轴承套圈的检查方法
轴承检验规范

轴承检验标准本标准规定了公司用深沟球轴承的规格型号和性能要求;本标准适用于公司深沟球轴承的采购、样品确认和来料检验。
GB/T276-94 深沟球轴承外型尺寸2005 滚动轴承公差GB/T4604-93 径向游隙GB/T307-94 轴承精度JB/T7047-93 轴承振动噪音滚动轴承公差的测量方法3.1 外观A.轴承外观应无烧伤、锈蚀、碰伤、粗磨痕、毛刺等缺陷;中,无润滑脂泄露;C.轴承包装应标识清楚、完整;内包装应完好、无破损。
3.2 尺寸d——轴承内径;D——轴承外径;B——宽度内外圈材质:GCr15 高碳铬轴承钢,硬度为HRC60~65钢球材质: GCr15 高碳铬轴承钢,硬度为HRC61~66轴承型号主要尺寸mm 额定负载 kN极限转速〔脂润滑〕r/mind D B r Cr Cor Rpm6801ZZ 12 21 5 30000 6806ZZ 30 42 7 13000 2Z代表两面带防尘盖附表13.3 轴承的制造精度轴承的尺寸精度按GB/T307-940级〔普通级〕,公差值如表:单位:mm保持架和防尘盖轴承用金属冲压波形保持架;防尘盖用双面金属防尘盖〔2ZZ型〕轴承的润滑3.5.1 轴承的润滑剂是由生产厂商在出厂前封装,要求工作温度在3.5.2 润滑脂具有很好的黏附性、耐磨性、耐温性、防锈性和润滑性,能够提高高温抗氧化性,延缓老化,能溶解积碳,防止金属磨屑和油污的结聚,提高机械的耐磨、耐压和耐腐蚀性。
.3 注脂量深沟球内径小于15mm以下的型号为20%-25%,内径大于17mm为25%-30%。
〔注:除去保持架、滚子,内圈与外圈之间的空间所占%〕。
3.6 使用寿命轴承正确安装后,电机在常温常压下运行20000小时无故障,在高温环境下80℃~90℃,相对湿度80%,运行200小时后,轴承的润滑脂无泄漏挥发。
振动及噪音需供方提供相关检验报告同时用以下方法判定:手感法:正常轴承的内外座圈与滚动体的间隙为0.005~0.010毫米。
轴承套圈安全隐患排查

轴承套圈安全隐患排查一、轴承套圈的常见安全隐患1. 轴承套圈损坏轴承套圈在使用过程中,可能会受到振动、摩擦、腐蚀等因素的影响,导致其损坏或破裂。
损坏的轴承套圈会使得轴承无法固定,进而影响机械设备的稳定性和安全性。
2. 轴承套圈变形轴承套圈在使用过程中,可能会因为受到外力或者高温等因素的影响而发生变形。
轴承套圈变形会导致轴承安装不牢固,影响机械设备的正常运转。
3. 错误安装在安装轴承套圈的过程中,如果存在操作不当或者使用不合适的工具,可能会导致轴承套圈的错误安装,使得轴承套圈无法起到固定轴承的作用。
4. 腐蚀损耗由于工作环境的原因,轴承套圈可能会发生腐蚀损耗,使得其表面出现氧化、锈蚀等现象,进而影响轴承套圈的使用寿命和安全性。
5. 重载在机械设备运行过程中,由于过载或者频繁振动等原因,可能会导致轴承套圈受到超负荷的压力,从而影响其正常工作状态。
6. 润滑不良如果轴承套圈的润滑不良,可能会导致其在工作中产生摩擦和磨损,进而影响轴承套圈的使用寿命和安全性。
以上这些安全隐患都可能会对轴承套圈的工作状态和安全性产生影响,因此需要对轴承套圈进行定期的安全隐患排查和处理。
二、轴承套圈安全隐患排查方法1. 目视检查通过目视检查轴承套圈的外观情况,观察是否有明显的损坏、变形、腐蚀等现象,以及安装是否正确、是否有氧化、锈蚀等情况。
目视检查是最为简单和快速的一种方法,能够初步了解轴承套圈的工作状态,是安全隐患排查的第一步。
2. 检测工具利用测量工具,如千分尺、外径千分尺、内径千分尺等,对轴承套圈的尺寸进行精确测量,以确定轴承套圈的尺寸是否符合标准要求,是否存在变形或者磨损等情况。
3. 超声波检测通过超声波检测仪器,对轴承套圈进行超声波探伤检测,以检测轴承套圈内部是否存在裂纹、气泡、夹杂等缺陷,从而判断其安全状态。
4. 涂覆检查在轴承套圈表面进行涂覆检查,观察轴承套圈是否已经进行了润滑,以及润滑情况是否良好。
如果发现润滑不良,应及时补充润滑剂,以确保轴承套圈的正常工作状态。
轴承外观检查验收标准

轴承外观检查验收标准(草案二)1 范围本文规定了按GB/T307.1、GB/T307.3、GB/T307.4制造的一般用途滚动轴承套圈和滚子外观质量要求本文适用于轴承外径大于200mm至430mm的大型轴承及外径大于440mm的特大型轴承套圈以及该尺寸段轴承装用的级滚子的最终检验本文不适用于滚针轴承和带冲压套圈的轴承2 引用标准和文件GB/T307.1 滚动轴承向心轴承公差GB/T307.3 滚动轴承通用技术规则GB/T307.4 滚动轴承推力轴承公差3 术语和定义3.1 表面3.1.1 工作表面轴承套圈的滚道、引导滚子和保持架的挡边表面。
滚子外径和与套圈引导挡边接触的滚子端面。
3.1.2 配合表面轴承内圈内孔表面、外圈外园柱面和端面。
3.1.3 其他表面套圈工作表面和配合表面以外的表面。
滚子工作表面以外的表面。
3.2 表面缺陷3.2.1 裂纹零件表面存在的缝隙(折叠除外)3.2.2 折叠热加工时金属没有熔接起来而形成的表面缝隙,具有裂纹的外观。
3.2.3 夹杂物金属在凝固过程夹杂的异物。
3.2.4 点子表面上不规则的小穴,通常为黑底。
3.2.5 腐蚀因化学侵蚀在表面上造成的带色的孔蚀和弧蚀。
3.2.6 黑皮在磨削工序中未被磨削的部分。
3.2.7 斑渍非孔蚀或弧坑的表面色斑。
3.2.8 拉毛在磨削工序中,因定位支承块摩擦而在圆周方向造成毛刺的环带,是对磨加工表面的明显破坏。
3.2.9 磨伤表面局部被磨产生的缺陷,与正常加工表面明显不同,且都有一定的深度。
3.2.10 彗星痕指在超精和抛光过程中,由于个别较大金刚砂颗粒脱落或搪塞于工作表面的低凹处,随着超精压力及运转形成的彗星状痕迹。
3.2.11 砂轮花在精磨工序中,由于砂轮颗粒不均或砂轮没有修整好,给工件表面造成的个别显见的粗大砂粒痕或是抛光、超精后表面残留的前工序的磨粒痕迹。
3.2.12 螺旋纹由于砂轮、导轮和刀板上的锐边毛刺等刮划,造成滚子外径上形似刀尖刻划的螺旋状白丝。
滚动轴承检测方法及先进设备

目录第一章国外滚动轴承部件的检测方法一、滚动轴承套圈沟道表面质量的检查方法 (1)二、轴承套圈内表面伤痕的检查方法 (2)三、用频谱分析法评定滚动表面的波纹度 (4)四、用干涉仪测量球轴承滚道表面轮廓 (8)五、陶瓷球超声波探伤法 (11)六、采用振动测量技术确定球与滚子的柔量 (12)七、电机轴承部件的使用故障 (15)第二章滚动轴承异常的检测方法一、用电测法检查滚动轴承缺陷 (18)二、几种诊断滚动轴承疲劳剥落的发生位置 (19)三、用振动标定滚动轴承异常的方法 (22)四、用声发射法诊断滚动轴承的异常 (24)五、用声传感器监视滚动轴承的损伤 (27)六、用应变仪检测故障的方法 (28)七、用复合传感器检测轴承的异常 (29)八、利用振动分析检测 (33)九、滚动接触亚表面疲劳裂纹的AE检测技术 (34)十、FAG应用信号处理和频率分析技术检测轴承 (36)十一、用手提式润滑脂铁粉浓度计测量轴承磨损状态 (38)十二、借助振动和声发射诊断滚动轴承的失效 (40)十三、模式识别在线检测轴承局部缺陷 (43)十四、轴承异常的逐次模糊诊断 (50)十五、近几年普遍应用的检测滚动轴承异常的方法 (50)十六、燃气涡轮发动机转子支承轴承的诊断 (53)第三章滚动轴承其它方面检测方法一、径向负荷下轴承力矩的测量方法 (55)二、滚动轴承非重复性旋转精度的动态测量 (57)三、测量轴承负荷的方法 (60)四、滚动轴承主轴径向旋转精度评定方法 (62)五、滚动轴承工业状态的振动与噪音监测技术对比 (65)六、超声波测试硬度的方法 (70)第四章国外滚动轴承检测的先进设备一、国外几种轴承振动测量仪简介 (70)二、前苏联研制的几种测量装置 (73)三、球轴承用径向游隙测量机 (76)四、瑞典SKF公司研制的检测设备 (77)五、飞机发动机轴承钢球的检测设备 (78)六、表面粗糙度测量仪 (78)七、大型轴承测量装置 (78)八、其它几种轴承检测仪器及装置 (79)、八、-前言近年来,人们对各种零件性能的要求,尤其是对滚动轴承性能的要求有了很大的提高。
轴承套圈的装配与调试技术要求
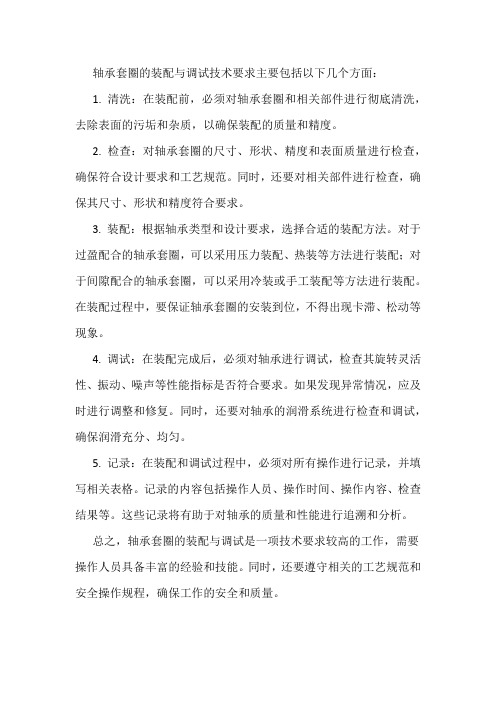
轴承套圈的装配与调试技术要求主要包括以下几个方面:
1. 清洗:在装配前,必须对轴承套圈和相关部件进行彻底清洗,去除表面的污垢和杂质,以确保装配的质量和精度。
2. 检查:对轴承套圈的尺寸、形状、精度和表面质量进行检查,确保符合设计要求和工艺规范。
同时,还要对相关部件进行检查,确保其尺寸、形状和精度符合要求。
3. 装配:根据轴承类型和设计要求,选择合适的装配方法。
对于过盈配合的轴承套圈,可以采用压力装配、热装等方法进行装配;对于间隙配合的轴承套圈,可以采用冷装或手工装配等方法进行装配。
在装配过程中,要保证轴承套圈的安装到位,不得出现卡滞、松动等现象。
4. 调试:在装配完成后,必须对轴承进行调试,检查其旋转灵活性、振动、噪声等性能指标是否符合要求。
如果发现异常情况,应及时进行调整和修复。
同时,还要对轴承的润滑系统进行检查和调试,确保润滑充分、均匀。
5. 记录:在装配和调试过程中,必须对所有操作进行记录,并填写相关表格。
记录的内容包括操作人员、操作时间、操作内容、检查结果等。
这些记录将有助于对轴承的质量和性能进行追溯和分析。
总之,轴承套圈的装配与调试是一项技术要求较高的工作,需要操作人员具备丰富的经验和技能。
同时,还要遵守相关的工艺规范和安全操作规程,确保工作的安全和质量。
深沟球轴承套圈技术条件与验收规则

进行切片投影即可,汽车发电机类(锻件)产品必须按规定执行!3-3判定3-3-1抽检项目按对产品质量影响严重程度分为A类不合格项、B类不合格项、C类不合格项A类不合格项:对产品使用安全性能有影响的不合格项目。
主要包括:硬度、裂纹。
B类不合格项:不影响产品组装及使用性能,经过全检或后工序加工可修复的不合格项目。
主要包括:严重锈蚀、尺寸偏差、无沟道、缺口。
C类不合格项:不影响产品正常使用的不合格项目。
主要是外观不良:包括小的生锈,擦伤(后工序加工能修复的)3-3-2不合格品处置3-3-2-1出现A类不合格的处置:△拒收;3-3-2-2出现B类不合格的处置:△对其中的缺工序及外观引起的不合格,允许100%全检后再次提交检查,经再次抽查合格后方能接收;△尺寸偏差引起的不合格,必须进100%检查,再次提交验收合格后方可放行,挑出的不合格品按废品处置;3-3-2-3出现C类不合格的处置:△由质保科组织评审作出相应处置措施:评审或让步接收。
3-4环保要求套圈原材料禁止使用以及含有由RoHS指令规定的六种化学物质:铅、镉、汞、六价铬、多溴联苯(PBB)、多溴联苯醚(PBDE)。
如使用以及含有,供方负有给需方提交产品安全数据表的义务。
3-5交货条件①凡是送交本工厂验收的轴承套圈产品,要求经过有效防锈并用人本集团统一的铁箱装箱形成一定的批量:②特殊情况下生产的产品或试制产品按生产计划或试制计划交检执行;③凡是送交本工厂验收的轴承套圈产品,运输要有可靠的防腐蚀措施;④每批送货的轴承套圈产品,送货单上要标明产品型号、批号以及套圈钢材的炉号,且必须附上自检报告及合格证、材质证明,并有生产单位专检人员签字盖章。
⑤轴承套圈产品进厂后,卸车之前由采购配送中心送货员负责将套圈产品型号、数量及供方有关资料交进货验收人员,进货验收人员核对无误后,进行卸车收货,把产品按要求放置于待检区,并通知质保科来料检验(IQC)人员进行产品抽检。
4、其它说明4-1 对合格分供方停止供货超过3个月的产品再次供货时,须提交样品及相关资料重新审查。
轴承套圈车加工终检标准

鑫泰轴承锻造有限公司车工车间产品质量最终检验标准抽样依据:GB2828-87抽样方案执行标准:AQL=1.0检验内容和检验方法:1.1外径检验项目:外径尺寸,椭圆度,锥度,棱圆度,直线度,粗糙度,垂直度.1.2外径检验方法:采用轴承专用D913(D914),H903仪器,配用分度值0.01mm的百分表和标准件来进行检测,直线度和粗糙度目测2.1高度检验项目:高度尺寸,平行差,平面度。
2.2高度检验方法:采用轴承专用G093(G904)仪器,配用分度值0.01mm的百分表和标准件来进行检测。
3.1内径检验项目:内经尺寸,椭圆度,锥度,垂直度,壁厚差,,粗糙度。
3.2内径检验方法:采用轴承专用D923(D924),H902仪器,配用分度值0.01mm的百分表和专用标准件来进行检测,直线度和粗糙度目测。
4.1沟道检验项目:沟径尺寸,沟椭圆,沟位置,沟测摆,沟曲率,沟壁厚,粗糙度。
4.2沟径检验方法:采用轴承专用D022,(D023),D013(D014),H902(H903)仪器,配用分度值0.01mm的百分表和专用标准件来进行检测,沟曲率用刮板,粗糙度目测。
5.1打标志检验项目:标志的深度,标志内部的凸出量,标志位置,标志内容(根据各厂家技术要求),等分。
5.2打标志检验方法:标志深度和凸出量采用G9039(G904)仪器加分度值0.01mm的百分表与尖表尖进行测量,标志位置采用游标卡尺检验,标志内容采用目测检验,等分采用专用模具进行检验。
6.1止动槽检验项目:止动槽底径,止动槽宽度,止动槽位置,止动槽毛刺。
6.2止动槽检验方法:止动槽底径用轴承专用D913(D914)仪器,配用分度值0.01mm的百分表和尖测脚测量,槽宽度用塞规测量,位置用G093(G904)仪器配用分度值0.01mm的百分表和标准件来进行检测。
7.1防尘槽检验项目:防尘槽底径,防尘槽口径,防尘槽椭圆,防尘槽位置。
7.2防尘槽检验方法:槽底尺寸椭圆用采用轴承专用D923(D924),H902仪器,配用分度值0.01mm的百分表和专用标准件来进行检测,槽位置用采用G9039(G904)仪器加分度值0.01mm的百分表与尖表尖进行测量,槽口采用塞规测量。
【精品】轮毂轴承质量检验基本常识

轮毂轴承质量检验基本常识轮毂轴承质量检验基本常识中图分类号:U260.331+.2文献标识码: A 文章编号:一轴承的结构轴承由于用途和工作条件不同,其结构变化甚多。
轮滚单元也是轴承的一种,但其基本结构是由4个零件组成:(1)内圈,(2)外圈,(3)滚动体(钢球或滚子),(4)保持架。
第一代轮毂单元:由双列圆锥滚子轴承或双列滚珠轴承组成。
第二代轮毂单元:外圈带法兰盘的双列圆锥滚子轴承,外圈带法蓝盘的双列角接触滚珠轴承。
第二代半轮毂单元:在第二代的基础上外加芯轴。
第三代轮毂单元:内外圈带法蓝盘的双列圆锥滚子轴承,内外圈带法兰盘的双列角接触滚珠轴承(带芯轴)。
二常用量具型号及使用方法游标卡尺游标卡尺的分类:有0.01、0.02、0.05和0.10的分度值,测量范围的上限至2000mm。
使用应注意的事项:A、测量工件时应按测量工件的尺寸的大小及精度要求来选用游标卡尺。
B、测量前应检查尺身游标刻线对齐情况,以免产生读数误差。
游标卡尺读数原理:利用游标卡尺的游标刻线间距与主尺刻线间差形成游标分度值。
测量时,在主尺上读取毫米数,在游标上读取小数值。
千分尺千分尺的分类:分度值为0.01mm,测量范围至500mm 的外径千分尺。
千分尺读数原理:利用等进螺旋原理将丝杆的角度旋转运动转变为测杆的直线位移。
读数方法:A、在固定套筒上读出毫米数或半毫米数。
B、看微分筒上哪一格与固定套筒上基准线对齐。
C、两次读数加起来。
使用应注意事项:千分尺的测量面应干净。
测量时先转微分筒,测量面接触前改用棘轮,直到发出咯咯声为止。
每把千分尺都有它的测量范围,按被测件的大小来选用。
但不能用它去测毛坯,更不能在工件旋转时去测量。
指示表(百分表和千分表)百分表的分度值为0.01,测量范围为0-3、0-5、0-10mm。
千分表的分度值为0.001,测量范围为0-1、0-2、0-3、0-5mm。
指示表是利用齿轮或杠杆齿轮传动,将测杆的直线位移变为指针的角位移的计量器具。
- 1、下载文档前请自行甄别文档内容的完整性,平台不提供额外的编辑、内容补充、找答案等附加服务。
- 2、"仅部分预览"的文档,不可在线预览部分如存在完整性等问题,可反馈申请退款(可完整预览的文档不适用该条件!)。
- 3、如文档侵犯您的权益,请联系客服反馈,我们会尽快为您处理(人工客服工作时间:9:00-18:30)。
轴承套圈的检查方法
-----------职工培训提纲一,轴承标准
GB----------JB-----------TC--------------QB
国标----机械行业标准----轴承行业标准-----企业标准(产品出厂标准,工序生产标准)
大部分标准是等效采用的国际标准,
二,轴承的一般检查方法
1,平面------------------------------------------三点支撑
宽度偏差△Bs(△Cs);平行差VBs(Vcs);平面度Api(内圈)Ape(外圈)。
平面度即是磨加工定位基准,又是测量基准。
对于单列圆锥滚子轴承而言,两端面的平行差没有什么实际意义。
2,内径-------------平面支撑
Δdmp—单一平面平均内径偏差(尺寸偏差)
V dp —单一平面内径变动量(内径椭圆)
V dmp —平均内径变动量(内径锥度)
Sd(Sd')-----内径垂直。
3,外径---------------------------------------------------平面支撑
ΔDmp —单一平面平均外径偏差(尺寸偏差)
V Dp —单一平面外径变动量(外径椭圆)
V Dmp —平均外径变动量(外径锥度)
S D(S D'')------外径垂直
4,内圈滚道------------------------三点支撑
△dimp---滚道尺寸
Vdip----滚道椭圆
△2β---滚道角度
Sdi(Sdi')----滚道垂直
5,外圈滚道------------------------------------------------三点支撑
△Emp----滚道尺寸
VEp----滚道椭圆
△2α----滚道角度
SE(SE')-----滚道垂直
6,挡边-----------------------------------------------------------平面支撑
△if-----挡边尺寸
Sif-----内圈大挡边平行差
角度------着色。
三,实例:外圈滚道测量方法
1,检验标准(QB)△Emp=+1--+12um
VEp=5um
SE'=6um
△2α=+/—3um.
2,千分表的示值:表一,+4/-3um
表二,-2/+4
3,问:表一,表二各是检测什么参数的?滚道尺寸?椭圆?垂直?
角度?。