1 轮毂轴承性能试验大纲
【精编范文】轴承检验指导书-推荐word版 (8页)

本文部分内容来自网络整理,本司不为其真实性负责,如有异议或侵权请及时联系,本司将立即删除!== 本文为word格式,下载后可方便编辑和修改! ==轴承检验指导书篇一:轴承外径检测操作作业指导书1.0目的:确保操作人员能正确的使用测量仪,并保证检测结果的准确性及真实性。
2.0范围:适用于本公司所有轴承产品的检测。
3.0定义:用来检测轴承产品的变化量。
4.0程序:4.1 使用前检测轴仪的外观、测点位置、清洁和磨损程度及测点的灵活性和检测轴仪上所使用的量表是否能正常工作。
4.1.1用相应的标准件校准轴仪:将标准件轻轻放在检测台上,使标准件紧靠辅助撑点,将检测的量表放在相应的检测位置上,按顺时针方向轻轻转动标准件,使量表能够检测到标准件所标定的位置,然后调整轴仪上的微调螺母将量表调到与标准件所指定的对应的数值上。
4.1.2测量:将需要检测的产品按照 4.1.1的方法放上,然后顺时针方向旋转,读出量表的最大值和最小值。
4.1.3结果:将所测定数据与工艺卡上的数据进行比对,方行合格的产品,根据不良品处理流程处理不良品。
5.0 操作工:负责按照以上的操作流程使用轴仪,检测所需要的项目并负责该量具的日常维护。
5.1.1 计量员:负责该量具的计量管理。
6.0参照轴仪的使用说明书。
篇二:轴承装配作业指导书装配作业指导书装配钳工的定义:把零件按机械设备的装配技术要求进行组件,部件装配和总装配,并经过调整,检验和试车等,使之成为合格的机械设备。
操作机械设备或使用工装、工具,进行机械设备零件、组建或成品组合装配与调试的人员。
1.基本要求1.1 必须按照设计、工艺要求及本规定和有关标准进行装配。
1.2 所有零部件(包括外购、外协件)必须为检验合格的方能进行装配。
1.4 零件在装配前必须清理和清洗干净,不得有毛刺、飞边、氧化皮、锈蚀、切屑、砂粒、灰尘和油污等,并应符合相应清洁度要求。
1.5 装配过程中零件不得磕碰、划伤和锈蚀。
轮毂轴承
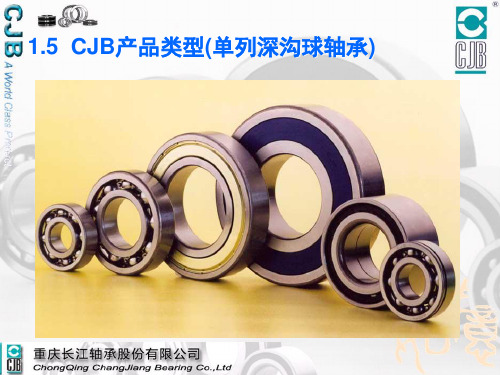
往返疲劳强度破 坏试验
刚性检测试验
3.5 轮毂轴承材料选取
轴承套圈、钢球材料的选取: 轴承套圈、钢球材料的选取: 轴承套圈、钢球均采用国内最好的GCr15 GCr15钢 相当于日本SUJ2 轴承套圈、钢球均采用国内最好的GCr15钢(相当于日本SUJ2 轮毂单元带法兰盘内、 钢),轮毂单元带法兰盘内、外圈采用机械性能优良的中碳钢 所有材料均采用长江轴承专用定制高性能轴承 或中碳合金钢,所有材料均采用长江轴承专用定制高性能轴承 材料。 材料。
2 0.7 2/3 1.8
3.3 轮毂球轴承设计开发流程 轴承模拟受力核算) (轴承模拟受力核算)
根据车身参数,核算轮胎部位受力情况。 根据车身参数,核算轮胎部位受力情况。
前(后)轴满载负荷: 轴满载负荷: G 轮距: 前(后)轮距:B 车辆满载重心高: 车辆满载重心高:hg 轮胎半径: 前(后)轮胎半径:R 轮胎偏心: 轮胎偏心:δ 车辆向心加速度: 车辆向心加速度:ψ 轮胎部位径向支承力: 轮胎部位径向支承力: Wr 轮胎部位轴向支承力: 轮胎部位轴向支承力: Wf Wr=G(0.5 =G(0.5± Wr=G(0.5±ψhg/B) Wf= Wr Wf=ψWr
CJB 为 SGM, SGMW传动与底盘系统供应轴承 供 传动与底盘系统供应轴承, 传动与底盘系统供应轴承 应商代码是 SGMW-118,传动系统轴承主要用于 传动系统轴承主要用于 D14,D16,D18,D20, F15项目 底盘系统轴承主要用于以 项目,底盘系统轴承主要用于以 项目 下车型 :
名称 SGMW 产品 轮毂轴承单元 车型 N1 SOP 日期 2004.12.01 供应数量 565000
Pm=[(P13n1t1+P23n2t2+…)/(n1t1+n2t2+…)]1/3
轮毂单元轴承座弯曲疲劳寿命测试规范

Q/WQZ165-2000 轮毂单元轴承座弯曲疲劳寿命测试规范1.0 范围本标准适用于轮毂单元轴承座弯曲疲劳寿命测试,允许在较大的弯曲载荷的作用下测定轴承座的弯曲疲劳寿命。
2.0 引用标准STI—13 德尔福轮毂轴承单元轴承座弯曲疲劳寿命测试3.0 测试规范3.1记录形式所有试验数据都要记录在《轮毂单元轴承座弯曲疲劳寿命试验记录单》上。
3.2设备要求试验设备应满足各试验参数的要求,且符合试验方法的要求。
3.2.1保持输入负荷不超过5%。
3.2.2保证轴向载荷频率在5—15赫兹。
3.2.3所有的控制元件应校准,且在规定的到期时间内。
3.3试验轴承样品3.3.1试验轴承单元应是经检测符合图纸要求的合格品,每一批次随机抽样八套,其中六套作为试验样品,另两套备用。
3.3.2在样品的非基准面上逐套编号,批与批,套与套不得重号或缺号,每种轴承编号的位置应一致。
3.3.3在试验前需对样品进行裂纹检查。
(推荐采用磁粉探伤)3.4试验方法3.4.1定义Q/WQZ165-2000径向负荷是一垂直于轴承旋转轴线且作用于车轮中心线的一恒力。
轴向负荷是一平行于试验轴承旋转轴线的一周期性循环力。
它与旋转轴线的距离等于轮毂的旋转半径。
所有的轴承均做失效。
3.4.2安装:3.4.2.1 将轮毂单元和各连接件及试验机接头擦试干净。
3.4.2.2 将连接板与机座连接好。
3.4.2.3将单元用规定的螺栓及力矩拧紧。
3.4.2.4 将轴承座与连接板按规定的要求连接好。
3.4.2.5 安装好径向加力臂。
3.4.2.6 安装好轴向加力臂。
3.4.3.1试验3.4.3.2将轴向载荷的循环频率设置为5赫兹。
3.4.3.3 记录试验开始的时间。
3.4.3.4 所有的轴承单元均做失效。
3.4.3.5 按此方法试验,其B10(最小)=250000次循环,B50(最小)=350000次循环。
3.4.3.6记录结束时间及所有相关数据。
Q/WQZ165-2000 3.4.3.7 记录轴承座失效形式。
轿车轮毂轴承耐久性试验载荷谱设计

轿车轮毂轴承耐久性试验载荷谱设计黎桂华1,2,李兴林3,鄢建辉3(1.华南理工大学 机械工程学院,广东 广州 510640;2.韶关东南轴承有限公司,广东 韶关 512029;3.杭州轴承试验研究中心,浙江 杭州 310022)摘要:为了满足加速寿命试验准则和有效缩短台架试验的时间,提出了通过改变侧向加速度的使用率,在保持侧向加速度最大值不变的前提下,设计轿车轮毂轴承耐久性试验载荷谱的思路。
关键词:滚动轴承;轿车轮毂轴承;耐久性试验;载荷谱中图分类号:TH133.33;TP80611 文献标识码:B 文章编号:1000-3762(2006)01-0027-02符号说明g重力加速度,9.81m/s2a g侧向加速度(转弯加速度,汽车右转弯为正值),m/s2H车辆重心(质心)对地面的高度,mmT轮距,mmW满载后前轴或后轴载重,kgR s轮胎半径,mmf w载荷系数F y作用于轮胎的轴向载荷(轴向的路面反作用力),NF z作用于轮胎的径向载荷(径向的路面反作用力),NP i侧向加速度的使用率,%C轮毂轴承的基本额定(径向)动载荷,N P m轮毂轴承所受的当量载荷,N下标r表示径向L表示左(轮)R表示右(轮)特定应用场合下的轴承寿命常常是通过专门试验来确定的,这种试验也称为台架试验(BE NCH TEST)或耐久性试验,它模拟实际应用场合的主要工作参数,使加速试验达到逼真的效果。
SK F 开发了一种A字形试验机,专门用于汽车轮毂轴承试验。
该试验机使用实际轿车装置系统,模拟轮毂的环境条件。
轿车轮毂轴承的耐久性试验模仿真实工况周期性地施加动态循环载荷,该载荷收稿日期:2005-08-01;修回日期:2005-09-10等效于轿车轮胎的径向、轴向载荷,综合考核轮毂轴承的设计、材料、工艺、热处理等,最终完成轮毂轴承的疲劳寿命的评定。
1 加速寿命试验的准则加速寿命试验是指在超过正常使用条件下的寿命试验。
在典型的应用场合,滚动接触表面发生初始疲劳剥落的时间大约为10~15年。
汽车轮毂试验的三个标准和分析过程

汽车轮毂试验的三个标准和分析过程一有关汽车轮毂的三个试验标准根据国内和国际标准化组织(ISO) 的规定,汽车轮毂必须满足三个典型试验的要求。
有关的国内标准与ISO 的标准是一致的,国外不同国家的标准可能不完全一样,但是基本方面还是一致的,只是具体载荷大小有所差别。
在国内,这三个试验对应的标准分别是:1. 车轮动态弯曲疲劳和径向疲劳试验方法- QCT221其中包含了动态弯曲和径向载荷两个疲劳试验标准。
2. 车轮冲击试验方法- GBT15704其中包含了轮毂冲击试验的标准。
下面简单介绍这三个试验标准。
标准1:汽车轻合金车轮的性能要求和试验方法QC/T221—1997前言本标准是根据1995 年标准制修订计划安排组织制定的。
本标准在制订过程中,参照采用了美国SFI、日本JASO 等有关标准。
本标准由机械工业部汽车工业司提出。
本标准由全国汽车标准化技术委员会归口。
本标准由广东南海中南铝合金轮毂有限公司负责起草、立中车轮制造有限公司参加起草。
本标准主要起草人:雷铭君。
1 范围本标准规定了汽车轻合金车轮的动态弯曲疲劳性能、动态径向疲劳性能要求及试验方法。
本标准适用于全部或部分轻合金制造的汽车车轮。
2 试验项目2.1 动态弯曲疲劳试验;2.2 动态径向疲劳试验。
3 试验样品弯曲疲劳和径向疲劳试验用的车轮应是未经试验或未使用过的新成品车轮,每个车轮只能做一次试验。
4 动态弯曲疲劳试验4.1 试验设备试验台应有一个旋转装置,车轮可在一固定不变的弯矩作用下旋转,或是车轮静止不动,而承受一个旋转弯曲力矩作用(见图1)4.2 试验程序4.2.1 准备工作根据车轮在车辆上安装的实际情况,按规定的扭矩最低值的115%,将车轮紧固在试验装置的支承面上,螺母不允许加润滑剂。
调整车轮位置后,将轮辋的轮缘夹紧到试验夹具上。
试验的连接件和车轮的配合面应去除多余的堆聚物、灰尘或杂质。
车轮的螺栓和螺母在试验过程中可再次紧固。
加载系统应保持规定的载荷,误差不超过±2.5%。
轮毂轴承质量检验基本常识

轮毂轴承质量检验基本常识前言轮毂轴承是汽车非常重要的零部件之一,它与汽车维护、安全密切相关。
检验好车轮轴承的质量,能对车辆的安全保障和维修方案提供参考依据。
本文将介绍轮毂轴承质量检验的基本常识。
检验工具和方法在检验前需要做好相关准备,包括检验所需工具和检验方法。
轮毂轴承检验工具包括:刻度尺、量规、卡尺、测试仪器、拉力计等。
检验方法主要有目测、手摸、听声、测量等。
在检验前可以先进行目测检查,查看轴承是否有明显的损坏,如裂纹、凹痕、断裂等。
接下来进行手摸检查,轻轻摇动轮毂,检查轮毂是否有松动、轻重不等等现象。
之后使用测试仪器和测量工具对轴承的外径大小、内径大小、宽度大小、轴承孔圆度、轮毂孔同心度、轴承间隙等参数进行测量,从而得出轮毂轴承质量合格与否的。
常见轮毂轴承质量问题以下是常见的轮毂轴承质量问题:1.外观问题:轮毂表面有划痕、铁锈、氧化、变形、变色等。
2.尺寸问题:尺寸大小不符合标准要求,如内径、外径、宽度等问题。
3.轴承间隙:间隙过大、过小都会影响轮毂轴承运转,从而影响车辆安全性。
4.齿轮问题:齿面严重磨损、减速比失调、其他齿轮问题等。
在检验轮毂轴承时,需要注意这些常见问题,保证检验结果准确性。
轮毂轴承质量判定标准轮毂轴承的合格标准主要分为以下几个方面:1.轴承尺寸:内径、外径、宽度等方面需要符合标准要求。
2.轴承间隙:间隙大小必须符合标准规定。
3.轮毂圆度:轮毂的圆度必须达到一定的标准。
4.强度、硬度标准:强度、硬度必须符合标准规定。
在检验时通过测量轮毂轴承的各项参数,判断是否符合合格标准,从而判定轮毂轴承的质量。
轮毂轴承是汽车重要的零部件之一,质量的好坏影响着车辆的维护和安全性能。
本文介绍了轮毂轴承质量检验的基本常识,包括检验工具和方法、常见问题以及质量判定标准,希望能够帮助大家更好地了解轮毂轴承质量检验。
轮辋性能测试实验报告(3篇)

第1篇一、实验目的1. 了解轮辋的基本结构及工作原理;2. 研究轮辋在不同工况下的力学性能;3. 评估轮辋在实际应用中的可靠性和安全性;4. 为轮辋的设计与制造提供实验依据。
二、实验原理轮辋是连接轮胎与车轴的重要部件,其性能直接影响到车辆的行驶安全。
本实验通过模拟实际工况,对轮辋进行力学性能测试,包括拉伸、弯曲、扭转等试验,以评估轮辋的力学性能。
三、实验材料与设备1. 实验材料:某品牌轮辋样品;2. 实验设备:万能试验机、测力传感器、千分尺、卡尺等。
四、实验方法与步骤1. 样品准备:选取具有代表性的轮辋样品,对其表面进行打磨、清洗,确保样品表面平整、无损伤;2. 样品尺寸测量:使用千分尺和卡尺测量轮辋样品的直径、宽度、厚度等尺寸参数;3. 拉伸试验:将轮辋样品固定在万能试验机上,进行拉伸试验,记录最大拉伸载荷和断裂伸长率;4. 弯曲试验:将轮辋样品固定在万能试验机上,进行弯曲试验,记录最大弯曲载荷和弯曲角度;5. 扭转试验:将轮辋样品固定在万能试验机上,进行扭转试验,记录最大扭转载荷和扭转角度;6. 数据处理与分析:对实验数据进行统计分析,得出轮辋在不同工况下的力学性能指标。
五、实验结果与分析1. 拉伸试验结果:轮辋样品的最大拉伸载荷为XXX N,断裂伸长率为XXX %。
结果表明,该轮辋具有良好的抗拉伸性能,满足实际应用需求;2. 弯曲试验结果:轮辋样品的最大弯曲载荷为XXX N,弯曲角度为XXX °。
结果表明,该轮辋具有良好的抗弯曲性能,能够承受一定的弯曲载荷;3. 扭转试验结果:轮辋样品的最大扭转载荷为XXX N,扭转角度为XXX °。
结果表明,该轮辋具有良好的抗扭转性能,能够承受一定的扭转载荷。
六、实验结论1. 通过本实验,验证了该轮辋具有良好的抗拉伸、抗弯曲和抗扭转性能,满足实际应用需求;2. 实验结果为轮辋的设计与制造提供了实验依据,有助于提高轮辋的可靠性和安全性;3. 建议在轮辋设计和制造过程中,充分考虑实际工况,优化轮辋结构,提高轮辋性能。
【精品】轮毂轴承质量检验基本常识

轮毂轴承质量检验基本常识轮毂轴承质量检验基本常识中图分类号:U260.331+.2文献标识码: A 文章编号:一轴承的结构轴承由于用途和工作条件不同,其结构变化甚多。
轮滚单元也是轴承的一种,但其基本结构是由4个零件组成:(1)内圈,(2)外圈,(3)滚动体(钢球或滚子),(4)保持架。
第一代轮毂单元:由双列圆锥滚子轴承或双列滚珠轴承组成。
第二代轮毂单元:外圈带法兰盘的双列圆锥滚子轴承,外圈带法蓝盘的双列角接触滚珠轴承。
第二代半轮毂单元:在第二代的基础上外加芯轴。
第三代轮毂单元:内外圈带法蓝盘的双列圆锥滚子轴承,内外圈带法兰盘的双列角接触滚珠轴承(带芯轴)。
二常用量具型号及使用方法游标卡尺游标卡尺的分类:有0.01、0.02、0.05和0.10的分度值,测量范围的上限至2000mm。
使用应注意的事项:A、测量工件时应按测量工件的尺寸的大小及精度要求来选用游标卡尺。
B、测量前应检查尺身游标刻线对齐情况,以免产生读数误差。
游标卡尺读数原理:利用游标卡尺的游标刻线间距与主尺刻线间差形成游标分度值。
测量时,在主尺上读取毫米数,在游标上读取小数值。
千分尺千分尺的分类:分度值为0.01mm,测量范围至500mm 的外径千分尺。
千分尺读数原理:利用等进螺旋原理将丝杆的角度旋转运动转变为测杆的直线位移。
读数方法:A、在固定套筒上读出毫米数或半毫米数。
B、看微分筒上哪一格与固定套筒上基准线对齐。
C、两次读数加起来。
使用应注意事项:千分尺的测量面应干净。
测量时先转微分筒,测量面接触前改用棘轮,直到发出咯咯声为止。
每把千分尺都有它的测量范围,按被测件的大小来选用。
但不能用它去测毛坯,更不能在工件旋转时去测量。
指示表(百分表和千分表)百分表的分度值为0.01,测量范围为0-3、0-5、0-10mm。
千分表的分度值为0.001,测量范围为0-1、0-2、0-3、0-5mm。
指示表是利用齿轮或杠杆齿轮传动,将测杆的直线位移变为指针的角位移的计量器具。
- 1、下载文档前请自行甄别文档内容的完整性,平台不提供额外的编辑、内容补充、找答案等附加服务。
- 2、"仅部分预览"的文档,不可在线预览部分如存在完整性等问题,可反馈申请退款(可完整预览的文档不适用该条件!)。
- 3、如文档侵犯您的权益,请联系客服反馈,我们会尽快为您处理(人工客服工作时间:9:00-18:30)。
车型零部件性能试验
试验大纲
产品名称:轮毂轴承
产品图号:
试验类型:性能检验
试验日期:
编制:审核:批准:
1.试验依据:
乘用车及商务车轮毂轴承技术标准
2.试验目的:
验证产品的性能是否满足要求。
3.试验对象:
轮毂轴承。
4.要求:
负荷试验机的压力不小于10KN,室温在20±1℃。
5.试验方法
5.1密封泥水试验
5.1.1定义:泥水试验是使轴承在泥浆水喷溅的条件下,用轴承寿命来描述轴承防泥水能力的试验。
5.1.2试验准备
5.1.2.1样本容量:2套,抽样4套,其中2套为备品及分析用
5.1.2.2样品套圈的端面上逐套编号
5.1.2.3样品在各项测试前应擦试干净,不得有油污
5.1.2.4称质量采用的天平精度应不低于6级,并定期鉴定.
5.1.2.5轴承在上机试验前称其质量
5.1.2.6与轴承配合的轴与壳体的公差应符合要求
5.1.2.7试验轴承必须安装正确,不得有压偏现象,不准敲打密封圈
5.1.3试验条件
5.1.3.1试验机为通过鉴定合格的轴承试验机
5.1.3.2试验条件:
泥水应符合:JISZ8901 8级,重量比为5%;流量:1×103m3/min
转速:N=300rpm时,向密封件喷溅试验1小时
N=1000rpm时,不喷溅试验1小时
目标时间:100小时
5.1.4试验过程
5.1.4.1凡因设备仪器故障或操作人员违反试验规程造成轴承失效时,应从记录中剔除
5.1.4.2试验轴承出现异常振动、噪声及其它异常现象时,应及时停机处理
5.1.4.3试验在载荷下起动和停机
5.2漏脂试验
5.2.1定义:漏脂试验是轴承在一定条件下运转,用轴承腔内润滑脂泄漏到轴承外部的情况来描述其防漏脂能力的试验。
5.2.2试验准备
5.2.2.1样本容量:4套,抽样数量6套,其中2套为备品及分析用。
5.2.2.2样品套圈的端面上逐套编号
5.2.2.3样品在各项测试前应擦试干净,不得有油污
5.2.2.4称质量采用的天平精度应不低于6级,并定期鉴定.
5.2.2.5轴承在上机试验前称其质量
5.2.2.6与轴承配合的轴与壳体的公差应符合要求
5.2.2.7试验轴承必须安装正确,不得有压偏现象,不准敲打密封圈
5.2.3试验条件
5.2.3.1试验机为通过鉴定合格的密封轴承试验机
5.2.3.2试验条件:
试验转速:900转/分
环境温度: 10~30ºC
试验径向载荷:1500N
试验时间:48小时
螺母扭紧力:200Nm~260Nm
5.2.4试验过程
5.2.4.1开始每30分钟记录一次轴承温度及环境温度,待温度稳定后,每一小时记录一次.
5.2.4.2凡因设备仪器故障或操作人员违反试验规程造成轴承失效时,应从记录中剔除
5.2.4.3试验轴承出现异常振动、噪声及其它异常现象时,应及时停机处理
5.2.4.4试验在载荷下起动和停机
5.3强化试验
5.3.1 本试验大纲制定参考STI-03C标准改动而成的。
5.3.2在表1所示条件下试验,评价噪音、裂纹,滚道表面剥落和压痕。
在评价标准不能被满足之前,做试验是为了掌握极限的性能。
(试验样本轴承数量为6套,并4套需做到失效为止)
25小时轴承未损坏75个小时可以停止试验。
(部分车型参数:车重: 2600Kg ;前轴重:1350Kg;)
5.3.3测试规范
a)保持输入负荷误差不超过5%。
保证循环时间误差不超过3%。
测量和记录轴承单元在HUB非配合外径表面的温度。
控制试验轴承单元试验时的振动值。
保证转速误差不超过2%。
保证载荷、电流、试验温度、振动值超标时能自动停机。
所有的控制元件应校准,且在规定的到期时间内。
5.3.4安装
a)试验轴承必须履行下列检查:
b) 记录轴承的重量,精确到十分之一克。
c) 测量和记录轴承安装前后的游隙。
d)测量和记录轴承的旋转力矩。
(轴承在300rpm的转速下运转三分钟后所测力矩。
)
e)安装方法
f)将轮毂单元用规定的压紧螺杆及力矩拧紧。
h)联接套与试验机连接好。
i)连接好径向加力臂。
j)连接好轴向加力臂。
k)安装好振动和温度传感器。
5.3.5记录
a)记录试验开始的时间。
b)每隔两小时人工记录试验情况一次。
c)每5分钟电脑存盘一次试验原始数据。
d)当轴承失效时,要及时报告试验工程师或试验室主任。
e)记录试验结束时间。
f)将试验轴承从试验台上卸下,测量其游隙、重量和转矩。
j)将试验轴承装在盒中,并作好标记。
5.3.6试验后
a)如果轴承在理论的B10(25小时)寿命后还未失效,要将轴承贮存一年,然后再破坏及丢弃。
b)如果轴承在理论的B10寿命前失效,或显示异常的特性,例如:噪声,过大的游隙,过多的漏脂等,要报告试验工程师,除非有其它方面的要求。
然后分解轴承,分析失效的原因,而油脂检验除外。
c)分析调查工装或负荷出问题的可能性,如果试验进行得适当,则将轴承及油脂提供给有关部门分析,并报告产品工程师。
5.4试验结果要求
5.4.1密封泥水试验
5.4.1.1试验后将漏到轴承外部的润滑脂和泥水污物擦净,称量轴承试后质量.
5.4.1.2拆掉密封圈,观察内外密封圈内和轴承内部油脂颜色,并观察进水情况。
5.4.1.3判定标准:试验达到目标时间,则判定为合格,(前二套要做完全试验)。
5.4.1.4轴承在试验过程中出现密封圈脱落,外圈止口处漏脂或密封圈与外圈相对转动,判定该套轴承不合格。
5.4.1.5批产品判定:如果进行批试验,按GB2829的规定,取不合格质量水平RQL为1.5,
判定水平Ⅰ,一次抽样方案,样本大小为2。
每批试验允许的不合格品数为0套。
5.4.2漏脂试验
5.4.2.1试验后将漏到轴承外部的润滑脂和油物擦净,称量轴承试后质量.
5.4.2.2漏脂判定指标: 漏脂率不超过5%为合格。
5.4.2.3轴承在试验过程中出现密封圈脱落,外圈止口处漏脂或密封圈与外圈相对转动,判定该套轴承不合格
5.4.2.4批产品判定:按GB2829的规定,取不合格质量水平RQL为1.5,判定水平Ⅰ,一次
抽样方案,样本大小为6。
每批试验允许的不合格品数为0套。
5.4.3强化试验
5.4.3.1试验室须及时准确地提供轴承的试验报告。
5.4.3.2试验数据需由工作需要的部门作出解释。
5.4.3.3所有原始数据要附给相关的工程部门,并存档在试验室的档案柜中。