带钢连续退火工艺技术介绍
罩退--连退

首先,罩退、连退都是冷轧退火的工艺,但是由于工艺不一样,得到成品性能也不一样,SPCC是冷轧牌号,一般供应商卖货都有中文注明是连退还是罩退的,钢厂也有材质单的。
罩退,热轧卷在冷轧后,将半成品卷卷心向下,一个个垒起来,大概是二层或者三层,放入到一个罩退退火炉,就是做的想个大罩子一样的退火室,控制温度,充分退火;连退,就是将冷轧卷,一个个卷打开,并且首尾相连(焊接一起)通过一个很大的退火炉,蛇形的,在里面绕来绕去,最后绕出来,完成退火;优劣处:罩退,优点,退火均匀,钢材冲压性能好,缺点,成本高,吨钢价格高50-100元,表面不是很光亮,常有残碳,所以这种钢材最终使用于冲压,汽车等行业,不适用于家电行业,特别是作家电外壳,容易影响后续喷涂;连退,优点,生产速度快,效率高,表面好,清洁光亮,缺点,成本低,力学性能差些,所以这种钢材最终使用于家电行业,不适用于冲压,汽车等行业,冲压成型性差些;1)生产工艺全氢罩式退火炉是冷轧钢卷以带有少量残余乳化液的状态,未作脱脂便送入罩式退火炉进行退火处理,在氢气气氛中冷却,然后通过平整机中间库直接送往平整机,再检查等,设备布置空间大,生产周期长,但产品规格和产量变化灵活性强。
连续退火线上冷轧带卷在进口段进行脱脂,在连续退火的第一段进行退火,随后采用气体或水等进行冷却,在退火第二段进行时效处理,然后进行在线平整,检查等,设备布置紧凑,占地面积小,生产周期短,但产品规格范围覆盖面不宜太宽,产量不宜太低。
2)总成本所谓总成本包含工艺设备新建的投资费用再加上生产运行费用。
对于全氢罩式退火工艺途径来说,其投资、消耗与维修费用与连续退火线相比都要低,只有人员较多和材料损失比较高。
此外,对于连续退火线而言,还应累加冶炼深冲钢种所需的附加费用(用于真空脱气、微合金化等)以及较昂贵的酸洗费用(用于清除热轧卷取温度较高而形成的红色氧化铁皮)。
所以,从有关的资料评价估计全氢罩式退火炉的总成本比连续退火机组低。
(完整word版)连续退火与罩式退火工艺比较_F

邯钢附企公司冷轧工程连续退火与罩式退火工艺比较10:29 AM目录1.概述 (1)2.两种工艺的比较 (2)2.1罩式退火工艺 (2)2.2 连续退火工艺 (4)2.3 两种退火工艺比较 (4)2.4 连续退火工艺的优势 (5)2.5实例 (6)3.生产成本比较 (8)4。
工程投资比较 (9)5.工程退火工艺选择建议 (9)1.概述带钢经过冷轧机大压下率冷轧,晶粒组织被延伸和硬化,不能进行进一步的加工成形,因此必须进行再结晶退火,控制晶粒的成长形成适当的组织,恢复材料塑性,这就是退火的目的。
低碳钢的退火通常是在还原性气氛中加热到A1点温度附近,并在该温度下保温一段时间后冷却,这种退火称为光亮退火。
根据退火炉的形式和操作方法可分为罩式退火工艺和连续退火工艺。
罩式退火工艺(也称为分批退火)是指对冷轧后的钢卷按工序顺序分别在脱脂机组(若需要)、罩式退火炉、平整机组、重卷机组进行相应处理,以整卷分批次退火生产冷轧商品卷的工艺。
在罩式退火工序,钢卷除装炉和卸炉外,以紧卷方式在炉内按一定卷数堆垛、静止放置,随炉温升降而加热和冷却。
罩式退火时钢卷有充分的加热和均热时间,使晶粒生长和取向结晶增加,通过缓慢的冷却过程使均热时多余的固溶碳和氮充分析出,得到良好的材质.紧卷的缺点在于热量传到钢卷内部缓慢,生产率低;由于钢卷多层叠压,造成各层钢卷间和同一钢卷内有温度差,这样钢卷沿长度方向机械性能不均;同时冷却时,紧卷收缩易造成带钢粘连。
连续退火工艺是将清洗、退火、平整、拉矫和分卷等工序集成在一条连续生产线上,将带钢进行连续展开退火生产冷轧商品卷的工艺。
具有生产周期短、布置紧凑、便于生产管理、劳动生产率高以及产品质量优良等优点。
因为连续生产,退火周期非常短,仅5分钟左右。
用连续退火时其特有的快速加热和冷却可得到较硬的材质,早期的连续退火机组大都用于硬质镀锡原板生产,不作为软钢板的退火。
近些年来通过钢的成分调整和热轧高温卷取使再结晶晶粒变大,经短时间过时效处理固溶碳完全析出,可以用连续退火生产有深冲性的冷轧钢板。
介绍连续热镀锌线的退火炉工艺以及节能技术
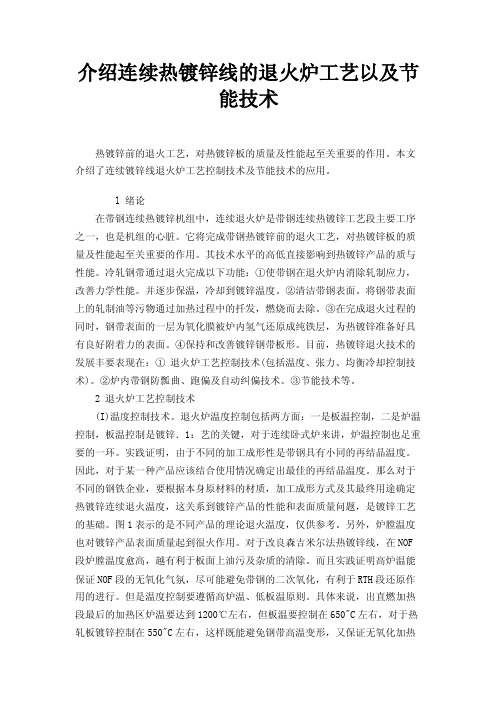
介绍连续热镀锌线的退火炉工艺以及节能技术热镀锌前的退火工艺,对热镀锌板的质量及性能起至关重要的作用。
本文介绍了连续镀锌线退火炉工艺控制技术及节能技术的应用。
l 绪论在带钢连续热镀锌机组中,连续退火炉是带钢连续热镀锌工艺段主要工序之一,也是机组的心脏。
它将完成带钢热镀锌前的退火工艺,对热镀锌板的质量及性能起至关重要的作用。
其技术水平的高低直接影响到热镀锌产品的质与性能。
冷轧钢带通过退火完成以下功能:①使带钢在退火炉内消除轧制应力,改善力学性能。
并逐步保温,冷却到镀锌温度。
②清洁带钢表面。
将钢带表面上的轧制油等污物通过加热过程中的扦发,燃烧而去除。
③在完成退火过程的同时,钢带表面的一层为氧化膜被炉内氢气还原成纯铁层,为热镀锌准备好具有良好附着力的表面。
④保持和改善镀锌钢带板形。
目前,热镀锌退火技术的发展丰要表现在:①退火炉工艺控制技术(包括温度、张力、均衡冷却控制技术)。
②炉内带钢防瓢曲、跑偏及自动纠偏技术。
③节能技术等。
2 退火炉工艺控制技术(I)温度控制技术。
退火炉温度控制包括两方面:一是板温控制,二是炉温控制,板温控制是镀锌.1:艺的关键,对于连续卧式炉来讲,炉温控制也足重要的一环。
实践证明,由于不同的加工成形性是带钢具有小同的再结晶温度。
因此,对于某一种产品应该结合使用情况确定出最佳的再结晶温度。
那么对于不同的钢铁企业,要根据本身原材料的材质,加工成形方式及其最终用途确定热镀锌连续退火温度,这关系到镀锌产品的性能和表面质量问题,是镀锌工艺的基础。
图1表示的是不同产品的理论退火温度,仅供参考。
另外,炉膛温度也对镀锌产品表面质量起到很火作用。
对于改良森吉米尔法热镀锌线,在NOF 段炉膛温度愈高,越有利于板面上油污及杂质的清除。
而且实践证明高炉温能保证NOF段的无氧化气氛,尽可能避免带钢的二次氧化,有利于RTH段还原作用的进行。
但是温度控制要遵循高炉温、低板温原则。
具体来说,出直燃加热段最后的加热区炉温要达到1200℃左右,但板温要控制在650"C左右,对于热轧板镀锌控制在550"C左右,这样既能避免钢带高温变形,又保证无氧化加热气氛。
冷轧不锈钢的退火及酸洗工艺
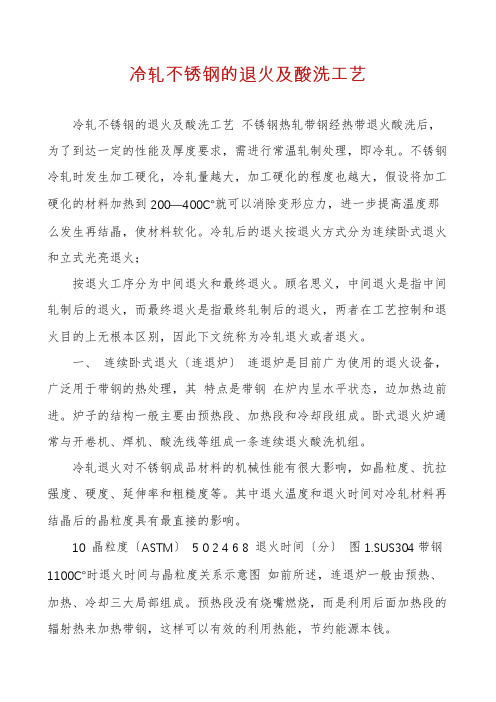
冷轧不锈钢的退火及酸洗工艺冷轧不锈钢的退火及酸洗工艺不锈钢热轧带钢经热带退火酸洗后,为了到达一定的性能及厚度要求,需进行常温轧制处理,即冷轧。
不锈钢冷轧时发生加工硬化,冷轧量越大,加工硬化的程度也越大,假设将加工硬化的材料加热到200—400℃就可以消除变形应力,进一步提高温度那么发生再结晶,使材料软化。
冷轧后的退火按退火方式分为连续卧式退火和立式光亮退火;按退火工序分为中间退火和最终退火。
顾名思义,中间退火是指中间轧制后的退火,而最终退火是指最终轧制后的退火,两者在工艺控制和退火目的上无根本区别,因此下文统称为冷轧退火或者退火。
一、连续卧式退火〔连退炉〕连退炉是目前广为使用的退火设备,广泛用于带钢的热处理,其特点是带钢在炉内呈水平状态,边加热边前进。
炉子的结构一般主要由预热段、加热段和冷却段组成。
卧式退火炉通常与开卷机、焊机、酸洗线等组成一条连续退火酸洗机组。
冷轧退火对不锈钢成品材料的机械性能有很大影响,如晶粒度、抗拉强度、硬度、延伸率和粗糙度等。
其中退火温度和退火时间对冷轧材料再结晶后的晶粒度具有最直接的影响。
10 晶粒度〔ASTM〕5 0 2 4 6 8 退火时间〔分〕图1.SUS304带钢1100℃时退火时间与晶粒度关系示意图如前所述,连退炉一般由预热、加热、冷却三大局部组成。
预热段没有烧嘴燃烧,而是利用后面加热段的辐射热来加热带钢,这样可以有效的利用热能,节约能源本钱。
加热段利用燃料燃烧直接对带钢进行加热,该段一般分为假设干各区,每个区都有高温计来控制和显示温度。
燃烧后高达700多度的废气被废气风机抽出加热室后进入换热器,在换热器内将冷的燃烧空气进行加热〔可加热到400多度〕,加热后的燃烧空气直接被送到各个烧嘴。
换热器的目的在于有效回收废气热量。
l 炉内燃烧条件的管理。
燃料〔液化石油气或天然气〕在炉内的燃烧状况对质量、本钱、热效率等都有很大影响。
空燃比是燃烧管理的一个重要指标。
空燃比越高,燃烧越充分,但是排废量也相应增加,炉内氧含量提高,增加了带钢的氧化程度。
万吨冷轧带钢不锈钢连续退火电解生产线可研

万吨冷轧带钢不锈钢连续退火电解生产线可研1. 引言不锈钢作为一种重要的材料,在工业生产中扮演着至关重要的角色。
为了满足不锈钢的巨大需求,以及提高不锈钢的质量和生产效率,建立一套高效的不锈钢生产线显得尤为重要。
本文将提出一种方案,即万吨冷轧带钢不锈钢连续退火电解生产线的可研。
2. 技术概述本方案旨在建立一套能够高效生产万吨冷轧带钢不锈钢的生产线,该生产线将采用连续退火电解工艺,以提高生产效率和质量稳定性。
具体的技术参数如下:•设备规模:万吨级•生产工艺:冷轧带钢不锈钢连续退火电解•钢带宽度:根据市场需求,可调节•退火温度:根据不同不锈钢材料的工艺要求,可调节•电解电流密度:根据不同不锈钢材料的工艺要求,可调节•生产效率:高达XX吨/小时3. 设备布置为了实现万吨级不锈钢生产,本方案将采用多条连续退火电解线并联的方式进行生产。
具体的设备布置如下:•进料系统:包括料场、卷材切割机和送料机构等。
•冷轧机组:用于将切割好的卷材进行冷轧,得到冷轧带钢。
•连续退火电解线:由多条退火电解段组成,每条段都配备有独立的加热设备和电解槽。
•出料系统:包括退火电解后的不锈钢卷材的剪切和堆垛机构等。
4. 工艺流程生产线的工艺流程如下:1.初始准备工作:将卷材从料场运至冷轧机组,进行切割和冷轧,得到冷轧带钢。
2.连续退火电解:冷轧带钢通过连续退火电解线,依次经过多条退火电解段。
每条段都能控制退火温度和电解电流密度,以满足不同材料的工艺要求。
3.产品出料:经过连续退火电解后,不锈钢卷材通过剪切和堆垛机构进行分离、切割和堆垛,最终得到成品不锈钢卷材。
5. 技术优势万吨冷轧带钢不锈钢连续退火电解生产线具有以下技术优势:•高效生产:通过连续退火电解工艺,生产线可实现高达XX吨/小时的生产效率,满足大规模生产需求。
•质量稳定:连续退火电解工艺能够提供更加稳定的退火温度和电解电流密度,进一步提高了不锈钢的质量稳定性。
•灵活调整:根据不同的市场需求和工艺要求,可以调整钢带宽度、退火温度和电解电流密度等关键参数,以实现生产线的灵活应变能力。
带钢冷轧前退火线工艺流程

带钢冷轧前退火线工艺流程下载温馨提示:该文档是我店铺精心编制而成,希望大家下载以后,能够帮助大家解决实际的问题。
文档下载后可定制随意修改,请根据实际需要进行相应的调整和使用,谢谢!并且,本店铺为大家提供各种各样类型的实用资料,如教育随笔、日记赏析、句子摘抄、古诗大全、经典美文、话题作文、工作总结、词语解析、文案摘录、其他资料等等,如想了解不同资料格式和写法,敬请关注!Download tips: This document is carefully compiled by theeditor. I hope that after you download them,they can help yousolve practical problems. The document can be customized andmodified after downloading,please adjust and use it according toactual needs, thank you!In addition, our shop provides you with various types ofpractical materials,such as educational essays, diaryappreciation,sentence excerpts,ancient poems,classic articles,topic composition,work summary,word parsing,copy excerpts,other materials and so on,want to know different data formats andwriting methods,please pay attention!带钢冷轧前退火线工艺流程:1. 装料,将钢卷装载到退火炉中。
连续退火带钢冷却技术最新进展
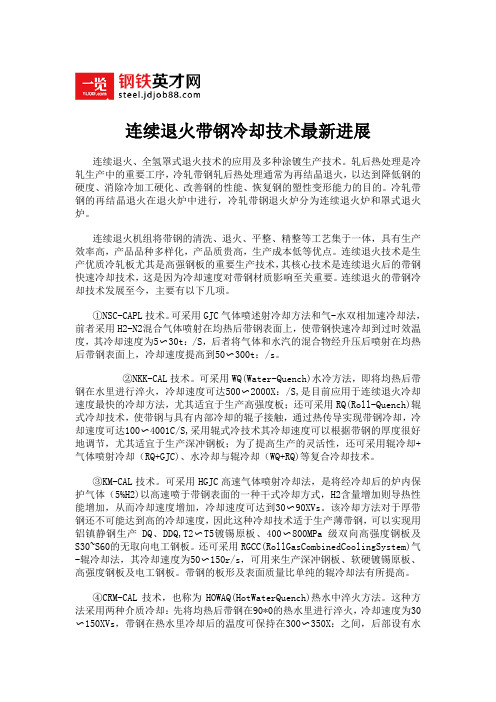
连续退火带钢冷却技术最新进展连续退火、全氢罩式退火技术的应用及多种涂镀生产技术。
轧后热处理是冷轧生产中的重要工序,冷轧带钢轧后热处理通常为再结晶退火,以达到降低钢的硬度、消除冷加工硬化、改善钢的性能、恢复钢的塑性变形能力的目的。
冷轧带钢的再结晶退火在退火炉中进行,冷轧带钢退火炉分为连续退火炉和罩式退火炉。
连续退火机组将带钢的清洗、退火、平整、精整等工艺集于一体,具有生产效率高,产品品种多样化,产品质贵高,生产成本低等优点。
连续退火技术是生产优质冷轧板尤其是高强钢板的重要生产技术,其核心技术是连续退火后的带钢快速冷却技术,这是因为冷却速度对带钢材质影响至关重要。
连续退火的带钢冷却技术发展至今,主要有以下几项。
①NSC-CAPL技术。
可采用GJC气体喷述射冷却方法和气-水双相加速冷却法,前者采用H2-N2混合气体喷射在均热后带钢表面上,使带钢快速冷却到过时效温度,其冷却速度为5〜30t:/S,后者将气体和水汽的混合物经升压后喷射在均热后带钢表面上,冷却速度提高到50〜300t:/s。
②NKK-CAL技术。
可采用WQ(Water-Quench)水冷方法,即将均热后带钢在水里进行淬火,冷却速度可达500〜2000X:/S,是目前应用于连续退火冷却速度最快的冷却方法,尤其适宜于生产高强度板;还可采用RQ(Roll-Quench)辊式冷却技术,使带钢与具有内部冷却的辊子接触,通过热传导实现带钢冷却,冷却速度可达100〜4001C/S,采用辊式冷技术其冷却速度可以根据带钢的厚度很好地调节,尤其适宜于生产深冲钢板;为了提高生产的灵活性,还可采用辊冷却+气体喷射冷却(RQ+GJC)、水冷却与辊冷却(WQ+RQ)等复合冷却技术。
③KM-CAL技术。
可采用HGJC高速气体喷射冷却法,是将经冷却后的炉内保护气体(5%H2)以高速喷于带钢表面的一种干式冷却方式,H2含量增加则导热性能增加,从而冷却速度增加,冷却速度可达到30〜90XVs。
冷轧带钢连续退火机组的技术特点及应用
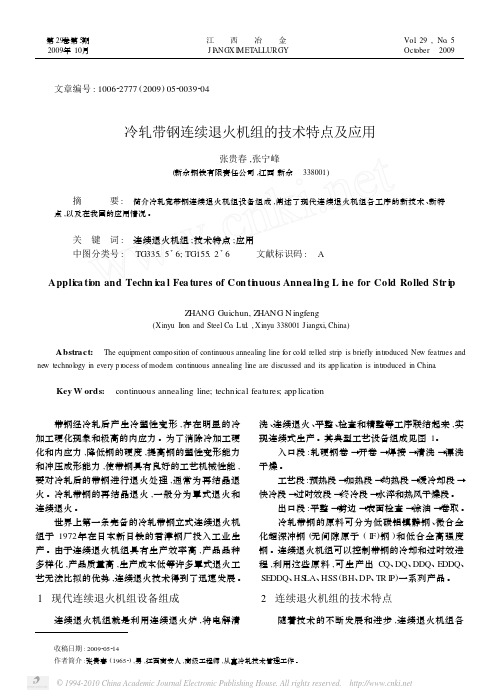
收稿日期:2009205214作者简介:张贵春(19652),男,江西高安人,高级工程师,从事冷轧技术管理工作。
文章编号:100622777(2009)0520039204冷轧带钢连续退火机组的技术特点及应用张贵春,张宁峰(新余钢铁有限责任公司,江西新余 338001) 摘 要: 简介冷轧宽带钢连续退火机组设备组成,阐述了现代连续退火机组各工序的新技术、新特点,以及在我国的应用情况。
关 键 词: 连续退火机组;技术特点;应用中图分类号: TG335.5+6;TG155.2+6 文献标识码: AAppli ca ti on and Techn i ca l Fea tures of Con ti n uous Annea li n g L i n e for Cold Rolled Str i pZ HANG Guichun,Z HANG N ingfeng(Xinyu Ir on and Steel Co .L td .,Xinyu 338001J iangxi,China ) Abstract: The equi pment compositi on of continuous annealing line f or cold relled stri p is briefly intr oduced .Ne w featrues andne w technol ogy in every p r ocess of modern continuous annealing line are discussed and its app licati on is intr oduced in China . Key W ords: continuous annealing line;technical features;app licati on 带钢经冷轧后产生冷塑性变形,存在明显的冷加工硬化现象和极高的内应力。
- 1、下载文档前请自行甄别文档内容的完整性,平台不提供额外的编辑、内容补充、找答案等附加服务。
- 2、"仅部分预览"的文档,不可在线预览部分如存在完整性等问题,可反馈申请退款(可完整预览的文档不适用该条件!)。
- 3、如文档侵犯您的权益,请联系客服反馈,我们会尽快为您处理(人工客服工作时间:9:00-18:30)。
以上所述机理适用于低碳钢。对无间隙(IF)钢,即那些含有钛或铌的理想配比或者略微超过理想配比的合金钢,则毋需过时效处理。由于IF钢中碳和氮元素主要在热轧期间以Ti—C-N或Nb-C2析出,因此由于连续退火中将不会发生时效作用。
目前全世界已经建成和投产近六十多条连续退火机组,随着各种新工艺和新技术的不断开发和完善,连续退火技术正在广泛地取代了罩式退火技术,实现冷轧带纲快速、经济和大规模的生产。在镀锡原板品种上,连续退火机组已经能够生产从T1–T5,DR8–DR10全部调质度;在冷轧板品种上,连续退火机组不仅能够生产DDQ、EDDQ等深冲和超深冲软材,还能够生产各类高强钢(HSS),不仅有CQ级HSS,DQ级HSS,而且还出现了DDQ深冲级HSS、烘烤硬化性DQ级HSS,以及低屈服点超高强钢(LOW YR/SUPER-HSS)和TRIP等高强钢新品种。
成品率高:工艺过程紧凑,避免了罩式退火工艺中钢卷多次搬运擦伤、粘结、折边等缺陷。
当然,在具备上述优点的同时,连续退火机组也ห้องสมุดไป่ตู้在着不足,主要表面在以下方面:
极限规格带钢(厚度大于2.5mm或0.15mm以下的超薄规格)用立式连续退火生产比较困难。
设备和技术复杂,要求技术人员、机组操作和维护人员的素质要求较高。
对热轧条件的分析,热轧的轧制温度必须达到Ar3相变点以上,否则不仅得不到好的金相组织,而且在高温卷取时,晶粒变得粗大,这样rm值和延伸性下降。采用高温卷取的目有:1)碳化物的聚集;2)AIN析出物的聚集。碳化物粗大化后使碳化物的平均间隔变成再结晶晶粒直径数倍以上,晶界移动的阻力因碳化物而大幅度减少。再结晶晶粒直径继续长大,引起屈服应力下降。同样由于快速加热,在再结晶时,碳溶解速度变缓,固溶碳量少,对深冲有利的(111)成份增加,rm值得到了提高。但温度过高,则会产生粗大晶粒,导致材料特性恶化,表面质量也变坏。
在连续退火的典型特性快速冷却期间内,铁素体里碳的溶解急剧降低。随着残遗在固溶体里碳的平衡,只会发生部分渗碳体的析出。较高的冷却速度导致铁基体里出现更大量的过饱和碳,在过时效的初期,原子析出沉淀的高势能受到细散碳化物迅速析出的影响而降低。这些碳化物为那些仍固溶的残留碳析出充当核的作用。由于碳化物之间的距离较短,在过时效期间,游离碳原子便会非均匀析出,即过时效时间会缩短。对于较低的冷却速度,碳化物的析出量较少,由于析出的势能较低,碳化物之间的间距变大,残留固溶碳由于需要经过较长的距离才能扩散至析出核和品界,故需要较长的过时效时间。
使用这二种方法的不同退火周期,可以制造各种质量的钢种,包括CQ(商用级),DQ(冲压级),DDQ(深冲级),HSS(高强钢)等品种。
(1) 低碳软钢、商用钢和冲压钢的连续退火原理(3)
冷轧板要求具备如下的可成形性:CQ板延展性、DQ板的延展性和慢速时效性(低屈服点延长)、DDQ板延展性和非时效性(几乎无屈服点延长)和深冲性(Landford值)。
钢的成分对连续退火带钢的性能影响起着至关重要的作用。铝镇静钢中的碳作为固溶碳,其对钢的时效性和退火时再结晶状态均有很大影响。由于连续退火热处理周期制度多少有些不同,如果考虑时效性、延伸性的最佳平衡,碳的含量在0.02%左右最理想。若在0.002~0.015%范围内,除非增加碳化物形成元素,否则即使加快连续退火的冷却速度、也得不到过时效处理所需要的过饱和度。碳含量0.002%以下的钢与连续退火的热过程无关,时效性良好。若碳含量0.02%以上则含碳量越多,时效性能越好,但随强度升高的同时,延伸率、深冲性变坏。AIN的N在热轧卷取时使其充分析出是非常必要的。AIN析出物数量少,再结晶后的晶粒成长性才变得良好,延伸率也上升,因而希望N的绝对量要少。AI除了起到脱氧剂作用外,还起到固定N的效果。因此在AIN析出中必须添加必要的数量。在一般情况下,热轧时要使AIN完全析出、需要添加比N当量稍多的量。Mn和O相互作用,对再结晶的结合组织有影响。钢中Mn含量高,深冲性rm值降低,并随含固溶碳含量增高,深冲性下降程度越厉害。由于Mn含量能够防止S引起热脆性,故Mn含量不可降得太低,一般为0.10-0.15%以宜。另外,Mn含量越低,过时效时碳化物越容易析出。
表12.5.2.5B-1和表12.5.2.5B-2列出了N厂连续退火机组采用喷气冷却和辊冷生产CQ、DQ、DDQ、EDDQ和U-EDDQ各钢种的化学成份、热轧条件、退火条件和产品的机械性能。
连续退火工艺将脱脂、退火、平整、分卷等数个工序集成在一条机组内,与罩式炉相比,具备有以下优点:(1)(2)
产品质量高:连续退火产品表面光洁,残碳和铁粉含量远低于罩式退火;板型好,性能均匀,缺陷少。
生产率高:生产周期可由原来10天左右缩短到至多1个小时左右,由此生产备料大减,生产过程简化,管理方便。
节省劳动生产力:由于工序的合并,加之连续退火机组较高的自动化程度,使得操作人员数量大量节省。
随着连续退火工艺技术和设备的不断完善和发展,产量和速度也在不断提高,机组最高年产量已经达到和超过100万t/a/(如韩国POSCO光阳2#线和日本川铁的千叶3#线),日本川铁的千叶4#KM-CAL机组最高速度已达1000m/min。
a. 连续退火带钢金属热处理工艺
冷轧板的性能由钢的化学成份、冷热轧制条件以及退火工艺来确定。为了获得良好的带钢成型性,必须调整生产过程中的各道生产条件,从而达到最优控制带钢的析出条件、显微构造和组织的目的。
迄今建造的连续退火机组主要采用了二大类不同的退火周期制度,见图12.5.2.5B-2。
方法一为;加热到退火温度,保温,冷却到过时效温度,在此温度上保温,随后冷到室温。
方法二为:加热到退火温度,用喷气冷却法冷却到某一中间温度,随后快冷到较低温度(如水淬至室温),然后又重新加热到过时效温度,并在此温度上保温一段时间,最后再快冷到室温。生产双相钢时,带钢在第一次快冷后,无需加热到过时效温度过程。
过时效阶段区分二个机理,一个是在晶粒边界处继续析出Fe3C,另一个是铁素体结晶内部的析出。在过时效过程中,Fe3C继续析出,并随时效温度的下降,碳溶解度也在下降。析出的晶核有二种,一种是过时效过程中沿铁素体晶界析出的Fe3C碳化物,一种是始终存在的少量与碳结合的晶格畸变。多余的碳则被固溶在铁素体中。一次冷却速度越快,过时效中固溶碳的析出动能则越大,过时效后钢中铁素体里固溶碳的含量就愈少。另一方面,碳化物的形成对钢的性能会产生影响,结构中细小的碳化物会降低其延伸性,并同时提高材料的屈服强度。铁素体中的固溶碳会引起时效,即随温度和时间的增加,带钢延伸率会降低而屈服限、0.2%延伸极限和抗张强度都会提高。
连续退火过程中加热期间,带钢中碳化物结构将部分或完全被溶解.这取决于含碳量以及碳化物的大小,如图12.5.2.5B-1所示。该过程还受加热速度快慢、退火温度高低和碳化物粗大程度的反作用影响。
钢被加热到退火温度并均热后,碳的溶解达到了平衡,并且根据退火温度会发生有限的晶粒生长。然而,连续退火机组里较高的冷却速度阻碍了固溶碳的析出,使其在冷却阶段的碳化物析出偏离平衡,只有通过调整冷却和过时效参数,才能控制碳化物的分布和固溶碳含量,从而获得合适的机械性能并消除时效影响。
带钢晶粒大小直接影响其屈服限和延伸性,固溶Fe3C的析出物会降低其延伸性。间隙溶解碳和间隙氮的含量以及由于添加铝、硼、钛后与这二种元素形成的AlN、BN、TiN等化合物的含量也都会对机械性能产生较大影响。
冷却和过时效的条件对冷轧低碳钢性能的影响简要解释如下:
带钢在A1温度时,碳在铁素体中溶解度按质量计约为2%,并随温度降低而下降。在均热后的第一次冷却时,Fe3C沿着晶粒边界析出,冷却速度愈慢,则析出量愈多。当第一次冷却结束时,在固溶碳周围或多或少残留着饱和的铁素体。在第一次冷却后,接着是过时效处理过程。
与罩式退火不同,连续退火机组高温均热时间较短,冷却速度较快,因此必须在炼钢时对钢的化学成份作相应调整和控制,为获得满意的再结晶状况和成形特性,须将填隙式溶解元素(碳和氮)以及固溶加强元素(锰,硅和磷)维持在较低含量水平。
带钢在热轧时,就必须满足合适的条件,诸如完全析出以及粗大的碳化物和氮化物的生成。均匀一致大的铁素体晶粒。
对于连续退火条件分析,各种连续退火工艺的根本不同之处在于其采用的急冷速度不同,例如某连续退火工艺中水淬冷却WQ法为2000℃/s,辊冷RQ法200℃/s,所对应的时效处理前者1分钟就够了,而后者要2~3分钟。连续退火的加热速度以20~30℃/S的温升速度就行,对于如图12.5.2.5B-6所示碳化物粗大化的材料,慢慢的加热可以得到良好的rm值。以20~30℃/s的加热速度并充分考虑了再结晶时,可以减少固溶碳并改善集合组织。而均热温度,从再结晶粒得到充分成长的角度上讲,希望有个高的温度,但从能源成本和生产性效率,每种品种选定在700~800℃之间比较适宜。从均热到急冷之间,首先采用喷气缓冷到适当的温度,以防止高温下急速冷却很多细微的碳化物被析出,使延伸性下降。因此有必要在均热后缓冷到适当的温度。然后采用快速冷却,使固溶碳达到过饱和,这样只需短时间的过时效处理就能促使固溶碳析出来。
连续退火中,由于加热速度较快(约10~80℃/秒),故再结晶期间内钢组织不会受到影响。只有在600℃温度范围下,当均热时间足够长时,才能使在罩式退火工艺里对冷轧带材的深冲性起改善作用的AIN析出效应得到应用。由于在连续退火工艺中难以使该均热时间延长,因此通常冷轧低碳钢采用连续退火所能达到的Lankford(rm)值较低(如图12.5.2.5B-3所示),即材料的深冲性不好。
深冲性由材料的组织所决定,并且可以通过调整材料成分和连续退火的保温时间来控制。延伸性和时效性主要受成品板材中碳和氮的存在状态(固溶或析出)的影响,对连铸低碳铝镇静钢,钢中氮元素在材料阶段可由铝固定,但碳的析出应选择适当的时效条件和快冷条件来控制。低碳铝镇静钢适用于CQ和DQ,而IF钢适用于要求无时效特性和对深冲性有要求的DDQ、EDDQ和SEDDQ。IF钢在炼钢阶段作了脱碳处理,并且其中的碳和氮还通过添加钛、铌等元素来进行固定,最后在连续退火过程中在相当高的温度中均热保温处理后,使其成为无时效产品。(7)