萃取精馏的研究进展
萃取精馏法分离醋酸_水的研究

萃取精馏法分离醋酸_水的研究首先,我们来了解一下醋酸和水的性质。
醋酸(CH3COOH)和水(H2O)的沸点分别为118.1℃和100℃。
由于醋酸和水分子之间存在氢键的形成,所以它们的溶解度也比较高。
根据这些特性,我们可以使用乙酸乙酯(CH3COOCH2CH3)作为辅助溶剂来进行分离。
乙酸乙酯的沸点为77.1℃,与醋酸和水的沸点相差较大,因此适合用于分离。
实验步骤如下:1.准备实验器材和试剂:萃取精馏装置、醋酸、水、乙酸乙酯等。
2.将醋酸和水混合,并在磁力搅拌下充分溶解,得到一个醋酸浓度适中的混合液。
3.将混合液倒入萃取瓶中,加入适量的乙酸乙酯作为辅助溶剂。
4.装配好精馏装置,并进行加热。
由于醋酸和乙酸乙酯的沸点较低,所以可以通过加热沸腾的方式将它们分离出来。
5.开始加热,通过冷凝管冷却蒸汽进一步分离液体。
醋酸和乙酸乙酯的混合物沸点较低,它们蒸发出来的蒸汽会在冷凝管中冷却凝结为液体。
而水由于沸点较高,大部分会留在混合液中。
6.不断收集冷凝管中的液体,直到乙酸乙酯停止蒸发。
通过上述步骤,我们可以将醋酸和水进行有效分离。
在整个分离过程中,乙酸乙酯作为辅助溶剂起到了重要的作用。
由于乙酸乙酯与醋酸的亲合力较大,所以分离效果较好。
这种分离方法的优点是简单、高效,可以用于实验室的小规模分离。
但是需要注意的是,乙酸乙酯是挥发性较大的有机溶剂,对人体有一定的刺激性,应在通风良好的环境下进行操作,并注意防止火源等安全事故的发生。
在研究的过程中,我们还可以对分离后的纯醋酸和纯水进行进一步的化学和物理性质分析,以进一步了解这两种物质的特性和应用。
通过以上研究,我们可以进一步认识醋酸和水的相互作用以及利用萃取精馏法进行分离的原理和方法。
这有助于我们更好地理解化学反应和实践中的分离纯化过程,为实验和工业生产提供指导和参考。
精馏耦合工艺研究进展及展望
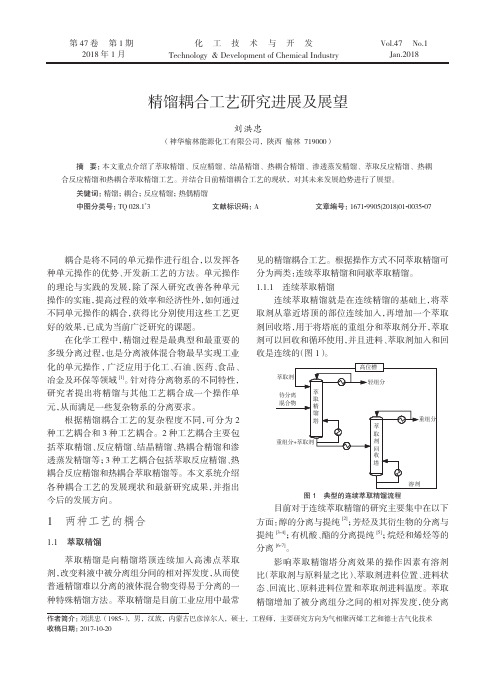
第 47 卷 第 1 期2018 年 1 月Vol.47 No.1Jan.2018化工技术与开发Technology & Development of Chemical Industry精馏耦合工艺研究进展及展望刘洪忠(神华榆林能源化工有限公司,陕西 榆林 719000)摘 要:本文重点介绍了萃取精馏、反应精馏、结晶精馏、热耦合精馏、渗透蒸发精馏、萃取反应精馏、热耦合反应精馏和热耦合萃取精馏工艺。
并结合目前精馏耦合工艺的现状,对其未来发展趋势进行了展望。
关键词:精馏;耦合;反应精馏;热偶精馏中图分类号:TQ 028.1+3 文献标识码:A 文章编号:1671-9905(2018)01-0035-07作者简介:刘洪忠(1985-),男,汉族,内蒙古巴彦淖尔人,硕士,工程师,主要研究方向为气相聚丙烯工艺和德士古气化技术收稿日期:2017-10-20耦合是将不同的单元操作进行组合,以发挥各种单元操作的优势、开发新工艺的方法。
单元操作的理论与实践的发展,除了深入研究改善各种单元操作的实施,提高过程的效率和经济性外,如何通过不同单元操作的耦合,获得比分别使用这些工艺更好的效果,已成为当前广泛研究的课题。
在化学工程中,精馏过程是最典型和最重要的多级分离过程,也是分离液体混合物最早实现工业化的单元操作, 广泛应用于化工、石油、医药、食品、冶金及环保等领域[1]。
针对待分离物系的不同特性,研究者提出将精馏与其他工艺耦合成一个操作单元,从而满足一些复杂物系的分离要求。
根据精馏耦合工艺的复杂程度不同,可分为2种工艺耦合和3种工艺耦合。
2种工艺耦合主要包括萃取精馏、反应精馏、结晶精馏、热耦合精馏和渗透蒸发精馏等;3种工艺耦合包括萃取反应精馏、热耦合反应精馏和热耦合萃取精馏等。
本文系统介绍各种耦合工艺的发展现状和最新研究成果,并指出今后的发展方向。
1 两种工艺的耦合1.1 萃取精馏萃取精馏是向精馏塔顶连续加入高沸点萃取剂,改变料液中被分离组分间的相对挥发度,从而使普通精馏难以分离的液体混合物变得易于分离的一种特殊精馏方法。
萃取精馏分离邻二甲苯与苯乙烯研究
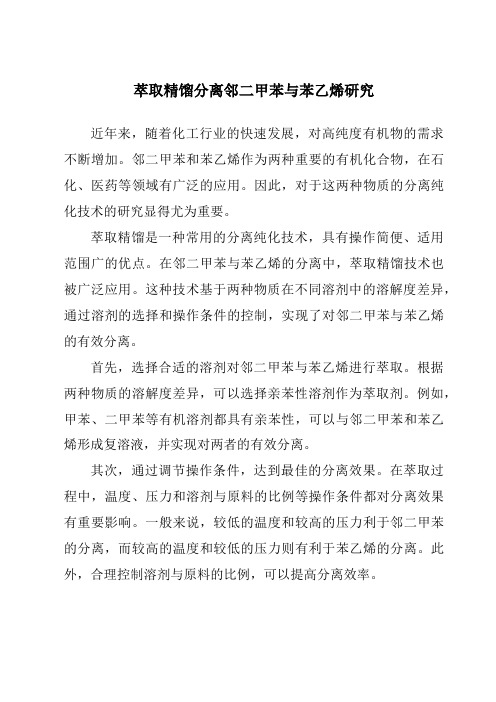
萃取精馏分离邻二甲苯与苯乙烯研究
近年来,随着化工行业的快速发展,对高纯度有机物的需求不断增加。
邻二甲苯和苯乙烯作为两种重要的有机化合物,在石化、医药等领域有广泛的应用。
因此,对于这两种物质的分离纯化技术的研究显得尤为重要。
萃取精馏是一种常用的分离纯化技术,具有操作简便、适用范围广的优点。
在邻二甲苯与苯乙烯的分离中,萃取精馏技术也被广泛应用。
这种技术基于两种物质在不同溶剂中的溶解度差异,通过溶剂的选择和操作条件的控制,实现了对邻二甲苯与苯乙烯的有效分离。
首先,选择合适的溶剂对邻二甲苯与苯乙烯进行萃取。
根据两种物质的溶解度差异,可以选择亲苯性溶剂作为萃取剂。
例如,甲苯、二甲苯等有机溶剂都具有亲苯性,可以与邻二甲苯和苯乙烯形成复溶液,并实现对两者的有效分离。
其次,通过调节操作条件,达到最佳的分离效果。
在萃取过程中,温度、压力和溶剂与原料的比例等操作条件都对分离效果有重要影响。
一般来说,较低的温度和较高的压力利于邻二甲苯的分离,而较高的温度和较低的压力则有利于苯乙烯的分离。
此外,合理控制溶剂与原料的比例,可以提高分离效率。
最后,对分离后的产物进行精馏操作,进一步提高纯度。
通过精馏,可以将溶剂从邻二甲苯和苯乙烯中分离出来,从而获得高纯度的邻二甲苯和苯乙烯。
总之,萃取精馏是一种有效的邻二甲苯与苯乙烯分离纯化技术。
通过选择合适的溶剂、调节操作条件以及进行精馏操作,可以实现对这两种物质的高效分离。
随着研究的不断深入,相信萃取精馏技术在有机物分离纯化领域的应用将会得到进一步拓展,为化工行业的发展做出更大贡献。
精馏分离技术研究新进展
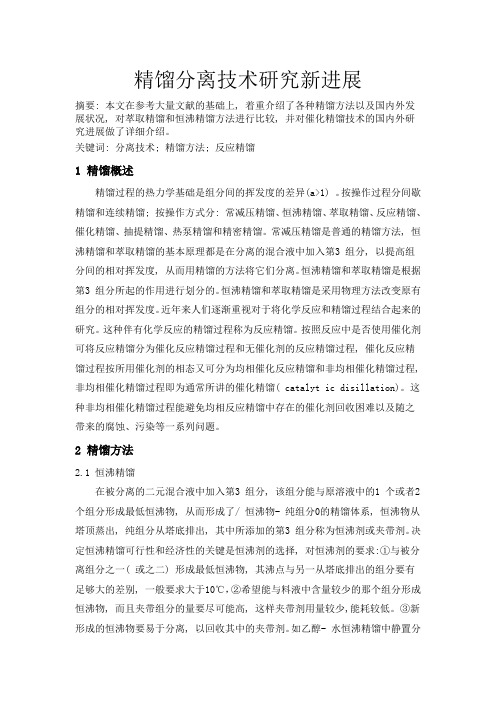
精馏分离技术研究新进展摘要: 本文在参考大量文献的基础上, 着重介绍了各种精馏方法以及国内外发展状况, 对萃取精馏和恒沸精馏方法进行比较, 并对催化精馏技术的国内外研究进展做了详细介绍。
关键词: 分离技术; 精馏方法; 反应精馏1 精馏概述精馏过程的热力学基础是组分间的挥发度的差异(a>1) 。
按操作过程分间歇精馏和连续精馏; 按操作方式分: 常减压精馏、恒沸精馏、萃取精馏、反应精馏、催化精馏、抽提精馏、热泵精馏和精密精馏。
常减压精馏是普通的精馏方法, 恒沸精馏和萃取精馏的基本原理都是在分离的混合液中加入第3 组分, 以提高组分间的相对挥发度, 从而用精馏的方法将它们分离。
恒沸精馏和萃取精馏是根据第3 组分所起的作用进行划分的。
恒沸精馏和萃取精馏是采用物理方法改变原有组分的相对挥发度。
近年来人们逐渐重视对于将化学反应和精馏过程结合起来的研究。
这种伴有化学反应的精馏过程称为反应精馏。
按照反应中是否使用催化剂可将反应精馏分为催化反应精馏过程和无催化剂的反应精馏过程, 催化反应精馏过程按所用催化剂的相态又可分为均相催化反应精馏和非均相催化精馏过程, 非均相催化精馏过程即为通常所讲的催化精馏( catalyt ic disillation)。
这种非均相催化精馏过程能避免均相反应精馏中存在的催化剂回收困难以及随之带来的腐蚀、污染等一系列问题。
2 精馏方法2.1 恒沸精馏在被分离的二元混合液中加入第3 组分, 该组分能与原溶液中的1 个或者2 个组分形成最低恒沸物, 从而形成了/ 恒沸物- 纯组分0的精馏体系, 恒沸物从塔顶蒸出, 纯组分从塔底排出, 其中所添加的第3 组分称为恒沸剂或夹带剂。
决定恒沸精馏可行性和经济性的关键是恒沸剂的选择, 对恒沸剂的要求:①与被分离组分之一( 或之二) 形成最低恒沸物, 其沸点与另一从塔底排出的组分要有足够大的差别, 一般要求大于10℃,②希望能与料液中含量较少的那个组分形成恒沸物, 而且夹带组分的量要尽可能高, 这样夹带剂用量较少,能耗较低。
萃取精馏分离dmc—me共沸物的研究
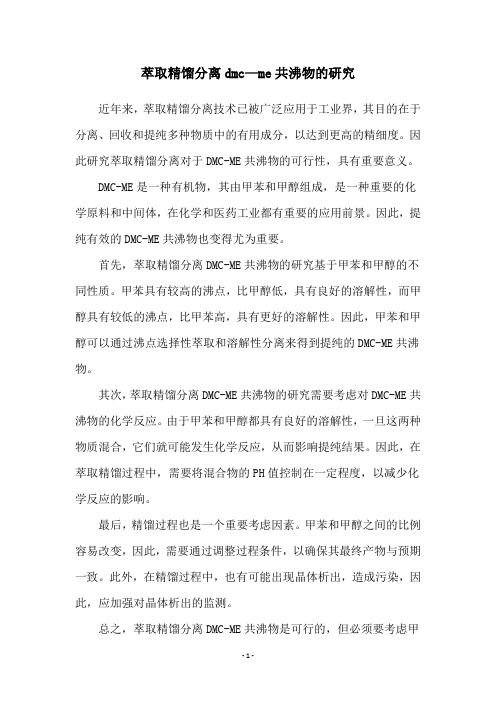
萃取精馏分离dmc—me共沸物的研究
近年来,萃取精馏分离技术已被广泛应用于工业界,其目的在于分离、回收和提纯多种物质中的有用成分,以达到更高的精细度。
因此研究萃取精馏分离对于DMC-ME共沸物的可行性,具有重要意义。
DMC-ME是一种有机物,其由甲苯和甲醇组成,是一种重要的化学原料和中间体,在化学和医药工业都有重要的应用前景。
因此,提纯有效的DMC-ME共沸物也变得尤为重要。
首先,萃取精馏分离DMC-ME共沸物的研究基于甲苯和甲醇的不同性质。
甲苯具有较高的沸点,比甲醇低,具有良好的溶解性,而甲醇具有较低的沸点,比甲苯高,具有更好的溶解性。
因此,甲苯和甲醇可以通过沸点选择性萃取和溶解性分离来得到提纯的DMC-ME共沸物。
其次,萃取精馏分离DMC-ME共沸物的研究需要考虑对DMC-ME共沸物的化学反应。
由于甲苯和甲醇都具有良好的溶解性,一旦这两种物质混合,它们就可能发生化学反应,从而影响提纯结果。
因此,在萃取精馏过程中,需要将混合物的PH值控制在一定程度,以减少化学反应的影响。
最后,精馏过程也是一个重要考虑因素。
甲苯和甲醇之间的比例容易改变,因此,需要通过调整过程条件,以确保其最终产物与预期一致。
此外,在精馏过程中,也有可能出现晶体析出,造成污染,因此,应加强对晶体析出的监测。
总之,萃取精馏分离DMC-ME共沸物是可行的,但必须要考虑甲
苯和甲醇之间特征和性质的差异,以及存在的可能化学反应。
在萃取精馏过程中,需要调整过程条件以保证提纯结果准确。
此外,也应加强对晶体析出的监测,以确保其产物的有效性和洁净度。
萃取精馏分离醋酸_水体系的模拟计算及实验研究

萃取精馏分离醋酸_水体系的模拟计算及实验研究模拟计算在分离过程中起着重要的作用。
它可以通过模拟计算分析分离塔设备的结构和操作参数对分离效果的影响,优化分离过程,提高产品纯度和产能。
模拟计算可以利用平衡数据、物理化学性质和传质动力学数据等基本数据建立模型,通过求解该模型得到各组分在分离过程中的浓度分布、温度分布等重要参数。
常用的模拟计算软件有Aspen Plus、HYSYS 等。
在模拟计算中,需要将醋酸-水体系分为两个相,即醋酸富集相和醋酸稀释相。
首先确定该体系的物理化学性质参数,如醋酸和水的摩尔质量、密度、粘度、表面张力等。
其次根据摩尔分数计算出各组分的蒸气压,选取适当的化学平衡模型对相平衡进行计算。
可以采用等温闪蒸或者将该体系建模为一个摄动分离塔进行模拟计算,通过求解塔的平均物力和能力平衡,得到分离相的物相组成和温度分布。
另外,实验研究也是分离过程中不可或缺的一部分。
实验研究可以验证模拟计算结果的准确性,并提供更真实的数据用于模拟计算中的校正。
在实验中,可以通过探究醋酸-水混合物在不同温度下的平衡分离行为,测量醋酸富集相和醋酸稀释相的物相组成和温度等数据,并进行分析。
此外,可以模拟实际的分离工艺,搭建精馏塔设备并优化操作条件,进一步提高分离效果。
在工业应用方面,萃取精馏分离醋酸-水体系被广泛应用于醋酸生产中。
醋酸是一种重要的有机溶剂,广泛应用于化工、医药、食品等领域。
通过萃取精馏分离,可以获得高纯度的醋酸,并回收原料中的水,实现资源的循环利用。
同时,通过模拟计算和实验研究的指导,可以优化分离工艺,提高产品质量和产能,并减少能源消耗和废水排放。
综上所述,萃取精馏分离醋酸-水体系的模拟计算和实验研究方法在工业生产中具有重要的应用价值。
通过这些方法,可以优化分离工艺,提高产品质量和产能,实现资源的循环利用,对于醋酸生产和相关领域的发展具有重要的促进作用。
基于中间再沸器的萃取精馏精制含水乙腈的过程研究
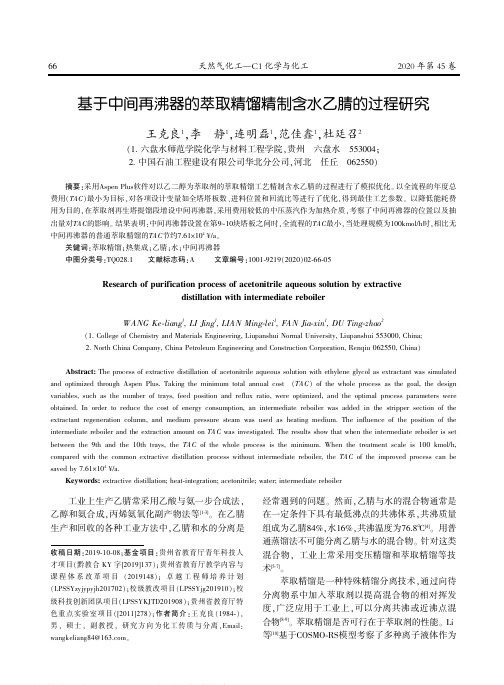
工业上生产乙腈常采用乙酸与氨一步合成法,乙醇和氨合成,丙烯氨氧化副产物法等[1⁃3]。
在乙腈生产和回收的各种工业方法中,乙腈和水的分离是经常遇到的问题。
然而,乙腈与水的混合物通常是在一定条件下具有最低沸点的共沸体系,共沸质量组成为乙腈84%,水16%,共沸温度为76.8℃[4]。
用普通蒸馏法不可能分离乙腈与水的混合物。
针对这类混合物,工业上常采用变压精馏和萃取精馏等技术[5⁃7]。
萃取精馏是一种特殊精馏分离技术,通过向待分离物系中加入萃取剂以提高混合物的相对挥发度,广泛应用于工业上,可以分离共沸或近沸点混合物[8⁃9]。
萃取精馏是否可行在于萃取剂的性能。
Li 等[10]基于COSMO⁃RS模型考察了多种离子液体作为基于中间再沸器的萃取精馏精制含水乙腈的过程研究王克良1,李静1,连明磊1,范佳鑫1,杜廷召2(1.六盘水师范学院化学与材料工程学院,贵州六盘水553004;2.中国石油工程建设有限公司华北分公司,河北任丘062550)摘要:采用Aspen Plus软件对以乙二醇为萃取剂的萃取精馏工艺精制含水乙腈的过程进行了模拟优化。
以全流程的年度总费用(TAC)最小为目标,对各项设计变量如全塔塔板数、进料位置和回流比等进行了优化,得到最佳工艺参数。
以降低能耗费用为目的,在萃取剂再生塔提馏段增设中间再沸器,采用费用较低的中压蒸汽作为加热介质,考察了中间再沸器的位置以及抽出量对TAC的影响。
结果表明:中间再沸器设置在第9~10块塔板之间时,全流程的TAC最小,当处理规模为100kmol/h时,相比无中间再沸器的普通萃取精馏的TAC节约7.61×104¥/a。
关键词:萃取精馏;热集成;乙腈;水;中间再沸器中图分类号:TQ028.1文献标志码:A文章编号:1001⁃9219(2020)02⁃66⁃05Research of purification process of acetonitrile aqueous solution by extractivedistillation with intermediate reboilerWANG Ke⁃liang1,LI Jing1,LIAN Ming⁃lei1,FA N Jia⁃xin1,DU Ting⁃zhao2(1.College of Chemistry and Materials Engineering,Liupanshui Normal University,Liupanshui553000,China;2.North China Company,China Petroleum Engineering and Construction Corporation,Renqiu062550,China)Abstract:The process of extractive distillation of acetonitrile aqueous solution with ethylene glycol as extractant was simulated and optimized through Aspen Plus.Taking the minimum total annual cost(TAC)of the whole process as the goal,the design variables,such as the number of trays,feed position and reflux ratio,were optimized,and the optimal process parameters were obtained.In order to reduce the cost of energy consumption,an intermediate reboiler was added in the stripper section of the extractant regeneration column,and medium pressure steam was used as heating medium.The influence of the position of the intermediate reboiler and the extraction amount on TAC was investigated.The results show that when the intermediate reboiler is set between the9th and the10th trays,the TAC of the whole process is the minimum.When the treatment scale is100kmol/h, compared with the common extractive distillation process without intermediate reboiler,the TAC of the improved process can be saved by7.61×104¥/a.Keywords:extractive distillation;heat⁃integration;acetonitrile;water;intermediate reboiler收稿日期:2019⁃10⁃08;基金项目:贵州省教育厅青年科技人才项目(黔教合KY字[2019]137);贵州省教育厅教学内容与课程体系改革项目(2019148);卓越工程师培养计划(LPSSYzyjypyjh201702);校级教改项目(LPSSYjg201910);校级科技创新团队项目(LPSSYKJTD201908);贵州省教育厅特色重点实验室项目([2011]278);作者简介:王克良(1984⁃),男,硕士,副教授,研究方向为化工传质与分离,Email:*********************。
萃取精馏

萃取精馏及其应用摘要:萃取精馏在近沸点物系和共沸物的分离方面是很有潜力的操作过程。
萃取精馏是一种特殊的精馏方法。
以改变塔内需要分离组分的相对挥发度。
选择合适的溶剂可以增强分离组分之间的相对挥发度, 从而可以使难分离物系转化为容易分离的物系。
本文对萃取精馏的优缺点进行阐述以及提出对缺点的改进并对萃取精馏的前景进行展望。
Extractive distillation in nearly boiling material and separating azeotrope is very potential operation process. Extractive distillation is a kind of special rectification method. In order to change the tower requires the separation of components of the relative volatility of separation. This paper expounds the advantages and disadvantages of extract:extractive distillation extraction agent advantages and disadvantages application prospect Extractive distillation in nearly boiling material and separating azeotrope is very potential operation process. Extractive distillation is a kind of special rectification method. In order to change the tower requires the separation of components of the relative volatility of separation. This paper expounds the advantages and disadvantages of extractive distillation and put forward to the disadvantages of improvement and Prospect of extractive distillation.Abstracr :Extractive distillation in nearly boiling material and separating azeotrope is very potential operation process. Extractive distillation is a kind of special rectification method. In order to change the tower requires the separation of components of the relative volatility of separation. This paper expounds the advantages and disadvantages of extractive distillation and put forward to the disadvantages of improvement and Prospect of extractive distillation.Key words : extractive distillation extraction agent advantages and disadvantages application prospect一、萃取精馏的简介萃取精馏:向精馏塔顶连续加入高沸点添加剂,改变料液中被分离组分间的相对挥发度,使普通精馏难以分离的液体混合物变得易于分离的一种特殊精馏方法。
- 1、下载文档前请自行甄别文档内容的完整性,平台不提供额外的编辑、内容补充、找答案等附加服务。
- 2、"仅部分预览"的文档,不可在线预览部分如存在完整性等问题,可反馈申请退款(可完整预览的文档不适用该条件!)。
- 3、如文档侵犯您的权益,请联系客服反馈,我们会尽快为您处理(人工客服工作时间:9:00-18:30)。
分,而且也可以用来分离非极性组分。近年来,加
盐萃取精馏在工业上已经被成功地应用。因此对萃
取精馏溶剂进行优化,有必要进行加盐萃取精馏的
理论研究。
目前加盐萃取精馏溶液理论方面的研究还非常
缺乏,对盐的选择缺乏理论指导,加盐提高相对挥
发度的机理不清楚。作者试图利用定标粒子理论,
从微观上解释加盐萃取精馏的机理。定标粒子理论
将分子设计应用于萃取精馏溶剂筛选可以大大 减少实验工作量,缩短工作时间。具体到分子设计
化工进展 2001 年第 9 期 !
的计算过程,有两个难点需要解决:一是基团如何
组合成分子;二是计算的准确性。对于前者,可以
通过文献上介绍的一些方法处理基团在数学上的排
列组合问题,利用计算机运行速度快的特点实现自
在萃取精馏工艺路线以及溶剂不便改动的情况 下,采用高效新型的塔板内构件,是提高萃取精馏 塔生产能力的有效策略。如近年来开发出来的多溢 流复合斜孔塔板[8]就可以代替原有的浮阀塔板以提 高生产能力。
多溢流 斜 孔 塔 板 是 在 斜 孔 塔 板 的 基 础 上, 对 MD 塔板进行了研究和分析后,开发出的一种具有 MD 塔板多溢流结构的优点,又有斜孔塔板优点的 复合型塔板。它采用类似 MD 塔板的降液管形式, 但降液管只用一根或者两根而不是很多根,结构比 较简单,液体流动距离较长,塔的处理能力与板效 率都比较高。由于计算机技术和塔板设计技术的不 断发展,塔板的结构参数还可以根据塔内的汽液负
寻找最佳的溶剂是一个复杂的课题。根据我们 从事萃取精馏研究的经验,认为应该从如下 2 个步 骤出发,对溶剂逐一进行筛选。 3.1 计算筛选
当基础溶剂或助溶剂为有机溶剂(包括水) 时,由于有机溶剂种类众多,如果单凭实验从中挑 出最佳的符合某一分离体系的溶剂,将是十分繁琐 的,8 年代以来计算机辅助分子设计的出现为此 提供了便 利。 现 在 计 算 机 辅 助 分 子 设 计 ( CAMD) 的研究和应用非常活跃[l ,ll],而且通常由 UNIFAC 基团贡献法来实现的。UNIFAC 基团贡献法是分子 设计的重要工具,分子设计的主要过程是由若干基 团自动组合成分子,然后按照预定分子的目标性质 对所生成的分子群进行筛选,从而找出目标性质最 优的分子作为溶剂。
s 不太准确,但是可以应用溶液理论的一般知识 判断 sl和 s2的大小,从而判断加盐对提高相对挥 发度 是 否 有 利。 在 盐 浓 度 不 是 太 高 时, 如 果
sl > s2,那么加盐就一定能够提高被分离组分无 限稀释时的相对挥发度,且 sl - s2越大,加盐提 高相对挥发度的效果就越明显。
沸点、化学稳定性、水解性和腐蚀性等。在溶剂选
择的过程中如果注意考虑到这些因素,那么还能够
有助于问题的简化,尽快找到最佳的基础溶剂或助
溶剂。
3.3 加盐萃取精馏的理论研究
已经发现,溶剂加盐是萃取精馏溶剂优化的一
个重要策略。由此开发出来的流程就是加盐萃取精
馏流程。加 盐 萃 取 精 馏 不 仅 可 以 用 来 分 离 极 性 组
近年来在开发新的分离技术过程中,各种分离 方法之 间 的 结 合 日 益 受 到 重 视, 对 萃 取 精 馏 亦 如 此。例如分离醇水溶液如果采用萃取精馏与恒沸精 馏结合[7],就可以较好地发挥出萃取精馏能耗低、 产品纯度高的优点。首先利用萃取精馏得到纯度较 高的醇溶液,然后经过恒沸精馏制得高纯度的醇产 品,这种方法比单独的萃取精馏或恒沸精馏流程从 能耗和操作控制难易综合方面都要好。
计算值
!S 3 . 75
实测值
3 . 73
相对误差 / % 0 . 54
!25 2 . 26 2 . 28 0 . 88
!35 1 . 87 1 . 94 3 . 61
!45 1 . 66 1 . 76 5 . 68
和!Gij
之
间
的
关
系
如下:
S
G ij
=
"Gi "Gj
(l)
!GijΒιβλιοθήκη ="Gi POi "Gj POj
(2)
其中 POi、 POj 为饱和蒸汽压。这些数据的获得除数
据库查 询 以 外[l2], 只 能 依 靠 实 验 方 法。 实 验 测 定
S
G ij
或!Gij
的方法有好几种,可见文献[l3
~
l5]。其
(3)
其中!G 为无盐时的相对挥发度,!Gs 为加盐后的
相对挥发度, sl和 s2为溶质的盐效应常数, cs 为
盐浓度(mol·L - l)。
由定标粒子理论导出了 s 和无限稀释相对挥 发度之间的关系。上式的右边表示微观量,左边表
示宏观量,因此使微观和宏观建立起了一座桥梁。
即使有时限于定标粒子理论的发展水平定量算出的
!!!!"
专专论论与与综综述述 Monograph and Review
!!!!!!!!!!!!!!!!!!!!!!!!!!!!!!!"
萃取精馏的研究进展
!!!!"
!!!!!!!!!!!!!!!!!!!!!!!!!!!!!!!"
雷志刚 王洪有 许 峥 周荣琪 段占庭 (清华大学化工系,北京,100084)
非极性体系,那么溶剂加盐为提高分离能力提供了
8 2001 年第 9 期 化工进展
一条可以借鉴的思路;如果分离除醇水以外的极性 体系,可以 设 想 采 用 溶 剂 加 盐 的 方 式 仍 然 是 可 行 的。有了这一点就可以对许多现有的萃取精馏溶剂 进行改进和优化。
表 1 无限稀释相对挥发度 计算值与实验值比较( T : 323 . 15K)
以加盐 DMF 萃取精馏分离 C4 为例,加盐后 C4 无限稀释相对挥发度的计算值与实验值的对比如表
l 所示。表 l 说明计算值与实验值吻合良好,因此
对于萃取精馏从微观上推算宏观是可能的。
式(3)的导出具有重要的意义,它将加盐萃
取精馏的思想推广到了分离非极性体系,而不仅限
于分离醇水溶液。如果是采用萃取精馏的方法分离
有物性数据库中没有的显性质,才采用基团贡献法
计算。将物性数据库与基团贡献法结合起来,使得
分子设计的结果更为准确可靠。
萃取精馏的有机溶剂经过分子设计缩小搜索范
围,但是助溶剂有时是盐类和聚合物,现阶段萃取
精馏的分子设计对此可能就存在困难。因此萃取精
馏的分子设计以后的发展方向是扩大分子设计的应
用范围,并且使设计结果具有较高的准确性。
工业上常见的丁烯 / 丁二烯等多组分 C4 气体的 萃取精馏分离,按照萃取精馏双塔流程的模式,应 该采用萃取精馏塔(1)—溶剂回收塔(1)—萃取精馏 塔(2)—溶 剂 回 收 塔(2)的 常 规 思 路 进 行 分 离[2,3], 其流程见图 1。
! !""# 年第 $ 期 化工进展
图 1 ACN 法 C4 抽提工艺流程 1
1 萃取精馏流程安排
萃取精馏过程一般采用双塔流程,由萃取精馏
塔和溶剂回收塔组成[1]。萃取精馏的流程设计非常 重要。一个好的萃取精馏工艺流程,不仅能耗可以 降低,而且能够充分地发挥设备的潜力,提高生产 能力。在有些情况下,萃取精馏过程的双塔流程模 式并不是一成不变的。如溶剂沸点太高时,可以对 溶剂回 收 塔 进 行 改 进, 如 加 入 一 定 量 水 以 降 低 沸 点,在下一个塔中再回收溶剂,这时就不是双塔流 程,就需要再增加塔设备。
动组合;对于后者,计算分子的目标性质时,一般
是基于 UNIFAC 划分的基团,通过基团参数按照一
定方式加合来实现,因此要收集广泛的基团参数。
目标性质计算准确性在很大程度上依赖于基团参数
的可靠性。但是限于 UNIFAC 模型的预测精度,基
团参数并不是对每一种物质都能保证准确,所以采
取的解决办法是建立一套强有力的物性数据库,只
中气提法最具应用前景,因此得到了越来越广泛的
应用。
在最后确定溶剂以及进行设计计算时,还必须
进行全浓 度 下 的 汽 液 平 衡 实 验 和 萃 取 精 馏 工 艺 实
验,以验证和比较所选的溶剂并为后续的工业推广
提供依据。如果汽液平衡实验和工艺实验证明了溶
剂的效果,那么就说明此溶剂对于分离过程来说是
可行的。当然选择溶剂还必须考虑其他的因素,如
该流程是最早应用和开发的。但是存在的缺点 是塔 个 数 多, 设 备 投 资 大; 丁 二 烯 反 复 汽 化 和 冷 凝,能耗 较 大。 在 一 萃 塔 和 二 萃 塔 之 间 设 置 一 蒸 塔,作用是使富含丁二烯的 C4 组分与萃取剂 ACN 完全分离。但是这并没有必要,因为在二萃塔中仍 然需要 用 到 萃 取 剂, 因 此 可 以 将 一 蒸 塔 去 掉[4,5]。 采用萃取精馏塔(l)—萃取精馏塔(2)—溶剂回收塔 (2)的流程 2 思路进行分离,使流程 l 得到简化。 如果从减少流程 2 中二萃塔液相负荷的角度来考 虑,可以对流程 2 继续进行优化[6],一萃塔侧线汽 相采出进入二萃塔,从而减少液相负荷,达到提高 生产能力的目的。
2 萃取精馏塔的塔板结构
一般萃取精馏最大的缺点是溶剂量太大,溶剂 比均在 5 ~ 9 以上。国内分离 C4 的两套装置 ACN 法 和 DMF 法的溶剂量都很大,一萃塔溶剂比在 7 ~ 8, 不仅能量、溶剂消耗高,且萃取精馏塔内液体负荷 很高,降低了塔的生产能力和塔板效率,使实际塔 板数增加,抵消了由于加入溶剂后提高相对挥发度 使所需塔板数减少的效果。而且,由于板上液体负 荷大,容易液泛,降低了塔操作的允许汽液负荷。 因此,萃取精馏塔的生产能力一般较低。
3. 2 实验筛选
经过计算筛选出来的有限的有机溶剂,以及不
能经过计算筛选的盐类、高分子聚合物一起必须通
过实验方法进行验证。对于萃取精馏来说,要实现