SY型高刚度轧钢机标准修订说明
轧钢机的弹性变形、轧件厚度及板形控制

1、基本功能和类型 一般称之为板厚自动控制(AGC)系统(Automatic Gauge Control),它包括: 测厚部份 检测轧件的实际厚度 厚度比较及调节系统 与设定值比较得出厚差δh,经计算后得出压下调节量δS。 辊缝调节 根据实际测出的压下量变化△S与计算得出的δS 值进行比较,输出电流信号,使液压侗服阀动作,完成辊缝的调节。 轧件变形区部份 这是厚度控制的对象,也是闭环控制系统中的一环。 根据轧件的测厚方法,厚度AGC系统可分为三种类型: 1)直接测厚的反馈式AGC。由测厚仪直接测得轧机出口的轧件厚度h,与设定值比较后得出偏差δh ,将此反馈给系统变换为辊缝调节量δS ,使压下装置移动相应的值以消除厚差δh 。
α=1,K=∞ 全补偿 α>0 ∞>K>C 硬特性(部份补偿) α=0,K=C 恒原始辊缝控制 不补偿 α>-∞,C>K>0,软特性(反方向部份补偿) α= - ∞ ,K=0,△P =0 恒压力控制(反方向全补偿)
以上控制方式的关系曲线见图示。同时也可以用P-H图表示。
一般在成品机架上为保持出口板厚不变,采用硬特性。而在平整机上,采用恒压力控制保持压力波动为零,使其出口板形良好,同时消除轧辊偏心对板厚的影响。
在压力反馈回路中,给出不同的辊缝调节系数Cp ,就能实现各种控制特性的厚度控制。如果将位置反馈回路断开,只是将轧制力P与给定的轧制力P0相比较,使系统保持P= P0,这就实现了恒压力控制。
从以上分析可知,提高机座的刚度系数C可以减小工作机座的弹性变形从而提高板厚精度。但是刚度的提高是有限的,完全依靠机座刚度系数C的提高来达到板厚精度是不可能实现的。必须通过轧机的板厚自动控制系统,可对板厚变化进行补偿实现高精度轧制。
其物理意义为单位板厚变化所对应的轧制力变化。当厚度变化为零时,这时当量刚度K为∞。以下用弹跳方程来分析实现这一过程的原理。
SY高刚度轧机压下螺母的改进
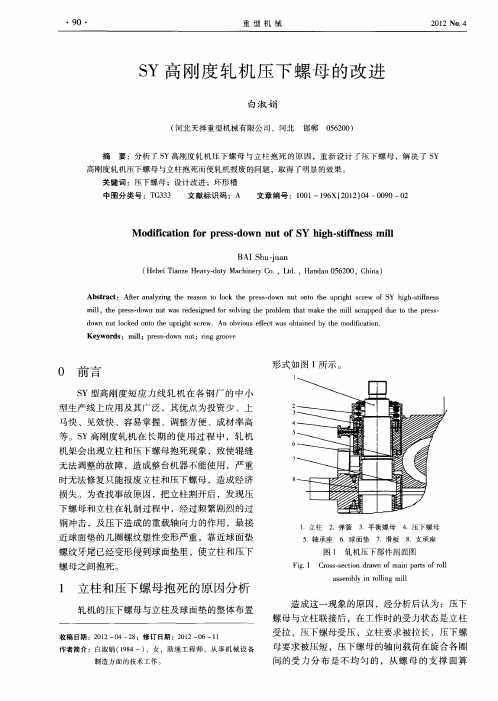
一
,
导 l
,
.
15
▲
R
, ‘‘
一
\ 1 . 1 4/6 2
’ ’ \ d 1 ) 0 2 ~ 一
图 3 改 进 后 压 螺 母
Fi . I r v d prs — wn nu g3 mp o e e sdo t
问的受 力 分 布 是 不 均 匀 的 ,从 螺 母 的 支 撑 面 算
作者简介 :白淑娟 (9 4一) 18 ,女 ,助理工 程师 ,从 事机械设 备
制造方面的技术工作。
重 型 机 械
・ 91・
起 ,第 一 圈受 载 最 大 , 占总 载 荷 的 3 . % , 以 33 后 各 圈 递 减 。旋 合 圈 数 越 多 ,载 荷 分 布 越 不 均 匀 ,到 第 8~1 0圈后 ,螺 纹几 乎不 受 载荷 。 由于 第 一 圈螺纹 受载 最 大 ,则 螺 纹牙变 形最 大 。 以 4 0 S 高 刚度 轧 机 为 例 ,原 压 下 螺 母 5 Y
d w u o k d o t h p ih ce o n n tlc e n o te u r t r w.An o vo s efc a ban d b h df ai n g s b iu f tw s o ti e y t e mo i c t . e i o Ke wo d : mi ;p e s d w u ;r g g o v y rs l l rs—o n n t i ro e n
关 键 词 :压 下 螺 母 ;设 计 改 进 ;环 形 槽 中 图 分 类 号 :T 33 G 3 文 献 标 识 码 :A 文 章 编 号 :10 16 2 1 )4— 0 0— 2 0 1— 9 X(0 2 0 0 9 0
轧钢机械设备

(5)连续式轧机
第44页/共81页
第45页/共81页
(6)串(顺)列往复式(跟踪式、越野式)轧机
第46页/共81页
(7)布棋式轧机
第47页/共81页
(8)复二重式轧机
第48页/共81页
1.4 主机列的构成及各部分的作用
二辊冷轧机
第49页/共81页
第50页/共81页
第51页/共81页
飞轮:轧制时,冲击负荷作用下,系统减速,负载的一部 分有飞轮放出储存的动能来克服。轧件轧出后(空载), 负载突减,主电机带动飞轮加速,飞轮储存能量。
1.3 轧钢机分类 1.3.1 轧钢机按用途分类:可直观显现轧机的主要性能参数 和所生产的产品形状、尺寸。
第7页/共81页
第8页/共81页
1.3.2 按结构分类:根据轧辊在机座中的布置形式 1.3.2.1轧辊水平布置
(1)二辊式轧钢机
第9页/共81页
第10页/共81页
(2)三辊式轧机
第11页/共81页
(5)板形控制:板形控制主要是通过变更轧辊凸度来控制。 为了增大轧辊凸度调整效果,开发了多种新型轧机。主要 有三种:1)横移工作辊:HC、CVC轧机;2)三菱重工及 新日铁开发的PC轧机,通过调整工作辊交叉角来形成不同 凸度辊缝;3)石川岛播磨开发的,在支撑辊中间设置液压 油腔,在其中注入高压油从而调整支撑辊凸度的VC轧机。
1.7.2 热轧板带轧钢机技术的新进展
(1)连铸坯连续铸轧直接将金属熔体“轧制”成半成品带坯 或成品带材的工艺称为连续铸轧。这种工艺的显著特点是其 结晶器为两个带水冷系统的旋转铸轧辊,熔体在其辊缝间完 成凝固和热轧两个过程,而且在很短的时间内(2—3s)完成的。
直接轧制即“连铸一切断一加热或补热一轧制”方式的组
《冶金标准》SY型高刚度轧钢机标准修订说明

《SY型高刚度轧钢机》标准修订说明随着国内棒线材生产线轧机装备水平的不断提高,现行 YB/T 027 — 92《SY型高刚度轧钢机》行业标准已经不能适应当前的使用需要。
为此2005年由中国钢铁工业协会提出并下达了“钢协质标专[2005]06号文”,要求由原标准的起草单位:中冶集团北京冶金设备研究设计总院负责对YB/T 027 — 92《SY型高刚度轧钢机》标准进行修订,并正式立项组成标准起草小组。
中冶集团北京冶金设备研究设计总院作为SY型高刚度轧机的最初设计者,已有20多年的设计经验。
在跟踪国际先进技术的同时,结合国内轧钢生产厂家的实际需要,对SY型高刚度轧机进行了不断地补充和完善。
增加了轧机规格,建全了技术规范,拓展了应用范围,使SY型高刚度轧机不仅可以在型、棒材生产线上使用,而且也可以在棒线材、窄带钢,以及棒带材复合生产线上使用。
故原标准十分有必要在原有基础之上进行修订和补充。
为了使标准修订能够适应当前生产的需要,标准起草小组成员首先走访了国内许多轧钢生产厂家,对轧材生产线的现状进行了充分地调研与分析;同时走访了制造轧线设备的主要制造厂家,对制造厂商的装备和工艺流程进行了充分地考察和交流。
通过走访调研,我们注意到,国内的钢铁企业轧钢生产线的设备普遍进行了更新换代,轧机装备水平都有了不同程度的提高;制造厂商的装备水平也有较大提高。
并且,随着ISO9000质量认证体系的推进,生产流程要求更加规范化。
随着轧钢生产产能的不断扩大,轧钢企业需要稳定高效的轧制设备,对轧机的质量及备品备件的通用性和互换性提出了更高的要求;制造厂商则希望批量化生产,以利于降低成本和缩短供货周期。
总之,结合设计、制造和使用厂家的要求,我们在考虑上述因素的基础上对原标准进行了全面系统的修订,现已形成了初稿即征求意见稿。
在修订中,我们重点把握的几项原则:1.以目前国内外最新技术和发展方向为基础;2.以制造和使用厂家的要求为依据;3.以SY型高刚度轧机的标准化系列化为原则。
高刚度短应力线轧机安全销的校核及改造
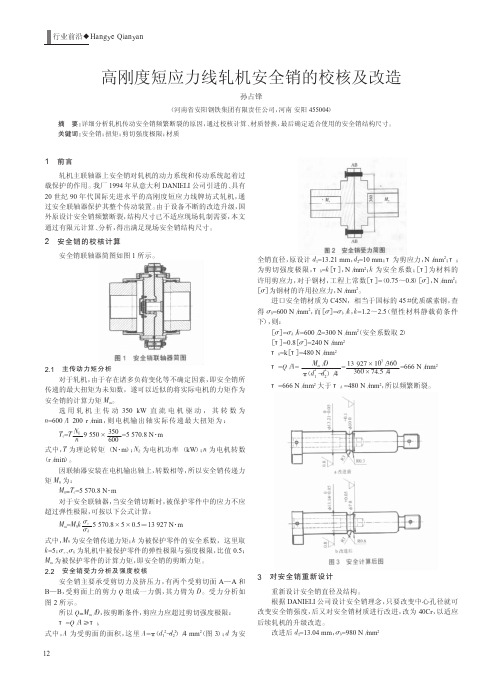
1前言轧机主联轴器上安全销对轧机的动力系统和传动系统起着过载保护的作用。
我厂1994年从意大利DANIELI 公司引进的、具有20世纪90年代国际先进水平的高刚度短应力线牌坊式轧机,通过安全联轴器保护其整个传动装置。
由于设备不断的改造升级,国外原设计安全销频繁断裂,结构尺寸已不适应现场轧制需要,本文通过有限元计算、分析,得出满足现场安全销结构尺寸。
2安全销的校核计算安全销联轴器简图如图1所示。
2.1主传动力矩分析对于轧机,由于存在诸多负荷变化等不确定因素,即安全销所传递的最大扭矩为未知数,遂可以近似的将实际电机的力矩作为安全销的计算力矩M m 。
选用轧机主传动350kW 直流电机驱动,其转数为n =600/1200r /min ,则电机输出轴实际传递最大扭矩为:T c =T N k n 9550×350600=5570.8N ·m式中,T 为理论转矩(N ·m );N k 为电机功率(kW );n 为电机转数(r /min )。
因联轴器安装在电机输出轴上,转数相等,所以安全销传递力矩M n 为:M n =T c =5570.8N ·m 对于安全联轴器,当安全销切断时,被保护零件中的应力不应超过弹性极限,可按以下公式计算:M m =M n k σe σb5570.8×5×0.5=13927N ·m式中,M n 为安全销传递力矩;k 为被保护零件的安全系数,这里取k =5;σe 、σb 为轧机中被保护零件的弹性极限与强度极限,比值0.5;M m 为被保护零件的计算力矩,即安全销的剪断力矩。
2.2安全销受力分析及强度校核安全销主要承受剪切力及挤压力,有两个受剪切面A —A 和B —B ,受剪面上的剪力Q 组成一力偶,其力臂为D 。
受力分析如图2所示。
所以Q=M m /D ,按剪断条件,剪应力应超过剪切强度极限:τ=Q /A ≥τb式中,A 为受剪面的面积,这里A =π(d 12-d 22)/4mm 2(图3);d 为安全销直径,原设计d 1=13.21mm ,d 2=10mm ;τ为剪应力,N /mm 2;τb 为剪切强度极限,τb =k [τ],N /mm 2;k 为安全系数;[τ]为材料的许用剪应力,对于钢材,工程上常数[τ]=(0.75~0.8)[σ],N /mm 2;[σ]为钢材的许用拉应力,N /mm 2。
承钢棒材厂轧机调整工标准
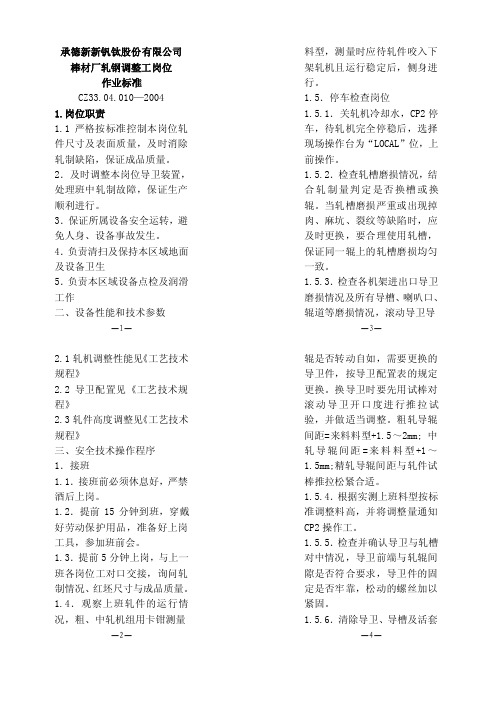
承德新新钒钛股份有限公司棒材厂轧钢调整工岗位作业标准CZ33.04.010—20041.岗位职责1.1严格按标准控制本岗位轧件尺寸及表面质量,及时消除轧制缺陷,保证成品质量。
2.及时调整本岗位导卫装置,处理班中轧制故障,保证生产顺利进行。
3.保证所属设备安全运转,避免人身、设备事故发生。
4.负责清扫及保持本区域地面及设备卫生5.负责本区域设备点检及润滑工作二、设备性能和技术参数—1—2.1轧机调整性能见《工艺技术规程》2.2导卫配置见《工艺技术规程》2.3轧件高度调整见《工艺技术规程》三、安全技术操作程序1.接班1.1.接班前必须休息好,严禁酒后上岗。
1.2.提前15分钟到班,穿戴好劳动保护用品,准备好上岗工具,参加班前会。
1.3.提前5分钟上岗,与上一班各岗位工对口交接,询问轧制情况、红坯尺寸与成品质量。
1.4.观察上班轧件的运行情况,粗、中轧机组用卡钳测量—2—料型,测量时应待轧件咬入下架轧机且运行稳定后,侧身进行。
1.5.停车检查岗位1.5.1.关轧机冷却水,CP2停车,待轧机完全停稳后,选择现场操作台为“LOCAL”位,上前操作。
1.5.2.检查轧槽磨损情况,结合轧制量判定是否换槽或换辊。
当轧槽磨损严重或出现掉肉、麻坑、裂纹等缺陷时,应及时更换,要合理使用轧槽,保证同一辊上的轧槽磨损均匀一致。
1.5.3.检查各机架进出口导卫磨损情况及所有导槽、喇叭口、辊道等磨损情况,滚动导卫导—3—辊是否转动自如,需要更换的导卫件,按导卫配置表的规定更换。
换导卫时要先用试棒对滚动导卫开口度进行推拉试验,并做适当调整。
粗轧导辊间距=来料料型+1.5~2mm; 中轧导辊间距=来料料型+1~1.5mm;精轧导辊间距与轧件试棒推拉松紧合适。
1.5.4.根据实测上班料型按标准调整料高,并将调整量通知CP2操作工。
1.5.5.检查并确认导卫与轧槽对中情况,导卫前端与轧辊间隙是否符合要求,导卫件的固定是否牢靠,松动的螺丝加以紧固。
3500mm宽厚板轧机的刚度测定与实际应用_潘海波
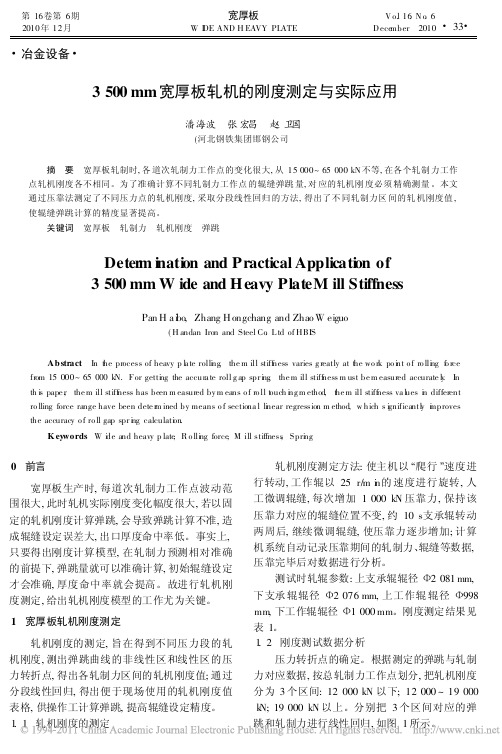
宽厚板
第 16卷
DS 弹跳 DS 轧制力 平均弹跳 总轧制力 /mm 1 . 22 1 . 31 1 . 41 1 . 50 1 . 59 1 . 69 1 . 78 1 . 87 1 . 88 1 . 97 2 . 07 2 . 16 2 . 26 2 . 35 2 . 44 2 . 53 2 . 62 2 . 72 2 . 81 2 . 91 3 . 01 3 . 10 3 . 20 3 . 29 3 . 39 3 . 48 3 . 58 3 . 67 3 . 77 3 . 87 3 . 96 4 . 06 4 . 16 4 . 25 4 . 35 4 . 45 4 . 55 /kN 2 867 3 114 3 364 3 621 3 889 4 158 4 440 4 720 4 730 5 013 5 304 5 614 5 916 6 229 6 549 6 870 7 200 7 533 7 867 8 204 8 549 8 905 9 258 9 611 9 977 10 346 10 714 11 087 11 466 11 848 12 240 12 640 13 039 13 442 13 862 14 285 14 694 /mm 1. 24 1. 33 1. 43 1. 52 1. 62 1. 71 1. 81 1. 90 1. 91 2. 00 2. 09 2. 19 2. 28 2. 38 2. 47 2. 56 2. 66 2. 75 2. 85 2. 94 3. 04 3. 13 3. 23 3. 33 3. 42 3. 52 3. 62 3. 71 3. 81 3. 90 4. 00 4. 10 4. 20 4. 29 4. 39 4. 49 4. 59 / kN 5 872 6 373 6 890 7 417 7 960 8 509 9 081 9 651 9 671 10 250 10 855 11 181 12 103 12 743 13 401 14 069 14 751 15 446 16 139 16 841 17 550 18 288 19 012 19 744 20 504 21 260 22 021 22 792 23 571 24 360 25 165 25 986 26 807 27 636 28 455 29 265 30 075
3500中厚板轧机--轧机毕业设计开题报告(可编辑)
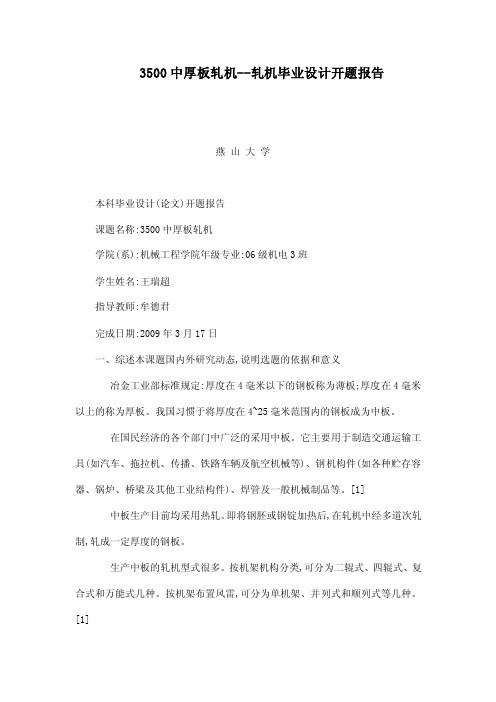
3500中厚板轧机--轧机毕业设计开题报告燕山大学本科毕业设计(论文)开题报告课题名称:3500中厚板轧机学院(系):机械工程学院年级专业:06级机电3班学生姓名:王瑞超指导教师:牟德君完成日期:2009年3月17日一、综述本课题国内外研究动态,说明选题的依据和意义冶金工业部标准规定:厚度在4毫米以下的钢板称为薄板;厚度在4毫米以上的称为厚板。
我国习惯于将厚度在4~25毫米范围内的钢板成为中板。
在国民经济的各个部门中广泛的采用中板。
它主要用于制造交通运输工具(如汽车、拖拉机、传播、铁路车辆及航空机械等)、钢机构件(如各种贮存容器、锅炉、桥梁及其他工业结构件)、焊管及一般机械制品等。
[1] 中板生产目前均采用热轧。
即将钢胚或钢锭加热后,在轧机中经多道次轧制,轧成一定厚度的钢板。
生产中板的轧机型式很多。
按机架机构分类,可分为二辊式、四辊式、复合式和万能式几种。
按机架布置风雷,可分为单机架、并列式和顺列式等几种。
[1]1.轧钢机的发展初轧机的发展。
初轧机的发展经过了3个阶段,到20世纪70年代初,初轧机的轧辊直径已增大到了1 500 mm。
我国从1959年开始自行设计制造开坯机,目前已制成700mm,750tam,850lnm,1 150mm初轧机。
20世纪80年代以来,连铸技术得到较大的发展,连铸比达到80%甚至更高,连铸连轧工艺和设备也日趋完善,初轧机的职能将逐步转变为配合连铸,弥补连铸在钢种和规格方面的不足。
带钢连轧机的发展。
在所有市场需求的钢材中,板带材占有相当大的比重。
我国于1981年从13本引进1 700mm热连轧机的全套设备。
随后,一大批具有先进生产工艺的热连轧和冷连轧板带厂迅速崛起,。
热连轧机发展的主要特点有:加大带卷和坯料重量,减少切头切尾的损耗,提高产品收得率;采用加速轧制,提高钢材产量;产品规格增加,精度提高;采用计算机控制,提高了自动化水平等。
冷轧钢板的生产成本、投资费用虽然比热轧钢板高,但由于冷轧钢板的性能和质量比热轧好,在同样用途下,可以节约金属材料达30%,故冷轧板生产得到迅速发展。
- 1、下载文档前请自行甄别文档内容的完整性,平台不提供额外的编辑、内容补充、找答案等附加服务。
- 2、"仅部分预览"的文档,不可在线预览部分如存在完整性等问题,可反馈申请退款(可完整预览的文档不适用该条件!)。
- 3、如文档侵犯您的权益,请联系客服反馈,我们会尽快为您处理(人工客服工作时间:9:00-18:30)。
SY型高刚度轧钢机标准修订说明《SY型高刚度轧钢机》标准修订说明随着国内棒线材生产线轧机装备水平的不断提高,现行 YB/T 027 — 92《SY型高刚度轧钢机》行业标准已经不能适应当前的使用需要。
为此2005年由中国钢铁工业协会提出并下达了“钢协质标专[2005]06号文”,要求由原标准的起草单位:中冶集团北京冶金设备研究设计总院负责对YB/T 027 — 92《SY型高刚度轧钢机》标准进行修订,并正式立项组成标准起草小组。
中冶集团北京冶金设备研究设计总院作为SY型高刚度轧机的最初设计者,已有20多年的设计经验。
在跟踪国际先进技术的同时,结合国内轧钢生产厂家的实际需要,对SY型高刚度轧机进行了不断地补充和完善。
增加了轧机规格,建全了技术规范,拓展了应用范围,使SY型高刚度轧机不仅可以在型、棒材生产线上使用,而且也可以在棒线材、窄带钢,以及棒带材复合生产线上使用。
故原标准十分有必要在原有基础之上进行修订和补充。
为了使标准修订能够适应当前生产的需要,标准起草小组成员首先走访了国内许多轧钢生产厂家,对轧材生产线的现状进行了充分地调研与分析;同时走访了制造轧线设备的主要制造厂家,对制造厂商的装备和工艺流程进行了充分地考察和交流。
通过走访调研,我们注意到,国内的钢铁企业轧钢生产线的设备普遍进行了更新换代,轧机装备水平都有了不同程度的提高;制造厂商的装备水平也有较大提高。
并且,随着ISO9000质量认证体系的推进,生产流程要求更加规范化。
随着轧钢生产产能的不断扩大,轧钢企业需要稳定高效的轧制设备,对轧机的质量及备品备件的通用性和互换性提出了更高的要求;制造厂商则希望批量化生产,以利于降低成本和缩短供货周期。
总之,结合设计、制造和使用厂家的要求,我们在考虑上述因素的基础上对原标准进行了全面系统的修订,现已形成了初稿即征求意见稿。
在修订中,我们重点把握的几项原则:1.以目前国内外最新技术和发展方向为基础;2.以制造和使用厂家的要求为依据;3.以SY型高刚度轧机的标准化系列化为原则。
主要修订内容如下:1.范围按规范将原标准本条题目“主题内容与适用范围”简化为“范围”。
本条主要变动如下:(1)将原标准技术条件明确为技术要求;增加了“检验方法和规则、标志、包装和贮运”以便与后续内容对应。
(2)根据实际情况,将轧机的适用范围拓展至轧制线材、窄带材的粗中轧机。
2.规范性引用文件按规范将原标准本条题目“引用标准”修改为“规范性引用文件”。
本条主要变动如下:(1)段首增加了引用说明,明确引用标准的版本。
(2)增加了“GB/T 3768 声学声压法测定噪声源声功率级…”标准条目,为本标准“6.3 整机躁声测定”规定了标准。
(3)增加了“GB/T 5226.1 机械安全机械电气设备…”标准条目,为本标准“5.6 安全要求”规定了标准。
(4)原YB3220.x 宝钢二高炉设备制造通用技术条件已不再适应现行要求,以JB/T替代。
3.术语、标记3.1对术语“刚度、弹跳量、径向调整量、轴向调整量、轴向窜动量”加英文注释。
3.1.5 将原标准轴向窜动量中“在轴向力的作用下…”,修改为“在轧制力的作用下…”,因为轴向力是轧制力的分力, 轴向窜动最终是由轧制力引起的。
3.2.1调整轧机的标记方法。
原轧机标记方法:SY – X X X – X¯¯¯¯¯¯¯¯¯¯类型(B型可不标出,A:A型即轴向调整方式与B型不同;C:C型即偏心套式规格(轧辊公称直径,cm)形式(2:二辊式)产品名称存在以下问题:现今SY型高刚度轧机只有二辊式,无须特殊标记;现轧机轧辊公称直径均以毫米mm为单位,不再以厘米cm为单位;前两项连列容易造成误解;现今轧机只有主流机型,原适用于横列式改造的派生系列极少应用,不应再罗列。
现标记方法:SY– XXX × XXX轧辊辊身长度,mm轧辊公称直径,mmSY型高刚度轧钢机现标记方法更符合通用标记方法。
3.2.2 调整轧机的标记示例:轧辊公称直径为250mm ,辊身长度为450mm的SY型高刚度轧钢机,原标记示例:SY-225×450 YB/T 027 — 92现标记示例:SY-250×450 YB/T 027 — 200X 4.1将原标准本条题目“型式”修改为“型式及外形尺寸”。
轧机型式化繁为简,直接定义主流机型,原派生系列因极少应用而不再罗列,在给出轧机型式简图同时,标注外形尺寸,结构工整。
4.1.1 将原标准4.1.1~4.1.4结构型式(包括A、B、C 型)说明,统一为对现机型结构型式的说明,说明SY型高刚度轧钢机为无牌坊、拉杆连接式短应力线机架结构,由辊系、压下装置及底座等组成;辊系及压下装置的结构;较原标准更明确。
4.1.2 轧机外形尺寸将原标准4.2.2项提至此处, 对应标注外形尺寸的轧机简图,列出各规格尺寸表,结构紧凑。
轧机规格根据实际应用情况,补充了SY-450、SY-550、SY-600、SY-650、SY-750、SY-850六种型号。
4.2 型号及基本参数本条主要变动如下:⑴补充了SY-450、SY-550、SY-600、SY-650、SY-750、SY-850六种型号,删除不再应用的C系列。
⑵删除轧制速度栏目。
轧制速度因工艺要求而异,在轧机适用范围内,以小规格棒材线速度最高,因普遍采用切分轧制,小规格棒材线速度最高不超过18m/s,相应轧机均能满足要求,故此不再标注。
⑶根据实际情况,修正轧机机架及底座重量。
5.2.1对技术性能作如下修订:补充了SY-450、SY-550、SY-600、SY-650、SY-750、SY-850六种型号,删除不再应用的C系列。
重新核定了轧机的静刚度。
5.2.3 将原标准中“轧机可实现轴向固定轴承的轴向游隙的预先调整,…”,修改为“轧机可实现止推轴承的轴向游隙的预先设置,…”,轧机是由止推轴承承受轴向力的,故由止推轴承代替轴向固定轴承更明确;止推轴承的轴向游隙可根据要求预先设置。
5.2.7 将原标准中“轧辊轴承的温升不得大于40℃,…”,修改为“轧辊轴承的温升不得大于60℃,…”,根据现场实际情况,轧辊轴承的温升只要不大于60℃,对轧辊轴承寿命及轧机均无较大影响。
5.3.1 将原标准中“滚动轴承的选用应该符合GB307.1的有关规定,轧辊轴承选用E级精度”,修改为“滚动轴承的选用应该符合GB/T307.1、GB/T307.3、JB/T5389.1的有关规定,轧辊轴承选用6级精度”,按现行要求修改。
5.3.2将原标准中“轧辊应符合GB1504的有关规定”,修改为“铸钢轧辊应符合GB/T1503的有关规定,铸铁轧辊应符合GB/T1504的有关规定”,轧机因工艺要求而采用相应材质的轧辊,故此增加对铸钢轧辊的要求。
5.3.3 增加“轧机末注明公差的线性和角度尺寸的一般公差、选用GB/T 1804中的m级。
轧机末注明的形位公差值、选用GB/T 1184中的K级”,明确末注明公差的范围。
5.3.4将原标准中“焊接件应符合YB3220.8的有关规定”,修改为“焊接件应符合JB/T5000.3的有关规定”。
以JB/T5000.3替代不再适应现行要求的YB3220.8 宝钢二高炉设备制造通用技术条件。
5.3.5将原标准中“铸铁件应符合YB3220.2的有关规定”,修改为“铸铁件应符合JB/T5000.4的有关规定”。
以JB/T5000.4替代不再适应现行要求的YB3220.2 宝钢二高炉设备制造通用技术条件。
5.3.6将原标准中“铜、铝合金铸件应符合YB3220.3的有关规定”,修改为“有色金属铸件应符合JB/T5000.5的有关规定”。
以JB/T5000.5替代不再适应现行要求的YB3220.3 宝钢二高炉设备制造通用技术条件。
5.3.7将原标准中“铸钢件应符合YB3220.1的有关规定”,修改为“铸钢件应符合JB/T5000.6、JB/T5000.7的有关规定”。
以JB/T5000. 6、JB/T5000.7替代不再适应现行要求的YB3220.1 宝钢二高炉设备制造通用技术条件。
5.3.8将原标准中“锻件应符合YB3220.7的有关规定”,修改为“锻件应符合JB/T5000.8的有关规定”。
以JB/T5000.8替代不再适应现行要求的YB3220.7 宝钢二高炉设备制造通用技术条件。
5.3.9将原标准中“机械加工件应符合YB3220.6的有关规定”,修改为“机械加工件应符合JB/T5000.9的有关规定”。
以JB/T5000.9替代不再适应现行要求的YB3220.6宝钢二高炉设备制造通用技术条件。
5.3.10将原标准中“轧机的涂装应符合YB3220.11的有关规定,…”,修改为“轧机的涂装应符合JB/T5000.12的有关规定,…”。
以JB/T5000.12替代不再适应现行要求的YB3220.11 宝钢二高炉设备制造通用技术条件。
5.4.1在轧机的轴承座、支承座加工要求中,新标准中取消各派生型式的称谓,与第3.2.1项相呼应。
5.4.2在轧机的拉杆加工要求中,新标准中取消各派生型式的称谓;将原立柱改为通用的拉杆称谓,与第4.1.1项相呼应。
5.4.3新标准中取消对已淘汰的C型轧机的偏心齿轮粗加工要求,同时增加了对轧机轴向调整机构中齿轮螺纹套粗加工的要求。
5.5.1将原标准中“轧机装配应符合YB3220.5的有关规定”,修改为“轧机装配应符合JB/T5000.10的有关规定及图纸要求”。
以JB/T5000.10替代不再适应现行要求的YB3220.5 宝钢二高炉设备制造通用技术条件。
5.5.2新标准中增加了“轧机配管应符合JB/T5000.11的有关规定及图纸要求”。
使轧机配管有了规范化要求。
5.5.3在轧机的精度要求中,对轧机的轧辊辊颈与四列圆柱轴承内圈内径间过盈量、轧辊固定端推力轴承的轴向间隙、上、下轧辊相对轴向窜动最大量的平均值、支承座与底座止口间间隙等项精度的要求进行了分组规定,较原标准更合理。
5.5.9新标准中增加了“径向调整上、下轧辊中心距,全程往返一次,行程应符合图纸要求”。
使轧机径向调整有了规范化要求。
5.6新标准中增加了安全要求,即“轧钢过程中,轧机严禁带钢压下”。
以防止由此引起的设备损毁、拉钢及堆钢等生产事故,消除安全隐患。
6 检验方法和规则新标准中要求按修订后的第5条款项进行检查及验收,提高了整机的性能。
7.1标志新标准中规定了产品标牌内容,主要包括:a)轧机的型号名称;b)主要技术参数;c)产品出厂编号;d)制造厂名称或商标;e)出厂日期。
较原标准更为明确。
修订后的新标准,更新了全部的引用标准;修订了原标准的技术参数;完善了轧机型号系列、检验手段及验收标准。