看完这6条,酸铜镀液故障处理你也会
电镀铜常见故障
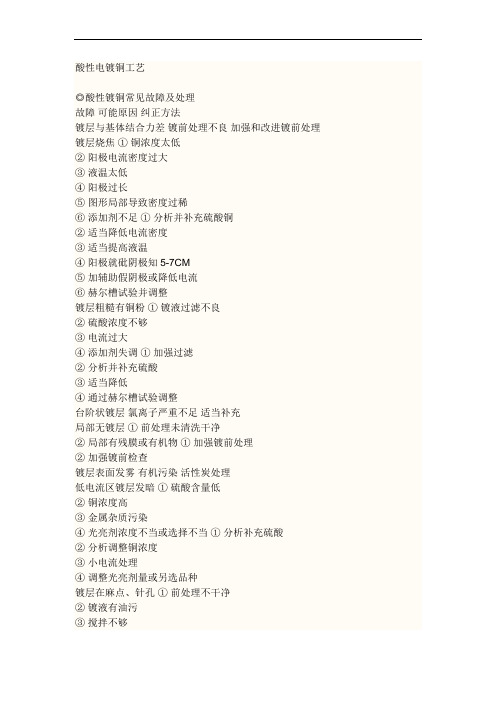
酸性电镀铜工艺◎酸性镀铜常见故障及处理故障可能原因纠正方法镀层与基体结合力差镀前处理不良加强和改进镀前处理镀层烧焦①铜浓度太低②阳极电流密度过大③液温太低④阳极过长⑤图形局部导致密度过稀⑥添加剂不足①分析并补充硫酸铜②适当降低电流密度③适当提高液温④阳极就砒阴极知5-7CM⑤加辅助假阴极或降低电流⑥赫尔槽试验并调整镀层粗糙有铜粉①镀液过滤不良②硫酸浓度不够③电流过大④添加剂失调①加强过滤②分析并补充硫酸③适当降低④通过赫尔槽试验调整台阶状镀层氯离子严重不足适当补充局部无镀层①前处理未清洗干净②局部有残膜或有机物①加强镀前处理②加强镀前检查镀层表面发雾有机污染活性炭处理低电流区镀层发暗①硫酸含量低②铜浓度高③金属杂质污染④光亮剂浓度不当或选择不当①分析补充硫酸②分析调整铜浓度③小电流处理④调整光亮剂量或另选品种镀层在麻点、针孔①前处理不干净②镀液有油污③搅拌不够④添加剂不足或润湿剂不足①加强镀前处理②活性炭处理③加强搅拌④调正或补充镀层脆性大①光亮剂过多②液温过低③金属杂质或有机杂质污染①活性炭处理或通电消耗②适当提高液温③小电流处理和活性炭处理金属化孔内有空白点①化学沉铜不完整②镀液内有悬浮物③镀前处理时间太长,蚀掉孔内镀层①检查化学沉铜工艺操作②加强过滤③改善前处理孔周围发暗(所谓鱼眼状镀层)①光亮剂过量②杂质污染引起周围镀层厚度不足③搅拌不当①调整光亮剂②净化镀液③调整搅拌阳极表面呈灰白色氯离子太多除去多余氯离子阳极钝化①阳极面积太小②阳极黑膜太厚①增大阳极面积至阴极的2倍②检查阳极含P是否太多。
硫酸铜电镀故障处理
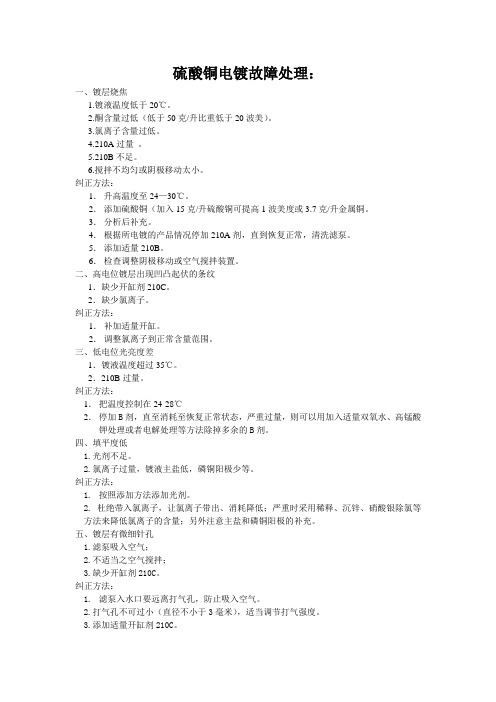
硫酸铜电镀故障处理:一、镀层烧焦1.镀液温度低于20℃。
2.酮含量过低(低于50克/升比重低于20波美)。
3.氯离子含量过低。
4.210A过量。
5.210B不足。
6.搅拌不均匀或阴极移动太小。
纠正方法:1.升高温度至24—30℃。
2.添加硫酸铜(加入15克/升硫酸铜可提高1波美度或3.7克/升金属铜。
3.分析后补充。
4.根据所电镀的产品情况停加210A剂,直到恢复正常,清洗滤泵。
5.添加适量210B。
6.检查调整阴极移动或空气搅拌装置。
二、高电位镀层出现凹凸起伏的条纹1.缺少开缸剂210C。
2.缺少氯离子。
纠正方法:1.补加适量开缸。
2.调整氯离子到正常含量范围。
三、低电位光亮度差1.镀液温度超过35℃。
2.210B过量。
纠正方法:1.把温度控制在24-28℃2.停加B剂,直至消耗至恢复正常状态,严重过量,则可以用加入适量双氧水、高锰酸钾处理或者电解处理等方法除掉多余的B剂。
四、填平度低1.光剂不足。
2.氯离子过量,镀液主盐低,磷铜阳极少等。
纠正方法:1.按照添加方法添加光剂。
2. 杜绝带入氯离子,让氯离子带出、消耗降低;严重时采用稀释、沉锌、硝酸银除氯等方法来降低氯离子的含量;另外注意主盐和磷铜阳极的补充。
五、镀层有微细针孔1.滤泵吸入空气;2.不适当之空气搅拌;3.缺少开缸剂210C。
纠正方法:1.滤泵入水口要远离打气孔,防止吸入空气。
2.打气孔不可过小(直径不小于3毫米),适当调节打气强度。
3.添加适量开缸剂210C。
六、镀层布满细小的微粒1.镀液内有悬浮的微小颗粒(例如活性炭粉)2.搅拌用之空气被污染。
3.田家硫酸铜时,过滤不充分。
4.使用不适当的阳极。
纠正方法:1.连续过滤镀液,建议使用助滤剂。
2.检查隔尘纲、隔油纲,最好使用无油气泵打气。
3.加强过滤,彻底滤清镀液。
4.使用合格的磷铜阳极。
七、阳极钝化1.主盐成分过高,或者温度过低形成主盐相对过高。
2.阳极袋堵塞。
3.镀液被大量铁杂质严重污染。
镀铜常见故障

(1)镀层发花或发雾。
1镀前处理不良,零件表面有油;清洗水或镀液中有油;2阳极面积太小或太短;3镀液中聚二硫二丙烷磺酸钠太多;4有机杂质太多;光亮剂没有搅均或十二烷基硫酸钠太少等会造成镀层发花或发雾。
分析故障,要先易后难,逐条进行。
例如先搅拌一下镀液,检查一下阳极面积,这样就可以排除由于光亮剂没有搅均和阳极面积太小而造成的故障。
同时也可从现象进行分析,假使发花现象仅出现在挂具下部的零件上,上部零件不发花,那就可能是阳极板太短而产生的,经检查并换上足够长的阳极板后,观察发花现象是否消失。
倘若发花现象出现在零件的向下面或挂具上部的零件上,那可能是清洗水或镀液中有油而引起的。
光亮硫酸盐镀铜对油污特别敏感,不管是毛坯上的油在镀前处理时未除净,还是镀前的清洗水或镀液中有微量的油,甚至是操作人员不干净的手摸了摸镀前的零件,都会使镀铜层发花。
假使原来镀铜出现发花或发雾,采用良好的前处理后,镀层不出现发花或发雾现象厂,证明原来的镀前处理有问题,应加强镀前处理。
否则,就应检查镀液中的情况。
镀液中是否有油,不但可以从现象进行判断,同时还可以通过小试验来了解。
取一定量的故障液做烧杯试验,先要使阴极样板上能看到类似于生产中的故障现象,接着对试验液进行除油处理,另外再取相同体积的故障液进行双氧水一活性炭处理,然后分别进行试验(试验液中需补充各种光亮剂)。
若用双氧水一活性炭处理过的镀液仍有发花或发雾,而经过除油处理的镀液不再出现发花或发雾,那么原镀液中有油,应进行除油处理。
假使用双氧水一活性炭处理后的镀液和经过除油处理的镀液一样,都不出现发花或发雾,那么原镀液可能是有机杂质过多。
只要用双氧水一活性炭处理镀液就可以了。
镀液中聚二硫二丙烷磺酸钠是否过多,只要向试验液中添加其他光亮剂,并适当稀释试验液后进行试验,假使经这样处理后镀层不发花(或不发雾),而且光亮度较好,这时可能原镀液中聚二硫二丙烷磺酸钠太多,应调整光亮剂的比例。
在含有十二烷基硫酸钠的镀铜液中,有时由于其含量过低,也会导致镀层出现发花现象。
酸性硫酸盐镀铜故障及其处理方法
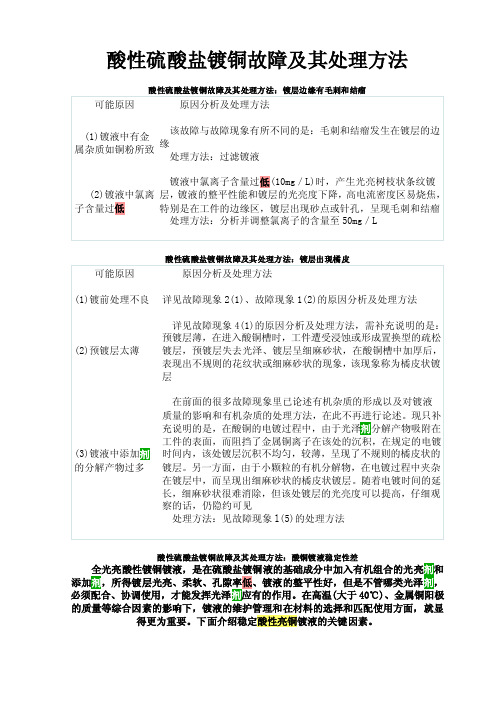
酸性硫酸盐镀铜故障及其处理方法
酸性硫酸盐镀铜故障及其处理方法:酸铜镀液稳定性差
全光亮酸性镀铜镀液,是在硫酸盐镀铜液的基础成分中加入有机组合的光亮剂和添加剂,所得镀层光亮、柔软、孔隙率低、镀液的整平性好,但是不管哪类光泽剂,必须配合、协调使用,才能发挥光泽剂应有的作用。
在高温(大于40℃)、金属铜阳极的质量等综合因素的影响下,镀液的维护管理和在材料的选择和匹配使用方面,就显得更为重要。
下面介绍稳定酸性亮铜镀液的关键因素。
酸性硫酸盐镀铜故障及其处理方法:沉积速度慢。
硫酸盐渡铜故障与处理

1、硫酸盐镀铜液故障的处理:整流电源如果用于光亮酸性镀铜的整流电源达不到一定的要求,镀铜层就达不到良好的光亮整平性及宽的范围。
经验表明:当采用硅整流器时,最好采用带平衡电抗器的六相双反星形整流,其波形好,相对节电;当采用可控硅整流器时,最好为五柱芯十二相整流并带平波电抗器。
一般三相全波或桥式硅整流器勉强可用,但效果不好。
三相全波或桥式可控硅整流器当负荷率达80%以上(如500A整流器必须开到400A 以上)勉强可用。
当波形良好的整流器因电源供电或内部故障造成三相缺相时,或可控硅与硅整流元件有损坏时,整流输出波形大大恶化。
若正常镀铜液突然效果不良时或几个相同镀槽采用相同整流器,其中一槽老是效果不如其他槽时,则应想到是否相应整流器出了毛病。
最好用示波器检查直流输出波形,也可用钳形电流表测定每个整流元件的工作电流,其相对误差不宜大于15%。
若某一个元件无电流或电流特别大,则应检查是否已损坏。
2、硫酸盐镀铜液故障的处理:含磷铜阳极酸性光亮镀铜使用的阳极必须是含磷铜阳极,这是由于纯铜阳极很容易溶解,使得阳极效率大于理论值。
这样,镀液中的铜含量逐渐增加,使硫酸铜大量积累,很快便超过了工艺规范上限而失去平衡。
另一方面纯铜阳极在溶解时会产生少量一价铜离子,它在镀液中很不稳定,通过歧化反应分解成为二价铜离子和微粒金属铜,在电镀过程中很容易在镀层上面成为毛刺。
为消除阳极一价铜的影响,人们最早使用阳极袋,但很快便发现泥渣过多妨碍了镀液的循环。
后改用无氧高导电性铜阳极(0FHC),虽然泥渣减少了,但仍不能阻止铜金属微粒的产生,于是又采用定期在镀液中加入双氧水使一价铜氧化成二价铜,但此法在化学反应中要消耗一部分硫酸,导致镀液中的硫酸质量浓度下降,必须及时补充,同时又要补充被双氧水氧化而损耗的光亮剂,增加了电镀成本。
1954年美国Nevers等人在纯铜中加入少量的磷作阳极时,发现阳极表面生成一层黑色胶状膜,在电镀时阳极溶解几乎不产生铜粉,泥渣极少,零件表面铜镀层不会产生毛刺。
酸性光亮镀铜故障处理
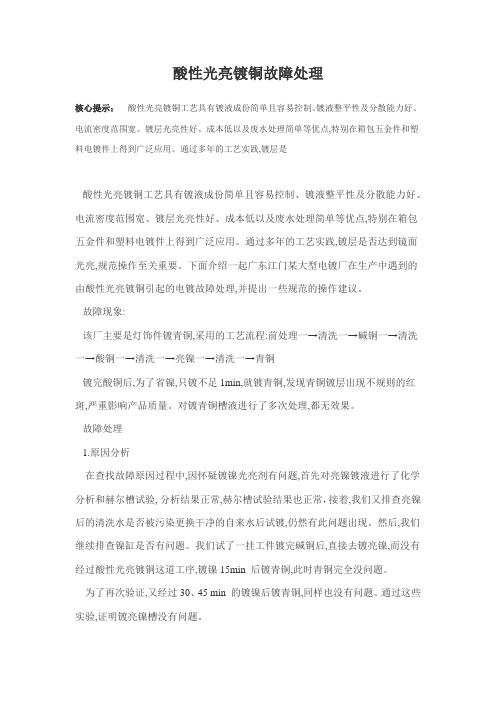
酸性光亮镀铜故障处理核心提示:酸性光亮镀铜工艺具有镀液成份简单且容易控制、镀液整平性及分散能力好、电流密度范围宽、镀层光亮性好、成本低以及废水处理简单等优点,特别在箱包五金件和塑料电镀件上得到广泛应用。
通过多年的工艺实践,镀层是酸性光亮镀铜工艺具有镀液成份简单且容易控制、镀液整平性及分散能力好、电流密度范围宽、镀层光亮性好、成本低以及废水处理简单等优点,特别在箱包五金件和塑料电镀件上得到广泛应用。
通过多年的工艺实践,镀层是否达到镜面光亮,规范操作至关重要。
下面介绍一起广东江门某大型电镀厂在生产中遇到的由酸性光亮镀铜引起的电镀故障处理,并提出一些规范的操作建议。
故障现象:该厂主要是灯饰件镀青铜,采用的工艺流程:前处理一→清洗一→碱铜一→清洗一→酸铜一→清洗一→亮镍一→清洗一→青铜镀完酸铜后,为了省镍,只镀不足1min,就镀青铜,发现青铜镀层出现不规则的红斑,严重影响产品质量。
对镀青铜槽液进行了多次处理,都无效果。
故障处理1.原因分析在查找故障原因过程中,因怀疑镀镍光亮剂有问题,首先对亮镍镀液进行了化学分析和赫尔槽试验, 分析结果正常,赫尔槽试验结果也正常,接着,我们又排查亮镍后的清洗水是否被污染更换干净的自来水后试镀,仍然有此问题出现。
然后,我们继续排查镍缸是否有问题。
我们试了一挂工件镀完碱铜后,直接去镀亮镍,而没有经过酸性光亮镀铜这道工序,镀镍15min 后镀青铜,此时青铜完全没问题。
为了再次验证,又经过30、45 min 的镀镍后镀青铜,同样也没有问题。
通过这些实验,证明镀亮镍槽没有问题。
但问题出现在哪道工序呢?我们又对镀铜进行排查口对酸性光亮镀铜液化学分析和赫尔槽试验,也没有发现什么问题,只不过赫尔槽试片显示添加剂有些过量和水线有些容易发黑而已。
再把酸性光亮镀铜槽后回收水、清洗水都更换,试镀仍然有问题。
最后我们把怀疑的焦点还是回到了酸性光亮镀铜。
对阳极进行了检查,发现表面有一层较厚的黑褐色膜,清洗后,试镀仍然不行。
酸性镀铜(故障处理方法)
c)阳极不合适或阳极电流密度过大(不可大于2.5A/平方分米
(9)光亮镍层在预镀铜上结合力差
a)填平剂过量
a)镀酸铜后10%的氢氧化钠液中电解处理30秒
(10)酸铜镀层在预镀镍上结合力差
a)预镀镍镀液含硫化物
a)采用不含硫的半光亮镍镀液
(11)镀层有微细针孔
a)滤泵吸入空气
c)增加阳极面积
d)检查导电情况
e)稀释镀液并分析是否补充其它原料
(7)加入添加剂后无相应效果
a)有机物污染
a)加入50-100毫克/升过硫酸钾(或钠)
b)加入5-10克/升活性碳份处理,然后补充添加剂
(8)添加剂消耗量大
a)镀液温度大于30℃
b)填平剂与光亮剂的添加比例不恰当
c)阳极表面污垢多
a)降温至正常工艺范围
a)过滤镀液
b)检查隔尘网,隔油网,最好用无油气泵打气,
c)检查温度,分析铜含量,氯离子
d)过滤镀液
e)使用磷铜阳极
(13)阳极钝化
a)硫酸含量过高
b)铜含量过高
c)氯离子含量过高
d)阳极袋堵塞
e)镀液被子大量铁杂质致使镀液比重过高
a)稀释镀液
b)稀释镀液
c)加入其它物质使其沉淀减少
d)清洗阳极袋
e)除杂质,稀释镀液
b)不适当的空气搅拌
c)缺少润湿剂
d)缺少开缸剂
a)滤泵入口要远离空气搅拌位置防止吸入气泡
b)打气喉之气孔不可过小,直径最好不小于3厘米
c)补足润湿剂
d)补加开缸剂
(12)镀层布满幼细的微粒
a)镀液内有悬浮的微细颗粒
b)搅拌的空气被污染
c)镀层烧焦形成海绵状镀层
酸性亮镀铜液镀层不亮是什么原因?如何处理?
酸性亮镀铜液镀层不亮是什么原因?如何处理?
酸性亮镀铜液镀层不亮是什么原因?如何处理?
原因:
①主盐及其他化学药品不纯。
硫酸铜系工业级,混有许多杂质,故配制溶液或平时添加后必须进行处理;
②添加剂消耗掉多少心中无数。
镀液中的添加剂随着工件的带出和镀层的夹杂而消耗掉,一部分添加剂在通电时.(电场作用下)发生电解而被分解、失效而影响镀层光亮;
③工艺条件的变化。
主要指镀液温度变化;
④阳极铜粉及l价铜的存在造成镀层不亮。
阳极铜粉通常是因阳极电流密度太大和阳极含磷量不适宜,使阳极出现钝化而产生。
l价铜离子也是源于某些还原剂带入或阳极钝化;
⑤氯离子含量的影响。
氯离子含量少使镀层发花,含量高使镀层光泽下降。
处理方法:
①可在硫酸铜电解液中加入1~2mL/L的H202(30%含量),再加入3g/L左右活性炭,同时消除有机杂质的影响。
硫酸应用化学纯级,因工业级的硫酸中铁等杂质太多,会使镀层不亮;
②应采用少加勤加的办法补充添加剂;
③要求温度保持10~35℃之间,当温度达38~40℃时,添加剂
消耗加快,补充量就多。
只有在最佳温度之内,才能获得光亮铜层;
④为消除l价铜的影响,每天加入30%的H2020.3mL/L,稀释后加入槽内(国外添加剂不用);
⑤一般控制氯离子含量在l0~80mg/L(国外添加剂除外)。
电镀常见故障原因与排除
4.调整PH值在8.5-9.0之间
5.双氧水-活性炭处理
镀层结合力不好
1.镀前处理不良
2.镀前没有良好活化
3.清洗水有油或活化酸有油
4.预镀层太薄
5.活化酸中有二价侗或二价铅杂质
6.镀液有油或六价铬
1.加强镀前处理
2.加强活化
3.更换清洗水或活化酸
4.加强预镀层厚度
3.PH值过高或温度过低
1.添加DY柔软剂
2.添加DY除杂水或小电流电解
3.提高PH值或提高温度
沉积速度慢
零件的深位镀不上镀层
1.镀液中有六价铬
2.镀液中有硝酸根
3.电流密度太小
1.将PH值调至3,加温至60℃,加入0.2-0.4克/升保险粉,搅拌60分钟,将PH值调至6.2,搅拌30分钟,加入0.3-0.5毫升/升30%的双氧水
2.镀液中有微细固体粒子
3.硫酸含量过低
4.阴极电流密度过大
1.加强底层质量
2.过滤
3.提高硫酸含量
4.降低电密度
氯化物酸性镀锌常见故障原因与排除方法
故障现象
故障原因
故障排除方法
镀层起泡
结合力不好
1.镀前处理不良
2.添加剂过多
3.硼酸过低
4.阴极电流密度过大
1.加强前处理
2.用活性炭吸附
3.补充硼酸
1.稀释镀液,调整各成分
2.提高硫酸含量
3.提高温度
4.增加阳极面积
5.用锌粉处理,方法同上
焦磷酸镀铜常见故障原因与排除方法
故障现象
镀层粗糙
故障原因
1.基体或预镀层粗糙
2.镀液中有铜粉或其它固体微粒
光亮酸性镀铜故障处理
光亮酸性镀铜故障处理1》镀层粗糙和毛刺(1)镀液中硫酸铜浓度过高或过低(处理:分析调整硫酸铜(150~220g/L)与硫酸(50~70g/L)质量浓度之比,一般为3:1。
硫酸铜的质量浓度过高,尤其是冬季,电极上、槽壁上会析出硫酸铜结晶,镀层产生毛刺;过低,则镀层粗糙。
)(2)阳极含磷量不足或过多(处理:检验阳极的含磷量。
其磷的质量分数应在0.04%~0.07%范围内。
若磷的质量分数低于0.02%时,形成的膜难以阻止一价铜离子的产生,而使镀液中铜粉增多;若磷的质量分数超过0.1%时,影响铜阳极的溶解,使镀液中二价铜离子的含量下降,并生成大量阳极泥。
平时要使用聚丙烯阳极袋,最好经过拉毛处理的,防止阳极泥污染镀液而造成镀层粗糙和毛刺。
)(3)镀液中混进了固体微粒或硫酸铜原料中有不溶性物质(处理:过滤溶液,如倒缸后仍引起毛刺,应检查过滤机、阳极袋。
检查硫酸铜中有无不溶性物质,可将硫酸铜原料溶解于水中,如呈混浊状,说明有不溶物质,应改用高纯度优质硫酸铜。
平时镀液最好采用连续过滤,既能消除一价铜,又能将悬浮物滤掉。
如在过滤机里加入少量大颗粒活性炭,还能把镀液中有机物一并除去,使镀液更清洁。
)(4)镀液中氯离子含量过高(处理:去除多余氯离子的方法很多,如锌粉法、银盐沉淀及去氯剂处理。
建议采用比较经济的稀释法,即根据分析氯离子的含量,先取出部分镀液,然后加水稀释,再补充硫酸铜、硫酸和光亮剂至工艺范围。
平时要采取各种措施,防止镀液中氯离子的积累。
一般氯离子控制在20~80mg/L,也有控制在50~120mg/L,视镀层质量而定。
)(5)氰化物镀铜打底的镀层上出现粗糙或毛刺(处理:检查氰化物镀铜后的工件表面,如有毛刺,过滤氰化物镀铜液。
)(6)微粒从压缩空气搅拌中混入(处理:检查,并清洗送风机、管道、空气过滤器。
)(7)镀液中有铜粉或一价铜(处理:加双氧水)(8)电流过大(处理:调整电流)(9)导电不良(处理:改善导电性能)(10)添加剂不足(处理:补加添加剂)(11)阳极质量不好(处理:改善阳极板)(12)Fe离子干扰(处理:电解、过滤)2》镀层出现针孔(1)清洗槽、酸洗槽、活化槽、氰化物镀铜槽和酸性镀铜槽被油污染(处理:更换清洗水、酸浸蚀液。
- 1、下载文档前请自行甄别文档内容的完整性,平台不提供额外的编辑、内容补充、找答案等附加服务。
- 2、"仅部分预览"的文档,不可在线预览部分如存在完整性等问题,可反馈申请退款(可完整预览的文档不适用该条件!)。
- 3、如文档侵犯您的权益,请联系客服反馈,我们会尽快为您处理(人工客服工作时间:9:00-18:30)。
看完这 6 条,酸铜镀液故障处理你也会
现代电镀网 5 月 5 日讯:
故障现象
可能原因 1.前处理不良 2.预镀层太薄 3.导电接触不良 4.镀液中硫酪铜含量太低 1.光亮剂剂不足 2.CI—偏高或不足 3.镀液温度高 4.硫酸含量偏高或硫酸铜偏低 5.镀液有杂质污染 6.阳极面积不够
纠正办法 1.加强前处理 2.加厚预镀层 3.检查并纠正 4.分析补充到配方规定范围内 1.用霍尔槽试样,适当补加 2.化验调整,偏高可用硫酸银或氧化亚铜 处理 3.降温 4.分析调整 5.对症处理 6.补加阳极 1.适当补加 2.降温 3.加大 DK 4.检查阳极,加双氧水 5.对症处理 1.分析处理 1.加强前处理 2.加双氧水 3.加计算量盐酸 4.对症处理 1.加计算量盐酸 2.调整之 1.适当升温 2.适量补充 3.适当降低 DK 1.霍尔槽小试调整 2.补充 加强前处理 1.加入计算量盐酸 2.调整 3.对症处理
结合力不好
镀层光亮度不足
1.光亮剂不足 2.镀液温度偏高 低 DK 处光亮度不足 3.DK 不够大 4.镀液中有铜粉或一价铜 5.镀液有杂质污染 1.光亮剂过量 1.前处理不良 2.镀液中有铜粉或一价铜 3.CI—不足 4.镕液内有杂质乐势 1.CI—偏低 2.光亮剂过量 1.镀液温度偏低 2.硫酸铜浓度偏低 3.DK 过大 1.润湿剂过量或不足 2.310B 不足 前处理不良 整平性不良 1.CI—偏低 2.硫酸含量偏高 3.镀液有杂质污染
镀层粗糙有针孔
条纹镀层 镀层边缘有毛刺或 烧焦
1.铁杂质过量,此时阳极上往往有蓝色结晶 1.更换部分或全部镀液 析出
。