几种常见退火工艺方法及比较
退火加工工艺介绍

退火科技名词定义中文名称:退火英文名称:annealing定义1:将金属构件加热到高于或低于临界点,保持一定时间,随后缓慢冷却,从而获得接近平衡状态的组织与性能的金属热处理工艺。
应用学科:电力(一级学科);热工自动化、电厂化学与金属(二级学科)定义2:将金属或合金加热到适当温度,保持一定时间,然后缓慢冷却的热处理工艺。
应用学科:机械工程(一级学科);机械工程(2)_热处理(二级学科);整体热处理(三级学科)定义3:(1)热变性核酸或蛋白质经缓慢降温后的复性过程。
(2)两条单链多核苷酸通过互补碱基之间的氢键形成双链分子的过程。
可发生在同一来源或不同来源核酸链之间,可以形成双链DNA分子、双链RNA或DNA-RNA杂交分子。
应用学科:生物化学与分子生物学(一级学科);总论(二级学科)本内容由全国科学技术名词审定委员会审定公布百科名片重结晶退火(完全退火)应用于平衡加热和冷却时有固态相变(重结晶)发生的合金。
其退火温度为各该合金的相变温度区间以上或退火以内的某一温度。
加热和冷却都是缓慢的。
合金于加热和冷却过程中各发生一次相变重结晶,故称为重结晶退火,常被简称为退火。
这种退火方法,相当普遍地应用于钢。
钢的重结晶退火工艺是:缓慢加热到Ac3(亚共析钢)或Ac1(共析钢或过共析钢)以上30~50℃,保持适当时间,然后缓慢冷却下来。
通过加热过程中发生的珠光体(或者还有先共析的铁素体或渗碳体)转变为奥氏体(第一回相变重结晶)以及冷却过程中发生的与此相反的第二回相变重结晶,形成晶粒较细、片层较厚、组织均匀的珠光体(或者还有先共析铁素体或渗碳体)。
退火温度在Ac3以上(亚共析钢)使钢发生完全的重结晶者,称为完全退火,退火温度在Ac1与Ac3之间 (亚共析钢)或Ac1与Acm之间(过共析钢),使钢发生部分的重结晶者,称为不完全退火。
前者主要用于亚共析钢的铸件、锻轧件、焊件,以消除组织缺陷(如魏氏组织、带状组织等),使组织变细和变均匀,以提高钢件的塑性和韧性。
退火--淬火--回火
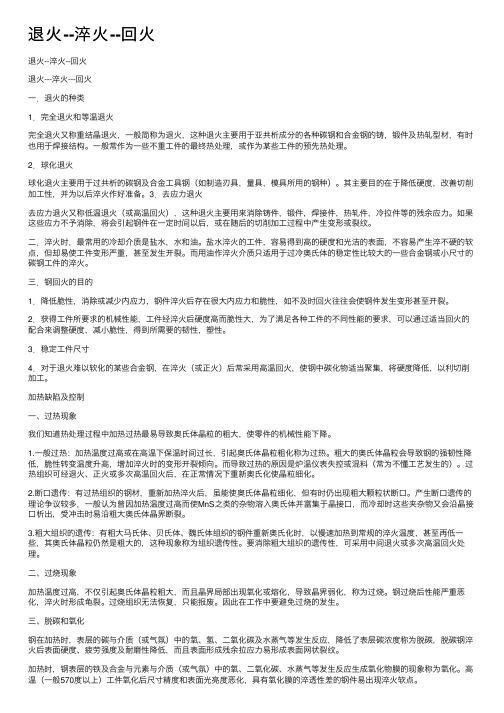
退⽕--淬⽕--回⽕退⽕--淬⽕--回⽕退⽕---淬⽕---回⽕⼀.退⽕的种类1.完全退⽕和等温退⽕完全退⽕⼜称重结晶退⽕,⼀般简称为退⽕,这种退⽕主要⽤于亚共析成分的各种碳钢和合⾦钢的铸,锻件及热轧型材,有时也⽤于焊接结构。
⼀般常作为⼀些不重⼯件的最终热处理,或作为某些⼯件的预先热处理。
2.球化退⽕球化退⽕主要⽤于过共析的碳钢及合⾦⼯具钢(如制造刃具,量具,模具所⽤的钢种)。
其主要⽬的在于降低硬度,改善切削加⼯性,并为以后淬⽕作好准备。
3.去应⼒退⽕去应⼒退⽕⼜称低温退⽕(或⾼温回⽕),这种退⽕主要⽤来消除铸件,锻件,焊接件,热轧件,冷拉件等的残余应⼒。
如果这些应⼒不予消除,将会引起钢件在⼀定时间以后,或在随后的切削加⼯过程中产⽣变形或裂纹。
⼆.淬⽕时,最常⽤的冷却介质是盐⽔,⽔和油。
盐⽔淬⽕的⼯件,容易得到⾼的硬度和光洁的表⾯,不容易产⽣淬不硬的软点,但却易使⼯件变形严重,甚⾄发⽣开裂。
⽽⽤油作淬⽕介质只适⽤于过冷奥⽒体的稳定性⽐较⼤的⼀些合⾦钢或⼩尺⼨的碳钢⼯件的淬⽕。
三.钢回⽕的⽬的1.降低脆性,消除或减少内应⼒,钢件淬⽕后存在很⼤内应⼒和脆性,如不及时回⽕往往会使钢件发⽣变形甚⾄开裂。
2.获得⼯件所要求的机械性能,⼯件经淬⽕后硬度⾼⽽脆性⼤,为了满⾜各种⼯件的不同性能的要求,可以通过适当回⽕的配合来调整硬度,减⼩脆性,得到所需要的韧性,塑性。
3.稳定⼯件尺⼨4.对于退⽕难以软化的某些合⾦钢,在淬⽕(或正⽕)后常采⽤⾼温回⽕,使钢中碳化物适当聚集,将硬度降低,以利切削加⼯。
加热缺陷及控制⼀、过热现象我们知道热处理过程中加热过热最易导致奥⽒体晶粒的粗⼤,使零件的机械性能下降。
1.⼀般过热:加热温度过⾼或在⾼温下保温时间过长,引起奥⽒体晶粒粗化称为过热。
粗⼤的奥⽒体晶粒会导致钢的强韧性降低,脆性转变温度升⾼,增加淬⽕时的变形开裂倾向。
⽽导致过热的原因是炉温仪表失控或混料(常为不懂⼯艺发⽣的)。
常用的退火工艺方法2-2
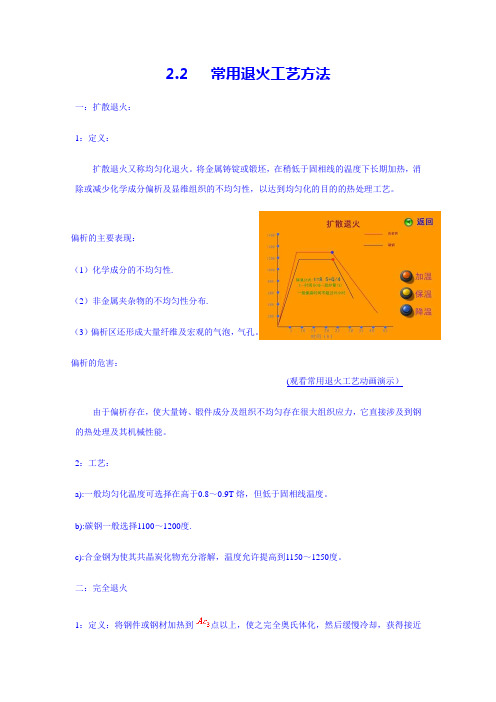
2.2 常用退火工艺方法一:扩散退火:1:定义:扩散退火又称均匀化退火。
将金属铸锭或锻坯,在稍低于固相线的温度下长期加热,消除或减少化学成分偏析及显维组织的不均匀性,以达到均匀化的目的的热处理工艺。
偏析的主要表现:(1)化学成分的不均匀性.(2)非金属夹杂物的不均匀性分布.(3)偏析区还形成大量纤维及宏观的气泡,气孔。
偏析的危害:(观看常用退火工艺动画演示)由于偏析存在,使大量铸、锻件成分及组织不均匀存在很大组织应力,它直接涉及到钢的热处理及其机械性能。
2:工艺:a):一般均匀化温度可选择在高于0.8~0.9T熔,但低于固相线温度。
b):碳钢一般选择1100~1200度.c):合金钢为使其共晶炭化物充分溶解,温度允许提高到1150~1250度。
二:完全退火1:定义:将钢件或钢材加热到点以上,使之完全奥氏体化,然后缓慢冷却,获得接近于平衡组织的热处理工艺。
2:目的:细化晶粒,降低硬度,改善33切削性能以及消除内力。
因此,完全退火不宜太高,一般在AC3点以上20-30,适用于含碳的中碳钢,三:不完全退火1:定义:将钢件加热之和之间,经保温并缓慢冷却,以获得接近平衡的组织。
这种热处理工艺成为不完全退火。
四:球化退火定义: 将钢中的碳化物球状化,或获得‘球状珠光体’的退火工艺称维球化退火。
1:方案1低于点温度的球化退火。
该种工艺方法是把退火钢材加热到略低于的温度,经长时间保温,使碳化物又片状变成球状的方法。
2:方案2往复球化退火。
这是一种周期退火,目的是加速球化过程。
3:方案3一次球化退火法。
此种退火工艺是目前生产上最常用的球化退火工艺。
实际上是一种不完全退火。
五:再结晶退火和消除应力退火1:定义:经过冷变形后的金属加热到再结晶温度以上,保持势道时间,使形变晶粒重新转变维均匀的等轴晶粒,以消除形变强化和残余应力的热处理工艺,称为再结晶退火。
再结晶退火在高于再结晶温度进行。
再结晶温度随着合金成分及冷塑性变形量而有所变化。
热处理工艺中的退火处理及其效果
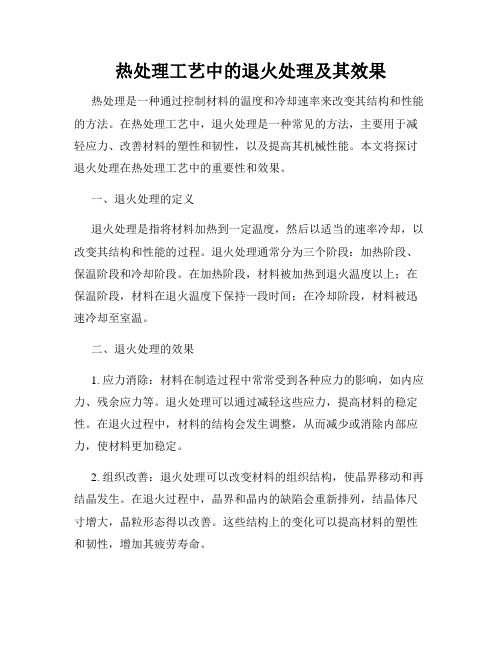
热处理工艺中的退火处理及其效果热处理是一种通过控制材料的温度和冷却速率来改变其结构和性能的方法。
在热处理工艺中,退火处理是一种常见的方法,主要用于减轻应力、改善材料的塑性和韧性,以及提高其机械性能。
本文将探讨退火处理在热处理工艺中的重要性和效果。
一、退火处理的定义退火处理是指将材料加热到一定温度,然后以适当的速率冷却,以改变其结构和性能的过程。
退火处理通常分为三个阶段:加热阶段、保温阶段和冷却阶段。
在加热阶段,材料被加热到退火温度以上;在保温阶段,材料在退火温度下保持一段时间;在冷却阶段,材料被迅速冷却至室温。
二、退火处理的效果1. 应力消除:材料在制造过程中常常受到各种应力的影响,如内应力、残余应力等。
退火处理可以通过减轻这些应力,提高材料的稳定性。
在退火过程中,材料的结构会发生调整,从而减少或消除内部应力,使材料更加稳定。
2. 组织改善:退火处理可以改变材料的组织结构,使晶界移动和再结晶发生。
在退火过程中,晶界和晶内的缺陷会重新排列,结晶体尺寸增大,晶粒形态得以改善。
这些结构上的变化可以提高材料的塑性和韧性,增加其疲劳寿命。
3. 机械性能提升:退火处理可以改善材料的机械性能。
材料经过退火处理后,其强度和硬度有所降低,但韧性和塑性得到提高。
退火处理还可改善材料的疲劳寿命和高温性能,使其更适应复杂的工作环境。
4. 尺寸稳定性改善:退火处理可以减少材料的尺寸变化。
在某些情况下,材料在制造过程中会发生尺寸变形或形状不稳定的问题。
通过退火处理,材料的形状和尺寸可以得到稳定,避免因尺寸变化而引起的问题。
三、常见的退火处理方法1. 线性退火:线性退火是最简单的退火处理方法之一。
在线性退火过程中,材料被加热到退火温度,然后以恒定速率冷却至室温。
这种方法适用于某些低碳钢和合金钢,可以改善材料的塑性和韧性。
2. 等温退火:等温退火是将材料加热到退火温度后保持一段时间,使其达到热平衡状态,然后再冷却至室温。
等温退火可以通过控制保温时间和温度来改变材料的组织结构和性能。
退火种类及正火特点
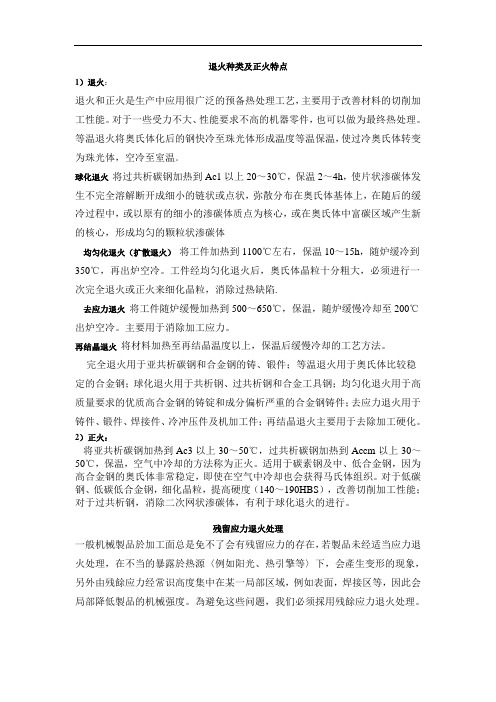
退火种类及正火特点1)退火:退火和正火是生产中应用很广泛的预备热处理工艺,主要用于改善材料的切削加工性能。
对于一些受力不大、性能要求不高的机器零件,也可以做为最终热处理。
等温退火将奥氏体化后的钢快冷至珠光体形成温度等温保温,使过冷奥氏体转变为珠光体,空冷至室温。
球化退火将过共析碳钢加热到Ac1以上20~30℃,保温2~4h,使片状渗碳体发生不完全溶解断开成细小的链状或点状,弥散分布在奥氏体基体上,在随后的缓冷过程中,或以原有的细小的渗碳体质点为核心,或在奥氏体中富碳区域产生新的核心,形成均匀的颗粒状渗碳体均匀化退火(扩散退火)将工件加热到1100℃左右,保温10~15h,随炉缓冷到350℃,再出炉空冷。
工件经均匀化退火后,奥氏体晶粒十分粗大,必须进行一次完全退火或正火来细化晶粒,消除过热缺陷.去应力退火将工件随炉缓慢加热到500~650℃,保温,随炉缓慢冷却至200℃出炉空冷。
主要用于消除加工应力。
再结晶退火将材料加热至再结晶温度以上,保温后缓慢冷却的工艺方法。
完全退火用于亚共析碳钢和合金钢的铸、锻件;等温退火用于奥氏体比较稳定的合金钢;球化退火用于共析钢、过共析钢和合金工具钢;均匀化退火用于高质量要求的优质高合金钢的铸锭和成分偏析严重的合金钢铸件;去应力退火用于铸件、锻件、焊接件、冷冲压件及机加工件;再结晶退火主要用于去除加工硬化。
2)正火:将亚共析碳钢加热到Ac3以上30~50℃,过共析碳钢加热到Accm以上30~50℃,保温,空气中冷却的方法称为正火。
适用于碳素钢及中、低合金钢,因为高合金钢的奥氏体非常稳定,即使在空气中冷却也会获得马氏体组织。
对于低碳钢、低碳低合金钢,细化晶粒,提高硬度(140~190HBS),改善切削加工性能;对于过共析钢,消除二次网状渗碳体,有利于球化退火的进行。
残留应力退火处理一般机械製品於加工面总是免不了会有残留应力的存在,若製品未经适当应力退火处理,在不当的暴露於热源〈例如阳光、热引擎等〉下,会產生变形的现象,另外由残餘应力经常识高度集中在某一局部区域,例如表面,焊接区等,因此会局部降低製品的机械强度。
钢的四把火及应用

退火:将钢加热到一定温度后炉冷处理正火:将钢加热到一定温度后空冷处理淬火:将钢加热到一定温度后水冷或油冷处理回火:将淬火过的钢重新加热到一个温度冷却1. 钢的退火钢的退火是把钢加热到适当温度,保温一定时间,然后缓慢冷却,以获得接近平衡组的热处理工艺。
退火的目的在于均匀化学成分、改善机械性能及工艺性能、消除或减少内应力并为零件最终热处理作好组织准备。
退火的目的在于:①改善或消除钢铁在铸造、锻压、轧制和焊接过程中所造成的各种组织缺陷以及残余应力,防止工件变形、开裂。
②软化工件以便进行切削加工。
③细化晶粒,改善组织以提高工件的机械性能。
④为最终热处理(淬火、回火)作好组织准备。
常用的退火工艺有:①完全退火。
用以细化中、低碳钢经铸造、锻压和焊接后出现的力学性能不佳的粗大过热组织。
将工件加热到铁素体全部转变为奥氏体的温度以上30~50℃,保温一段时间,然后随炉缓慢冷却,在冷却过程中奥氏体再次发生转变,即可使钢的组织变细。
②球化退火。
用以降低工具钢和轴承钢锻压后的偏高硬度。
将工件加热到钢开始形成奥氏体的温度以上20~40℃,保温后缓慢冷却,在冷却过程中珠光体中的片层状渗碳体变为球状,从而降低了硬度。
③等温退火。
用以降低某些镍、铬含量较高的合金结构钢的高硬度,以进行切削加工。
一般先以较快速度冷却到奥氏体最不稳定的温度,保温适当时间,奥氏体转变为托氏体或索氏体,硬度即可降低。
④再结晶退火。
用以消除金属线材、薄板在冷拔、冷轧过程中的硬化现象(硬度升高、塑性下降)。
加热温度一般为钢开始形成奥氏体的温度以下50~150℃,只有这样才能消除加工硬化效应使金属软化。
⑤石墨化退火。
用以使含有大量渗碳体的铸铁变成塑性良好的可锻铸铁。
工艺操作是将铸件加热到950℃左右,保温一定时间后适当冷却,使渗碳体分解形成团絮状石墨。
⑥扩散退火。
用以使合金铸件化学成分均匀化,提高其使用性能。
方法是在不发生熔化的前提下,将铸件加热到尽可能高的温度,并长时间保温,待合金中各种元素扩散趋于均匀分布后缓冷。
退火正火淬火及回火
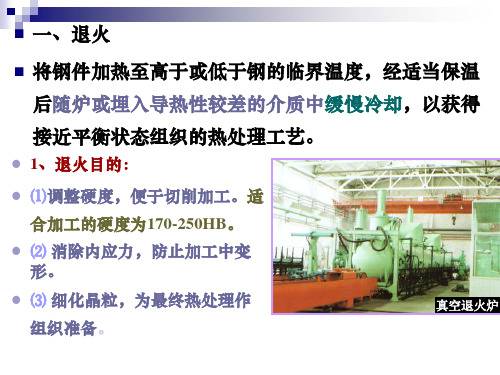
⑶对于某些高淬透性的钢,空冷即可淬火,如采用
回火软化既能降低硬度,又能缩短软化周期。 未经淬火的钢回火无意义,而淬火钢不回火在放置使
用过程中易变形或开裂。钢经淬火后应立即进行回火 。
2、钢在回火时的转变 淬火钢回火时的组织转变主要发生在加热阶段。随
Ac1+30~50℃,保温后快冷到Ar1以下的某一温度下停留,待 相变完成后出炉空冷。等温退火可缩短工件在炉内停留时间 。
⑶ 球化退火
球化退火是将钢中渗碳体球状化的退火工艺。 将工件加热到Ac1+ 30-50℃
保温后缓冷,或者加热后 快冷到略低于 Ar1 的温度 下保温,使珠光体中的渗 碳体球化后出炉空冷。主 要用于共析、过共析钢。
加热温度升高,淬火钢的组织发生四个阶段变化。
网带式回火电炉
①第一类回火脆性 又称不可逆回火脆性。是指淬火钢在250-350℃回火时出现的
脆性。
这种回火脆性是不可逆 的,只要在此温度范围 内回火就会出现脆性, 目前尚无有效消除办法。
回火时应避开这一温度 范围。
②第二类回火脆性 又称可逆回火脆性。是指淬火
硬化能力.
M深量度和的硬变度化随
②淬透性与淬硬层深度的关系 同一材料的淬硬层深度与工件尺寸、冷却介质有关。工件
尺寸小、介质冷却能力强,淬硬层深。 淬透性与工件尺寸、冷却介质无关。它只用于不同材料之
间的比较,是通过尺寸、冷却介质相同时的淬硬层深度来 确定的。
利用淬透性可控制淬硬层深度。 对于截面承载均匀的重要件,要全部淬透。如螺栓、
一、退火
将钢件加热至高于或低于钢的临界温度,经适当保温 后随炉或埋入导热性较差的介质中缓慢冷却,以获得
连拉连退中几种常见退火工艺及比较

缺点:耗电量大,无法实现退火速度自动跟踪(退火温度不能跟随线速作及时调整)。
3、接触式电刷传输大电流退火
接触式电刷传输大电流退火设备主要由可调变压器、电刷、电极轮、冷却液、收放线装置等组成。它是利用单丝通电流时会发热这一原理来实现退火的。
我们知道,铜杆和铝杆在拉丝机上拉拔的过程中,会发生硬化、变脆,为了恢复单丝的塑性,保持良好的电气性能,因此需要将线材在一定的温度下进行热处理(退火处理)。
目前常见的退火方法有:退火炉退火,热管式退火,接触式电刷传输大电流退火和感应式退火等几种方法,下面逐一ห้องสมุดไป่ตู้析、比较各种退火方法的优缺点。
1、退火炉退火
接触式电刷传输大电流退火设备,控制退火程度的方式一般有二种:控制退火电流及控制退火电压。退火电流与退火线径的平方成正比,并与退火的速度有关(速度越快,退火电流需要越大);退火电压仅取决于退火的速度和单丝的电阻率,与线径无关。基于上述原因,所以以控制退火电压来控制单丝退火程度(单丝的断裂伸长率)的方式比较常用(公司的四台铜拉机,都常用该方式给铜丝退火)。 在铜拉设备上,我们可以看到退火电气柜和退火箱之间,有二根粗大的铜(铝)排相连接,它们传输的是较低的电压(约70伏以下,可根据铜丝的生产线速自动调整),较大的电流(数千安培),打开退火箱后方的铁门,映入眼帘的就是那密密麻麻的导电炭刷(一个电极轮上有几十块烟盒般大小的炭刷),它们负责把铜(铝)排上的电流传输到电极轮上,这样电极轮转动受到的阻力较大。
该设备的主要优点:比较节能,能够实现在线连续退火,而且退火周期较短,能够实现退火速度自动跟踪(能自动根据单丝速度调整退火电压或电流,使单丝退火程度保持一致)。
- 1、下载文档前请自行甄别文档内容的完整性,平台不提供额外的编辑、内容补充、找答案等附加服务。
- 2、"仅部分预览"的文档,不可在线预览部分如存在完整性等问题,可反馈申请退款(可完整预览的文档不适用该条件!)。
- 3、如文档侵犯您的权益,请联系客服反馈,我们会尽快为您处理(人工客服工作时间:9:00-18:30)。
几种常见退火工艺及比较
我们知道,铜杆和铝杆在拉丝机上拉拔的过程中,会发生硬化、变脆,为了恢复单丝的塑性,保持良好的电气性能,因此需要将线材在一定的温度下进行热处理(退火处理)。
目前常见的退火方法有:退火炉退火,热管式退火,接触式电刷传输大电流退火和感应式退火等几种方法,下面逐一分析、比较各种退火方法的优缺点。
1、退火炉退火
退火炉退火设备主要由退火罐、加热丝、等组成(参见图1)。
它通过把单丝放置在一个加热的容器内,达到退火的目的。
该设备的主要优点:设备简单、易维护。
缺点:耗电量大,退火后单丝性能不稳定,不能在线连续退火,而且退火周期较长。
2、热管式退火
热管式退火设备主要由不锈钢管、加热丝、冷却液、收放线装置等组成(参见图2)。
它通过电热丝加热一根空心管,单丝通过加热的空心管,达到退火的目的。
该设备的主要优点:设备较简单,能够实现在线连续退火,而且退火周期相对较短。
缺点:耗电量大,无法实现退火速度自动跟踪(退火温度不能跟随线速作及时调整)。
3、接触式电刷传输大电流退火
接触式电刷传输大电流退火设备主要由可调变压器、电刷、电极轮、冷却液、收放线装置等组成。
它是利用单丝通电流时会发热这一原理来实现退火的。
该设备的主要优点:比较节能,能够实现在线连续退火,而且退火周期较短,能够实现退火速度自动跟踪(能自动根据单丝速度调整退火电压或电流,使单丝退火程度保持一致)。
缺点:由于靠电刷传输电流,电极轮转动使的阻力较大(费能),单丝和电极轮间有时会产
生火花,影响单丝的表面质量。
(参见图3)
图3 接触式电刷传输大电流退火示意图
图3中,电极轮1和电极轮3的电位相等(假设都是正极),电极轮2是负极,则电极轮1和电极轮2及电极轮2和电极轮3之间的单丝都有电流通过,并产生热量。
从图中可以看出,
电极轮1和电极轮2间的单丝发热比电极轮2和电极轮3的要少,单丝的相对温度较低(因为电极轮1和电极轮2间的单丝较长,通过的电流相对较小),该段称为预热段,电极轮2和电极轮3之间称为退火段。
因铜丝在较高的温度下易氧化,为了避免氧化的产生,通常采用水蒸汽保护(2#铜中拉采用冷却液保护)。
经过退火的单丝通过冷却液的冷却后,就可以上收线盘了。
接触式电刷传输大电流退火设备,控制退火程度的方式一般有二种:控制退火电流及控制退火电压。
退火电流与退火线径的平方成正比,并与退火的速度有关(速度越快,退火电流需要越大);退火电压仅取决于退火的速度和单丝的电阻率,与线径无关。
基于上述原因,所以以控制退火电压来控制单丝退火程度(单丝的断裂伸长率)的方式比较常用(公司的四台铜拉机,都常用该方式给铜丝退火)。
在铜拉设备上,我们可以看到退火电气柜和退火箱之间,有二根粗大的铜(铝)排相连接,它们传输的是较低的电压(约70伏以下,可根据铜丝的生产线速自动调整),较大的电流(数千安培),打开退火箱后方的铁门,映入眼帘的就是那密密麻麻的导电炭刷(一个电极轮上有几十块烟盒般大小的炭刷),它们负责把铜(铝)排上的电流传输到电极轮上,这样电极轮转动受到的阻力较大。
4、感应式退火
感应式退火设备主要由感应电源、感应线圈、等组成(参见图4),它是利用电磁感应原理达到给单丝退火的目的.
图4 感应退火示意图
该设备的主要优点有:不需要电刷等传输电流到单丝上,工作时所受的阻力较小,退火效率较高(耗电不足退火炉退火或热管式退火的一半),能够实现退火速度自动跟踪,对环境几乎没有污染。
缺点:设备价格较高。
交联机组上的导体预热器,往往是采用了先进的感应加热原理,导体通过感应线圈后,能使导体温度升为所需的温度(一般设定为90℃,交联设备上不需对导体退火,只是提高导体的温度,这样能使电缆的交联度均匀,大幅提升电缆的质量,而且也提高了生产效率)。