色差控制管理规定
印刷品色差国家标准
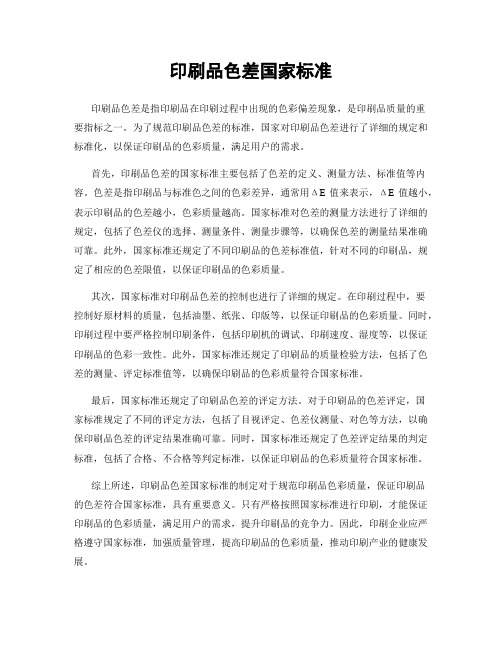
印刷品色差国家标准印刷品色差是指印刷品在印刷过程中出现的色彩偏差现象,是印刷品质量的重要指标之一。
为了规范印刷品色差的标准,国家对印刷品色差进行了详细的规定和标准化,以保证印刷品的色彩质量,满足用户的需求。
首先,印刷品色差的国家标准主要包括了色差的定义、测量方法、标准值等内容。
色差是指印刷品与标准色之间的色彩差异,通常用ΔE值来表示,ΔE值越小,表示印刷品的色差越小,色彩质量越高。
国家标准对色差的测量方法进行了详细的规定,包括了色差仪的选择、测量条件、测量步骤等,以确保色差的测量结果准确可靠。
此外,国家标准还规定了不同印刷品的色差标准值,针对不同的印刷品,规定了相应的色差限值,以保证印刷品的色彩质量。
其次,国家标准对印刷品色差的控制也进行了详细的规定。
在印刷过程中,要控制好原材料的质量,包括油墨、纸张、印版等,以保证印刷品的色彩质量。
同时,印刷过程中要严格控制印刷条件,包括印刷机的调试、印刷速度、湿度等,以保证印刷品的色彩一致性。
此外,国家标准还规定了印刷品的质量检验方法,包括了色差的测量、评定标准值等,以确保印刷品的色彩质量符合国家标准。
最后,国家标准还规定了印刷品色差的评定方法。
对于印刷品的色差评定,国家标准规定了不同的评定方法,包括了目视评定、色差仪测量、对色等方法,以确保印刷品色差的评定结果准确可靠。
同时,国家标准还规定了色差评定结果的判定标准,包括了合格、不合格等判定标准,以保证印刷品的色彩质量符合国家标准。
综上所述,印刷品色差国家标准的制定对于规范印刷品色彩质量,保证印刷品的色差符合国家标准,具有重要意义。
只有严格按照国家标准进行印刷,才能保证印刷品的色彩质量,满足用户的需求,提升印刷品的竞争力。
因此,印刷企业应严格遵守国家标准,加强质量管理,提高印刷品的色彩质量,推动印刷产业的健康发展。
印刷色差控制指引ZJ002
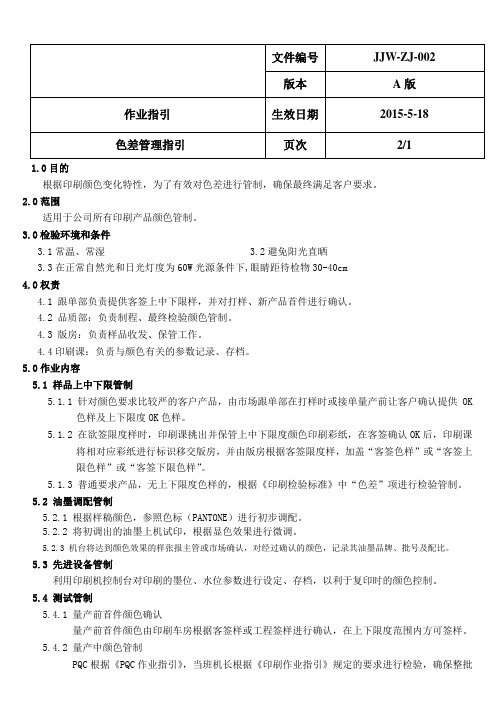
1.0目的根据印刷颜色变化特性,为了有效对色差进行管制,确保最终满足客户要求。
2.0范围适用于公司所有印刷产品颜色管制。
3.0检验环境和条件3.1常温、常湿 3.2避免阳光直晒3.3在正常自然光和日光灯度为60W光源条件下,眼睛距待检物30-40cm4.0权责4.1 跟单部负责提供客签上中下限样,并对打样、新产品首件进行确认。
4.2 品质部:负责制程、最终检验颜色管制。
4.3 版房:负责样品收发、保管工作。
4.4印刷课:负责与颜色有关的参数记录、存档。
5.0作业内容5.1 样品上中下限管制5.1.1 针对颜色要求比较严的客户产品,由市场跟单部在打样时或接单量产前让客户确认提供OK色样及上下限度OK色样。
5.1.2 在欲签限度样时,印刷课挑出并保管上中下限度颜色印刷彩纸,在客签确认OK后,印刷课将相对应彩纸进行标识移交版房,并由版房根据客签限度样,加盖“客签色样”或“客签上限色样”或“客签下限色样”。
5.1.3 普通要求产品,无上下限度色样的,根据《印刷检验标准》中“色差”项进行检验管制。
5.2 油墨调配管制5.2.1 根据样稿颜色,参照色标(PANTONE)进行初步调配。
5.2.2 将初调出的油墨上机试印,根据显色效果进行微调。
5.2.3机台将达到颜色效果的样张报主管或市场确认,对经过确认的颜色,记录其油墨品牌、批号及配比。
5.3 先进设备管制利用印刷机控制台对印刷的墨位、水位参数进行设定、存档,以利于复印时的颜色控制。
5.4 测试管制5.4.1 量产前首件颜色确认量产前首件颜色由印刷车房根据客签样或工程签样进行确认,在上下限度范围内方可签样。
5.4.2 量产中颜色管制PQC根据《PQC作业指引》,当班机长根据《印刷作业指引》规定的要求进行检验,确保整批产品颜色在上下限度内,并尽量保持整批颜色一致。
深圳市佳佳旺印刷有限公司5.5 最终限度管制5.5.1 在最终检验时,色差超过上下限度的产品要挑出。
色差控制管理规定

1、目的规范生产过程产品色差控制流程,保证生产过程中产品颜色与标样一致。
2、范围本程序适用于公司各生产工序。
3、定义无4、参考文件无5、职责5.1品管部负责标样的签发。
5.2品管部IPQC负责过程生产中的监控。
5.3生产车间负责按照标准操作。
6、工作内容6.1晒版6.1.1晒版须根据作业指导书要求设置曝光时间、显影时间。
晒版标准为阳图2%有点子,98%有轮廓,3%点子结实完整,97%的网点清晰透亮无灰雾。
6.1.2对于网点版,必须如实记录灯使用情况、爆光时间、药水情况,便于下次生产时还原工艺参数,以保障每次晒出的网点版的一致性。
6.1.3各种色彩控制条齐全完整。
6.2机台开机签样与标样色差的控制6.2.1公司所有生产的产品菲林必需有标准的颜色测控条。
6.2.2所有金银卡纸、镭射纸和珠光打底的产品(包括烟标和社会单)机台在签样与生产时按以下要求操作。
6.2.2.1颜色要求:目测与标样一致,以标样为准取五点平均后设值,用CRII5检测,△a≤1.5,△b≤1.5△E≤3.0,a,b值尽量与标样a,b值接近。
6.2.2.2取值要求:雪花油类在印刷雪花油后直接测量,非雪花油类用蒙片蒙住后测量取值,有渐变网在渐变网为零和100%处分别取值。
纸张有阴阳面的在同一面取值。
6.2.2.3测量要求:雪花油类产品在印刷雪花油后直接测量,非雪花油类用蒙片蒙住后测量,有渐变网在渐变网为零和100%处分别测量6.2.2.4蒙片要求:干净,统一,细哑光,与被检测色接触紧密。
6.2.2.5签样要求:目测与标样一致,△a≤1.5,△b≤1.5△E≤3.0,a,b值尽量与标样a,b值接近,横向密度D±0.03,D值尽量与标样一致。
6.2.2.6控制要求:目测与标样一致,△a≤1.5,△b≤1.5△E≤3.0,a,b值尽量与标样a,b值接近,横向密度D±0.03,D值尽量与标样一致,整批密度D±0.05,白卡或铜版纸密度D±0.02.6.2.3直接在白卡纸或铜版纸上面印刷的产品(包括烟标和社会单)机台在签样和生产时,颜色以仪器检测△a≤1.0,△b≤1.0,深色△E≤1.3,浅色△E≤0.8,横向密度D ±0.02,整批密度D±0.03.目测与标样一致。
正常色差允许范围
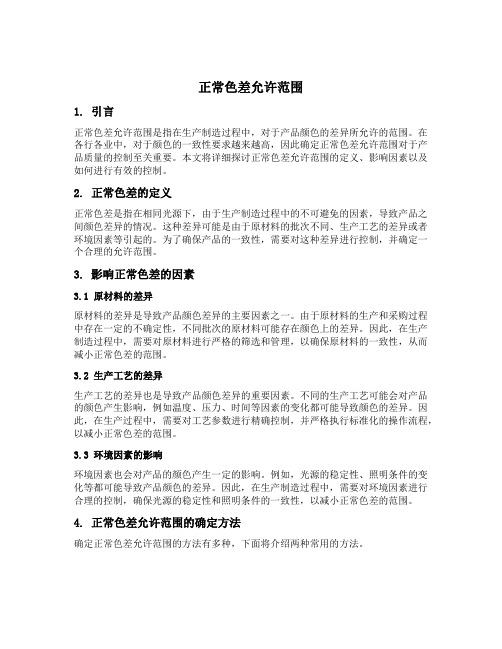
正常色差允许范围1. 引言正常色差允许范围是指在生产制造过程中,对于产品颜色的差异所允许的范围。
在各行各业中,对于颜色的一致性要求越来越高,因此确定正常色差允许范围对于产品质量的控制至关重要。
本文将详细探讨正常色差允许范围的定义、影响因素以及如何进行有效的控制。
2. 正常色差的定义正常色差是指在相同光源下,由于生产制造过程中的不可避免的因素,导致产品之间颜色差异的情况。
这种差异可能是由于原材料的批次不同、生产工艺的差异或者环境因素等引起的。
为了确保产品的一致性,需要对这种差异进行控制,并确定一个合理的允许范围。
3. 影响正常色差的因素3.1 原材料的差异原材料的差异是导致产品颜色差异的主要因素之一。
由于原材料的生产和采购过程中存在一定的不确定性,不同批次的原材料可能存在颜色上的差异。
因此,在生产制造过程中,需要对原材料进行严格的筛选和管理,以确保原材料的一致性,从而减小正常色差的范围。
3.2 生产工艺的差异生产工艺的差异也是导致产品颜色差异的重要因素。
不同的生产工艺可能会对产品的颜色产生影响,例如温度、压力、时间等因素的变化都可能导致颜色的差异。
因此,在生产过程中,需要对工艺参数进行精确控制,并严格执行标准化的操作流程,以减小正常色差的范围。
3.3 环境因素的影响环境因素也会对产品的颜色产生一定的影响。
例如,光源的稳定性、照明条件的变化等都可能导致产品颜色的差异。
因此,在生产制造过程中,需要对环境因素进行合理的控制,确保光源的稳定性和照明条件的一致性,以减小正常色差的范围。
4. 正常色差允许范围的确定方法确定正常色差允许范围的方法有多种,下面将介绍两种常用的方法。
4.1 CIE Lab色差公式CIE Lab色差公式是一种常用的确定正常色差允许范围的方法。
该方法基于人眼对颜色的感知,通过计算样品与标准样品之间的色差值来确定允许范围。
具体计算过程较为复杂,需要使用专业的色差仪和相关软件进行计算。
4.2 制定标准样品制定标准样品是另一种确定正常色差允许范围的常用方法。
专业的色彩管理和色差控制详解

四色 测量
印张测控条
(客户首签和大货首签)
分光密度仪
合格 收货
色差 ⊿E≦2.5
不合格 拒收
THANKS
ISO 12647-2∶2013标准的胶印过程控制
不同批次纸张色差
3%以下网点再现
50%网点扩大
实地密度浮动
中性灰的偏色
色彩的定义参数
L*= 100 white
L*= 50 grey
L*= 0 black
a*= - xx green
b*= + xx yellow
a*= + xx red b*= + xx blue
色差的定义公式
目录
01
色差的管理规范
02
色差的检测操作
观察标准三要素
c、
相同的标准光源-灯箱(D65和D50混合型)
相同的分光密度计-Xrite Exact 相同的测量位置(需标注)
b、记录标准灯管所使用的时间 所有标准的对色光源也是由灯管或灯炮所产生,而生产商也会列明其产 品在若干时间的运作内,其产品质量仍保持在可接受的公差内。 故此一个准确的时间记录器是不可缺少的。 通常这些灯管如果使用超过2000小时或一年,便需做出更换。
色差的颜色分析
当△L *<0,说明印刷样张的颜色比标准样张的颜色深,暗调部分图像易损失, 印刷时黑墨含量过高或油墨转移量不够。
若△a *>0、△b *>0,则说明印刷样张偏橙色,配墨时黄墨和品红墨含量过高或油 墨转移量过多;
若△a *>0、△b *<0,则说明印刷样张偏红,配墨时品红墨含量过高或油墨转移量 过多;
印刷标准上下限
同一产品的颜色标准和上下限样册 相同的颜色标准:Pantone PMS+色样册
色差管控标准

色差管控标准全文共四篇示例,供读者参考第一篇示例:色差管控标准是指在生产和加工过程中,为了确保产品的色彩一致性和质量稳定性,制定并执行的一系列措施和规范。
色差是指不同样品或产品之间在色彩方面的差异程度,色差管控标准的制定对于降低产品质量风险,提升生产效率,增强产品竞争力具有重要意义。
色差的出现可能源自原材料的差异、生产工艺的不足、设备的不稳定性等多方面因素,而严格的色差管控是防止这些因素带来色彩差异的有效手段。
在现代化生产加工中,色差管控标准已经成为企业保证产品色彩一致性、降低经营风险的基本要求。
色差管控标准的制定要根据具体产品的特性和生产工艺流程来确定,一般包括以下几个方面:确定色差的测量标准和方法。
对于不同产品来说,需要确定相应的色彩空间和色彩参数,以及使用何种色差仪器进行测量和检验。
明确色差的容忍度和界限。
必须根据产品的使用环境和需求,确定适宜的色差范围,确保在一定范围内的色差不会影响产品的质量和形象。
建立良好的色彩管理体系。
包括明确责任和权利、制定相应的SOP标准操作规范、配备合适的检测设备和人员等。
持续进行色差监控和改进。
通过定期监测产品的色差情况,及时发现问题并采取纠正措施,保证产品色彩的一致性和稳定性。
色差管控标准的实施有利于提高产品的质量稳定性和一致性,有效地降低产品的赔偿风险和投诉率。
对于消费者来说,也可以增加购买信心和满意度,提升品牌形象和市场竞争力。
色差管控标准的制定和执行是现代生产加工中的重要环节,对于提升企业产品质量、节约生产成本、提高客户满意度具有重要意义。
只有不断完善和执行色差管控标准,才能确保产品色彩的一致性和稳定性,提升企业的市场竞争力和可持续发展能力。
【色差管控标准】。
第二篇示例:色差是指在同一种颜色下,由于不同光源、不同材料或不同观察条件下所引起的颜色不一致现象。
在工业生产和质量控制中,色差一直是一个重要的指标,影响着产品的质量和外观。
对色差进行管控是十分必要的。
色差控制方法
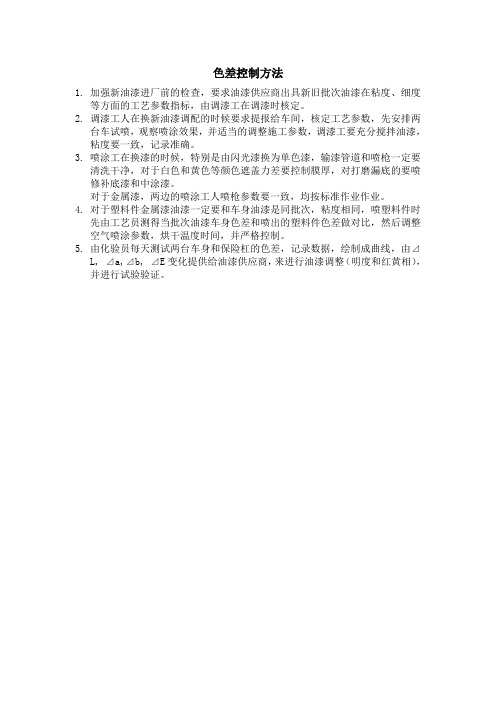
色差控制方法
1.加强新油漆进厂前的检查,要求油漆供应商出具新旧批次油漆在粘度、细度
等方面的工艺参数指标,由调漆工在调漆时核定。
2.调漆工人在换新油漆调配的时候要求提报给车间,核定工艺参数,先安排两
台车试喷,观察喷涂效果,并适当的调整施工参数,调漆工要充分搅拌油漆,粘度要一致,记录准确。
3.喷涂工在换漆的时候,特别是由闪光漆换为单色漆,输漆管道和喷枪一定要
清洗干净,对于白色和黄色等颜色遮盖力差要控制膜厚,对打磨漏底的要喷修补底漆和中涂漆。
对于金属漆,两边的喷涂工人喷枪参数要一致,均按标准作业作业。
4.对于塑料件金属漆油漆一定要和车身油漆是同批次,粘度相同,喷塑料件时
先由工艺员测得当批次油漆车身色差和喷出的塑料件色差做对比,然后调整空气喷涂参数,烘干温度时间,并严格控制。
5.由化验员每天测试两台车身和保险杠的色差,记录数据,绘制成曲线,由⊿
L, ⊿a,⊿b, ⊿E变化提供给油漆供应商,来进行油漆调整(明度和红黄相),并进行试验验证。
色差控制方案
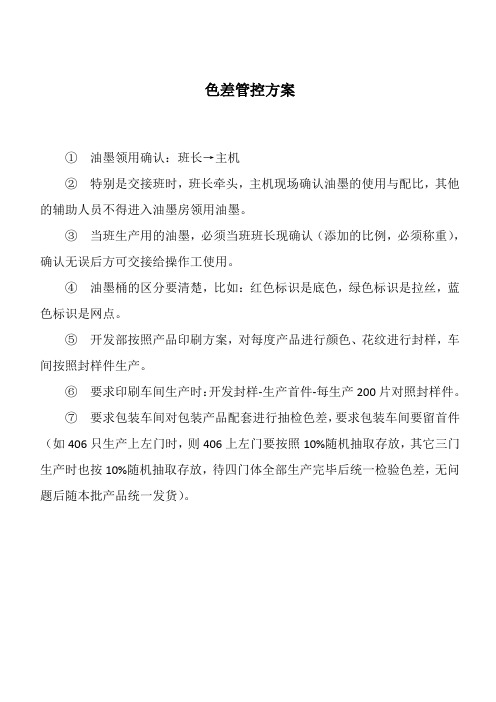
色差管控方案
①油墨领用确认:班长→主机
②特别是交接班时,班长牵头,主机现场确认油墨的使用与配比,其他的辅助人员不得进入油墨房领用油墨。
③当班生产用的油墨,必须当班班长现确认(添加的比例,必须称重),确认无误后方可交接给操作工使用。
④油墨桶的区分要清楚,比如:红色标识是底色,绿色标识是拉丝,蓝色标识是网点。
⑤开发部按照产品印刷方案,对每度产品进行颜色、花纹进行封样,车间按照封样件生产。
⑥要求印刷车间生产时:开发封样-生产首件-每生产200片对照封样件。
⑦要求包装车间对包装产品配套进行抽检色差,要求包装车间要留首件(如406只生产上左门时,则406上左门要按照10%随机抽取存放,其它三门生产时也按10%随机抽取存放,待四门体全部生产完毕后统一检验色差,无问题后随本批产品统一发货)。
- 1、下载文档前请自行甄别文档内容的完整性,平台不提供额外的编辑、内容补充、找答案等附加服务。
- 2、"仅部分预览"的文档,不可在线预览部分如存在完整性等问题,可反馈申请退款(可完整预览的文档不适用该条件!)。
- 3、如文档侵犯您的权益,请联系客服反馈,我们会尽快为您处理(人工客服工作时间:9:00-18:30)。
文件编码:GB080204.05版本:A
1、目的
规范生产过程产品色差控制流程,保证生产过程中产品颜色与标样一致。
2、范围
本程序适用于公司各生产工序。
3、定义
无
4、参考文件
无
5、职责
5.1品管部负责标样的签发。
5.2品管部IPQC负责过程生产中的监控。
5.3生产车间负责按照标准操作。
6、工作内容
6.1晒版
6.1.1晒版须根据作业指导书要求设置曝光时间、显影时间。
晒版标准为阳
图2%有点子,98%有轮廓,3%点子结实完整,97%的网点清晰透亮无灰雾。
6.1.2对于网点版,必须如实记录灯使用情况、爆光时间、药水情况,便于
下次生产时还原工艺参数,以保障每次晒出的网点版的一致性。
6.1.3各种色彩控制条齐全完整。
6.2机台开机签样与标样色差的控制
6.2.1公司所有生产的产品菲林必需有标准的颜色测控条。
6.2.2所有金银卡纸、镭射纸和珠光打底的产品(包括烟标和社会单)机台
在签样与生产时按以下要求操作。
6.2.2.1颜色要求:目测与标样一致,以标样为准取五点平均后设值,用
CRII5检测,△a≤1.5,△b≤1.5△E≤3.0,a,b值尽量与标样a,b值接近。
6.2.2.2取值要求:雪花油类在印刷
雪花油后直接测量,非雪花油类用蒙片蒙住后测量取值,有渐变网在渐变网为零和100%处分别取值。
纸张有阴阳面的在同一面取值。
6.2.2.3测量要求:雪花油类产品在印刷雪花油后直接测量,非雪花油类用蒙片蒙住后测量,有渐变网在渐变网为零和100%处分别测量
文件编码:GB080204.05版本:A
6.2.2.4蒙片要求:干净,统一,细哑光,与被检测色接触紧密。
6.2.2.5签样要求:目测与标样一致,△a≤1.5,△b≤1.5△E≤3.0,a,b值尽量与标样a,b值接近,横向密度D±0.03,D值尽量与标样一致。
6.2.2.6控制要求:目测与标样一致,△a≤1.5,△b≤1.5△E≤3.0,a,b值尽量与标样a,b值接近,横向密度D±0.03,D值尽量与标样一致,整批密度D ±0.05,白卡或铜版纸密度D±0.02.
6.2.3直接在白卡纸或铜版纸上面印刷的产品(包括烟标和社会单)机台在
签样和生产时,颜色以仪器检测△a≤1.0,△b≤1.0,深色△E≤1.3,浅色△E≤0.8,横向密度D±0.02,整批密度D±0.03.目测与标样一致。
6.2.4对于需覆膜产品必须经覆膜后看整体颜色与标样一致后。
按金银卡纸
或白卡纸或铜版纸印刷颜色控制要求控制。
6.2.5四色网点印刷产品的四色密度尽量在国家规定的标准范围内,即红:
1.35---1.45,黑1.7---1.8,黄1.25—1.35,蓝1.35—1.55。
每种产品的
四色密度标准由工艺技术标准部部纳入“产品工艺技术标准”。
6.2.6机台在签好开机样张后由机长用分光密度仪测出各个颜色的密度(批
次误差控制在±0.1以内);检测整个版面每种油墨是否开平,每种颜色的横向密度D±0.05,是否符合“产品工艺技术标准”的密度标准。
6.3生产过程中产品色差的控制
6.3.1机台在正式生产过程中不管是金银卡纸还是白卡纸或铜版纸每2500
张机长需检测颜色密度是否与签样一致、每2500张机台需检测颜色的L a b 值是否符合标准。
6.3.2机台必须将每板产品留样一张,(有雪花油的留雪花油样)在同一位
置剪一色块贴在自检互检表上,(金银卡纸还需留白卡样)0.由IPQC签字后交车间经理存档,以便机台、车间和IPQC对整批颜色进行监控。
6.3.2生产过程中停机后需至少放80张以上过版纸进行跑色。
保证停机后
开机生产的产品颜色一致。
6.3.3生产过程中每次停机后生产的前100张和生产过程中颜色波动异常且
超出标准上下限范围的。
机台单独做好标识,并在流程卡上注明,便于成品质检。
6.3.4品管部IPQC在机台生产过程中需按过程检验规定定时对产品进行抽
文件编码:GB080204.05版本:A
检,将检验结果数据记录在IPQC专检项目记录表上,并且需对机台生产的每板抽取一张和签样比较,检查颜色是否一致。
IPQC随时督导检查机台是否按照规定进行颜色密度和颜色L a b值的检测。
6.3.5生产过程中因纸张色差导致颜色不一致时,机台需及时通知IPQC和上报车间副经理进行解决,同时对所生产的产品进行分开标识。