要求在水溶液中进行处理,不管是否从外部供电,也必须在规定的温度范围 内进行处理以此保证处理过的不锈钢部件符合测试的要求。 8.3 清水漂洗 - 从钝化溶液中去除不锈钢部件后立即进行全面的清洗。可在静止的水中清 洗,可在流动的水中清洗,也可进行喷洗,或者几种方法结合起来清洗。清洗时也可使用单 独的化学方法来中和(详见9.2)钝化媒介。最后的漂洗液固体含量最多为200%。
10. 后清洗处理方法
10.1 尽管不锈钢在空气或其他氧化环境下会自行形成钝化层,有具体要求时,操作者应该 采用能加快化学清洗处理过的不锈钢表面形成钝化层的化学处理方法。例如能加快钝化层的 形成但是不能去除不锈钢表面游离铁的媒介的溶液应该是重铬酸钠溶液。 10.2 如果用户要求,按照6.2,7.2,或8.3要求的方法进行最后漂洗后的一小时以内,所有铁 素体和马氏体钢部件必须浸泡在含有4-6%(重量百分比)重铬酸钠溶液的水溶液中,温度 控制在140-160华氏度(60-71摄氏度),至少浸泡30分钟。然后根据6.2,7.2或8.3条的要求 进行漂洗。最后使不锈钢部件充分干燥。 10.3 购买者会具体要求其他的后清洗处理方法。
3. 术语
3.1 该标准特定的术语定义 - 在该标准规范中定义常用的术语 passivation 是必要的(详见 讨论)。 3.1.1 讨论 - 如果不锈钢暴露在空气或潮湿的环境下产生了防钝化膜,它会自动钝化。外界 表面污染物的存在,包括灰尘,油脂,游离铁等等物质可能会干涉钝化层的形成。清洗这些 污染物会同时使不锈钢钝化,因为有氧化物质接触不锈钢的表面。可形成氧化生锈环境的化 学处理方法也会使不锈钢表面的钝化层扩大。 3.1.1.1 在该规范中,除非有特殊的定义,否则钝化即定义为使用温和氧化物的化学方法处 理不锈钢的过程,例如硝酸盐溶液。该处理方法目的在于去除游离铁及其他异物,但不会去 除不锈钢上的热色调和氧化铁皮。假如为了提高不锈钢的切削加工性而多加了硫元素,钝化
不锈钢部件化学钝化处理的标准规范
1. 范围
1.1 该规范包含了不同种类的不锈钢不见化学钝化处理的方法。它包含对不锈钢不见进行除 锈,清洗及钝化处理的优点和注意事项。它列明了一些可替换用的测试方法保证对不锈钢部 件的此类处理的有效性,并且这些方法都是符合相关标准的。 1.2 实践 A380 中全面讨论了对不锈钢部件表面进行机械处理和化学处理的实验。 1.3 为不锈钢部件钝化定义了一些可供选择的化学处理方法。附录 X1 给出了一些非强制性 信息,提供了对于不同级别的不锈钢如何正确选择钝化处理方法的一般指导,但是没有提出 对特殊适应性或适应分类的级别,处理及规则的正确性提出参考建议。 1.4 该规范提及的测试方法是为了证明钝化的有效性,特别是对于处理多余的铁和其他氧化 物质时的有效性。这些测试方法包括: 1.4.1 实验 A- 水浸测试 1.4.2 实验 B- 高湿度测试 1.4.3 实验 C- 喷盐测试 1.4.4 实验 D- 硫酸铜测试 1.4.5 实验 E- 铁氰化钾硝酸盐测试 1.4.6 实验 F- 铁离子测试 1.5 测试值的标准单位为英寸/磅。括弧里的 SI 单位仅提供参考。 1.6 以下注意事项的警告只针对测试方法部分,即该规范的 14-18 章节:该标准并不旨在提 出所有的安全问题,如果有的话,与其使用相关。该标准的使用者有责任建立安全健康的实 验并在使用前确定规则限制的适用性。
11. 完成
11.1 钝化反应后的部件需呈现出干净的表面,用肉眼看无腐蚀,无凹痕,有光泽。
12. 检测机构
12.1 如果用户要求,购买者有权进行检验并决定检测机构是否有能力操作具体指定的实验。
13. 批次,测试频率和实验方法的选择
13.1 批次的定义 - 一批必须包含以下一种钝化部件,由操作者自行选择: 13.1.1 含有类似合金和生产工艺并在同一天或同一时间段内进行预处理和钝化处理后钝化 部件可确保钝化处理结果的一致性。 13.1.2 同一产品同一规格同一装运期的钝化部件。 13.1.3 涉及几种部件时,必须是经过了整个生产流程的不锈钢才能成为钝化部件。 13.2 除非购买协议具体说明需要测试的次数,每批测试一次就足够了。 13.3 购买协议需具体说明,每批不锈钢部件都要进行以下一种或几种测试实验。不是所有 的测试方法都适合不同级别的不锈钢。(详见备注2。) 13.3.1 实验 A- 水浸测试 13.3.2 实验 B- 高湿度测试 13.3.3 实验 C- 喷盐测试 13.3.4 实验 D- 硫酸铜测试 13.3.5 实验 E- 铁氰化钾硝酸盐测试
4. 订购须知
4.1 购买者负责指定适应特定材料的实验方法。该标准是美国联邦标准规范 QQ-P-35C 的代 替标准。该标准是否适合使用由购买者决定。 4.2 除非由购买者特别说明,适用于不锈钢部件的化学处理方法必须从上述钝化处理方法中 选择。
5. 材料及钝化处理的准备
5.1 钝化处理应使用下列一种或几种方法。对某一特定级别的不锈钢的特定处理方法的有效 性由其结果符合测试要求的程度来说明: 5.1.1 硝酸法 5.1.2 柠檬酸法 5.1.3 其他化学处理方法,包括电化学处理方法 5.1.4 中和法,以及 5.1.5 后清洗发 5.2 材料: 5.2.1 用于钝化处理的化学物质必须能产生符合该标准中一种或多种要求的钝化表层。根据 测试用不锈钢的大小和数量,注意所选化学物质的计量、浓度、纯净度及化学反应的温度。 5.2.2 操作员必须记录钝化溶液的浓度和温度以此证明处理每批不锈钢都需要特定的钝化 环境。该记录用于消费者购买不锈钢时检测产品使用。操作者禁止泄漏专利化学混合物的精 确成份,但是必须对混合物质做唯一的区别标记以便下次使用时精确无误。 5.2.3 操作者负责安全处理化学处理过程中产生的所有物质。 5.3 钝化处理的准备 5.3.1 钝化处理前的预处理方法和过程,包括除锈和酸浸的机械和化学处理方法是否单独使 用或者两者结合使用,必须符合实验 A380的要求。如果需要电化学清洗,必须按照实验 B254
的方法进行。 5.3.2 初加工过的不锈钢表面无油渍、油脂、锈斑、斑点及其他异物。 5.3.3 包括酸浸在内的对不锈钢进行的最后的表面处理,检测前不需要进行进一步的钝化处 理,除非购买者有特殊的要求。
6. 硝酸溶液处理法
6.1 钝化处理 6.1.1 在规定的时间特定的温度下,将不锈钢部件浸泡在以下水溶液中。 6.1.1.1 硝酸溶液1 - 该溶液中含有20-25%(容积百分比)的硝酸溶液和2.5+0.5%(重量 百分比)的重铬酸钠。在120-130华氏度(49-54摄氏度)的温度下,将不锈钢部件至少浸 泡20分钟的时间。 6.1.1.2 硝酸溶液2 - 该溶液含有20-45%(容积百分比)的硝酸溶液。在70-90华氏度(21-32 摄氏度)的温度下,将不锈钢部件至少浸泡30分钟的时间。 6.1.1.3 硝酸溶液3 - 该溶液含有20-25%(容积百分比)的硝酸溶液。在120-140华氏度 (49-60摄氏度)的温度下,将不锈钢部件至少浸泡20分钟的时间。 6.1.1.4 硝酸溶液4 - 该溶液含有45-55%(容积百分比)的硝酸溶液。在120-130华氏度 (49-54摄氏度)的温度下,将不锈钢部件至少浸泡30分钟的时间。 6.1.1.5 硝酸溶液5 - 其他温度,时间和不同浓度硝酸的组合,不管该溶液中有没有其他例 如催化剂、抑制剂或合适的溶液等等的化学物质,只要可以生成符合测试要求的不锈钢部件 的溶液都可以。 6.2 清水漂洗 - 从钝化溶液中去除不锈钢部件后立即进行全面的清洗。可在静止的水中清 洗,可在流动的水中清洗,也可进行喷洗,或者几种方法结合起来清洗。清洗时也可使用单 独的化学方法来中和(详见9.1)钝化媒介。最后的漂洗液固体含量最多为200%。
7. 柠檬酸溶液处理法
7.1 钝化处理方法 7.1.1 在规定的时间特定的温度下,将不锈钢部件浸泡在以下水溶液中。 7.1.1.1 柠檬酸溶液1 - 该溶液中含有4-10%(重量百分比)的柠檬酸溶液。在140-160华氏 度(60-71摄氏度)的温度下,将不锈钢部件至少浸泡4分钟的时间。 7.1.1.2 柠檬酸溶液2 - 该溶液中含有4-10%(重量百分比)的柠檬酸溶液。在120-140华氏 度(49-60摄氏度)的温度下,将不锈钢部件至少浸泡10分钟的时间。 7.1.1.3 柠檬酸溶液3 - 该溶液中含有4-10பைடு நூலகம்(重量百分比)的柠檬酸溶液。在70-120华氏 度(21-49摄氏度)的温度下,将不锈钢部件至少浸泡20分钟的时间。 7.1.1.4 柠檬酸溶液4 - 其他温度,时间和不同浓度柠檬酸溶液的组合,不管该溶液中有没 有其他例如催化剂、抑制剂或合适的溶液等等的化学物质用于提高清洗效率,只要可以生成 符合测试要求的不锈钢部件的溶液都可以。 7.1.1.5 柠檬酸溶液5 - 其他温度,时间和不同浓度柠檬酸溶液的组合,不管该溶液中有没 有其他例如催化剂、抑制剂或合适的溶液等等的化学物质用于提高清洗效率,只要可以生成 符合测试要求的不锈钢部件的溶液都可以。浸泡溶液的 PH 值在1.8-2.2之间。 7.2 清水漂洗 - 从钝化溶液中去除不锈钢部件后立即进行全面的清洗。可在静止的水中清
2. 相关文献
2.1 美国材料试验学会标准: A 380 对不锈钢部件,设备和 ASTM 年度图书卷 01.03.中材料的清洗,除锈及去钝化的实验 B 117 对 ASTM 年度图书卷 03.02.中材料进行喷盐(雾化)的实验 C 254 对不锈钢材料(ASTM 年度图书卷 02.05.中材料)编制及电镀的实验 2.2 联邦的规范标准: QQ-P-35C 耐腐蚀钢材的钝化处理方法