表面粗糙度改善..
《机械制造工艺学》教案 影响加工表面粗糙度的工艺因素及其改善措施
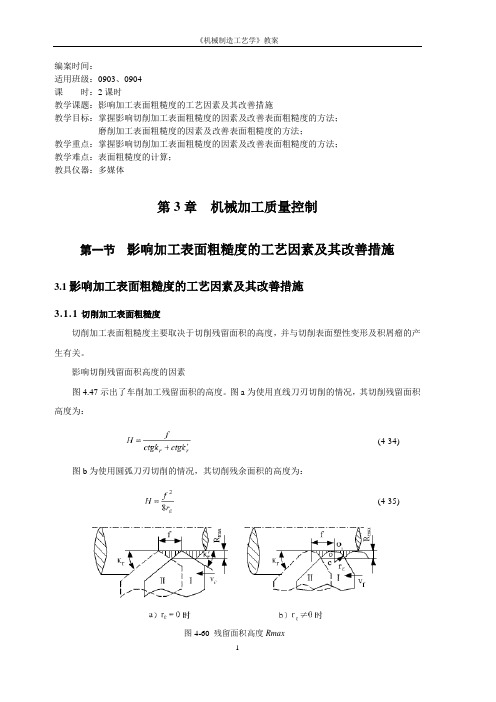
编案时间:适用班级:0903、0904课时:2课时教学课题:影响加工表面粗糙度的工艺因素及其改善措施教学目标:掌握影响切削加工表面粗糙度的因素及改善表面粗糙度的方法;磨削加工表面粗糙度的因素及改善表面粗糙度的方法;教学重点:掌握影响切削加工表面粗糙度的因素及改善表面粗糙度的方法;教学难点:表面粗糙度的计算;教具仪器:多媒体第3章机械加工质量控制第一节影响加工表面粗糙度的工艺因素及其改善措施3.1影响加工表面粗糙度的工艺因素及其改善措施3.1.1切削加工表面粗糙度切削加工表面粗糙度主要取决于切削残留面积的高度,并与切削表面塑性变形及积屑瘤的产生有关。
影响切削残留面积高度的因素图4.47示出了车削加工残留面积的高度。
图a为使用直线刀刃切削的情况,其切削残留面积高度为:(4-34) 图b为使用圆弧刀刃切削的情况,其切削残余面积的高度为:(4-35)图4-60 残留面积高度Rmax从上面两式可知,影响切削残留面积高度的因素主要包括:刀尖圆弧半径、主偏角、副偏角及进给量f等。
影响切削表面塑性变形和积屑瘤的因素图4-61示出了加工塑性材料时切削速度对表面粗糙度的影响。
切削速度v处于20~50m/min 时,表面粗糙度值最大,这是由于此时容易产生积屑瘤或鳞刺。
积屑瘤已在3.4节中介绍,鳞刺是指切削加工表面在切削速度方向产生的鱼鳞片状的毛刺。
在切削低碳钢、中碳钢、铬钢、不锈钢、铝合金、紫铜等塑性金属时,无论是车、刨、钻、插、滚齿、插齿和螺纹加工工序中都可能产生鳞刺。
积屑瘤和鳞刺均使表面粗糙度值加大。
当切削速度超100m/min时,表面粗糙度值下降,并趋于稳定。
在实际切削时,选择低速宽刀精切和高速精切,往往可以得到较小的表面粗糙度值。
图4-61 切削45钢时切削速度与粗糙度关系一般说,材料韧性越大或塑性变形趋势越大,被加工表面粗糙度就越大。
切削脆性材料比切削塑性材料容易达到表面粗糙度的要求。
对于同样的材料,金相组织越是粗大,切削加工后的表面粗糙度值也越大。
改善机械零件加工表面粗糙度的方法

在机械零件加工行业,工件表面粗糙度也称光洁度,一般精密加工件的表面粗糙度要求比较高,在机械零件加工过程中,以下5种方法可以控制机械零件加工表面粗糙度,快来看看吧!
1.切削加工用量:是指可以在切削进给量上,可适当减少表面加工量。
2.选用刀具几何参数:从加工刀具几何参数上,可适当减小副偏角和增大刀尖圆弧半径,必要时可磨出修光刃。
使切削加工容易,降低表面粗糙度。
3.控制机床振动:可从减小刀具与工件间的摩擦、挤压上着手,使刀具刃磨得锋利,加注切削液和对某些韧性好的工件材料进行适当的热处理等。
4.选择合理的加工工艺:对精密机械零件加工过程中,加工工艺流程也非常重要,如工艺流程不合理可能会影响加工品质与生产效率。
很多精密加工件需要粗加工后精加工完成光洁度要求。
5.原材料选择不同:机械设备零配件上,由很多不同原材料加工组成,根据原材料密度不同,加工过程中刀具与机床选用直接关联到表面粗糙度。
以上就是5种改善机械零件加工表面粗糙度的方法,,希望能够帮助到大家!。
单面刚性印制电路板的表面粗糙度与平整度优化
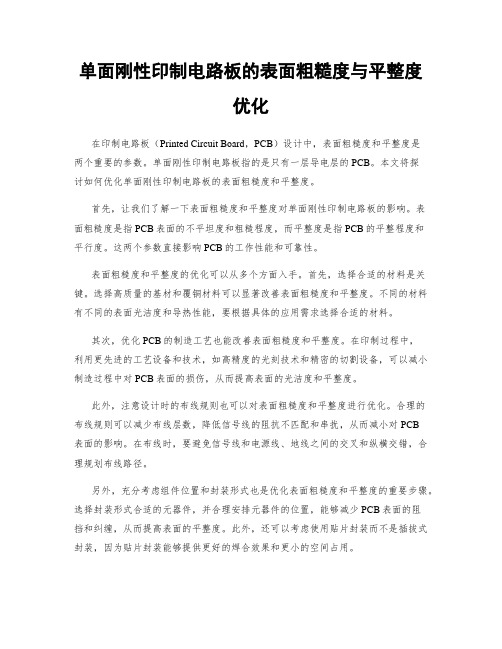
单面刚性印制电路板的表面粗糙度与平整度优化在印制电路板(Printed Circuit Board,PCB)设计中,表面粗糙度和平整度是两个重要的参数。
单面刚性印制电路板指的是只有一层导电层的PCB。
本文将探讨如何优化单面刚性印制电路板的表面粗糙度和平整度。
首先,让我们了解一下表面粗糙度和平整度对单面刚性印制电路板的影响。
表面粗糙度是指PCB表面的不平坦度和粗糙程度,而平整度是指PCB的平整程度和平行度。
这两个参数直接影响PCB的工作性能和可靠性。
表面粗糙度和平整度的优化可以从多个方面入手。
首先,选择合适的材料是关键。
选择高质量的基材和覆铜材料可以显著改善表面粗糙度和平整度。
不同的材料有不同的表面光洁度和导热性能,要根据具体的应用需求选择合适的材料。
其次,优化PCB的制造工艺也能改善表面粗糙度和平整度。
在印制过程中,利用更先进的工艺设备和技术,如高精度的光刻技术和精密的切割设备,可以减小制造过程中对PCB表面的损伤,从而提高表面的光洁度和平整度。
此外,注意设计时的布线规则也可以对表面粗糙度和平整度进行优化。
合理的布线规则可以减少布线层数,降低信号线的阻抗不匹配和串扰,从而减小对PCB表面的影响。
在布线时,要避免信号线和电源线、地线之间的交叉和纵横交错,合理规划布线路径。
另外,充分考虑组件位置和封装形式也是优化表面粗糙度和平整度的重要步骤。
选择封装形式合适的元器件,并合理安排元器件的位置,能够减少PCB表面的阻挡和纠缠,从而提高表面的平整度。
此外,还可以考虑使用贴片封装而不是插拔式封装,因为贴片封装能够提供更好的焊合效果和更小的空间占用。
最后,加强PCB表面的保护也是优化表面粗糙度和平整度的关键步骤。
在制造过程中,可以添加覆盖层或涂布覆盖层来保护PCB表面,防止氧化和腐蚀。
此外,在使用PCB时,还可以添加外壳或保护罩来防止机械损伤和灰尘的进入。
总之,单面刚性印制电路板的表面粗糙度和平整度优化是一个综合考虑材料选择、制造工艺、布线规则、元器件封装和表面保护等多个方面因素的过程。
改善黏着条件的措施
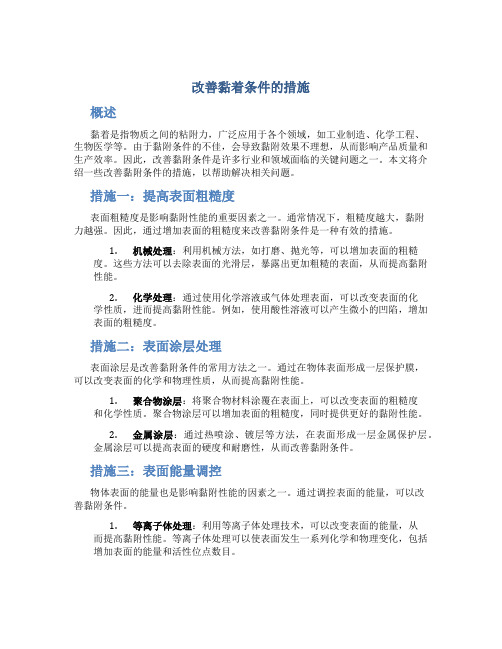
改善黏着条件的措施概述黏着是指物质之间的粘附力,广泛应用于各个领域,如工业制造、化学工程、生物医学等。
由于黏附条件的不佳,会导致黏附效果不理想,从而影响产品质量和生产效率。
因此,改善黏附条件是许多行业和领域面临的关键问题之一。
本文将介绍一些改善黏附条件的措施,以帮助解决相关问题。
措施一:提高表面粗糙度表面粗糙度是影响黏附性能的重要因素之一。
通常情况下,粗糙度越大,黏附力越强。
因此,通过增加表面的粗糙度来改善黏附条件是一种有效的措施。
1.机械处理:利用机械方法,如打磨、抛光等,可以增加表面的粗糙度。
这些方法可以去除表面的光滑层,暴露出更加粗糙的表面,从而提高黏附性能。
2.化学处理:通过使用化学溶液或气体处理表面,可以改变表面的化学性质,进而提高黏附性能。
例如,使用酸性溶液可以产生微小的凹陷,增加表面的粗糙度。
措施二:表面涂层处理表面涂层是改善黏附条件的常用方法之一。
通过在物体表面形成一层保护膜,可以改变表面的化学和物理性质,从而提高黏附性能。
1.聚合物涂层:将聚合物材料涂覆在表面上,可以改变表面的粗糙度和化学性质。
聚合物涂层可以增加表面的粗糙度,同时提供更好的黏附性能。
2.金属涂层:通过热喷涂、镀层等方法,在表面形成一层金属保护层。
金属涂层可以提高表面的硬度和耐磨性,从而改善黏附条件。
措施三:表面能量调控物体表面的能量也是影响黏附性能的因素之一。
通过调控表面的能量,可以改善黏附条件。
1.等离子体处理:利用等离子体处理技术,可以改变表面的能量,从而提高黏附性能。
等离子体处理可以使表面发生一系列化学和物理变化,包括增加表面的能量和活性位点数目。
2.离子注入:通过使用离子束注入技术,可以改变表面的化学性质,从而提高黏附性能。
离子注入可以提高表面的能量和化学活性,增强黏附力。
措施四:表面清洁处理表面的杂质和污染物也是影响黏附条件的重要因素之一。
通过表面清洁处理,可以去除表面的污染物,提高黏附性能。
1.溶剂清洗:使用溶剂来清洗表面,可以去除表面的油脂、尘埃等污染物。
车床工件表面粗糙度的形成原因及解决措施

车床工件表面粗糙度的形成原因及解决措施表面粗糙度是机械加工中衡量加工质量的重要因素,表面粗糙度对零件和机器有着重要的意义。
但由于工件材料、切削加工方式、表面硬化等原因,造成了表面粗糙度值提高。
本文详细分析了车床工件表面粗糙度的形成原因,并提出相应的解决措施。
标签:车床工件:表面:粗糙度:原因:解决措施1.引言在实际的机械加工中,工件表面会存在许多高低不平的微小峰谷,这是因为切屑分离时塑性变形、工艺系统的振动以及刀具与已加工表面问的摩擦等因素的影响。
这些零件被加工表面上的微观几何形状误差称为表面粗糙度。
表面粗糙度对零件的耐磨性、耐腐蚀性、疲劳强度和配合性质都有很大影响。
本文详细分析了车床工件表面粗糙度的形成原因,并提出相应的解决措施,具有一定的实际意义。
2.影响工件表面粗糙度的原因2.1工件材料性能。
塑性金属材料在加工的过程中,刀具挤压金属材料,使其产生塑性变形,切屑和工件分离是由于刀具外力的挤压,表面出现撕裂现象,这严重影响表面粗糙度。
伴随着工件材料韧性的提高,在切屑过程中材料的塑性变形也就越大,加工表面粗糙度也就越差。
脆性材料在加工时,所切削形成的铁屑为颗粒状,在切屑崩碎的过程中,加工表面容易产生细小的坑点,提高表面粗糙度值。
2.2刀具切削加工。
在普通刀具在切屑过程中,切削表面势必会产生残留面积,残留面积的高度则是影响加工表面粗糙度的主要因素。
在整个加工过程中,刀具的进给量、主偏角、副偏角、圆弧半径则是造成切削残留面积的主要因素。
砂轮磨削加工过程中,砂轮上硬质颗粒断裂后形成微刃,其分布情况和外形对表面粗糙度有着直接的影响。
因为磨削加工表面是大量微刃在金属表面切削出细小的切削痕迹构成的,所形成的切削痕迹越细小、越密集则表面粗糙度就越好,相反切削痕迹粗大、分布疏散,则表面粗糙度越差。
2.3表面冷作硬化。
在普通刀具切削或砂轮磨削过程中,表面层金属由于刀具外在切削力和材料本身的塑性,使其晶格产生剪切、滑移、拉长、扭曲、破碎,宏观的表现特点则是材料表面层变硬,屈服点提高,延生率降低。
影响加工表面粗糙度的工艺因素及其改善措施
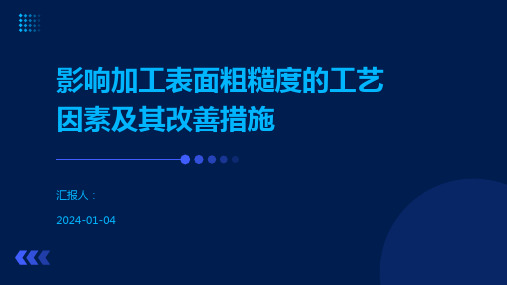
3. 采用适当的冷却方法,如切削液,以降低切削温度和减少热量对刀具的影响。
4. 定期检查和更换刀具,以确保刀具处于良好状态,从而保证加工表面质量。
工件材料对表面粗糙度的影响
04
硬度过低的工件材料在加工过程中容易产生塑性变形,使得工件表面粗糙度增加。
刀具磨损对表面粗糙度的影响
03
总结词
随着刀具磨损的增加,切削力通常会增大。这主要是因为刀具磨损导致切削刃变钝,切削刃与工件之间的摩擦增大,切削力也随之增大。
详细描述
在切削过程中,刀具的切削刃会逐渐磨损,导致切削刃变钝。钝的切削刃与工件表面的摩擦增大,使得切削力增加。这不仅会影响切削过程的稳定性,还可能导致切削热增加,进一步加剧刀具磨损。
影响加工表面粗糙度的工艺因素及其改善措施
汇报人:
2024-01-04
切削用量对表面粗糙度的影响刀具几何参数对表面粗糙度的影响刀具磨损对表面粗糙度的影响工件材料对表面粗糙度的影响切削液对表面粗糙度的影响改善加工表面粗糙度的措施
目录
切削用量对表面粗糙度的影响
01
01
02
在切削塑性材料时,适当降低切削速度可以有效减小表面粗糙度值。在切削脆性材料时,切削速度对表面粗糙度的影响较小。
切削速度越高,切削力越大,切削温度越高,从而使得工件材料软化,容易产生塑性变形,导致表面粗糙度值增大。
进给量增大,切削厚度增加,切削力也相应增大,切削过程中工件材料的塑性变形增大,导致表面粗糙度值增大。
适当减小进给量,可以减小表面粗糙度值。但进给量过小会导致切削力过小,反而使得表面粗糙度值增大。因此,需要根据工件材料、刀具材料和加工要求等因素选择合适的进给量。
化学研磨与机械研磨改善金属表面粗糙度获得平滑光亮表面
化学研磨与机械研磨改善金属表面粗糙度获得平滑光亮表面化学研磨与机械研磨有本质上的不同"化学研磨"是将被研磨面上的微小凸部与凹部相比较的情况下使其凸部优先溶解,改善金属表面粗糙度,获得平滑光亮表面的过程。
"机械研磨"是将被研磨面的凸部用切削,磨耗或者塑性变形等方式除去,获得平滑光亮表面的过程。
两种研磨方式对金属表面有不同的影响,金属表面的许多性质被改变,所以化学研磨与机械研磨有本质上的不同。
由于机械抛光的局限性,使不锈钢等金属工件不能发挥其应有的功能,对这些问题难于解决,在20世纪80年代出现了不锈钢电解化学研磨抛光技术,一定程度上解决了机械抛光难于解决的问题,优势明显。
但是,电化学研磨抛光仍有许多缺点。
不锈钢会不会生锈?大多数人认为不锈钢是不会生锈,包括全国大部分金属表面处理、金属加工厂、五金磨光厂、不锈钢金属抛光厂工作人员。
据研磨专家深圳莱纳克科技有限公司专家介绍,其实不然,不锈钢和其它许多金属一样,用手接触或者接触空气,受环境影响时也会被氧化生锈。
另外,不锈钢工件表面经过机械加工例如焊接、冲压、卷曲、热处理等工艺处理之后生成一层乌黑的氧化变质硬化层,同时又形成了许多肉眼看见和看不见的微小毛刺,以及锐角毛边等。
一、抛光方法一般情况下用机械的方法很难将它们除去,影响其工件材质本身特性的发挥。
为了解决这些问题,深圳市莱纳克科技有限公司(专业生产及销售高精度的研磨、抛光、珩磨机设备,并提供对各类材质的零部件进行平面研磨、抛光等加工服务。
)使用各种方法对不锈钢等金属表面进行研磨抛光处理。
1、机械研磨抛光:a)砂轮抛光b)喷沙抛光c)研削抛光d)挤压抛光2、化学研磨抛光:a)电解化学研磨抛光b)化学研磨抛光3、复合研磨抛光:机械法和化学法两种研磨方式的组合对于不同的金属材质,不同的使用场合,对金属工件表面不同的需求,必须采用不同的研磨方法或者几种研磨方式组合进行研磨加工处理才能使加工工件满足使用上的要求。
精密研磨对光学玻璃二次压型毛坯表面粗糙度的改善研究
精密研磨对光学玻璃二次压型毛坯表面粗糙度的改善研究摘要:随着光学技术的迅猛发展,光学玻璃的质量要求越来越高。
本文以光学玻璃的二次压型毛坯表面粗糙度改善为研究主题,通过精密研磨技术对其进行优化。
本研究采用了多种实验方法,包括砂轮研磨、抛光和超级抛光等,通过对比不同处理方法对表面粗糙度的影响,选择最佳的研磨工艺参数,最终实现了对光学玻璃二次压型毛坯表面粗糙度的有效改善。
1. 引言光学玻璃是一种广泛应用于光学元件制造中的材料,其表面质量对光学系统的性能起着重要影响。
然而,光学玻璃在二次压型毛坯表面往往存在着较高的粗糙度,这对后续的加工和使用带来了困难。
因此,精密研磨技术在对光学玻璃二次压型毛坯表面粗糙度进行改善方面具有重要应用价值。
2. 实验方法2.1 砂轮研磨砂轮研磨是常用的精密研磨方法之一。
我们选择合适的砂轮材料和粒度,并通过调整不同研磨参数,如研磨速度、研磨压力和研磨时间等进行实验。
通过测量实验样品的表面粗糙度,评估砂轮研磨对光学玻璃表面粗糙度的改善效果。
2.2 抛光抛光是一种常见的表面处理方法,在精密研磨中也得到了广泛应用。
我们选用了合适的抛光工具和抛光剂,并通过调整抛光压力、抛光时间等参数进行实验。
同样地,通过测量实验样品的表面粗糙度,评估抛光对光学玻璃表面粗糙度的改善效果。
2.3 超级抛光超级抛光是一种高效的表面处理方法,相较于传统抛光,它能更好地提高光学玻璃表面的平整度和清晰度。
我们采用了高级的超级抛光技术,并通过改变超级抛光剂的配比、抛光工具的材料等参数进行实验。
同样地,通过测量实验样品的表面粗糙度,评估超级抛光对光学玻璃表面粗糙度的改善效果。
3. 结果与讨论通过实验数据的分析,我们发现砂轮研磨、抛光和超级抛光对光学玻璃二次压型毛坯表面粗糙度的改善都具有一定的效果。
在不同处理方法中,超级抛光对表面粗糙度的改善效果最为明显,其次是抛光,而砂轮研磨的改善效果相对较低。
这是由于超级抛光采用了更高级的抛光剂和优质的抛光工具,能够更好地去除光学玻璃表面的微小缺陷和磨削痕迹,从而提高表面的光洁度。
表面粗糙度计算的误差分析与改进方法研究
表面粗糙度计算的误差分析与改进方法研究表面粗糙度是表面几何形态的一个重要指标,它在制造领域以及质量控制等方面有着广泛的应用。
表面粗糙度的计算是基于表面上小范围内的形态变化量,并且通过不同的计算方法来描述不同尺度下的表面粗糙度。
这篇文章将对表面粗糙度计算的误差分析和改进方法进行探讨。
1. 误差源分析1.1 仪器误差表面粗糙度计算的误差源包括仪器误差和环境噪声干扰。
仪器误差是指表面粗糙度测试设备在测量时所带来的误差。
由于实验仪器精度不同,从而导致表面粗糙度数据的误差大小也不同。
因此,在表面粗糙度测试中,应根据需要选择适当的测量精度和测量设备。
同时,根据实际应用的粗糙度要求,适当控制精度不必要的提高,这样可以有效降低测试成本。
1.2 环境噪声干扰环境噪声干扰是指在表面粗糙度测试过程中,由环境噪声污染信号引起的测量误差。
由于现实环境中存在各种各样的干扰源,例如电磁辐射、机械振动等,从而导致表面粗糙度测试结果的误差。
解决这个问题需要采取一系列措施,如在测试过程中有效隔离干扰源、防止干扰源的信号波形入侵等。
2. 计算方法的误差分析2.1 平均高度Ra的误差分析平均高度Ra是表面粗糙度计算中最常用的指标之一。
计算公式为:Ra=1/n∑|yi-y|其中,yi是预先选择的一条长度为l的参考线,n是样本点数。
平均高度Ra的误差来源于采样点不足或过多。
当采样点过少时,计算得到的结果可能与真实值相差较大,因为样本点不能充分反映表面的实际形态。
相反,当采样点过多时,计算出来的平均值会趋近于真实值,但是计算时间会变长,且样本误差还是存在的。
因此,正确选择采样点数极为重要。
2.2 峰值Rp和谷值Rv的误差分析峰值Rp和谷值Rv是表面粗糙度描述不规则凸凹形态的重要指标。
计算公式为:Rp=max(yi)-yiRv=yi-min(yi)其中,yi是预先选择的一条长度为l的参考线。
峰值Rp和谷值Rv的误差来源于设置计算区域的不同,以及区域内样本点的选择。
尼龙 表面粗糙度 加工
尼龙表面粗糙度加工
尼龙的表面粗糙度可以通过多种加工方法进行调整和改善。
以下是一些常见的尼龙表面加工方法:
1. 研磨:使用砂纸、砂轮或其他磨料材料对尼龙表面进行研磨,以去除表面粗糙或不平整的部分,从而提高表面质量和光洁度。
2. 打磨和抛光:使用打磨工具和磨料对尼龙表面进行打磨和抛光,以去除表面凹凸不平和不均匀的部分,使表面更光滑。
3. 焊接:对尼龙进行热焊接或摩擦焊接,可以消除表面上的瑕疵和粗糙度,获得更平滑的表面。
4. 化学处理:通过在尼龙表面应用化学物质或溶液,如溶剂或酸洗剂,可以去除表面的污垢、氧化层和不均匀的部分,从而改善表面质量。
5. 表面涂层:可以在尼龙表面涂覆一层涂料、涂漆或镀层,以增加表面的光滑度和防护性,从而改善表面粗糙度。
6. 硬化处理:通过在尼龙表面进行热处理或化学处理,可以增加表面的硬度和耐磨性,从而改善表面质量和减少摩擦。
这些加工方法可以根据具体需要进行选择和组合使用,以达到所需的表面粗糙度和质量要求。
不同的加工方法可能适用于不同类型的尼龙,因此在进行加工前应了解尼龙的性质和要求。
同时,需要注意加工过程中的安全措施,避免产生有害物质或对尼龙造成损害。
- 1、下载文档前请自行甄别文档内容的完整性,平台不提供额外的编辑、内容补充、找答案等附加服务。
- 2、"仅部分预览"的文档,不可在线预览部分如存在完整性等问题,可反馈申请退款(可完整预览的文档不适用该条件!)。
- 3、如文档侵犯您的权益,请联系客服反馈,我们会尽快为您处理(人工客服工作时间:9:00-18:30)。
j.研磨刷輪的目數定義:
所谓目数,是指刷丝内所含磨料的粒度或粗细度,一般定义是指在1 英寸(inch)*1英寸(inch)的面积内有多少个网孔数,即筛网的 网孔数,磨料能通过该网孔即定义为多少目数:如320目,就是该磨 料能通过1inch*1inch内有320个网孔的筛网。以此类推,目数越大, 说明磨料粒度越细,目数越小,说明磨料粒度越大。
全成信電子(深圳)有限公司
表1. 研磨后表面粗糙度标准值
钻孔后去毛刺 2.0~3.5um
光敏膜/干膜前处理 1.5~3.0um
防焊(绿油)前处理 1.5~2.5um
( 注:以上數據待研究確認) 在PCB制造的各道工序上,表面粗糙度太小会导致镀层、干膜或防 焊层附着力不够造成脱皮、剥离或甩油情况,而过大则会造成表面不 平、干膜气泡和防焊层外观不良等缺陷,因此建议选择刷磨轮供应商 并仔细控制刷板机电流、传送速度等关键参数,在磨痕试验和水破试 验OK的前提下,一定要使表面粗糙度处于上述表1的控制范围内。
图2:OK磨痕 8 请定期检查刷辊及其背压轮,并及时更换磨损严重的背压轮。 刷辊与背压轮间不平行会导致图3所示的磨痕缺陷。(见图3)
全成信電子(深圳)有限公司
2).微观不平度十点高度Rz 在取样长度内5个最大的外轮廓高峰的平均值与5个最大的轮廓谷 深的平均值之和。
其中
ypi-------第i个最大的轮廓谷峰高, yvi-------第i个最大的外轮廓谷深。
全成信電子(深圳)有限公司
3).轮廓峰谷高度Rt 在取样长度内轮廓峰顶线和轮廓谷底线之间的距离。
全成信電子(深圳)定:王洋洋 审 核:
日 期:2005.12.25
全成信電子(深圳)有限公司
一.铜面粗糙度基本知识
1.研磨刷辊的种类
a.在PCB制造过程中用到的研磨刷辊按功能可分为两类: 研磨刷辊和清洗刷辊。 b.研磨刷辊按材质可分为四类: 尼龙针刷辊、不织布刷辊、陶瓷刷辊和高切削刷辊
全成信電子(深圳)有限公司
4、工艺方面:长期不整刷,由于不完全均匀放板的长期积累,也会 出 现“狗骨头”现象。 根据以上产生“狗骨头”现象的原因,采取以下对策来加以克服: 1、操作方面:尽量选用自动左右放板机,放板宽度一定要调整 合理。若采用人工放板,操作工人一定要严格按照要求左右放板,并紧 贴左右挡板。这对提高刷辊寿命肯定有用! 2、配置刷辊:应按照放板宽度或传送宽度确定刷辊有效宽度而 做特殊“削边”处理! 3、设备方面:及时更换已磨损的背压轮。 4、工艺方面:应建立每班检查磨痕的制度,每一班用整刷板整 修刷辊,直至磨痕OK后再刷板。
全成信電子(深圳)有限公司
c.尼龙针刷辊按制造工艺的不同又分为: 钢带缠绕式、编织式、开槽嵌入式、圆孔嵌入式和胶板 植入式五种 d.刷辊按刷丝含磨料不同又分为:
碳化硅(SiC)磨料类、氧化铝(AO)磨料类和纯尼龙/纯不
织布类。 e.按粒度分布范围,可分为: 60#、80#、100#、120#、150#、180#、240# 320#、400#、500#、600#、800#、1000# 1200#、1500#
全成信電子(深圳)有限公司
k.表面粗糙度測試方法和判定數值:
经刷磨轮研磨后的铜皮表面是一个凸凹不平的表面,用电镜可以看出明 显的磨痕。表面粗糙度测试方法就是一种将一个截面上的凸凹不平展示 为一种如下曲线的直观测试技术:
如图所示,Rz表示在取样长度内5个最大轮廓峰高的平均值与5个最 大的轮廓谷深的平均值之和。
图1:标准冷却水喷淋图
全成信電子(深圳)有限公司
6 请注意:一定要控制水温≤35°C,水压在2~8Kg/cm 之间!这 对保证研磨效果十分重要! (具體參數需驗証) 7 放置一基板在刷辊正上(下)方,基板不动,启动刷辊,此时刷 辊与基板接触的磨痕宽应在8—16mm之间。 (具體參數需驗証) (见图2)
全成信電子(深圳)有限公司
b.研磨刷辊的使用方法:
1 请按刷辊端面或内孔上的转向标志正确地安装刷辊。 2 3 4 5 刷辊安装在刷板机上时,必须使刷面成水平状态。 请按设备制造商的要求安装刷辊并遵循相应的安全规范。 未安装好刷辊之前,不要除去保护膜以防弄脏刷辊。 刷辊启动使用前,务必先打开水源开关喷水。并注意经常检查喷 嘴,以保证冷却水的充足 供应,这对减少尼龙污染塞孔和降低刷 辊磨损十分重要!另外,请选用合适的喷嘴,使喷出的水面整个 地覆盖刷辊面。(参见图1) )。
全成信電子(深圳)有限公司
二.銅面粗糙度改善計劃:
a.研磨刷辊“狗骨头”现象产生的原因及其对策
不论是尼龙针刷辊或者是不织布刷辊在现场的使用过程中,如果操 作或配置不当,时常会出现行业内人士所说的“狗骨头”或“哑铃 状”—两头大现象。如上图所示! 这种现象的出现,一种直接损失就是刷辊寿命变短,另一种情况 就是放板位置刚好在“狗骨头”端部时刷板效果肯定不好! 现场观察分析,发现产生这种现象的主要原因有以下几个方面: 1、操作方面:放板不均匀或总在中间放板时就会出现这种现象。 2、配置刷辊:有些设备的传送宽度和刷辊宽度配合要求刷辊的 有效长度不超过传送宽度,这就要求对配置的刷辊作特殊的“削边”处 理。 3、设备方面:由于设备上背压轮的长期磨损,严重时既是刷辊 表面平整,作出的磨痕仍然表现出“狗骨头”现象。
全成信電子(深圳)有限公司
f.尼龙针刷的特点是使用寿命长,研磨效果适中,特别适用 于线宽/线距>=8mil,铜箔厚度>=1oz条件下的PCB的表 面处理。 g.不织布刷辊按制造工艺不同分为:
辐射状(Flap type),圆片状(Disk type)和整体海棉状
(Sponge type)三类。
全成信電子(深圳)有限公司
h.不织布刷辊的特点是研磨精细,所处理的表面粗糙度 均匀一致,从而能明显提高光敏膜和绿油膜的附着力, 特别适用于线宽/线距<=4mil,铜箔厚度<=1oz的 PCB的制造。在钻孔后去毛刺(burr)去除、光敏膜前
处理和绿油(防焊)前处理领域有其卓越的表现。
i.表面粗糙度Ra、Rz、Rt的定義:
1).轮廓算术平均差Ra 在取样长度内轮廓偏距绝对值的算术平均值。