中厚板的控制轧制与控制冷却工艺
钢材控制轧制和控制冷却
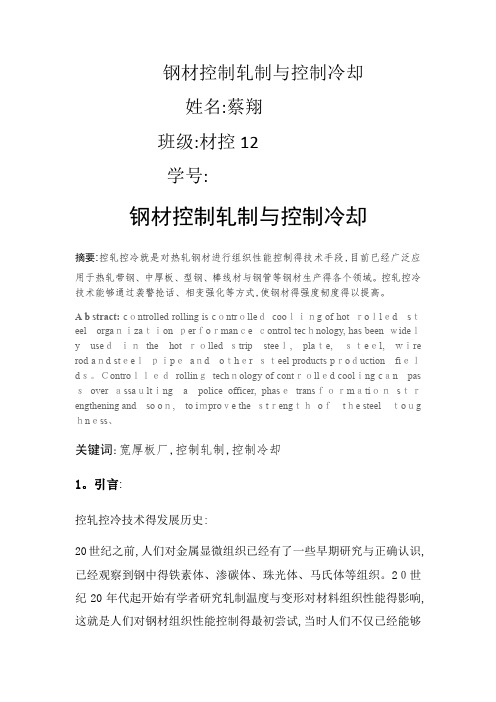
钢材控制轧制与控制冷却姓名:蔡翔班级:材控12学号:钢材控制轧制与控制冷却摘要:控轧控冷就是对热轧钢材进行组织性能控制得技术手段,目前已经广泛应用于热轧带钢、中厚板、型钢、棒线材与钢管等钢材生产得各个领域。
控轧控冷技术能够通过袭警抢话、相变强化等方式,使钢材得强度韧度得以提高。
Abstract: controlled rolling is controlledcooling of hot rolled steel organization performance control technology, has been widely usedinthe hot rolled strip steel,plate,steel,wire rod and steelpipeand other steel products production fields。
Controlledrollingtechnology of controlled cooling can pas sover assaulting a police officer, phasetransformationstrengthening and so on,to improve the strengthofthe steeltoug hness、关键词:宽厚板厂,控制轧制,控制冷却1。
引言:控轧控冷技术得发展历史:20世纪之前,人们对金属显微组织已经有了一些早期研究与正确认识,已经观察到钢中得铁素体、渗碳体、珠光体、马氏体等组织。
20世纪20年代起开始有学者研究轧制温度与变形对材料组织性能得影响,这就是人们对钢材组织性能控制得最初尝试,当时人们不仅已经能够使用金相显微镜来观察钢得组织形貌,而且还通过X射线衍射技术得使用加深了对金属微观组织结构得认识、1980年OLAC层流层装置投产,控轧控冷在板带、棒线材等大面积应用,技术已成熟,理论进展发展迅速、2 控轧控冷技术得冶金学原理2。
钢材控制轧制和控制冷却技术

§2控轧控冷理论
(2)控轧时微量元素碳氮化物的析出
①、各阶段Nb(C,N)析出状态
1)出炉前Nb(C,N)质点状态。
2)出炉后冷却到轧制前Nb(C,N)析出状态,未变形A 体中Nb(C,N)析出很慢。
3)变形 A体中Nb(C,N)析出状态,变形使Nb的析出 加快(形变诱导析出),Nb(C,N)在900℃析出最快,孕 育期最短,低温轧制(未再结晶区)加速C和Nb扩散速度。Nb (C,N)析出在晶界处以及晶内和亚晶界上,颗粒细小,控 轧就是利用细小质点固定亚晶界而阻止A体晶粒再结晶达到细 化目的。
② 、 Nb、Ti 含 量 < 0 . 1 % , 提 高 钢 粗 化 温 度 到 1 0 5 0 ~ 1100℃。
V<0.1%时,A体在950℃开始粗化。 ③、钢中含Al,使A体粗化温度在900~950℃
§2控轧控冷理论
(2)抑制A体再结晶 ①、对动态再结晶临界变形量的 影响,显著阻滞形变A体动态 再结晶。 ②、对再结晶数量的影响 ③、对再结晶速度影响。 1)含Nb钢再结晶开始和完 成时间都比不含Nb钢推迟。 2)当Nb达到0.06%时,阻止 再结晶作用达到饱和。
变形条件对ar3的影响1加热温度原始a体晶粒度2轧制温度t2控轧控冷理论3变形量4冷却速度3ar3的变化对组织的影响单纯从相变后f体晶粒长大观点ar3低对获得细晶f体有利变形引起相变温度的变化较复杂1在再结晶区变形2在未再结晶区变形型控轧2控轧控冷理论3变形条件对ap转变的影响1变形使p体转变加速从而使钢的淬透性变坏
§2控轧控冷理论
③、第三阶段,在两相区内轧制(A r3—A r1间) 1)该区对未再结晶A体加工,还对F体加工。 2)产生织构 3)形变诱导析出物可使脆性转变温度降低 4)工艺对性能影响大
中厚板控制冷却技术研究

中厚板控制冷却技术研究作者:刘辉来源:《商品与质量·学术观察》2014年第01期摘要:控制冷却是提高中厚板产品性能和附加值的重要手段。
它能简化生产工艺并提高生产效率,节约能源及昂贵合金元素,并有很大的经济效益。
本文就控制冷却技术的现状、控制冷却的作用、影响冷却质量的主要因素以及控制冷却技术在应用中需解决的几个问题四方面进行阐述。
关键词:中厚板控制冷却因素1、控制冷却技术的现状中厚钢板大约有 200 年的生产历史,它是国家工业化进程和发展中不可缺少的钢铁品种,被广泛用于大直径输送管、压力容器、锅炉、桥梁、海洋平台、各类舰艇、坦克装甲、车辆、建筑构件、机器结构等领域。
世界钢铁工业的发展历程表明,中厚板的生产水平及材料所具有的水平也是国家钢铁工业及钢铁材料水平的一个重要标志。
随着我国经济的快速增长,中厚板的市场需求将越来越大,同时市场竞争也将越来越激烈。
各中厚板厂家为了提高产品竞争力,纷纷采用新的设备或者新的控轧控冷工艺来提高中厚板的综合性能。
控制轧制和控制冷却工艺(CRC)是现代钢铁工业最大的技术成就之一。
对于一些钢材,控轧控冷后不必实施常规轧制的轧后热处理工艺,从而简化了生产工艺,提高了生产效率,并且可以节约能源,省去昂贵的合金元素,具有很大的社会效益和经济效益。
随着用户对中厚板质量和性能的要求越来越高,控制轧制和控制冷却新工艺逐渐应用于中厚板生产领域。
控制冷却是中厚板生产中提高产品质量、开发高附加值产品的最重要的手段。
但是我国有些钢厂的控制冷却装置使用效果并不理想,有的甚至基本不用,成为一种摆设。
不少厂家采用的是简易喷淋冷却装置及用控温轧制来替代控制轧制。
而控轧控冷技术在日本应用率达 70%以上。
国内许多中厚板厂只是引进国外的控轧控冷设备,对国外工艺技术消化不彻底,没有充分发挥出控轧控冷技术的潜力。
近几年,各中厚板厂在残酷的市场竞争中充分认识到控制冷却的优越性,相继安装了控制冷却设备,同时积极开发冷却控制系统。
控制轧制及控制冷却技术在型钢生产中的应用

控制轧制及控制冷却技术在型钢生产中的应用一、引言型钢是一种重要的金属材料,在建筑、汽车制造、机械制造等领域具有广泛的应用。
为了提高型钢的质量和性能,控制轧制及控制冷却技术被广泛应用于型钢生产中。
这些技术通过精确控制轧制工艺参数和冷却过程,可以有效提高型钢的强度、塑性和表面质量,满足不同领域对型钢材料性能的需求。
二、控制轧制技术的应用1. 调整轧制温度和速度在型钢轧制中,通过调整轧制温度和轧制速度,可以控制晶粒的细化和晶格的取向,从而提高型钢的强度和塑性。
尤其是在热轧过程中,通过精确控制轧制温度和速度,可以有效控制晶粒生长,减少析出相的尺寸,使得型钢的晶粒细化,提高强度和硬度。
2. 控制轧制力和变形量通过精确控制轧制力和变形量,可以有效调整型钢的组织结构和力学性能。
在轧制过程中,通过监测轧辊力和变形量,可以实现对型钢的细微调整,达到提高型钢性能的目的。
在轧制高强度型钢时,通过增加轧制力和变形量,可以有效提高型钢的强度和硬度。
3. 控制轧制辊形状通过选择合适的轧辊形状,可以实现更加精确的型钢轧制。
不同形状的轧辊对型钢的变形和组织结构有着不同的影响,因此通过调整轧辊的形状,可以实现对型钢结构和性能的精细控制。
三、控制冷却技术的应用1. 控制冷却速度在型钢生产中,通过控制冷却速度,可以实现对型钢组织和性能的调整。
在快速冷却条件下,型钢的组织结构更加均匀,晶粒更加细小,从而提高了型钢的强度和韧性。
在慢速冷却条件下,型钢的组织结构更加致密,表面质量更好,适用于高表面质量要求的场合。
2. 控制冷却介质不同的冷却介质对型钢的冷却效果和组织结构有着不同的影响。
通过选择合适的冷却介质,可以实现对型钢组织和性能的精细调控。
对于高强度型钢,可以采用高效的水冷或气体冷却,快速降温,实现对型钢强度和硬度的提高。
3. 控制冷却方式在型钢生产中,采用不同的冷却方式,可以实现对型钢的细微调整。
采用直接水冷或间接水冷,可以分别实现快速和慢速的冷却效果,从而满足不同型钢的冷却需求。
控制轧制和控制冷却工艺讲义

控制轧制和控制冷却工艺讲义控制轧制和冷却工艺讲义一、轧制工艺控制1. 轧制温度控制a. 在热轧过程中,轧机和钢坯之间的接触摩擦会产生高温,因此需要控制轧机温度,避免过热。
b. 实时监测轧机温度,根据温度变化调整轧制速度和冷却水量,确保温度适中。
c. 使用专用液体和冷却器进行在线冷却,防止轧机过热引起事故。
2. 轧制力控制a. 测量轧机产生的轧制力,确保轧机施加的压力适中。
b. 监控轧制力的变化,根据钢坯的变形情况调整轧制力,使钢坯的形状和尺寸满足要求。
c. 根据轧制力的大小调整轧制速度,保持稳定的轧制负荷。
3. 轧制速度控制a. 根据不同钢材的特性和规格,调整轧制速度,确保成品钢材的质量和尺寸满足要求。
b. 控制轧制速度的稳定性,避免过快或过慢的轧制速度导致钢材质量不达标。
4. 轧辊调整控制a. 定期检查和调整轧辊的位置和间距,确保钢坯能够顺利通过轧机,避免产生不均匀的轧制力和过度变形。
b. 根据车间实际情况和轧制工艺要求,调整轧辊的工作方式和参数,使轧制过程更加稳定和高效。
二、冷却工艺控制1. 冷却水量控制a. 根据钢材的材质和规格,调整冷却水的流量和压力,确保钢材迅速冷却到所需温度。
b. 监测冷却水流量和温度,根据实时数据调整冷却水量,确保冷却效果和成品钢材的质量。
2. 冷却速度控制a. 根据不同的冷却工艺要求,调整冷却速度,使钢材的组织和性能满足要求。
b. 监控冷却速度的变化,根据实时数据调整冷却速度,确保成品钢材的质量和性能稳定。
3. 冷却方法控制a. 根据钢材的特性和要求,选择合适的冷却方法,如水冷、风冷等。
b. 根据不同冷却方法的特点和效果,调整冷却工艺参数,使冷却效果和成品钢材的质量最优化。
4. 冷却设备维护a. 定期检查和维护冷却设备,确保设备的正常运行和效果良好。
b. 清洗和更换冷却设备中的阻塞、损坏部件,保证冷却水的流量和质量。
以上是对控制轧制和控制冷却工艺的讲义,通过合理的工艺控制和设备维护,能够提高轧制和冷却过程的效率和质量,满足钢材的要求。
中厚钢板的生产中控轧控冷工艺

目前在中厚钢板的生产中控轧控冷(TMCP)工艺已普遍应用,并在管线钢、高强度结构钢、海洋平台用钢、造船板等的生产中发挥了积极作用,大大提高了钢板的综合性能,节约了名贵的合金元素。
但是,TMCP处置惩罚的钢板性能离散度较大,并且一些钢种要求很苛刻的临界轧制。
因此,对付生产厚规格、高性能钢板,尤其是要求性能均匀性比力高的锅炉压力容器钢板、桥梁钢板、高层修建钢板、Z向钢板等,传统的离线热处置惩罚方法仍然是难以替代的。
因此一个定位于生产高性能品种钢为主的中厚板厂,建立一条现代化的中厚板热处置惩罚生产线,是在设计之初就必须考虑的问题。
建立热处置惩罚工序应统筹考虑的问题1 对炼钢、轧钢工序设备的要求中厚板轧后热处置惩罚炉是生产高技能含量、高附加值产物不可缺少的主要设备,因此应定位在生产“双高”产物,要求钢质纯净、有害元素和混合物含量低,板坯厚度要满足一定的压缩比,配备有控轧控冷设施等。
这就要求前面的炼钢和轧钢工序具备生产“双高”产物的条件,如炼钢工序要配备有铁水预处置惩罚设施、大吨位的顶底复吹转炉或高功率电炉、LF/VD/RH等炉外精炼设施、直弧形大板坯连铸机等,轧钢工序要配备有高刚度强力轧机、ACC(DQ)、强力矫直机等。
2 对轧钢厂的园地要求在建立中厚板厂时,要考虑精整的能力足够大,也就是背面剪切、冷床等的能力要大于前面轧钢能力,以便于充实发挥轧机的潜能。
同样如果一其中厚板厂定位于生产高技能含量、高附加值产物时,就要考虑厂房后部工序要留有充实的火焰切割、探伤、热处置惩罚生产线的园地。
因为对付需要热处置惩罚的钢板来说,一般40mm以上的厚规格钢板受剪切能力限制,需要火焰切割,并且热处置惩罚的钢种许多要求逐张探伤。
因此,在厂房设计时要留有足够的园地,不然将严重制约生产能力的发挥。
置惩罚用度,但正火通过再结晶细化均匀组织,对付某些微小的探伤缺陷有改进作用,尤其是合金含量较高的钢种。
因此,有些品种可摆设在热处置惩罚之后探伤。
轧钢论文
2008级轧钢(1)班毕业论文论文题目:中厚板的控制轧制和控制冷却学校名称:河北理工大学继续教育学院专业名称:轧钢学号:20080710215姓名:仇占明指导教师:汪青山2010.11.21目录一、引言 (1)二、TMCP的概念和特征 (2)三、中厚板的控制轧制基础 (3)四、中厚板控轧工艺过程的新方法 (7)五、低碳贝氏体钢的发展 (7)六.TMCP钢在不同领域应用的状况 (10)七.中厚板的控制冷却设计 (13)八.加速冷却设备 (15)九.今后的展望 (18)十.结论 (15)参考文献 (17)中厚板的控制轧制和控制冷却摘要60年代以后,对中厚板热变形过程中钢的组织变化进行了多方面的深入系统的研究工作。
进一步证实了坯料加热.热轧和轧后的冷却条件对钢板的组织和性能有极大的影响,引起冶金工作者的重视,为形成中厚板的控制轧制和控制冷却工艺及其机理创造了有利条件,打下了基础。
目前,这相研究已经日趋完善,形成了新的中厚板工艺——控制轧制和控制冷却,即TMCP技术。
关键词:中厚板控制轧制控制冷却组织性能。
一、引言TMCP (Thermo Mechanical Control Process:热机械控制工艺)作为提高钢材的强度、韧性和焊接性的材质控制工艺技术,它是以厚板为中心进行开发的。
所谓TMCP就是在热轧过程中,在控制加热温度、轧制温度和压下量的控制轧制(CR Control Rolling)的基础上,再实施空冷或控制冷却(加速冷却/ACC:Accelerated Cooling)的技术总称,本文从狭义上是指控制轧制后的加速冷却技术,简称为TMCP。
虽然在20世纪50年代已采用了轧制后直接淬火工艺,但尚未达到批量化生产。
其原因是轧制长度受到限制、冷却均匀性(材质和形状)等课题尚未解决等。
其后,经过冶金学和冷却控制设备的研究,到了20世纪80年代开发出了TMCP技术。
自TMCP开发以来已经历了20多年的时间,在这期间TMCP的应用范围不断扩大,目前已成为生产厚板不可或缺的技术。
中厚板轧后控制冷却系统
茹主 工 艺 圣 }
中厚 板 轧 后控 制 冷 却 系统
Ac ee ae n r l d Co l g S se i c lr td Co to l o i y tm e n n
M i d ea d He v lt d l n a y P a e
LUTo UWe, i 技术 和手段来 研究高 精度 的AGC 刘涛 ,余伟 ,张立杰 ,何春 雨,李彦彬 ,徐 言 东/ I a , Y Z A G L-e H h ny , L Y nbn H N ii, EC u —u I a—i,X a—0 j UY ndI 系统也还有许多工作要做 。
作者简介 张 飞 f9 9 ) 男 ,湖 南 宁 乡 17一 , 人 ,机械工程博 士后 ,研 究方向为轧
制 过程 的智 能化 控 制 。
别而 规格更 厚 的产 品 ;轧后 控冷 术 、板速控 制技术 等 配套技术 解
系统可代 替正火工艺 、离线淬火一 决 控 冷 中 的 相 关 问题 。代 表 性 回火热 处理 工序 。 目前AC 技术 的控 冷技术 包括 :新 日铁C C C L 技
了企业 的品种 结构 ,为企 业带 来 技 术 ,曼 海 姆 一 MAC 技 术 , OS
效益 。
蒂 森 I C 冷却 技 术 ,克 莱 西姆 S强
A O DC 技术 。表 1 为国外控冷技术 特点及应 用情况 。
轧 后 控 冷 技 术 发 展
国外控 制冷却技术的发展 2 世 纪 6 年 代 第 一 套 层 流 0 0
版社.04 20
生产 的重 要工 艺技术 ,通 过应 用 中 问题 的不 断 出现 ,如 冷却能 力
改善 钢板 的力 学性 能 ,在不 降低 尾 温度 控制效 果差 及冷却 速度 控
精选控制轧制和控制冷却工艺讲义
5.2.2现代化宽厚板厂控制轧制和控制冷却技术
近三十年以来 ,控制轧制和控制冷却技术在国外得到了迅速的发展 ,国外大多数宽厚板厂均采用控制轧制和控制冷却工艺 ,生产具有高强度、高韧性、良好焊接性的优质钢板。
获得细小铁素体晶粒的途径——三阶段控制轧制原理
奥氏体再结晶区域轧制 (≥ 950℃ )在奥氏体再结晶区域轧制时 ,轧件在轧机变形区内发生动态回复和不完全再结晶。在两道次之间的间隙时间内 ,完成静态回复和静态再结晶。加热后获得的奥氏体晶粒随着反复轧制——再结晶而逐渐变细。
图中第Ⅰ 阶段 ,由于轧件温度较高 ,奥氏体再结晶在短时间内完成且迅速长大 ,未见明显的晶粒细小。
不然,出于平整道次压下率确定不合适,引起晶粒严重不均,产生个别特大晶粒,造成混晶,导致性能下降。
道次变形分配
满足奥氏体再结晶区和未再结晶区临界变形量的要求,要考虑轧机设备能力及生产率的要求。压下量的分配一殷在奥氏体区采用大的道次变形量 ,以增加奥氏体的再结晶数量,细化晶粒。在未再结晶区在不发生部分再结晶的前提下,尽可能采用大的道次变形量,以增加形变带,为铁素体相变形核创造有利条件。在轧机能力比较小的条件下,采用在未再结晶区多道次、每道次小变形量并缩短中间停留时间的快轧控制方案,也取得较好的效果,而且不降低轧机产量。经验结论 在未再结晶区大于45—50%的总变形率有利于铁素休晶粒细化。
5.2板带钢控轧与控冷应用实例
5.2.1北极管线用针状铁素体钢
管线钢的发展历史
60年代末70年代初,美国石油组织在API 5LX和API 5LS标准中提出了微合金控轧钢X56、X60、X65三种钢 .这种钢突破了传统钢的观念,碳含量为0.1-0.14%,在钢中加入≤0.2%的Nb、V、Ti等合金元素,并通过控轧工艺使钢的力学性能得到显著改善。到1973年和1985年,API标准又相继增加了X70和X80钢,而后又开发了X100管线钢,碳含量降到0.01-0.04%,碳当量相应地降到0.35以下,真正出现了现代意义上的多元微合金化控轧控冷钢。
线材生产中的控制轧制和控制冷却技术
线材生产中的控制轧制和控制冷却技术线材是现代工业生产中使用频繁的一种材料,它广泛应用于电线电缆、机械制造、建筑材料等行业。
在线材生产过程中,控制轧制和控制冷却技术是关键的环节,它们直接影响着线材的质量、机械性能和用途范围。
一、控制轧制控制轧制是指通过改变轧制变形量、轧制温度、轧制速度、轧制力等因素,控制金属材料的形变和微观组织,达到调整线材力学性能、改善表面质量和优化产品用途的目的。
1、轧制变形量控制轧制变形量是指轧制前后的减压变化,它对线材的力学性能和表面质量有着直接影响。
为了保证线材的质量稳定和合格率,轧制变形量控制必须精准可靠,并考虑到批量变化和轧制型号的特定要求。
目前,国内外的轧制变形量控制采用电液伺服技术,通过实时监测轧制变形量变化,及时控制系统参数的变化,保证线材轧制变形量的稳定。
2、轧制温度控制轧制温度是指线材在轧制时的温度,它对线材的力学性能和表面质量有着重大影响。
过高或过低的温度会导致线材的晶粒过大或过小,从而影响线材的硬度、韧性和塑性等力学性能。
为了提高线材的机械性能和用途范围,轧制温度控制必须准确可靠,并考虑到金属材料的温度敏感性和轧制工艺的特定要求。
目前,国内外的轧制温度控制采用激光测温技术或红外线测温技术,通过实时监测线材温度变化,及时调整轧制温度,保证线材轧制温度的稳定。
3、轧制速度控制轧制速度是指线材在轧制过程中的速度,它对线材的表面质量和机械性能有着直接影响。
过高或过低的轧制速度会导致线材表面的纹路不均匀和线材的硬度、韧性等力学性能下降。
为了提高线材的表面质量和机械性能,轧制速度控制必须准确可靠,并考虑到轧制型号的特定要求。
目前,国内外的轧制速度控制采用伺服电机技术或电磁流体技术,通过实时监测线材的速度变化,及时调整轧制速度,保证线材轧制速度的稳定。
二、控制冷却控制冷却是指针对金属材料在热加工过程中产生的内应力、变形、晶粒长大等现象,通过采用不同的冷却方式和工艺参数,调整金属材料的组织和性能。
- 1、下载文档前请自行甄别文档内容的完整性,平台不提供额外的编辑、内容补充、找答案等附加服务。
- 2、"仅部分预览"的文档,不可在线预览部分如存在完整性等问题,可反馈申请退款(可完整预览的文档不适用该条件!)。
- 3、如文档侵犯您的权益,请联系客服反馈,我们会尽快为您处理(人工客服工作时间:9:00-18:30)。
中厚板的控制轧制与控制冷却工艺孙洪亮(材料成型及控制工程,1233010149)【摘要】近三十年以来,控制轧制和控制冷却技术在国外得到了迅速的发展,各国先后开展了多方面的理论研究和应用技术研究,并在轧钢生产中加以利用,明显的改善和提高了钢材的强韧性和使用性能,为了节约能耗、简化生产工艺和开发钢材新品种创造了有力条件。
目前国内外大多数宽厚板厂均采用控制轧制和控制冷却工艺,生产具有高强度、高韧性、良好焊接性的优质钢板。
控制轧制和控制冷却工艺的开发与理论研究进一步揭示了热变形过程中变形和冷却工艺参数与钢材的组织变化、相关规律以及钢材性能之间的内在关系,充实和形成了钢材热变形条件下的物理冶金工程理论,为制定合理的热轧生产工艺提供理论依据。
关键词:宽厚板厂,控制轧制,控制冷却【关键词】控制轧制;控制冷却;冷却段长度In the controlled rolling and controlled cooling technology of plate Abstract:For nearly 30 years, controlled rolling and controlled cooling technology obtained the rapid development in foreign countries, and countries successively carried out various theoretical research and applied technology research, and tries to use in the production of steel rolling, the obvious improve and enhance the tenacity of steel and the use of performance, in order to save energy consumption, simplify production process and development of new steel varieties created favourable conditions. Most lenient plate factory at home and abroad adopt controlled rolling and controlled cooling technology, production has high strength, high toughness and good weldability of high qualified steel plate. Controlled rolling and controlledcooling technology development and theory research of further reveals that the thermal deformation in the process of deformation and cooling process parameters and the change of the organization of the steel, the relevant laws and the internal relations between steel performance, enrich and formed steel thermal deformation under the condition of physical metallurgy engineering theory, to provide theoretical basis for reasonable hot-rolling process. Keywords: generous plate factory, controlled rolling and controlled coolingKey Words:Control rolling; Controlled cooling; Cooling length1引言近代工业发展对热轧非调质钢板的性能要求越来越高,除了具有高强度外,还要有良好的韧性、焊接性能及低的冷脆性。
目前世界上许多国家都利用控轧和控冷工艺生产高寒地区使用的输油、输气管道用钢板、低碳含铌的低合金高强度钢板、高韧性钢板,以及造船板、桥梁钢板、压力容器用钢板等。
控制轧制工艺的机理和特点:控制轧制工艺是指钢坯在稳定的奥氏体区域(Ar3)或在亚稳定区域(Ar3~Ar1)内进行轧制,然后空冷或控制冷却速度,以获得铁素体与珠光体组织,某些情况下可获得贝氏体组织。
现代控制轧制工艺应用了奥氏体的再结晶和未再结晶两方面的理论,通过降低板坯的加热温度、控制变形量和终轧温度,充分利用固溶强化、沉淀强化、位错强化和晶粒细化机理,使钢板内部晶粒达到最大细化从而改变低温韧性,增加强度,提高焊接性能和成型性能。
所以说,控制轧制工艺实际上是将形变与相变结合起来的一种综合强化工艺。
2文献综述2.1控制冷却系统的分类2.1.1冷却方式按冷却方式的不同,加速冷却可以归纳为三种类型。
(1)同时冷却方式。
即钢板进入冷却装置后,同时向钢板全长喷水使钢板达到规定的温度。
为了避免因辊道与钢板下表面的长时间接触造成冷却不均,冷却装置所在辊道具有摆动功能。
冷却装置的长度比最大的控冷轧件长度略长。
同时冷却方式可减少钢板头尾温差。
(2)连续冷却方式。
即钢板在通过控制冷却装置的过程中,边前进,边冷却,使之从头至尾渐次达到规定的终冷温度。
这是目前世界上采用最多的冷却方式。
(3)兼容冷却方式。
当钢板较厚较短时,可采用同时冷却方式;当钢板较长时,可采用连续冷却方式。
2.1.2冷却状态冷却状态是指钢板在控制冷却是否处于压力结束状态。
钢板在辊压状态下称为约束型冷却,反之,称为非约束型冷却。
约束型冷却装置主要用于直接淬火处理。
通过改善冷却均匀性,一些新建的控制冷却装置实现了在非约束型冷却方式下对钢板的直接淬火处理。
2.1.3喷水方式按喷水方式主要可以将冷却系统分为:层流、水幕、高压喷嘴、气水冷却等方式。
主要特点比较如下:高压喷嘴(MLPIC)特点:高密度、高压力的冷却水可连续到达钢板表面并形成紊流,水压可高达5bar,冷却水渗透性高,适合汽膜较厚的情况;冷却速度调节范围较宽,可用于加速冷却和直接淬火。
耗水量大,对水质要求高,喷嘴易堵塞。
集管层流冷却特点:水流为层流状,钢板冷却均匀,可冷却厚度20~50mm厚的钢板;需要的冷却区长,不易实现高冷速,不适合直接淬火冷却,对水质要求较高。
水幕冷却特点:水流为层流状,没有相邻水柱在冲击钢板时形成的干扰;冷却效率最高,对水质要求不严,冷却速度调节范围小,对需低速冷却的厚钢板不适用。
气水冷却(ADCO)特点:采用压缩空气使水雾化,钢板冷却均匀,冷却速度调节范围最宽。
设备管线复杂,噪声大。
2.2冷却装置与矫直机的关系(1)紧凑式。
控制冷却装置与热矫直机紧靠布置,同步操作,适合于厂房受限制的旧厂改造。
(2)分离式。
控制冷却的钢板完全离开控制冷却设备后再进入矫直机。
矫直速度和冷却装置内钢板移动速度一般均为0~2.5m/s。
两者工艺速度存在同步的条件,但也存在不利的影响。
冷却段钢板的速度根据钢种和规格确定。
而矫直速度还应参照板形情况。
薄规格钢板冷却时移动速度一般较快。
如果钢板强度高,钢板与矫直辊间的接触面减小,摩擦力小,矫直速度高时可能出现打滑。
2.3确定冷却装置位置的因素(1)冷却装置应靠近轧机。
轧件在轧机中结束变形后,将产生晶粒组织的回复和静态再结晶。
以C含量(质量分数)0.2%,变形量30%的钢为例,950℃时变形完成后的第10s,60%的奥氏体晶粒发生了再结晶。
钢板终轧至冷却开始的时间不宜超过20s。
(2)避开易受到冷却水及蒸汽的干扰工艺仪表。
为测厚仪、测宽仪、板形仪、钢板平面形状测量仪、镰刀弯测量仪留出安装位置。
(3)控制轧制中交叉轧制必要的辊道长度。
(4)应考虑矫直机对控制冷却装置位置的影响。
有少部分厂将矫直机设置在控制冷却装置前。
还有一些在控制冷却装置前设预矫直机,在控制冷却装置后再设矫直机。
其目的是保证钢板进入控制冷却段时具有平直的板形,也因为高强度钢板在冷却后很难再进行矫直。
在冷却装置前设置(预)矫直机将拉大了主轧线的设备间距,同时增加了钢板终轧至开始控制冷却的时间,会降低了控轧控冷的效果。
(5)采取同时冷却方式时,钢板完全进入冷却段后才开始喷水冷却,冷却装置更易于靠近轧机布置;采取连续冷却方式时,钢板应以冷却速度进入冷却段,冷却装置和轧机之间应留出钢板减速需要的辊道长度。
2.4 控轧控冷工艺对宽厚板工厂设备的要求控制轧制的显著特点是超低温轧制和高的轧制负荷,因而对轧机设备提出了极高的要求。
对于5m级宽厚板轧机,最大轧制压力应达100MN。
为了确保成品钢板的厚度精度、低平凸度、良好的平直度,轧机的刚性系数应达10kN/mm,支承辊直径达2000~2400mm,同时应采用工作辊弯辊等平直度控制手段。
为了确保控制轧制所需的大轧制力矩,轧机主传动电机功率应达2×10000 kW (上、下单独传动),允许最大过载力矩达2×4000kNm,电机转速0~60/120 r/min,最大轧制速度达6.5~7m/s。
经控制冷却后的钢板温度低于600℃,高牌号管线钢低于500℃,因而对加速冷却装置、热矫直机的能力及钢板平直度确保功能提出了很高的要求。
为了使冷却后的钢板在长度、宽度方向上温度均匀,国外加速冷却装置及相关计算机控制系统均有特殊控制功能。
为了保证钢板热矫直后具有良好平直度,国外出现了最大矫直力达40000kN等级的强力热矫直机,矫直辊辊缝调节采用全液压方式且具有动态调整功能,上辊组具有整体前后、左右倾斜功能及整体正弯、负弯功能,以消除钢板的单边浪、双边浪及中浪。
随着控轧控冷技术的发展,经控轧控冷工艺生产的钢板强度将进一步提高。
国外许多宽厚板厂已完成X100管线钢制造技术的开发及焊管试验,现具备小批量供货能力。
这对剪切线设备提出了新的要求。
国外出现了可剪切钢板强度达1200MPa(厚度≤40mm)的强力三曲轴(或二曲轴)滚切式剪切机,此类设备适应了控轧控冷技术的发展。
控轧控冷工艺复杂,各类工艺参数控制精度要求极高。
从加热至热矫直机(即:轧制线),至少必须由两级计算机(L1、L2)实施生产工艺过程全自动控制,同时必须设置大量的钢板位置检测仪表及测温仪表。
国外大多数宽厚板厂均采用四级计算机控制。