PCB资料→印制电路板可制造性设计规范
PCBA可制造设计规范
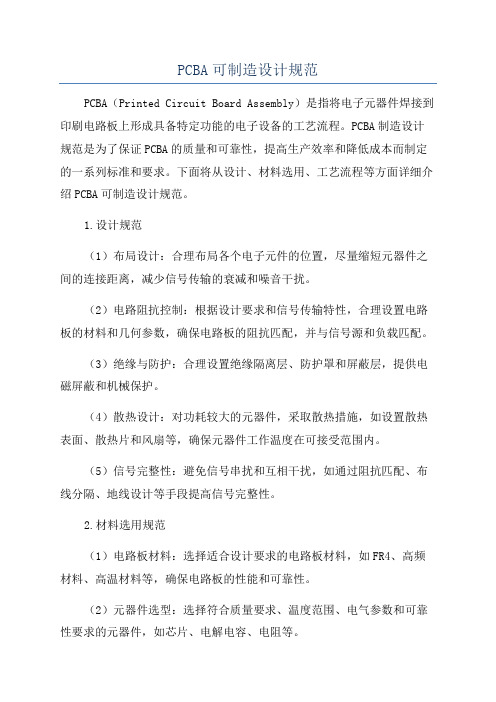
PCBA可制造设计规范PCBA(Printed Circuit Board Assembly)是指将电子元器件焊接到印刷电路板上形成具备特定功能的电子设备的工艺流程。
PCBA制造设计规范是为了保证PCBA的质量和可靠性,提高生产效率和降低成本而制定的一系列标准和要求。
下面将从设计、材料选用、工艺流程等方面详细介绍PCBA可制造设计规范。
1.设计规范(1)布局设计:合理布局各个电子元件的位置,尽量缩短元器件之间的连接距离,减少信号传输的衰减和噪音干扰。
(2)电路阻抗控制:根据设计要求和信号传输特性,合理设置电路板的材料和几何参数,确保电路板的阻抗匹配,并与信号源和负载匹配。
(3)绝缘与防护:合理设置绝缘隔离层、防护罩和屏蔽层,提供电磁屏蔽和机械保护。
(4)散热设计:对功耗较大的元器件,采取散热措施,如设置散热表面、散热片和风扇等,确保元器件工作温度在可接受范围内。
(5)信号完整性:避免信号串扰和互相干扰,如通过阻抗匹配、布线分隔、地线设计等手段提高信号完整性。
2.材料选用规范(1)电路板材料:选择适合设计要求的电路板材料,如FR4、高频材料、高温材料等,确保电路板的性能和可靠性。
(2)元器件选型:选择符合质量要求、温度范围、电气参数和可靠性要求的元器件,如芯片、电解电容、电阻等。
(3)焊接材料:选用适合工艺流程的焊接材料,如无铅焊料、焊膏等,确保焊接质量和可靠性。
3.工艺流程规范(1)印刷:确保PCB板材表面光洁、均匀,印刷厚度均匀一致,避免短路和偏厚现象。
(2)贴片:确保元器件与PCB板材精准对位,减少误差和偏离,避免虚焊、漏焊和偏焊。
(3)回流焊接:控制焊接温度和时间,确保焊点可靠性和焊接质量,避免过热和虚焊。
(4)清洗:清除焊接过程中产生的残留物,如焊膏、金属颗粒等,保证PCBA表面的干净和可靠性。
(5)测试与检验:进行全面的功能测试和质量检验,确保PCBA的功能和质量达到设计要求。
4.环境标准(1)温度和湿度:控制生产环境的温度和湿度,以确保PCBA的稳定性和可靠性。
印制电路板工艺的设计规范标准[详]
![印制电路板工艺的设计规范标准[详]](https://img.taocdn.com/s3/m/afcaeb8fe45c3b3566ec8b6f.png)
印制电路板工艺设计规范一、目的:规范印制电路板工艺设计,满足印制电路板可制造性设计的要求,为硬件设计人员提供印制电路板工艺设计准则,为工艺人员审核印制电路板可制造性提供工艺审核准则。
二、范围:本规范规定了硬件设计人员设计印制电路板时应该遵循的工艺设计要求,适用于公司设计的所有印制电路板。
三、特殊定义:印制电路板(PCB, printed circuit board):在绝缘基材上,按预定设计形成印制组件或印制线路或两者结合的导电图形的印制板。
组件面(Component Side):安装有主要器件(IC 等主要器件)和大多数元器件的印制电路板一面,其特征表现为器件复杂,对印制电路板组装工艺流程有较大影响。
通常以顶面(Top )定义。
焊接面(Solder Side ):与印制电路板的组件面相对应的另一面,其特征表现为元器件较为简单。
通常以底面(Bottom )定义。
金属化孔( Plated Through Hole):孔壁沉积有金属的孔。
主要用于层间导电图形的电气连接。
非金属化孔(Unsupported hole):没有用电镀层或其它导电材料涂覆的孔。
引线孔(组件孔):印制电路板上用来将元器件引线电气连接到印制电路板导体上的金属化孔。
通孔:金属化孔贯穿连接(Hole Through Connection)的简称。
盲孔(Blind via ):多层印制电路板外层与内层层间导电图形电气连接的金属化孔。
埋孔 (Buried Via) :多层印制电路板内层层间导电图形电气连接的金属化孔。
测试孔:设计用于印制电路板及印制电路板组件电气性能测试的电气连接孔。
安装孔:为穿过元器件的机械固定脚,固定元器件于印制电路板上的孔,可以是金属化孔,也可以是非金属化孔,形状因需要而定。
塞孔:用阻焊油墨阻塞通孔。
阻焊膜(Solder Mask, Solder Resist):用于在焊接过程中及焊接后提供介质和机械屏蔽的一种覆膜。
印制电路板设计规范

印制电路板设计规范印制电路板(Printed Circuit Board,简称PCB)设计规范是指为了保证电路板的设计、制造和使用中的质量和可靠性,制定的一系列规则和准则。
以下是一份典型的PCB设计规范,详细介绍了各个方面的要求。
一、电路板尺寸和层数1.PCB尺寸应符合实际需求,合理调整尺寸以满足其他设备的要求。
2.PCB层数应根据电路复杂度、电磁兼容性和成本等因素合理选择。
二、布局设计1.元器件布局应科学合理,尽量避免元器件之间的相互干扰。
2.高频信号和低频信号的布局应相互分离,以减少相互干扰。
3.电源和地线应尽量宽厚,减小电阻和电感,提高电路的稳定性。
三、网络连接1.信号线应尽量短、直且排布整齐,最大程度地避免信号交叉和串扰。
2.不同信号层之间的信号连线应通过过孔、通孔或阻抗匹配的方式进行连接。
四、电源和地线设计1.电源线和地线应尽量宽厚,减小电阻和电感,提高电压的稳定性。
2.电源和地线的路径应尽量短,减少电源回路的串扰和噪声。
五、元器件选择和焊接1.元器件的选择应根据设计需求,考虑其性能、品质和可靠性。
2.焊接工艺应符合IPC-610标准,保证焊点的牢固和质量。
六、阻抗匹配和信号完整性1.高速信号线应进行阻抗匹配,以减少反射和信号失真。
2.信号线应采用差分传输方式,以提高抗干扰能力和信号完整性。
七、电磁兼容性设计1.尽量合理布局和组织信号线,以减少电磁干扰和辐射。
2.使用合适的屏蔽措施,包括屏蔽罩、电磁屏蔽层和绕线等。
八、PCB制造和组装1.PCB制造应按照标准工艺进行,确保PCB质量和可靠性。
2.元器件的组装应按照标准操作进行,保证焊接质量。
九、测试和调试1.PCB设计完成后,应进行严格的电路测试和调试,确保其性能和可靠性。
2.测试和调试工具应符合要求,确保测试结果的准确性和可靠性。
以上是一份典型的PCB设计规范,设计师在进行PCB设计时应考虑到电路的复杂性、可靠性和成本等因素,并严格按照规范进行设计和制造,以提高电路板的质量和可靠性。
PCB可制造性设计工艺规范

PCB可制造性设计工艺规范PCB(Printed Circuit Board,印刷电路板)是电子产品中非常常见的一部分。
它是由一种基层材料(通常是玻璃纤维增强复合材料)和通过印刷或压合技术固定在基层上的导电层构成的。
PCB可制造性设计工艺规范是一系列准则和要求,用于确保PCB的设计在生产制造过程中能够达到高质量和可重复性。
首先,对于PCB可制造性设计工艺规范来说,一个重要的方面是布局和布线。
布局指的是元件在PCB上的位置和排列方式,而布线则是指通过导线将元件连接在一起。
在布局方面,应该根据电路的需求和元件的特性进行合理的布局,避免不必要的干扰和噪音。
在布线方面,应该注意导线的长度、走线的宽度和间距,以及阻抗匹配和传输速率等因素。
其次,PCB可制造性设计工艺规范还包括了对于孔的规定。
在PCB制造过程中,通常需要在板上打孔以安装元件。
对于孔的规定,包括孔的类型(如贴片孔、通孔等)、孔的直径和位置等。
这些规定需要考虑到元件的尺寸和安装的要求,以及后续的焊接和连接等操作。
此外,在PCB可制造性设计工艺规范中还包括了对于焊盘和焊接的要求。
焊盘是指用于连接元件和导线的金属圆盘。
对于焊盘的规定,包括焊盘的形状、尺寸和间距等。
而对于焊接的要求,包括焊接的方法、焊点的形状和强度等。
这些规定需要考虑到焊接工艺的可行性和可靠性,以及后续的维修和升级等操作。
最后,PCB可制造性设计工艺规范还应该包括对于阻焊和丝印的要求。
阻焊是一种覆盖在PCB表面的绝缘材料,用于保护导线和焊盘不受外界环境的影响。
对于阻焊的规定,包括阻焊的类型、颜色和厚度等。
丝印则是一种印刷在PCB表面的文字和标记,用于标识元件和线路的位置和功能。
对于丝印的规定,包括丝印的颜色、位置和字体等。
总的来说,PCB可制造性设计工艺规范是为了确保PCB在生产制造过程中能够达到高质量和可重复性而制定的一系列准则和要求。
这些准则和要求涵盖了PCB布局和布线、孔的规定、焊盘和焊接的要求,以及阻焊和丝印等方面。
PCB设计的可制造性原则

PCB设计的可制造性原那么1. 引言在电子产品制造过程中,PCB〔Printed Circuit Board,印制电路板〕的设计是非常关键的一步。
一个好的PCB设计不仅可以提高产品的性能和可靠性,还可以降低制造本钱和生产周期。
为了确保PCB设计的可制造性,设计人员需要遵循一些根本原那么和最正确实践。
本文将介绍一些常用的PCB设计的可制造性原那么。
2. 原那么一:保持布局简单和紧凑在进行PCB设计时,保持布局简单和紧凑是非常重要的原那么。
简单的布局可以降低PCB的复杂性,减少错误的可能性。
紧凑的布局可以缩短信号传输路径,减少电磁干扰,提高信号完整性。
3. 原那么二:考虑耦合和信号完整性PCB上的不同电路和组件之间存在着耦合作用。
在设计PCB时,需要考虑不同信号之间的干扰和交叉耦合。
通过合理的布局和地线规划,可以减少电磁干扰的影响,并提高信号的完整性。
4. 原那么三:合理设置电源和地线电源和地线的布局在PCB设计中扮演着重要的角色。
良好的电源和地线布局可以确保良好的电源分配和地线回流,减少电源噪声和干扰。
在设计中,应尽量将电源和地线别离,并使用适宜的地引脚和电源引脚进行连接。
5. 原那么四:防止过于密集的布线在PCB设计中,过于密集的布线可能导致信号干扰和短路等问题。
因此,应尽量防止过于密集的布线,合理规划和安排信号线和电源线的路径。
同时,应留出足够的空白区域,方便焊接和维修工作。
6. 原那么五:合理选择元件和材料在PCB设计中,选择适宜的元件和材料也是非常重要的。
适宜的元件和材料可以提供更好的性能和可靠性。
应选择具有良好可焊性和耐高温的元件,并防止使用过时或质量不佳的元件和材料。
7. 原那么六:考虑制造和组装过程在PCB设计中,要考虑制造和组装过程。
例如,要确保元件的放置和布线不会影响到焊接和组装的顺利进行。
同时,要尽量减少PCB板的层数和复杂性,以降低制造和组装的本钱。
8. 原那么七:进行设计验证和测试PCB设计完成后,应进行设计验证和测试。
印制电路板(PCB)设计规范

印制电路板(PCB)设计规范版本(V1.0)编制:审核:会签:批准:生效日期:印制电路板(PCB)设计规范(V1.0)1范围本设计规范规定了印制电路板设计中的基本原则和技术要求。
本设计规范适用于盈科电子有限公司的印刷电路板的设计。
2引用文件(本设计规范参考了美的空调事业部的电子设备用印刷电路板的设计。
)下列标准所包含的条文,通过在本标准中引用而构成为本标准的条文。
本标准出版时,所示版本均为有效。
所有标准都会被修订,使用本标准的各方应探讨使用下列标准最新版本的可能性。
GB4706.1-1998 家用和类似用途电器的安全QJ/MK03.025-2003 空调器防火规范参考文件:GB 4588.3-1988印刷电路板设计和使用QJ 3103-1999印刷电路板设计规范(中国航天工业总公司)3定义无。
4基本原则在进行印制板设计时,应考虑本规范所述的四个基本原则。
4.1电气连接的准确性印制板设计时,应使用电原理图所规定的元器件,印制导线的连接关系应与电原理图导线连接关系相一致,印制板和电原理图上元件序号应一一对应。
注:如因结构、电气性能或其它物理性能要求不宜在印制板上布设的导线,应在相应文件(如电原理图上)上做相应修改。
4.2可靠性和安全性印制板电路设计应符合电磁兼容和电器安规的要求。
4.3工艺性印制板电路设计时,应考虑印制板制造工艺和电控装配工艺的要求,尽可能有利于制造、装配和维修,降低焊接不良率。
4.4经济性印制板电路设计在满足使用的安全性和可靠性要求的前提下,应充分考虑其设计方法、选择的基材、制造工艺等,力求经济实用,成本最低。
5技术要求5.1印制板的选用5.1.1印制电路板的层的选择一般情况下,应该选择单面板。
在结构受到限制或其他特殊情况下,经过研发经理的批准,可以选择用双面板设计。
5.1.2 印制电路板的材料和品牌的选择5.1.2.1双面板应采用玻璃纤维板FR-4,单面板应采用半玻纤板CEM-1或纸板,特殊情况下,如果品质可以得到确保,经过研发部长、市场部长、制造部长共同批准,单面板可以使用环氧树脂板FR-1、FR-2。
PCB可制造性设计规范

PCB可制造性设计规范PCB (Printed Circuit Board)的制造性设计规范是指在设计和布局PCB电路板时所需考虑的一系列规范和标准,以确保电路板的制造过程顺利进行并获得可靠性和性能。
一、尺寸规范1.PCB电路板的尺寸要符合制造商的要求,包括最小尺寸、最大尺寸和板上零部件之间的间距。
2.确保电路板的边缘清晰、平整,并防止零部件或钳具与电路板边缘重叠。
二、层规范1.根据设计要求确定所需的层次和层的数量,确保原理图和布局文件的一致性。
2.定义PCB的地平面层、电源层、信号层和垫层、焊盘层等的位置和规格。
三、元件布局规范1. 合理布局元件,以最小化路径长度和EMI (Electromagnetic Interference),提高电路的可靠性和性能。
2.避免元件之间的相互干扰和干涉,确保元件之间有足够的间距,以便于焊接工序和维修。
四、接线规范1.线路走向应简洁、直接,避免交叉和环形走线。
2.确保信号和电源线路之间的隔离,并使用正确的引脚布局和接线技术。
五、电路可靠性规范1.选择适当的层次和厚度,以确保足够强度和刚度。
2.确保电路板表面和感应部件光滑,以防止划伤和损坏。
六、焊接规范1.在设计中使用标准的焊盘尺寸和间距,以方便后续的手工或自动焊接。
2.制定适当的焊盘和焊缺陷防范措施,以最小化焊接问题的发生。
七、标准规范1. 遵循IPC (Institute for Interconnecting and Packaging Electronic Circuits)标准,以确保PCB的制造符合国际标准。
2.正确标注和命名电路板上的元件和信号,以方便生产和测试。
八、生产文件和图纸规范1.提供准确和详细的生产文件和图纸,包括层叠图、金属化孔、引线表和拼图图等。
2.确保文件和图纸的易读性和可修改性。
九、封装规范1.选择适当的封装类型和尺寸,以满足电路板的要求。
2.避免使用不常见或过于复杂的封装,以确保可靠的元件焊接和连接。
PCB印刷电路板设计规范
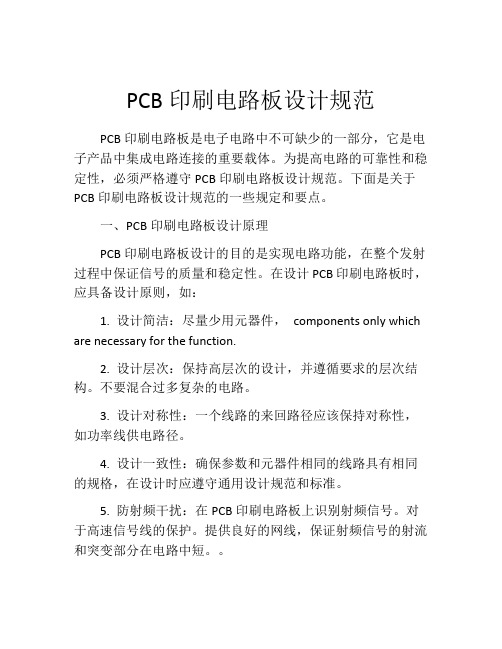
PCB印刷电路板设计规范PCB印刷电路板是电子电路中不可缺少的一部分,它是电子产品中集成电路连接的重要载体。
为提高电路的可靠性和稳定性,必须严格遵守PCB印刷电路板设计规范。
下面是关于PCB印刷电路板设计规范的一些规定和要点。
一、PCB印刷电路板设计原理PCB印刷电路板设计的目的是实现电路功能,在整个发射过程中保证信号的质量和稳定性。
在设计PCB印刷电路板时,应具备设计原则,如:1. 设计简洁:尽量少用元器件,components only which are necessary for the function.2. 设计层次:保持高层次的设计,并遵循要求的层次结构。
不要混合过多复杂的电路。
3. 设计对称性:一个线路的来回路径应该保持对称性,如功率线供电路径。
4. 设计一致性:确保参数和元器件相同的线路具有相同的规格,在设计时应遵守通用设计规范和标准。
5. 防射频干扰:在PCB印刷电路板上识别射频信号。
对于高速信号线的保护。
提供良好的网线,保证射频信号的射流和突变部分在电路中短。
6. 防静电:需要注意PCB印刷电路板的静电防护,以防止电路受到静电干扰。
需要添加适当的静电保护元器件。
7. 适当绝缘:在电路设计中,需要考虑线路之间的绝缘,以避免短路、干扰和其他负面影响。
二、PCB印刷电路板设计规范:1. 设计电路结构设计PCB印刷电路板时应注意电路结构。
电路结构应当与电路损耗降低、电路反射、电路跟踪、回路抗干扰等因素进行考虑。
在设计电路时,应遵循最短电路路径、最大电路距离和最好射穴连接的原则。
2. 选择元器件在设计PCB印刷电路板时,需要选择适当的元器件。
当选择元件时,应考虑到电路功耗、电路稳定性和使用寿命,以保证元件的正确性。
元器件的数量应尽可能少,选择元件的大小、功率和频率等也应考虑到电源供电的稳定性、输入输出容量、适应性等因素,以减少规格复杂度和设备出错的风险。
3. 设置型号标识在设计PCB印刷电路板时,应将每个元件和每条线路标记。
- 1、下载文档前请自行甄别文档内容的完整性,平台不提供额外的编辑、内容补充、找答案等附加服务。
- 2、"仅部分预览"的文档,不可在线预览部分如存在完整性等问题,可反馈申请退款(可完整预览的文档不适用该条件!)。
- 3、如文档侵犯您的权益,请联系客服反馈,我们会尽快为您处理(人工客服工作时间:9:00-18:30)。
1范围1.1主题内容本标准规定了电子产品中印制电路板设计时应遵循的基本要求。
1.2适用范围本标准适用于以环氧玻璃布层压板为基板的表面组装印制板设计,采用其它材料为基板的设计也可参照使用。
2引用标准GB 2036-94 印制电路术语GB 3375-82 焊接名词术语SJ/T 10668-1995 表面组装技术术语SJ/T 10669-1995 表面组装元器件可焊性试验Q/DG 72-2002 PCB设计规范3定义3.1术语本标准采用GB 3375、GB2036、SJ/T 10668定义的术语。
3.2缩写词a. SMC/SMD(Surface mounted components/ Surface mounted devices):表面组装元器件;b. SMT(Surface mounted technology):表面组装技术;c. SOP(Small outline package):小外形封装,两侧具有翼形或J形短引线的一种表面组装元器件封装形式;d. SOT(Small outline transistor):小外形晶体管;e. PLCC(Plasti c leaded chip carrier):塑封有引线芯片载体,四边具有J形短引线,典型引线间距为1.27mm,采用塑料封装的芯片载体,外形有正方和矩形两种形式f.;QFP(Quad flat package):四边扁平封装,四边具有翼形短引线,引线间距为1.00mm,0.80mm,0.65mm,0.50mm,0.30mm等;g. DIP (Dual in-line package):双列直插式封装h.;BQFP (QFP with buffer):带缓冲垫封装的Q FP;i. PCB (Printed circuit board):印制板。
J.BGA(Ball Grid Array):球形栅格列阵4一般要求4.1印制电路板的尺寸厚度4.1.1印制板最小尺寸L×W为80mm×70mm,最大尺寸L×W为457mm×407mm4.1.2印制板厚度一般为0.8~2.0mm。
4.2印制电路板的外形要求对于波峰焊,要求外形应该是矩形的,如果有缺槽,应考虑用工艺拼板的方式将缺槽补齐;对于纯SMT板,允许有缺槽,但缺槽尺寸应小于所在边长度的1/3,以确保PCB在链条上传送平稳.(如图1所示)图1 PCB板的外形要求4.3印制电路板的工艺边要求在PCB布局时要留出3~5mm的工艺边,所谓工艺边,就是为PCB组装时便于设备传送、夹持。
在这个范围内不允许布放元器件焊盘(整机连线用焊盘除外)但可走线。
如果印制线路板上元器件过多,不得已要超出3mm范围时,可以在板的边缘加上3mm的辅边,辅边开V形槽,在生产后用手掰断即可。
4.4印制电路板的MARK点的设计要求基准点是供自动化设备做自动对位用的,视觉系统的基准点类型有几种,最佳的基准点标记是实心圆,基准点标记直径一般设置为1mm,按精度需求可采用PCB板基准点和局部基准点,PCB基准点用于整个PCB光学定位,局部基准点用于引脚数量多、间距小的单个器件。
推荐的MARK点如图2所示:图2 MARK点的设计形状实心圆尺寸d=1.0mm+/-0.025mm;无阻焊保护区D=3.0mm;基材:良好的对比度;无氧化;无阻焊剂;平整度<0.015 mm。
使用3+1 Fiducial Marks,Mark点中心距离板边缘5mm双面都有贴片元件,则每一面都应有Mark点.局部Mark点建议采用二个。
Mark点可以是裸铜、由清澈的防氧化涂层保护的裸铜、镀镍或镀锡、或焊锡涂层(热风均匀的)4.5印制电路板坐标原点的要求为了和贴片机的GEB文件相对应,减少相对误差,建议以左下角的全局MARK点作为PCB 设计时的坐标原点尽量使用现有的环氧布层压板FR-4,且保证热风整平均匀。
4.7元器件的选择4.7.1无源元件应优选矩形片状封装。
4.7.2片状电阻和电容优选1206封装。
4.7.3钽电容器优选模压塑料封装。
4.7.4通用表面组装二极管和三极管优选高外形的SOT23,且尽量用标准的表贴二极管。
4.7.5有源器件优选具有J型或鸥翼形引脚的器件。
4.7.6QFP优选带缓冲垫封装(BQFP),且0.3mm的QFP尽量的用BGA来代替。
4.7.7SOP、PLCC、QFP的引脚应有良好的共面性,其最高引脚的脚底与最低三条引脚的脚底形成的平面之间的垂直距离要求不大于0.1mm,特殊情况下可放宽到与引脚厚度相同。
4.7.8元器件应能耐受的焊接条件是:再流焊时为230℃、20s,波峰焊时260℃、10s。
4.7.9慎重选用圆柱形的电阻、电容和二极管;4.7.10所有元器件的可焊性应符合SJ/T10669中的要求。
4.8印制电路安装孔的设计要求,为了确保波峰焊时熔融的焊锡不会堵塞安装孔,定位孔、非接地安装孔,除了功能必须要求金属化的孔外,一般均应设计成非金属化孔。
4.9表面组装元器件的焊盘图形设计原则a.表面组装焊盘尺寸应与所用元器件的外形、焊端、引脚等尺寸相匹配;b.有源器件的焊盘图形优选长圆形焊盘;c.同一元器件相邻焊盘之间的中心距应等于相邻引线的中心距;d.对称引脚的焊盘,设计时应严格保持其对称性。
e.SMD器件的引脚与大面积筒箔连接时,要进行热隔离处理(如图3)。
图3 热隔离带的设计4.10印制电路金属化、安装孔孔以及插装元器件焊盘的尺寸设计依照电子工程研究所标准Q/DG 72-2002来执行。
对于长边尺寸小于50mm 、或短边小于50 mm 、或尺寸范围小于125×100mm 的PCB ,宜采用拼板的方式,转换为符合生产要求的理想尺寸,以便于组装。
拼板连接时主要考虑的是拼板分离后边缘是否整齐;分离是否方便,在经插装工序时是否有足够的刚度拼板的连接方式主要有双面对刻V 形槽、长槽孔加圆孔、长槽孔三种,如图4所示:图4 拼版的布局设计5 详细要求5.1 各种不同元器件的焊盘图形设计5.1.1 无源元器件的焊盘图形设计 5.1.1.1矩形元件的焊盘图形设计电阻和电容的外形及焊盘图形见图5。
焊盘宽度按式(1)、电阻焊盘长度按式(2)、电容焊盘长度按式(3)、焊盘间距按式(4)计算。
K W A -max = (1)K T H B ++max max (电阻)= (2)K T H B -+m i n m a x 0=(电容 (3)K T L G --=max max 2 (4)式中:A −− 为焊盘宽度,mm (mil );B −− 为焊盘长度,mm (mil ); G −− 为焊盘间距,mm (mil ); W max −− 为元件最大宽度,mm (mil ); H max −− 为元件最大高度,mm (mil ); T max −− 为元件端焊头最大宽度,mm (mil ); T min −− 为元件端焊头最小宽度,mm (mil ); L max −− 为元件最大长度,mm (mil ); K =0.25mm (10mil)。
表2 片状电容的焊盘尺寸mm5.1.1.2模压塑封钽电容器的焊盘设计钽电容器的外形及焊盘图形见图6。
焊盘宽度按式(5)、焊盘长度按式(6)、焊盘间距按式(7)计算。
KA-W= (5)max+= (6)B-HKTmaxmin=2 (7)G--LKTmaxmax式中:A −−为焊盘宽度,mm(mil);B −−为焊盘长度,mm(mil);G −−为焊盘间距,mm(mil);W max−−为元件最大宽度,mm(mil);H max−−为元件最大高度(指焊端高度),mm(mil);T min−−为元件端焊头最小宽度,mm(mil);L max−−为元件最大长度,mm(mil);T max−−为元件端焊头最大宽度,mm(mil);K=0.25mm (10mil)。
常用模压塑封钽电容器的焊盘尺寸列入表3。
表3 模压塑封钽电容器的焊盘尺寸mm(mil)5.1.1.3圆柱形元器件的焊盘设计焊盘图形为长方形。
采用再流焊时,还必须设计有凹形槽(见图7),其宽度一般为0.3 0.05mm。
如果焊前采用胶粘剂固定元器件,则不必设计凹槽。
常用圆柱形元器件的焊盘宽度、焊盘长度、焊盘间距及凹形槽长度列入表4。
表4 圆柱形表面组装元器件的焊盘尺寸mm(mil)图7 圆柱形表面组装元器件的焊盘图形5.1.2有源器件的焊盘图形设计5.1.2.1一般原则a.焊盘宽度和焊盘间距尺寸的设计焊盘宽度与焊盘间距的尺寸之比分为Ⅰ、Ⅱ、Ⅲ三种系列,即把器件的引脚中心距分别按系列I为7:3、系列Ⅱ为6:4、系列Ⅲ为5:5不同的比例进行分割,优选系列Ⅱ。
当引脚中心距为1.27mm时,三种比例的焊盘宽度和焊盘间距见表5。
优选系列Ⅱ时,不同的引脚中心距对应的焊盘宽度和焊盘间距尺寸按表6选取表5 1.27mm引脚中心距器件焊盘宽度和焊盘间距系列b. 焊盘长度一般为器件可焊引脚长度2.5~3倍,推荐3倍。
5.1.2.2晶体管焊盘图形设计焊盘的中心距离等于器件引线间的中心距离,焊盘尺寸在可焊端四周延伸0.38mm (15mil )。
常用的SOT23、SOT89、SOT143焊盘图形见图8、 图9、图10。
图8 SOT23焊盘示意图(单位mm )5.1.2.3SOP 式中:D −− F −− K =图11 SOP 外形及焊盘示意图5.1.2.4SOJ 器件焊盘图形设计焊盘宽度为0.76mm ,焊盘间距为0.51mm ,焊盘长度为2mm 。
两排焊盘内侧间距应保证引脚外侧部分的焊盘长度为整个焊盘长度的2/3。
焊盘与引脚的相对位置见图12。
5.1.2.5PLCC器件焊盘图形的设计PLCC的外形及焊盘形状见图13,焊盘宽度一般为0.76mm,焊盘间距为0.51mm,焊盘长度为2mm,相对焊盘外侧间距的计算按式(9)、(10)。
=1 (9)A+CK=2 (10)B+CK式中:A−−横向焊盘外侧间距,mm(mil);B−−纵向焊盘外侧间距,mm(mil);C1/C2−−器件的宽(含引脚),mm(mil);K=0.76mm(30mil)图13 PLCC外形及焊盘示意图5.1.2.6 5.1.2.6BGA等球状栅格列阵元器件的焊盘设计原则a.PCB上的每个焊球的中心与BGA底部相对应的焊球中心相吻合;b.PCB焊盘图形为实心圆,导通孔不能加工在焊盘上;c.与焊盘连接的导线宽度要一致,一般为0.15mm~0.2mm;d.阻焊尺寸比焊盘尺寸大0.1mm~0.15mm;e.导通孔在孔化电镀后,必须采用介质材料或导电胶进行堵塞,高度不得超过焊盘高度;f.在BGA器件外廓四角加工丝网图形,丝网图形的线宽为0.2mm~0.25mm。