改善报告案例
工厂改善案例分析报告范文

工厂改善案例分析报告范文一、案例背景本案例分析报告旨在通过具体工厂改善案例,探讨生产效率提升、成本控制、质量管理以及员工参与度提高等方面的实践与效果。
所选工厂为一家中型企业,主要生产电子产品配件,近年来面临激烈的市场竞争和成本压力。
二、改善前状况改善前,该工厂存在以下问题:1. 生产效率低下,设备老化,工艺流程不顺畅。
2. 成本控制不严格,原材料浪费严重。
3. 产品质量不稳定,客户投诉率高。
4. 员工参与度低,缺乏改进意识和动力。
三、改善目标1. 提升生产效率,减少设备故障率。
2. 严格控制成本,减少原材料浪费。
3. 提高产品质量,降低客户投诉率。
4. 增强员工参与度,培养改进文化。
四、改善措施1. 设备升级与维护:投资更新关键生产设备,并对现有设备进行定期维护,以减少故障率和提高生产效率。
2. 工艺流程优化:重新设计工艺流程,消除不必要的步骤,实现生产流程的简化和标准化。
3. 成本控制:实施精细化管理,对原材料采购、使用和库存进行严格监控,减少浪费。
4. 质量管理体系建设:建立全面的质量管理体系,从原材料检验到最终产品出厂,每个环节都有严格的质量控制。
5. 员工培训与激励:开展定期的员工培训,提高员工技能和质量意识。
同时,设立奖励机制,鼓励员工提出改进建议和参与改进活动。
五、改善过程1. 项目启动:成立专门的改善小组,明确改善目标和责任分工。
2. 现状分析:收集数据,分析生产效率、成本、质量等方面的问题。
3. 方案设计:根据分析结果,设计具体的改善措施和实施计划。
4. 方案实施:按照计划逐步实施改善措施,包括设备升级、工艺调整、培训等。
5. 监控与调整:在实施过程中,持续监控效果,并根据反馈进行调整优化。
六、改善效果1. 生产效率提升:通过设备升级和工艺优化,生产效率提高了20%。
2. 成本降低:原材料浪费减少,单位产品成本下降了15%。
3. 质量提升:客户投诉率下降了30%,产品一次合格率提高到98%。
改善案例报告
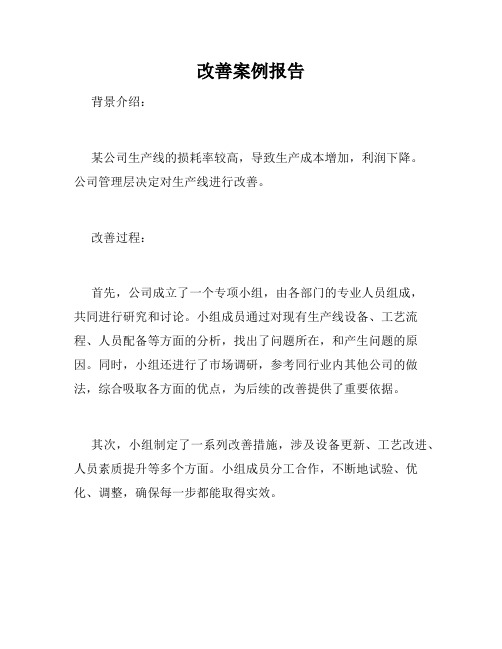
改善案例报告背景介绍:某公司生产线的损耗率较高,导致生产成本增加,利润下降。
公司管理层决定对生产线进行改善。
改善过程:首先,公司成立了一个专项小组,由各部门的专业人员组成,共同进行研究和讨论。
小组成员通过对现有生产线设备、工艺流程、人员配备等方面的分析,找出了问题所在,和产生问题的原因。
同时,小组还进行了市场调研,参考同行业内其他公司的做法,综合吸取各方面的优点,为后续的改善提供了重要依据。
其次,小组制定了一系列改善措施,涉及设备更新、工艺改进、人员素质提升等多个方面。
小组成员分工合作,不断地试验、优化、调整,确保每一步都能取得实效。
最后,在经过多次尝试后,公司成功地实施了一系列改善措施。
生产线的损耗率大幅下降,同时,产品的质量也有了明显的提升。
这一切,为公司的发展增添了助力。
改善结果:通过此次改善,不仅使公司得到了一次振奋,同时也发现了公司存在的不足和不良习惯。
公司经过不断的调整和完善,进一步提高了生产效率、降低了生产成本、改善了产品质量。
接着展开:从这次改善中,我们可以看到,一个企业想要成功,离不开不断地改进,不断地突破自我。
这需要有一个良好的团队合作,更需要领导的正确决策和坚定信念。
同时,对于一次成功的改善,我们也需要认真总结其成功的经验,在今后的发展中进一步提高业务技能和经验。
结论:改善不是一次性活动,而是一个企业需要持续关注的重点。
事实证明,在面对问题和挑战时,企业需要有高度的敏感性和反应力,只有不断地突破追求,才能在竞争中占据有利位置,实现可持续发展。
鱼骨图经典案例分析及改善报告

结果改善案例分析报告

结果改善案例分析报告近年来,随着企业竞争的加剧和市场环境的不断变化,越来越多的企业面临着业绩下滑、利润减少等问题。
为了应对这些挑战,企业需要不断寻求改善措施并推动其实施。
本文将以某公司为例,分析其改善案例并提出相应的建议。
某公司是一家制造业企业,主要生产汽车配件。
然而,最近几年,该公司面临着利润下降、产品质量问题、客户投诉增加等诸多挑战。
为了改善这些问题,公司制定了一系列的改善方案,并在一年的时间内进行了执行。
首先,针对利润下降的问题,公司进行了成本管理方面的改善。
通过对各个生产环节进行精细化的成本控制,公司降低了生产成本,提高了利润率。
例如,针对原材料采购成本,公司进行了供应商谈判并优化了供应链管理,降低了原材料采购成本;同时通过改善生产工艺和提高设备利用率,减少了设备折旧和生产周期,降低了生产成本。
其次,针对产品质量问题,公司进行了生产流程优化和质量控制方面的改善。
公司引入了先进的生产技术和质量管理方法,并对生产过程进行了全面的监控和管理。
通过合理安排生产流程、提高操作技能、加强设备维护等措施,公司成功降低了产品不良率。
此外,公司建立了完善的客户反馈机制,及时收集和处理客户投诉,并对相关问题进行深入分析和改进。
最后,为了应对客户投诉增加的问题,公司进行了客户关系管理方面的改善。
公司加强了与客户的沟通和合作,提高了产品的定制化能力和交货期可靠性。
此外,公司对销售团队进行了培训,加强了售前售后服务,提高了客户满意度。
通过以上一系列的改善措施,该公司取得了显著的效果。
利润率提高了10%,产品质量得到了显著改善,客户投诉量减少了20%。
这些改善不仅为公司带来了经济效益,也增强了公司在市场中的竞争力。
基于以上分析,针对该公司的改善案例,我们提出以下建议:首先,公司应继续注重成本管理,寻找降低成本的机会,并进一步提高利润率。
其次,公司应持续改进生产流程和质量控制,加强员工培训和设备维护,进一步提升产品质量。
化工企业改善案例报告范文

化工企业改善案例报告范文1. 简介本报告旨在介绍化工企业改善案例,探讨如何通过改进管理和工艺流程来提高企业的效益和竞争力。
本案例以某化工企业为例,通过引入先进的生产技术和管理理念,取得了显著的改善效果。
2. 基本情况该化工企业是一家中型企业,主要从事某种化学原料的生产和销售。
由于市场竞争的加剧,企业利润逐年下降并面临被淘汰的危险。
为了解决这个问题,企业决定进行全面的改善。
3. 改善方案3.1 引入先进的生产技术企业决定引进一套先进的生产设备,该设备具有高效率、低能耗的特点。
通过对生产设备进行改造和升级,生产效率得到了显著提高。
与此同时,企业还加大了对员工培训的力度,提高了员工的技术水平,使其能够更好地操作和维护新设备。
3.2 优化供应链管理传统的供应链管理方式效率低下,存在很多浪费和瓶颈。
为了提高供应链管理的效率,企业决定引入先进的ERP系统,实现供应链的透明化和自动化。
通过ERP系统,企业能够更好地控制原材料的采购和库存,减少了库存的积压和过剩,降低了原材料的损耗和浪费。
3.3 推行精益生产企业决定推行精益生产的理念,通过持续改进和消除浪费来提高生产效率。
为此,企业组织了一支专门的改善团队,负责进行现场改进和员工培训。
通过对生产流程的详细分析和改善,企业成功地减少了生产周期和生产成本,提高了产品的质量和交付能力。
3.4 加强质量管理质量是化工企业的核心竞争力之一,为了提高产品质量,企业决定引入全面质量管理体系,采取有效的措施控制和改进产品质量。
企业的质量管理部门定期对生产过程进行检查和监控,对不合格产品进行追溯和处理,确保产品符合国家和行业的相关标准。
4. 改善效果经过一段时间的努力,企业取得了显著的改善效果:- 生产效率提高了30%,生产成本降低了20%;- 产品质量得到了显著的提升,不合格率下降了50%;- 储备物料的积压量减少了50%,库存周转率提高了30%;- 员工的工作积极性和满意度得到了提高,员工流失率下降了20%。
案例:改善A3报告
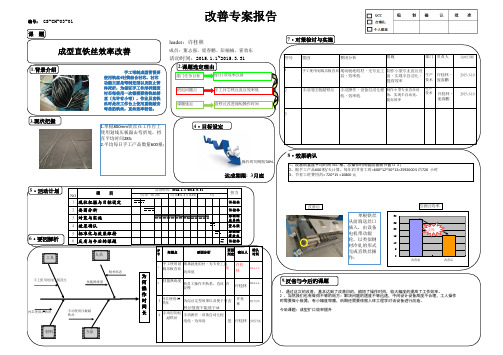
编号:GS-CH-03-01leader :许桂林成员:董志强、庞春鹏、彭楠楠、霍效东活动时间:2015.1.1~2015.3.31NO 1234改善比1071075改善前286改善后16现场就地取材,无专业工具效率低许桂林3为保证定型效果以及便于弯制否铁丝强度不能低于4#4手动操作,设备自动化程度低,效率低是许桂林衬芯使用4#铁丝2015/1/6手动用压板敲铁丝2015/1/61月第3周~2月第4周3月标准化与效果维持彭楠楠霍效东效果确认董志强活动时间:2015.1.1~2015.3.311月第一周~2周反省与今后的课题许桂林担当项 目要因分析许桂林对策与实施彭楠楠庞春鹏现状把握与目标设定许桂林改善专案报告51015202530改善前改善后成型直铁丝效率改善7‧对策检讨与实施6‧要因解析1.背景介绍4‧目标设定课題3.现状把握8‧效果确认5‧活动计划达成期限: 3月底2.课题选定理由人员工具材料精神状态方法手动使用压板敲铁丝衬芯使用4#铁丝技能熟练度为何操作时间长部门任务目标每月1项效率改善班组问题点手工衬芯铁丝直丝效率低课题选定直铁丝改进缩短操作时间许桂林2014-1-6否新员工操作不熟悉,直丝较慢技能熟练度22014-1-6许桂林是手工使用划线压板直丝1确认时间确认人要因判定要因分析问题点序号手工使用划线压板直丝9.反省与今后的课题1、通过这次的改善,基本达到了改善目的,缩短了操作时间,较大幅度的提高了工作效率。
2 、当然我们也有做得不够的地方:解决问题的速度不够迅速,中间设计设备高度不合理,工人操作时需要做小板凳,有小幅度弯腰,后期还需要依据人体工程学对该设备进行改造。
今后课题:成型扩口效率提升改善后43%改善后效率1.单根800mm 铁丝在工作台上使用划线压板敲击弯折处,捋直平均时间28S ;2.平均每日手工产品数量600根;操作时间缩短30%32015-3-10生产技术制作小型专业直丝设备,实现半自动化,提高效率手动操作,设备自动化程低,效率低手动用压板敲铁丝22015-3-10许桂林、庞春鹏生产技术制作小型专业直丝设备,实现半自动化,提高效率现场就地取材,无专业工具,效率低手工使用划线压板直丝1完成日期负责人部门措施要因分析要因序号1、改善后直丝平均时间16S/根,总操作时间较改善前节省12 S ;2、据手工产品600 根/天计算,每年约节省工时=600*12*30*12=2592000 S 约720 小时3、节省工时费用约= 720*15 =10800 元手工弯制成型管需要使用铁丝+衬簧组合衬芯,衬芯功能主要是弯制定型以及防止管体死折,为保证手工件形状精度衬芯每使用一次都需要将铁丝捋直(允许有小弯),作业员直铁丝时是在工作台上使用重物敲击弯曲的铁丝,直丝效率较低。
8D报告案例
–1. 文件标准化,修改搬运、贮存作业标准书. –2. 对库管课员工进行标准的培训宣贯.
五.8D改善案例
D8.恭贺小组
• 成效计算:以每卷成本50元计,改善前自99年5-1月统计 破损200卷,损失金额10,000元;改善后虽成本投入增加 1元,同样可减少损失9,800元.
五.8D改善案例
D5.长期对策
5.1决定采用长期对策
– 1.修改搬运、贮存作业方法,将原来搬运和堆放高度3层改 为2层,减少重力。 – 2.改变包装方法,每卷产品用托盘运装。 – 3.包装箱内部增加泡沫,以减少碰撞冲力。
五.8D改善案例 5.2验证长期对策(小批量验证)
小组采用同一规格20μMHT机用膜产品按照三 项措施各100卷进行小批量验证
5
25
0
0
A BC DE F GH
五.8D改善案例
4.3 确定根本原因并识别可能的方案
• 通过小组因果分析,验证统计确定产品堆放高度过高 、包装方式不合理是导致产品端口受损根本原因。
• 识别可能的解决方案。
– 修改搬运、贮存作业方法,将原来搬运 和堆放高度3层改为 2层,减少重力。
– 改变包装方法,每卷产品用托盘运装。 – 包装箱内部增加泡沫,以减少碰撞冲力。 – ……。
•经确认后,没有不良品再流出的可能,不会再扩大损 失。
五.8D改善案例
D4. 原因分析
•识别可能原因(因果图) • 选择最有可能的原因(矩阵图) • 确定是否是根本原因 • 识别可能方案
五.8D改善案例
4.1 因果分析
环
法
库房湿度大
精益改善案例提案改善报告
精益改善案例提案改善报告一、背景我们所处的公司是一家生产化妆品的企业,由于市场竞争激烈和内部管理不足等多种原因,导致生产效率低下,产品质量不稳定,在市场上的竞争力较弱。
为此,我们决定通过精益管理的方法来对生产过程进行改善,提高生产效率和产品质量,以增强企业的市场竞争力。
二、问题定义通过对企业生产过程的分析,我们发现以下问题:1. 生产过程中存在大量浪费,如原料浪费、等待时间浪费、生产线下停机时间浪费等,导致生产效率低下;2. 生产线某些工站出现了制造不良品的情况,存在质量问题;3. 生产过程中缺乏可视化管理,员工难以及时发现和解决问题。
三、改善方案针对上述问题,我们提出以下改善方案:1. 实施6S管理6S管理是指整理、整顿、清洁、清点、标准化和维护的管理方法,通过对现场进行整理、清理、标识等操作,去除生产过程中的浪费,提高生产效率。
同时,开展6S培训,增强员工的职业素养和安全意识,营造整洁有序的工作环境,提高工作效率和生产质量。
2. 引入可视化管理针对生产过程中缺乏可视化管理的问题,我们将引入可视化管理技术,将生产过程中的各项数据实时呈现在生产线上方的显示屏上,让员工随时了解生产状况,更好地发现和解决问题。
3. 实施质量管理和问题解决在生产过程中,存在不良品生成的情况,我们将加强质量管理,对生产过程中的各项质量参数进行监控和检测,及时发现和解决问题。
同时,我们将建立定期例会和工作汇报机制,及时解决员工工作中遇到的问题,为员工提供更好的工作支持。
四、实施计划通过培训,将6S管理理念传递至员工,开展整理、整顿、清洁等活动,打造整洁有序的生产环境,提高生产效率和产品质量。
引入并实施可视化管理系统,打造实时监控的全新生产模式,加强员工生产意识和工作效率,实现生产流程信息和数据的可视化和透明化。
五、效果预期通过精益管理的方法,我们期望实现以下效果:1. 生产效率提高:通过实施6S管理和改善流程,去除浪费,提高生产效率,降低生产成本。
工厂改善报告汇总
改善前 无
改善后
改善前问题点
改善后优点
因机床无水泵,加工过程中刀件易损坏, 在机床上安装循环水泵,安装冷却水管,对刀具进行冷却;机
严重影响刀具寿命,及加工效率,使刀 具寿命缩短,百分之六十左右,大约每
器 员设工计对A此过dd程给Y予中o设存ur计在T和一ex安定t 装缺道陷具,,需使要正额常外损加耗装下冷降却,水降泵低,了我生公产司
改善前 无
改善后
改善前问题点
改善后优点
由于空气湿度较大,空气机系统设备运 时形成水份过多,在过滤器中及储气罐 内积储,平均两至三小时放水一次也难 保证空气水分滤净,从而保证不了涂装 喷漆用气。
改善后:
从 棉节的省造A成人dd员喷Y漆及o质劳ur量动T缺强ex陷度t 。方面考虑,保证了涂装喷漆用气质量,
方案:修改设备程序,删除程序多余步骤,减少不必要的等待
时 和,间由,A原增dd来加Y的停o4止u0r秒时T的/e件x缓t提冲升,到减31小.5设秒备/件震,动整,体使提设升备效动率作2更1.2加5%柔,
提升后月生产能力可达10000多套,满足交付要求,并去掉手 动安装线;改善后能源节省:两台设备总功率为3千瓦,每年 可节省电费5000多元; 改善后人工节省:按每年12万套计算,可节省工时3400小时, 节省80000多元;
开A泵漆管阀门A1,B泵B2漆管,控制人员去换漆,日可节约60 分钟。
改善案例-〔 YFC组D立i机a效gr率a提m升〕
改善前 无
改善后 无
改善前问题点
改善后优点
YFC脚踏板月订单10000套,现双班四人 生产每天360套,月生产能力只能达到 8000套,无法满足交付需求,为满足交
付需求,需要增加手工线进行生产,手 工线每班3人,人员工时浪费较大;
超实用精益改善案例(某集团改善报告)
xxx精密机械有限公司
改善前生产现场
改善后生产现场
工具摆放不整齐,没有标示,经常用 工具时需要到处寻找工具浪费时间
工具摆放整齐、标示清楚明了, 员工不需要再寻找工具。
xxx精密机械有限公司
改善后标准工作表及负荷表
标准工作表
质量检验
起亚机
安全预防
+
哈斯 机
+
哈斯 机
+ +
品 检
+
半品
半品数量
3
北
接拍时间/U秒
1 下料
卧铣
15
5
1 下料
卧铣
10
3
2 飞底面
立铣
35
15
2 飞底面
立铣
30
15
3 铣长度
哈斯机
15
60
3 铣长度
哈斯机
10
64
4 铣内腔
起亚机
15
270
4 铣内腔
起亚机
10
110
5 铣外宽
哈斯机
15
80
5 铣外宽及沉孔 哈斯机
15
80
6 反面沉孔
佳铁
15
18
7 自检
60
6 自检
60
8 研磨去毛刺 振动研磨
120
周期时间/u秒
289
46302011生产线员工技能表
一级:(能培训员工,并且使他们能达到二级水平)
二级:(单独熟练操作)
三级:(能操作但不熟练)
产品
工序 下料
姓名
夏世强
飞面
46302011AG
铣长度 与粗加 工内腔
内腔精 加工
- 1、下载文档前请自行甄别文档内容的完整性,平台不提供额外的编辑、内容补充、找答案等附加服务。
- 2、"仅部分预览"的文档,不可在线预览部分如存在完整性等问题,可反馈申请退款(可完整预览的文档不适用该条件!)。
- 3、如文档侵犯您的权益,请联系客服反馈,我们会尽快为您处理(人工客服工作时间:9:00-18:30)。
改善案例-NSLED灯板不良改善一、成立改善小组
小组成员
二、选题
三、现状调查
从2011年1月到6月LED灯板不良持续上升,总不良数达到897件;到2011年6月份不良率达到1.31%,占总不良率的31%。
以下为897个不良品中,选取100个不良品进行测量分析的结果,主要不良现象为:R1损坏与LED断路。
四、设定目标
1、设定目标值:NSLED灯板不良率从6月的1.31%,6个月内下降至0.5%以下。
2、可行性分析:
LED灯板也作为PCB板的一种,可以把不良率控制在与其他PCB同一个水平线。
其他PCB不良在0.5%左右,LED灯板因为元器件比较少,并且LED的本身寿命比较长,不良率可以比其他PCB更低。
根据其他同行业不良率统计结果,同比情况下不良率也是可以控制在0.5%以下。
五、分析原因
六、要因确认
末端要因分析表
七、制定对策
八、对策实施
1、先对现有元器件进行测试合格后,把这些元器件填入图纸进行指定,并作为进货
检查项进行检查。
2、模拟实际使用条件进行寿命验证
使用条件:冰箱实际使用:10年=3650天
每天打开冰箱门次数:20次
每次打开平均时间:20秒
试验条件:5℃90%条件下测试
按照20秒开20秒关的循环测试 循环次数73000次,约34天 测试数量:30个
3、在工程检查项中,明确LED 灯检查方法,并对每批冰箱完成下线后再随机抽取进行检查。
4、单面板改成双面板,确保电气距离。
5、PCB 上追加压敏电阻及保险丝。
效果验证1:变更前与变更后进行雷击对比试验确认。
试验标准:
■ 电压:±2KV,±4KV,±6KV ■ 浪涌角度:0°,45°,90°,135° ■ 浪涌次数:每个电压,每个角度各3次 ■ 试验数量:3块LED 灯
对比试验结果
电压
改善前 改善后
±2KV 1.NG 铜箔烧断 2.NG 电阻及稳压管坏
OK
±4KV
OK
变更前
变更后
变更前
变更后
试验设备
±6KV
OK
不良现象:
效果验证2:电源噪音测试
试验顺序
极性
引加电源 试验时间
Pulse 周期及宽度
实验结果
1 ±
500V 各阶段别 5分钟
Pulse 周期 16ms Pulse 宽度 50ns ,1us
OK 2 1000V OK 3
1400V
OK 4 1600V OK 5 1800V OK 6
2000V
OK
6.其他改善:考虑实际安装干涉,电容式样及位置变更。
九、效果检查
2KV 限流电阻开路损坏,稳压二极管短路损坏,LED 灯不亮
2KV 铜箔烧断,LED 灯不亮
变更前
变更后
通过各种改善对策实施后,不良率逐渐下降,到12月不良率从6月的1.31%下降到0.42%,达成先前0.50%以下的目标。
分析:对策实际实施时间为8月,并且由于是市场不良,改善效果有滞后性。
十、经济效益
1.减少不良数:
根据1月到8月平均不良数,预测9月到12月不进行改善时的不良数。
1451/8*4=726件
实际9月到12月出现不良数:285件
2011年9月到12月减少不良数:726–285=441件
2012年整年预计减少不良数:1322件以上(考虑改善滞后性)
2.经济效益计算:
单件平均维修费用:120元(上门费+材料)
2011年9月到12月经济效益:120*441=52920元
2012年整年预计经济效益:120*1322=158640元
十一、巩固措施
1、将此次改善的设计方案作为标准化设计方案,在后续的新品开发上也同样使用此方案设计。
2、在此次改善中已通过寿命及其他试验的元器件列入合格元器件库,在其他LED灯板开发及其他PCB开发时继续使用此类合格元器件。
十二、总结与后续事项
1、总结:
通过本次改善小组活动,在公司层面上改善了市场不良,为公司节省了维修方面大量投入,并且给公司的品质形象带来了大的改善;在个人能力方面,提高了团队意识、品质意识、及技术方面有很大的提升,为今后类似改善小组的活动打下了基础。
2、后续事项
●通过本次改善,了解到在冰箱内潮湿环境下,依然存在LED灯板短路的隐患,
在今后的开发中需要对LED灯板外围结构进行密封处理,进一步进行改善。
●虽然大部分品牌冰箱LED灯板因为成本便宜采用RC电源方案,但是RC电源为
非隔离电源,整个LED灯板都带有强电,再加上冰箱内部潮湿环境及恶劣电源抗干扰能力差,始终存在品质隐患。
●如采用隔离电源方式,虽然可以在品质上提高,但是需要另外的隔离电源板及
另外的空间装配隔离电源,价格涨幅比较大,需要在后续开发项目中继续研讨。