冷轧板的退火工艺:连续退火和罩式退火的比较
冷轧板带生产技术与管理之四-退火处理

焊机类型
焊机类型及型号说明
型号: MSW-C150D-26-2R2P) MSW: MASH SEAM WELDER(窄搭接焊机) C: C型架并带有铡刀式剪子 150D: 电源的额定容量是150KVA 2: 带钢最大厚度是2.3cm 6: 带钢最大宽度是1850cm 2R: 2个压轮和2个焊轮 2P: 2个通道(带有一个预载料通道)
八、全氢罩式退火炉的特点
九、退火方式比较
十、罩式退火工艺流程
60万吨的产能,约需 要退火炉35~40座, 投资大约6~7亿元人 民币。
例:年产60万吨的罩式退火机组构成
十一、罩式退火车间平面布置举例
十二、罩式退火工艺流程图
十三、全氢罩式退火炉控制界面举例
十四、罩式退火炉工艺曲线
连续退火篇
2、高强钢的退火原理
BH钢强化原理示意图
DP及TRIP钢种强化机理示意图
连退机组各钢种退火曲线
1、CQ
2、DQ(LC)
3、DQ(ULC)
4、DDQ
5、EDDQ
6、S-EDDQ
7、CQ-HSS 440
8、CQ-HSS 590
9、DQ-HSS 340 +DQ-HSS 440
10、DDQ-HSS 340 + DDQ-HSS 440
ULC类别钢种退火原理示意图
2、高强钢的退火原理
连续退火生产高强钢强化机理: 1)析出强化:通过在钢中形成分散状的、由碳与添加元素所形 成碳化物的析出物导致位错移动受阻,从而导致钢的强度增加。 析出强化采用的添加元素有钛、铌、钒等。 2)固溶强化:因固溶元素原子存在导致铁素体晶格产生畸变, 而导致位错运动受阻,并由此导致钢强度增加。通常采用的固溶 强化元素有硅、锰、磷等。 3)相变强化:由马氏体和贝氏体等低温相变生成物分散而导致 的强化; 4)晶粒细化:通过加快冷却速度,细化晶粒
(完整word版)连续退火与罩式退火工艺比较_F

邯钢附企公司冷轧工程连续退火与罩式退火工艺比较10:29 AM目录1.概述 (1)2.两种工艺的比较 (2)2.1罩式退火工艺 (2)2.2 连续退火工艺 (4)2.3 两种退火工艺比较 (4)2.4 连续退火工艺的优势 (5)2.5实例 (6)3.生产成本比较 (8)4。
工程投资比较 (9)5.工程退火工艺选择建议 (9)1.概述带钢经过冷轧机大压下率冷轧,晶粒组织被延伸和硬化,不能进行进一步的加工成形,因此必须进行再结晶退火,控制晶粒的成长形成适当的组织,恢复材料塑性,这就是退火的目的。
低碳钢的退火通常是在还原性气氛中加热到A1点温度附近,并在该温度下保温一段时间后冷却,这种退火称为光亮退火。
根据退火炉的形式和操作方法可分为罩式退火工艺和连续退火工艺。
罩式退火工艺(也称为分批退火)是指对冷轧后的钢卷按工序顺序分别在脱脂机组(若需要)、罩式退火炉、平整机组、重卷机组进行相应处理,以整卷分批次退火生产冷轧商品卷的工艺。
在罩式退火工序,钢卷除装炉和卸炉外,以紧卷方式在炉内按一定卷数堆垛、静止放置,随炉温升降而加热和冷却。
罩式退火时钢卷有充分的加热和均热时间,使晶粒生长和取向结晶增加,通过缓慢的冷却过程使均热时多余的固溶碳和氮充分析出,得到良好的材质.紧卷的缺点在于热量传到钢卷内部缓慢,生产率低;由于钢卷多层叠压,造成各层钢卷间和同一钢卷内有温度差,这样钢卷沿长度方向机械性能不均;同时冷却时,紧卷收缩易造成带钢粘连。
连续退火工艺是将清洗、退火、平整、拉矫和分卷等工序集成在一条连续生产线上,将带钢进行连续展开退火生产冷轧商品卷的工艺。
具有生产周期短、布置紧凑、便于生产管理、劳动生产率高以及产品质量优良等优点。
因为连续生产,退火周期非常短,仅5分钟左右。
用连续退火时其特有的快速加热和冷却可得到较硬的材质,早期的连续退火机组大都用于硬质镀锡原板生产,不作为软钢板的退火。
近些年来通过钢的成分调整和热轧高温卷取使再结晶晶粒变大,经短时间过时效处理固溶碳完全析出,可以用连续退火生产有深冲性的冷轧钢板。
冷轧板和热轧板的区别-罩式炉退火

冷轧板和热轧板的区别-罩式炉退火来源:江苏邦泰炉业有限公司 /冷轧板和热轧板的区别-罩式炉退火1.热轧用连铸板坯或初轧板坯作原料,经步进式加热炉加热,高压水除鳞后进入粗轧机,粗轧料经切头、尾、再进入精轧机,实施计算机控制轧制,终轧后即经过层流冷却(计算机控制冷却速率)和卷取机卷取、成为直发卷。
直发卷的头、尾往往呈舌状及鱼尾状,厚度、宽度精度较差,边部常存在浪形、折边、塔形等缺陷。
其卷重较重、钢卷内径为760mm。
(一般制管行业喜欢使用。
)将直发卷经切头、切尾、切边及多道次的矫直、平整等精整线处理后,台车炉再切板或重卷,即成为:热轧钢板、平整热轧钢卷、纵切带等产品。
热轧精整卷若经酸洗去除氧化皮并涂油后即成热轧酸洗板卷。
该产品有局部替代冷轧板的趋向,价格适中,深受广大用户喜爱。
2.冷轧用热轧钢卷为原料,经酸洗去除氧化皮后进行冷连轧,其成品为轧硬卷,由于连续冷变形引起的冷作硬化使轧硬卷的强度、硬度上升、韧塑指标下降,因此冲压性能将恶化,只能用于简单变形的零件。
轧硬卷可作为热镀锌厂的原料,罩式炉因为热镀锌机组均设置有退火线。
轧硬卷重一般在6~13.5吨,钢卷内径为610mm。
一般冷连轧板、卷均应经过连续退火(CAPL机组)或罩式炉退火消除冷作硬化及轧制应力,达到相应标准的力学性能指标。
冷轧钢板的表面质量、外观、尺寸精度均优于热轧板,且其产品厚度右轧薄至0.18mm左右,因此深受广大用户罩式炉退火青睐。
以冷轧钢卷为基板进行产品的深加工,成为高附加值产品。
如电镀锌、热镀锌、耐指纹电镀锌、彩涂钢板卷及减振复合钢板、PVC复膜钢板等,使这些产品具有美观、高抗腐蚀等优良品质,得到了广泛应用。
冷轧钢卷经退火后必须进行精整,包括切头、尾、切边、矫平、平整、重卷、或纵剪切板等。
冷轧产品广泛应用于汽车制造、家电产品、仪表开关、建筑、办公家具等行业。
Tags: 罩式炉退火。
冷轧工艺介绍
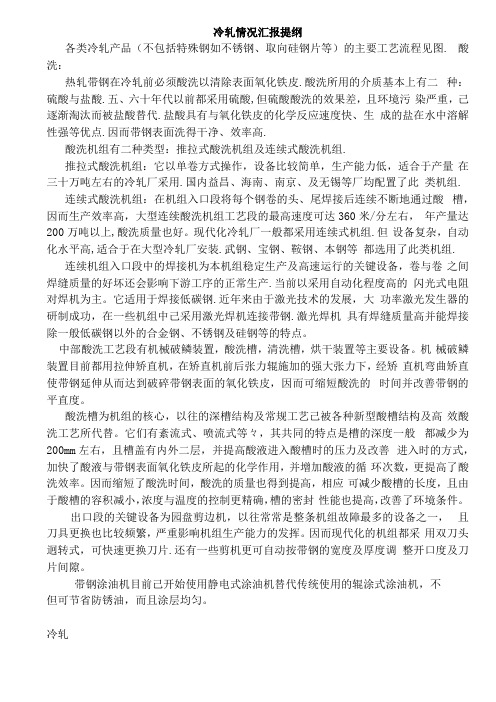
冷轧情况汇报提纲各类冷轧产品(不包括特殊钢如不锈钢、取向硅钢片等)的主要工艺流程见图. 酸洗:热轧带钢在冷轧前必须酸洗以清除表面氧化铁皮.酸洗所用的介质基本上有二种:硫酸与盐酸.五、六十年代以前都采用硫酸,但硫酸酸洗的效果差,且环境污染严重,己逐渐淘汰而被盐酸替代.盐酸具有与氧化铁皮的化学反应速度快、生成的盐在水中溶解性强等优点.因而带钢表面洗得干净、效率高.酸洗机组有二种类型:推拉式酸洗机组及连续式酸洗机组.推拉式酸洗机组:它以单卷方式操作,设备比较简单,生产能力低,适合于产量在三十万吨左右的冷轧厂采用.国内益昌、海南、南京、及无锡等厂均配置了此类机组.连续式酸洗机组:在机组入口段将每个钢卷的头、尾焊接后连续不断地通过酸槽,因而生产效率高,大型连续酸洗机组工艺段的最高速度可达360米/分左右,年产量达200万吨以上,酸洗质量也好。
现代化冷轧厂一般都采用连续式机组.但设备复杂,自动化水平高,适合于在大型冷轧厂安装.武钢、宝钢、鞍钢、本钢等都选用了此类机组.连续机组入口段中的焊接机为本机组稳定生产及高速运行的关键设备,卷与卷之间焊缝质量的好坏还会影响下游工序的正常生产.当前以采用自动化程度高的闪光式电阻对焊机为主。
它适用于焊接低碳钢.近年来由于激光技术的发展,大功率激光发生器的研制成功,在一些机组中己采用激光焊机连接带钢.激光焊机具有焊缝质量高并能焊接除一般低碳钢以外的合金钢、不锈钢及硅钢等的特点。
中部酸洗工艺段有机械破鳞装置,酸洗槽,清洗槽,烘干装置等主要设备。
机械破鳞装置目前都用拉伸矫直机,在矫直机前后张力辊施加的强大张力下,经矫直机弯曲矫直使带钢延伸从而达到破碎带钢表面的氧化铁皮,因而可缩短酸洗的时间并改善带钢的平直度。
酸洗槽为机组的核心,以往的深槽结构及常规工艺己被各种新型酸槽结构及高效酸洗工艺所代替。
它们有紊流式、喷流式等々,其共同的特点是槽的深度一般都减少为200mm左右,且槽盖有内外二层,并提高酸液进入酸槽时的压力及改善进入时的方式,加快了酸液与带钢表面氧化铁皮所起的化学作用,并增加酸液的循环次数,更提高了酸洗效率。
冷轧罩式退火工艺及原理201807

应力过大造成的粘结风险,尤其对于特殊规格,根据实际温度差采用
相应时间的带罩缓慢冷却,降低冷却过程中的压应力,最大程度上减 少粘结风险;同时合理配炉,采用规格和卷位的合理搭配,减少易发
生粘结钢卷的粘结倾向。
• 平整生产的张力和速度控制:对于粘结较严重的钢卷在采用大张力和 高速生产,大于500m/min,使粘结情况减弱。
轧钢工培训材料
2018年7月
罩式退火工艺及原理
1、冷轧工序组织变化 2、退火原因 3、退火目的及作用 4、罩退与连续退火线比较 5、罩式退火工艺流程图 6、常用退火工艺曲线 7、罩式退火温度分布特点 8、退火粘结问题 9、钢卷在加热过程热应力分布
1、冷轧工序组织变化
酸轧工序压下率控制标准,以及带 钢组织演变机理和特点
加热过程的温度分布
冷却过程的温度分布
因钢卷整卷退火,在退火过程中温度存在差异。加热过程中,钢卷 外圈温度高芯部温度低,钢卷膨胀外圈受拉应力,内圈受压应力; 反之在冷却过程中外圈温度低芯部温度高,钢卷整体外圈受压应力 ,内圈受拉应力。
8、退火粘结问题
在冷硬卷的紧卷立卷再结晶退火过程中,经常发生相邻卷层间粘到一 起,增加了后道工序平整机的开卷张力,并且在开卷过程中会造成板 带撕裂,出现皱痕等情况,并且因同样的粘结力会造成不同程度板形 缺陷,这种缺陷就是我们通常称为的罩式炉粘钢。
4、罩退与连续退火线比较区别
• 罩式退火:生产周期长(几十个小时), 与清洗线、平整线分开布置,整体联成一条冷板生产流程,但 可选择的进行脱脂清洗,且钢种及规格对整体生产的影响较小, 可小批量灵活的组织生产,单炉台生产,炉台数量可根据产量 和品种变化随时增减,中间工序有库存缓冲,产量和品种适应 能力强,适合多品种,小批量生产及试验生产。 • 连续退火:生产周期短(几分钟),脱脂清洗、退火、平整联 成一条整体生产线,生产效率高,但受计划影响启停和规格品 种切换等成本高,产品规格覆盖范围不宜太宽, 产量不宜太低。 适合大批量,少品种生产。
罩式退火和连续退火优缺点
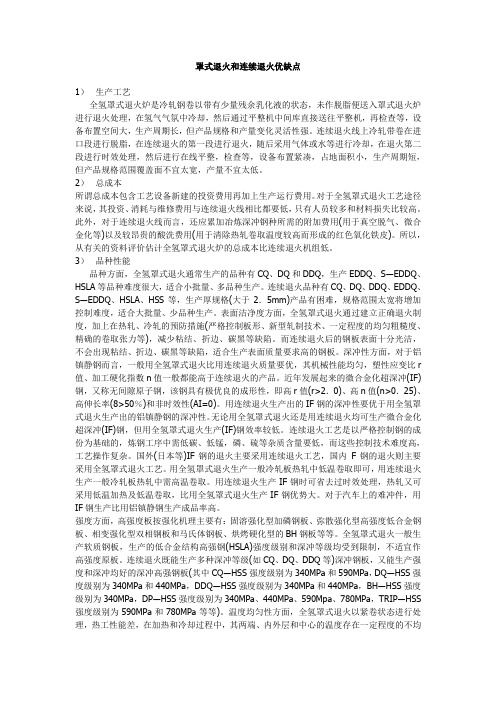
罩式退火和连续退火优缺点1)生产工艺全氢罩式退火炉是冷轧钢卷以带有少量残余乳化液的状态,未作脱脂便送入罩式退火炉进行退火处理,在氢气气氛中冷却,然后通过平整机中间库直接送往平整机,再检查等,设备布置空间大,生产周期长,但产品规格和产量变化灵活性强。
连续退火线上冷轧带卷在进口段进行脱脂,在连续退火的第一段进行退火,随后采用气体或水等进行冷却,在退火第二段进行时效处理,然后进行在线平整,检查等,设备布置紧凑,占地面积小,生产周期短,但产品规格范围覆盖面不宜太宽,产量不宜太低。
2)总成本所谓总成本包含工艺设备新建的投资费用再加上生产运行费用。
对于全氢罩式退火工艺途径来说,其投资、消耗与维修费用与连续退火线相比都要低,只有人员较多和材料损失比较高。
此外,对于连续退火线而言,还应累加冶炼深冲钢种所需的附加费用(用于真空脱气、微合金化等)以及较昂贵的酸洗费用(用于清除热轧卷取温度较高而形成的红色氧化铁皮)。
所以,从有关的资料评价估计全氢罩式退火炉的总成本比连续退火机组低。
3)品种性能品种方面,全氢罩式退火通常生产的品种有CQ、DQ和DDQ,生产EDDQ、S―EDDQ、HSLA等品种难度很大,适合小批量、多品种生产。
连续退火品种有CQ、DQ、DDQ、EDDQ、S―EDDQ、HSLA、HSS等,生产厚规格(大于2.5mm)产品有困难,规格范围太宽将增加控制难度,适合大批量、少品种生产。
表面洁净度方面,全氢罩式退火通过建立正确退火制度,加上在热轧、冷轧的预防措施(严格控制板形、新型轧制技术、一定程度的均匀粗糙度、精确的卷取张力等),减少粘结、折边、碳黑等缺陷。
而连续退火后的钢板表面十分光洁,不会出现粘结、折边、碳黑等缺陷,适合生产表面质量要求高的钢板。
深冲性方面,对于铝镇静钢而言,一般用全氢罩式退火比用连续退火质量要优,其机械性能均匀,塑性应变比r 值、加工硬化指数n值一般都能高于连续退火的产品。
近年发展起来的微合金化超深冲(IF)钢,又称无间隙原子钢,该钢具有极优良的成形性,即高r值(r>2.0)、高n值(n>0.25)、高伸长率(8>50%)和非时效性(AI=0)。
冷轧罩式退火炉工艺

冷轧罩式退火炉工艺
冷轧罩式退火炉工艺是一种用于冷轧钢板的热处理工艺,目的是通过退火处理改善钢板的机械性能和表面质量。
该工艺主要分为以下几个步骤:
1. 预处理:将冷轧钢板进行预处理,包括除油、切割等工序,确保钢板表面干净。
2. 裂解和脱碳:将冷轧钢板放入罩式退火炉中,加热至高温,使钢板中的碳元素析出并迁移到钢板表面,从而减少钢板中的碳含量。
同时,通过裂解处理,使钢板内的应力得以释放。
3. 保温和冷却:在高温环境中保温一段时间,使钢板内部温度均匀分布,然后逐渐将炉温降低,进行冷却。
冷却速度可以根据需要进行调整,以控制钢板的组织和性能。
4. 清洗和抛光:冷轧钢板经过退火处理后,表面可能会出现一定程度的氧化和残余物,需要进行清洗和抛光,使钢板表面光洁。
5. 检验和包装:对退火后的钢板进行检验,包括尺寸、平直度、表面质量等指标的检测。
合格的钢板经过包装后,可以进行下一步的使用或销售。
钢铁工业退火板卷-连续退火法、罩式退火法的系数计算

钢铁工业退火板卷-连续退火法、罩式退火法的系数计算钢铁工业中,退火是一种重要的热处理工艺,用于改善钢材的力学性能和组织结构。
在退火过程中,常用的两种方法是连续退火法和罩式退火法。
1. 连续退火法:连续退火法是指将钢板卷通过连续生产线进行退火。
在连续退火过程中,钢板经过预热、退火、冷却等多个连续阶段。
该方法可以有效提高生产效率。
计算连续退火法的系数时,通常需要考虑以下几个因素:a. 加热速度:加热速度对退火效果有很大影响,通常以升温速度来表示。
升温速度越快,钢板的退火效果越差。
系数可根据实际经验确定。
b. 保温时间:保温时间是指钢板在退火温度下停留的时间。
保温时间越长,退火效果越好。
系数可根据实际经验确定。
c. 冷却速度:冷却速度是指钢板从退火温度降温的速度。
冷却速度越慢,退火效果越好。
系数可根据实际经验确定。
2. 罩式退火法:罩式退火法是指将钢板卷放入具有特定气氛的容器中进行退火。
在罩式退火过程中,钢板表面被罩中的气氛包围,并通过加热使其均匀退火。
该方法常用于对钢板表面进行退火,以达到改善表面性能的目的。
计算罩式退火法的系数时,主要考虑以下几个因素:a. 罩气体成分:罩气体成分对钢板的退火效果有很大影响,通常要求罩气体中含有一定的还原性气体(如氢气)。
系数可根据实际经验确定。
b. 罩气体压力:罩气体的压力对退火效果有一定影响。
通常要求罩气体的压力保持在一定范围内。
系数可根据实际经验确定。
c. 加热温度:加热温度是罩式退火的关键参数之一。
加热温度越高,退火效果越好,但同时也会增加能耗和材料损失。
系数可根据实际经验确定。
以上是钢铁工业中连续退火法和罩式退火法系数计算的一些基本考虑因素,具体系数的确定需要结合实际生产情况和工艺要求,通过试验和经验总结来确定。
- 1、下载文档前请自行甄别文档内容的完整性,平台不提供额外的编辑、内容补充、找答案等附加服务。
- 2、"仅部分预览"的文档,不可在线预览部分如存在完整性等问题,可反馈申请退款(可完整预览的文档不适用该条件!)。
- 3、如文档侵犯您的权益,请联系客服反馈,我们会尽快为您处理(人工客服工作时间:9:00-18:30)。
冷轧板的退火工艺:连续退火和罩式退火的比较冷轧产品是钢材中的精品,属高端产品,具有加工精细、技术密集、工艺链长、品种繁多、用途广泛等特点。
国际钢铁工业发展实践表明,随着经济社会发展,冷轧产品在钢材消费总量中的比重在不断提高,并发挥着越来越重要的作用。
冷轧后热处理是冷轧生产中的重要工序,冷轧板多为低碳钢,其轧后热处理通常为再结晶退火,冷轧板通过再结晶退火达到降低钢的硬度、消除冷加工硬化、改善钢的性能、恢复钢的塑性变形能力之目的。
冷轧板的再结晶退火在退火炉中进行,冷轧板退火炉分为罩式退火炉和连续退火炉,罩式退火炉又分为全氢罩式退火炉与普通罩式退火炉。
冷轧板退火技术的发展与罩式退火炉和连续退火炉的发展是密不可分的[10]。
退火工艺流程如图2.1所示:图2.1 退火工艺流程示意图表2.4 某钢厂罩式退火炉工艺参数热点/冷点温度CQ:710℃/640℃DQ:710 ℃/660℃DDQ:710 ℃/680℃HSLA:680℃/660℃一般生产中CQ、DQ热点和冷点温度差要大一些。
分别为90 ℃、70 ℃开始喷淋冷却温度内罩表面温度200 ℃,卷心温度:380℃左右生产调试中进行检测试验以确定不同钢卷开始喷淋冷却工艺出炉温度160 ℃出炉吊至终冷台冷却到平整温度约40 ℃图2.3 典型的罩式炉退火工艺温度曲线图罩式退火工艺罩式退火是冷轧钢卷传统的退火工艺。
在长时间退火过程中,钢的组织进行再结晶,消除加工硬化现象,同时生成具有良好成型性能的显微组织,从而获得优良的机械性能。
退火时,每炉一般以4个左右钢卷为一垛,各钢卷之间放置对流板,扣上保护罩(即内罩),保护罩内通保护气体,再扣上加热罩(即外罩),将带钢加热到一定温度保温后再冷却。
罩式退火炉发展十分迅速,2O世纪7O年代的普通罩式退火炉主要采用高氮低氢的氮氢型保护气体(氢气的体积分数2%~4%,氮气的体积分数为96%~98%)和普通炉台循环风机,生产效率低,退火质量差,能耗高;为了弥补普通罩式炉的缺陷,充分发挥罩式炉组织生产灵活,适于小批量多品种生产,建造投资灵活,可分批进行的优点,7O年代末奥地利EBNER公司开发出HICON/H 炉(强对流全氢退火炉),8O年代初德国LOI公司开发出HPH炉(高功率全氢退火炉)。
由于这两种全氢炉生产效率比普通罩式炉提高一倍,产品深冲性良好,表面光洁,故在全世界范围内得到迅速推广和应用。
全氢炉主要分布在欧洲各国,90年代全世界此类退火炉已达到了500多座,分布在世界2O多个国家和地区。
9O年代以后,我国的罩式退火炉也逐渐采用高氢型保护气体(氢气的体积分数为75%,氮气的体积分数为25%)或全氢型保护气体(氢气的体积分数为100%)和强对流炉台循环风机,生产效率有了大幅度提高,退火质量明显改观,能耗大幅下降。
随着对冷轧板性能的日益提高,普通的氮氢型罩式退火炉正逐渐被淘汰。
目前广泛使用的全氢罩式退火炉具有以下明显优势:采用大功率、大风量的炉台循环风机,加速了气体循环,强化了对流传热;采用全氢作为保护气氛,充分发挥了氢气质量轻、渗透能力强、导热系数大、还原能力强的优势;采用气--水冷却系统,起到了快速冷却的目的,提高了生产效率,改善了钢卷退火质量[11 12]。
全氢罩式退火炉与普通罩式退火炉的比较全氢罩式退火炉由于氢气的热传导性好,渗透力强,其传热速度比氮气快,强化了对流传热,加热时内罩壁热量对带钢卷以及带钢卷层间的传热(冷却时方向相反)速度要比普通罩式退火炉快得多,因此使用全氢并与大叶轮循环风机配合作强对流循环,可获得满意的加热或冷却效果,从而大大缩短了处理带钢卷的加热冷却时间,一般全氢罩式退火炉生产效率比普通罩式退火炉高40%一60%。
而且在大量生产情况下,可以做到钢卷外部无过热。
全氢罩式退火炉由于炉温比较均匀,加热时无局部过热现象,因此处理后的带钢卷机械性能均匀,同时也消除了普通罩式退火炉中所出现的带钢粘结现象。
另外,由于微小氢原子在带钢卷圈层中穿透非常快,在100℃时,它使带钢卷上残留的润滑剂还原为碳氢化合物,从而降低其沸点,加快了碳氢化合物的蒸发,不致发生润滑剂的分解而残留在带钢卷的表面上。
在600℃时,强烈的还原性氢可以有效地将残留氧化物还原形成水蒸汽,这种水蒸汽与带钢卷上残留的碳反应,形成一氧化碳,随氢气一起排出炉外。
因此在全氢罩式退火处理的宽带钢卷有较高的表面光洁度。
燃料消耗量低。
全氢罩式退火炉由于强对流传热,显著提高传热效率,使燃料消耗减少。
电能消耗低。
全氢罩式退火炉由于氢比重低,在高温时,循环风机功率可大幅度下降,其节能的电费就可弥补氢气费用。
保护气体消耗量低。
全氧罩式退火炉采用全金属封闭炉台,在整个过程中,不需氢气冲洗绝热材料释放的杂质。
在操作上,在开始吹扫和加热升温初期采用氮气,然后随着温度的升高转换为氢气,流量由小到大,在进入加热段的2/3处,即关闭氢气出口阀,停止供氢气,在冷却时由于氢气体积缩小、压力下降,此时需补充少量氢气,以保持内部压力稳定。
总的来说,氢消耗量还是低的。
氮气仅在退火开始及结束前清扫时使用,故氮气用量比传统罩式炉减少14%左右。
连续退火1)连续退火工艺罩式退火炉尽管建设投资小而灵活。
组织生产方便,但其退火工艺有不足之处,尤其普通罩式退火炉更明显,存在生产周期长、生产过程不连续,产品机械性能不够均匀和表面质最不佳以及劳动定员多、占地面积大等缺点。
为了克服以上这些缺点,日本几家主要钢铁公司致力于连续退火工艺的开发研究,将电解清洗、连续退火、平整、精整检查等各主要生产工序联成一体,组成连续退火生产线,最终取得了成功。
70年代共建了3条连续退火线,都在日本。
进入80年代,世界各钢铁厂相继建设连续退火线,1992年全世界已有49条连续退火线。
由于连续退火机组具有生产效率高(生产周期由10天左右缩短到lh以内),产品品种多样化,产品质量高,生产成本低等许多罩式退火工艺无法比拟的优势,连续退火技术得到了迅速发展。
目前,日本用连续退火工艺生产的冷轧板己占总量的80%左右。
近年来,连续退火线在国内大型钢厂(宝钢、鞍钢、武钢等)迅速崛起,从而带动冷轧生产向专业化、高速化、现代化方向发展。
连续退火机组有四种类型:NSC—CAPL(日本新日铁)、KM—CAL(日本川崎制铁)、NKK—CAL(日本钢管)、CRM—HOWAQ(比利时)。
由于CRM—HOWAQ类型一次冷却采用热水,世界上发展较慢,所以主要是前三种类型。
前三种连续退火机组的退火技术有其共同点,主要是通过控制一次冷却速度、一次冷却终了温度和过时效温度,使钢中固溶碳充分析出。
然而这三种连续退火机组在一次冷却技术、张力控制和板温控制方面各有其不同的特点。
一次冷却技术是连续退火技术的核心,它直接影响连续退火机组对产品品种的适应能力和改善产品机械性能[13]。
2)连续退火技术的发展(1)一次冷却技术一次冷却技术最为关键,其优劣直接影响产品机械性能,退火周期及机组所适应的品种。
各种一次冷却技术发展情况如下:(1)气体喷射冷却(GJC):由新日铁70年代开发,采用喷射循环保护气体进行冷却,冷却速度慢,约5—3O℃/s,使过时效时间变长。
(2)冷水淬冷却(WQ):由日本钢管开发,将炉内带钢由700~850℃冷却到560℃,再水淬冷却至65℃左右,冷却速度为500—2000℃/s,为去除带钢表面氧化膜,带钢要经酸洗、中和、漂洗、烘干,再重新加热过时效或回火。
由于冷却速度极快,仅1min过时效就能析出过饱和固溶碳,生产深冲板。
另外钢中加入适量舍金元素,能经水淬一次冷却形成双相钢、BH钢等。
这种方法冷却速度过快,冷却终点温度难以控制,并且能耗高。
(3)辊式冷却:日本钢管1982年研制成功这种技术,并用于神户制钢的连续退火机组上。
辊式冷却是使带钢与内部通水冷却的辊子接触,通过热传导对带钢冷却,冷却速度为100~300℃/s,改变带钢与水冷辊的接触时问可调节冷却速度。
这种方法冷却速度快,并可准确控制冷却终点温度,但冷却均匀性差,冷却辊工作条件恶劣,寿命低。
日本钢管还开发了水淬和辊冷联合冷却(WQ+RC)技术,兼有2种冷却的特点。
(4)高速气体喷射冷却(HGJC,H—GJC): HGJC是由川崎制铁与三菱重工共同开发,采用窄缝喷嘴向带钢两面喷射气体,调节风机出口的阀板改变冷却速度,冷却装置分成多个区段,以使带钢宽度方向冷却均匀。
喷嘴喷射的气体中含氢,这能增加导热性,从而可加速一次冷却,冷却速度可达1O--100℃/s。
HGJC技术与日本钢管的RQ(辊冷)技术结合可以扩大冷却速度范围达50--150℃/s,板形与表面质量比单独RQ要好。
新日铁1987年成功地在八幡厂№2机组上使用了H—GJC技术,其与HGJC不同之处是采用圆柱状喷嘴及挡板,可有效地减轻气体回流,保证带钢宽度方向的均匀冷却,所需电机功率小。
(5)气水双相冷却(ACC):这是新日铁开发的口琴式气流雾化水冷却喷嘴,并采用了参照模式白适应控制法及卡尔曼过滤法的控制系统.能精确控制冷却终点温度4OO±5℃及冷却速度。
ACC的喷嘴有气体侧向喷射窄槽,带宽方向冷却均匀,改变供水流量来调节冷却能力,可保持不同厚度带钢有同一冷却速度。
一次冷却起始温度700℃,气水比>0.13Nm3/1,ACC需要后续表面处理。
(6)热水淬冷却(HOWAC):是新日铁与比利时考柯尔桑布尔钢铁公司联合开发的冷却技术,通过沉没辊的上下移动,使一次冷却的终点温度控制十分简单,并在热水淬系统后设有水雾冷却(一步冷却)用于生产高强度板或镀锡原板,采用HOWAC需要后续表面处理。
各种一次冷却技术特点比较见表2.5:表2.5 一次冷却技术特性比较(2)过时效及回火技术带钢经一次冷却后要经过时效处理,过时效温度控制有3种,多数炉子为400℃等温时效;也有斜坡时效,即逐步降温时效,以加快固溶碳的析出;还有一种为先等温再斜坡过时效。
过时效的时间与一次冷却速度有关,一次冷却速度愈快,过时效时间愈短。
根据一次冷却速度不同,过时效时间约需1.5~5min。
当生产高强度钢板时,一次快冷后,则采用300℃回火l~2.5min。
(3)张力及板温控制技术80年代中期以来,新建连续退火机组趋向高速高产,开发出一系列张力及板温控制技术,也称高速通板技术。
新日铁开发采用的技术有:炉子段高精度张力控制器,炉后设分段张紧辊装置,设中心位置控制器,一次冷却段横向冷却模型控制系统,炉子段张力监测控制系统,炉辊自动速度调节系统,低惯性高响应张力调节系统,以及在过时效段后设置张力辊等等[14]。
日本钢管采用如下技术:交流矢量控制晶体管变换器,多重反射式温度计和动态板温控制模型;川崎制铁开发的技术如下:高功能矢量变换器和低惯性高响应装置,可使张力精度达±98N,利用有限元瓢曲模拟模型设计辊子形状以防止宽带钢瓢曲。