煤气发生炉主要设备构造及工艺
第四期煤气发生炉的操作
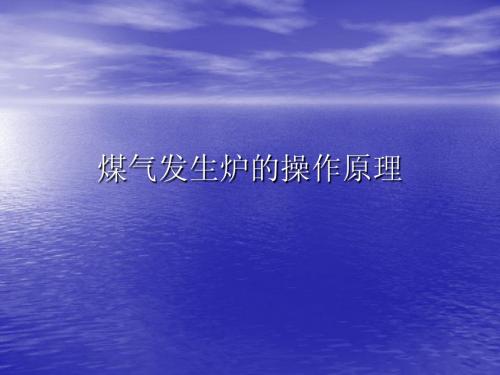
• 2、混合气温度
混合气温度表示进入炉内的空气与水蒸气的比例。温度 过高,则火层温度下降,煤气质量变坏;过低则火层温度 升高,易炼炉。故混合气温度要求控制在50--57℃ 升高,易炼炉。故混合气温度要求控制在50--57℃. 3、煤气出口温度 煤气出口温度应该控制在520-570℃ 煤气出口温度应该控制在520-570℃之间,煤气出口温 度正常时。炉面为暗红色,煤块可以分辨清楚,煤气为深 黄色;煤气出口温度过高时,炉面红亮,煤块难以分辨, 煤气发青、发黑;煤气出口温度过低时,炉面发黑,煤气 毛白汽,可以通过调节加煤量、混合气温度、扎钎、清灰 等操作来调节煤气出口。 4、鼓风压力 鼓风压力的大小决定于燃料层的阻力与煤气出口的压力, 故鼓风压力的大小取决于所用燃料的质量、炉层的分布与 煤气管道的畅通情况。但在所有因素都一定的情况下,鼓 风压力要求稳定,因为如果鼓风压力不稳,易影响炉层的 分布、煤气的质量。
煤气发生炉内气化过程示意图
2、气化反应进行的条件
• 在发生炉内进行的一系列反应除了反应(4)是单 在发生炉内进行的一系列反应除了反应(4
相反应外,其余的都是多相反应。因此高温与高 的鼓风速度是强化气化过程的条件。高温有利于 加速还原反应的进行,高的鼓风速度有利于促进 气体分子的扩散。但温度的升高受到炉内炉渣炼 结的限制,鼓风速度的提高相对减少了气体与C 结的限制,鼓风速度的提高相对减少了气体与C的 接触时间,不利于反应的进行。所以高温与高的 鼓风速度是有条件的,我们要求控制鼓风温度为 50-57 ℃ 50-
空层、煤层(分第一还原层、第二还原层)、火层(氧化层)、灰层。 见发生炉内气化过程示意图
• 混合煤气的反应包括两类反应:一是碳与氧气的反应,另一类是碳与
水蒸气的反应。 • 空气与水蒸气的混合气进入灰层,被灼热的炉灰加热,继续上升遇到 火层,与氧化层中的碳发生如下反应 C+O2-----CO2+97650KCal -----CO (1) 2C+O2-----2CO+58860KCal -----2CO+58860KCal (2) 此时温度急剧上升至1200℃ 此时温度急剧上升至1200℃,混合气中几乎已无氧气,此过程主要生 成CO2、与少量CO。经过氧化层反应后,气体继续上升至煤层,发生 与少量CO。经过氧化层反应后,气体继续上升至煤层,发生 如下反应: C+CO2-----2CO-38790KCal -----2CO(3) C+H2O-----CO+H2-28380KCal -----CO+H (4) C+2H2O-----CO2+2H2-28380KCal -----CO (5) 在煤层 反应产物是CO、H2,煤层温度一般在700--1000 ℃ 反应产物是CO、H2,煤层温度一般在700--1000
煤气发生炉操作规程
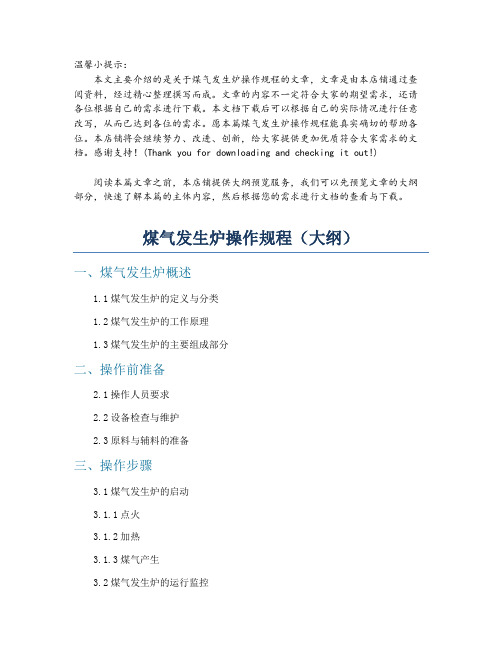
温馨小提示:本文主要介绍的是关于煤气发生炉操作规程的文章,文章是由本店铺通过查阅资料,经过精心整理撰写而成。
文章的内容不一定符合大家的期望需求,还请各位根据自己的需求进行下载。
本文档下载后可以根据自己的实际情况进行任意改写,从而已达到各位的需求。
愿本篇煤气发生炉操作规程能真实确切的帮助各位。
本店铺将会继续努力、改进、创新,给大家提供更加优质符合大家需求的文档。
感谢支持!(Thank you for downloading and checking it out!)阅读本篇文章之前,本店铺提供大纲预览服务,我们可以先预览文章的大纲部分,快速了解本篇的主体内容,然后根据您的需求进行文档的查看与下载。
煤气发生炉操作规程(大纲)一、煤气发生炉概述1.1煤气发生炉的定义与分类1.2煤气发生炉的工作原理1.3煤气发生炉的主要组成部分二、操作前准备2.1操作人员要求2.2设备检查与维护2.3原料与辅料的准备三、操作步骤3.1煤气发生炉的启动3.1.1点火3.1.2加热3.1.3煤气产生3.2煤气发生炉的运行监控3.2.1参数监控3.2.2设备巡检3.2.3异常处理3.3煤气发生炉的停车3.3.1停车操作3.3.2设备清洗与维护四、安全与环境保护4.1安全操作规程4.1.1通用安全要求4.1.2高压气体操作安全4.2环境保护措施4.2.1废气处理4.2.2废水处理4.2.3噪音防治五、设备维护与故障排除5.1设备维护保养5.1.1日常保养5.1.2定期检修5.2常见故障与排除方法5.2.1故障诊断5.2.2故障排除六、质量检验与控制6.1煤气质量检验6.1.1检验方法6.1.2检验标准6.2质量控制措施6.2.1工艺参数控制6.2.2设备精度控制七、应急预案7.1紧急情况处理7.1.1紧急停车7.1.2人员疏散7.2应急设备与物资7.2.1应急设备配置7.2.2应急物资准备八、培训与考核8.1操作人员培训8.1.1培训内容8.1.2培训方法8.2操作人员考核8.2.1考核标准8.2.2考核流程一、煤气发生炉概述1.1煤气发生炉的定义与分类煤气发生炉是一种以固体燃料(如煤、生物质等)为原料,通过化学反应产生煤气的设备。
煤气发生炉主要设备构造及工艺

煤气发生炉主要设备构造及工艺第二章煤气发生炉工艺及主要设备构造煤炭气化技术自1839年俄国第一台空气鼓风液态排渣气化炉问世以来,至今已有100多年的历史。
我国的煤炭气化技术起步较晚,上世纪50年代初期,为了适应国民经济恢复和发展的需要,借鉴苏、美40年代末期的设计,开始自制常压固定床煤气发生炉煤气化设备。
经过几十年的实践,通过不断改进,在加煤、排灰、气化工艺的自动控制等方面取得了可喜的进步。
在山东冶金、耐材系统,因所用窑炉对煤气的洁净度要求不高,发生炉煤气较多应用单段炉热煤气及两段炉热脱焦油煤气。
本章针对这一特点,重点介绍单段炉热煤气站及两段炉热脱焦油煤气站的工艺流程和各种设备的结构特点。
第一节工艺流程煤气站的工艺流程按净化系统来分,可分为热煤气和冷煤气两大系统。
热煤气是煤气由发生炉出来后只经过粗略除尘,便直接送往用户。
一般在用户对煤气含尘量要求不高、距离较近的窑炉使用。
其特点是,系统比较简单,投资少,能充分利用煤气的显热和焦油的化学热。
但煤气不能远距离输送,且宜堵塞管路、烧嘴,一旦堵塞,不便清理。
冷煤气是煤气出炉后,经过冷却、除尘、除焦油并经加压后的冷净煤气,系统比较复杂,但煤气质量高,输送距离远,应用范围比较广,能适应各种窑炉的要求。
一、单段炉热煤气发生站工艺流程烟煤、无烟煤、焦炭为原料的热发生炉煤气站工艺流程见图2-1。
热发生炉煤气站工艺流程为:按使用要求外购的烟煤或无烟煤在煤场经破碎、筛分后运至上煤系统,通过输送皮带、电动葫芦或爬梯等形式,间歇的将煤送到加煤机构,加入到炉内。
在煤气炉内,粒煤与由鼓风机带入的汽、风混合物进行气化反应。
生成的出炉脏煤气,其温度约400~600℃,经过旋风除尘器除去粒度较大的粉尘后,通过带内衬砖(或保温)和排灰斗的热煤气管道直接送往窑炉。
17图2-1 单段炉热煤气站工艺流程二、两段炉热脱焦油煤气站工艺流程两段炉热脱焦油煤气站工艺流程如图2-2所示:图2-2 两段炉热脱焦油煤气站工艺流程两段炉热脱焦油煤气站工艺流程为:原料煤在煤场进行破碎、筛分后,符合工艺要求粒度的中块煤,经上煤系统加入到煤仓中,再经加煤机构间歇地进入煤气炉内,煤受到来自气化层的热煤气加热脱除水分及挥发分成为低温干馏半焦。
两段式煤气发生炉内部构造
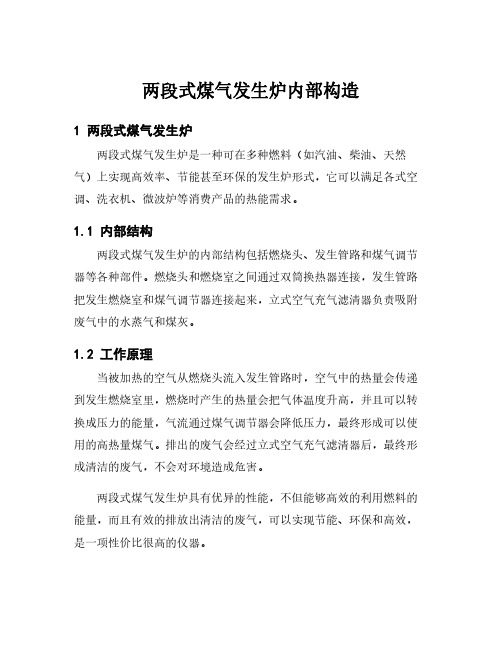
两段式煤气发生炉内部构造
1两段式煤气发生炉
两段式煤气发生炉是一种可在多种燃料(如汽油、柴油、天然气)上实现高效率、节能甚至环保的发生炉形式,它可以满足各式空调、洗衣机、微波炉等消费产品的热能需求。
1.1内部结构
两段式煤气发生炉的内部结构包括燃烧头、发生管路和煤气调节器等各种部件。
燃烧头和燃烧室之间通过双筒换热器连接,发生管路把发生燃烧室和煤气调节器连接起来,立式空气充气滤清器负责吸附废气中的水蒸气和煤灰。
1.2工作原理
当被加热的空气从燃烧头流入发生管路时,空气中的热量会传递到发生燃烧室里,燃烧时产生的热量会把气体温度升高,并且可以转换成压力的能量,气流通过煤气调节器会降低压力,最终形成可以使用的高热量煤气。
排出的废气会经过立式空气充气滤清器后,最终形成清洁的废气,不会对环境造成危害。
两段式煤气发生炉具有优异的性能,不但能够高效的利用燃料的能量,而且有效的排放出清洁的废气,可以实现节能、环保和高效,是一项性价比很高的仪器。
两段式煤气发生炉主要设备介绍1聚辰

147两段式煤气发生炉主要设备介绍炉体:炉体为整体结构制造.炉体上部包括:发生顶部约1000L的预热水箱.下部的水夹套留有足够的蒸气贮存空间,提供气化剂所需要的自产蒸气.夹套外则附有玻璃液位计,夹套采用定时补水,(内部锅炉式煤气站配有热器和集汽包)具体水位视玻璃液位计标志而定.炉底部:发生炉底部有炉栅、炉栅支座、灰盘、灰梨、支撑环、刺轮、水封及底部通气室组成。
灰梨固定在炉体下部外侧,炉栅、炉栅支座、灰盘及底部刺轮结为一体由液压驱动,与灰梨配合把炉体中气化后剩余灰渣排除炉外。
灰盘与炉体之间靠水封实现气密。
炉栅炉栅是由耐热磨铸钢制成的铸件,它被螺栓依此紧固在炉栅支座上。
灰渣排除气化后剩余灰渣积存与灰盘中,依靠灰盘的转动与灰梨配合把它由水封中驱除,流入溜灰槽,最后由操作人员运送到灰渣堆存处。
栅炉驱动炉栅借助个液压油缸,对称的同时拉动刺轮的转动,两个液压油缸对称地紧固在刺轮两边灰盘承上,每次驱动一个齿轮间距。
气化剂的产生和底部气化室工艺鼓风机把空气送入混合器与蒸汽混合后形成汽化剂,汽化剂的温度采用“自动/手动”控制方式气化剂通过底部通气室进入炉内,通气室和转动部分的衔接密封靠两级水封完成。
耐火砖及保温处理发生炉内高温反应区与炉壁间衬有一层耐火砖和50mm厚的隔热保温层,避免了反应热量散失和反应物对炉壁产生的腐蚀,而且附带地解决了材料的热胀冷缩问题。
周围耐火砖中有六个对称的圆形通道,在通道出口装有底部气流节气,以便保证煤气流量的均衡。
旋风除尘器带有灰尘的高温底部煤气通过旋风除尘器后,大部分灰尘被清除,通过锁灰斗两道滑板阀定期的排除。
当含尘的煤气进入旋风除尘器后,在旋转过程中产生离心力,将密度大于气体的尘粒力和向下的重力沿壁面下落进入排灰管,由操作工定期排出。
旋风除尘器的阻力降为90pa--120pa,除尘效率:80pa—90pa换热器(内部锅炉):它是一台单程列管式换热器、利用高温煤气的余热通过热交换而产生蒸汽;煤气走管程内部,软化水走管程外部进行热交换。
煤气发生炉的构造

煤气发生炉的构造煤气发生炉种类很多,有固定炉排式及旋转炉排式的煤气炉,也有无底固定风帽式煤气炉及阶梯煤气炉。
下面简要介绍我厂自行设计制造的MHZ-1850旋转炉排煤气发生炉的结构。
1、加煤系统加煤斗应用8m/m钢板卷制,上面装有水封槽,并用加煤盖密封,制造时,应保证水封高度大于炉内最大压力。
锥形钟招与底座以园环面密封,加煤时可将杠杆一边抖动,一边逐渐往上升,这时加煤斗座的煤快首先滑向导向环,按自由落体规律炉膛中间区域,当锥形钟罩下降至导向环下端后,煤块即沿着钟罩面凭借惯性力向炉膛四周滑下,如果操作得当,可命名煤层分布均匀。
加煤斗悬挂于加煤小车,用卷扬机牵引沿弧形轨道上下,在加煤斗和加煤座盖上安装机械自动开启装置,实现自动加煤动作。
2、观察,搅火(打钎)装置钎孔上座膛有锥形内孔与钎孔锥盖密封。
钎孔下座用螺栓和上座相连接,并与筒体上盖固定3、炉体部分筒体用10m/m铜板卷成,也可利用化工厂报废的旧筒体,内侧镶有大刀口耐火砖,下面适当位置开有活动炉门,用来生火,出渣及维修等。
筒体上盖用16-18mm钢板制成,内浇注耐火可塑料,上面装有加煤系统及观察、搅火装置。
筒体上盖有螺栓与筒体固定。
并用耐火可塑料密封,上盖的吊装须待可塑料干燥后进行。
筒体、操作平台及其他装置的全部重量通过构架立柱传递到基础。
4、基础部分基础用150#素砼浇注100-150mm在四个立柱位置加钢筋网,配筋Φ12螺纹钢,面积1000×1000,间距150×150。
灰盘的传动系统,回转系统,一次风机安装予埋件按图布置,一次浇注。
5、鼓风系统(一次风)一次风机将空气和水蒸汽的混合气体打入Φ220进风管内,在通过一组宝塔形风帽进入炉内,冷凝水通过回水管进入盛水箱内,盛水箱出水口标高应高于下水道,以防回水。
6、净化储存及主煤气管由炉体上侧输出的煤气通过Φ400~4600出气管进入简易净化储存器。
储存器出口接主煤气管主煤气管Φ400-Φ600,用4MM钢板卷焊,内衬δ=20~30mm矾土水泥素砼,并在管壁上用Φ4~Φ6钢筋焊上脚子,不但减少煤气余热损失,提高炉膛温度。
煤气发生炉工作原理与结构
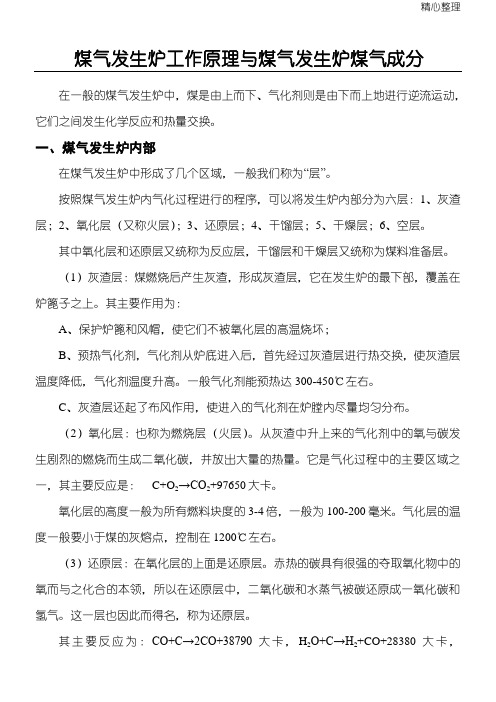
精心整理煤气发生炉工作原理与煤气发生炉煤气成分在一般的煤气发生炉中,煤是由上而下、气化剂则是由下而上地进行逆流运动,它们之间发生化学反应和热量交换。
一、煤气发生炉内部在煤气发生炉中形成了几个区域,一般我们称为“层”。
层;2(A B C (度一般要小于煤的灰熔点,控制在1200℃左右。
(3)还原层:在氧化层的上面是还原层。
赤热的碳具有很强的夺取氧化物中的氧而与之化合的本领,所以在还原层中,二氧化碳和水蒸气被碳还原成一氧化碳和氢气。
这一层也因此而得名,称为还原层。
其主要反应为:CO+C→2CO+38790大卡,H 2O+C→H 2+CO+28380大卡,2H2O+C→CO2+2H2+17970大卡。
由于还原层位于氧化层之上,从上升的气体中得到大量热量,因此还原层有较高的温度约800-1100℃,这就为需要吸收热量的还原反应提供了条件。
而严格地讲,还原层还有第一、第二之分,下部温度较高的地方称第一还原层,温度达950-1100℃,其厚度为300-400毫米左右;第二层为700-950℃之间,其厚度为第一还原层1.5倍,约在450毫米左右。
((在室温层高。
(CO单叙述,我们可以看出煤气发生炉内进行的气化过程是比较复杂的,既有气化反应,也有干馏和干燥过程。
而且在实际生产的发生炉中,分层也不是很严格的,相邻两层往往是相互交错的,各层的温度也是逐步过渡的,很难具体划分,各层中气体成份的变化就更加复杂了,即使在专门的研究中,看法也是分歧的。
二、煤气炉的结构对于固定床煤气炉有多种结构型式,按不同部位分述如下:1、加煤装置:间歇式加煤罩、双料钟、振动给煤机、拨齿加煤机。
2、炉体结构:带压力全水套、半水套、无水套(耐火材料炉衬)、常压全水套。
3、炉篦:宝塔型、型钢焊接型。
4、灰盘传动结构:拨齿型、蜗轮蜗杆型。
三、煤气发生炉煤气成分所谓煤气发生炉炉出煤气,是指煤在煤气发生炉内气化反应所产生的,自煤气2、煤气中的H2S煤气中的H2S含量多少与气化用煤中的含硫多少有关,一般煤中硫分的80%以H2S状态转入煤气中,20%的硫分残留在灰渣中。
煤气发生炉结构图

煤气发生炉结构图煤气发生炉是一种常见的燃烧设备,广泛用于燃料转换和能源生产过程中。
它通过将煤炭等燃料加热,并在缺氧条件下将其转化为可燃气体,从而生成煤气。
煤气由可燃气体(如一氧化碳和氢气)以及一些不可燃气体(如二氧化碳和氮气)组成。
煤气发生炉的结构图可以帮助我们了解其基本组成部分和工作原理。
一般而言,煤气发生炉主要由以下几个主要部分组成。
1. 燃料储存器:燃料(如煤炭)被储存在燃料储存器中,以供后续的燃烧过程使用。
2. 炉体:炉体是煤气发生炉的主要部分,通常由耐火砖或耐火材料构成。
炉体用于承载和分离燃料,以使其在缺氧条件下转化为可燃气体。
在炉体的上部,通常有一个燃烧室,用于将煤气与空气混合并点燃。
3. 空气供给系统:煤气发生炉需要空气来支持燃烧过程。
空气供给系统通常包括风机、风道和调节装置,用于控制并输送适量的空气至炉体。
4. 渣口和灰斗:在煤气发生炉内,碳和灰分等杂质将通过渣口自动排出。
随着燃料的燃烧,残留下来的灰渣会被输送至灰斗中进一步处理。
5. 控制系统:煤气发生炉通常配备了控制系统,用于监测和控制炉内的温度、压力和燃料供应等参数。
这些控制系统可以自动化调整,以确保炉体正常运行。
煤气发生炉的工作原理主要由下述过程组成。
首先,将燃料(如煤炭)投入燃料储存器,并通过供料系统将燃料传输至煤气发生炉的燃料进料装置。
燃料进入炉体后,通过一系列加热与分解反应,燃料会产生可燃气体。
这些反应中涉及的物理和化学过程包括干馏、氧化、还原和脱水等。
在这个过程中,主要的产物是一氧化碳和氢气。
这些可燃气体被输送至燃烧室,与通过空气供给系统输送的空气混合并点燃。
这种点燃反应会产生高温燃烧火焰,用于提供热量或驱动其他设备。
在燃料燃烧的过程中,部分炉内温度会超过1000℃。
这种高温环境有助于完全燃烧燃料中的碳残留物,并将其转化为灰渣。
灰渣通过渣口自动排放,并输送至灰斗中进一步处理。
煤气发生炉的设计和结构根据使用环境和需求的不同而变化。
- 1、下载文档前请自行甄别文档内容的完整性,平台不提供额外的编辑、内容补充、找答案等附加服务。
- 2、"仅部分预览"的文档,不可在线预览部分如存在完整性等问题,可反馈申请退款(可完整预览的文档不适用该条件!)。
- 3、如文档侵犯您的权益,请联系客服反馈,我们会尽快为您处理(人工客服工作时间:9:00-18:30)。
规格参数
单段炉
两段炉
W-G型
MQLⅡ3000
MQLⅡ3200
炉膛内径(mm)
2400
3000
3000
3200
水夹套受热面积(m2)
.66
32.04
30.25
16.00
35.41
适用煤种
不粘结或弱粘结烟煤
无烟煤
不粘结或弱粘结烟煤
煤的粒度(mm)
13~25,25~50,30~60
40~60
耗煤量(kg/h)
900~1250
1500~2150
1660~2300
~2200
~2400
空气消耗量(m3/kg煤)
2.0~2.5
2.0~2.5
2.0~2.5
2.0~2.5
2.0~2.5
蒸汽消耗量(t/ h)(kg/kg煤)
0.3~0.5
0.3~0.5
0.3~0.5
0.3~0.5
0.3~0.5
5225~5434
煤气出口压力(kPa)
上段煤气
0.8~1.2
0.8~1.2
<4.0
0.98
3.0~3.5
下段煤气
1.47
3.5~4.5
煤气出口
温度(℃)
上段煤气
400~550
400~550
400~550
80~120
80~120
下段煤气
450~550
450~550
最大炉底鼓风压力(kPa)
3.0
(一)炉型结构特点
3BD煤气炉的结构组成如图2-3所示。
这类炉型由上、中、下三部分组成。上部包括加煤机、炉盖、探火孔等主要部件。中部包括炉体、水夹套,碎渣圈、小灰刀等。
下部包括炉篦、灰盘及其传动装置、排灰刀、鼓风箱等。炉体水夹套由四个支柱支撑在基础上,其中一个支柱是活动支柱,可以拆下,以便更换炉篦、灰盘。在灰盘、鼓风箱处设有水封,以保证炉子的气密性。灰盘水封还起到防爆作用,当炉内发生爆炸事故时,可以通过灰盘水封泄压。
每台煤气炉附带一台蒸汽汇集器,汇集器与炉体水夹套之间的连接管路不能装设任何隔断装置。汇集器将炉体水夹套产生的蒸汽汇集起来,经过汽水分离后,热水通过管道流回水夹套循环使用,蒸汽则供煤气站使用。炉体水夹套与汇集器构成的汽水循环原理是:低温的软化水进入蒸汽汇集器,然后由下降管流到炉体水夹套的下部,在水夹套内的水由于受到炉膛内料层传过来的热量而升温,在水夹套内产生了蒸汽和水的混合物。因汽水混合物比重较小,水的比重较大,汽水混合物由上升管进入到蒸汽汇集器,水由下降管进入到水夹套,因而形成汽水的自然循环。
第二章煤气发生炉工艺及主要设备构造
煤炭气化技术自1839年俄国第一台空气鼓风液态排渣气化炉问世以来,至今已有100多年的历史。我国的煤炭气化技术起步较晚,上世纪50年代初期,为了适应国民经济恢复和发展的需要,借鉴苏、美40年代末期的设计,开始自制常压固定床煤气发生炉煤气化设备。经过几十年的实践,通过不断改进,在加煤、排灰、气化工艺的自动控制等方面取得了可喜的进步。
二、两段炉热脱焦油煤气站工艺流程
两段炉热脱焦油煤气站工艺流程如图2-2所示:
两段炉热脱焦油煤气站工艺流程为:原料煤在煤场进行破碎、筛分后,符合工艺要求粒度的中块煤,经上煤系统加入到煤仓中,再经加煤机构间歇地进入煤气炉内,煤受到来自气化层的热煤气加热脱除水分及挥发分成为低温干馏半焦。半焦下行至气化层(还原层和氧化层),与由炉底进入的空气和水蒸汽进行气化反应,生成发生炉煤气,下部的灰渣从煤气炉灰盘经大灰刀排出。部分煤气经过包围干馏层的火道引出,成为下段煤气,其出口温度根据不同炉型约为400~600℃,煤气压力为1.5~4.5kPa,经过底部旋风除尘器除去颗粒较大的灰尘后进入煤气总管。另一部分煤气进入干馏层,与干馏煤气混合后从两段炉顶部引出,称为上段煤气,其出口温度约为100~150℃,煤气压力约为1~3.5kPa。上段煤气经旋风除油器除去带出物和大颗粒焦油,进入电捕焦油器脱除焦油后在煤气总管与下段煤气混合得热脱焦油煤气供用户。由于工艺的原因,挥发分较高的弱粘结性烟煤特别适用两段式煤气发生炉。
冷煤气是煤气出炉后,经过冷却、除尘、除焦油并经加压后的冷净煤气,系统比较复杂,但煤气质量高,输送距离远,应用范围比较广,能适应各种窑炉的要求。
一、单段炉热煤气发生站工艺流程
烟煤、无烟煤、焦炭为原料的热发生炉煤气站工艺流程见图2-1。
热发生炉煤气站工艺流程为:按使用要求外购的烟煤或无烟煤在煤场经破碎、筛分后运至上煤系统,通过输送皮带、电动葫芦或爬梯等形式,间歇的将煤送到加煤机构,加入到炉内。在煤气炉内,粒煤与由鼓风机带入的汽、风混合物进行气化反应。生成的出炉脏煤气,其温度约400~600℃,经过旋风除尘器除去粒度较大的粉尘后,通过带内衬砖(或保温)和排灰斗的热煤气管道直接送往窑炉。
煤气产量(Nm3/h)
3000~400
5000~6500
5000~7000
5500~7000
6500~7500
煤气热值
(kJ/ Nm3)
混合煤气
5225~5643
5225~5643
5225~5643
5850~6270
5850~6270
上段煤气
7110~7520
7110~7520
下段煤气
5225~5434
第二节煤气发生炉的结构
常压固定床混合煤气发生炉在我国是一种使用最广泛的气化设备,国内常用的大致有Д型炉篦湿式排灰的混合煤气发生炉、W-G型干式排灰的混合煤气发生炉、两段式煤气发生炉等几种。表2-1是山东冶金机械厂生产的部分煤气发生炉的技术性能参数。
一、Д型炉篦湿式排灰的混合煤气发生炉
Д型的煤气发生炉其炉篦形状与俄文字母“Д”相似而因此命名。3BD煤气炉属于“Д”型炉的一种,是在原3AД-135煤气炉基础上由山东冶金机械厂改进而成,下面通过介绍3BD型煤气炉,了解“Д”型炉的结构型式特点。
在山东冶金、耐材系统,因所用窑炉对煤气的洁净度要求不高,发生炉煤气较多应用单段炉热煤气及两段炉热脱焦油煤气。本章针对这一特点,重点介绍单段炉热煤气站及两段炉热脱焦油煤气站的工艺流程和各种设备的结构特点。
第一节工艺流程
煤气站的工艺流程按净化系统来分,可分为热煤气和冷煤气两大系统。
热煤气是煤气由发生炉出来后只经过粗略除尘,便直接送往用户。一般在用户对煤气含尘量要求不高、距离较近的窑炉使用。其特点是,系统比较简单,投资少,能充分利用煤气的显热和焦油的化学热。但煤气不能远距离输送,且宜堵塞管路、烧嘴,一旦堵塞,不便清理。