切削因素对粗糙度的影响.
切削力与表面粗糙度间的关系分析与建模
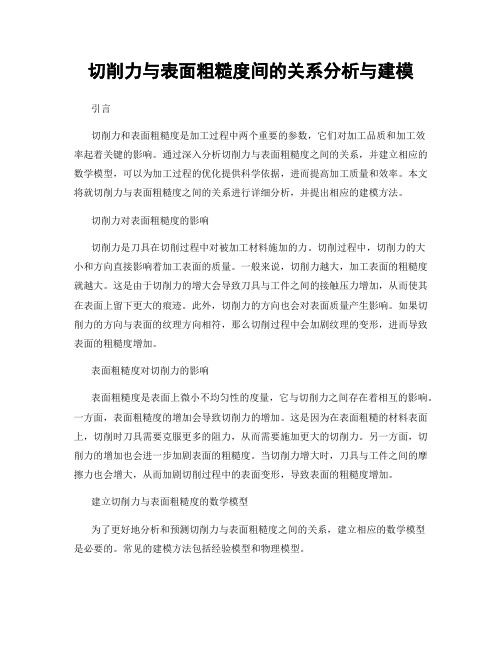
切削力与表面粗糙度间的关系分析与建模引言切削力和表面粗糙度是加工过程中两个重要的参数,它们对加工品质和加工效率起着关键的影响。
通过深入分析切削力与表面粗糙度之间的关系,并建立相应的数学模型,可以为加工过程的优化提供科学依据,进而提高加工质量和效率。
本文将就切削力与表面粗糙度之间的关系进行详细分析,并提出相应的建模方法。
切削力对表面粗糙度的影响切削力是刀具在切削过程中对被加工材料施加的力。
切削过程中,切削力的大小和方向直接影响着加工表面的质量。
一般来说,切削力越大,加工表面的粗糙度就越大。
这是由于切削力的增大会导致刀具与工件之间的接触压力增加,从而使其在表面上留下更大的痕迹。
此外,切削力的方向也会对表面质量产生影响。
如果切削力的方向与表面的纹理方向相符,那么切削过程中会加剧纹理的变形,进而导致表面的粗糙度增加。
表面粗糙度对切削力的影响表面粗糙度是表面上微小不均匀性的度量,它与切削力之间存在着相互的影响。
一方面,表面粗糙度的增加会导致切削力的增加。
这是因为在表面粗糙的材料表面上,切削时刀具需要克服更多的阻力,从而需要施加更大的切削力。
另一方面,切削力的增加也会进一步加剧表面的粗糙度。
当切削力增大时,刀具与工件之间的摩擦力也会增大,从而加剧切削过程中的表面变形,导致表面的粗糙度增加。
建立切削力与表面粗糙度的数学模型为了更好地分析和预测切削力与表面粗糙度之间的关系,建立相应的数学模型是必要的。
常见的建模方法包括经验模型和物理模型。
经验模型是根据大量实验数据总结出来的经验公式,它基于试验结果来预测切削力和表面粗糙度之间的关系。
经验模型的建立过程较为简单,但其预测的准确性可能较低,并且适用范围有限。
常见的经验模型包括切削力公式和表面粗糙度公式等。
物理模型则基于切削力和表面粗糙度之间的物理机理建立,通常使用数学方程或有限元模拟等方法进行求解。
物理模型的建立较为复杂,需要考虑切削力的各个因素对表面粗糙度的影响,并进行参数的优化调整。
切削三要素对表面粗糙度的影响说课稿
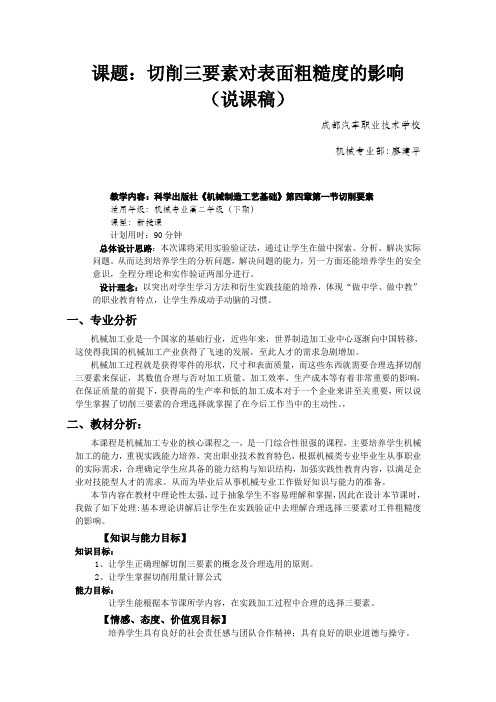
课题:切削三要素对表面粗糙度的影响(说课稿)成都汽车职业技术学校机械专业部:廖建平教学内容:科学出版社《机械制造工艺基础》第四章第一节切削要素适用年级:机械专业高二年级(下期)课型:新授课计划用时:90分钟总体设计思路:本次课将采用实验验证法,通过让学生在做中探索、分析、解决实际问题。
从而达到培养学生的分析问题,解决问题的能力,另一方面还能培养学生的安全意识,全程分理论和实作验证两部分进行。
设计理念:以突出对学生学习方法和衍生实践技能的培养,体现“做中学、做中教”的职业教育特点,让学生养成动手动脑的习惯。
一、专业分析机械加工业是一个国家的基础行业,近些年来,世界制造加工业中心逐渐向中国转移,这使得我国的机械加工产业获得了飞速的发展,至此人才的需求急剧增加。
机械加工过程就是获得零件的形状,尺寸和表面质量,而这些东西就需要合理选择切削三要素来保证,其数值合理与否对加工质量、加工效率、生产成本等有着非常重要的影响,在保证质量的前提下,获得高的生产率和低的加工成本对于一个企业来讲至关重要,所以说学生掌握了切削三要素的合理选择就掌握了在今后工作当中的主动性。
,二、教材分析:本课程是机械加工专业的核心课程之一,是一门综合性很强的课程,主要培养学生机械加工的能力,重视实践能力培养,突出职业技术教育特色,根据机械类专业毕业生从事职业的实际需求,合理确定学生应具备的能力结构与知识结构,加强实践性教育内容,以满足企业对技能型人才的需求。
从而为毕业后从事机械专业工作做好知识与能力的准备。
本节内容在教材中理论性太强,过于抽象学生不容易理解和掌握,因此在设计本节课时,我做了如下处理:基本理论讲解后让学生在实践验证中去理解合理选择三要素对工件粗糙度的影响。
【知识与能力目标】知识目标:1、让学生正确理解切削三要素的概念及合理选用的原则。
2、让学生掌握切削用量计算公式能力目标:让学生能根据本节课所学内容,在实践加工过程中合理的选择三要素。
2.2 切削对表面加工的影响(了解)
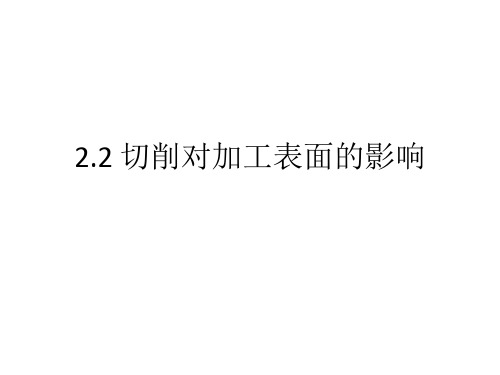
在切削过程中,由于切削力的作用,工件已
加工表面产生了很大的塑性变形且温度升 高。 而晶格扭曲,晶粒长大、破碎,阻碍了表 层金属的进一步变形,使材料强化,硬度提高; 同时较高的切削温度又将引起金属的相变。
可见,工件已加工表面的硬度变化就是这种 强化和相变作用的综合结果。
当塑性变形引起的强化起主导作用时,已 加工表面就硬化;当较高的切削温度引起的 相变起主导作用时,则根据相变的具体情况 而定,如在磨削淬火钢时,若发生退火,则表层 硬度降低,但在充分冷却的条件下,却可能引 起二次淬火而使表层硬度提高。
余面积、积屑瘤、振动波纹、切削力、切 削热等。 要做到这些,可以从刀具材料、刀
具角度、切削用量、工件材料、切削液等 多方面着手,尽可能地減軽以上因素对工件 已加工表面质量的不良影响 。
2.积屑瘤
在采用中等切削速度而又能形成连续性切 屑的情况下,加工一般钢料或其他塑性材料 时,切屑沿刀具前面滑出时,其底层受到很大 的摩擦力 。 当摩擦阻力超过切屑内部分子 间的结合力时, 一部分金属停滞下来,使刀具 切削刃附近的前面上粘附上一块很硬的金 属 。 这块很硬的金属称为积屑瘤 。
在切削处于相对稳定的状态时,积屑 瘤 可 以代替刀刃进行切削,粗加工时对刀刃有保 护作用 。 但积屑瘤轮廓很不规则,切削时会 将工件表面划出深浅、宽窄不一的沟纹;脱
生松动,影响传动副的工作性能。
还有一些其他原因,如鱗刺、刀具的边界 磨损、排屑不 畅而划伤工件已加工表面等, 均会使表面粗糙度值增大。
二、 表层材质变化
1.加工硬化 加工硬化是指在切削过程中,工件已加
工表面受刀刃和后面的挤压和摩擦而产生 塑性变形, 使表层组织发生变化,硬度显著提 高的现象。 其硬化层深度可以达到 0·02 -0. 30 mm,表层硬度约为原工件材料的1. 2-2倍。
影响机械加工表面粗糙度的几个因素及措施

职教类影响机械加工表面粗糙度的几个因素及措施摘要:表面粗糙度是零件表面所具有的微小峰谷的不平程度,它是评价零件的一项重要指标。
一般说来,它的波距和波高都比较小,是一种微观的几何形状误差。
对机械加工表面,表面粗糙度是由切削时的刀痕,刀具和加工表面之间的摩擦,切削时的塑性变形,以及工艺系统中的高频振动等原因所造成的。
表面粗糙度是检验零件质量的主要依据,它的选择直接关系到生产成本、产品的质量、使用寿命。
关键词:机械加工表面粗糙度提高措施随着工业技术的飞速发展,机器的使用要求越来越高,一些重要零件在高压力、高速、高温等高要求条件下工作,表面层的任何缺陷,不仅直接影响零件的工作性能,而且还可能引起应力集中、应力腐蚀等现象,将进一步加速零件的失效,这一切都与加工表面质量有很大关系。
因而表面质量问题越来越受到各方面的重视。
一、机械加工表面粗糙度对零件使用性能的影响表面粗糙度对零件的配合精度,疲劳强度、抗腐蚀性,摩擦磨损等使用性能都有很大的影响。
1、表面质量对零件配合精度的影响(1)对间隙配合的影响由于零件表面的凹凸不平,两接触表面总有一些凸峰相接触。
表面粗糙度过大,则零件相对运动过程中,接触表面会很快磨损,从而使间隙增大,引起配合性质改变,影响配合的稳定性。
特别是在零件尺寸和公差小的情况下,此影响更为明显。
(2)对过盈配合的影响粗糙表面在装配压入过程中,会将相接触的峰顶挤平,减少实际有效过盈量,降低了配合的连接强度。
2、表面质量对疲劳强度的影响零件表面越粗糙,则表面上的凹痕就越深明,产生的应力集中现象就越严重。
当零件受到交变载荷的作用时,疲劳强度会降低,零件疲劳损坏的可能性增大。
3、表面质量对零件抗腐蚀性的影响零件表面越粗糙,则积聚在零件表面的腐蚀气体或液体也越多,且通过表面的微观凹谷向零件表层渗透,形成表面锈蚀。
4、表面质量对零件摩擦磨损的影响两接触表面作相对运动时,表面越粗糙,摩擦系数越大,摩擦阻力越大,因摩擦消耗的能量也越大,并且还影响零件相对运动的灵活性。
浅谈加工表面粗糙度和物理力学性能的影响因素研究
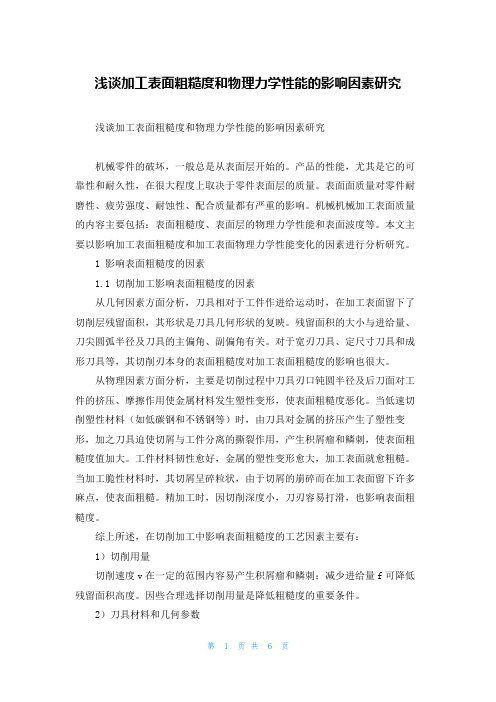
浅谈加工表面粗糙度和物理力学性能的影响因素研究浅谈加工表面粗糙度和物理力学性能的影响因素研究机械零件的破坏,一般总是从表面层开始的。
产品的性能,尤其是它的可靠性和耐久性,在很大程度上取决于零件表面层的质量。
表面面质量对零件耐磨性、疲劳强度、耐蚀性、配合质量都有严重的影响。
机械机械加工表面质量的内容主要包括:表面粗糙度、表面层的物理力学性能和表面波度等。
本文主要以影响加工表面粗糙度和加工表面物理力学性能变化的因素进行分析研究。
1 影响表面粗糙度的因素1.1 切削加工影响表面粗糙度的因素从几何因素方面分析,刀具相对于工件作进给运动时,在加工表面留下了切削层残留面积,其形状是刀具几何形状的复映。
残留面积的大小与进给量、刀尖圆弧半径及刀具的主偏角、副偏角有关。
对于宽刃刀具、定尺寸刀具和成形刀具等,其切削刃本身的表面粗糙度对加工表面粗糙度的影响也很大。
从物理因素方面分析,主要是切削过程中刀具刃口钝圆半径及后刀面对工件的挤压、摩擦作用使金属材料发生塑性变形,使表面粗糙度恶化。
当低速切削塑性材料(如低碳钢和不锈钢等)时,由刀具对金属的挤压产生了塑性变形,加之刀具迫使切屑与工件分离的撕裂作用,产生积屑瘤和鳞刺,使表面粗糙度值加大。
工件材料韧性愈好,金属的塑性变形愈大,加工表面就愈粗糙。
当加工脆性材料时,其切屑呈碎粒状,由于切屑的崩碎而在加工表面留下许多麻点,使表面粗糙。
精加工时,因切削深度小,刀刃容易打滑,也影响表面粗糙度。
综上所述,在切削加工中影响表面粗糙度的工艺因素主要有:1)切削用量切削速度v在一定的范围内容易产生积屑瘤和鳞刺;减少进给量f可降低残留面积高度。
因些合理选择切削用量是降低粗糙度的重要条件。
2)刀具材料和几何参数实践表明,在切削条件相同时,用硬质合金刀具加工的工作表面粗糙度比用高速钢刀具加工的低。
用金钢石车刀加工因不易形成积屑瘤,故可获得粗糙度很低的表面。
刀类圆弧半径rE、主偏角KC和副偏角kcC均影响残留面积的大小。
影响表面粗糙度的因素

.影响表面粗糙度的因素1.切削加工中影响表面粗糙度的因素1)?几何因素2)物理因素切削加工后表面粗糙度的实际轮廓形状一般都与由纯几何因素形成的理想轮廓有较大的差别。
这是由于存在与被加工材料的性质及切削机理有关的物理因素的缘故。
采用低切削速度加工塑性金属材料(如低碳钢、铬钢、不锈钢、高温合金、铝合金等)时,容易出现积屑瘤与鳞刺,使加工表面粗糙度严重恶化,成为影响加工表面质量的主要因素。
刀具与被加工材料的挤压与磨擦使金属材料发生塑性变形,也会增大表面粗糙度。
切削加工中的振动,使工件的表面粗糙度增大。
从物理因素看,降低表面粗糙度的主要措施是减少加工时的塑性变形,避免产生积屑瘤和鳞刺。
其主要影响因素有切削速度、被加工材料的性质、刀具的几何形状、材料性质和刃磨质量。
适当增大刀具的前角,可以降低被切削材料的塑性变形;降低刀具前刀面和后刀面的表面粗糙度可以抑制积屑瘤的生成;增大刀具后角,可以减少刀具和工件的摩擦;合理选择冷却润滑液,可以减少材料的变形和摩擦,降低切削区的温度;采取上述各项措施均有利于减小加工表面的粗糙度。
2.磨削中影响表面粗糙度的因素三.影响加工表面金属层物理力学性能的因素加工过程中,由于切削力和切削热的作用,工件表面金属层的物理力学性能会发生很大的变化,导致表面层金属和基体材料的性能有很大的差异。
其影响因素主要表现为三个方面。
1.表面层金属材料的加工硬化切削(磨削)过程中产生的塑性变形,会使表层金属的晶格发生畸变,晶粒间产生剪切滑移,晶粒被拉长,甚至破碎,从而使表层金属的硬度和强度提高,这种现象称为加工硬化。
加工硬化的程度取决于塑性变形的程度。
影响加工硬化的因素(1)?切削力越大,塑性变形越大,硬化程度也越大。
因此,当进给量、背吃刀量增大,刀具前角减小时,都会因切削力增大而使加工硬化程度增大。
(2)?切削温度越高,会使加工硬化作用减小。
如切削速度增大,会使切削温度升高,加工硬化程度将会减小。
金属切削中的切削参数对加工表面粗糙度的影响因素分析
金属切削中的切削参数对加工表面粗糙度的影响因素分析金属切削是一种常见的加工方法,其表面粗糙度直接影响着工件的质量和性能。
而切削参数是控制金属切削加工过程中的重要因素之一。
本文将分析不同切削参数对加工表面粗糙度的影响因素。
切削速度是切削过程中最直接影响加工表面粗糙度的参数之一。
一方面,较高的切削速度可以有效减小切削力,防止刀具磨损过快,从而减少加工表面的毛刺和热裂纹等缺陷。
另一方面,切削速度过高也会增加切削温度,容易导致材料软化和工件表面烧伤。
因此,在实际应用中需要根据具体材料和切削条件进行合理的选择。
切削深度是指每次切削过程中微小切削层的厚度。
切削深度的增加会增加金属切削过程中的切削力和切削温度。
当切削深度过大时,刀具容易磨损,加工表面粗糙度也会相应增加。
因此,在切削深度的选择上,需要综合考虑材料的性质、刀具的工作特点以及加工表面的粗糙度要求。
进给量是指刀具在单位时间内沿工件表面移动的距离。
较大的进给量会导致切削力的增大,从而增加加工表面的粗糙度。
因此,在控制加工表面粗糙度时,需要选择适当的进给量,以确保加工质量和生产效率的平衡。
刀具的选择对加工表面粗糙度也有重要影响。
刀具的几何形状、材料和涂层等因素会直接影响加工表面的质量和粗糙度。
例如,具有较小刀尖半径的刀具可以得到较好的加工表面质量,但刀具寿命会相应减少。
相反,较大刀尖半径的刀具可以提高刀具寿命,但加工表面的粗糙度会相应增加。
因此,在选择刀具时,需要根据具体的加工要求进行合理搭配。
除了以上切削参数外,材料的性质也会对加工表面粗糙度产生影响。
不同的材料对切削力、切削温度等参数的响应不同,因此加工表面的粗糙度也会有差异。
例如,硬材料通常需要较高的切削速度和切削深度,以获得更好的加工表面质量。
此外,切削液的使用也可以改善加工表面粗糙度。
切削液能够冷却切削区域,降低切削温度,减少切削力,从而有助于提高加工表面的质量。
同时,切削液还能起到润滑和清洁的作用,延长工具的使用寿命。
切削速度与表面粗糙度关系
切削速度与表面粗糙度关系引言:在机械加工过程中,切削速度是一个重要的参数,它直接影响到加工表面的质量和粗糙度。
切削速度的选择对于提高加工效率、降低成本以及改善产品质量具有重要意义。
本文将探讨切削速度与表面粗糙度之间的关系,并分析其影响因素。
一、切削速度对表面粗糙度的影响切削速度是指在单位时间内切削刀具相对于工件的线速度。
切削速度的变化会直接影响到切削刀具与工件之间的摩擦情况,从而影响到加工表面的粗糙度。
一般来说,切削速度越高,加工表面的粗糙度越低;反之,切削速度越低,加工表面的粗糙度越高。
二、切削速度与切削力的关系切削速度的增加会使切削力增加,而切削力的大小直接影响到加工表面的质量。
当切削速度过高时,切削力增大,易导致切削刀具与工件之间的磨损加剧,从而影响到加工表面的粗糙度。
因此,在选择切削速度时,需要综合考虑切削力的大小,以确保加工表面的质量。
三、切削速度与切削温度的关系切削速度的增加会使切削温度升高,而切削温度的高低也会对加工表面的粗糙度产生影响。
当切削温度过高时,易导致工件表面产生热变形和热裂纹,从而影响到加工表面的质量。
因此,在选择切削速度时,需要兼顾切削温度的控制,以确保加工表面的粗糙度达到要求。
四、切削速度与切削液的关系切削液在机械加工中起着冷却、润滑和清洁的作用,对于控制切削温度、减小切削力以及改善加工表面的质量具有重要意义。
切削速度的增加会使切削液的使用效果降低,从而影响到加工表面的粗糙度。
因此,在选择切削速度时,需要根据具体情况合理选择切削液的类型和使用方式,以最大程度地提高加工表面的质量。
五、其他影响切削速度与表面粗糙度的因素除了切削速度外,还有一些其他因素也会对加工表面的粗糙度产生影响,如切削刀具的材料和几何形状、切削深度、进给量等。
这些因素与切削速度之间存在着复杂的相互关系,需要综合考虑,进行合理的调整,以达到最佳的加工效果。
结论:切削速度是影响加工表面粗糙度的重要因素之一。
表面粗糙度及其影响因素
表面粗糙度及其影响因素一、切削加工中影响表面粗糙度的因素影响表面粗糙度的因素主要有几何因素和物理因素。
1.几何因素:式中 f ——进给量。
Kr ——主偏角。
Kr’——副偏角考虑刀尖圆弧角:式中 f ——进给量。
r ——刀尖圆弧半径。
如图11-8、9所示,用刀尖圆弧半径r=0的车刀纵车外圆时,每完成一单位进给量f后,留在已加工表面上的残留面积,它的高度Rmax即为理论粗糙度的轮廓最大高度Ry。
图11- 8 图11- 9图11- 10 加工后表面实际轮廓和理论轮廓切削加工后表面粗糙度的实际轮廓形状,一般都与纯几何因素所形成的理论轮廓有较大的差别,如图11-10。
这是由于切削加工中有塑性变形发生的缘故。
生产中,若使用的机床精度高和材料的切削加工性好,选用合理的刀具几何形状、切削用量和在刀具刃磨质量高、工艺系统刚性足够情况下,加工后表面实际粗糙度接近理论粗糙度,这样减小表面粗糙度数值、提高加工表面质量的措施,主要是减小残留面积的高度Ry。
2.物理因素多数情况下是在已加工表面的残留面积上叠加着一些不规则的金属生成物、粘附物或刻痕。
形成它们的原因有积屑瘤、鳞刺、振动、摩擦、切削刃不平整、切屑划伤等。
3.积屑瘤的影响积屑瘤的生成、长大和脱落将严重影响工件表面粗糙度。
同时,由于部分积屑瘤碎屑嵌在工件表面上,在工件表面上形成硬质点。
见图11-11。
图11- 11 图11- 12鳞刺的影响鳞刺的出现,使已加工表面更为粗糙不平。
鳞刺的形成分为:抹拭阶段:前一鳞刺已经形成,新鳞刺还未出现;而切屑沿着前刀面流出,切屑以刚切离的新鲜表面抹拭刀——屑摩擦面,将摩擦面上有润滑作用的吸附膜逐渐拭净,以致摩擦系数逐渐增大,并使刀具和切屑实际接触面积增大,为这两相摩擦材料的冷焊创造条件,如图11-12(a)。
导裂阶段:由于在第一阶段里,切屑将前刀面上的摩擦面抹拭干净,而前刀面与切屑之间又有巨大的压力作用着,于是切屑与刀具就发生冷焊现象,切屑便停留在前刀面上,暂时不再沿前刀面流出。
机械零件表面质量影响粗糙度的原因
机械零件加工质量中,表面质量是衡量一个机械零件是否合格的重要指标之一。
而表面粗糙度则是衡量表面质量的指标。
粗糙度越高,表面质量越差,越容易造成机械设备的损坏。
那么,在机械零件的加工生产中,主要影响粗糙度的原因都有哪些呢?1、切削加工影响表面粗糙度因素在进行切削加工的时候,表面会留下切削层残留面积,其形状是刀具几何形状的的反应,想要减小残留面积的高度,可以减小进给量、主偏角、副偏角并增大刀尖圆弧半径。
除此之外,适当让刀具的前角增大,可以让塑性变形的程度减少,同时配合使用润滑液、提高刀具刃磨质量,还有助于减小切削时的塑性变形并抑制刀瘤、鳞刺的生成,对于减小表面粗糙度还是有一定帮助的。
2、工件材料的性质对塑性材料进行加工时,刀具会对金属产生挤压作用,出现塑性变形现象,在加上刀具会让切屑与工件产生撕裂作用,让金属的表面粗糙度变大,工件材料韧性越好,金属的塑性变形越大,加工表面就会越粗糙。
对脆性材料进行加工时,会产生碎粒切屑,这会在金属加工表面造成污染,留下麻点,让金属的表面粗糙度变大。
3、磨削加工影响表面粗糙度的因素磨削加工表面粗糙度的形成过程与切削加工表面粗糙度形成过程一样。
磨削加工表面粗糙度的形成,也是因为几何因素与表面金属的塑性变形来决定的。
影响磨削表面粗糙的主要因素有:(1)磨削加工中砂轮的粒度与硬度砂轮硬度的选择要根据产品表面精度要求来决定,应让磨粒钝化后及时脱落,露出新的磨粒后继续磨削。
砂轮粒度越细,单位面积上磨粒数越多。
(2)砂轮的修整由于磨削加工中,砂轮在磨削过程中会出现钝化,所以对砂轮应该进行及时修整,确保砂轮的微刃性和等高性。
(3)工件材质工件材料的硬度、塑性、韧性和导热性,对于表面粗糙度都会有一定的影响,工件硬度高,磨粒易钝化。
工件硬度低,砂轮容易阻塞,这些都会造成表面粗糙度增高。
- 1、下载文档前请自行甄别文档内容的完整性,平台不提供额外的编辑、内容补充、找答案等附加服务。
- 2、"仅部分预览"的文档,不可在线预览部分如存在完整性等问题,可反馈申请退款(可完整预览的文档不适用该条件!)。
- 3、如文档侵犯您的权益,请联系客服反馈,我们会尽快为您处理(人工客服工作时间:9:00-18:30)。
“工程材料与成形加工基础实验远程教学系统”用户手册
切削因素对粗糙度的影响
实验目的:1.了解加工表面粗糙度的影响因素. 2.了解降低表面粗糙度的工艺措施.
实验原理:
一、影响表面粗糙度的因素
1、切削时刀刃在已加工表面上遗留下来的刀痕------主要因素;
2、切削时塑性材料前刀面的挤压和摩擦作用,形成积屑瘤或鳞刺;
3、刀具后刀面与已加工表面的摩擦及挤压导致弹性恢复、硬化甚至龟裂;
4、切削脆性材料时切削崩碎形成的麻点痕迹;
5、加工系统的高频震动形成的振纹。
、降低加工表面粗糙度的工艺措施
1、合适的切削条件
(1)切削速度v: 塑性材料,用低速或高速,避免产生切削瘤,降低表面粗糙度.
(2)进给量f: 减小进给量,可有效地减小残留面积高度,降低表面粗糙度.
(3)背吃刀量: 背吃刀量过小,则刀尖圆弧过度刃口切不下切削层,加工表面引起附加塑性变形,影响表面粗糙度.
(4)切削液: 冷却润滑作用,减小摩擦,降低温度,从而减小切削过程的塑性变形,抑制鳞刺和积屑瘤的生成,降低表面粗糙度.
2、合理的刀具几何参数和刀具材料
(1)前角γ o : 增大γ o, 可抑制积屑瘤产生,降低表面粗糙度.
(2)副偏角k 'r :减小k 'r,可减小残留面积,高度h.降低表面粗糙度.
(3刀尖圆弧过渡半径r Σ : 增大r Σ ,可减小残留高度, 降低表面粗糙度.
(4)刀具材料: 刀具材料与工件材料分子亲和力小,前刀面上形成积屑瘤的机率小,则表面粗糙度下降.
3、改善工件材料的力学性能和金相组织
材料硬度越高→切削抗力越大→切削温度越高→刀具磨损越快→表面质量越不稳定. 材料越软(塑性越好) →切削变形越大→切削温度越高→刀具磨损越快→表面质量越低.
处理方法:
低碳钢(塑性大): 正火(提高硬度).
高碳钢(硬度高):球化退火(提高塑性).
中碳钢可调质处理(提高力学性能).
实验设备:。