钢轨伤损检测技术和设备
钢轨伤损-标准-检测与维修可修改文字

典型钢轨伤损-缺陷类
焊接接头裂纹
典型钢轨伤损-疲劳类
轨头鱼鳞状剥离
典型钢轨伤损-疲劳类
钢轨表面剥离
典型钢轨伤损-疲劳类
轨头剥离严重时引发的掉块
典型钢轨伤损-疲劳类
轨头核伤及断轨典型钢轨伤损-磨耗类
钢轨波磨
1.2 焊接接头伤损
伤损现象及形成原因
提高钢轨硬度
➢ 钢轨耐磨性能随硬度增加。采用轨头全长淬火热处理 钢轨或合金钢轨,将钢轨头部硬度提高到340-370HB, 可显著延长曲线钢轨使用寿命。
科学合理的轮缘润滑
➢ 采用固体润滑。采用固体润滑时,曲线钢轨侧磨可维 持在0.02mm/Mt左右且基本无剥离。使用车载喷脂润 滑时,减磨效果相当但钢轨剥离严重。
钢轨材质不良
疲劳裂纹萌生及扩展
鱼鳞
麻点
剥离掉块 核伤及断轨
钢轨疲劳的减缓措施
改善钢轨材质
➢ 提高钢轨材料的纯净度。减少夹杂物,减少有害元素 及气体含量。
➢ 改进热处理工艺。轨头应具有足够深度和均匀的淬火 硬化层,细化珠光体晶粒。
➢ 采用优质合金钢轨。
合理地进行钢轨大机打磨
➢ 采用钢轨预打磨去除钢轨表面脱碳层; ➢ 采用钢轨定期打磨,提高钢轨磨耗速率,去除钢轨表
严格控制钢中夹杂物含量。要求A类(硫化物) 夹杂物≤2-2.5级,B类(氧化物)、C类(硅 酸盐)、D类(球状氧化物)夹杂物≤1.01.5级。
轨钢中非金属夹杂物要求/级
标准
TB/T2344 250 km/h 350km/h
A类(硫 B类(氧 化物) 化铝)
≤2.5 ≤2.5 ≤2.0
≤2.0 ≤1.5 ≤1.0
钢轨平直度要求/mm
浅谈铁路线路钢轨设备伤损主要类型及检测方法

浅谈铁路线路钢轨设备伤损主要类型及检测方法铁路线路的铁轨是其中最重要的构成部分之一,其在长期的使用过程中,会逐渐出现一些伤损情况。
这些伤损的主要类型包括:弯曲、断裂、疲劳、磨损和裂纹等。
其中,弯曲和断裂是较为严重的伤损类型,容易导致运行事故的发生,因此必须加以重视。
1. 直接观察法直接观察法是最基本的、也是最直接的一种检测方法。
通过对铁轨表面进行目测观察,可以快速发现铁轨表面的裂缝、磨损等缺陷,以及铁轨的弯曲、扭曲等情况。
这种方法通常用于定期巡视、日常维护和突发情况的处理。
2. 光学检测法光学检测法是利用光学显微镜、摄像头等设备对铁轨表面进行高倍率放大,以发现微小裂缝、麻点、划痕等伤损类型。
这种方法对于发现疲劳、裂纹等内部伤损情况非常有效,但要求对设备的操作和手段的熟练度较高。
3. 超声波检测法超声波检测法是利用超声波穿透铁轨,对铁轨内部的各种伤损进行检测。
超声波在穿过铁轨时,会受到材料的反射、散射等影响,形成一定的声波图谱,通过对图谱的分析和处理,可以发现铁轨内部的伤损情况。
这种方法对于裂纹、疲劳等内部伤损情况的检测效果较好,但需要专业的设备和技术人员。
4. 磁粉探伤法磁粉探伤法是一种利用磁力线对铁轨表面进行检测的方法。
磁粉探伤时,将铁轨表面涂上一层磁性粉末,然后通过磁力线的作用,使粉末在伤损部位形成某种形状的磁性粉末图案,从而发现铁轨表面的裂纹、缺陷和疲劳等伤损。
综上所述,铁路线路钢轨设备的伤损类型较为丰富,检测方法也各有优缺点。
因此,在铁路运行过程中,需要结合各种检测手段,及时发现铁轨的各种伤损情况,以保证铁路运行的安全性和可靠性。
浅谈铁路线路钢轨设备伤损主要类型及检测方法

浅谈铁路线路钢轨设备伤损主要类型及检测方法铁路线路是现代交通运输的重要组成部分,它承担着连接城市与城市、地区与地区的重要任务。
而铁路线路的钢轨设备作为铁路运输的基础设施,其安全性和稳定性至关重要。
由于长期的使用和自然因素的影响,钢轨设备难免会出现损伤。
及时发现并修复钢轨设备的损伤对于保障铁路线路的安全和畅通具有重要意义。
本文将就铁路线路钢轨设备的损伤主要类型及检测方法进行探讨。
1. 疲劳裂纹疲劳裂纹是由于轮轨交会反复作用下引起的,通常出现在轨道的压应力和拉应力交替作用的地方,是铁路线路钢轨设备的常见损伤。
疲劳裂纹的存在会导致钢轨设备的强度下降,如果不及时修复会引发更严重的安全隐患。
2. 磨耗磨耗是指钢轨设备在使用过程中,由于轮轨间的摩擦作用,导致表面金属材料的逐渐流失。
磨耗会引起钢轨设备的几何形态发生变化,进而影响其使用寿命和安全性。
3. 变形变形是指钢轨设备在运行过程中由于受到外力作用或者自身质量和温度引起的形状改变。
变形会导致钢轨设备的受力状态发生变化,进而影响其安全性和稳定性。
4. 腐蚀腐蚀是指钢轨设备在使用过程中,由于大气、水分、化学物质等外界环境因素的影响,导致金属材料发生化学反应而引起的损伤。
腐蚀会导致钢轨设备的强度和稳定性下降,严重时甚至会影响使用寿命。
1. 目视检查目视检查是最基础的检测方法,通过铁路工作人员巡视铁路线路,发现可能存在的钢轨设备损伤。
目视检查通常是靠经验进行的,需要高度的警惕性和责任心。
目视检查存在局限性,不能发现微小和隐蔽的损伤。
2. 超声波检测超声波检测是一种非破坏性的检测方法,通过超声波技术对钢轨设备的内部进行检测。
超声波可以穿透金属材料,当遇到内部缺陷时会发生反射。
通过分析超声波的反射信号,可以确定钢轨设备的损伤情况和位置。
3. 磁粉检测磁粉检测是一种常用的表面缺陷检测方法,通过在钢轨设备表面喷洒磁粉,并施加磁场,当表面存在裂纹和其他缺陷时,磁粉会在这些缺陷处聚集形成磁束。
浅谈铁路线路钢轨设备伤损主要类型及检测方法

浅谈铁路线路钢轨设备伤损主要类型及检测方法铁路线路作为重要的基础设施,铁路伤损的检测和修复对于保障铁路运输安全和高效运营至关重要。
铁路线路中的钢轨对列车行驶产生重要的作用,而钢轨的损伤会对列车以及路面整体的安全造成影响。
因此,钢轨的检测和维护也是铁路运输保障体系中的重要组成部分。
1. 变形伤损钢轨的变形伤损通常是由于列车行驶时对钢轨的冲击和振动等因素产生的,这些因素会导致钢轨发生变形。
钢轨变形主要表现为弯曲和扭曲,严重时会导致钢轨断裂。
变形伤损可导致轨面不平整,对列车行驶造成较大的滚动阻力。
2. 磨损伤损钢轨的磨损伤损主要是由于列车行驶时的摩擦和磨损作用导致的。
磨损伤损通常会导致钢轨表面变得粗糙,轨面高度缩短,对列车行驶造成较大的噪音和震动。
3. 腐蚀伤损钢轨的腐蚀伤损通常是由于大气中的化学物质和水分在钢轨表面的作用下产生的,腐蚀伤损严重时会导致钢轨断裂。
腐蚀伤损可导致钢轨表面光滑度下降,对列车行驶造成较大的阻力,严重影响铁路运输的安全和效率。
二、钢轨设备伤损的检测方法1. 视觉检测法视觉检测法是最基本的钢轨设备伤损检测方法之一,通过人工检查钢轨表面是否存在变形、磨损、腐蚀等伤损。
视觉检测法适用于各种轨道型号和业务,但由于其受专业人员技术水平的限制,检测结果可能存在不确定性。
2. 触发式检测法触发式检测法是通过调用钢轨设备伤损监测仪器,对钢轨表面进行接触式探测,通过感应点的信号反馈,获得钢轨伤损的信息。
触发式检测法在检测的精度和可靠性方面都比视觉检测法更高,但需要具有专业修理能力的技术人员进行操作。
非接触式检测法采用光学原理进行检测,对钢轨表面图像进行采集和分析,得到钢轨伤损信息。
该方法不会对钢轨表面造成损伤,而且可以进行远距离检测,减少对区间列车的影响。
缺点是需要设备成本高。
总之,不同的钢轨设备伤损检测方法在检测精度、成本和适用范围等方面各具优势和劣势。
有效的钢轨设备伤损检测方法可以大幅度提高铁路运输的安全性和效率,在铁路运输保障中扮演着重要角色。
铁路钢轨缺陷伤损巡检与监测技术综述

铁路钢轨缺陷伤损巡检与监测技术综述随着我国高速铁路的快速发展,对钢轨基础的设施维护和安全防护提出了挑战。
标签:铁路钢轨;缺陷伤损;监测技术钢轨服役缺陷损伤类型较为复杂,铁路运输通过轮轨相互作用实现列车运行,铁路损伤是铁路运输中最昂贵的问题一、钢轨常见的伤损及检测分析1.最常见的伤损是:(1)铁路轨头的横向裂缝。
这是由于轨道材料的缺陷或接触疲劳,严重的磨损和磨损,大部分在5毫米到10毫米之间(2)轨道接头损伤。
大部分的伤害都是由于保护和一个较低的圆圈造成的。
由较小的弧线束产生的损伤,通常在接缝的夹板上表现出来,表现为垫圈磨损和轨道顶部的减压现象。
(3)轨道的水平和垂直纵向裂缝。
这是由于轧制过程的缺陷或通常发生在钢轨表面的外部载荷造成的。
(4)铁路底部裂缝。
这是一种横向裂缝或从轨道底部坠落的现象,主要是由弯曲缺陷、生锈的洞和轨道表面的划痕造成的。
(5)焊接损伤。
这些缺陷,如冷凝孔隙、气孔、烧伤、光斑、裂缝、焊缝、焊缝、焊缝、焊缝、焊缝等,都是极其有害的。
2.目前,无损检测技术主要用于钢轨的探伤,它不会对试件的材料和结构造成损伤,可以通过声、光、电、磁等物理手段检测被测零件的缺陷位置、尺寸、性质和数量。
具体包括以下检测方法:(1)超声探伤检测。
对于铸件、钻孔、焊接和金属、非金属和复合材料板,可以检测出内部缺陷的大小、位置、性质、掩埋等。
然而,很难准确地量化缺陷,也需要对试件的形状进行一些限制。
(2)射线探伤。
适用于铸件和焊缝等部件的内部容积型缺陷可以显示和保存检测结果,但检测成本很高,很难检测出裂纹类型的缺陷。
(3)碳粉探伤。
铸件、锻件、焊接件和机械件的内部缺陷具有灵敏度高、检测速度快、操作简单等优点;然而,缺陷只能检测表面和附近表面的内部缺陷的位置和长度,而不能检测内部缺陷的深度。
(4)渗透探伤。
它适用于有色金属的铸造、锻造和焊接缺陷。
(5)涡流探伤。
它适用于在广泛领域中检测钢铁和有色金属等导电材料,并应使用无接触自动检测。
第4章 钢轨伤损检测技术-2

第一节 钢轨功用、类型及探伤概述
抗拉强度: σs=227+803%C+87%Si+115%Mr+133%Cr+891%P+61 4%V±19 屈服强度: σy=101+469%C+36%Si+85%Mn16+116%Cr+0%P+634 %V±21 伸长率: δ0=30.8-22.6%C-1.7%Si+0%Mn-2.3%Cr+0%P+ 4%V±0.9
第一节 钢轨功用、类型及探伤概述 设计原则: 保持稳定 钢轨高:轨底宽=1.15—1.20 轧制冷却均匀各部轧制合理
第一节 钢轨功用、类型及探伤概述
钢轨截面的主要尺寸:
50轨
第一节 钢轨功用、类型及探伤概述
60轨
第一节 钢轨功用、类型及探伤概述
75轨
第一节 钢轨功用、类型及探伤概述
第三 钢轨材质及其力学指标 钢轨的材质和机械性能取决于化学成分、金属组织和热 处理工艺。
第一节 钢轨功用、类型及探伤概述
钢轨的力学性能也是钢轨的主要特征,包括强度极限 σb、屈服极限σs、疲劳极限σr 、伸长率、断面收缩率ψ、 冲击韧性αk 和布氏硬度指标HB等。这些指标对钢轨的 承载能力、磨损、压溃、断裂及其他损伤有很大影响, 高速铁路钢轨还对裂纹扩展速度、残余应力、落锤性能 等提出了比常规铁路更高的要求。
重轨。按轨型分类 分为重轨和轻轨。 从国内铁道应用而言,50㎏/m及以上钢轨均称 之为 目前使用的钢轨主要是50㎏/m及以上的钢轨。 在高速铁路和繁忙干线上主要使用60kg/m钢轨, 在重载铁路上使用75kg/m钢轨。
第一节 钢轨功用、类型及探伤概述
按轨钢的化学成分分类 分为碳素钢轨,如U71Mn(钢中无其他合金元素,又 称普通轨钢);
浅谈铁路线路钢轨设备伤损主要类型及检测方法
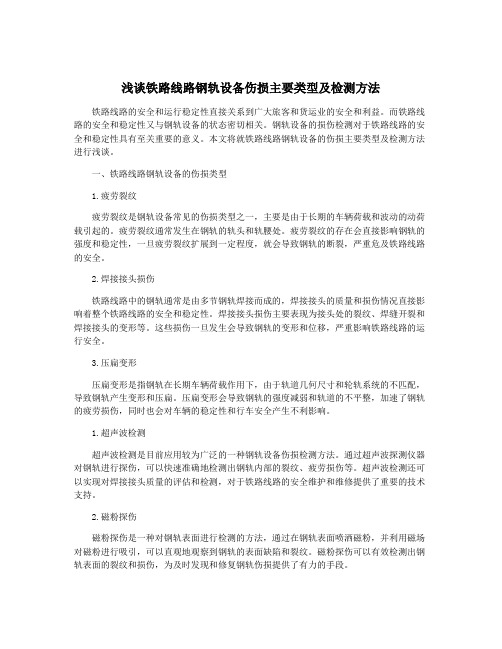
浅谈铁路线路钢轨设备伤损主要类型及检测方法铁路线路的安全和运行稳定性直接关系到广大旅客和货运业的安全和利益。
而铁路线路的安全和稳定性又与钢轨设备的状态密切相关。
钢轨设备的损伤检测对于铁路线路的安全和稳定性具有至关重要的意义。
本文将就铁路线路钢轨设备的伤损主要类型及检测方法进行浅谈。
一、铁路线路钢轨设备的伤损类型1.疲劳裂纹疲劳裂纹是钢轨设备常见的伤损类型之一,主要是由于长期的车辆荷载和波动的动荷载引起的。
疲劳裂纹通常发生在钢轨的轨头和轨腰处。
疲劳裂纹的存在会直接影响钢轨的强度和稳定性,一旦疲劳裂纹扩展到一定程度,就会导致钢轨的断裂,严重危及铁路线路的安全。
2.焊接接头损伤铁路线路中的钢轨通常是由多节钢轨焊接而成的,焊接接头的质量和损伤情况直接影响着整个铁路线路的安全和稳定性。
焊接接头损伤主要表现为接头处的裂纹、焊缝开裂和焊接接头的变形等。
这些损伤一旦发生会导致钢轨的变形和位移,严重影响铁路线路的运行安全。
3.压扁变形压扁变形是指钢轨在长期车辆荷载作用下,由于轨道几何尺寸和轮轨系统的不匹配,导致钢轨产生变形和压扁。
压扁变形会导致钢轨的强度减弱和轨道的不平整,加速了钢轨的疲劳损伤,同时也会对车辆的稳定性和行车安全产生不利影响。
1.超声波检测超声波检测是目前应用较为广泛的一种钢轨设备伤损检测方法。
通过超声波探测仪器对钢轨进行探伤,可以快速准确地检测出钢轨内部的裂纹、疲劳损伤等。
超声波检测还可以实现对焊接接头质量的评估和检测,对于铁路线路的安全维护和维修提供了重要的技术支持。
2.磁粉探伤磁粉探伤是一种对钢轨表面进行检测的方法,通过在钢轨表面喷洒磁粉,并利用磁场对磁粉进行吸引,可以直观地观察到钢轨的表面缺陷和裂纹。
磁粉探伤可以有效检测出钢轨表面的裂纹和损伤,为及时发现和修复钢轨伤损提供了有力的手段。
3.动载试验动载试验是指通过实际列车运行时的振动和荷载对铁路线路进行监测和检测。
通过动载试验可以实时地监测钢轨的变形和振动情况,及时发现钢轨的伤损状况,为铁路线路的修复和维护提供了重要的数据支持。
浅谈铁路线路钢轨设备伤损主要类型及检测方法

浅谈铁路线路钢轨设备伤损主要类型及检测方法铁路线路是国家交通网的重要组成部分。
铁路线路的牢固程度和安全性不仅关系到列车行驶速度和运行时间,更关系到旅客货物的安全。
线路钢轨是铁路线路的重要组成部分,也是铁路线路传播荷载的主要组成部分。
然而,由于线路钢轨在平时运行过程中承受着沉重的工作任务,所以必然会出现一些疲劳和损坏的情况。
线路钢轨的损伤并不是一种单一的形式,不同类型的损伤会对列车运行产生不同的安全隐患。
常见的钢轨损伤类型包括疲劳断裂、应力腐蚀开裂、裂纹、捆扎以及变形等。
这些钢轨损伤类型都需要及时检测,以保证钢轨的正常运行和列车的运行安全。
疲劳断裂是钢轨损伤中最常见的一种类型。
它是由于线路不平、地震、温度变化等因素引起的轨道载荷不稳定和铁路轨道钢轨的疲劳断裂产生的。
疲劳断裂的主要特征是发生在钢轨的脚部和头部,出现断裂口,随着时间的推移,断口处会出现变形和变色的情况。
疲劳断裂的检测方法主要有脉冲热成像技术、超声波测试技术和涡流测试技术等。
应力腐蚀开裂是钢轨损伤的另一种常见类型。
它是由于环境中的气体、水分、盐度等因素作用于钢轨表面而引起的。
应力腐蚀开裂的主要特征是在钢轨表面产生裂纹,严重的情况会导致钢轨断裂。
应力腐蚀开裂的检测方法主要有超声波检测技术、渗透测试技术和磁粉检测技术等。
裂纹是一种较为小型的钢轨损伤,通常出现在钢轨的脚部和边缘。
裂纹的主要特征是钢轨表面出现细小的裂纹,导致轨道变形和破损。
裂纹的检测方法主要有感应测试技术、渗透测试技术和超声波测试技术等。
捆扎是钢轨损伤中一种特殊的损坏类型。
它是由于地震、张力作用和温度变化等因素引起的,会导致钢轨的扭曲和弯曲。
捆扎的主要特征是钢轨的变形和变形。
捆扎的检测方法主要有激光测试技术、光电测试技术和位移测试技术等。
总之,钢轨损伤的类型各不相同,而且每一种类型都有独特的检测方法。
高效、准确、可靠的线路钢轨设备检测技术不仅有助于保障铁路线路的运行安全,更有利于提高铁路线路的运行质量和效率。
- 1、下载文档前请自行甄别文档内容的完整性,平台不提供额外的编辑、内容补充、找答案等附加服务。
- 2、"仅部分预览"的文档,不可在线预览部分如存在完整性等问题,可反馈申请退款(可完整预览的文档不适用该条件!)。
- 3、如文档侵犯您的权益,请联系客服反馈,我们会尽快为您处理(人工客服工作时间:9:00-18:30)。
❝钢轨轮廓及平顺度测量仪
❝钢轨表面裂纹深度测量仪
❝导波法钢轨损伤测量设备
❝螺栓松动或损坏自动识别设备
❝光纤光栅技术对轨道交通结构沉降实时监测系统
功能:钢轨横断面轮廓和纵向平顺度测量◦横断面测量和磨耗分析
◦纵向粗糙度测量、短波不平顺和波磨分析◦自动测量和分析数据
普通版
◦便携
◦自备电源(单次充电>30小
时)
◦精度:微米/插值
◦横断面测量及垂磨、侧磨计
算报告生成
算、报告生成
◦纵向平顺度测量及滤波和
1/3倍频程分析报告生成
1/3倍频程分析、报告生成
高精度版
◦便携
◦自备电源(单次充电>30小时)
自备电源(单次充电30小时)◦精度:微米
◦横断面测量及垂磨、侧磨计算、
报告生成
◦纵向平顺度测量及滤波和1/3倍
频程分析、报告生成
频程分析报告生成
◦三维模型的廓面计算
标准配置
◦扫描仪;
◦平板电脑;
◦移动电源;
具包;
◦工具包;
◦数据采集软件;◦数据处理软件。
功能:采用涡流技术检测钢轨表面疲劳裂纹(鱼鳞 纹)的深度
◦
裂纹深度测量和显示◦
数据快速存储◦
平板电脑显示◦自带电源
功能:基于超声导波技术检测钢轨长度方向的表面 和内部损伤
◦
在线和离线设备◦
检测钢轨纵向不连续(锈蚀掉块、电击伤)◦
精度:毫米级◦
分辨率:损伤>4mm ◦
检测范围:1km ◦损伤精确定位:定位误差<1%
识别各种钢轨纵向不连续(断裂电缆识别各种钢轨纵向不连续(断裂、电缆
线、接头、列车)
功能:检测扣件螺栓、浮置板剪力铰螺栓等的松动、 断裂
◦近距离非接触采集和判别压力传感器
无线射频识别
5.光纤光栅技术对轨道交通结构沉降实时监测系统
系统主要硬件
系统主要硬件设备
设备•光纤光栅传感器波长信号的读取和解调,•实时监测结构的沉降变形、振动加速度
概述
与计算机设备配套使用
1.1.光纤光栅光纤光栅沉降静力水准仪准仪、加速、加速
2.光纤光栅解调仪
度计
•利用VPN 网络设备或•提供数据快速计算、 4.通讯通讯发送发送及接及接收收设备
3.工控机
3G 设备进行关键数据(如超限警报)发送、接收
传输功能,保证与软件兼容,具有较大的存储空间及便携性
说明
关键硬件设备参数
光纤光栅静力水准仪
内部意
设计图
整体图
量程0~100mm(可定制其他量程)
精度1‰F.S*.示意分辨率0.01mm 连接方式PC/FC或熔接使用温度-30~85℃温度补偿方式
自补偿
外形尺寸Φ90×200mm(可根据量程进行定制)
*注:‰F.S.指测量精度为满量程的1‰
说明
关键硬件设备参数
光纤光栅加速度计
•精度高、灵敏度高、抗干扰、寿命长等
优点
•可与其他类型的光纤光栅传感器组成全
光监测网
•可长期经受的恶劣条件
项目参数
标准量程10G
测量精度3‰F.S.*
分辨率0.1 ‰ F.S.(在与SEN-01解调仪配套情况下)
波长范围1525nm~1565nm
尺寸23×26×61.5 mm
连接形式FC/PC或熔接
使用温度-30℃~85℃
*注:‰F.S.指测量精度为满量
程的1‰
说明
现场硬件设备
控制机柜
VPN 中心端现场沉降监测
服务器及相关采集光纤光栅调中端设备
仪等设备已安装于地铁1号线晓东村沉降监测服务器
节仪
站三角机房内,并已投入数据采集工作中。
晓东村站三角机
说明
系统软件组成及功能
数据库软沉降监测数据服务器件软件
昆明轨道交降交通沉降实时监测软件系统基于
windows 操作系统开发可光纤光栅沉降监测系统解调仪物理量转换软件
开发,可
适用于目
前各种常昆明市轨道交通基础结构沉降实时监测系统研究项目
(一期)
软件
用操作系统。
监测系统现场监测系统现场实施实施
平面布局
隧道测量起点附近最近的定位铜钉为基准,铜钉处设置基准的水准仪静力水准仪
⏹共布置14处断面,其中隧道11处、过渡段3处
⏹在矩形隧道的2处双线断面中间挡墙也安装静力水准仪共设置21个静力水安装静力水准仪,共设置21个静力水准仪▲共布置3处断面,分别布置于盾构隧道、加速度计布处断,分别布盾矩形隧道及过渡段
▲每处断面中,安装在轨枕块、轨道板和底座板上,共9个加速度计
监测系统现场监测系统现场实施实施
纵断面布局
试验段起点隧道底部到终点隧道底
部的高程差约有7.64m ,采用级联传
感器克服高程差带来的数据误差。
全站仪定高程程误
标记高程
现场设备现场设备安装安装
水管安装
细节
处理
现场安装水管
✓需避免与已有线路建筑冲突
水管气泡排除检漏工作•保证保证监测
监测精度✓水管气泡排除、检漏工作
•不影响地铁正常运营
•
现场水管防护处
现场设备
现场设备安装
安装 水准仪和加速度计安装
级联传感
器
水准仪安装级联水准仪安
装
水准仪过线网安装
监测传感
器
加速度计
数据传输及监控
系统数据传输网络
通过VPN网络和3G无线网络连接组成
各传感器的数据经数据传输网络保存在服务器的数据库
通过3G设备和VPN设备与服务器相沉降超限通过VPN或3G网络自动报警
系统传输网络拓连,实现数据的查询分析
扑
现场实施
数据传输及监控
系统应用
•提供现场多水准仪传感器数据查询数据询
接收数据时间累计沉降量相对沉降量
提供多速度计传感加速度计编号加速度计数据分析系统报警记录
•提供现场多加速度计传感器数据查询
加速度时域分析传感器编号
接收
数据时间
计算沉降量
加速度频域分析
•提供系统故障报警查询
系统报警记录
•沉降超限超限自动报警
线路纵向相对沉降监测
盾构隧道纵向相对沉降监测
-4-6-54 测点1沉降量
去噪后-9-8-7沉降量/m m
沉降变化曲线
处理
通过引起基础振动使得液压发生变化通过引起基础振动使得液压发生变化,液面压力和位移的关系的瞬间变化被捕捉记录,液面平稳后恢复正常,表现出传感器有较好的监测能力
/时间/10分钟。