精馏塔工艺设计
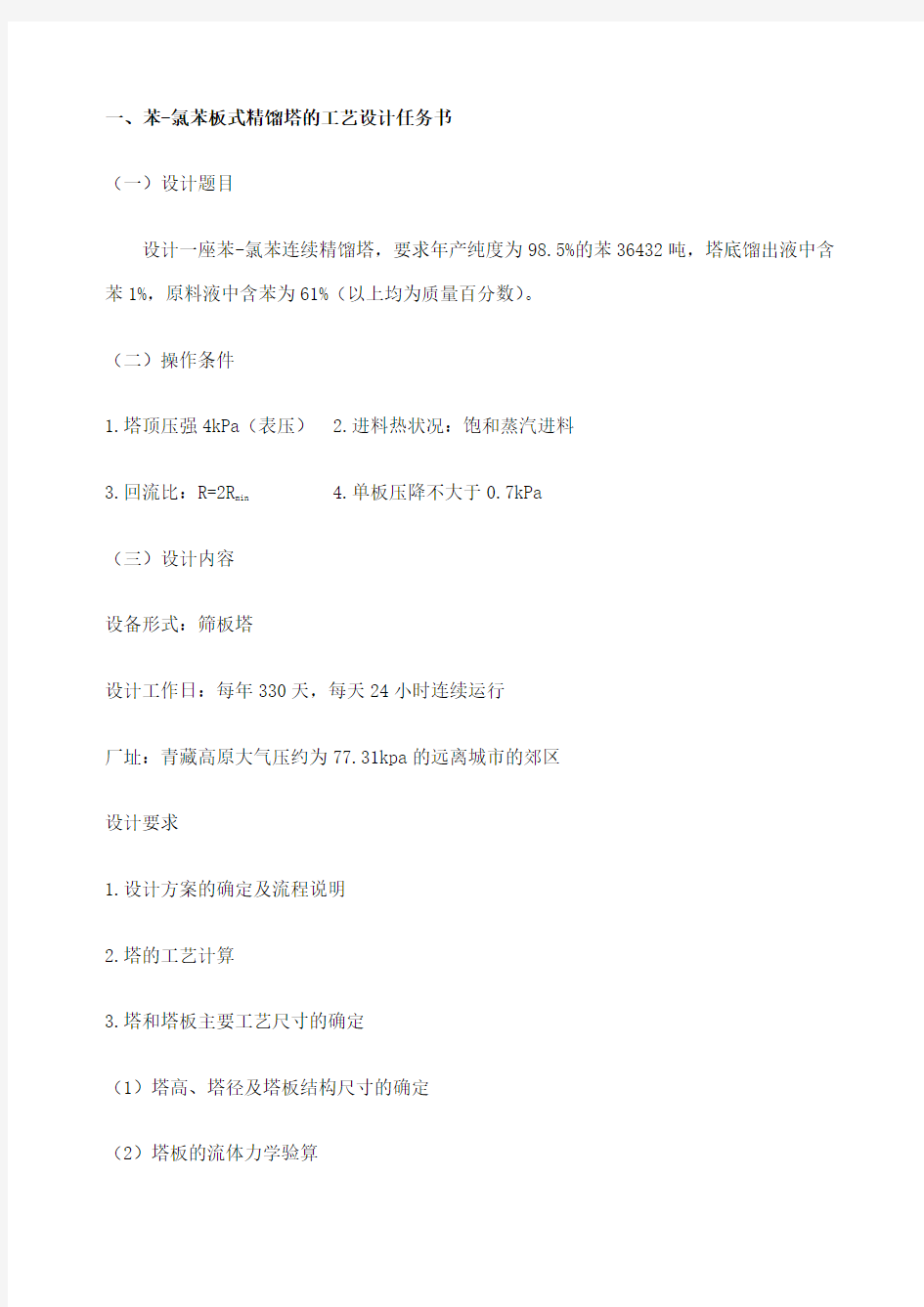

一、苯-氯苯板式精馏塔的工艺设计任务书
(一)设计题目
设计一座苯-氯苯连续精馏塔,要求年产纯度为98.5%的苯36432吨,塔底馏出液中含苯1%,原料液中含苯为61%(以上均为质量百分数)。
(二)操作条件
1.塔顶压强4kPa(表压)
2.进料热状况:饱和蒸汽进料
4.单板压降不大于0.7kPa
3.回流比:R=2R
min
(三)设计内容
设备形式:筛板塔
设计工作日:每年330天,每天24小时连续运行
厂址:青藏高原大气压约为77.31kpa的远离城市的郊区
设计要求
1.设计方案的确定及流程说明
2.塔的工艺计算
3.塔和塔板主要工艺尺寸的确定
(1)塔高、塔径及塔板结构尺寸的确定
(2)塔板的流体力学验算
(3)塔板的负荷性能图绘制
(4)生产工艺流程图及精馏塔工艺条件图的绘制
4、塔的工艺计算结果汇总一览表
5、对本设计的评述或对有关问题的分析与讨论(四)基础数据
p(mmHg)
1.组分的饱和蒸汽压
i
2.组分的液相密度ρ(kg/m3)
3.组分的表面张力σ(mN/m)
4.液体粘度μ(mPa?s)
5.Antoine常数
二、苯-氯苯板式精馏塔的工艺计算书(精馏段部分)(一)设计方案的确定及工艺流程的说明
原料液经卧式列管式预热器预热至泡点后送入连续板式精馏塔(筛板塔),塔顶上升蒸汽流采用强制循环式列管全凝器冷凝后一部分作为回流液,其余作为产品经冷却后送至苯液贮罐;塔釜采用热虹吸立式再沸器提供汽相流,塔釜产品经卧式列管式冷却器冷却后送入氯苯贮罐。
典型的连续精馏流程为原料液经预热器加热后到指定的温度后,送入精馏塔的进料板,在进料上与自塔上部下降的回流液体汇合后,逐板溢流,最后流入塔底再沸器中。在每层板上,回流液体与上升蒸气互相接触,进行热和质的传递过程。操作时,连续地从再沸器取出部分液体作为塔底产品(釜残液),部分液体汽化,产生上升蒸气,依次通过各层塔板。塔顶蒸气进入冷凝器中被全部冷凝,并将部分冷凝液用泵送回塔顶作为回流液体,其余部分经冷却器后被送出作为塔顶产品(馏出液)。 (二)全塔的物料衡算
1.料液及塔顶底产品含苯的摩尔分率
苯和氯苯的相对摩尔质量分别为78.11 kg/kmol 和112.6kg/kmol
=+=
6
.112/39.011.78/61.011
.78/61.0F x 0.693
2.平均摩尔质量
3.料液及塔顶底产品的摩尔流率
依题给条件:一年以330天,一天以24小时计,有:
h kmol 62.5824
330989
.010*******=???=
D ,
全塔物料衡算: W x D x F x W D F w D f +=+= ?25.6kmol/h W kmol/h
22.84==F
(三)塔板数的确定 1.理论塔板数T N 的求取 2)确定操作的回流比R
将1)表中数据作图得y x ~曲线及y x t ~-曲线。在y x ~图上,因q=0, e (0.693,0.693)查得693.0=q y ,31.0=q x 。故有:
7624.031
.0693.0693.0989.0min =--=--=
q q q D x y y x R ;525.12min ==R R
3)求理论塔板数(图解法)
精馏段操作线:392.0604.01
1
+=++
+=
x R x x R R y D
总理论板层数:6.5(包括再沸器) 进料板位层:4 2.实际塔板数p N 1)全塔效率T E
选用m T E μlog 616.017.0-=公式计算。该式适用于液相粘度为0.07~1.4mPa ·s 的烃类物系,式中的m μ为全塔平均温度下以进料组成表示的平均粘度。
塔的平均温度为0.5(80+129)=104.5℃(取塔顶底的算术平均值),在此平均温度下查化工原理附录得:s mPa 246.0?=A μ,s mPa 352.0?=B μ。
2)实际塔板数p N (近似取两段效率相同)
精馏段:651.0/31==Np 块 提馏段:551.0/5.21==Np 块
(四)塔的精馏段操作工艺条件及相关物性数据的计算 1.平均压强m p
取每层塔板压降为0.7kPa 计算。
塔顶:kPa 31.81431.77=+=D p
加料板:kPa 51.8567.031.81=+=?F p 塔底:kPa 01.8957.051.85=+=?W p
精馏段平均压强kPa 41.832/)51.8531.81(=+=m p
提馏段平均压强kPa 26.872/)51.8501.89(=+=m p 2.平均温度m t
B B A A x P x P P ο
ο+=和 C
t B
A P +-
=οlg 两式联立由试差法求得 35.73=D t ℃ ;76.83=F t ℃ ;79.125=W t ℃
精馏段平均温度:t t =73.35+83.76
2
=78.55℃
提馏段平均温度:t t =
125.79+83.76
2
=104.715℃
3.平均分子量m M
塔顶: 989.01==D x y ,93.01=x (查相平衡图)
加料板:725.0=F y ,38.0=F x (查相平衡图)
塔底: 075.0=W y ,014.0=W x
精馏段:kg/kmol 04.832/)59.8749.78(=+=Vm M
提馏段:kg/kmol 8.982/)01.11059.87(=+=Vm M 4.平均密度m ρ 1)液相平均密度m L ρ,
塔顶:35.73=D t ℃ 3/2.822m Kg A =ρ3/3.1049m Kg =B ρ
进料板:76.83=F t ℃3/8.810m Kg A =ρ3/7.1037m Kg =B ρ
塔底:76.83=w t 3/7.761m Kg A =ρ3/6.989m Kg =B ρ 精馏段:3/05.8862/)2.9479.824(m Kg Lm =+=ρ
提馏段:3/9.9662/)6.9862.947(m Kg Lm =+=ρ 2)汽相平均密度m V ρ,
精馏段:3/38.2)
15.27355.78(314.804
.8381.84m Kg RT M P m vm m Vm =+??==
ρ
提馏段:3/76.2)
15.27371.104(314.836
.9981.84m Kg RT M P m vm m Vm =+??==
ρ 5.液体的平均表面张力m σ
塔顶:35.73=D t ℃;m mN DA /09.22=σm mN DB /44.24=σ
进料板:76.83=F t ℃;m mN FA /82.20=σ m mN FB /34.23=σ
塔底:79.125=W t ℃; m mN WA /82.15=σ m mN WB /77.18=σ
精馏段:m mN Lm /86.212/)59.2144.24(=+=σ
提馏段:m mN Lm /18.202/)77.1859.21(=+=σ 6.液体的平均粘度m L μ,
塔顶:35.73=D t ℃s mpa DA ?=332.0μs mpa DB ?=457.0μ
加料板:76.83=F t ℃s mpa FA ?=298.0μs mpa FB ?=416.0μ
塔底:79.125=F t ℃,s mpa FA ?=206.0μ,s mpa FB ?=302.0μ
精馏段:s mpa Lm ?=+=3335.02/)334.0333.0(μ
提馏段:s mpa Lm ?=+=317.02/)3003.0334.0(μ (五)精馏段的汽液负荷计算
汽相摩尔流率h Kmol D R V /02.14862.58525.2)1(=?=+=
汽相体积流量s m VM Vs Vm Vm /43.138
.2360004
.8302.14836003=??==
ρ
液相回流摩尔流率h Kmol RD L /40.8962.58525.1=?==
液相体积流量s m LM Ls Lm Lm /0025.005
.88636000
.9040.8936003=??==
ρ
(六)塔和塔板主要工艺结构尺寸的计算 1.塔径
1)初选塔板间距m m 400=T H 及板上液层高度mm 50=L h ,则: 2)按Smith 法求取允许的空塔气速m ax u (即泛点气速F u )
查Smith 通用关联图得075.020=C
负荷因子0763.0)20
86.21(
075.0)20
(
2
.02.020=?==L
C C σ 泛点气速:
s m u /47.138
.238
.205.8860763
.0max =-=m/s
3)操作气速
取s m u u /029.147.17.07.0max =?== 4)精馏段的塔径
圆整取mm 1400=D
塔截面积为222539.1)4.1(4
4
m D A T =?=
=
π
π
此时的操作气速s m u /935.0011
.242
.1==
。 2.塔板工艺结构尺寸的设计与计算 1)溢流装置
采用单溢流型的平顶弓形溢流堰、弓形降液管、凹形受液盘,且不设进口内堰。 ①溢流堰长(出口堰长)w l
取m 84.04.16.06.0=?==D l w ②出口堰高w h
t t t
=0.6
t t
t t
2.5=1
3.92t 查得E=1.02
③降液管的宽度d W 和降液管的面积f
A
由66.0/=D l w ,查化原下P 147图11-16得055.0/,1.0/==T f d A A D W ,即:
m 14.0=d W ,2055.0m A f = 液体在降液管内的停留时间
s Ls
H A T
f 555.133600>==
τ(满足要求)
④降液管的底隙高度o h
液体通过降液管底隙的流速一般为0.07~0.25m/s ,取液体通过降液管底隙的流速
m/s 1.0='o
u ,则有: 故降液管设计合底隙高度设计合理 2)塔板布置
1.塔板分块 因D=1400 故塔板分4块
2.边缘区宽度 m W s 09.0'=m W c 04.0= ②开孔区面积a A
式中:()0.47m 2/=+-=s d W W D x 3)开孔数n 和开孔率φ
取筛孔的孔径mm 5=o d ,正三角形排列,筛板采用碳钢,其厚度mm 3=δ,且取
0.3/=o d t 。故孔心距mm 1553=?=t 。
每层塔板的开孔数576911582
==
t
A n (孔)
每层塔板的开孔率()
101.03907
.0/907.02
2===
o d t φ(φ应在5~15%,故满足要求) 气体通过筛孔的孔速s m A V u s
/54.120
0==
4)精馏段的塔高1Z
m Z 24.0)16(H )1-N (T 精精=-==; (七)塔板上的流体力学验算 1.塔板压降
1)气体通过干板的压降c h
???
? ???
???
??=L V c C u h ρρ2
00051.0 84.0=o C 。 2)气体通过板上液层的压降1h
动能因子)/(52.138.2983.02/10m s Kg F ?== 查化原图得60.0=β
3)气体克服液体表面张力产生的压降σh 4)气体通过筛板的压降(单板压降)p h 和p p Δ
Kpa Kpa gh P P L p 7.0539.0<==?ρ(满足工艺要求)。
2.雾沫夹带量v e 的验算
验算结果表明不会产生过量的雾沫夹带。 3.漏液的验算
漏液点的气速om u
s m h h C u V L l o /16.7/)13.00056.0(4.40min =-+=ρρσ<11.07m/s
筛板的稳定性系数)5.1(75.1min
00>==
u u K (无漏液)
4.液泛的验算
为防止降液管发生液泛,应使降液管中的清液层高度()w T d h H ΦH +≤
取?=0.5;m h H w T 218.0)(=+?
()w T d h H ΦH +≤成立,故不会产生液泛。
通过流体力学验算,可认为精馏段塔径及塔板各工艺结构尺寸合适,若要做出最合理的设计,还需重选T H 及L h ,进行优化设计。 (八)塔板负荷性能图 1.液沫夹带线(1)
2
.36
5.210
7.5??????-?=
-L T
a
v h H u e σ
(1) 式中:s f
T s a V A A V u 688.0=-=
将已知数据代入式(1)
3
/255.17905.2s
s L u -= (1-1)
在操作范围内,任取几个s L 值,依式(1-1)算出对应的s V 值列于下表:
依据表中数据作出雾沫夹带线(1) 2.液泛线(2)
t t =t t +t 1+t t
H 1=∈0(t t +t tt )=0.0216+0.4584t t 2
3
?
t t =0.00201
t t =0.0236+0.015t t 2+0.4544t t 2
3?
t t =0.153(
t t t t +t 0
)2
3/22223.817.17066976.11Ls Ls Vs --= (2-2)
在操作范围内,任取几个s L 值,依式(2-2)算出对应的s V 值列于下表:
依据表中数据作出液泛线(2) 3.液相负荷上限线(3)
/s m 00847.03max ,==
τ
f
T s A H L (3-3) 4.漏液线(气相负荷下限线)(4)
整理得:
L V
s S 32
2
min
,66.6555.0+= (4-4)
在操作范围内,任取几个s L 值,依式(4-4)算出对应的s V 值列于下表:
依据表中数据作出漏液线(4) 5.液相负荷下限线(5)
取平堰堰上液层高度006.0=ow h m
s m Ls /000716.03min = (5-5)
操作弹性定义为操作线与界限曲线交点的气相最大负荷max ,s V 与气相允许最小负荷
min ,s V 之比,即:
操作弹性=06.38.045
.2min ,max ,==s s V V
三、塔的提馏段操作工艺条件 (五)提馏段的汽液负荷计算
汽相摩尔流率h Kmol F q V V /8.63)1('=--=
汽相体积流量s m M V Vs Vm
Vm
/634.03600'3==
ρ
液相回流摩尔流率h Kmol L L /4.89'==
液相体积流量s m M L Ls Lm
Lm
/0027.03600'3==
ρ
(六)塔和塔板主要工艺结构尺寸的计算 1.塔径
1)初选塔板间距mm 500=T H 及板上液层高度m m 60=L h ,则: 2)按Smith 法求取允许的空塔气速m ax u (即泛点气速F u )
查Smith 通用关联图得09.020=C
负荷因子0902.0)20
18.20(
09.0)20
(
2
.02.020=?==L
C C σ 泛点气速: 3)操作气速
取s m u u /181.1687.17.07.0max =?== 4)精馏段的塔径
圆整取mm 1000=D
塔截面积为222785.0)0.1(4
4
m D A T =?=
=
π
π
此时的操作气速s m u /81.0785
.0634
.0==
。 2.塔板工艺结构尺寸的设计与计算 1)溢流装置
采用单溢流型的平顶弓形溢流堰、弓形降液管、平形受液盘,且不设进口内堰。 ①溢流堰长(出口堰长)w l
取m 7.07.0==D l w ②出口堰高w h
0431.00169.006.0=-=-=ow L w h h h m ③降液管的宽度d W 和降液管的面积f
A
由7.0/=D l w ,查化原下P 147图11-16得09.0/,139.0/==T f d A A D W ,即:
m 139.0=d W ,2065.0m A f =
液体在降液管内的停留时间
s L H A S
T
f 513>==
τ(满足要求) ④降液管的底隙高度o h
液体通过降液管底隙的流速一般为0.07~0.25m/s ,取液体通过降液管底隙的流速
m/s 08.0='o
u ,则有: 故降液管设计合底隙高度设计合理 3)塔板布置
1.塔板分块 因D=1000 故塔板分3块
2.边缘区宽度 m W W s a 065.0'==m W c 035.0= ②开孔区面积a A
式中:()()m 311.0065.01736.07.02/=+-=+-=s d W W D x
3)开孔数n 和开孔率φ
取筛孔的孔径mm 5=o d ,正三角形排列,筛板采用碳钢,其厚度mm 3=δ,且取
0.3/=o d t 。故孔心距mm 1553=?=t 。
每层塔板的开孔数2731155.12
==
t
A n (孔) 每层塔板的开孔率()
101.03907
.0/907.02
2===
o d t φ(φ应在5~15%,故满足要求) 气体通过筛孔的孔速s m A V u s
/81.110
0==
4)精馏段的塔高1Z
(七)塔板上的流体力学验算 1.塔板压降
1)气体通过干板的压降c h
???
? ???
???
??=L V c C u h ρρ2
00051.0 84.0=o C 。 2)气体通过板上液层的压降l h
动能因子)/(61.176.2968.02/10m s Kg F ?== 查化原图得
60.00
=ε
3)气体克服液体表面张力产生的压降σh 4)气体通过筛板的压降(单板压降)p h 和p p Δ
Kpa Kpa gh P P L p 7.0626.0<==?ρ(满足工艺要求)。
2.雾沫夹带量v e 的验算
验算结果表明不会产生过量的雾沫夹带。 3.漏液的验算
漏液点的气速om u
筛板的稳定性系数58.1min
00==
u u K (大于1.5,不会产生过量液漏)
4.液泛的验算
为防止降液管发生液泛,应使降液管中的清液层高度()w T d h H ΦH +≤
()w T d h H ΦH +≤成立,故不会产生液泛。
通过流体力学验算,可认为精馏段塔径及塔板各工艺结构尺寸合适,若要做出最合理的设计,还需重选T H 及L h ,进行优化设计。 (八)塔板负荷性能图 1.雾沫夹带线(1)
2
.365.2107.5??????
-?=-L T
a v h H u e σ (1) 式中:s f
T s a V A A V u 527.1=-=
将已知数据代入式(1)
3
/2672.861.1s
s L V -= (1-1)
在操作范围内,任取几个s L 值,依式(1-1)算出对应的s V 值列于下表:
依据表中数据作出雾沫夹带线(1) 2.液泛线
设备选型-精馏塔设计说明书
第三章设备选型-精馏塔设计说明书3.1 概述 本章是对各种塔设备的设计说明与选型。 3.2设计依据 气液传质分离用的最多的为塔式设备。它分为板式塔和填料塔两大类。板式塔和填料塔均可用作蒸馏、吸收等气液传质过程,但两者各有优缺点,根据具体情况进行选择。设计所依据的规范如下: 《F1型浮阀》JBT1118 《钢制压力容器》GB 150-1998 《钢制塔式容器》JB4710-92 《碳素钢、低合金钢人孔与手孔类型与技术条件》HG21514-95 《钢制压力容器用封头标准》JB/T 4746-2002 《中国地震动参数区划图》GB 18306-2001 《建筑结构荷载规范》GB50009-2001 3.3 塔简述 3.3.1填料塔简述 (1)填料塔
填料塔是以塔内的填料作为气液两相间接触构件的传质设备,由外壳、填料、填料支承、液体分布器、中间支承和再分布器、气体和液体进出口接管等部件组成。 填料是填料塔的核心,它提供了塔内气液两相的接触面,填料与塔的结构决定了塔的性能。填料必须具备较大的比表面,有较高的空隙率、良好的润湿性、耐腐蚀、一定的机械强度、密度小、价格低廉等。常用的填料有拉西环、鲍尔环、弧鞍形和矩鞍形填料,20世纪80年代后开发的新型填料如QH—1型扁环填料、八四内弧环、刺猬形填料、金属板状填料、规整板波纹填料、格栅填料等,为先进的填料塔设计提供了基础。 填料塔适用于快速和瞬间反应的吸收过程,多用于气体的净化。该塔结构简单,易于用耐腐蚀材料制作,气液接触面积大,接触时间长,气量变化时塔的适应性强,塔阻力小,压力损失为300~700Pa,与板式塔相比处理风量小,空塔气速通常为0.5-1.2 m/s,气速过大会形成液泛,喷淋密度6-8 m3/(m2.h)以保证填料润湿,液气比控制在2-10L/m3。填料塔不宜处理含尘量较大的烟气,设计时应克服塔内气液分布不均的问题。 (2)规整填料 塔填料分为散装填料、规整填料(含格栅填料) 和散装填料规整排列3种,前2种填料应用广泛。 在规整填料中,单向斜波填料如JKB,SM,SP等国产波纹填料已达到国外MELLAPAK、FLEXIPAC等同类填料水平;双向斜波填料如ZUPAK、DAPAK 等填料与国外的RASCHIG SUPER-PAK、INTALOX STRUCTURED PACKING 同处国际先进水平;双向曲波填料如CHAOPAK等乃最新自主创新技术,与相应型号的单向斜波填料相比,在分离效率相同的情况下,通量可提高25% -35%,比国外的单向曲波填料MELLAPAK PLUS通量至少提高5%。上述规整填料已成功应用于φ6400,φ8200,φ8400,φ8600,φ8800,φ10200mm等多座大塔中。 (3)板波纹填料 板波纹填料由开孔板组成,材料薄,空隙率大,加之排列规整,因而气体通过能力大,压降小。其比表面积大,能从选材上确保液体在板面上形成稳定薄液
精馏塔设计流程
在一常压操作的连续精馏塔内分离水—乙醇混合物。已知原料的处理量为2000吨、组成为36%(乙醇的质量分率,下同),要求塔顶馏出液的组成为82%,塔底釜液的组成为6%。 设计条件如下: 操作压力 5kPa(塔顶表压); 进料热状况 自选 ; 回流比 自选; 单板压降 ≤; 根据上述工艺条件作出筛板塔的设计计算。 【设计计算】 (一)设计方案的确定 本设计任务为分离水—乙醇混合物。对于二元混合物的分离,应采用连续精馏流程。 设计中采用泡点进料,将原料液通过预料器加热至泡点后送入精馏塔内。塔顶上升蒸气采用全凝器冷凝,冷凝液在泡点下一部分回流至塔内其余部分经产品冷却器冷却后送至储罐。该物系属易分离物系,最小回流比较小,故操作回流比取最小回流比的倍。塔釜采用间接蒸汽加热,塔底产品经冷却后送至储罐。 (二)精馏塔的物料衡算 1. 原料液及塔顶、塔底产品的摩尔分率 乙醇的摩尔质量 A M =46.07kg/kmol 水的摩尔质量 B M =18.02kg/kmol F x =18.002 .1864.007.4636.007 .4636.0=+= D x =64.002.1818.007.4682.007 .4682.0=+= W x =024.002 .1894.007.4606.007 .4606.0=+= 2.原料液及塔顶、塔底产品的平均摩尔质量 F M =×+×=23.07kg/kmol D M =×+×=35.97kg/kmol W M =×+×=18.69kg/kmol 3.物料衡算 以每年工作250天,每天工作12小时计算 原料处理量 F = 90.2812 25007.231000 2000=???kmol/h 总物料衡算 =W D + 水物料衡算 ×=+W
年产5.4万吨丙烯精馏塔的工艺设计
年产5.4万吨丙烯精馏塔 的工艺设计
目录 摘要............................................................. I 第1章绪论.. (2) 1.1丙烯的性质 (2) 1.1.1 丙烯的物理性质 (2) 1.1.2 丙烯的化学性质 (2) 1.2丙烯的发展前景 (2) 1.3丙烯的生产技术进展 (3) 1.3.1 概况 (3) 1.3.2 丙烯的来源 (3) 1.3.3 丙烯的生产方法 (3) 1.3.4 丙烯生产新技术现状及发展趋势 (4) 第2章丙烯精馏塔的物料衡算及热量衡算 (4) 2.2.1 确定关键组分 (5) 2.2.2计算每小时塔顶产量 (5) 2.2.4物料衡算计算结果见表2.5 (7) 2.3塔温的确定 (8) 2.3.1 确定进料温度 (8) 2.3.2 确定塔顶温度 (8) 2.3.3 确定塔釜温度 (8) 第3章精馏塔板数及塔径的计算 (10) 3.1塔板数的计算 (10) 3.1.1 最小回流比的计算 (10) 3.1.2 计算最少理论板数 (11) 3.1.3 塔板数和实际回流比的确定 (11) 3.2确定进料位置 (11) 3.3全塔热量衡算 (12)
3.3.1 冷凝器的热量衡算 (12) 3.3.2 再沸器的热量衡算 (13) 3.3.3 全塔热量衡算 (13) 3.4板间距离的选定和塔径的确定 (14) 3.4.1 计算混合液塔顶、塔釜、进料的密度及气体的密度 (14) 3.4.2 求液体及气体的体积流量 (16) 3.4.3 初选板间距及塔径的估算 (17) 3.5浮阀塔塔板结构尺寸确定 (18) 3.5.1塔板布置 (18) 3.5.2 溢流堰及降液管设计计算 (19) 3.6塔高的计算 (21) 第四章流体力学计算及塔板负荷性能图 (22) 4.1水利学计算 (22) 4.1.1 塔板总压力降的计算 (22) 4.1.2 雾沫夹带 (23) 4.1.3 淹塔情况校核 (26) 4.2浮阀塔的负荷性能图 (27) 4.2.1 雾沫夹带线 (27) 4.2.2 液泛线 (28) 4.2.3 降液管超负荷线 (29) 4.2.4泄露线 (29) 4.2.5 液相下限线 (30) 4.2.6 操作点 (30) 总论 (32) 致谢 (33) 参考文献 (35) 附录 (38)
乙醇——水筛板精馏塔工艺设计-课程设计
学院 化工原理课程设计任务书 专业: 班级: 姓名: 学号: 设计时间: 设计题目:乙醇——水筛板精馏塔工艺设计 (取至南京某厂药用酒精生产现场) 设计条件: 1. 常压操作,P=1 atm(绝压)。 2. 原料来至上游的粗馏塔,为95——96℃的饱和蒸汽。因沿 程热损失,进精馏塔时原料液温度降为90℃。 3. 塔顶产品为浓度92.41%(质量分率)的药用乙醇,产量为 40吨/日。 4.塔釜排出的残液中要求乙醇的浓度不大于0.03%(质量分 率)。 5.塔釜采用饱和水蒸汽加热(加热方式自选);塔顶采用全凝器,泡点回流。 。 6.操作回流比R=(1.1——2.0)R min 设计任务: 1. 完成该精馏塔工艺设计,包括辅助设备及进出口接管的计 算和选型。 2.画出带控制点的工艺流程图,t-x-y相平衡图,塔板负 荷性能图,筛孔布置图以及塔的工艺条件图。 3.写出该精流塔的设计说明书,包括设计结果汇总和对自己 设计的评价。 指导教师:时间
1设计任务 1.1 任务 1.1.1 设计题目乙醇—水筛板精馏塔工艺设计(取至南京某厂药用酒 精生产现场) 1.1.2 设计条件 1.常压操作,P=1 atm(绝压)。 2.原料来至上游的粗馏塔,为95-96℃的饱和蒸气。 因沿程热损失,进精馏塔时原料液温度降为90℃。 3.塔顶产品为浓度92.41%(质量分率)的药用乙醇, 产量为40吨/日。 4.塔釜排出的残液中要求乙醇的浓度不大于0.03% (质量分率)。 5.塔釜采用饱和水蒸气加热(加热方式自选);塔顶 采用全凝器,泡点回流。 6.操作回流比R=(1.1—2.0) R。 min 1.1.3 设计任务 1.完成该精馏塔工艺设计,包括辅助设备及进出口接 管的计算和选型。 2.画出带控制点的工艺流程示意图,t-x-y相平衡 图,塔板负荷性能图,筛孔布置图以及塔的工艺条 件图。 3.写出该精馏塔的设计说明书,包括设计结果汇总 和对自己设计的评价。 1.2 设计方案论证及确定 1.2.1 生产时日 设计要求塔日产40吨92.41%乙醇,工厂实行三班制,每班工作8小时,每天24小时连续正常工作。 1.2.2 选择塔型 精馏塔属气—液传质设备。气—液传质设备主要分为板式塔和填料塔两大类。该塔设计生产时日要求较大,由板式塔与填料塔比较[1]知:板式塔直径放大
分离乙醇水精馏塔设计含经典工艺流程图和塔设备图
分离乙醇-水的精馏塔设计设计人员: 所在班级:化学工程与工艺成绩: 指导老师:日期:
化工原理课程设计任务书 一、设计题目:乙醇---水连续精馏塔的设计 二、设计任务及操作条件 (1)进精馏塔的料液含乙醇35%(质量分数,下同),其余为水; (2)产品的乙醇含量不得低于90%; (3)塔顶易挥发组分回收率为99%; (4)生产能力为50000吨/年90%的乙醇产品; (5)每年按330天计,每天24小时连续运行。 (6)操作条件 a)塔顶压强 4kPa (表压) b)进料热状态自选 c)回流比自选 d)加热蒸汽压力低压蒸汽(或自选) e)单板压降 kPa。 三、设备形式:筛板塔或浮阀塔 四、设计内容:
1、设计说明书的内容 1)精馏塔的物料衡算; 2)塔板数的确定; 3)精馏塔的工艺条件及有关物性数据的计算; 4)精馏塔的塔体工艺尺寸计算; 5)塔板主要工艺尺寸的计算; 6)塔板的流体力学验算; 7)塔板负荷性能图; 8)精馏塔接管尺寸计算; 9)对设计过程的评述和有关问题的讨论; 2、设计图纸要求; 1)绘制生产工艺流程图(A2 号图纸); 2)绘制精馏塔设计条件图(A2 号图纸); 五、设计基础数据: 1.常压下乙醇---水体系的t-x-y 数据; 2.乙醇的密度、粘度、表面张力等物性参数。
一、设计题目:乙醇---水连续精馏塔的设计 二、设计任务及操作条件:进精馏塔的料液含乙醇35%(质量分数,下同),其余为 水;产品的乙醇含量不得低于90%;塔顶易挥发组分回收率为99%,生产能力为50000吨/年90%的乙醇产品;每年按330天计,每天24小时连续运行。塔顶压强 4kPa (表压)进料热状态自选回流比自选加热蒸汽压力低压蒸汽(或自选)单板压降≤0.7kPa。 三、设备形式:筛板塔 四、设计内容: 1)精馏塔的物料衡算: 原料乙醇的组成 xF==0.1740 原料乙醇组成 xD0.7788 塔顶易挥发组分回收率90% 平均摩尔质量 MF = 由于生产能力50000吨/年,. 则 qn,F 所以,qn,D 2)塔板数的确定:
精馏塔工艺工艺设计方案计算
第三章 精馏塔工艺设计计算 塔设备是化工、石油化工、生物化工、制药等生产过程中广泛采用的气液传质设备。根据塔内气液接触构件的结构形式,可分为板式塔和填料塔两大类。 板式塔内设置一定数量的塔板,气体以鼓泡或喷射形势穿过板上的液层,进行传质与传热,在正常操作下,气象为分散相,液相为连续相,气相组成呈阶梯变化,属逐级接触逆流操作过程。 本次设计的萃取剂回收塔为精馏塔,综合考虑生产能力、分离效率、塔压降、操作弹性、结构造价等因素将该精馏塔设计为筛板塔。 3.1 设计依据[6] 3.1.1 板式塔的塔体工艺尺寸计算公式 (1) 塔的有效高度 T T T H E N Z )1( -= (3-1) 式中 Z –––––板式塔的有效高度,m ; N T –––––塔内所需要的理论板层数; E T –––––总板效率; H T –––––塔板间距,m 。 (2) 塔径的计算 u V D S π4= (3-2) 式中 D –––––塔径,m ; V S –––––气体体积流量,m 3/s u –––––空塔气速,m/s u =(0.6~0.8)u max (3-3) V V L C u ρρρ-=max (3-4) 式中 L ρ–––––液相密度,kg/m 3
V ρ–––––气相密度,kg/m 3 C –––––负荷因子,m/s 2 .02020?? ? ??=L C C σ (3-5) 式中 C –––––操作物系的负荷因子,m/s L σ–––––操作物系的液体表面张力,mN/m 3.1.2 板式塔的塔板工艺尺寸计算公式 (1) 溢流装置设计 W OW L h h h += (3-6) 式中 L h –––––板上清液层高度,m ; OW h –––––堰上液层高度,m 。 3 2100084.2??? ? ??=W h OW l L E h (3-7) 式中 h L –––––塔内液体流量,m ; E –––––液流收缩系数,取E=1。 h T f L H A 3600= θ≥3~5 (3-8) 006.00-=W h h (3-9) ' 360000u l L h W h = (3-10) 式中 u 0ˊ–––––液体通过底隙时的流速,m/s 。 (2) 踏板设计 开孔区面积a A : ??? ? ??+-=-r x r x r x A a 1222sin 1802π (3-11)
精馏塔工艺设计
一、苯-氯苯板式精馏塔的工艺设计任务书(一)设计题目 设计一座苯-氯苯连续精馏塔,要求年产纯度为%的苯36432吨,塔底馏出液中含苯1%,原料液中含苯为61%(以上均为质量百分数)。 (二)操作条件 1.塔顶压强4kPa(表压) 2.进料热状况:饱和蒸汽进料 3.回流比:R=2R min 4.单板压降不大于 (三)设计内容 设备形式:筛板塔 设计工作日:每年330天,每天24小时连续运行 厂址:青藏高原大气压约为的远离城市的郊区 设计要求 1.设计方案的确定及流程说明 2.塔的工艺计算 3.塔和塔板主要工艺尺寸的确定 (1)塔高、塔径及塔板结构尺寸的确定 (2)塔板的流体力学验算 (3)塔板的负荷性能图绘制 (4)生产工艺流程图及精馏塔工艺条件图的绘制 4、塔的工艺计算结果汇总一览表 5、对本设计的评述或对有关问题的分析与讨论 (四)基础数据
1.组分的饱和蒸汽压 p(mmHg) i 2.组分的液相密度ρ(kg/m3) 3.组分的表面张力σ(mN/m) 4.液体粘度μ(mPas) 常数
二、苯-氯苯板式精馏塔的工艺计算书(精馏段部分) (一)设计方案的确定及工艺流程的说明 原料液经卧式列管式预热器预热至泡点后送入连续板式精馏塔(筛板塔),塔顶上升蒸汽流采用强制循环式列管全凝器冷凝后一部分作为回流液,其余作为产品经冷却后送至苯液贮罐;塔釜采用热虹吸立式再沸器提供汽相流,塔釜产品经卧式列管式冷却器冷却后送入氯苯贮罐。 典型的连续精馏流程为原料液经预热器加热后到指定的温度后,送入精馏塔的进料板,在进料上与自塔上部下降的回流液体汇合后,逐板溢流,最后流入塔底再沸器中。在每层板上,回流液体与上升蒸气互相接触,进行热和质的传递过程。操作时,连续地从再沸器取出部分液体作为塔底产品(釜残液),部分液体汽化,产生上升蒸气,依次通过各层塔板。塔顶蒸气进入冷凝器中被全部冷凝,并将部分冷凝液用泵送回塔顶作为回流液体,其余部分经冷却器后被送出作为塔顶产品(馏出液)。 (二)全塔的物料衡算 1.料液及塔顶底产品含苯的摩尔分率 苯和氯苯的相对摩尔质量分别为 kg/kmol 和kmol =+= 6 .112/39.011.78/61.011 .78/61.0F x 2.平均摩尔质量 3.料液及塔顶底产品的摩尔流率 依题给条件:一年以330天,一天以24小时计,有: h kmol 62.5824 330989 .010*******=???= D ,
精馏塔的设计(毕业设计)
精馏塔尺寸设计计算 初馏塔的主要任务是分离乙酸和水、醋酸乙烯,釜液回收的乙酸作为气体分离塔吸收液及物料,塔顶醋酸乙烯和水经冷却后进行相分离。塔顶温度为102℃,塔釜温度为117℃,操作压力4kPa。 由于浮阀塔塔板需按一定的中心距开阀孔,阀孔上覆以可以升降的阀片,其结构比泡罩塔简单,而且生产能力大,效率高,弹性大。所以该初馏塔设计为浮阀塔,浮阀选用F1型重阀。在工艺过程中,对初馏塔的处理量要求较大,塔内液体流量大,所以塔板的液流形式选择双流型,以便减少液面落差,改善气液分布状况。 4.2.1 操作理论板数和操作回流比 初馏塔精馏过程计算采用简捷计算法。 (1)最少理论板数N m 系统最少理论板数,即所涉及蒸馏系统(包括塔顶全凝器和塔釜再沸器)在全回流下所需要的全部理论板数,一般按Fenske方程[20]求取。 式中x D,l,x D,h——轻、重关键组分在塔顶馏出物(液相或气相)中的摩尔分数; x W,l,x W,h——轻、重关键组分在塔釜液相中的摩尔分数; αav——轻、重关键组分在塔内的平均相对挥发度; N m——系统最少平衡级(理论板)数。 塔顶和塔釜的相对挥发度分别为αD=1.78,αW=1.84,则精馏段的平均相对挥发度: 由式(4-9)得最少理论板数: 初馏塔塔顶有全凝器与塔釜有再沸器,塔的最少理论板数N m应较小,则最少理论板数:。 (2)最小回流比 最小回流比,即在给定条件下以无穷多的塔板满足分离要求时,所需回流比R m,可用Underwood法计算。此法需先求出一个Underwood参数θ。 求出θ代入式(4-11)即得最小回流比。
式中——进料(包括气、液两相)中i组分的摩尔分数; c——组分个数; αi——i组分的相对挥发度; θ——Underwood参数; ——塔顶馏出物中i组分的摩尔分数。 进料状态为泡点液体进料,即q=1。取塔顶与塔釜温度的加权平均值为进料板温度(即计算温度),则 在进料板温度109.04℃下,取组分B(H2O)为基准组分,则各组分的相对挥发度分别为αAB=2.1,αBB=1,αCB=0.93,所以 利用试差法解得θ=0.9658,并代入式(4-11)得 (3)操作回流比R和操作理论板数N0 操作回流比与操作理论板数的选用取决于操作费用与基建投资的权衡。一般按R/R m=1.2~1.5的关系求出R,再根据Gilliland关联[20]求出N0。 取R/R m=1.2,得R=26.34,则有: 查Gilliland图得 解得操作理论板数N0=51。 4.2.2 实际塔板数 (1)进料板位置的确定 对于泡点进料,可用Kirkbride提出的经验式进行计算。
化工原理课程设计--- 乙醇——水筛板精馏塔工艺设计
化工原理课程设计任务书 专业:班级: 姓名: 学号: 设计时间: 设计题目:乙醇——水筛板精馏塔工艺设计 (取至南京某厂药用酒精生产现场) 设计条件: 1. 常压操作,P=1 atm(绝压)。 2. 原料来至上游的粗馏塔,为95——96℃的饱和蒸汽。因沿 程热损失,进精馏塔时原料液温度降为90℃。 3. 塔顶产品为浓度92.41%(质量分率)的药用乙醇,产量为 40吨/日。 4.塔釜排出的残液中要求乙醇的浓度不大于0.03%(质量分 率)。 5.塔釜采用饱和水蒸汽加热(加热方式自选);塔顶采用全凝器,泡点回流。 。 6.操作回流比R=(1.1——2.0)R min 设计任务: 1. 完成该精馏塔工艺设计,包括辅助设备及进出口接管的计 算和选型。 2.画出带控制点的工艺流程图,t-x-y相平衡图,塔板负 荷性能图,筛孔布置图以及塔的工艺条件图。 3.写出该精流塔的设计说明书,包括设计结果汇总和对自己 设计的评价。 指导教师:时间 1设计任务
1.1 任务 1.1.1 设计题目乙醇—水筛板精馏塔工艺设计(取至南京某厂药用酒 精生产现场) 1.1.2 设计条件 1.常压操作,P=1 atm(绝压)。 2.原料来至上游的粗馏塔,为95-96℃的饱和蒸气。 因沿程热损失,进精馏塔时原料液温度降为90℃。 3.塔顶产品为浓度92.41%(质量分率)的药用乙醇, 产量为40吨/日。 4.塔釜排出的残液中要求乙醇的浓度不大于0.03% (质量分率)。 5.塔釜采用饱和水蒸气加热(加热方式自选);塔顶 采用全凝器,泡点回流。 6.操作回流比R=(1.1—2.0) R。 min 1.1.3 设计任务 1.完成该精馏塔工艺设计,包括辅助设备及进出口接 管的计算和选型。 2.画出带控制点的工艺流程示意图,t-x-y相平衡 图,塔板负荷性能图,筛孔布置图以及塔的工艺条 件图。 3.写出该精馏塔的设计说明书,包括设计结果汇总 和对自己设计的评价。 1.2 设计方案论证及确定 1.2.1 生产时日 设计要求塔日产40吨92.41%乙醇,工厂实行三班制,每班工作8小时,每天24小时连续正常工作。 1.2.2 选择塔型 精馏塔属气—液传质设备。气—液传质设备主要分为板式塔和填料塔两大类。该塔设计生产时日要求较大,由板式塔与填料塔比较[1]知:板式塔直径放大时,塔板效率较稳定,且持液量较大,液气比适应范围大,因此本次精馏塔设备选择板式塔。筛板塔是降液管塔板中结构最简单的,它与泡罩塔相比较具有下列优点:生产能力大10-15%,板效率提高15%左右,而压降可降低30%左右,另外筛板塔结构简单,消耗金属少,塔板的造价可减少40%左右,安装容易,也便于
分离乙醇水精馏塔设计(含经典实用工艺流程图和塔设备图).doc
分离乙醇-水的精馏塔设计 设计人员: 所在班级:化学工程与工艺成绩: 指导老师:日期:
化工原理课程设计任务书 一、设计题目:乙醇---水连续精馏塔的设计 二、设计任务及操作条件 (1)进精馏塔的料液含乙醇35%(质量分数,下同),其余为水; (2)产品的乙醇含量不得低于90%; (3)塔顶易挥发组分回收率为99%; (4)生产能力为50000吨/年90%的乙醇产品; (5)每年按330天计,每天24小时连续运行。 (6)操作条件 a)塔顶压强 4kPa (表压) b)进料热状态自选 c)回流比自选 d)加热蒸汽压力低压蒸汽(或自选) e)单板压降 kPa。 三、设备形式:筛板塔或浮阀塔 四、设计内容: 1、设计说明书的内容 1)精馏塔的物料衡算; 2)塔板数的确定; 3)精馏塔的工艺条件及有关物性数据的计算; 4)精馏塔的塔体工艺尺寸计算;
5)塔板主要工艺尺寸的计算; 6)塔板的流体力学验算; 7)塔板负荷性能图; 8)精馏塔接管尺寸计算; 9)对设计过程的评述和有关问题的讨论; 2、设计图纸要求; 1)绘制生产工艺流程图(A2 号图纸); 2)绘制精馏塔设计条件图(A2 号图纸); 五、设计基础数据: 1.常压下乙醇---水体系的t-x-y 数据; 2.乙醇的密度、粘度、表面张力等物性参数。 一、设计题目:乙醇---水连续精馏塔的设计 二、设计任务及操作条件:进精馏塔的料液含乙醇35%(质量分 数,下同),其余为水;产品的乙醇含量不得低于90%;塔 顶易挥发组分回收率为99%,生产能力为50000吨/年90% 的乙醇产品;每年按330天计,每天24小时连续运行。塔顶 压强 4kPa (表压)进料热状态自选回流比自选加热蒸汽 压力低压蒸汽(或自选)单板压降≤0.7kPa。 三、设备形式:筛板塔 四、设计内容: 1)精馏塔的物料衡算: 原料乙醇的组成 xF==0.1740
精馏塔工艺设计
一、苯-氯苯板式精馏塔的工艺设计任务书 (一)设计题目 设计一座苯-氯苯连续精馏塔,要求年产纯度为98.5%的苯36432吨,塔底馏出液中含苯1%,原料液中含苯为61%(以上均为质量百分数)。 (二)操作条件 1.塔顶压强4kPa(表压) 2.进料热状况:饱和蒸汽进料 3.回流比:R=2R 4.单板压降不大于0.7kPa min (三)设计内容 设备形式:筛板塔 设计工作日:每年330天,每天24小时连续运行 厂址:青藏高原大气压约为77.31kpa的远离城市的郊区 设计要求 1.设计方案的确定及流程说明 2.塔的工艺计算 3.塔和塔板主要工艺尺寸的确定 (1)塔高、塔径及塔板结构尺寸的确定 (2)塔板的流体力学验算 (3)塔板的负荷性能图绘制 (4)生产工艺流程图及精馏塔工艺条件图的绘制 4、塔的工艺计算结果汇总一览表 5、对本设计的评述或对有关问题的分析与讨论 (四)基础数据
1.组分的饱和蒸汽压 i p (mmHg ) 2.组分的液相密度ρ(kg/m 3 ) 3.组分的表面张力σ(mN/m ) 4.液体粘度μ(mPa ?s )
5.Antoine常数 二、苯-氯苯板式精馏塔的工艺计算书(精馏段部分) (一)设计方案的确定及工艺流程的说明 原料液经卧式列管式预热器预热至泡点后送入连续板式精馏塔(筛板塔),塔顶上升蒸汽流采用强制循环式列管全凝器冷凝后一部分作为回流液,其余作为产品经冷却后送至苯液贮罐;塔釜采用热虹吸立式再沸器提供汽相流,塔釜产品经卧式列管式冷却器冷却后送入氯苯贮罐。 典型的连续精馏流程为原料液经预热器加热后到指定的温度后,送入精馏塔的进料板,在进料上与自塔上部下降的回流液体汇合后,逐板溢流,最后流入塔底再沸器中。在每层板上,回流液体与上升蒸气互相接触,进行热和质的传递过程。操作时,连续地从再沸器取出部分液体作为塔底产品(釜残液),部分液体汽化,产生上升蒸气,依次通过各层塔板。塔顶蒸气进入冷凝器中被全部冷凝,并将部分冷凝液用泵送回塔顶作为回流液体,其余部分经冷却器后被送出作为塔顶产品(馏出液)。 (二)全塔的物料衡算 1.料液及塔顶底产品含苯的摩尔分率 苯和氯苯的相对摩尔质量分别为78.11 kg/kmol和112.6kg/kmol
精馏塔设计图(参考版)
仅供参考 ∠1∶10 设计数量 职务姓名日期制图校核审核审定批准 比例 图幅 1∶20 A1 版次 设计项目设计阶段 毕业设计施工图 精馏塔 重量(Kg) 单件总重备注 件号 图号或标准号 名称 材料12345基础环 筋板盖板垫板静电接地板14824241Q235-A Q235-A Q235-A Q235-A Q235-A Q235-A Q235-A Q235-A Q235-A Q235-A Q235-A Q235-A·F 16MnR Q235-A 6 789 10 111213 14151617JB4710-92 GB/T3092-93HG20594-97JB4710-92GB/T3092-93HG20594-97JB4710-92 GB/T3092-93HG20594-97HG5-1373-80引出孔 φ159×4.5引出管 DN40法兰 PN1.0,DN40排气管 φ80接管 DN20,L=250法兰 PN1.0,DN20液封盘 塔釜隔板筒体 φ1600×16进料管 DN32法兰 PN1.0,DN32吊柱 111411111111 6.723.931.55322.7 94.2374.19140.62.97 5.382.364.67 1.170.411.0321.9376181210.69 2.02380Q235-A·F Q235-A 1111111311177511组合件16MnR Q235-A Q235-A Q235-A Q235-A Q235-A Q235-A 45Q235-A·F Q235-A Q235-A Q235-A Q235-A 组合件Q235-A 111111224Q235-A 16MnR Q235-A Q235-A Q235-A Q235-A Q235-A 1819202122232425 2627282930313233343536 3738394041 扁钢 8×16HG20594-97HG20594-97HG20594-97HG20594-97GB/T3092-93GB/T3092-93GB/T3092-93HG8162-87JB/T4737-95HG20594-97HG20594-97GB/T3092-93GB/T3092-93GB/T3092-93JB/T4736-95HG21515-95HJ97403224-3HJ97403224-7JB/T4734-95JB4710-92JB4710-921Q235-A HG20652-1998JB/ZQ4363-86上封头DN1600×16接管 DN20,L=250法兰 PN1.0,DN20出气管 DN600法兰 PN1.0,DN600接管 DN20,L=250法兰 PN1.0,DN20气体出口挡板回流管 DN45法兰 PN1.0,DN45补强圈 DN450×8人孔 DN450塔盘接管 DN20,L=250法兰 PN1.0,DN20下封头DN1600×16裙座筒体 法兰 PN1.0,DN20引出管 DN20引出孔 φ133×4检查孔 排净孔地脚螺栓M42×4.5GB704-88370.70.411.0382.3248.10.411.031.874.150.962.36118.3 310.10.411.03370.738021.032.612.2442.540.6 16.944.3δ=8 1 40 6 23 45 41 39 38 37789 10 1112 3635 34 33 3213 14 31 15 1630 2917 28 2726 25 24 2318 19 202122 a b c d e f i g h j1 k l n m5 m7 Ⅵ Ⅴ Ⅳ Ⅲ Ⅱ Ⅰ 技术要求 1、本设备按GB150-1998《钢制压力容器》和HG20652-95《钢制化工容器制造技术要求》进行 制造、试验和验收,并接受劳动部颁发《压力容器安全技术监察规程》的监督;2、焊条采用电弧焊,焊条牌号E4301; 3、焊接接头型式及尺寸,除图中标明外,按HG20583-1998规定,角焊缝的焊接尺寸按较薄板 厚度,法兰焊接按相应法兰中的规定; 4、容器上A、B类焊缝采用探伤检查,探伤长度20%; 5、设备制造完毕后,卧立以0.2MPa进行水压试验; 6、塔体直线允许度误差是H/1000,每米不得超过3mm,塔体安装垂直度允差是最大30mm; 7、裙座螺栓孔中心圆直径允差以及相邻两孔或任意两弦长允差为2mm; 8、塔盘制造安装按JB1205《塔盘技术条件》进行; 9、管口及支座方位见接管方位图。 技术特性表 管口表 总质量:27685 Kg e m1-7a f i g h j2n j4 l j3 k j1 b c d j3 序号 项 目指 标11 109 87654 3 21设计压力 MPa 设计温度 ℃工作压力 MPa 工作温度 ℃工作介质主要受压元件许用应力 MPa 焊缝接头系数腐蚀裕量 mm 全容积 m 容器类别 0.11500.027102 筒体、封头、法兰1700.58157.9327符号公称尺寸连接尺寸标准紧密面 型式用途或名称b c d e f g h i j1-4k l m1-7n 2060020453220202020402045040 HG20594-97HG20594-97HG20594-97HG20594-97HG20594-97HG20594-97HG20594-97HG20594-97HG20594-97HG20594-97HG20594-97HG20594-97 HG21515-95凹凹凹凹凹凹凹凹凹凹凹凹凹 温度计口气相出口压力计口回流口进料口液面计口液面计口温度计口排气管口至再沸器口出料口人孔再沸器返回口 313028263335373929 2732 3436 38404142 43 444546 474849 505125 24 2322 21201918 1716 151******** 8 7654 32114m6 m7 m5 m4 m3 m2 m1 1 2 3 4 5 30 31 32 33 3435 5051管口方位示意图 A、B类焊缝 1:2 整体示意图1:2 Ⅵ Ⅴ 1:5 1:5 Ⅳ A B B向 A向 Ⅲ 1:5 Ⅱ 1:5 Ⅰ 1:10 平台一 平台二 357 2901
板式精馏塔设计方案
板式精馏塔设计方案 一、设计方案确定 1.1 精馏流程 精馏装置包括精馏塔,原料预热器,再沸器,冷凝器,釜液冷却器和产品冷却器等,为保持塔的操作稳定性,流程中用泵直接送入塔原料,乙醇、水混合原料液经预热器加热至泡点后,送入精馏塔。塔顶上升蒸汽采用全凝器冷凝后经分配器一部分回流,一部分经过冷却器后送入产品储槽,塔釜采用间接蒸汽再沸器供热,塔底产品经冷却后为冷却水循环利用。 塔板是板式塔的主要构件,分为错流式塔板和逆流式塔板两类,工业中以错流式为主,常用的错流式塔板有:泡罩塔板,筛孔塔板,浮阀塔板。泡罩塔板是工业上应用最早的塔板,其主要的优点是操作弹性较大,液气比围较大,不易堵塞;但由于生产能力及板效率底,已逐渐被筛孔塔板和浮阀塔板所替代。筛孔塔板优点是结构简单,造价低,板上液面落差小,气体压强底,生产能力大;其缺点是筛孔易堵塞,易产生漏液,导致操作弹性减小,传质效率下降。而浮阀塔板是在泡罩塔板和筛孔塔板的基础上发展起来的,它吸收了前述两种塔板的优点。浮阀塔板结构简单,制造方便,造价底;塔板开孔率大,故生产能力大;由于阀片可随气量变化自由升降,故操作弹性大;因上升气流水平吹入液层,气液接触时间长,故塔板效率较高。但浮阀塔板也有缺点,即不易处理易结焦、高粘度的物料,而设计的原料是乙醇-水溶液,不属于此类。故总结上述,设计时选择的是浮阀塔板。 1.2设计方案论证及确定 1.2.1 生产时日及处理量的选择:设计要求塔年处理11.5万吨乙醇—水溶液系统,年工作日300d,每天工作24h。 1.2.2 选择用板式塔不用填料塔的原因:因为精馏塔精馏塔对塔设备的要求大致如下: (1)生产能力大:即单位塔截面大的气液相流率,不会产生液泛等不正常流动。
筛板精馏塔课程设计心得体会
竭诚为您提供优质文档/双击可除筛板精馏塔课程设计心得体会 篇一:化工原理课程设计筛板精馏塔的设计 化工原理课程设计任务书 班级:生工081 姓名:丁尚080811110183 陈国钰080811110184 设计题目:乙醇水溶液筛板精馏塔的工艺设计一.基础数据 1.原料液量:8000kg·h-1 2.原料液组成:乙醇:22.6%,水:77.4% 3.原料液温度:25℃ 4.馏出液组成:乙醇含量大于:93.2%釜液组成:乙醇含量小于:1.1% (以上浓度均指质量分率) 5.操作压力:常压二.设计范围 1.精馏系统工艺流程设计,绘流程图一张 2.筛板精馏塔的工艺计算
3.筛板精馏塔塔板结构的工艺设计,绘制塔板负荷性能图,塔板结构图和整体设备结构图 4.附属设备选型计算20XX.7.8 目录 第一章:概述 (2) 第二章:精馏工艺流程确定 (4) 第三章:精馏塔的物料衡算 (5) 10) 第五章:塔板结构的工艺设计 (19) 第六章:塔板流体力学校核 (29) 第七章:塔板负荷性能图 (33) 第八章:塔的总体结构的确定 (39) 第九章:馏塔附属设备选型计算 (46) 参考文
献 (51) 附录 (52) 第一章概述 塔设备是化工,石油化工和炼油等生产中最重要的设备之一。它可使气液或液液两相之间进行紧密接触,达到相际传质及传热的目的。它是实现精馏,吸收,解吸和萃取等化工单元操作的主要设备。塔设备在化工过程中有时也用来实现工业气体的冷却与回收,气体的湿法净制和干燥,以及兼有气液两相传质和传热的增湿,减湿等。 在板式塔中,塔内装有一定数量的塔盘,气体以鼓泡或喷射的形式穿过塔板上的液层使两相密切接触,进行传质,两相的组分浓度沿塔高呈阶梯式变化。在填料塔中,塔内装填一定段数和一定高度的填料层,液体沿填料表面成膜状向下流动,作为连续相的液体自下向上流动,与液体逆流传质。两相的组分浓度沿塔高呈阶梯式变化。 不管是何种塔型,除了首先要能使气(汽)液两相充分接触,获得较高的传热效率外,还希望能综合满足下列要求: (1)生产能力大。在较大的气(汽)液流速下,仍不致发生大量的物沫夹带及液泛等破坏正常操作的现象。 (2)操作稳定,操作弹性大。当塔设备的气(汽)液负
精馏塔的设计详解-共21页
目录 一.前言 (3) 二.塔设备任务书 (4) 三.塔设备已知条件 (5) 四.塔设备设计计算 (6) 1、选择塔体和裙座的材料 (6) 2、塔体和封头壁厚的计算 (6) 3、设备质量载荷计算 (7) 4、风载荷与风弯距计算 (9) 5、地震载荷与地震弯距计算 (12) 6、偏心载荷与偏心弯距计算 (13) 7、最大弯距计算 (14) 8、塔体危险截面强度和稳定性校核 (14) 9、裙座强度和稳定性校核 (16) 10、塔设备压力试验时的应力校核 (18) 11、基础环设计 (18) 12、地脚螺栓设计 (19) 五.塔设备结构设计 (20) 六.参考文献 (21) 七.结束语 (21)
前言 苯(C6H6)在常温下为一种无色、有甜味的透明液体,并具有强烈的芳香气味。苯可燃,有毒,也是一种致癌物质。它难溶于水,易溶于有机溶剂,本身也可作为有机溶剂。苯具有的环系叫苯环,是最简单的芳环。苯分子去掉一个氢以后的结构叫苯基,用Ph表示。因此苯也可表示为PhH。苯是一种石油化工基本原料。苯的产量和生产的技术水平是一个国家石油化工发展水平的标志之一。 甲苯是有机化合物,属芳香烃,分子式为C6H5CH3。在常温下呈液体状,无色、易燃。它的沸点为110.8℃,凝固点为-95℃,密度为0.866克/厘米3。甲苯不溶于水,但溶于乙醇和苯的溶剂中。甲苯容易发生氯化,生成苯—氯甲烷或苯三氯甲烷,它们都是工业上很好的溶剂;它还容易硝化,生成对硝基甲苯或邻硝基甲苯,它们都是染料的原料;它还容易磺化,生成邻甲苯磺酸或对甲苯磺酸,它们是做染料或制糖精的原料。甲苯的蒸汽与空气混合形成爆炸性物质,因此它可以制造梯思梯炸药。甲苯与苯的性质很相似,是工业上应用很广的原料。但其蒸汽有毒,可以通过呼吸道对人体造成危害,使用和生产时要防止它进入呼吸器官。 苯和甲苯都是重要的基本有机化工原料。工业上常用精馏方法将他们分离。精馏是分离液体混合物最早实现工业化的典型单元操作,广泛应用于化工,石油,医药,冶金及环境保护等领域。它是通过加热造成汽液两相体系,利用混合物中各组分挥发度的差别实现组分的分离与提纯的目的。 实现精馏操作的主要设备是精馏塔。精馏塔主要有板式塔和填料塔。板式塔的核心部件为塔板,其功能是使气液两相保持密切而又充分的接触。塔板的结构主要由气体通道、溢流堰和降液管。本设计主要是对板式塔的设计。
精馏塔工艺设计
一、苯-氯苯板式精馅塔的工艺设计任务书 (一)设计题目 设计一座苯-氯苯连续精饰塔,要求年产纯度为%的苯36432吨,塔底镭出液中含苯1%,原料液中含苯为61% (以上均为质量百分数)。 (二)操作条件 1?塔顶压强4kPa (表压)2.进料热状况:饱和蒸汽进料 3.回流比:R=2R ttia 4.单板压降不大于 (三)设计内容 设备形式:筛板塔 设计工作日:每年330天,每天24小时连续运行 厂址:青藏高原大气压约为的远离城市的郊区 设计要求 1.设计方案的确定及流程说明 2.塔的工艺计算 3.塔和塔板主要工艺尺寸的确定 (1)塔高、塔径及塔板结构尺寸的确定 (2)塔板的流体力学验算 (3)塔板的负荷性能图绘制 (4)生产工艺流程图及精懈塔工艺条件图的绘制 4.塔的工艺计算结果汇总一览表
5.对本设计的评述或对有关问题的分析与讨论(四)基础数据
1.组分的饱和蒸汽压p; (mmHg) 2?组分的液相密度卩(kg/m5) 3.组分的表面张力er (mN/m) 4?液体粘度U (mPas) 常数
二、苯-氯苯板式精憎塔的工艺计算书(精馆段部分) (一)设计方案的确定及工艺流程的说明 原料液经卧式列管式预热器预热至泡点后送入连续板式精饰塔(筛板塔),塔顶上升蒸汽流采用强制循环式列管全凝器冷凝后一部分作为回流液,其余作为产品经冷却后送至苯液贮罐;塔釜采用热虹吸立式再沸器提供汽相流,塔釜产品经卧式列管式冷却器冷却后送入氯苯贮罐。 典型的连续精饰流程为原料液经预热器加热后到指定的温度后,送入精懈塔的进料板,在进料上与自塔上部下降的回流液体汇合后,逐板溢流,最后流入塔底再沸器中。在每层板上,回流液体与上升蒸气互相接触,进行热和质的传递过程。操作时,连续地从再沸器取出部分液体作为塔底产品(釜残液),部分液体汽化,产生上升蒸气,依次通过各层塔板。塔顶蒸气进入冷凝器中被全部冷凝,并将部分冷凝液用泵送回塔顶作为回流液体,其余部分经冷却器后被送出作为塔顶产品(饰出液)。 (二)全塔的物料衡算 1.料液及塔顶底产品含苯的摩尔分率 苯和氯苯的相对摩尔质量分别为kg/kmol和kmol 0. 61/78. 11 x P = --------------------------------------- = 0.61/78. 11 + 0. 39/112.6 2.平均摩尔质量 3.料液及塔顶底产品的縻尔流率 依题给条件:一年以330天,一天以24小时计,有:
精馏塔计算方法
目录 1 设计任务书 (1) 1.1 设计题目……………………………………………………………………………………………………………………………………………………………………… 1.2 已知条件……………………………………………………………………………………………………………………………………………………………………… 1.3设计要求………………………………………………………………………………………………………………………………………………………………………… 2 精馏设计方案选定 (1) 2.1 精馏方式选择………………………………………………………………………………………………………………………………………………………………… 2.2 操作压力的选择………………………………………………………………………………………………………………………………………………………………… 2.4 加料方式和加热状态的选择…………………………………………………………………………………………………………………………………………………… 2.3 塔板形式的选择………………………………………………………………………………………………………………………………………………………………… 2.5 再沸器、冷凝器等附属设备的安排…………………………………………………………………………………………………………………………………………… 2.6 精馏流程示意图………………………………………………………………………………………………………………………………………………………………… 3 精馏塔工艺计算 (2) 3.1 物料衡算………………………………………………………………………………………………………………………………………………………………………… 3.2 精馏工艺条件计算……………………………………………………………………………………………………………………………………………………………… 3.3热量衡算………………………………………………………………………………………………………………………………………………………………………… 4 塔板工艺尺寸设计 (4) 4.1 设计板参数………………………………………………………………………………………………………………………………………………………………………