中厚板在线控制冷却与淬火技术
中厚板控制冷却技术

中厚板控制冷却技术李嘉欣(辽宁科技大学材料成型及控制工程12级,学号1233010154)[摘要]控制轧制和控制冷却是现代化中厚板厂的主导生产工艺,用于生产优质的中厚钢板。
本文介绍了中厚板控制冷却技术的发展和现状,阐明了控冷对钢材组织性能的影响,对各种冷却方式进行了分析、比较,讨论了影响控制冷却效果的主要因素,并提出了应用控冷技术应该解决的几个问题,掌握这些情况对于中厚板厂选择合适的冷却方式和控冷系统的改造有一定参考作用。
[关键词]中厚板;控制冷却;冷却方式;发展Controlled Cooling Technology for Medium PlateAbstract: The control rolling and control cooling is a dominated process in a modern medium plate, which is used for producing quality medium steel plate. This paper reviews the development and current situation of the technology of controlled cooling for medium plate,and describes the effect of controlled cooling on the structure and properties of medium plate. The performances of all kinds of cooling methods are analyzed and compared. The main factors influencing the effect of controlled cooling are discussed. In addition,some key problems to be solved in the application are also given. It can be used for reference in choosing of suitable cooling methods and the controlled cooling systems.Keywords:medium plate;controlled cooling;cooling mode;development1前言传统的中厚板生产工艺,钢板轧后到精整之前,要经过长时间的自然空冷降温,这不但影响产量,而且还因冷床不足导致钢板在蓝脆温度下剪切,增加了钢板的废品率。
中厚板生产线冷却控制系统改造与实现
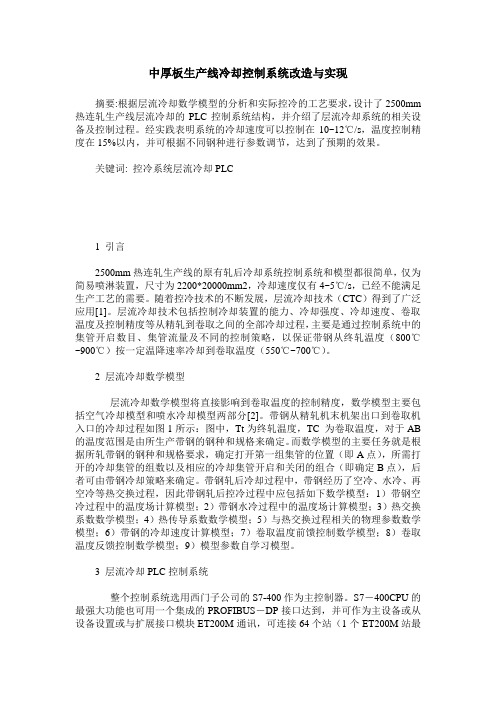
中厚板生产线冷却控制系统改造与实现摘要:根据层流冷却数学模型的分析和实际控冷的工艺要求,设计了2500mm 热连轧生产线层流冷却的PLC控制系统结构,并介绍了层流冷却系统的相关设备及控制过程。
经实践表明系统的冷却速度可以控制在10~12℃/s,温度控制精度在15%以内,并可根据不同钢种进行参数调节,达到了预期的效果。
关键词: 控冷系统层流冷却PLC1 引言2500mm热连轧生产线的原有轧后冷却系统控制系统和模型都很简单,仅为简易喷淋装置,尺寸为2200*20000mm2,冷却速度仅有4~5℃/s,已经不能满足生产工艺的需要。
随着控冷技术的不断发展,层流冷却技术(CTC)得到了广泛应用[1]。
层流冷却技术包括控制冷却装置的能力、冷却强度、冷却速度、卷取温度及控制精度等从精轧到卷取之间的全部冷却过程,主要是通过控制系统中的集管开启数目、集管流量及不同的控制策略,以保证带钢从终轧温度(800℃~900℃)按一定温降速率冷却到卷取温度(550℃~700℃)。
2 层流冷却数学模型层流冷却数学模型将直接影响到卷取温度的控制精度,数学模型主要包括空气冷却模型和喷水冷却模型两部分[2]。
带钢从精轧机末机架出口到卷取机入口的冷却过程如图1所示:图中,Tt为终轧温度,TC 为卷取温度,对于AB 的温度范围是由所生产带钢的钢种和规格来确定。
而数学模型的主要任务就是根据所轧带钢的钢种和规格要求,确定打开第一组集管的位置(即A点),所需打开的冷却集管的组数以及相应的冷却集管开启和关闭的组合(即确定B点),后者可由带钢冷却策略来确定。
带钢轧后冷却过程中,带钢经历了空冷、水冷、再空冷等热交换过程,因此带钢轧后控冷过程中应包括如下数学模型:1)带钢空冷过程中的温度场计算模型;2)带钢水冷过程中的温度场计算模型;3)热交换系数数学模型;4)热传导系数数学模型;5)与热交换过程相关的物理参数数学模型;6)带钢的冷却速度计算模型;7)卷取温度前馈控制数学模型;8)卷取温度反馈控制数学模型;9)模型参数自学习模型。
中厚板正火控制冷却系统的设计与应用

中厚板正火控制冷却系统的设计与应用摘要:中厚板正火控制冷却系统是钢板加热过程中至关重要的一个环节。
本文介绍了该系统的设计和应用,包括液压系统、传动系统、控制系统和冷却系统。
在操作过程中,通过控制液压系统调整钢板的进出速度,以及配置不同的传动系统和冷却系统,可以提高钢板的成品率和质量。
具体实验结果表明,采用中厚板正火控制冷却系统可以使钢板达到更加均匀的温度分布和良好的表面质量。
关键词:中厚板、正火、控制、冷却系统、成品率、质量正文:一、引言中厚板的加热处理中,正火是一个十分重要的工艺环节。
而中厚板正火控制冷却系统则是决定正火工艺质量的关键因素之一。
在钢板加热过程中,采用合理的控制冷却系统可以使钢板达到更加均匀的温度分布和良好的表面质量,从而提高钢板的成品率和质量。
二、设计和应用1.设计原理中厚板正火控制冷却系统是由液压系统、传动系统、控制系统和冷却系统组成的。
在操作过程中,通过控制液压系统的启停和调整,调整钢板的进出速度,以及配置不同的传动系统和冷却系统,使钢板可以达到最优的正火工艺质量。
2.液压系统液压系统是整个控制系统中最重要的部分之一,主要用于钢板的进出速度、合模压力和上下模板移动控制。
通过液压油泵的输出,产生高压油流,驱动静压缸和冷却卷筒,使中厚板在正火过程中保持平稳和平衡。
3.传动系统传动系统是决定中厚板正火控制冷却系统公差的重要因素,主要分为同步传动系统和不同步传动系统,通过不同的传动系统结构来解决钢板进出系统中的同步问题。
4.控制系统控制系统是中厚板正火控制冷却系统的核心部分,主要处理中厚板的各个加热环节,通过不同的控制方式,可以实现钢板的进出控制、温度控制、压力控制和冷却控制等。
5.冷却系统冷却系统是中厚板正火控制冷却系统中最后一步的控制环节,通过钢板温度传感器收集钢板的温度信息,然后通过冷却卷筒将钢板整体冷却到合理的温度范围内,从而达到最优的正火工艺质量。
三、实验结果通过对中厚板正火控制冷却系统的设计和应用分析,实验结果表明,采用中厚板正火控制冷却系统可以使钢板达到更加均匀的温度分布和良好的表面质量,并且可以提高钢板的成品率和质量。
中厚板表面热处理技术

中厚板表面热处理技术金属表面处理的方法1 前言中厚板的控轧控冷工艺发展很快,目前很大一部分通过控轧控冷工艺生产的钢板可以取代热处理钢板,即可节省能源,降低生产成本,而且从质量和性能上说也不次于热处理钢板。
然而,从当今的中厚板控轧控冷技术水平来说,中厚板的表面热处理工艺仍然还不能取消。
这是因为:1)从工艺上说,退火、回火、调质、缓冷等表面处理用控轧控冷工艺还实现不了;2)从钢种上说,耐压、耐候、抗压板、海上平台板、模具工具板、高中压锅炉容器板、合金结结板、桥梁板、不锈钢板及高牌号管线与船用板等,目前采用控轧控冷工艺尚有困难;3)从板厚上说,控轧控冷工艺多用于板厚在30mm以下。
而且线外热处理钢板的性能比较均匀稳定,偏差也小。
特别是热轧钢板性能不合要求时,通过线外热处理尚有补救的可能,一些控轧后钢板还可作为热处理的基板,使热处理钢板性能达到更高更完美。
当前,宽厚板性能的重要性越来越被人们所共识,一个现代化宽厚板厂的热处理工序,应该说是确保生产出高性能钢板所不可缺少的。
2 中厚板热处理的特点2.1 处理种类齐全随着用户对中厚板品种和质量的要求越来越严格,与其他钢材相比,中厚板热处理种类要求更加齐全,有正火(常化)、调质(淬火+回火、正火+回火)、高温回火、退火、淬火(水淬、油淬)及缓冷等方法,通常以正火处理最为普遍。
2.2 热处理量大在热轧钢材中以中厚板热处理量较大,一个现代化中厚板厂热处理量约占总产量的20%以上。
2.3 处理钢板尺寸与面积大热处理中厚板最宽可达5400mm,最长达到27m,一般要求长达18m,因此,炉子尺寸很大,有的热处理炉内宽达5800mm,长达102m。
2.4 钢板单重大一块钢板通常重达20t~30t,最重可达到1250t,因此,需要为之配套装出炉机械与吊车安置大吨位的设备。
2.5 淬火和快冷用水量大由于钢板单重大,淬火与快冷瞬间用水量高达10000m3~14000m3,供水系统很庞大,多数都需设有储水池或水塔来满足。
北京科技大学科技成果——常压多功能无约束中厚板淬火控冷系统

北京科技大学科技成果——常压多功能无约束中厚板淬火控冷系统成果简介由北京科技大学机械和信息两学院与太原钢铁公司联合开发的常压多功能无约束中厚板淬火控冷系统,已在太钢不锈热轧厂一次投产成功,使原热处理淬火线月产量增加一倍,生产稳定。
据近8个月统计,已完成4万吨的不锈钢固溶处理,1Cr18Ni9Ti 一次性合格率提高13.34%,0Cr18Ni9一次性合格率提高2.5%,16MnR 一次性合格率提高29%,不锈钢一次性合格率稳定在98%以上。
由于具备淬火和控冷两种功能,扩大了热轧厂的品种,填补了热轧厂调质钢生产的空白。
技术特点(1)采用流射沸腾强化机理,冷却速率高。
目前使用的冷却速率,对板厚20mm不锈钢可达45℃/s以上,对板厚40mm不锈钢可达22℃/s以上。
,(2)与目前我国进口的压力淬火机和辊式淬火机不同,该系统利用“流场、温度场、应力场和组织场的耦合和解耦”、“计算机仿真”和“物理模拟”技术,实现无约束连续淬火板形平直度控制。
淬火后板形平直度符合或高于工艺要求,能顺利通过后面的矫直机和抛丸机。
(3)采用“强适应钢板横向冷却曲线”,保证横向板形平直。
采用“一对一模拟控制技术”,保证良好上下水比。
采用“阻尼反抑制”和“多级均匀阻尼技术”,保证每个喷嘴的下水均匀。
采用“多集管水源稳定技术”,保证每一时刻水流的稳定。
采用“全场变形控制技术”,保证钢板纵向平直。
(4)用高低位水箱储能、计算机在线跟踪控制、干净水直接溢流回收无泄漏和大型复杂系统水流动态控制集成技术,使瞬间供水量达到900m3/h水系统的5-6倍,满足淬火控冷要求,大大节省投资。
(5)采用人工智能控制目标温度预报和控冷模型优化技术。
建成了用于工业生产兼具强、弱冷系统和淬火控冷两种功能的常化线炉后常压(0.1MPa)热处理系统。
技术水平2001年12月17日经山西省科委组织鉴定,本系统为国内外首创,处国际领先水平。
应用范围可用于中厚钢板常化线炉后淬火控冷,也可用于轧后加速冷却和直接淬火上(即ACC+DQ)。
铝合金中厚板在线淬火工艺探讨

铝合金中厚板在线淬火工艺探讨潘 亮(中冶东方工程技术有限公司,山东 青岛 266555)摘 要:本文论述了铝合金中厚板在线淬火工艺,重点介绍了现有离线淬火工艺的劣势、在线淬火工艺的优势、在线淬火工艺的实施方法。
关键词:铝合金中厚板;热处理;离线淬火;在线淬火中图分类号:TG156.3 文献标识码:A 文章编号:1002-5065(2019)10-0019-2On-line Quenching Technology for Medium and Heavy Aluminum Alloy PlatesPAN Liang(Zhongye Oriental Engineering Technology Co., Ltd. Qingdao 266555, China)Abstract: This paper describes the on-line quenching process for medium and heavy aluminium alloy plates, focusing on the disadvantages of the existing off-line quenching process, the advantages of the on-line quenching process and the implementation method of the on-line quenching process.Keywords: aluminium alloy plate; heat treatment; off-line quenching; on-line quenching对铝板带材加工企业来说,加工工艺正追求高效率、高品质、节能、降耗、环保的目标。
对于以2XXX、6XXX、7XXX系等可热处理强化合金为主的铝合金中厚板产品,淬火及时效是一种有效提高铝合金强度性能的工艺。
日本JFE公司开发和应用的中厚板制造技术介绍

日本JFE钢铁公司开始开发采用水淬火的热机械控制工艺(TMCP),作为高强度、高韧性,具有优良焊接性能钢板生产技术的核心技术。
下面简单介绍由JFE钢铁公司开发和应用的中厚板制造技术,包括超级-OLAC技术,一种新的中厚板加速冷却技术以及HOP技术(热处理在线工艺),一种加速冷却后的在线热处理工艺。
同时,下面还介绍Easyfab钢板制造技术,即通过应用具有新功能的冷矫直机将中厚板中残余应力降至零。
一、新加速冷却技术——“超级-OLAC”技术的开发与控制轧制技术一起,加速冷却技术是TMCP工艺的核心技术。
JFE钢铁公司是世界上首家开发并成功在中厚板生产中应用在线加速冷却技术的钢铁企业。
在上世纪90年代初,采用加速冷却技术制造的TMCP钢实现了提高钢板强度、改进焊接性能的目的,从而有助于焊接结构建筑用钢使用的合理化和提高建筑的安全性,并开始用于造船业。
然而,最近几年对钢板质量的要求日趋严格,如减少强度下降等。
为了满足新的要求,基于一个全新的概念,JFE钢铁公司进行了大量研究以获得解决与传统冷却技术问题相关的方案,并开发出新一代加速冷却工艺,称之为超级-OLAC工艺,并应用于JFE钢铁公司西日本钢厂。
当中厚板进行水淬火时出现的热传递和沸腾现象可以大致分为两种方式,即核胞沸腾和薄膜沸腾。
在前一种沸腾中,冷却水直接与钢接触,热量通过产生的泡传递。
相比之下,后一种沸腾中在钢与冷却水间形成一个蒸汽薄膜,热量是通过蒸汽薄膜传递。
核胞沸腾的冷却能力比薄膜沸腾更高。
在中厚板冷却开始时,中厚板表面温度较高,薄膜沸腾起主导作用。
然而,随着中厚板表面温度的下降,蒸汽薄膜变得不稳定,冷却水开始局部上直接与中厚板接触,沸腾逐渐转向核胞沸腾。
此外,在瞬时沸腾状态下,当薄膜沸腾和核胞沸腾共存时,随着冷却的继续,冷却能力提高。
采用传统冷却方法,如喷淋冷却和层流冷却时,如果冷却水流量提高以强化冷却,冷却迅速地转换成瞬时沸腾,是核胞沸腾和薄膜沸腾的混合。
9 中厚板的控制轧制与控制冷却

9中厚板的控制轧制与控制冷却9.1中厚板的主要性能指标中厚板轧制过程是钢坯在承受巨大外力作用下产生塑性变形的过程,在整个变形过程中不仅可使钢板获得所必须的尺寸和形状,而且也使之获得所必须的组织和性能。
借助装备水平和自动化程度的提高保证中厚板形状和尺寸精度的相关内容在本书的以上各章已有详细论述,本章将着重介绍在特定的设备条件下,如何通过钢板生产工艺参数的合理控制来获得理想的组织和性能。
中厚板的主要性能指标包括力学性能(屈服强度、抗拉强度、伸长率、冲击功等)、工艺性能(冷弯、冲压、焊接性能等)和理化性能(如耐蚀、耐火性能)等。
根据钢板用途的不同在相关标准中对所要求的各种性能指标都有明确的规定。
如GB/T 1591—94标准对Q345中厚板拉伸、冲击和冷弯性能的规定如表9-1所示。
本节仅就结构钢中厚板中常接触到的几种性能指标介绍如下。
9.1.1强度指标对于结构钢中厚板,在工程中常用的强度指标有:(1)比例极限ζP。
拉伸试样中的弹性变形阶段,应力和应变的关系符合虎克定律,当试样被拉至具有一定的应力时,应力.应变曲线偏离了直线关系。
当该曲线与应力轴夹角的正切值已较直线部分增加50%时,此应力即为该材料的比例极限。
(2)弹性极限ζe。
弹性极限是指完全卸载后不出现任何明显残余应变的最大应力。
弹性极限的高低除受材料本身性质、材料的加工条件和试验条件等各种因素的影响外,还取决于测量应变时所用仪器的灵敏度。
仪器越灵敏,越能在早期检测出塑性变形的出现,则弹性极限的数值就越低。
为了便于比较,技术上规定一个基准的应变量,弹性极限就是产生该基准永久应变量的应力值。
基准量的大小通常确定为10-2%。
为了更早期发现材料的弹性一塑性过渡,就要用更灵敏的测量仪器。
产生2×10-4%残余应变量的应力值称为“真弹性极限”。
这个应力值相当于驱使几百个位错运动的应力,很接近于“临界”的形变应力。
(3)屈服强度ζs。
有屈服效应的材料,在拉伸过程中负荷不增加或有所降低而试样能继续变形的最小负荷所对应的应力称为屈服应力。
- 1、下载文档前请自行甄别文档内容的完整性,平台不提供额外的编辑、内容补充、找答案等附加服务。
- 2、"仅部分预览"的文档,不可在线预览部分如存在完整性等问题,可反馈申请退款(可完整预览的文档不适用该条件!)。
- 3、如文档侵犯您的权益,请联系客服反馈,我们会尽快为您处理(人工客服工作时间:9:00-18:30)。
图 1 冷却模型
11 控制冷 却技 术要点 .
( 钢板上 、下表面及内部冷却均匀的控制技 1 )
术。由于上 、下表面采用的喷嘴形式不同,以及受 中心部位的冷却能力,通过控制钢板的移动速度来 钢板上表面滞 留水 的存在等因素影 响 ,使钢板在 满 足不 同材质 、不 同规格板 材 的 目标强度 。 上 、下表面冷却能力相 同时 ,所需 的冷却水量不 与常规淬火相比,直接淬火的优点在于对同一 同。因此上 、下表 面的冷却水量要选择适当的比 例; 合金成分的钢板具有更高的淬透性 ,并且对 N 和 b T 等合金元素 的使用要求更加灵活。利用这些合 i 金 元素 可以在钢 中形成 稳定 的氮化 物和碳化 物 ,在 板坯高温加热时,它们在奥氏体相中产生固溶 , 从 而 提高淬 透性和充 分发 挥析 出硬化 功能 。
强度 (lm) 。 Nm 2;后 一晶粒尺寸系数 ,为曲线
斜率 ; 一 △ 固溶强化作用的增长量 (m 2; N m) l △ _ 淀 强 化 作 用 的 增 长 量 ( /m); 广 沉 Nr 2 a
△ 『 位 错 强化 的 增 长 量 ( lm2; 体 晶粒尺寸的影响
素体晶粒直径 (m 。 ) 韧 性断裂 强度 为 :
: ~ … … … … … … … … … … … …
嚆 舛
曼
() 2
K D
式 中 ,G —材 料 的 剪 切 模 量 ( a P );
表 面 能
冷 却速 度 ( , :) 8
△ — .2% Nb一 0 % v ; 0 - 0.4 Nb一 .9 V; 0 0.3 - 0% 00 %
火 也 是 一样 ,必 须 避 免 轧制 终 了时 温 度 过 高 或过
时 闻
模型 1 控冷 ;模型 2 一 一淬火 。
低 ,否则 ,如果轧制后钢板温度过高会使奥氏体的 晶粒粗大化 ,而温度过低则会导致奥 氏体向铁素体 相变。因此 ,作为直接淬火前道工序 的轧制必须严 格控制终轧温度 ,并且为了保证奥氏体能够全部转
();K J 一常 数 ;
素 体 晶 粒 直 径
(m) 一韧性 断裂强度 (/m2。 ; Nr ) a
O、△一 1 0 再加热 ;●、▲一110o再加热。 0C 2 0 C
钢材的屈服强度 ,断裂强度与铁素体晶粒尺寸 的 成正比,即晶粒尺寸越细小 ,屈服强度和
殊钢 ,所生产的钢板均已获得满意的结果 2。 )
强度 ,必须有不同的冷却速度。冷却速度由冷却水 量和钢板 的移动速度决定 ,冷却速度一般控制在
5 6℃/ : ~1 s
2 在线控制冷却和直接淬火机理
21 在 线控制 冷却机 理 .
f)始冷 温度 和终 冷温 度 对钢 板 的显微 组 织状 4
、 D /
…… … … ( i )
晶时 的屈服
冷却 速度( ℃
△ —_.2 N 一 . % v ; O - 0o % N - . % V; o0 % b 00 3 - .4 b 0 9 0
式中,
堀 服强 度 (l 2;o Nmm) r
O、△ 1 0 ℃再加热 ;●、▲一 1 0 再加热 。 一 0 2 0o 1 C
直接 淬火后 的钢板 必须进 行 回火 处理 ,目前在
f 2 )保证钢板沿宽度、长度方向都能均匀冷却
的控制技术。钢板上表面的滞 留水向边部流出,以 及冷却水 向边部喷溅等都会影响到沿钢板宽度方向 冷却的均匀性。因此 ,必须加大中心部位的冷却能 力。一般采用控制冷却水的办法解决 。沿长度方向
CF H!
轧制工艺来获得晶粒细化 的铁素体和珠光体组织 , 使钢板达到工艺所要求的强韧性并改善加工性能及 焊接性能 。细化铁素体 晶粒不仅能提高钢的强度 ,
而且 改善 钢 的韧性 ,如霍 尔一 奇公 式 给 出如 下 相 佩
应关系:
=
言
扣
瑶
基
嫡 嚣
【0A' a qZ '] O+ O + o+ O -, m  ̄w
也存 在类 似情况 ; ()不 同材 质 和规格 的钢板 所要 达 到 的 目标 强 3 度是 不 同的 ,为 了满足不 同材质 和规格 钢板 的 目标
国外的同类生产线上已设有在线回火炉等设备,实 现了钢板淬火回火处理连续化作业。 直接 淬 火 不 但适 用 于调 质 60M a 0 a 0 P 、80MP 级 的钢 种 ,而且适 用于全 部要进行 淬火 和 回火 的特
( 见图 1 。 )
温度
态时,经过急冷处理 ( 快速冷却)使钢板产生马氏 体相变 ,即奥氏体全部转变为马氏体的工艺过程。
对 同样 厚度 、材质 的钢板 ,直接 淬火 的冷却速度 比 控制冷 却 的冷却速度 还要 大 。
在进行常规热处理时 ,为了得到适当晶粒度的
奥 氏体组织 ,要考虑 A3 r相变点和使奥氏体晶粒粗 大化温度 ,必须实施正确的淬火加热控制。直接淬
一
目技雍
很大 的,若冷却不均匀 ,就会造成钢板性能不均
匀 ,而且 不能得 到 良好 的板形 。因此 ,在控 制冷却
12 直接 淬火技 术要 点 . 直 接 淬火 是 一种 代 替 二 次 加 热 淬 火 的 工艺 技 术 。它是 在热轧 终 了 ,钢材组 织处 于完全 奥氏体状
和淬火过程中, 实现温度的高精度控制,保证钢板 冷却均匀 ,是实现控制冷却和淬火技术的关键所在
态, 钢板的性能都有重要影响,因此要精确控制始
冷温度 ( 在A3 一般 r )和终 冷温度 (0 ~0 30 60℃) 。
在线控制轧制和控制冷却是通过采用最优化的
表 2 直接淬火钢板的化学成分和机械性能
…
…
2 1年 期 13 一 - 筻 09 璺 3 鞠L
y . @ CLo zs c c m j h