橡胶制品模具撕边槽 余料槽及防焦边槽标准
橡胶件外观检验规范
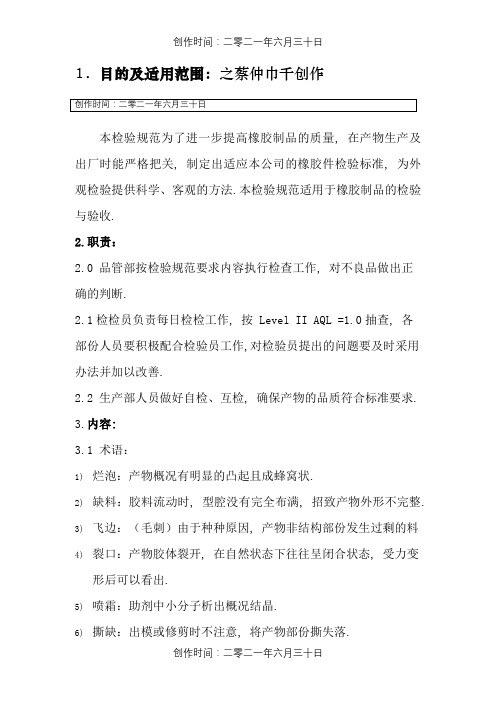
1.目的及适用范围:之蔡仲巾千创作本检验规范为了进一步提高橡胶制品的质量, 在产物生产及出厂时能严格把关, 制定出适应本公司的橡胶件检验标准, 为外观检验提供科学、客观的方法.本检验规范适用于橡胶制品的检验与验收.2.职责:2.0 品管部按检验规范要求内容执行检查工作, 对不良品做出正确的判断.2.1检检员负责每日检检工作, 按 Level II AQL =1.0抽查, 各部份人员要积极配合检验员工作,对检验员提出的问题要及时采用办法并加以改善.2.2 生产部人员做好自检、互检, 确保产物的品质符合标准要求.3.内容:3.1 术语:1)烂泡:产物概况有明显的凸起且成蜂窝状.2)缺料:胶料流动时, 型腔没有完全布满, 招致产物外形不完整.3)飞边:(毛刺)由于种种原因, 产物非结构部份发生过剩的料4)裂口:产物胶体裂开, 在自然状态下往往呈闭合状态, 受力变形后可以看出.5)喷霜:助剂中小分子析出概况结晶.6)撕缺:出模或修剪时不注意, 将产物部份撕失落.7)气泡:产物概况有明显凸起且呈球面状.8)焦边:分型处打皱并裂开.9)杂质:与生产使用的胶料不融合, 在产物上显示出分歧颜色或明显异物.10)撬坏:脱模时用力撬产物的内外概况或其它部位, 招致产物有明显裂口.11)分层:胶体之间分开不相粘, 出现出有条理的现象.12)脱胶:产物的胶料与骨架明显分开, 骨架概况没有任何一点胶料附着在上面.13)模脏:产物概况有明显的光洁度不够或产物概况有凹陷现象.14)老化胶:废边遗留在型腔内, 再生产时废边黏附在产物概况上.15)欠硫:由于温渡过低或胶料硫化增进剂过少, 造成产物欠硫,产物内部胶体呈砂孔, 不致密, 胶体呈鼓起状态.16)厚薄不均:产物同一概况手触摸有凹凸感, 厚度尺寸有不同.17)变形:产物收外力后, 造成扭曲等形状变动.3.2 检验方法3.2.1 外观缺陷的检验方法及要求:照度:正常日光灯, 室内无日光时用40W日光灯或60W普通灯胆的照度为标准.目测距离:眼睛距离产物30-----40CM直视为准观察时间:<10秒 (每个可见平面需要3秒)3.2.2 外观尺寸及尺寸的配合的检验方法使用普通长度丈量仪或各种量规进行丈量.3.3 检验项目及标准。
模具分型面避空标准

模具分型面避空标准
1. 任一产品尺寸达到 200M M 以上的产品整圈排气槽内边缘离产品外缘
10-15MM 为好,分
型线接触面30-50MM 或以上。
(见图示)避空时要千万注意流道。
产品分型面分胶位留
255,2
注意避空部分尖角倒圆 角.
255MM 长.
25-30MM
模型边缘留 10MM,绿 色部份避空0.15MM.
2.
100-200MM 的产品整圈排气槽内边缘离产品外缘
8-10M M 为好,分型接触面
30-40MM 或以上。
(见图示)避空时要千万注意流道。
注意避空部分尖角倒圆
产品分型面分胶位留
20-25MM
模型边缘留10MM,红色
注意避空部分尖角倒圆
角.
3。
100以下的产品整圈排气槽内边缘离产品外缘6-8MM为好,分型接触面20-30MM或以上。
(见图示)避空时要千万注意流
道。
此产品52MM长.
注意避空部分尖角倒圆角
产品分型面分胶位
留15-20MM
模型边缘留10MM,
红色部份避空
0.15MM.
4.AB成型类。
(见图示)
了这些只要留25M M\
分胶位,后面可以
避空。
有此产品的碰穿位,如果面积比较大,边
缘留10-15MM,中间红色避空0。
15MM 。
方便钳工配模具。
橡胶产品基本缺陷产生原因及解决措施PPT79页

气泡
五、产品缺陷、4M原因分析、措施
气泡4M分析:人(man )
主要生产原因
1. 上料不到位(如部分产品在生产 时,竖放则会造成闷气,从而产生气 泡)。
2. 排气次数过少。
解决措施 1.进行现场培训,提高员工技
能和质量意识及自检意识。 2.严格按工艺规定操作,按照
作业指导书生产。
五、产品缺陷、4M原因分析、措施
五、产品缺陷、4M原因分析、措施
裂口4M分析:机(machine)
主要生产原因
解决措施
1.热板温度过高 。
2.模具结构设计不合理:型腔部位有 尖角、模具拐角处R偏小。 3.脱模器具有尖角 。
1.调整热板温度。 2.及时修理模具,将有尖角地
方打磨和拐角处R增大 。 3.将脱模器砂成圆角。 4.定期清洗模具。
3.上料方法不合理。
根据具体问题重新制定合理工 艺。途径:由班长/工序质控 员以《硫化工艺完善记录》形 式提出更改,或工艺员主动更 改。
4.脱模剂选用不当,浓度大,未规定 喷涂位置、喷涂次数。
5.胶料从上模流道板溢出造成产品缺 料。
增加压力,减小注射压力流量 ,检查增压时间和模具行程。
五、产品缺陷、4M原因分析、措施
入合格骨架内生产。
五、产品缺陷、4M原因分析、措施
缺陷名称:缺 料
定 义:胶料流动时,型腔 没有完全充满, 失去应有的形状 导致产品外形不 完整。
缺料
五、产品缺陷、4M原因分析、措施
缺料4M分析:人(man )
主要生产原因
1.硫化人员不按作业指导书要求操作 ,没有得到有效培训或操作工技能不 熟练:如:上料不到位(上错、上偏) 、初压过大、排气次数过少、脱模剂 使用不当:如临时选用其它脱模剂或 不同浓度的同类脱模剂、喷涂不均匀 。
塑料塑胶模具验收标准

优质参考文档塑料塑胶模具验收标准一、成型产品外观、尺寸、协作1、产品外表不允许缺陷:缺料、烧焦、顶白、白线、披峰、起泡、拉白〔或拉裂、拉断〕、烘印、皱纹。
2.、熔接痕:一般圆形穿孔熔接痕长度不大于 5mm,异形穿孔熔接痕长度小于15mm,熔接痕强度并能通过功能安全测试。
3、收缩:外观面明显处不允许有收缩,不明显处允许有稍微缩水〔手感不到凹痕〕。
4、一般小型产品平面不平度小于 0.3mm,有装配要求的需保证装配要求。
5、外观明显处不能有气纹、料花,产品一般不能有气泡。
6、产品的几何外形,尺寸大小精度应符合正式有效的开模图纸〔或 3D 文件〕要求,产品公差需依据公差原则,轴类尺寸公差为负公差,孔类尺寸公差为正公差,顾客有要求的按要求。
7、产品壁厚:产品壁厚一般要求做到平均壁厚,非平均壁厚应符合图纸要求,公差依据模具特性应做到-0.1mm。
8、产品协作:面壳底壳协作——外表错位小于 0.1mm,不能有刮手现象,有协作要求的孔、轴、面要保证协作间隔和使用要求。
二、模具外观1、模具铭牌内容完整,字符清楚,排列整齐。
2、铭牌应固定在模脚上靠近模板和基准角的地方。
铭牌固定牢靠、不易剥落。
3、冷却水嘴应选用塑料块插水嘴,顾客另有要求的按要求。
4、冷却水嘴不应伸出模架外表。
5、冷却水嘴需加工沉孔,沉孔直径为 25mm、30mm、35mm 三种规格,孔口倒角,倒角应全都。
6、冷却水嘴应有进出标记。
7、标记英文字符和数字应大于 5。
8、位置在水嘴正下方 10mm 处,字迹应清楚、美观、整齐、间距均匀。
9、模具配件应不影响模具的吊装和存放。
安装时下方有外露的油缸、水嘴,预复位机构等,应有支撑腿保护。
10、支撑腿的安装应用螺钉穿过支撑腿固定在模架上,过长的支撑腿可用车加工外螺纹柱子紧固在模架上。
11、模具顶出孔尺寸应符合指定的注塑机要求,除小型模具外,不能只用一个中心顶出。
优质参考文档12、定位圈应固定牢靠,圈直径为 100mm、250mm 两种,定位圈高出底板10~20mm。
翻边、整形模检验标准
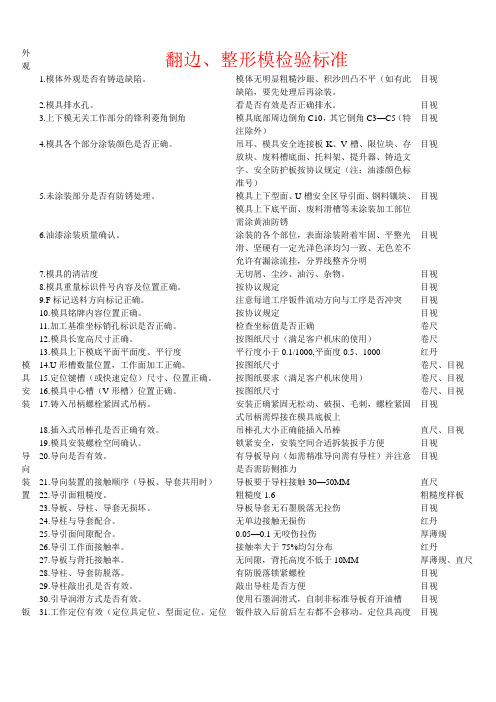
外观翻边、整形模检验标准1.模体外观是否有铸造缺陷。
模体无明显粗糙沙眼、积沙凹凸不平(如有此缺陷,要先处理后再涂装。
目视2.模具排水孔。
看是否有效是否正确排水。
目视3.上下模无关工作部分的锋利菱角倒角模具底部周边倒角C10,其它倒角C3—C5(特注除外)目视4.模具各个部分涂装颜色是否正确。
吊耳、模具安全连接板K、V槽、限位块、存放块、废料槽底面、托料架、提升器、铸造文字、安全防护板按协议规定(注:油漆颜色标准号)目视5.未涂装部分是否有防锈处理。
模具上下型面、U槽安全区导引面、钢料镶块、模具上下底平面、废料滑槽等未涂装加工部位需涂黄油防锈目视6.油漆涂装质量确认。
涂装的各个部位,表面涂装附着牢固、平整光滑、坚硬有一定光泽色泽均匀一致、无色差不允许有漏涂流挂,分界线整齐分明目视7.模具的清洁度无切屑、尘沙、油污、杂物。
目视8.模具重量标识件号内容及位置正确。
按协议规定目视9.F标记送料方向标记正确。
注意每道工序钣件流动方向与工序是否冲突目视10.模具铭牌内容位置正确。
按协议规定目视11.加工基准坐标销孔标识是否正确。
检查坐标值是否正确卷尺12.模具长宽高尺寸正确。
按图纸尺寸(满足客户机床的使用)卷尺13.模具上下模底平面平面度、平行度平行度小于0.1/1000,平面度0.5、1000 红丹模具安装14.U形槽数量位置,工作面加工正确。
按图纸尺寸卷尺、目视15.定位键槽(或快速定位)尺寸、位置正确。
按图纸要求(满足客户机床使用)卷尺、目视16.模具中心槽(V形槽)位置正确。
按图纸尺寸卷尺、目视17.铸入吊柄螺栓紧固式吊柄。
安装正确紧固无松动、破损、毛刺,螺栓紧固式吊柄需焊接在模具底板上目视18.插入式吊棒孔是否正确有效。
吊棒孔大小正确能插入吊棒直尺、目视19.模具安装螺栓空间确认。
锁紧安全,安装空间合适拆装扳手方便目视导向装置20.导向是否有效。
有导板导向(如需精准导向需有导柱)并注意是否需防侧推力目视21.导向装置的接触顺序(导板、导套共用时)导板要于导柱接触30—50MM 直尺22.导引面粗糙度。
2.磨削加工余量标准
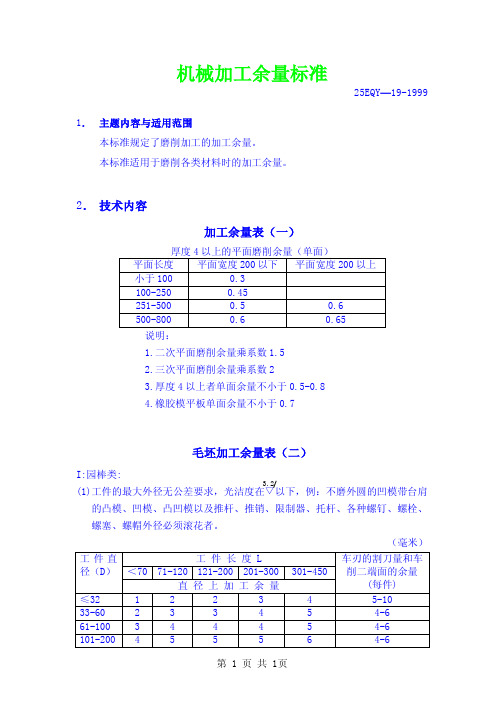
机械加工余量标准25EQY —19-19991. 主题内容与适用范围本标准规定了磨削加工的加工余量。
本标准适用于磨削各类材料时的加工余量。
2. 技术内容加工余量表(一)厚度4以上的平面磨削余量(单面)平面长度 平面宽度200以下 平面宽度200以上 小于100 0.3 100-250 0.45 251-500 0.5 0.6 500-800 0.6 0.65 说明:1.二次平面磨削余量乘系数1.52.三次平面磨削余量乘系数23.厚度4以上者单面余量不小于0.5-0.84.橡胶模平板单面余量不小于0.7毛坯加工余量表(二)I:园棒类:(1)的凸模、凹模、凸凹模以及推杆、推销、限制器、托杆、各种螺钉、螺栓、螺塞、螺帽外径必须滚花者。
(毫米)工 件 长 度 L <70 71-120 121-200 201-300 301-450 工件直径(D ) 直 径 上 加 工 余 量车刃的割刀量和车削二端面的余量(每件) ≤32 1 2 2 3 4 5-10 33-60 2 3 3 4 5 4-6 61-100 3 4 4 4 5 4-6 101-200 4 5 5 5 6 4-6当D <36时并不适应于调头夹加工,在加工单个工件时,应在L 上加夹头量10-15。
(2)工件的最大外径有公差配合如:外圆须磨加工的凹模,挡料销、肩台须磨加工的凸模或凸凹模等。
(毫米)工 件 长 度 L <50 51-80 81-150 151-250 251-420 工件直径(D ) 直 径 上 加 工 余 量车刃的割刀量和车削二端面的余量(每件) ≤15 3 3 4 4 5 5-10 16-32 3 4 4 5 6 5-10 33-60 4 4 5 6 6 5-8 61-100 5 5 5 6 7 5-8 101-200 6 6 6 7 7 5-8 当D <36时,不适合调头加工,在加工单个零件时,应加夹头量10-15。
毛坯加工余量表(三)Ⅱ:圆形锻件类(不(1)不淬火钢表面粗糙配合要求者,例如:固定板、退料板等。
橡胶磨具的设计(技术参数的控制)

橡胶磨具的设计(技术参数的控制)
一、产品的排料方式
1.产品的形状、体积、硬度,不同选择不同的排列方式。
备注:以上在一般情况下可以参考的排列方式,特殊模具结构原因选择其他作业方式。
二、模板尺寸设定
1.模板尺寸,主要指模具面和电热板面的接触的尺寸,模具承受压力面越大,压强就越小,产品毛边加厚,容易缺料不良,相反模具承压面越小,承受压强就越大,产品毛边就越薄,不易缺料,模温更加均匀。
2.模板尺寸因制品的要求尺寸及报价的孔数不同而设定,一般情况模具型腔面设计成正方形,这样模具受压均匀,模温也更加均匀。
3.计算公式:
M=﹛ODX(1+K)+2XL ﹜XC+80mm ↓↓↓↓↓↓
模
产
预
加
预腔排列数为10孔
M=﹛15X(1+0.03)+2X1.5﹜X10+80=264.5mm
模板可以选择260mmX260mm 尺寸,若计算后数值280mm-300mm 则可以选择310mmX310mm 模板。
以上只针对O-ring 及普通垫片类产品。
若由其他不规则型号楷模时模板尺寸需要重新评估。
三、排气槽/排气孔的设定
1.排气槽设定依产品的形状及高度要求不同而不同。
一般O-ring 产品可以设定宽度3.0X 深度0.30mm-0.50mm,产品较厚可以适当的做调整。
2.排气孔设定主要依产品的内径及线径要求而不同一般O-ring 及其他E 类产品
离,有利于排气。
四、切嘴形状及尺寸设定:
模具切嘴设定需考量,材质本身加成本,因产品形状不同,可以适当做调整。
五、模具结构设计。
常用机械加工余量标准

常用机械加工余量标准(总5页) --本页仅作预览文档封面,使用时请删除本页--机械加工余量标准25EQY —19-19991. 主题内容与适用范围本标准规定了磨削加工的加工余量。
本标准适用于磨削各类材料时的加工余量。
2. 技术内容加工余量表(一)说明:1. 二次平面磨削余量乘系数2. 三次平面磨削余量乘系数23. 厚度4以上者单面余量不小于橡胶模平板单面余量不小于毛坯加工余量表(二)I:园棒类:(1)的凸模、凹模、凸凹模以及推杆、推销、限制器、托杆、各种螺钉、螺栓、螺塞、螺帽外径必须滚花者。
(毫米)当D <36时并不适应于调头夹加工,在加工单个工件时,应在L 上加夹头量10-15。
(2)凹模,挡料销、肩台须磨加工的凸模或凸凹模等。
当D <36时,不适合调头加工,在加工单个零件时,应加夹头量10-15。
毛坯加工余量表(三)(1)等。
注:表中的加工余量为最小余量,其最大余量不得超过厂规定标准。
毛坯加工余量表(四)Ⅲ:矩形锻件类:表内的加工余量为最小余量,其最大余量不得超过厂规定标准。
平面、端面磨削加工余量表(五)一、平面二、端面注:20-40% 如需磨两次的零件,其磨量应适当增加10-20%环形工件磨削加工余量表(六)注:φ50以下,壁厚10以上者,或长度为100-300者,用上限 φ50-φ100,壁厚20以下者,或长度为200-500者,用上限 φ100以上者,壁厚30以下者,或长度为300-600者,用上限φ6以下小孔研磨量表(七)注:本表只适用于淬火件当长度e小于15毫米时,表内数值应加大20-30%导柱衬套磨削加工余量表(八)镗孔加工余量表(九)附注:当一次镗削时,加工余量应该是粗加工余量加工精加工余量。
- 1、下载文档前请自行甄别文档内容的完整性,平台不提供额外的编辑、内容补充、找答案等附加服务。
- 2、"仅部分预览"的文档,不可在线预览部分如存在完整性等问题,可反馈申请退款(可完整预览的文档不适用该条件!)。
- 3、如文档侵犯您的权益,请联系客服反馈,我们会尽快为您处理(人工客服工作时间:9:00-18:30)。
橡胶制品模具撕边槽、余料槽及防焦边槽标准
1.范围
本标准规定了橡胶制品模具撕边槽、余料槽及防焦边槽的形状尺寸、分布位置、适用范围、技术要求和制造要求。
(本标准使用单位为mm)2.规范性引用文件
下列文件中的条款通过本标准的引用而成为本标准的条款,凡是注明日期的引用文件,其随后所有的修改单(不包括勘误的内容)成修订版均不适用于本标准然而,鼓励根据本标准达成协议的各方研究是否可使用这些文件的最新版本。
凡不注明日期的引用文件,其最新版本适用于本标准。
GB/T699 碳素结构钢
合金结构钢
GB/T1804 一般公差、线形尺寸的未注公差
GB1031 评定表面粗糙度的参数及其取值和一般规则
3.定义
.撕边槽:在模具分型面处离型腔位置较近的位置加工一沟槽,在产品后道整形过程中起到撕边作用;
.余料槽:在离型腔或撕边槽一定位置加工一沟槽或减除承压面,在成型过程中起到存放余胶,增加产品上正压力,使产品飞边较薄,以便于后道整理或冷冻除飞边。
.防焦槽:对于较厚的橡胶产品,在其分型处加工与产品型腔相连的台阶,以防止在硫化过程中由于制品内外硫化程度不统一而在分型处造成烂边现象。
4.位置
.撕边槽、余料槽及防焦边槽的相对位置如下所示
5.撕边槽 撕边槽代号:用S-阿拉伯数字表示,其中,S 代表撕边槽。
阿拉伯数字表示撕边槽序号。
撕边槽形状、尺寸、技术要求及适用范围见下表:
撕边槽防焦槽
6.余料槽
余料槽代号:用Y-阿拉伯数字表示,其中,Y表示余料槽,阿拉伯数字表示余料槽序号;
7.防焦边槽
防焦边槽代号,用FJ-阿拉伯数字表示,其中,FJ表示防焦边槽,阿拉伯数字表示防焦边槽序号。
防焦边槽形状、尺寸、技术要求及适用范围见下表;
使用方式
对于成型件单耗易控制,橡胶硬度适当的橡胶制品模具,可选择加工撕边槽和余料槽;对于产品有特殊要求或产品整理方式不同的模具,可只选择开余料槽,主要包括产品为切割成型或切割飞边,以及产品必须用剪刀等工具修边和冷冻除飞边。
对于产品分型面处飞边较厚,其产品应设置撕边槽和余料槽;
9.制造要求
制造过程中必须按图纸或本标准要求加工撕边槽、余料槽和防焦边槽;
对于加工撕边槽时,一次性切割量不宜过大,避免造成型腔与撕边槽之间部分有裂纹,从而影响撕边槽寿命。
本标准所采用的模具材料包括:GB699-88 45#优质碳素结构钢、GB3077-88 40Cr 合金结构钢、易切削热塑性模具钢SMI以及日本JIS标准S50C等,材料硬度为HRC22-55;。