SPC-统计过程控制管理程序
SPC统计过程控制的使用步骤

SPC统计过程控制的使用步骤简介SPC (Statistical Process Control) 统计过程控制是一种基于统计方法的质量管理工具,用于监控和控制过程中的变异性。
通过采集数据并分析,SPC可帮助组织识别潜在的问题,并采取必要的纠正措施来提高过程的稳定性和一致性。
本文将介绍SPC的使用步骤,帮助读者了解如何应用SPC来优化工作流程。
步骤一:确定关键过程在应用SPC之前,首要任务是确定要监控和控制的关键过程。
关键过程是对产品或服务质量具有重要影响的主要步骤。
通过识别关键过程,可以更具针对性地收集数据,并制定相应的控制策略。
步骤二:收集数据采集准确的数据是SPC的基础。
数据收集的频率和样本量应根据过程的特点和要求进行确定。
通常,数据可以通过手动记录、传感器或监控设备等方式收集。
在收集数据时,需要记录以下信息: - 时间戳 - 数据值 - 样本编号(可选) - 采集人员(可选)确保数据采集的一致性和准确性对于后续的分析至关重要。
步骤三:数据分析和控制图绘制在SPC中,数据分析是一个关键的环节。
通过分析数据,可以了解过程中的变异性,并绘制控制图以显示过程的稳定性。
以下是数据分析和控制图绘制的步骤: 1. 计算每个样本的平均值和标准差。
2. 绘制一个均值控制图,用于监控过程的中心线移动。
3. 绘制一个范围控制图,用于监控过程的变异性。
4. 检查控制图上的点是否超出控制限。
超出控制限的点可能表示过程存在特殊因素,需要进行进一步的调查和改进。
控制图的使用可以帮助识别过程的异常变动,并及时采取纠正措施来消除或减少变异性。
步骤四:解读控制图理解控制图上的模式和趋势对于SPC的有效运用至关重要。
常见的控制图模式包括: - 单点超出控制限 - 连续点超出上限或下限 - 渐进的点 - 周期性变化根据控制图上的模式和趋势,可以判断过程是否稳定,以及是否存在特殊因素影响。
步骤五:采取纠正措施如果控制图上的点超出控制限或存在异常模式,需要采取相应的纠正措施来解决问题。
【8A版】SPC控制程序文件

【8A版】SPC控制程序文件一、目的SPC(统计过程控制)控制程序的目的在于通过运用统计技术对生产过程中的各个阶段进行监控和评估,及时发现过程中的异常波动,采取相应的措施进行纠正和预防,从而确保产品质量的稳定性和一致性,提高生产效率,降低生产成本。
二、适用范围本 SPC 控制程序适用于公司内所有生产过程中关键质量特性的监控和控制,包括原材料采购、零部件加工、产品装配、成品检验等环节。
三、职责分工1、质量部门负责制定和维护 SPC 控制计划,确定需要控制的关键质量特性、控制方法、抽样频率和样本数量等。
收集和分析质量数据,绘制控制图,并对过程的稳定性和能力进行评估。
当发现过程异常时,组织相关部门进行原因分析,制定改进措施,并跟踪措施的实施效果。
2、生产部门按照 SPC 控制计划的要求进行生产过程的操作和监控,确保生产条件的稳定。
负责对生产过程中的设备、工装进行日常维护和保养,保证其处于良好的运行状态。
配合质量部门进行过程异常的原因分析和改进措施的实施。
3、技术部门负责提供生产过程中的技术支持,确定合理的工艺参数和作业指导书。
参与过程异常的原因分析,对工艺改进提出建议和方案。
4、其他相关部门按照职责分工,配合质量部门、生产部门和技术部门做好 SPC 控制工作。
四、工作流程1、确定关键质量特性质量部门根据产品的质量要求、客户的需求以及以往的生产经验,确定需要进行 SPC 控制的关键质量特性。
这些关键质量特性应能够反映产品的主要性能和质量指标。
2、制定控制计划质量部门根据确定的关键质量特性,制定 SPC 控制计划。
控制计划应包括控制项目、控制方法、抽样频率、样本数量、测量工具、控制图类型、控制限的计算方法、异常判定准则等内容。
3、数据收集生产部门按照控制计划的要求,在生产过程中对关键质量特性进行抽样测量,并将测量数据记录在相应的表格中。
数据的收集应保证准确、及时、完整。
4、绘制控制图质量部门将收集到的数据输入到统计软件中,绘制相应的控制图,如均值极差控制图(XR 图)、均值标准差控制图(XS 图)、中位数极差控制图(XR 图)等。
SPC统计过程控制程序
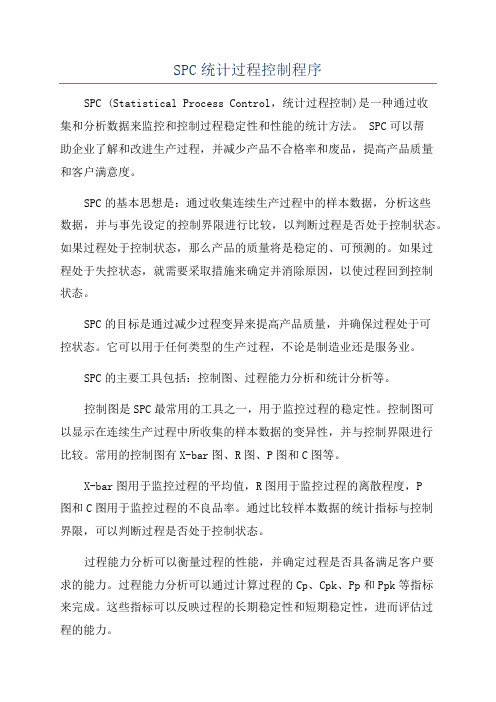
SPC统计过程控制程序SPC (Statistical Process Control,统计过程控制)是一种通过收集和分析数据来监控和控制过程稳定性和性能的统计方法。
SPC可以帮助企业了解和改进生产过程,并减少产品不合格率和废品,提高产品质量和客户满意度。
SPC的基本思想是:通过收集连续生产过程中的样本数据,分析这些数据,并与事先设定的控制界限进行比较,以判断过程是否处于控制状态。
如果过程处于控制状态,那么产品的质量将是稳定的、可预测的。
如果过程处于失控状态,就需要采取措施来确定并消除原因,以使过程回到控制状态。
SPC的目标是通过减少过程变异来提高产品质量,并确保过程处于可控状态。
它可以用于任何类型的生产过程,不论是制造业还是服务业。
SPC的主要工具包括:控制图、过程能力分析和统计分析等。
控制图是SPC最常用的工具之一,用于监控过程的稳定性。
控制图可以显示在连续生产过程中所收集的样本数据的变异性,并与控制界限进行比较。
常用的控制图有X-bar图、R图、P图和C图等。
X-bar图用于监控过程的平均值,R图用于监控过程的离散程度,P图和C图用于监控过程的不良品率。
通过比较样本数据的统计指标与控制界限,可以判断过程是否处于控制状态。
过程能力分析可以衡量过程的性能,并确定过程是否具备满足客户要求的能力。
过程能力分析可以通过计算过程的Cp、Cpk、Pp和Ppk等指标来完成。
这些指标可以反映过程的长期稳定性和短期稳定性,进而评估过程的能力。
统计分析是SPC的基础,通过对收集到的数据进行概率分布拟合、假设检验等统计分析方法,可以确定控制界限的设置和过程能力的评估。
统计分析能够为决策提供科学的依据。
SPC的应用可以帮助企业实现以下几个方面的目标:1.提高产品质量:SPC可以监控和控制生产过程中的变异性,降低产品缺陷和废品率,提高产品质量和一致性。
2.降低成本:通过减少废品和不良品的产生,可以降低生产成本。
3.提高生产效率:SPC可以帮助发现和解决生产过程中的问题,提升生产效率和产能。
SPC统计过程控制程序

5.3.6应意识到并不是所有的特殊原因都是有害的,有些特殊原因可以对制造改进起到积极作用。应对这些特殊原因进行评定。
5.2现行过程能力的研究:
5.2.1当制造件正式批准后,进行批量制造的第二个月开始,横向协调小组成员进行现行过程能力的研究;
5.2.2在稳定的制造过程中发生重要的过程事件时,应在过程控制图表上加以记录,如:更改工装、机器维修、原材料批号更改、工艺参数的调整、操作人员的更换等;
5.2.3在以下情况必须重新进行过程能力的研究:
6.相关文件:
6.1《统计过程控制(SPC)》参考手册;
6.2《纠正预防措施控制程序》;
7.质量记录:
7.1《控制图》;
8.流程图:
无
5.3.4控制图判异准则:控制图中出现以下情况时可以判定异常:
a)有超出控制限的点;
b)有7点以上连续在中心线的同侧;
c)有7点以上连续在控制限第3区间附近;
d)有7点以上连续上升或下降;有明显的非随机图形,主要包括:有周期性、分布宽度异常、明显的上升或下降趋势、子组内数据间有相关性等。
5.3.5异常处理:
a)控制计划中的特殊特性发生了变化;
b)控制图出现了异常(除偶然原因外,发生趋势性的变化);
c)设备重大维修之后,应做CMK(设备过程能力指数)检测。
5.3计量型数据控制图:
5.3.1控制图数据采集:
a)抽样时尽量保证子组中为连续抽样,并分不同模号进行统计。本公司选定子组大小初始研究时为5,之后可以适当减少;
SPC统计过程控制管理程序

XX 汽车零部件有限公司文件编号版本号A/0 SPC 统计过程控制管理程序制定部门生效日期1.目的使用适当的统计技术来验证和分析过程能力、产品特性、过程特性和其他与质量相关的数据、资料,以发现问题,并进行原因分析和采取对策,确保过程稳定及降低不良率,进而提高产品质量。
2.适用范围适用于本公司物料进料检验、计量测试、过程控制、成品检验、可靠性测试、客户投诉及内部质量审核结果等资料的统计分析。
3.职责3.1品保部:负责统计技术的选用,人员培训,对产品和过程特殊特性、重要特性进行数据的收集、分析及处理 ,采用相应的的SPC 统计控制图控制 ,并组织相关职能部门制定纠正和预防措施,验证效果。
3.2各部门负责各自相关数据的传递及纠正预防措施工的实施.4.定义(无)5.管理流程:作业流程图负责部门输入SPC 数据收品保部数据收集统计技术分类品保部相关部门统计技术SPC 管理程序过程重点提示进料检验、试产/量产、过程控制和成品检验、生产过程中各项统计资料收集,依《控制计划》表所列统计方法要求的方法实施。
推移图:分析品质状况的趋势。
特性要因图(鱼骨图):分析各种品质问题原因,以掌握真正原因,并提出对策。
柏拉图:品质问题的重点分析,适用于客户退回品、制程不良品问题分析。
平均数 -极差图:分析和管制制程能力,适用于重点尺寸、特性的管制。
不良率管制图:不良率的控制,适用于制程不良率的管制。
统计工具的选择:在产品质量先期策划阶段期间,需先针对每项制程,妥当地决定选择其适当的统计输出文件 /表单《控制计划》《初始过程能力研究计划表》XX汽车零部件有限公司SPC 统计过程控制管理程序文件编号版本号A/0制定部门生效日期工具,并纳入控制计划内。
公司目前根据实际情况,参阅《SPC 统计制程控制工作指引》,对于计量型统计数据,使用平均值-极差控制图。
对于计数型统计数据,使用不良率控制图填写《初始过程能力研究计划表》。
选取运作稳定的工序,收集质量特性值,数据收集需 100 个以上。
统计过程控制(SPC)及反应计划

深圳亚翔塑胶五金厂ATLAS PLASTICS&METAL PRODUCT FACTORY SZ文件/指引名称统计过程控制(SPC)及反应计划文件/指引编号TS-QW-EG-04页数1/8文件/指引版本 A 生效日期2006-06-01编写人吴永东部门主管审批李承俊管理者代表确认金东奎生效日期版本修改履历2006-06-01 A 首次发行受控编号1A 2A 3A 4A 5A 6A 7A 8A 接收部门总经办营业部采购部工程部成型部品质部装配部仓务部接收人/受控编号9A 10A 11A接收部门行政部财务部信息技术部接收人/文件控制印章如印章之颜色不是红色﹐则是非受控副本﹐文件/指引名称统计过程控制(SPC)及反应计划文件/指引编号TS-QW-EG-04页数2/8文件/指引版本 A 生效日期2006-06-011. 目的通过应用控制图方法,对产品制造过程关键工序的主要质量特性/重要特性进行控制,及时发现异常因素并加以消除,确保工序处于稳定的受控的状态。
2. 范围适用于公司生产过程各关键工序主要质量特性/重要特性的控制。
3. 术语及定义3.1术语σ标准偏差 CL 中心线LCL 控制下限 LSL 规格下限UCL 控制上限 USL 规格上限SPC 统计过程控制 PP 过程实绩CP 能力指数 CPk 稳定过程的能力指数3.2定义计量型数据:可以连续不间断取值的数据。
计数型数据:不可以连续不间断取值的数据。
稳定性:不存在变差的特殊原因处于统计控制的状态。
规格限:本公司或由供应商或客户对相关过程或产品特性所定的控制界限。
变差:过程的单个输出之间不可避免的差别,原因可分成两类:普通和特殊原因。
4.职责4.1技术部4.1.1 在制定控制计划中确定关键的工序参数或控制特性;4.1.2 选取合适的控制图类型(如: X-R,np图),确定取样数量及测试频率;4.1.3 计算持续的中心线和控制界限,包括对控制界限进行修订;4.1.4 检查完成的控制图,分析其趋势/异常情形;4.1.5 工序能力的研究。
SPC-统计过程控制管理程序
SPC-统计过程控制管理程序1、⽬的通过SPC,识别过程变差的原因,针对原因采取措施,消除原因,减少过程变差。
2、范围适⽤于公司SPC。
3、术语引⽤SPC⼿册中附录G的术语及符号。
4、职责技术部负责SPC,其他部门配合。
5、⼯作程序5.1本公司统计过程控制采⽤的⽅法:a)计数型数据:采⽤P控制图,计算过程能⼒(即PPM值)。
b)计量型数据;采⽤X—R控制图,计算Ppk和Cpk。
5.1.1X—R控制图的绘制和使⽤A、收集数据数据是以样本容量恒定的⼩⼦组的形式报出的,这种⼦组通常包括2-5件连续的产品,并周期性的抽取⼦组(例如:每15分钟抽样⼀次,每班抽取两次等)。
应制定⼀个收集数据的计划并将它作为收集、记录及将数据画到控制图上的依据。
A.1选择⼦组⼤⼩、频率和数据a.⼦组⼤⼩:⼀般由4-5件连续⽣产的产品的组合,仅代表单⼀⼑具、冲模板等⽣产出的产品。
b.⼦组频率:应当在适当的时间收集⾜够的⼦组,⼀般对正在⽣产的产品进⾏监测的⼦组频率可以是每班两次、每⼩时⼀次或其他可⾏的频率。
c.⼦组数的⼤⼩:⼀般情况下,包含100或更多单值读数的25或更多个⼦组数可以很好的⽤来检验稳定性。
A.2建⽴控制图及记录原始数据X—R图通常是将X图画在R图之上⽅,下⾯在接⼀个数据栏。
X和R的值为纵坐标,按时间先后的⼦组为横坐标。
数据值以及极差和均值点应纵向对齐。
数据栏应包括每个读数的空间。
同时还应包括记录读数的和、均值(X)、极差(R)以及⽇期或其他识别⼦组的代码的空间。
填⼊每个⼦组的单个读数及识别代码。
A.3计算每个⼦组的均值(X)和极差(R)画在控制图上的特性量是每个⼦组的样本均值(X)和样本极差(R),合在⼀起后它们分别反映整个过程的均值及其极差。
对于每个⼦组,计算:X 1+X 2+…+X nX=nR=X 最⼤值—X 最⼩值式中:X 1+X 2+…+X n 为⼦组内的每个测量值。
n 为⼦组的样本容量A .4选择控制图的刻度两个控制图的纵坐标分别⽤于X 和R 的测量值。
SPC控制程序(含流程图)
文件制修订记录1.0目的:规范统计制程管制SPC运作,以确保各项管制能有效实施,预防重大质量异常的发生。
2.0范围:适用于本公司所有制程,包含成品、半成品、设备。
3.0职责:3.1品质部:主导全厂SPC的推行和运作,提供必要的技术支持和培训,和工程部一起选择管制项目,决定管制标准,监督生产单位的品质状况,协助生产单位分析解决问题,验证改善效果。
4.0定义:4.1SPC:统计制程管制,是一种借助数理统计方法对制程品质状况进行管控的工具。
它对生产过程进行分析评价,根据反馈资讯及时发现系统性因素出现的征兆并采取措施消除其影响,使过程维持在仅受随机性因素影响的受控状态,以达到控制质量的目的。
4.2关键管制特性:有关产品的要求(尺寸、性能测试)或制程参数具有特别的重要性之管制特性,在控制计划&FMEA中以『★』标示,5.0作业内容:5.1实施SPC的两个阶段5.1.1分析阶段:分析阶段的主要目的在于:(1).了解制程现状;(2).使制程处于稳定状态;(3).使制程能力足够。
分析阶段首先要进行的工作是生产准备,即把生产过程所需的原料、劳动力、设备、测量系统等按照标准要求进行准备,生产准备完成后就可以进行生产,注意一定要确保生产是在影响生产的各要素无异常的情况下进行。
然后可以用生产过程收集的资料计算控制界限,作成分析用管制图、直方图、或进行过程能力分析,检验生产过程是否处于稳定状态以及过程能力是否足够。
如果任何一个不能满足则必须寻找原因进行改进,重新进行生产及分析。
直到达到了分析阶段的三个目的,则可认宣告结束,进入SPC监控阶段。
5.1.2监控阶段监控阶段的主要工作是使用控制用控制图对制程进行监控。
此时控制图的控制界限已经根据分析阶段的结果而确定;生产过程的资料及时绘制到控制图上并密切观察控制图,控制图中点的波动情况可以显示出过程受控或失控,如果发现失控,必须寻找原因并尽快消除其影响。
监控可以充分体现出SPC预防控制的作用。
统计过程控制(SPC)管理办法
统计过程控制(SPC)管理办法JD/G13。
15。
A1-—20141.目的和适用范围1.1目的:为建立济南动力部统计过程控制(SPC)体系,通过对济南动力部的关键、重要生产过程进行有效识别,对过程和产品特性变化连续的监视测量和分析评估,根据结果制定改进措施,达到对生产过程的控制和持续改进的目的。
1。
2适用范围:济南动力部统计过程控制体系的管理.2.职责2.1 质量部负责根据生产过程和产品关键重要特性以及各加工部的反馈意见,实施统计过程控制(SPC)的立项;负责统计过程控制(SPC)有效运行的监督管理。
2.2 各加工部负责协助质量部筛选、确定、建立项目;负责统计过程(SPC)的数据采集、录入;负责将各过程SPC项目列入控制计划加以受控;负责组织技术人员对异常特性分析和按期出具报告,以及异常点改进计划的反馈、制定和实施。
3。
工作流程图4.工作内容/要求4。
1定义4。
1。
1 SPC统计过程控制主要是指应用统计分析技术对生产过程进行实时监控,科学的区分出生产过程中产品质量的随机波动与异常波动,从而对生产过程的异常趋势提出预警,以便生产管理人员及时采取措施,消除异常,恢复过程的稳定,从而达到提高和控制质量的目的.4.1。
2 CpK:过程能力指数也称工序能力指数,是指工序在一定时间里,处于控制状态(稳定状态)下的实际加工能力。
它是工序固有的能力,或者说它是工序保证质量的能力。
这里所指的工序,是指操作者、机器、原材料、工艺方法和生产环境等五个基本质量因素综合作用的过程,也就是产品质量的生产过程。
产品质量就是工序中的各个质量因素所起作用的综合表现。
4.1.3 PpK:控制图中用来计算工序性能或叫过程性能的指数。
代表初期工序能力,应用于试产阶段和工序不稳定的情况下。
是经过长期的数据收集,并在数据中包含所有预期的变差源。
它所描述的过程可以是不稳定的,也称是不受控的。
因此PPK指数测量值不能用于预测未来,给出的结果也不能反映未来.但是可以与CPK指数对比以显示系统过程对失控的反应,以及影响过程稳定性的特殊原因。
SPC统计过程控制程序
SPC统计过程控制程序1目的在产品生产过程中,对客户要求或对产品质量影响较大的质量特性采用适宜的统计技术,确保生产过程及产品质量得到有效的控制。
2范围本程序适用于公司相关生产过程的SPC管控。
3定义SPC----Statistical Process Control的缩写,即统计过程控制。
SPC就是应用统计技术对过程中的各个阶段进行监控,从而达到改进与保证质量的目的。
SPC强调全过程的预防。
控制图----对过程质量加以测定、记录从而进行控制管理的一种用科学方法设计的图。
图上有中心线(CL)、控制界限(UCL)和下控制界限(LCL),并有按时间顺序抽取的样本统计量数值的描点序列。
4职责品管部负责SPC数据的采集与统计工作,生产车间配合品管部落实好纠正和预防措施。
5程序5.1控制图的选择SPC采集的数据属计量型数据,故采用最基本最常用的X-R均值-极差控制图。
均值控制图主要用于观察数据分布的均值的变化,R控制图用于观察数据分布的分散情况或变异度的变化。
5.2数据的采集由过程检验员按固定的时间间隔对所要控制的特性进行测量,每次抽取5个样本,要求为同一型号同一时段生产的产品,方法为连续性抽样。
产品在测量过程中必须统一测量手法,每个产品测量次数不超3次。
5.3数据的统计每次抽样测试完毕后将数据输入电脑表格中,数据组数达到一定数量时会产生UCL控制上限、CL标准值、LCL控制下限(样本量5个,故控制限公式计算的系数采用0.58),以后每一次的测量均以该控制限为准。
5.4纠正措施每次输入数据若出现均值和极差控制图中有失控点时,采取相应的纠正措施。
由检验员填写《失控通知单》,与班组长或者部门主管分析原因,商定采取相应措施,由操作责任人执行并在《失控通知单》上签字。
对车间出现的批量问题需及时进行反馈、处理,报废数量在30件以上的需填写《不合格品处理单》,待处理产品数量达到500件以上需开《纠正预防措施处理单》,返工返修的产品需填写《返工返修单》。
- 1、下载文档前请自行甄别文档内容的完整性,平台不提供额外的编辑、内容补充、找答案等附加服务。
- 2、"仅部分预览"的文档,不可在线预览部分如存在完整性等问题,可反馈申请退款(可完整预览的文档不适用该条件!)。
- 3、如文档侵犯您的权益,请联系客服反馈,我们会尽快为您处理(人工客服工作时间:9:00-18:30)。
1、目的通过SPC,识别过程变差的原因,针对原因采取措施,消除原因,减少过程变差。
2、范围适用于公司SPC。
3、术语引用SPC手册中附录G的术语及符号。
4、职责技术部负责SPC,其他部门配合。
5、工作程序5.1本公司统计过程控制采用的方法:a)计数型数据:采用P控制图,计算过程能力(即PPM值)。
b)计量型数据;采用X—R控制图,计算Ppk和Cpk。
5.1.1X—R控制图的绘制和使用A、收集数据数据是以样本容量恒定的小子组的形式报出的,这种子组通常包括2-5件连续的产品,并周期性的抽取子组(例如:每15分钟抽样一次,每班抽取两次等)。
应制定一个收集数据的计划并将它作为收集、记录及将数据画到控制图上的依据。
A.1选择子组大小、频率和数据a.子组大小:一般由4-5件连续生产的产品的组合,仅代表单一刀具、冲模板等生产出的产品。
b.子组频率:应当在适当的时间收集足够的子组,一般对正在生产的产品进行监测的子组频率可以是每班两次、每小时一次或其他可行的频率。
c.子组数的大小:一般情况下,包含100或更多单值读数的25或更多个子组数可以很好的用来检验稳定性。
A.2建立控制图及记录原始数据X—R图通常是将X图画在R图之上方,下面在接一个数据栏。
X和R的值为纵坐标,按时间先后的子组为横坐标。
数据值以及极差和均值点应纵向对齐。
数据栏应包括每个读数的空间。
同时还应包括记录读数的和、均值(X)、极差(R)以及日期或其他识别子组的代码的空间。
填入每个子组的单个读数及识别代码。
A.3计算每个子组的均值(X)和极差(R)画在控制图上的特性量是每个子组的样本均值(X)和样本极差(R),合在一起后它们分别反映整个过程的均值及其极差。
对于每个子组,计算:X 1+X 2+…+X nX=nR=X 最大值—X 最小值式中:X 1+X 2+…+X n 为子组内的每个测量值。
n 为子组的样本容量A .4选择控制图的刻度两个控制图的纵坐标分别用于X 和R 的测量值。
对于X 图,坐标上的刻度值的最大值与最小值之差应至少为子组均值的最大值与最小值差的2倍。
对于R 图,刻度值应从最低值为0开始到最大值之间的差值为初始阶段所遇到的最大极差的2倍。
A .5将均值和极差画在控制图上将均值和极差分别画在其各自的图上将各点用直线连接起来从而得到可见的图形和趋势。
简要的浏览一下所有画上去的点,看是否合理,如果有的点高的很多或者低的很多,需确认计算和画图是否正确,应确保所画的X 和R 点在纵向是对应的。
B 、计算控制限B .1计算平均极差(R)及过程均值(X ) R 1+ R 2+…R kR=kX 1+X 2+…X kX =k式中:k 为子组的数量,R 1和X 1即为第一个子组的极差和均值,R 2和X 2为第一个子组的极差和均值,等等。
B .2计算控制限计算控制限:UCL R =D 4RLCL R =D 3RUCL X = X +A 2RLCL X = X —A 2R将平均极差和过程均值画成水平实线,各控制限画成水平虚线,把线标上记号。
C.过程控制解释C.1分析极差图上的数据点a.超出界限的点:出现一个或多个点超出任何一个控制限是该点处于失控状态的主要证据。
任何超出控制限的点立即进行分析,找出存在特殊原因的信号。
给任何超出控制限的点做标记,以便根据特殊原因实际开始的时间进行调查,采取纠正措施。
超出极差上控制限的点通常说明存在下列情况中的一种或几种:1)控制限计算错误或描点时描错;2)零件间的变化性或分布的宽度已经增大(即变坏),这种增大可以发生在某个时间点上,也可能是整个趋势的一部分;3)测量系统变坏(例如,不同的检验员或量具)4)测量系统没有适当的分辨力。
有一点位于控制限之下(对于样本容量大小等于7的情况),说明存在下列的一种或几种情况:1)控制限或描点错误;2)分布的宽度变小(即变好);3)测量系统已改变(包括数据编辑或变换)。
b.链:有下列现象之一表明过程已改变或出现这种趋势1)连续7点位于平均值的一侧;2)连续7点上升(后点等于或大于前点)或下降。
标记这些点,分析原因,采取措施。
高于平均极差的链或上升链说明存在下列情况之一或全部:1)输出值的宽度增加,其原因可能是无规律的(例如设备工作不正常或固定松动)或是由于过程中的某个要素变化(例如:使用新的不是很一致的原材料),这些都是常见的问题,需要纠正;2)测量系统改变(例如,新的检验员和量具)。
低于平均极差的链,或下降链表明存在下列情况之一或全部:1)输出值分布宽度减小,这常常是一个好状态,应研究以便推广应用和改进过程;2)测量系统改变,这样会掩盖过程真实性能的变化。
c.明显的非随机图形:明显的趋势(尽管它们不属于链的情况),周期性,数据点的分布在整个控制限内,或子组内数据间有规律的关系等。
分析并找出原因,采取措施。
一般情况下大约2/3的描点应落在控制限的中间三分之一的区域内,大约1/3的点落在其外的三分之二的区域。
如果显著多于2/3以上的描点落在离极差均值很近之处,则应对下列情况的一种或更多进行调查:1)控制限计算错误或描点时描错;2)过程或取样方法被分层;每个子组系统化包含了从两个或多个具有完全不同的过程均值的过程流的测量值(例如从几组轴中每组抽一根测取数据);3)数据已经被编辑;如果显著少于2/3以下的描点落在离极差均值很近的区域,则应对下列情况的一种或两种进行调查:1)控制限计算错误或描点时描错;2)过程或抽样方法造成连续的子组中包含从两个或多个具有明显不同的变化性的过程流的测量值(例如:输入材料批次混淆)。
如果存在几个过程流,应分别识别和追踪。
C.2识别并标注特殊原因对极差数据内每个特殊原因进行标注,作过程操作分析,从而确定该原因并改进对过程的理解,纠正条件并且防止再发生。
C.3重新计算控制限(极差图)排除所有已被识别并解决或固定下来的特殊原因影响的子组,然后重新计算新的平均极差和控制限,并画下来。
由于特殊原因而从极差图中去掉的子组,也应从均值图中去掉。
修改后的平均极差和均值可用于重新计算均值的试验控制限。
C.4分析均值图上的数据点a.超出控制限的点:出现一点或多点超出任一控制限就证明在这点出现特殊原因。
应立即对操作进行分析。
在控制图上标注这样的数据点。
一点超出任一控制限通常表明存在下列情况之一或更多:1)控制限或描点错误;2)过程已改变,或是在当时的那一点(可能是一件独立的事件)或是一种趋势的一部分;3)测量系统发生改变(例如,不同的检验员和量具)。
b.链:有下列现象之一表明过程已改变或出现这种趋势1)连续7点位于平均值的一侧;2)连续7点上升(后点等于或大于前点)或下降;标记这些点,分析原因,采取措施。
与过程均值有关的链通常表明出现下列情况之一或两者:1)过程均值已改变——也许还在变化;2)测量系统已改变(漂移、偏倚、灵敏度等)。
c.明显的非随机图形:如明显的趋势(尽管它们不属于链的情况),周期性,数据点的分布在整个控制限内,或子组内数据间有规律的关系等。
分析并找出原因,采取措施。
一般情况下大约2/3的描点应落在控制限的中间三分之一的中间区域内,大约1/3的点落在其外的三分之二的区域。
1/20的点应落在控制限较近之处(位于外1/3的区域)。
另外,存在大约1/150的点落在控制限之外,但可认为是受控稳定系统合理的一部分——就是说,在约99.73%的点位于控制限之内。
如果大大超过2/3以上的描点落在过程均值很近之处,则应对下列情况的一种或更多进行调查:1)控制限计算错误或描点时描错;2)过程或取样方法被分层;每个子组包含了从两个或多个具有不同均值的过程流的测量值;3)数据已经被编辑;如果显著少于2/3以下的数据点落在过程均值很近的区域,则应对下列情况的一种或两种进行调查:1)控制限计算错误或描点时描错;2)过程或抽样方法造成连续的子组中包含从两个或多个具有明显不同过程流的测量值。
如果存在几个过程流,应分别识别和追踪。
C.5识别并标注特殊原因对均值数据中每一个显示处于失控状态的条件进行一次过程操作分析,从而确定特殊原因产生的理由,,纠正该状态,并且防止再发生。
C.6重新计算控制限(均值图)排除所有已被识别并解决或固定下来的特殊原因影响的任何失控的点,然后重新计算并描画过程均值和控制限。
确保当与新的控制限相比时,所有的数据点看起来都处于受控状态。
D.过程能力解释D.1计算过程的标准偏差只要过程的极差和均值都处于统计受控状态,则可用估计的过程标准偏差(σR/d2)来评价过程的能力。
σR/dD.2计算过程能力USL-X X-LSL对于Ppk= min[,]3σs 3σsσs= n (X i-X)2∑i=1 n-1USL-X X-LSL对于Cpk= min[,]3σR/d2 3σR/d2式中:USL,LSL=规范上限和下限,σR/d2为估计的过程标准偏差,σs为过程总变差。
D.3评价过程能力根据是否符合顾客的要求来评价过程能力。
顾客要求的过程能力参见《PPAP控制程序》。
不论是对未满足的能力指数值作出响应,或是为超过最低能力指数要求对持续改进成本和质量性能作出响应,所要求的措施是相同的:1)通过减少普通原因引起的变差或将过程均值调整到接近目标值方法来改进过程性能,这通常意味着要采取管理措施来改进系统;在那些要采取更为紧急措施来满足短期需要的情况,可用以下两种临时的办法:1)对输出进行筛选,根据需要进行报废或返工处置;2)改变规范使之与过程性能一致(这样既不能改进过程也不能满足顾客要求);以上两种方法与过程改进相比显然是下策。
D.4提高过程能力为了提高过程能力,必须重视减少普通原因。
必须将注意力直接集中在系统中,即造成过程变异性的根本因素上,例如:机器性能、输入材料的一致性、过程操作的基本方法、培训方法或工作环境。
一般来说,纠正这些造成不可接受的过程能力的系统原因可能会超出操作者或它们的现场管理人员的能力。
相反,需要采取管理层介入做一些基本的变化、分配资源,并为改进过程的整个性能进行协调。
用短期的局部措施来纠正系统是不会成功的。
D.5对修改的过程绘制控制图并分析对过程已采取了系统的措施后,其效果应在控制图上表现出来。
控制图变成了验证措施是否有效的一种方式。
在对过程实施改变时,应仔细的监视控制图。
在该变化期间会使操作发生混乱,有可能造成新的控制问题,掩盖系统变化的真实效果。
在变化时期的所有不稳定的因素都能解决后,应评定新的过程能力并将他作为将来操作新控制限的基础,通常情况下,变化后用25个子组的数据足以建立新的控制限。
5.1.2 P控制图的绘制和使用A.收集数据A.1 选择子组的容量,频率及数量a.子组容量:用于计数型数据的控制图一般要求较大的子组容量(例如50到200或更多)以便检验出性能的一般变化。