大型引风机叶轮的动平衡问题及对策
引风机的振动故障分析及处理
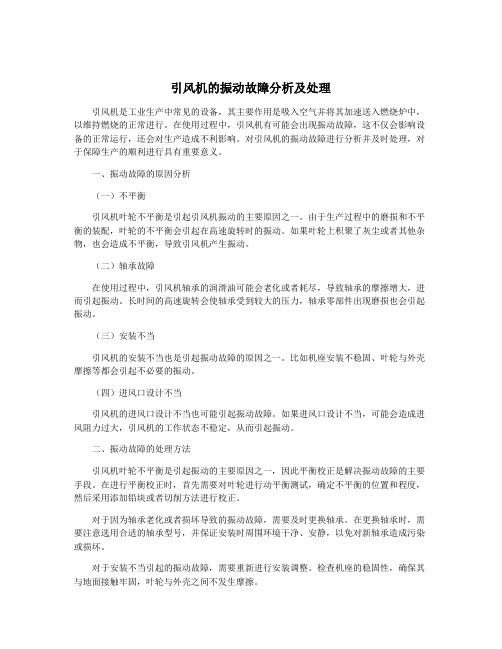
引风机的振动故障分析及处理引风机是工业生产中常见的设备,其主要作用是吸入空气并将其加速送入燃烧炉中,以维持燃烧的正常进行。
在使用过程中,引风机有可能会出现振动故障,这不仅会影响设备的正常运行,还会对生产造成不利影响。
对引风机的振动故障进行分析并及时处理,对于保障生产的顺利进行具有重要意义。
一、振动故障的原因分析(一)不平衡引风机叶轮不平衡是引起引风机振动的主要原因之一。
由于生产过程中的磨损和不平衡的装配,叶轮的不平衡会引起在高速旋转时的振动。
如果叶轮上积聚了灰尘或者其他杂物,也会造成不平衡,导致引风机产生振动。
(二)轴承故障在使用过程中,引风机轴承的润滑油可能会老化或者耗尽,导致轴承的摩擦增大,进而引起振动。
长时间的高速旋转会使轴承受到较大的压力,轴承零部件出现磨损也会引起振动。
(三)安装不当引风机的安装不当也是引起振动故障的原因之一。
比如机座安装不稳固、叶轮与外壳摩擦等都会引起不必要的振动。
(四)进风口设计不当引风机的进风口设计不当也可能引起振动故障。
如果进风口设计不当,可能会造成进风阻力过大,引风机的工作状态不稳定,从而引起振动。
二、振动故障的处理方法引风机叶轮不平衡是引起振动的主要原因之一,因此平衡校正是解决振动故障的主要手段。
在进行平衡校正时,首先需要对叶轮进行动平衡测试,确定不平衡的位置和程度,然后采用添加铅块或者切削方法进行校正。
对于因为轴承老化或者损坏导致的振动故障,需要及时更换轴承。
在更换轴承时,需要注意选用合适的轴承型号,并保证安装时周围环境干净、安静,以免对新轴承造成污染或损坏。
对于安装不当引起的振动故障,需要重新进行安装调整。
检查机座的稳固性,确保其与地面接触牢固,叶轮与外壳之间不发生摩擦。
三、振动故障的预防措施(一)定期检查为了及时发现引风机的振动故障,经常性的定期检查是很有必要的。
通过定期检查可以发现引风机的潜在问题,及时进行处理,避免振动故障对生产造成不利影响。
(二)保持清洁定期清洁引风机的叶轮和轴承是预防振动故障的有效手段。
大型火电厂风机质量不平衡故障分析及处理
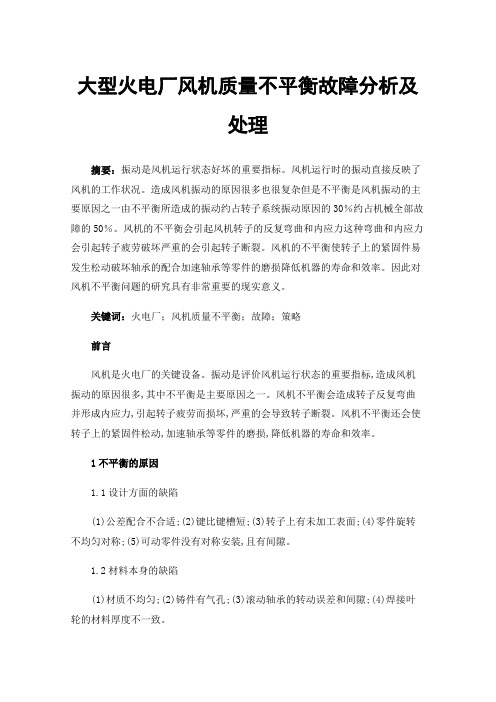
大型火电厂风机质量不平衡故障分析及处理摘要:振动是风机运行状态好坏的重要指标。
风机运行时的振动直接反映了风机的工作状况。
造成风机振动的原因很多也很复杂但是不平衡是风机振动的主要原因之一由不平衡所造成的振动约占转子系统振动原因的30%约占机械全部故障的50%。
风机的不平衡会引起风机转子的反复弯曲和内应力这种弯曲和内应力会引起转子疲劳破坏严重的会引起转子断裂。
风机的不平衡使转子上的紧固件易发生松动破坏轴承的配合加速轴承等零件的磨损降低机器的寿命和效率。
因此对风机不平衡问题的研究具有非常重要的现实意义。
关键词:火电厂;风机质量不平衡;故障;策略前言风机是火电厂的关键设备。
振动是评价风机运行状态的重要指标,造成风机振动的原因很多,其中不平衡是主要原因之一。
风机不平衡会造成转子反复弯曲并形成内应力,引起转子疲劳而损坏,严重的会导致转子断裂。
风机不平衡还会使转子上的紧固件松动,加速轴承等零件的磨损,降低机器的寿命和效率。
1不平衡的原因1.1设计方面的缺陷(1)公差配合不合适;(2)键比键槽短;(3)转子上有未加工表面;(4)零件旋转不均匀对称;(5)可动零件没有对称安装,且有间隙。
1.2材料本身的缺陷(1)材质不均匀;(2)铸件有气孔;(3)滚动轴承的转动误差和间隙;(4)焊接叶轮的材料厚度不一致。
1.3加工与装配方面的缺陷(1)切削加工造成的误差;(2)加工产生的永久变形;(3)焊接和浇铸产生的缺陷;(4)零件装配尺寸不合格;(5)固定螺钉拧紧程度不均匀造成挠曲。
2不平衡的特征2.1频率特征在频谱图中,谐波能量集中于基频,二倍频、三倍频较小,甚至没有,这是与基础松动的重要区别。
2.2幅值特征随着运行时间的增加,叶轮磨损不断加大,且因磨损的不均匀,致使不平衡量逐渐增大,风机振动的幅值随时间递增。
有的风机为了防磨,在叶片上粘贴或焊有防磨层。
由于粘贴或焊接不牢,在风机启停过程中,有可能造成防磨层成块脱落,打破风机原有平衡,致使振动幅值陡然增大。
引风机的振动故障分析及处理
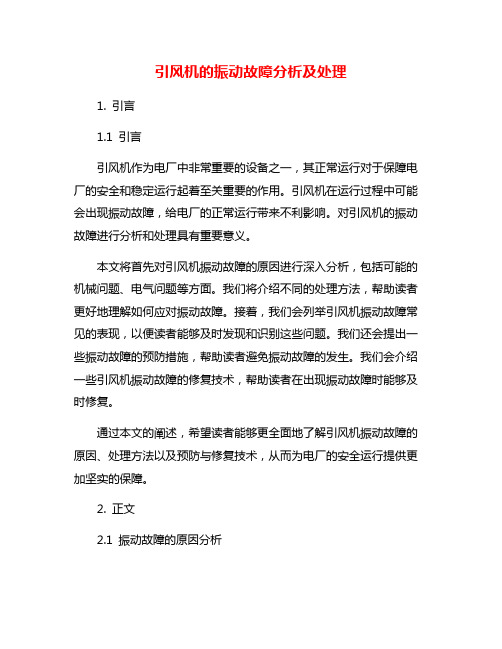
引风机的振动故障分析及处理1. 引言1.1 引言引风机作为电厂中非常重要的设备之一,其正常运行对于保障电厂的安全和稳定运行起着至关重要的作用。
引风机在运行过程中可能会出现振动故障,给电厂的正常运行带来不利影响。
对引风机的振动故障进行分析和处理具有重要意义。
本文将首先对引风机振动故障的原因进行深入分析,包括可能的机械问题、电气问题等方面。
我们将介绍不同的处理方法,帮助读者更好地理解如何应对振动故障。
接着,我们会列举引风机振动故障常见的表现,以便读者能够及时发现和识别这些问题。
我们还会提出一些振动故障的预防措施,帮助读者避免振动故障的发生。
我们会介绍一些引风机振动故障的修复技术,帮助读者在出现振动故障时能够及时修复。
通过本文的阐述,希望读者能够更全面地了解引风机振动故障的原因、处理方法以及预防与修复技术,从而为电厂的安全运行提供更加坚实的保障。
2. 正文2.1 振动故障的原因分析1. 设备不平衡: 引风机如果在运转过程中出现不平衡的情况,会导致振动增大,进而引起振动故障。
设备不平衡的原因可能是安装不当、零部件损坏或磨损等。
2. 轴承故障: 轴承是引风机重要的零部件,如果轴承损坏或磨损严重,会导致引风机的振动增大。
轴承故障可能是因为润滑不良、使用时间过长或维护不当等原因造成的。
3. 转子失衡: 引风机转子失衡会导致设备振动,转子失衡的原因可能是设备设计缺陷、制造质量不过关或使用条件恶劣等。
4. 风叶损坏: 引风机风叶损坏会导致不均匀的气流通过,在高速运转时可能会产生振动。
风叶损坏的原因可能是使用过程中的磨损、腐蚀或碰撞等。
5. 安装松动: 引风机在运行过程中,如果有安装的螺栓松动或固定件松动,会导致设备振动。
定期检查设备安装状态十分重要。
以上是引风机振动故障的原因分析,只有找准问题的根源,才能有针对性地制定解决方案。
在实际运行中,需要密切关注设备运行情况,及时发现问题并采取有效的措施进行处理,以避免产生严重的事故。
风机运行中常见故障及处理措施分析

风机运行中常见故障及处理措施分析风机是一种常见的工业设备,广泛应用于化工、建筑、矿山等领域。
在风机运行过程中,常常会出现一些故障,影响设备的正常运行。
本文将针对风机运行中常见的故障进行分析,并提出相应的处理措施,以帮助读者更好地了解风机设备的运行情况,并及时解决常见故障,保障设备的正常运转。
1. 叶轮受损叶轮是风机的关键部件,负责产生风力。
在风机运行中,叶轮受损是比较常见的故障之一。
叶轮的损坏可能是由于长时间使用导致磨损、受到外部冲击或者材料质量问题等因素所造成的。
处理措施:一旦发现叶轮受损,应立即停止使用风机,并对叶轮进行更换或修复。
定期对叶轮进行检查和维护,以延长叶轮的使用寿命。
2. 风机噪音过大风机运行时出现异常噪音,可能是由于叶轮不平衡、轴承磨损、电机故障等原因所引起的。
处理措施:首先需排除外部杂音的干扰,确认噪音是否来自风机本身。
然后对风机进行逐一检查,发现问题及时进行维修或更换有问题的零部件。
定期对风机进行维护保养,减少噪音产生的可能性。
3. 电机发热风机的电机在长时间运行后会发生发热现象,造成设备损坏的风险。
处理措施:检查电机的通风系统是否正常,通风不良是导致电机发热的主要原因之一。
在使用过程中要注意电机的负载情况,避免超负荷运行。
当发现电机发热时,应及时停机进行散热,排除故障点并及时维修。
4. 风机效率下降风机长时间运行或者受到外部环境影响,可能会导致风机效率下降,影响设备的正常运行。
处理措施:定期对风机进行检修,清洗叶片和进气口,及时更换滤网,保证风机的通风效果。
注意避免风机过载运行,降低风机的负荷,有助于提高风机的工作效率。
处理措施:首先排除外部因素对风机振动的影响,然后检查风机本身的问题。
如发现叶轮不平衡,可采取平衡处理措施;如底座不牢固,可加固风机底座。
定期对风机进行动平衡调整,是减小振动的有效手段。
解决风机叶轮不平衡的方法
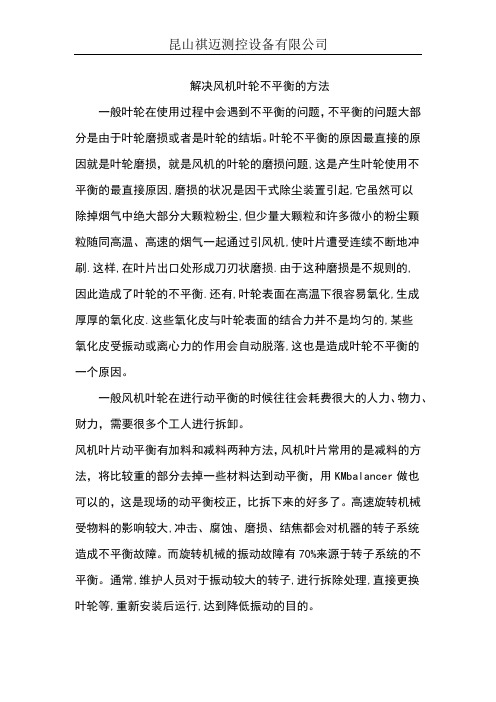
解决风机叶轮不平衡的方法
一般叶轮在使用过程中会遇到不平衡的问题,不平衡的问题大部分是由于叶轮磨损或者是叶轮的结垢。
叶轮不平衡的原因最直接的原因就是叶轮磨损,就是风机的叶轮的磨损问题,这是产生叶轮使用不
平衡的最直接原因,磨损的状况是因干式除尘装置引起,它虽然可以
除掉烟气中绝大部分大颗粒粉尘,但少量大颗粒和许多微小的粉尘颗
粒随同高温、高速的烟气一起通过引风机,使叶片遭受连续不断地冲刷.这样,在叶片出口处形成刀刃状磨损.由于这种磨损是不规则的,
因此造成了叶轮的不平衡.还有,叶轮表面在高温下很容易氧化,生成厚厚的氧化皮.这些氧化皮与叶轮表面的结合力并不是均匀的,某些
氧化皮受振动或离心力的作用会自动脱落,这也是造成叶轮不平衡的
一个原因。
一般风机叶轮在进行动平衡的时候往往会耗费很大的人力、物力、财力,需要很多个工人进行拆卸。
风机叶片动平衡有加料和减料两种方法,风机叶片常用的是减料的方法,将比较重的部分去掉一些材料达到动平衡,用KMbalancer做也可以的,这是现场的动平衡校正,比拆下来的好多了。
高速旋转机械受物料的影响较大,冲击、腐蚀、磨损、结焦都会对机器的转子系统
造成不平衡故障。
而旋转机械的振动故障有70%来源于转子系统的不平衡。
通常,维护人员对于振动较大的转子,进行拆除处理,直接更换
叶轮等,重新安装后运行,达到降低振动的目的。
然而,由于旋转部件原始不平衡量的存在,导致机器运转后,有时振动依然超过标准的允许值。
为防止毁机,威胁现场人员的安全与保障生产的正常运行,需进行动平衡校正。
锅炉引风机叶轮现场动平衡调试的技术应用

锅炉引风机叶轮现场动平衡调试的技术应用锅炉引风机由于长期处于高温及高尘的工作环境,容易导致叶轮在运转过程中变形,从而使得引风机工作中产生振动从而轴承的疲劳,严重影响设备的正常运行,因此在平时引风机检修过程中要对叶片进行平衡校正处理,本文根据个人在工作中的经验简单介绍锅炉引风机叶轮现场平衡调试的方法,供各位同仁交流。
标签:锅炉引风机;动平衡调试;三点法1 引风机产生不平衡的原因分析1.1 风机叶轮磨损及氧化锅炉引风机的工作环境中会伴随着大量颗粒粉尘,粉尘颗粒伴随着高速流动和高温的气体通过引风机的叶轮,从而使得引风机叶轮在工作中不断的冲刷,长期如此在叶轮的工作面处形成刀刃状的磨损,就会产生常见的叶片有薄厚不均匀,造成风机叶轮的不平衡。
另外,由于高温潮湿的环境会加速风机叶轮的氧化,氧化是不均匀分布,导致叶轮不平衡。
1.2 风机叶轮上产生污垢由于锅炉引风机工作环境潮湿而伴随这大量的粉尘,而且经过高温气体的作用,很容易使粉尘被吸附在叶轮的非工作面上,长期积累会在非工作面上形成比较严重的粉尘结垢,并且是逐渐的增厚。
随着叶轮的得转动,部分尘垢会因离心力和振动脱漏,导致叶轮平衡不稳定,影响风机平衡。
2 锅炉引风机叶轮现场动平衡调试的方法在实际的维护工作中,锅炉引风机叶轮平衡调试中常见的方法为三点作图法,因其操作简单,外界影响因素小,因此在实际工作中显得更加有效,成功率高。
下面就简单介绍下三点作图法的具体操作过程:2.1 三点作图法现场动平衡调试步骤2.1.1 确定初始最大振幅A0在风机轴承水平方向上用测振表测得最大初始振幅A02.1.2 将刚性转子分为三等分,别且标记为A、B、C。
(如下图1所示)2.1.3确定风机叶轮动平衡试加配重块质量G。
G=(150*ll*G1)/(r1*n/300)2)G-试加重量(g);G1-转子重量(Kg);11-原始振幅(mm);r1-试加重量安装半径(mm);n-转子转速(r/min)注:在加配重时焊条重量也应计算在内。
用三圆法解决风机叶轮的动平衡失衡的实践
11 Cement equipment management水泥设备管理 / 技术0 前 言风机叶轮磨损或是叶轮积灰时或导致风机叶轮的动平衡失衡,处理失衡的办法很简单,就是通过动平衡仪来做动平衡即可,但如果问题来的比较仓促,现场又没有动平衡仪,时间紧迫,又不允许设备长时间的停转,在这种情况下该如何才能处理风机叶轮的失衡情况呢? 前不久公司就碰到过这样的事情,使用三圆法计算的方式对风机叶轮进行动平衡找正。
1 情况介绍我公司水泥磨系统为半终粉磨系统,重点设备参数见表1,经过长时间的运行后,利用短暂的停车机会对系统设备进行检查,检查时发现循环风机叶片磨损严重,叶片和叶轮后盘焊接处均出现了磨损现象,好在停磨及时,否则可能出现叶轮飞出的情况,经过分析研究公司决定立即对叶轮进行堆焊,遂于2014年6月24日对水泥粉磨系统的循环风机叶轮进行了耐磨堆焊,风机叶轮堆焊后是必须作动平衡的,因我单位动平衡仪器出现故障无法使用,迫于生产需求只能无动平衡仪器的情况下对叶轮进行动平衡找正。
表1 水泥磨系统设备配置2 方式与步骤2.1 采集数据与绘图(1)不加任何平衡块的情况下启动风机测量其振动值,垂直振动值⊥0.217mm,水平振动值-0.581mm(水平、垂直振动值当中取最大值记为R1)。
(2)绘制出以R1作为半径的圆,即R1=581μm的圆(如图1所示)。
图1 圆的绘制(3) 在风机叶轮上确定三个点位分别以A、B、C作标记(在叶轮上找任意的三个点,但三个点位相互的夹角必须是已知的),图2中所示A点和B点的夹角为72°,A点和C点的夹角为90°。
在图1所绘图上也找到相应的三个点位分别记为A1、B1、C1。
图2 三个点位的确定(4)将同等重量的平衡块(在找正当中本人使用了重量为198.5g的平衡卡,根据风机叶轮的大小选择平衡卡的重量可大可小)加在A、B、C三点上时启动风机,分别记下三个振动值Ra、Rb、Rc。
风机叶轮动平衡方法
风机叶轮动平衡方法
风机叶轮动平衡是指对风机叶轮进行调整,使其在运转过程中达到平衡状态,避免振动和噪音的产生,提高风机的工作效率和使用寿命。
常用的风机叶轮动平衡方法有以下几种:
1. 静平衡:静平衡是在叶轮未安装在风机上时进行的平衡调整。
通过在叶轮上加装或削减一定质量的块体,使叶轮的重心与叶轮轴线重合,从而达到静平衡状态。
2. 动平衡:动平衡是在叶轮安装在风机上并运转时进行的平衡调整。
首先使用动态平衡仪测试叶轮的不平衡情况,然后在叶轮上加装或削减一定质量的块体,以消除或减小叶轮的不平衡。
3. 双面动平衡:双面动平衡是指对风机叶轮两侧进行动平衡调整。
即在叶轮两侧分别加装或削减一定质量的块体,以使叶轮两侧的不平衡量减小或归零。
4. 动平衡校正:对于动平衡调整效果不理想的情况,可以使用动平衡校正方法。
该方法主要通过切削、加工或重调叶轮的鼻部、叶片或轮毂,使叶轮达到平衡状态。
5. 振动监测和调整:在风机运行过程中,可以使用振动监测仪器进行振动检测,根据检测结果进行调整。
通过调整叶轮的平衡状况,减小风机的振动和噪音。
需要注意的是,风机叶轮动平衡的方法选择要根据具体情况和要求,有时可能需要结合不同的方法进行调整。
同时,在进行叶轮动平衡调整时,要保证操作安全,并严格按照相关标准和规范进行操作。
大型离心式风机动平衡修复技术
大型离心式风机动平衡修复技术摘要:随着科技和生产的快速发展,机械设备工作强度不断提高,生产效率和自动化水平越来越高。
同时,设备结构越来越复杂,功能越来越完善,设备各部分间关系越来越密切。
离心式风机是工厂重要设备,应根据实际情况与管理要求,研究能诊断离心式风机故障的系统,以确保其安全可靠运行和顺利生产。
关键词:离心式风机;动平衡;修复离心式风机是大容量锅炉必不可少辅助设备,风机的正常运转直接关系到锅炉的正常运转,当风机转子旋转时,常会发生振动,尤其是对新安装或经修补的叶轮运行风机振动更大。
振动会增加轴承负荷,缩短使用寿命,增加机械噪音,严重时会导致设备地脚螺栓断裂、电机烧毁、被迫停机,从而影响安全生产。
基于此,本文详细分析了大型离心式风机动平衡修复技术。
一、离心式风机概述风机在工作中,气流由风机轴向进入叶片空间,然后在叶轮驱动下随叶轮旋转;能在惯性作用下提高能量,沿半径方向离开叶轮,靠产生的离心力来做功的风机称为离心式风机。
离心式风机由叶轮旋转所产生的离心力,转化为流体能的机械能。
能量流动后,压力上升,从而可从一个空间流到另一个空间。
发动机驱动叶轮旋转的具体过程,叶轮叶片间的离心力作用下的气体,从叶轮中心甩到边缘,以高速离开叶轮,进入外壳沿外壳运动,最后的排气管道的气体管道。
同时,叶轮中心会产生一个真空,环境气体作用下的外部压力,并吸引到叶轮,连续吸入和连续流出,风机流量的空气供应。
二、动平衡技术动平衡技术能解决振动问题,可分为动平衡机动平衡、现场动平衡、在线动平衡(包含自动动平衡)。
动平衡机动平衡:将转子从机器中拆卸下来,放置在动平衡机上,一般要求支撑位为转子的轴承位,通过动平衡机的驱动装置使转子运转起来,在选定的平衡转速上测试不平衡,通过加重或去重方式减小不平衡量,使转子振动达到标准要求。
此过程要求为:保证支撑位的支撑部分与该处转子轴径有以上差值;保证动平衡机驱动与转子对应轴径有以上差值,最好保证驱动皮带竖直。
三点加重法解决风机动不平衡
三点加重法解决风机动不平衡中国铝业青海分公司第一电解厂160kA260台预焙电解槽1987年投产,年产10万t,并建有两套具有20世纪80年代技术水平的电解干法净化系统,干法净化工艺流程从功能上主要包括电解槽集气、吸附反应、气固分离、氧化铝输送、机械排风五个部分。
机械排风由6台800KW 锅炉引风机完成,机械排风是整个净化系统的主动力源,净化系统的烟气输送、氧化铝输送、除尘器等均在负压状态下操作,不向外界排放污染物。
但是排烟机锅炉引风机的故障率较高,特别是风机振动问题引起的机械故障较多,严重影响净化效果。
风机的振动:风机转子振动类型有横向振动,轴向振动及扭转振动,其中横向振动对机械动转的影响最为严重,因此横向振动是振动检测的主要对象。
风机在运转一段时期后,由于叶轮的磨损,致使风机工作时振动超差。
离心锅炉引风机型号y4-73-11No、28D,轴功率为800KW,转速为750r/min,流量为500000m3/h,是整个净化系统烟气流动的动力源,将净化处理的干净烟气排入大气。
在工作过程中我们通常用单面三点加重法来解决风机的现场动不平衡问题。
操作步骤:第一步:清除叶片上的积灰或积粉;第二步:选取试重;第三步:加重测振;第四步:加重校正。
测试时初始振速V0=20mm/s选取试重M=400g在叶轮上标示P1(α=0°),P2(α=120°),P3(α=240°)三点,分别加试重M,并测得振速分别为V1=10mm/s,V2=21mm/s,V3=30mm/s。
依下列公式计算得:K2=(V12+V22+V32-3V02)/3M2=0.0005mx=(V12-V02)/(2MK2)-M/2=-950my=(V22-V32)/(2√3 MK2)=-665m=√mx2+my2=1159.6α=tg-1(my/mx)=38.9°试验结果:在叶轮218.9°位置加重1159.6g时,达到了现场动不平衡消振的要求。
- 1、下载文档前请自行甄别文档内容的完整性,平台不提供额外的编辑、内容补充、找答案等附加服务。
- 2、"仅部分预览"的文档,不可在线预览部分如存在完整性等问题,可反馈申请退款(可完整预览的文档不适用该条件!)。
- 3、如文档侵犯您的权益,请联系客服反馈,我们会尽快为您处理(人工客服工作时间:9:00-18:30)。
大型引风机叶轮的动平衡问题及对策
叶轮产生不平衡问题的主要原因
叶轮在使用中产生不平衡的原因可简要分为两种:叶轮的磨损与叶轮的结垢。
造成这两种情况与引风机前接的除尘装置有关,干法除尘装置引起叶轮不平衡的原因以磨损为主,而湿法除尘装置影响叶轮不平衡的原因以结垢为主。
现分述如下。
1.叶轮的磨损
干式除尘装置虽然可以除掉烟气中绝大部分大颗粒的粉尘,但少量大颗粒和许多微小的粉尘颗粒随同高温、高速的烟气一起通过引风机,使叶片遭受连续不断地冲刷。
长此以往,在叶片出口处形成刀刃状磨损。
由于这种磨损是不规则的,因此造成了叶轮的不平衡。
此外,叶轮表面在高温下很容易氧化,生成厚厚的氧化皮。
这些氧化皮与叶轮表面的结合力并不是均匀的,某些氧化皮受振动或离心力的作用会自动脱落,这也是造成叶轮不平衡的一个原因。
2.叶轮的结垢
经湿法除尘装置(文丘里水膜除尘器)净化过的烟气湿度很大,δ除净的粉尘颗粒虽然很小,但粘度很大。
当它们通过引风机时,在气体涡流的作用下会被吸附在叶片非工作面上,特别在非工作面的进口处与出口处形成比较严重的粉尘结垢,并且逐渐增厚。
当部分灰垢在离心力和振动的共同作用下脱落时,叶轮的平衡遭到破坏,整个引风
机都会产生振动。
二、解决叶轮不平衡的对策
1.解决叶轮磨损的方法
对干式除尘引起的叶轮磨损,除提高除尘器的除尘效果之外,最有效的方法是提高叶轮的抗磨损能力。
目前,这方面比较成熟的方法是热喷涂技术,即用特殊的手段将耐磨、耐高温的金属或陶瓷等材料变成高温、高速的粒子流,喷涂到叶轮的叶片表面,形成一层比叶轮本身材料耐磨、耐高温和抗氧化性能高得多的超强外衣。
这样不仅可减轻磨损造成叶轮动平衡的破坏,还可减轻氧化层产生造成的不平衡问题。
选用引风机时,干式除尘应优先选用经过热喷涂处理的叶轮。
使用中δ经过热喷涂处理的叶轮,在设备维修时,可考虑对叶轮进行热喷涂处理。
虽然这样会增加叶轮的制造或维修费用,但却提高叶轮的使用寿命l~2倍,延长了引风机的大修周期。
从而降低了引风机和整个生产系统的运行成本,综合效益很好。
2.解决叶轮结垢的方法
(1)喷水除垢:这是一种常用的除垢方法,喷水系统装在引风机的机壳上,由管道、3个喷嘴(1个λ于叶轮出口处,2个λ于进口处)及排水孔组成。
水源一般为自来水,压力约0.3MPa。
这种方法通常还是有效的。
缺点是ÿ次停机除垢的时间较长,ÿ月需停机数次进行除垢。
影响机组的正常使用。
(2)高压气体除垢:该系统采用与喷水系统相似的结构,但其管
道为耐高压管道、专用的喷嘴和高压气源。
这种装置对叶片的除垢是快速有效的,它可以在引风机正常停机的间隙,开启高压气源,仅用数十秒的时间即可完成除垢。
由于操作简单方便,一天可以进行许多次,不但解决了人工除垢费力、费时的问题,还明显降低了整个机组的生产成本。
问题是用户是否有现成的高压气源(压力在0.8~1.5MPa 之间,可以用压缩空气或氮气),否则,需要专用的高压压缩机设备。
(3)气流连续吹扫除垢:从结构上讲,连续吹扫装置不需要外部气源,它利用引风机本身的排气压力,将少量的烟气(额定风量的1%~2%)从引风机的内部引向专用喷嘴,喷嘴λ于叶轮的进口,以很高的速度将烟气咳射到叶片的非工作表面,这种吹扫是连续地,它随着引风机的开启而开始,不但将刚刚粘到叶片上的粉尘吹掉,还可防止粉尘沉积加厚,且无需停机除垢。
该装置结构简单、对引风机改动量很小,防结垢效果很好,是一种很有发展的新技术。
3.叶轮动平街的校正
无论是采用热喷涂处理的叶轮,还是采用各种方法除垢的叶轮,其效果都不会一劳永逸。
引风机在长期使用后,仍会出现振动超过允许上限值阶情况。
此时,叶轮的不平衡问题只能通过动平衡校正来解决。