新工艺制备微晶玻璃
一种高结晶度锂铝硅透明微晶玻璃及其制备方法

一种高结晶度锂铝硅透明微晶玻璃及其制备方法在当代材料科学领域,锂铝硅透明微晶玻璃因其卓越的物理和化学性能而备受关注。
本文将介绍一种具有高结晶度的锂铝硅透明微晶玻璃及其制备方法,该材料在光学、热学以及机械性能方面表现出色,有望在高科技领域得到广泛应用。
一、高结晶度锂铝硅透明微晶玻璃的概述高结晶度锂铝硅透明微晶玻璃是一种新型的无机非晶材料,其主要成分为锂、铝、硅以及少量的氧化钠、氧化钾等。
该玻璃具有较高的结晶度,晶体尺寸细小且分布均匀,因此具有优异的透明性、机械强度、热稳定性和化学稳定性。
二、制备方法1.原料准备:选取高纯度的锂、铝、硅原料,以及适量的助熔剂和晶核剂。
2.混合配料:按照一定的比例将原料混合均匀,确保各组分充分接触。
3.熔融:将混合好的原料放入高温炉中进行熔融,温度控制在1600-1800℃之间,保温一定时间,使原料充分熔化。
4.浇注:将熔融的玻璃液倒入预热的模具中,进行浇注成型。
5.退火:将浇注成型的玻璃进行退火处理,以消除内应力,提高玻璃的透明度。
6.热处理:将退火后的玻璃进行热处理,以促进晶体生长,提高结晶度。
7.冷加工:对热处理后的玻璃进行切割、打磨等冷加工,以满足实际应用需求。
三、性能特点1.优异的透明性:高结晶度锂铝硅透明微晶玻璃具有良好的透明性,可见光透过率可达90%以上。
2.高机械强度:该玻璃具有较高的弯曲强度和抗压强度,可满足高强度应用场景的需求。
3.良好的热稳定性:该玻璃具有较低的热膨胀系数,耐热冲击性能优良。
4.优异的化学稳定性:该玻璃具有良好的耐酸碱性和耐腐蚀性,可应用于复杂环境。
四、应用领域高结晶度锂铝硅透明微晶玻璃可广泛应用于光学、电子、建筑、航空航天等领域,如高性能显示屏、光学仪器、防弹玻璃、高温观察窗等。
本文介绍了一种高结晶度锂铝硅透明微晶玻璃及其制备方法,该材料具有优异的物理和化学性能,有望在多个领域发挥重要作用。
微晶玻璃制备工艺流程
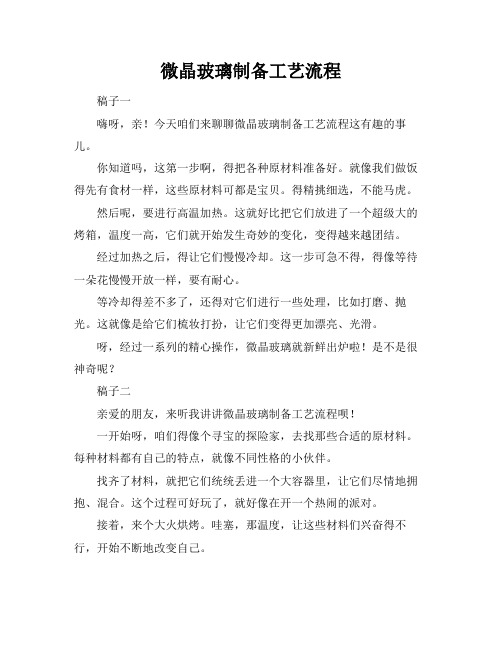
微晶玻璃制备工艺流程
稿子一
嗨呀,亲!今天咱们来聊聊微晶玻璃制备工艺流程这有趣的事儿。
你知道吗,这第一步啊,得把各种原材料准备好。
就像我们做饭得先有食材一样,这些原材料可都是宝贝。
得精挑细选,不能马虎。
然后呢,要进行高温加热。
这就好比把它们放进了一个超级大的烤箱,温度一高,它们就开始发生奇妙的变化,变得越来越团结。
经过加热之后,得让它们慢慢冷却。
这一步可急不得,得像等待一朵花慢慢开放一样,要有耐心。
等冷却得差不多了,还得对它们进行一些处理,比如打磨、抛光。
这就像是给它们梳妆打扮,让它们变得更加漂亮、光滑。
呀,经过一系列的精心操作,微晶玻璃就新鲜出炉啦!是不是很神奇呢?
稿子二
亲爱的朋友,来听我讲讲微晶玻璃制备工艺流程呗!
一开始呀,咱们得像个寻宝的探险家,去找那些合适的原材料。
每种材料都有自己的特点,就像不同性格的小伙伴。
找齐了材料,就把它们统统丢进一个大容器里,让它们尽情地拥抱、混合。
这个过程可好玩了,就好像在开一个热闹的派对。
接着,来个大火烘烤。
哇塞,那温度,让这些材料们兴奋得不行,开始不断地改变自己。
烘烤完了,不能着急,得慢慢等它们凉快下来。
这时候就像是让它们休息一下,喘口气。
等它们休息好了,再给它们来个“美容护理”,把不平整的地方磨一磨,让它们变得亮晶晶的。
在整个过程中,每一步都得小心翼翼,就像照顾小宝宝一样。
不然一不小心,可就前功尽弃啦。
当看到那完美的微晶玻璃出现在眼前,心里那个美呀,别提多有成就感啦!。
微晶玻璃生产工艺设计
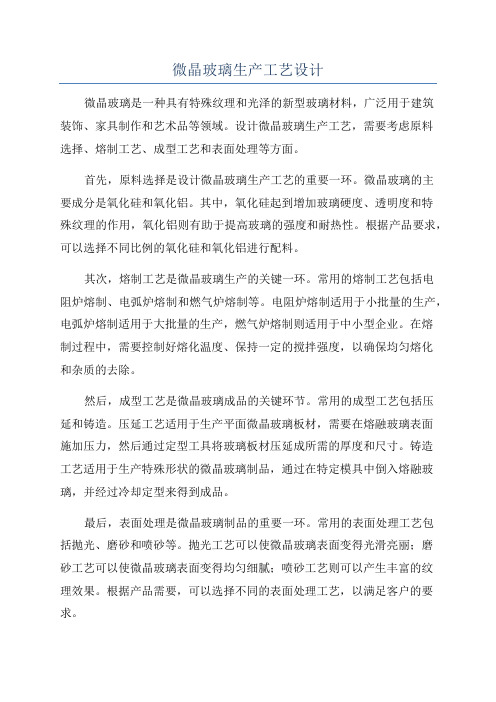
微晶玻璃生产工艺设计微晶玻璃是一种具有特殊纹理和光泽的新型玻璃材料,广泛用于建筑装饰、家具制作和艺术品等领域。
设计微晶玻璃生产工艺,需要考虑原料选择、熔制工艺、成型工艺和表面处理等方面。
首先,原料选择是设计微晶玻璃生产工艺的重要一环。
微晶玻璃的主要成分是氧化硅和氧化铝。
其中,氧化硅起到增加玻璃硬度、透明度和特殊纹理的作用,氧化铝则有助于提高玻璃的强度和耐热性。
根据产品要求,可以选择不同比例的氧化硅和氧化铝进行配料。
其次,熔制工艺是微晶玻璃生产的关键一环。
常用的熔制工艺包括电阻炉熔制、电弧炉熔制和燃气炉熔制等。
电阻炉熔制适用于小批量的生产,电弧炉熔制适用于大批量的生产,燃气炉熔制则适用于中小型企业。
在熔制过程中,需要控制好熔化温度、保持一定的搅拌强度,以确保均匀熔化和杂质的去除。
然后,成型工艺是微晶玻璃成品的关键环节。
常用的成型工艺包括压延和铸造。
压延工艺适用于生产平面微晶玻璃板材,需要在熔融玻璃表面施加压力,然后通过定型工具将玻璃板材压延成所需的厚度和尺寸。
铸造工艺适用于生产特殊形状的微晶玻璃制品,通过在特定模具中倒入熔融玻璃,并经过冷却定型来得到成品。
最后,表面处理是微晶玻璃制品的重要一环。
常用的表面处理工艺包括抛光、磨砂和喷砂等。
抛光工艺可以使微晶玻璃表面变得光滑亮丽;磨砂工艺可以使微晶玻璃表面变得均匀细腻;喷砂工艺则可以产生丰富的纹理效果。
根据产品需要,可以选择不同的表面处理工艺,以满足客户的要求。
综上所述,设计微晶玻璃生产工艺需要考虑原料选择、熔制工艺、成型工艺和表面处理等方面。
通过合理的工艺设计和优质的原材料,可以生产出质量优良、纹理独特的微晶玻璃制品。
微晶玻璃合成方法

微晶玻璃合成方法
微晶玻璃是一种新兴的材料,具有良好的透明性、耐热性和硬度,广泛应用于光电、光学和电子领域。
以下是微晶玻璃合成方法:
1. 溶胶-凝胶法
该方法是将适当比例的硅源和其他金属氧化物以适当的溶剂中溶解,形成溶胶,经凝胶反应后形成凝胶体。
通过高温热处理,可将凝胶体转化为微晶玻璃。
2. 气相沉积法
气相沉积法是将金属氧化物的气相混合,经催化剂的作用,在合适的条件下形成固体颗粒,最终形成微晶玻璃。
3. RF磁控溅射法
该方法将金属靶材表面加热后,利用载气将金属原子或分子离子化,然后通过电场引导原子或分子沉积到基板上,形成微晶玻璃。
4. 熔融过程
该方法是利用传统的熔融工艺,将原料熔融后快速冷却,形成微晶玻璃。
这种方
法不仅操作简单,而且可以制备大量的微晶玻璃。
溶胶凝胶制备玻璃

溶胶凝胶技术制备微晶玻璃摘要:玻璃的制备工艺多种多样,而用溶胶-凝胶法制备玻璃是近年来兴起的新工艺,本文简单介绍了利用溶胶-凝胶法制备微晶玻璃的状况。
关键词:溶胶凝胶;微晶玻璃;新型;0 前言玻璃是一种经过高温熔融得到的非晶态固体材料,具无规则结构的非晶态无机物,原子排列近似液体,近程有序,形状又象固体那样保持一定的形状。
通常可按照生产工艺、成分和性能进行分类,具有各向同性、亚稳性、无固定熔点、可逆渐变性和连续性的特性。
玻璃的制备方法多种多样,根据不同的方法可分别从固态、气态、液态进行制备[1]。
气态:气体辉光放电法、电解沉积法、溅射法、化学气相沉积法、物理气相沉积法;液态:急冷法(熔融冷却法);固态:粉末冶金法。
这些方法都是较为传统的制备方法。
随着制备技术的不断研究和发展,一些新的制备技术不断被应用于制备玻璃。
如:辐照法、悬浮熔炼技术、溶胶-凝胶法、落管技术、粒子注入法、冲击波法、低熔点氧化物包裹法等。
其中急冷法又可以细化出几种:喷枪法、锤砧法、离心法、压延法、单辊法、熔体沾出法和融滴法。
溶胶-凝胶合成法是在20世纪60年代中期作为制备玻璃、陶瓷材料的一种工艺发展起来的、在低温或温和条件下合成无机化合物和无机材料的重要方法。
溶胶是指微粒尺寸介于1-100nm之间的固体质点分散于介质中所形成的多相体系;凝胶则是溶胶通过凝胶化作用(gelation)转变而成的、含有亚微米孔和聚合链的相互连接的坚实的网络,是一种无流动性的半刚性(semi-rigid)的固相体系。
1 特点溶胶-凝胶法的优点:①通过溶液混合,易获得需要的均相多组分体系;②可大幅降低制备温度,在较温和的条件下合成出陶瓷、玻璃、纳米复合材料等功能材料;③可制备高纯或超纯物质,且可避免在高温下对反应容器的污染等问题;④溶胶或凝胶的流变性质有利于某种技术如喷射、旋涂、浸拉、浸渍等的实现。
该制备方法存在的不足:①原料(金属醇盐)价格昂贵,醇的回收使技术和设备投资增加,且有机物危害健康,工业化生产有一定难度;②整个溶胶-凝胶过程通常需几天或几周的时间,时间较长;③凝胶中存在大量微孔,干燥过程中会逸出许多气体和有机物,干燥收缩大。
微晶玻璃制备工艺优缺点分析
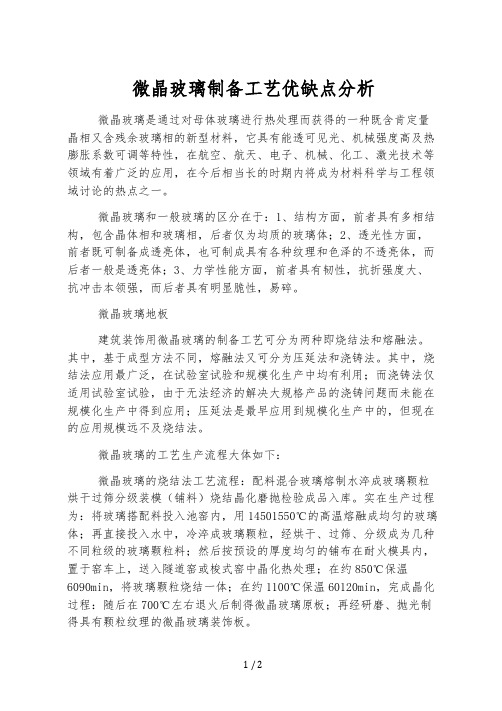
微晶玻璃制备工艺优缺点分析微晶玻璃是通过对母体玻璃进行热处理而获得的一种既含肯定量晶相又含残余玻璃相的新型材料,它具有能透可见光、机械强度高及热膨胀系数可调等特性,在航空、航天、电子、机械、化工、激光技术等领域有着广泛的应用,在今后相当长的时期内将成为材料科学与工程领域讨论的热点之一。
微晶玻璃和一般玻璃的区分在于:1、结构方面,前者具有多相结构,包含晶体相和玻璃相,后者仅为均质的玻璃体;2、透光性方面,前者既可制备成透亮体,也可制成具有各种纹理和色泽的不透亮体,而后者一般是透亮体;3、力学性能方面,前者具有韧性,抗折强度大、抗冲击本领强,而后者具有明显脆性,易碎。
微晶玻璃地板建筑装饰用微晶玻璃的制备工艺可分为两种即烧结法和熔融法。
其中,基于成型方法不同,熔融法又可分为压延法和浇铸法。
其中,烧结法应用最广泛,在试验室试验和规模化生产中均有利用;而浇铸法仅适用试验室试验,由于无法经济的解决大规格产品的浇铸问题而未能在规模化生产中得到应用;压延法是最早应用到规模化生产中的,但现在的应用规模远不及烧结法。
微晶玻璃的工艺生产流程大体如下:微晶玻璃的烧结法工艺流程:配料混合玻璃熔制水淬成玻璃颗粒烘干过筛分级装模(铺料)烧结晶化磨抛检验成品入库。
实在生产过程为:将玻璃搭配料投入池窑内,用14501550℃的高温熔融成均匀的玻璃体;再直接投入水中,冷淬成玻璃颗粒,经烘干、过筛、分级成为几种不同粒级的玻璃颗粒料;然后按预设的厚度均匀的铺布在耐火模具内,置于窑车上,送入隧道窑或梭式窑中晶化热处理;在约850℃保温6090min,将玻璃颗粒烧结一体;在约1100℃保温60120min,完成晶化过程:随后在700℃左右退火后制得微晶玻璃原板;再经研磨、抛光制得具有颗粒纹理的微晶玻璃装饰板。
微晶玻璃的熔融法工艺流程:将玻璃搭配料熔融成玻璃液后,采纳适当的成型方法制成母玻璃板,退火后直接进入晶化窑,经肯定的晶化热处理后,制成晶粒细小、含量多、结构均匀的微晶玻璃制品。
溶胶-凝胶技术制备新型微晶玻璃

2) 水解反应 :非电离式分子前驱物 ,如金属醇盐 M (OR) n ,n 为金属 M 的原子价 ,R 代表烷基 ,与水反应 :
M(OR) n + xH2O M(OH) x (OR) n - x + xROH 反应可延续进行 ,直至生成 M(OH) n 。
3) 缩聚反应 :可分为 失水缩聚 : - M - OH + HO - M M - O - M - + H2 O 失醇缩聚 : - M - OR + HO - M M - O - M - + ROH
传统的该类微晶玻璃的典型是光敏微晶玻璃 ,而 用溶胶 - 凝胶法将金属单质 Au 、Ag 等在 SiO2 玻璃中 均匀析出形成的具有复相结构的材料 ,却具有独特的 光学性能和半导体特性 ,其在压敏 、气敏 、湿敏等领域 具有广泛的潜在应用 。 3. 1. 2 氧化物半导体复相微晶玻璃[10]
以氧化物半导体如 ZnO 、CdO 、FeO 等过渡金属氧 化物与玻璃复合而形成的复相结构 ,通常具有良好的 电性能 ,这类材料在电子压敏材料等方面有着广阔的 应用前景 。 3. 1. 3 化合物半导体复相微晶玻璃[9~10]
要使不同反应速度的多组分同时形成均匀的溶 胶 ,需要对反应速度慢的组分进行预反应 ,或者抑制反 应速度快的组分 ,有时采用多原子的金属醇盐也是必 不可少的 。加入乙醇溶剂来抑制金属醇盐和水的混合 物的不互溶 ,也可以用超声的方法来加以克服 。 2. 1. 2 干燥
干燥阶段是至关重要的 ,尤其是制备块状材料时 , 更需要有效的干燥方法 ,这方面的研究已很多 。以前 用于制备多孔催化剂载体的超临界干燥 ,为制备无裂 纹的块状材料提供了一种有效的方法 。DCCA ( drying control chemical additives) 为制备大块材料开辟了新的 途径 ,而不需要复杂的预先自动蒸压过程 。 2. 1. 3 气氛处理
微晶玻璃的制备原理及其工艺过程

微晶玻璃的制备原理及其工艺过程一、微晶玻璃的制备原理微晶玻璃的制备主要通过两种方式实现:一种是熔融法,另一种是溶胶-凝胶法。
在熔融法中,玻璃材料首先被加热熔化,然后通过凝固过程形成微晶结构;在溶胶-凝胶法中,玻璃材料首先被溶解在溶剂中形成胶体溶液,然后通过凝胶过程形成微晶结构。
下面分别介绍这两种方法的制备原理。
1. 熔融法熔融法是最常用的微晶玻璃制备方法之一,其制备原理如下:首先将玻璃材料加热至熔化状态,然后通过控制降温速度和结晶条件,使其形成微晶结构。
具体步骤为:首先选取合适的玻璃成分,按一定比例混合搅拌;然后将混合了的玻璃粉末或块料加热至一定温度,使其熔化成液体;接着控制降温速度,使液态玻璃逐渐凝固结晶,形成微晶结构。
2. 溶胶-凝胶法溶胶-凝胶法是一种通过溶液的化学反应形成凝胶,然后通过加热干燥凝胶形成玻璃的方法。
其制备原理如下:首先将玻璃原料溶解在溶剂中形成胶体溶液;然后通过化学反应或加热使胶体溶液发生凝胶化反应,形成凝胶;最后将凝胶干燥成固体微晶玻璃。
二、微晶玻璃的制备工艺过程微晶玻璃的制备工艺过程包括以下步骤:原料准备、配料混合、熔炼、成型、退火、抛光等。
下面逐步介绍微晶玻璃的制备工艺过程。
1. 原料准备首先需要选取适合的玻璃成分,通常包括硼、硅、氧、钠、铝等元素。
这些原料按照一定比例进行称量,然后通过干燥、筛分等工艺处理,以确保原材料的质量和粒度符合要求。
2. 配料混合将称量好的原料按照配方比例混合搅拌,使各种元素均匀分布。
混合的过程一般在干燥室内进行,以防止水分对玻璃成分的影响。
3. 熔炼混合好的玻璃成分被加热至高温,使其熔融成液体。
熔炼温度一般在1200℃以上,根据不同的成分可以有所调整。
在熔炼过程中,需要不断搅拌,以确保成分混合均匀。
4. 成型熔融玻璃液通过拉拔、注射、压铸等方式成型,形成所需形状的微晶玻璃坯料。
成型过程需要控制温度、压力等参数,确保成型的精度和质量。
5. 退火成型后的微晶玻璃坯料进行退火处理,即将其加热至一定温度,然后缓慢冷却。
- 1、下载文档前请自行甄别文档内容的完整性,平台不提供额外的编辑、内容补充、找答案等附加服务。
- 2、"仅部分预览"的文档,不可在线预览部分如存在完整性等问题,可反馈申请退款(可完整预览的文档不适用该条件!)。
- 3、如文档侵犯您的权益,请联系客服反馈,我们会尽快为您处理(人工客服工作时间:9:00-18:30)。
尾矿微晶玻璃制备新工艺
利用尾矿制作微晶玻璃国内外已进行了大量研究,目前制作尾矿微晶玻璃装饰板的方法主要有压延法、浇铸法和烧结法。
压延法为前苏联在20世纪70年代所创,国内技术还不成熟,生产中析晶难以控制,板材炸裂严重,成品率低。
浇铸法是将熔化澄清好的玻璃液浇注在模具上,再置于晶化炉中晶化和退火处理。
国内尚无厂家采用此法生产。
浇铸法对模具质量要求高,生产效率,成品率低,生产大规格板材困难,对某些异形板的生产有一定优势。
烧结法为日本首创,是将熔融玻璃液水淬而得颗粒料与晶化分成二次烧成。
它将玻璃工艺、陶瓷工艺、石材加工工艺有机“融合”,目前国内已形成规模和效益,占整个建筑装饰微晶玻璃市场99%以上的企业均采用烧结法生产工艺。
烧结法目前最大的问题是表面层致密化深度浅(2mm左右),内部气孔难以排除,板材容易变形(尤其是大规格)。
尽管国内许多学者对上述问题进行了大量研究,但至今仍未得到解决。
综上所述,现有三种制作尾矿微晶玻璃板的方法都存在不同缺陷。
比较而言,烧结法进行了工业化生产,技术相对成熟,目前尾矿微晶玻璃的生产绝大部分采用烧结法。
本研究在充分吸收熔融浇铸法和烧结法优点的基础上,提出一种制作尾矿微晶玻璃板的新方法———碎粒压延法,是通过控制水淬玻璃的颗粒级配及颗粒加入量生产微晶玻璃的工艺方法。
实验过程
微晶玻璃主要原料为宜春钽铌矿选矿时产生的尾矿。
钽铌尾矿的化学成分和粒度组成见表 1和表 2。
钽铌尾矿的主要矿物组成为钠长石、锂云母和高岭土。
由表 1可见, 钽铌尾矿主要化学成分为 SiO2 和 A l2O3 ,另外还含有一定量的 K2O 、Na2O 和 Li2 O,这些碱金属氧化物的存在可降低玻璃熔化温度和降低玻璃粘度, 没有发现 C aO,且 Fe2 O3 含量很低,为微晶玻璃的制作提供了有利条件。
由表 2可见,粒度小于 0. 1mm 的颗粒占 32. 25%, 0.
1 ~ 0. 56mm 的颗粒占 67. 75%,经过简单过筛处理后可直接应用。
基础玻璃成分选择在 CaO - A l2 O3 - S Oi2 系统的玻璃形成区内, 基础玻璃化学组成见表 3。
CaO 以化学纯氧化钙引入, Na2O 以无水碳酸钠引入,其他组分均由钽铌尾矿引入。
引入 CaO 的目的是为了形成合适的微晶相,引入 Na2 O的目的是降低玻璃的熔化温度和改
善玻璃的成型性能。
碎粒压延法工艺过程如下 :钽铌尾矿经 20目和 80目方孔筛过筛后备用。
按基础玻璃的化学组成称量各种原料,混合均匀的玻璃配合料用坩埚盛装 ,在硅钼棒电炉中熔制, 熔制温度为 1400℃, 保温 2h。
将熔制好的玻璃液水淬成颗粒,然后烘干,并称量一定的量 ,再从炉中取出熔制好的玻璃液, 将称量好的水淬玻璃颗粒倒入玻璃液中并搅拌均匀,最后将玻璃液和水淬玻璃颗粒的混合物倒在铁板上压延成玻璃试样,其中水淬玻璃的用量为 9. 43%,玻璃熔体的用量为 90. 57%。
将采用碎粒压延法制备的玻璃试样在不同的热处理制度下进行核化和晶化 ,最后获得微晶玻璃试样。
实验结果与讨论
3. 1 差热分析
将制得的水淬玻璃试样用瓷研钵磨细, 过 200目筛 ,作 DTA 分析试验 ,以拟定核化
和晶化的热处理制度。
差热分析采用国产 LTC - 2 型差热分析仪, 参比物为经过 1400℃煅烧的 A l2 O3 粉, 升温速率为 10℃ / min。
差热分析曲线如图 1所示。
可以看出 ,在716℃有一强放热峰。
本次试验中 1、2、3号试样的核化温度均为 700℃,保温 2h;晶化
温度均为 900℃,保温时间分别为 45min、30min和 15min。
4、5、6、7号试样的核化温度均为 600℃,保温 2h;晶化温度均为 800℃, 保温时间分别为 60min 、45min、30min、
和 15min。
8、9号试样的核化温度均为 600℃,保温 2h;晶化温度均为 750℃,保温时间分别为 30min和 15min。
3. 2X -射线衍射分析
图2微晶玻璃试样的X -射线衍射谱
图2为 9个微晶玻璃试样的 X -射线衍射谱。
从谱线可以看出 , 9个试样的非晶体散射特征很弱 ,主要表现为晶体的衍射特征,说明在本试验采用的微晶化热处理条件下, 9个微晶玻璃试样的结晶程度都较高。
另外, 从衍射图中还可看出 ,随着核化和晶化温度升高以及晶化时间的延长, 微晶玻璃的结晶率是逐渐增加的。
3. 3微晶玻璃的显微结构
图 3为微晶玻璃试样的显微结构。
各试样的结晶都较充分, 这与 X -射线衍射分析结果是一致的。
各试样中的微晶体主要呈粒状集合体形貌, 整体结构均匀一致, 微晶体的尺寸基本上控制在 10μm 以下。
随着热处理温度的升高,晶粒大小无明显变化, 微观结构都比较致密, 微观结构中未见气孔出现。
根据断裂理论[ 8] ,晶粒的微细化和显微结构的致密化都为力学性能的提高创造了有利的基础条件。
故从理论上分析可知 ,采用碎粒压延法制备的微晶玻璃应该具有较好的力学性能,即具有较高的抗压和抗折强度。
结论
⑴以钽铌尾矿为主要原料,采用碎粒压延法工艺可直接成型为微晶玻璃板。
碎粒压延法与烧结法相比,气孔少、成品率高、成品质量好;与压延法、浇铸法相比,结晶过程容易控制,结晶率高,且晶化时间短,因此碎粒压延法具有很好的推广前景,且易在烧结法、压延法、浇铸法的基础上实现工业化改造。
⑵采用碎粒压延法制备钽铌尾矿微晶玻璃较理想的热处理制度是 :核化温度 600 ~700℃,保温时间 2h,晶化温度 750 ~ 900℃,保温时间 15 ~ 60m in。
⑶采用碎粒压延法制作钽铌尾矿微晶玻璃具有合理的显微结构,晶粒细小, 晶粒尺寸都控制在 10μm 以下 ,没有气孔 ,致密度高,致使碎粒压延法生产的微晶玻璃具有良好的力学性能。