气动系统典型实例教材
气动系统的基本认识一体化课程实施课件.

按钮
实例
气缸
4
2
2
5
3
1
1
3
如图所示为客车门工作机构图,它是利用压缩空气来驱动气缸从而带 动门的开关,当气缸活塞杆伸出,门就关上;气缸活塞杆收缩,门就打 开。
气动系统各构成部分的作用
(1)气源装置:主要是把空气压缩到原来体积的1/7左右形 成压缩空气,并对压缩空气进行净化处理,最终向系统提 供洁净、干燥的压缩空气。 (2)执行元件:是以压缩空气为动力源,将气体的压力 能再转化为机械能的装置,用来实现既定的动作。气动系 统常用的执行元件为气缸和气动马达或摆动马达等。
准化。
二、气压传动的优缺点
2.缺点
1)由于空气压缩性大,气缸的动作速度易随外加负载的变化而变化,稳 定性差,给位置和速度控制带来较大影响。
2)目前气动系统的压力级(一般小于0.8MPa)不高,总的输出力不大。 3)工作介质(空气)没有润滑性,系统中必须采取措施进行给油润滑。 4)气动元件在工作时噪声较大,因此高速排气时需要加装消声器。
2.后冷却器
图为常用的蛇管式后冷却器。 热压缩空气在浸没于冷水中 的蛇形管内流动,冷却水在 水套中流动,经管壁进行热 交换,使压缩空气得到冷却。
1-活塞;2-气缸;3-排气阀;4-排气管 图 后冷却器
3.油水分离器
当压缩空气进入油 水分离器后,产生 流向和速度的急剧 变化,再依靠惯性 作用,将密度比压 缩空气大的油滴和 水滴分离出来。图 为常见的撞击式和 环形回转式油水分 离器。
0.2~1.0MPa 1.0~10MPa
>10MPa
容积型 速度型
往复型 活塞式、膜片式 旋转型 滑片式、螺杆式
液压传动与气动技术课程教案典型气动系统

液压传动与气动技术课程教案-典型气动系统第一章:气动系统概述教学目标:1. 了解气动系统的定义、组成和特点;2. 掌握气动系统的基本工作原理;3. 熟悉气动系统在工业中的应用。
教学内容:1. 气动系统的定义和组成;2. 气动系统的工作原理;3. 气动系统在工业中的应用案例。
教学方法:1. 讲授:讲解气动系统的定义、组成和特点;2. 演示:通过视频或实物展示气动系统的工作原理;3. 案例分析:分析气动系统在工业中的应用案例。
教学评估:1. 课堂问答:检查学生对气动系统定义、组成和工作原理的理解;2. 小组讨论:让学生探讨气动系统在工业中的应用案例,分享自己的观点。
第二章:气源设备及处理元件教学目标:1. 掌握气源设备的种类和功能;2. 熟悉气动处理元件的作用和结构;3. 了解气源系统的设计原则。
教学内容:1. 气源设备的种类和功能;2. 气动处理元件的作用和结构;3. 气源系统的设计原则。
教学方法:1. 讲授:讲解气源设备的种类和功能、气动处理元件的作用和结构;2. 互动:引导学生参与讨论气源系统的设计原则;3. 实操:演示气源设备和处理元件的安装与调试。
教学评估:1. 课堂问答:检查学生对气源设备、气动处理元件的理解;2. 实操考核:评估学生在实操中对气源设备和处理元件的安装与调试能力。
第三章:执行元件及控制元件教学目标:1. 掌握气动执行元件的种类和特点;2. 熟悉气动控制元件的功能和结构;3. 了解执行元件和控制元件在气动系统中的应用。
教学内容:1. 气动执行元件的种类和特点;2. 气动控制元件的功能和结构;3. 执行元件和控制元件在气动系统中的应用。
1. 讲授:讲解气动执行元件的种类和特点、气动控制元件的功能和结构;2. 互动:引导学生探讨执行元件和控制元件在气动系统中的应用;3. 实操:演示执行元件和控制元件的安装与调试。
教学评估:1. 课堂问答:检查学生对气动执行元件、气动控制元件的理解;2. 实操考核:评估学生在实操中对执行元件和控制元件的安装与调试能力。
液压传动与气动技术课程教案典型气动系统
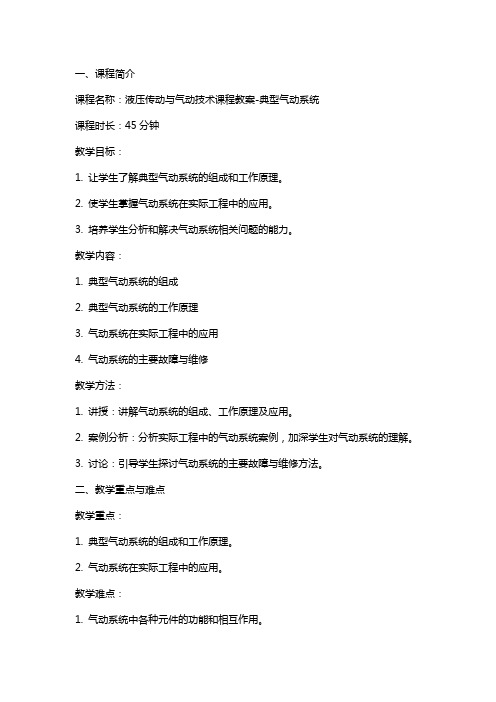
一、课程简介课程名称:液压传动与气动技术课程教案-典型气动系统课程时长:45分钟教学目标:1. 让学生了解典型气动系统的组成和工作原理。
2. 使学生掌握气动系统在实际工程中的应用。
3. 培养学生分析和解决气动系统相关问题的能力。
教学内容:1. 典型气动系统的组成2. 典型气动系统的工作原理3. 气动系统在实际工程中的应用4. 气动系统的主要故障与维修教学方法:1. 讲授:讲解气动系统的组成、工作原理及应用。
2. 案例分析:分析实际工程中的气动系统案例,加深学生对气动系统的理解。
3. 讨论:引导学生探讨气动系统的主要故障与维修方法。
二、教学重点与难点教学重点:1. 典型气动系统的组成和工作原理。
2. 气动系统在实际工程中的应用。
教学难点:1. 气动系统中各种元件的功能和相互作用。
2. 气动系统故障诊断与维修方法。
三、教学准备1. 教材或教学资源:《液压传动与气动技术》相关章节。
2. 教学PPT或幻灯片。
3. 气动系统示意图或实物模型。
4. 相关工程案例资料。
四、教学过程1. 导入:简要介绍液压传动与气动技术的基本概念,引出本节课的主题——典型气动系统。
2. 讲解典型气动系统的组成:讲解气源、执行元件、控制元件、辅助元件等组成部分的功能和作用。
3. 分析典型气动系统的工作原理:通过气动系统示意图或实物模型,讲解气动系统的工作原理和流程。
4. 案例分析:介绍实际工程中典型的气动系统应用案例,让学生了解气动系统在工程实践中的应用。
5. 讨论气动系统的主要故障与维修:引导学生分析气动系统可能出现的故障,讨论故障原因和维修方法。
6. 总结:回顾本节课的主要内容,强调气动系统的组成、工作原理及其在工程中的应用。
7. 作业布置:布置相关练习题,巩固所学知识。
五、教学反思课后对学生学习效果进行评估,针对存在的问题进行教学反思,调整教学方法,以提高教学效果。
关注学生对气动系统知识的实际应用能力,鼓励学生参与实践活动,提高学生的实际操作技能。
气动系统基础资料PPT课件

气源装置及气动元件
➢ 气源装置 ➢ 气动控制阀 ➢ 气动执行元件 ➢ 气动辅件
第9页/共101页
气压传动的组成及工作原理
• 气压传动,是以压缩空气为工作介质进行能量 传递和信号传递的一门技术。
• 气压传动的工作原理是利用空压机把电动机或 其它原动机输出的机械能转换为空气的压力能, 然后在控制元件的作用下,通过执行元件把压 力能转换为直线运动或回转运动形式的机械能, 从而完成各种动作,并对外做功。由此可知, 气压传动系统和液压传动系统类似,也是由四 部 分 组 成 的 , 它 们 第是10:页/共101页
第16页/共101页
气动控制阀
➢压力控制阀
• 减压阀—气动三大件之一, 用于稳定用气压力。
• 溢流阀—只作安全阀用。 • 顺序阀—由于气缸(马达)
的软特性,很难用顺序阀 实现两个执行元件的顺序 动作
第17页/共101页
减压阀(调压阀):减压和稳压
调整手柄
调压弹簧 下弹簧座 膜片
调压阀 图17-15
• 气体流动基本方程 • 连续性方程
ρ1v1A1 =ρ2v2A2 (注意ρ1≠ρ2)
第7页/共101页
• 伯努利方程
▪ 在低速流动时,气体可认为是不可压缩的( ρ =常数),则有
v2/2 ρ + p = 常数
p1+ v12/2 ρ = p2 + v22/2 ρ+ ⊿p ⊿p——压力损失,包括沿程压力损失和局部压力损失
• 节流阀的应用
节流阀的应用 图17-24 图17-24 节流阀的应用
第24页/共101页
排气节流阀: 不仅具有节流调速的作用,而且还
能起到降低排放气流噪声的作用
常见气路和设计教材PPT(共 36张)

例题1 设计一个双向调速的气路: 要求:1、执行元件为单作用气缸
2、其它元件任选
答案1
例题2 用单作用气缸设计一个生产流水线上的阻挡机构,要求气缸开始为伸出状态,当接 触产品并且完成此处工序后迅速缩回使工件通过。 要求:1、选择合适的气缸类型
2、画出气路图
答案2
例题3
设计一个气路
现有单动押出型气缸
•
3、大概是没有了当初那种毫无顾虑的勇气,才变成现在所谓成熟稳重的样子。
•
4、世界上只有想不通的人,没有走不通的路。将帅的坚强意志,就像城市主要街道汇集点上的方尖碑一样,在军事艺术中占有十分突出的地位。
•
5、世上最美好的事是:我已经长大,父母还未老;我有能力报答,父母仍然健康。
•
6、没什么可怕的,大家都一样,在试探中不断前行。
•
7、时间就像一张网,你撒在哪里,你的收获就在哪里。纽扣第一颗就扣错了,可你扣到最后一颗才发现。有些事一开始就是错的,可只有到最后才不得不承认。
(检测部分)
检测装置
限位开关 光电管 限位阀 接近开关 传感器
气动系统图实例
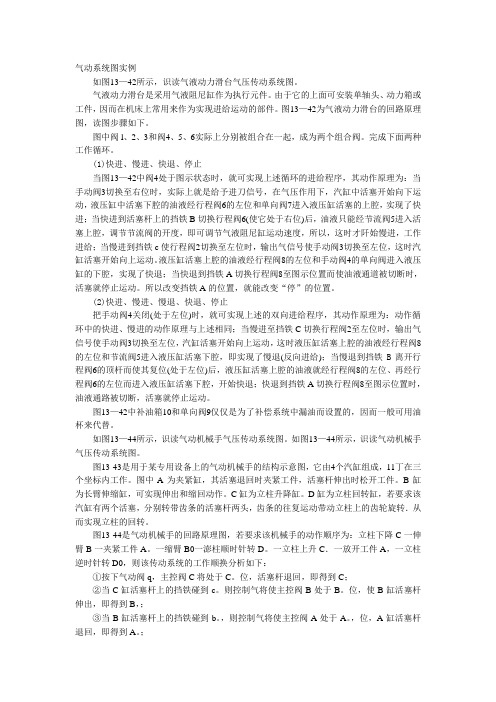
气动系统图实例如图13—42所示,识读气液动力滑台气压传动系统图。
气液动力滑台是采用气液阻尼缸作为执行元件。
由于它的上面可安装单轴头、动力箱或工件,因而在机床上常用来作为实现进给运动的部件。
图13—42为气液动力滑台的回路原理图,读图步骤如下。
图中阀l、2、3和阀4、5、6实际上分别被组合在一起,成为两个组合阀。
完成下面两种工作循环。
(1)快进、慢进、快退、停止当图13—42中阀4处于图示状态时,就可实现上述循环的进给程序,其动作原理为:当手动阀3切换至右位时,实际上就是给予进刀信号,在气压作用下,汽缸中活塞开始向下运动,液压缸中活塞下腔的油液经行程阀6的左位和单向阀7进入液压缸活塞的上腔,实现了快进;当快进到活塞杆上的挡铁B切换行程阀6(使它处于右位)后,油液只能经节流阀5进入活塞上腔,调节节流阀的开度,即可调节气液阻尼缸运动速度,所以,这时才阡始慢进,工作进给;当慢进到挡铁c使行程阀2切换至左位时,输出气信号使手动阀3切换至左位,这时汽缸活塞开始向上运动。
液压缸活塞上腔的油液经行程阀8的左位和手动阀4的单向阀进入液压缸的下腔,实现了快退;当快退到挡铁A切换行程阀8至图示位置而使油液通道被切断时,活塞就停止运动。
所以改变挡铁A的位置,就能改变“停”的位置。
(2)快进、慢进、慢退、快退、停止把手动阀4关闭(处于左位)时,就可实现上述的双向进给程序,其动作原理为:动作循环中的快进、慢进的动作原理与上述相同;当慢进至挡铁C切换行程阀2至左位时,输出气信号使手动阀3切换至左位,汽缸活塞开始向上运动,这时液压缸活塞上腔的油液经行程阀8的左位和节流阀5进入液压缸活塞下腔,即实现了慢退(反向进给);当慢退到挡铁B离开行程阀6的顶杆而使其复位(处于左位)后,液压缸活塞上腔的油液就经行程阀8的左位、再经行程阀6的左位而进入液压缸活塞下腔,开始快退;快退到挡铁A切换行程阀8至图示位置时,油液通路被切断,活塞就停止运动。
第九章 典型气动系统
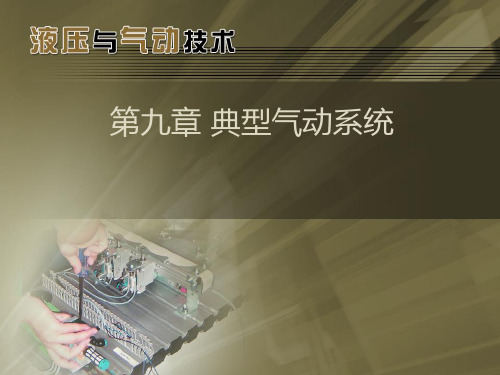
9.4 数控加工中心气动换刀系统
为XH754卧式加工中 心。这种换刀机构不 需要机械手,结构比 较简单。刀库转位由 伺服电动机通过齿轮 、蜗杆蜗轮的传动来 实现。气压传动系统 在换刀过程中实现主 轴的定位、松刀、拔 刀、向主轴锥孔吹气 和插刀等动作。
1)当数控系统发出换刀指令,主轴停转,同时4YA通电, 压缩空气经气动三大件1→换向阀4→单向节流阀5→主轴 定位缸A右腔,缸A活塞左移,使主轴自动定位。
3)当缸B活塞上的挡块碰到电气开关b1时,5YA断 电,1YA通电,阀1处于左位,回转缸D顺时针方 向回转,使机械手进入下料点下料。
4)当回转缸D活塞杆上的挡块压下电器行程开关c1 时,1YA断电,2YA通电,阀1处于右位,回转缸 D复位。
5)回转缸复位时,其上挡块碰到电气行程开关c0 时,6YA通电,2YA断电,阀2处于右位;水平缸 B活塞杆退回。
第九章 典型气动系统
9.1 工件夹紧气压传动系统
工件夹紧气压传动系统是机械加工自动线 、组合机床中常用的夹紧装置。
一个动作循环,即缸A活塞杆伸出压下(定 位)→夹紧缸B、C活塞杆伸出夹紧(加工)→ 夹紧缸B、C活塞杆返回→缸A的活塞杆返回。
当工件运动到指定位 置后,气缸A的活塞杆 伸出,将工件定位后 两侧的气缸B和C的活 塞杆伸出,从两侧面 夹紧工件,而后进行 机械加工
1YA:回转缸D转位 2YA:回转缸D复位 3YA:垂直缸C下降
4YA:垂直缸C上升 5YA:水平缸B伸出 6YA:水平缸B退回
1)按下启动按钮,4YA通电,阀7处于上位,压缩 空气进入垂直气缸C下腔,活塞杆上升。
2)当气缸C活塞杆上的挡块碰到电气行程开关a1时 ,4YA断电,5YA通电,阀2处于左位,水平气缸 B活塞杆伸出,带动机械手进入工作点并夹取工件 。
气动系统识别及原理认识PPT课件

高压压缩机
3.68MPa~3.92MPa 吹瓶间 吹瓶模具
●按空压机输出压力大小分类
低压空压机 0.2 ~ 1.0MPa 中压空压机 1.0 ~ 10MPa 高压空压机 10 ~ 100MPa 超高压空压机 >100MPa
可编辑
8
二.压力的概念及单位
2.1.一些压力的概念
绝对压力:相对于绝对真空的压力值
入、举起和进给等操作上。
可编辑
34
2.典型气缸的介绍—普通气缸
双作用气缸动作原理(Double-acting cylinders)
可编辑
35
气动系统
气动压力
空气压缩机
压缩空气
气动执行元件
气动控制元件
气动工作实例
2020/1/8
36
3、气缸的结构
1).结构和部件名称
可编辑
37
密封件
可编辑
38
2020/1/8
《设备基础知识》 气动部分
5
1、气动系统的构造
压缩空气的产生
压缩空气的处理及传输
可编辑
压缩空气 的消耗
6
2.DG工厂压缩机房实图
输送管道
储气罐
干燥器
压缩机
2020/1/8
《设备基础知识》 气动部分
7
3.DG工厂的压缩空气输送流程
低压压缩机
干燥 去除
水份
过滤 去除
微粒灰尘
低压储存缸 0.8MPa~0.9MPa 用途:生产线
可编辑
27
3、压缩空气的润滑装置
气动三联件FRL
可编辑28Fra bibliotek3、压缩空气的润滑装置
气动三联件FRL
可编辑
- 1、下载文档前请自行甄别文档内容的完整性,平台不提供额外的编辑、内容补充、找答案等附加服务。
- 2、"仅部分预览"的文档,不可在线预览部分如存在完整性等问题,可反馈申请退款(可完整预览的文档不适用该条件!)。
- 3、如文档侵犯您的权益,请联系客服反馈,我们会尽快为您处理(人工客服工作时间:9:00-18:30)。
第九章气压系统典型实例
第一节工件夹紧气压传动系统
工件夹紧气压传动系统是机械加工自动线和组合机床中常用的夹紧装置的驱动系统。
图9-1为机床夹具的气动夹紧系统,其动作循环是:当工件运动到指定位置后,气缸A活塞杆伸出,将工件定位后两侧的气缸B和C的活塞杆同时伸出,从两侧面对工件夹紧,然后再进行切削加工,加工完后各夹紧缸退回,将工件松开。
图9-1机床夹具气动夹紧系统
1—脚踏阀2—行程阀3、5—单向节流阀4、6—换向阀
具体工作原理如下:用脚踏下阀1,压缩空气进入缸A的上腔。
使活塞下降定位工件;当压下行程阀2时,压缩空气经单向节流阀5使二位三通气控换向阀6换向(调节节流阀开口可以控制阀6的延时接通时间),压缩空气通过阀4进入两侧气缸B和C的无杆腔,使活塞杆前进而夹紧工件。
然后钻头开始钻孔,同时流过换向阀4的一部分压缩空气经过单向节流阀3进入换向阀4右端,经过一段时间(由节流阀控制)后换向阀4右位接通,两侧气缸后退到原来位置。
同时,一部分压缩空气作为信号进入脚踏阀1的右端,使阀1右位接通,压缩空气进入缸A的下腔,使活塞杆退回原位。
活塞杆上升的同时使机动行程阀2复位,气控换向阀6也复位(此时主阀3右位接通),由于气缸B、C的无杆腔通过阀6、阀4排气,换向阀6自动复位到左位,完成一个工作循环。
该回路只有再踏下脚踏阀1才能开始下一个工作循环。
第二节数控加工中心气动系统
图9-2所示为某数控加工中心气动系统原理图,该系统主要实现加工中心的自动换刀功能,在换刀过程中实现主轴定位、主轴松刀、拔刀、向主轴锥孔吹气排屑和插刀动作。
图9-2 数控加工中心气动系统原理图
具体工作原理如下:当数控系统发出换刀指令时,主轴停止旋转,同时4YA通电,压缩空气经气动三联件1、换向阀4、单向节流阀5进入主轴定位缸A的右腔,缸A的活塞左移,使主轴自动定位。
定位后压下开关,使6Y A通电,压缩空气经换向阀6、快速排气阀8进入气液增压器B的上腔,增压腔的高压油使活塞伸出,实现主轴松刀,同时使8YA通电,压缩空气经换向阀9、单向节流阀11进入缸C的上腔,缸C下腔排气,活塞下移实现拔刀。
由回转刀库交换刀具,同时1Y A通电,压缩空气经换向阀2、单向节流阀3向主轴锥孔吹气。
稍后1YA断电、2YA通电,停止吹气,8YA断电、7YA通电,压缩空气经换向阀9、单向节流阀10进入缸C的下腔,活塞上移,实现插刀动作。
6Y A断电、5Y A通电,压缩空气经阀6进入气液增压器B的下腔,使活塞退回,主轴的机械机构使刀具夹紧。
4YA断电、3Y A通电,缸A的活塞在弹簧力的作用下复位,回复到开始状态,换刀结束。
第三节气动机械手气压传动系统
气动机械手是机械手的一种,它具有结构简单,重量轻,动作迅速,平稳可靠,不污染工作环境等优点。
在要求工作环境洁净、工作负载较小、自动生产的设备和生产线上应用广泛,它能按照预定的控制程序动作。
图9-3为一种简单的可移动式气动机械手的结构示意图。
它由A、B、C、D四个气缸组成,能实现手指夹持、手臂伸缩、立柱升降、回转四个
动作。
图9-3 气动机械手的结构示意图
图9-4为一种通用机械手的气动系统工作原理图(手指部分为真空吸头,即无A气缸
部分),要求其工作循环为:立柱上升→伸臂→立柱顺时针转→真空吸头取工件→立柱逆时
针转→缩臂→立柱下降。
图9-4 通用机械手气动系统工作原理图
三个气缸均有三位四通双电控换向阀1、2、7和单向节流阀3、4、5、6组成换向、调
速回路。
各气缸的行程位置均有电气行程开关进行控制。
表9-1为该机械手在工作循环中各
电磁铁的动作顺序表。
表9-1 电磁铁动作顺序表
垂直缸上升水平缸伸出回转缸转位回转缸复位水平缸退回垂直缸下降1Y A +-
2Y A +-
3Y A +
4Y A +-
5Y A +-
6Y A +-
下面结合表9-1来分析它的工作循环:
按下它的启动按钮,4Y A通电,阀7处于上位,压缩空气进入垂直气缸C下腔,活塞杆上升。
当缸C活塞上的挡块碰到电气行程开关a1时,4Y A断电,5Y A通电,阀2处于左位,水平气缸B活塞杆伸出,带动真空吸头进入工作点并吸取工件。
当缸B活塞上的挡块碰到电气开关b1时,5Y A断电,1YA通电,阀1处于左位,回转缸D顺时针方向回转,使真空吸头进入下料点下料。
当回转缸D活塞杆上的挡块压下电器行程开关c1时,1YA断电,2YA通电,阀1处于右位,回转缸b复位。
回转缸复位时,其上挡块碰到电气程开关c0时,6Y A通电,2YA断电,阀2处于右位,水平缸B活塞杆退回。
水平缸退回时,挡块碰到b0,6YA断电,3Y A通电,阀7处于下位,垂直缸活塞杆下降,到原位时,碰上电气行程开关a0,3Y A断电,至此完成一个工作循环,如再给启动信号。
可进行同样的工作循环。
根据需要只要改变电气行程开关的位置,调节单向节流阀的开度,即可改变各气缸的运动速度和行程。
第四节拉门自动开闭系统
该装置通过连杆机构将气缸活塞杆的直线运动转换成拉门商场、宾馆等公共场所使用的开闭运动,利用超低压气动阀来检测行人的踏板动作。
在拉门内、外装踏板6和11,踏板下方装有完全封闭的橡胶管,管的一端与超低压气动阀7和12的控制口连接。
当人站在踏板上时,橡胶管里压力上升,超低压气动阀动作。
其气动回路如图9-5所示。
图9-5 拉门自动开闭气压传动系统
首先使手动阀1上位接入工作状态,空气通过气动换向阀2、单向节流阀3进入气缸4的无杆腔,将活塞杆推出(门关闭)。
当人站在踏板6上后,气动控制阀7动作,空气通过梭阀8、单节流阀9和气罐10使气动换向阀2换向,压缩空气进入气缸4的有杆腔,活塞杆退回(门打开)。
当行人经过门后踏上踏板11时,气动控制阀12动作,使梭阀8上面的通口关闭,下面的通口接通(此时由于人已离开踏板6,阀7复位)。
气罐10中的空气经单向节流阀9、梭阀8和阀12放气(人离开踏板11后,阀12已复位),经过延时(由节流阀控制)后阀2复位,气缸4的无杆腔进气,活塞杆伸出(关闭拉门)。
该回路利用逻辑“或”的功能,回路比较简单,很少产生误动作。
行人从门的哪一边进出均可。
减压阀13可使关门的力自由调节,十分便利。
如将手动阀复位,则可变为手动门。
思考题及习题
9-1在图9-1所示的工件夹紧气压传动系统中,工件夹紧的时间是怎样调节的?
9-2简述加工中心气动系统工作原理?
9-3在图9-3中,要求该机械手的工作循环是:立柱下降→伸臂→立柱逆时针转→(真空吸头取工件)→立柱顺时针转→缩臂→立柱上升。
试画出电磁铁动作顺序表,分析它的工作循环。
9-4在自动拉门气压传动系统中利用了哪个元件的什么逻辑功能?。