机械加工精度与加工误差(
第三章机械加工精度(3.2)
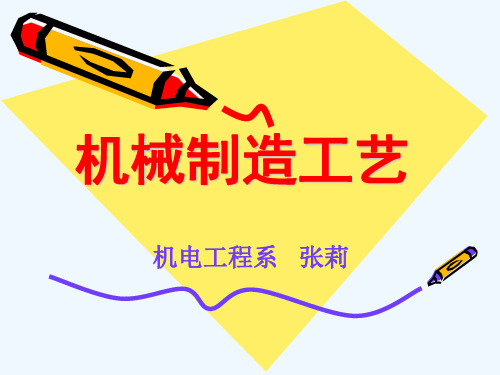
若齿轮Z1有转角误差δ1,造成Z2的转角误差为: δ12=i12δ1 传到丝杠上的转角误差为δ1n,即: Z1
Z2
δ1
δ2
δ1n=i1nδ1
δ2n=i2nδ2
………………
δn δnn=innδn
n
Zn
在任一时刻,各齿轮的转角误差反映到丝杠的总误差为:
i Σ 1 n 2 n nn j jn
学习目的
了解各种因素对加工精度的影响规律,找出提 高加工精度的途径,以保证零件的加工质量。
3. 2 工艺系统的几何误差
一、加工原理误差
加工原理误差是指由于采用了近似的加工方法、近似 的成形运动或近似的刀具轮廓而产生的误差。 例如滚齿用的齿轮滚刀,就有两种误差,一是为了制 造方便,采用阿基米德蜗杆代替渐开线基本蜗杆而产生的 刀刃齿廓近似造形误差;二是由于滚刀切削刃数有限,切 削是不连续的,因而滚切出的齿轮齿形不是光滑的渐开线, 而是折线,见图。 成形车刀、成形铣刀也采用了近似的刀具轮廓。
• 答:孔径没有误差,有圆柱度误差。轴线 不直。因为误差敏感方向不断变化。
讨 论
若镗杆进给,即镗杆既旋转又移动(图示), 导轨误差对加工精度有无影响?
答:不会产生孔的形状误差,但会产生孔的位 置误差。
讨
论
• 刨平面时,导轨误差对加工精度有何影 响? • 答:产生加工表面的直线度误差、平面 度误差。
主轴回转误差在实际中多表现为漂移。 漂移是指主轴回转轴线在每一转内的每一瞬时的变动 方位和变动量都是变化的一种现象。
Ⅰ理想回转轴线
Ⅱ实际回转轴线
2)影响主轴回转精度的主要因素
轴承本身误差
轴承间隙
轴承间同轴度误差 各段轴颈、轴孔的同轴度误差 主轴系统的刚度和热变形等 但它们对主轴回转精度的影响大小随加工方式而不同。
关于机械加工精度与加工误差的分析

关于机械加工精度与加工误差的分析笔者具体分析了加工精确度和加工误差等的基础内容。
以实践情况为例,具体的论述了误差产生的缘由,并且论述了降低误差现象发生几率的措施。
标签:加工精度;加工误差;减小误差引言在平时的工作中,我们不乏见到加工方面的内容,对精确性和误差等都不陌生。
不过真正深入了解的话,会发现其是一门非常深入的学科知识。
不管我们工作中如何努力,都无法将误差发生的几率降低为零,因此我们可以做的只能是通过合理的措施来切实的提升精确性,进而降低误差现象的发生几率。
1 加工精度与加工误差概述所谓的精确度,具体的说是零件在生产之后的具体的数值和设想数值之间符合程度。
不论是我们如何努力,都无法保证生产的零件和我们期待中的一模一样,都会存在各种各样的问题,我们将这种问题称为误差。
以工艺体系来看,它的组成部分有四个,分别是机床、刀具、工件以及夹具。
它们在工作的时候会生成很多不一样的误差,而此类误差在不一样的状态中会通过不一样的形式体现出来。
2 机械加工精度与加工误差的分析2.1 工艺系统集合误差2.1.1 机床的几何误差。
在工作中,刀具的的成形活动均是经由机床来实现的,所以,零件的加工精确性会对机床的精确性产生很大的干扰。
常见的机床生产方面的误差有如下的一些:主轴回转误差、导轨误差等。
如果机床磨损的话,就会导致它的精确性明显的变低。
(1)主轴回转误差。
主轴是机床非常关键的一个组成部分,它把力和运动传递给刀具等,一旦它出现了回转误差的话,就会导致零件的精确性受到很大的干扰。
所谓的回转误差,具体的说是主轴短时间的回转轴线比对于它的平均轴线来讲,出现的变动量。
常见的类型有三个,分别是径向圆跳动、轴向窜动和角度摆动。
导致它形成的原因有很多,比如轴承自身的问题,主轴的挠度等等。
不过它们对回转精确性的影响并不是完全一样的,会因为加工状态而产生变化。
产生轴向窜动的主要原因是主轴轴肩端面和轴承承载端面对主轴回转轴线有垂直度误差。
第四章 机械加工质量及其控制
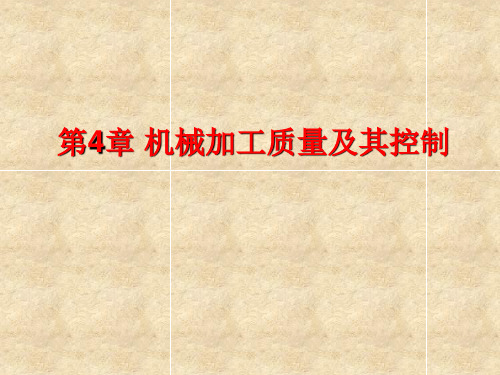
工艺系统刚度主要取决于薄弱环节的刚度。
2)机床刚度
y机床 y主轴 y刀架 y尾座
k主轴= k尾架= k刀架= Fp 2 y主轴 Fp 2 y尾架 Fp y刀架
机床的刚度取决于部件的刚度。
(2)工艺系统刚度对加工精度的影响
常见的几种工艺系统中其低刚度环节所在位置:
镗孔:工件进给孔为椭圆形。
避免措施
提高主轴及箱体的制造精度、选用高精度的轴承、提高主轴 部件的装配精度、对高速主轴部件进行平衡、对滚动轴承进 行预紧等,均可提高机床主轴的回转精度。
2)导轨误差
(a) 在水平面 内的直线度误 差 误差敏感方向
(b) 在垂直平面 内的直线度
ΔR ≈Δ22/D 设Δ2=
工艺系统的刚度在不同的加工位置上是各不相同的,当主轴箱 刚度与尾座刚度相等时,工艺系统刚度在工件全长上的差别最 小,工件在轴截面内几何形状误差最小。
在车床上加工短而粗的光轴(工件刚度相对于机床刚度大 得多),已知径向切削分力
Fp
=1000N,主轴刚度
k主轴
=100000N/mm,尾座刚度
k尾座
=50000N/mm,
正确地选用刀具材料和选用新型耐磨的刀具材料,合理地选 用刀具几何参数和切削用量,正确地刃磨刀具,正确地采用冷 却润滑液等,均可有效地减少刀具的尺寸磨损。必要时还可采 用补偿装置对刀具尺寸磨损进行自动补偿。
10000.054 mm, 加工一合金钢管,其外径为
工件长度
l =2100mm,圆柱度公差在全长范围内
c)采用合理的装夹方式和加工方式
2)减小切削力及其变化 合理地选择刀具材料、 增大前角和主偏角、对 工件材料进行合理的热 处理以改善材料的加工 性能等,都可使切削力 减小。
机械加工精度的影响因素及其控制措施

浅析机械加工精度的影响因素及其控制措施摘要:如何提高机械零件的加工精度,是每个从事机械加工者在加工前必须考虑的问题,文章现对影响机械加工精度的因素进行了较全面的分析,并针对各种影响因素阐述了相应的控制措施。
关键词:加工精度;因素;措施1 机械加工精度和加工误差1.1 加工精度零件加工后的实际几何参数(尺寸、形状和位置)与理想几何参数相符合的程度。
符合程度越高则加工精度就越高。
加工精度包括尺寸精度、形状精度和位置精度。
1.2 加工误差零件加工后的实际几何参数对理想几何参数的偏离程度称为加工误差。
加工误差的大小表示了加工精度的高低,加工误差是加工精度的度量。
在实际生产中,加工精度的高低是以加工误差的大小来衡量的。
2 加工精度的影响因素零件加工的误差是由于工件与刀具在切削过程中相互位置发生变动而造成。
加工误差包括加工原理误差、机床几何误差、夹具误差、刀具制造误差、工艺系统受力变形、工艺系统热变形、刀具磨损、残余应力引起变形、测量误差等。
2.1 加工原理误差加工原理误差是指由于采用了近似的加工方法、近似的成形运动或近似的刀具轮廓而产生的误差。
例如滚齿用的齿轮滚刀,就有两种误差,一是为了制造方便,采用阿基米德蜗杆代替渐开线基本蜗杆而产生的刀刃齿廓近似造形误差;二是由于滚刀切削刃数有限,切削是不连续的,因而滚切出的齿轮齿形不是光滑的渐开线,而是折线。
2.2 机床几何误差机床几何误差的来源主要指机床制造、磨损或安装带来的误差。
机床几何误差主要有:(1)主轴回转误差:即主轴回转时实际回转轴线与理想回转轴线的偏移量。
包括轴向窜动、径向跳动、角度摆动三种基本形式。
主轴的轴向窜动对内、外圆的加工精度没有影响,但加工端面时,会使加工的端面与内外圆轴线产生垂直度误差。
主轴每转一周,要沿轴向窜动一次,使得切出的端面产生平面度误差。
当加工螺纹时,会产生螺距误差。
主轴的纯径向跳动会使镗削加工时镗出的孔为椭圆形。
主轴角度摆动会造成车削外圆或内孔的锥度误差;在镗孔时,若工件进给会使镗出的孔为椭圆形。
加工精度概述及加工原理误差和调整误差
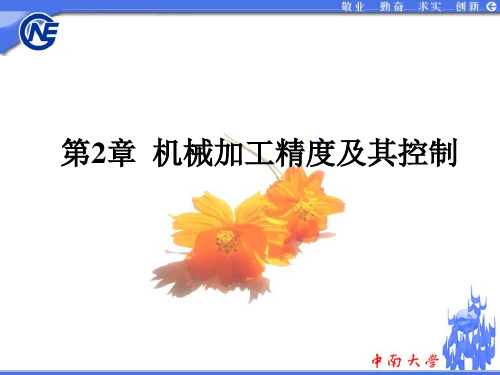
2.1 概述 2.1.1 机械加工精度 零件加工后的实际几何参数(尺寸、形状和表面的相互位置)与理 想零件的几何参数相符合的程度。 机械加工误差:零件加工后的实际几何参数(尺寸、形状和表面间的 相互位置)与理想零件的几何参数相偏离的程度。 包含3方面:尺寸精度、形状精度和位置精度。 联系:一般形状公差应限制在位置公差之内,而位置公差一般也应 限制在尺寸公差之内。
2.2.2 调整误差
由于调整不准确而产生的误差。工艺系统的调整有两种基本方式(M-2), 不同的调整方式有不同的误差来源。 1.试切法调整 试切法加工中,经过反复地试切、测量、调整,直至符合规定的尺寸要 求才正式切削整个待加工表面。这时引起调整误差的因素有以下3方面: (1)测量误差 指量具本身的精度、测量方法或使用条件下的误差(如 温度影响、操作者的细心程度)等;
(5)测量误差、工件毛坯内应力而引起的加工误差„ „
加工过程中可能出现的种种原始误差归纳如下:
图2 加工过程中的原始误差
2.1.3 误差的敏感方向 对加工精度影响最大的那个方向(即通过切削刃的加工表面的法向)
如图3,车削时工件的回转轴心是O,刀 尖正确位置在A,设某一瞬时由于各种原始 误差的影响,使刀尖位移到A′,则: 原始误差: δ =AA’
机械加工时,工艺系统的误差称为原始误差(“因”,根源),加 工误差是“果”,是表现。提高和保证加工精度的问题就是控制和减小 原始误差的问题。
2.1.2 影响始误差
上工序存在以下一些原始误差: (1)工件的装夹误差:包括定位误差和夹紧误差; (2)调整误差:包括夹具和定位菱形销的位置调整误差、对刀调整误差; (3)机床、刀具、夹具的制造误差; (4)工艺系统动误差:包括切削力、切削热、磨擦引起的工艺系统的变形和 磨损;
机械加工精度的概念
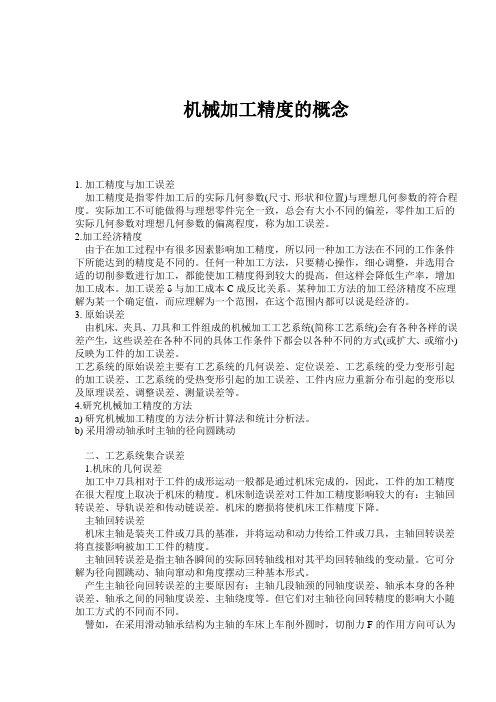
机械加工精度的概念1. 加工精度与加工误差加工精度是指零件加工后的实际几何参数(尺寸、形状和位置)与理想几何参数的符合程度。
实际加工不可能做得与理想零件完全一致,总会有大小不同的偏差,零件加工后的实际几何参数对理想几何参数的偏离程度,称为加工误差。
2.加工经济精度由于在加工过程中有很多因素影响加工精度,所以同一种加工方法在不同的工作条件下所能达到的精度是不同的。
任何一种加工方法,只要精心操作,细心调整,并选用合适的切削参数进行加工,都能使加工精度得到较大的提高,但这样会降低生产率,增加加工成本。
加工误差δ与加工成本C成反比关系。
某种加工方法的加工经济精度不应理解为某一个确定值,而应理解为一个范围,在这个范围内都可以说是经济的。
3. 原始误差由机床、夹具、刀具和工件组成的机械加工工艺系统(简称工艺系统)会有各种各样的误差产生,这些误差在各种不同的具体工作条件下都会以各种不同的方式(或扩大、或缩小)反映为工件的加工误差。
工艺系统的原始误差主要有工艺系统的几何误差、定位误差、工艺系统的受力变形引起的加工误差、工艺系统的受热变形引起的加工误差、工件内应力重新分布引起的变形以及原理误差、调整误差、测量误差等。
4.研究机械加工精度的方法a) 研究机械加工精度的方法分析计算法和统计分析法。
b) 采用滑动轴承时主轴的径向圆跳动二、工艺系统集合误差1.机床的几何误差加工中刀具相对于工件的成形运动一般都是通过机床完成的,因此,工件的加工精度在很大程度上取决于机床的精度。
机床制造误差对工件加工精度影响较大的有:主轴回转误差、导轨误差和传动链误差。
机床的磨损将使机床工作精度下降。
主轴回转误差机床主轴是装夹工件或刀具的基准,并将运动和动力传给工件或刀具,主轴回转误差将直接影响被加工工件的精度。
主轴回转误差是指主轴各瞬间的实际回转轴线相对其平均回转轴线的变动量。
它可分解为径向圆跳动、轴向窜动和角度摆动三种基本形式。
产生主轴径向回转误差的主要原因有:主轴几段轴颈的同轴度误差、轴承本身的各种误差、轴承之间的同轴度误差、主轴绕度等。
机械加工精度与加工误差
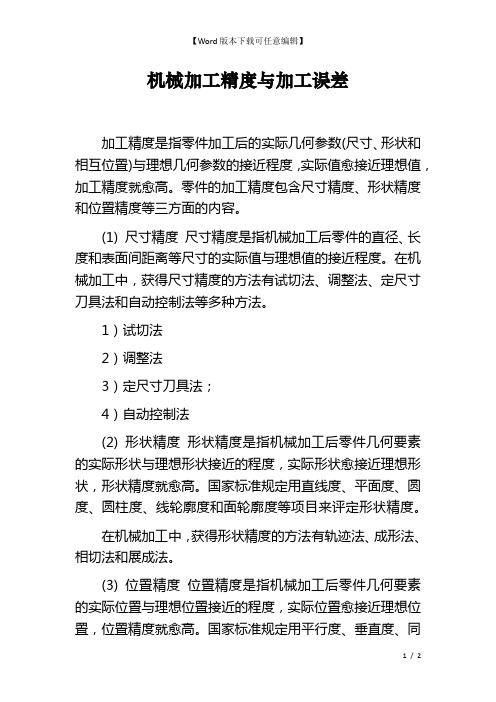
机械加工精度与加工误差加工精度是指零件加工后的实际几何参数(尺寸、形状和相互位置)与理想几何参数的接近程度,实际值愈接近理想值,加工精度就愈高。
零件的加工精度包含尺寸精度、形状精度和位置精度等三方面的内容。
(1) 尺寸精度尺寸精度是指机械加工后零件的直径、长度和表面间距离等尺寸的实际值与理想值的接近程度。
在机械加工中,获得尺寸精度的方法有试切法、调整法、定尺寸刀具法和自动控制法等多种方法。
1)试切法2)调整法3)定尺寸刀具法;4)自动控制法(2) 形状精度形状精度是指机械加工后零件几何要素的实际形状与理想形状接近的程度,实际形状愈接近理想形状,形状精度就愈高。
国家标准规定用直线度、平面度、圆度、圆柱度、线轮廓度和面轮廓度等项目来评定形状精度。
在机械加工中,获得形状精度的方法有轨迹法、成形法、相切法和展成法。
(3) 位置精度位置精度是指机械加工后零件几何要素的实际位置与理想位置接近的程度,实际位置愈接近理想位置,位置精度就愈高。
国家标准规定用平行度、垂直度、同轴度、对称度、位置度、圆跳动和全跳动等项目来评定位置精度。
在机械加工中,获得位置精度的方法有直接找正法、划线找正法和夹具装夹法。
加工过程中有很多因素影响加工精度,实际加工不可能把零件做得与理想零件完全一致;零件加工后的实际几何参数(尺寸、形状和相互位置)对理想几何参数的偏离量称为加工误差。
加工过程中有很多因素影响零件的加工精度,即使是同一种加工方法只要工作条件稍有变化它们所能到达的加工精度也不一样。
例如,采用较高精度的设备,适当选用切削用量,精心完成加工过程中的每一个操作,就能得到较高的加工精度,但这会增加加工成本。
加工经济精度是指在正常生产条件下(采用符合质量标准的设备、工艺装备和标准技术等级的工人,不延长加工时间)所能保证的加工精度。
机械制造技术基础 第五章 机械加工精度 课后答案

1.什么是加工精度和加工误差?两者含义有何异同?加工精度都包括哪些方面?答:加工精度是指零件加工后的实际几何参数与理想零件的几何参数相符合的程度。
加工误差是指零件加工后的实际几何参数与理想零件的几何参数偏离程度。
它们都是和理想零件的比较结果,但加工精度考虑是符合程度,而加工误差考虑的是偏离程度。
加工精度包括尺寸精度、形状精度、位置精度。
2.获得零件尺寸精度、形状精度和位置精度的方法有哪些?答:获得零件尺寸精度的方法(1)试切法。
(2)调整法。
(3)定尺寸精度法。
(4)自动控制法。
获得形状精度的方法(1)轨迹法。
(2)成形法。
(3)展成法。
获得位置精度的方法(1)多次装夹加工时,依靠夹具的正确定位。
(2)工件一次装夹多个表面时,依靠机床的精度来保证。
3.影响加工精度的因素有哪些?答:1)原理误差。
2)安装误差。
3)测量误差和调整误差。
4)机床、夹具、刀具的制造精度和磨损。
5)机床、夹具、刀具、工件的受力变形。
6)机床、刀具、工件的受热变形。
4.何谓“原理误差”?它对零件加工的精度有何影响?答:原理误差是因利用近似加工原理或近似的刀具切削刃形状而产生的误差。
5.什么是主轴回转精度?其对加工精度有哪些影响?6.普通车床主轴前端锥孔或三爪卡盘夹爪的定心表面,出现过大的径向跳动时,常在刀架上安装内圆磨头进行自磨自的修磨加工,修磨后的定心表面,其径向跳动量确实大为减小,试问:(1)修磨后是否提高了主轴回转精度?为什么?(2)在机床主轴存在几何偏心的情况下,以精车过的轴套工件的外圈定位来精车轴套内孔时,会产生怎样的加工误差?7.提高机床主轴回转精度有哪些途径?在实际生产中转移主轴回转误差常用的工艺方法有哪些?8.何谓误差敏感方向?试举例说明导轨误差在不同机床上的误差敏感方向?9.。
- 1、下载文档前请自行甄别文档内容的完整性,平台不提供额外的编辑、内容补充、找答案等附加服务。
- 2、"仅部分预览"的文档,不可在线预览部分如存在完整性等问题,可反馈申请退款(可完整预览的文档不适用该条件!)。
- 3、如文档侵犯您的权益,请联系客服反馈,我们会尽快为您处理(人工客服工作时间:9:00-18:30)。
第七章机械加工精度本章主要介绍以下内容:1.机械加工精度的基本概念2.影响机械加工精度的因素3.加工误差的统计分析4.提高加工精度的途径课时分配:1、4,各0.5学时,2、 3,各1.5学时重点:影响机械加工精度的因素难点:加工误差的统计分析随着机器速度、负载的增高以及自动化生产的需要,对机器性能的要求也不断提高,因此保证机器零件具有更高的加工精度也越显得重要。
我们在实际生产中经常遇到和需要解决的工艺问题,多数也是加工精度问题。
研究机械加工精度的目的是研究加工系统中各种误差的物理实质,掌握其变化的基本规律,分析工艺系统中各种误差与加工精度之间的关系,寻求提高加工精度的途径,以保征零件的机械加工质量,机械加工精度是本课程的核心内容之一。
本章讨论的内容有机械加工精度的基本概念、影响加工精度的因素、加工误差的综合分析及提高加工精度的途径四个方面。
7.1机械加工精度概述一、加工精度与加工误差(见P194)1、加工精度是指零件加工后的实际几何参数(尺寸、形状和位置)与理想几何参数的符合程度。
符合程度越高,加工精度越高。
一般机械加工精度是在零件工作图上给定的,其包括:1)零件的尺寸精度:加工后零件的实际尺寸与零件理想尺寸相符的程度。
2)零件的形状精度:加工后零件的实际形状与零件理想形状相符的程度。
3)零件的位置精度:加工后零件的实际位置与零件理想位置相符的程度。
2、获得加工精度的方法:1)试切法:即试切--测量--再试切--直至测量结果达到图纸给定要求的方法。
2)定尺寸刀具法:用刀具的相应尺寸来保证加工表面的尺寸。
3)调整法:按零件规定的尺寸预先调整好刀具与工件的相对位置来保证加工表面尺寸的方法。
3、加工误差:实际加工不可能做得与理想零件完全一致,总会有大小不同的偏差,零件加工后的实际几何参数对理想几何参数的偏离程度,称为加工误差。
加工误差的大小表示了加工精度的高低。
生产实际中用控制加工误差的方法来保证加工精度。
4、误差的敏感方向:加工误差对加工精度影响最大的方向,为误差的敏感方向。
例如:车削外圆柱面,加工误差敏感方向为外圆的直径方向。
(见P195图7.2)二、加工经济精度由于在加工过程中有很多因素影响加工精度,所以同一种加工方法在不同的工作条件下所能达到的精度是不同的。
任何一种加工方法,只要精心操作,细心调整,并选用合适的切削参数进行加工,都能使加工精度得到较大的提高,但这样会降低生产率,增加加工成本。
加工误差δ与加工成本C成反比关系。
某种加工方法的加工经济精度不应理解为某一个确定值,而应理解为一个范围,在这个范围内都可以说是经济的。
三、研究机械加工精度的方法—因素分析法和统计分析法。
(见P194)因素分析法:通过分析、计算或实验、测试等方法,研究某一确定因素对加工精度的影响。
一般不考虑其它因素的同时作用,主要是分析各项误差单独的变化规律;统计分析法:运用数理统计方法对生产中一批工件的实测结果进行数据处理,用以控制工艺过程的正常进行。
主要是研究各项误差综合的变化规律,只适合于大批、大量的生产条件。
四、原始误差由机床、夹具、刀具和工件组成的机械加工工艺系统(简称工艺系统)会有各种各样的误差产生,这些误差在各种不同的具体工作条件下都会以各种不同的方式(或扩大、或缩小)反映为工件的加工误差。
工艺系统中凡是能直接引起加工误差的因素都称为原始误差。
工艺系统的原始误差主要有:1、加工前的误差(原理误差、调整误差、工艺系统的几何误差、定位误差)2、加工过程中的误差(工艺系统的受力变形引起的加工误差、工艺系统的受热变形引起的加工误差)3、加工后的误差(工件内应力重新分布引起的变形以及、测量误差)等。
7.2影响加工误差的因素(一)加工原理误差:定义:由于采用近似的加工运动或近似的刀具轮廓所产生的加工误差,为加工原理误差。
(1)采用近似的刀具轮廓形状:例如:模数铣刀铣齿轮。
(2)采用近似的加工运动:例如:车削蜗杆时,由于蜗杆螺距Pg=πm,而π=3.1415926…,是无理数,所以螺距值只能用近似值代替。
因而,刀具与工件之间的螺旋轨迹是近似的加工运动。
(二)机床调整误差:机床调整:是指使刀具的切削刃与定位基准保持正确位置的过程。
(1)进给机构的调整误差:主要指进刀位置误差;(2)定位元件的位置误差:使工件与机床之间的位置不正确,而产生误差;(3)模板(或样板)的制造误差:使对刀不准确。
(三)装夹误差:定义:工件在装夹过程中产生的误差,为装夹误差。
装夹误差包括定位误差和夹紧误差。
定位误差是指一批工件采用调整法加工时因定位不正确而引起的尺寸或位置的最大变动量。
定位误差由基准不重合误差和定位副制造不准确误差造成。
1、基准不重合误差在零件图上用来确定某一表面尺寸、位置所依据的基准称为设计基准。
在工序图上用来确定本工序被加工表面加工后的尺寸、位置所依据的基准称为工序基准。
一般情况下,工序基准应与设计基准重合。
在机床上对工件进行加工时,须选择工件上若干几何要素作为加工(或测量)时的定位基准(或测量基准),如果所选用的定位基准(或测量基准)与设计基准不重合,就会产生基准不重合误差。
基准不重合误差等于定位基准相对于设计基准在工序尺寸方向上的最大变动量。
基准不重合误差分析示例图示零件,设e面已加工好,今在铣床上用调整法加工f面和g面。
在加工f面时若选e面为定位基准,则f面的设计基准和定位基准都是e面,基准重合,没有基准不重合误差,尺寸A的制造公差为T A。
加工g面时,定位基准有两种不同的选择技术方案,一种技术方案(技术方案Ⅰ)加工时选用f面作为定位基准,定位基准与设计基准重合,没有基准不重合误差,尺寸B的制造公差为T B;但这种定位方式的夹具结构复杂,夹紧力的作用方向与铣削力方向相反,不够合理,操作也不方便。
另一种技术方案(技术方案Ⅱ)是选用e面作为定位基准来加工g面,此时,工序尺寸C是直接得到的,尺寸B是间接得到的,由于定位基准e与设计基准f不重合而给g面加工带来的基准不重合误差等于设计基准f面相对于定位基准e面在尺寸B方向上的最大变动量T A。
定位基准与设计基准不重合时所产生的基准不重合误差,只有在采用调整法加工时才会产生,在试切法加工中不会产生。
2、定位副制造不准确误差工件在夹具中的正确位置是由夹具上的定位元件来确定的。
夹具上的定位元件不可能按基本尺寸制造得绝对准确,它们的实际尺寸(或位置)都允许在分别规定的公差范围内变动。
同时,工件上的定位基准面也会有制造误差。
工件定位面与夹具定位元件共同构成定位副,由于定位副制造得不准确和定位副间的配合间隙引起的工件最大位置变动量,称为定位副制造不准确误差。
如图所示工件的孔装夹在水平放置的心轴上铣削平面,要求保证尺寸h,由于定位基准与设计基准重合,故无基准不重合误差;但由于工件的定位基面(内孔D)和夹具定位元件(心轴d1)皆有制造误差,如果心轴制造得刚好为d1min,而工件得内孔刚好为D max(如图示),当工件在水平放置得心轴上定位时,工件内孔与心轴在P点接触,工件实际内孔中心的最大下移量△ab=(D max-d1min)/2,△ab就是定位副制造不准确而引起的误差。
基准不重合误差的方向和定位副制造不准确误差的方向可能不相同,定位误差取为基准不重合误差和定位副制造不准确误差的矢量和。
(四)工艺系统集合误差1、机床的几何误差加工中刀具相对于工件的成形运动一般都是通过机床完成的,因此,工件的加工精度在很大程度上取决于机床的精度。
机床制造误差对工件加工精度影响较大的有:主轴回转误差、导轨误差和传动链误差。
机床的磨损将使机床工作精度下降。
1)主轴回转误差(见P196)机床主轴是装夹工件或刀具的基准,并将运动和动力传给工件或刀具,主轴回转误差将直接影响被加工工件的精度。
主轴回转误差是指主轴各瞬间的实际回转轴线相对其平均回转轴线的变动量。
它可分解为径向圆跳动、轴向窜动和角度摆动三种基本形式。
产生主轴径向回转误差的主要原因有:主轴几段轴颈的同轴度误差、轴承本身的各种误差、轴承之间的同轴度误差、主轴绕度等。
但它们对主轴径向回转精度的影响大小随加工方式的不同而不同。
采用滑动轴承时主轴的径向圆跳动譬如,在采用滑动轴承结构为主轴的车床上车削外圆时,切削力F的作用方向可认为大体上时不变的,见上图,在切削力F的作用下,主轴颈以不同的部位和轴承内径的某一固定部位相接触,此时主轴颈的圆度误差对主轴径向回转精度影响较大,而轴承内径的圆度误差对主轴径向回转精度的影响则不大;在镗床上镗孔时,由于切削力F的作用方向随着主轴的回转而回转,在切削力F的作用下,主轴总是以其轴颈某一固定部位与轴承内表面的不同部位接触,因此,轴承内表面的圆度误差对主轴径向回转精度影响较大,而主轴颈圆度误差的影响则不大。
图中的δd表示径向跳动量。
产生轴向窜动的主要原因是主轴轴肩端面和轴承承载端面对主轴回转轴线有垂直度误差。
不同的加工方法,主轴回转误差所引起的的加工误差也不同。
主轴回转误差产生的加工误差见P197表7.1。
1)径向跳动:影响工件圆度; 2)轴向窜动:影响轴向尺寸,加工螺纹时影响螺距值; 3)角度摆动:影响圆柱度;提高主轴回转精度的措施:主要是要消除轴承的间隙。
适当提高主轴及箱体的制造精度,选用高精度的轴承,提高主轴部件的装配精度,对高速主轴部件进行平衡,对滚动轴承进行预紧等,均可提高机床主轴的回转精度。
2)导轨误差(见P197)导轨是机床上确定各机床部件相对位置关系的基准,也是机床运动的基准。
车床导轨的精度要求主要有以下三个方面:在水平面内的直线度;在垂直面内的直线度;前后导轨的平行度(扭曲)。
a)导轨在水平面内的直线度误差:卧式车床导轨在水平面内的直线度误差△1将直接反映在被加工工件表面的法线方向(加工误差的敏感方向)上,对加工精度的影响最大。
b)导轨在垂直平面内的直线度误差:卧式车床导轨在垂直面内的直线度误差△2可引起被加工工件的形状误差和尺寸误差。
但△2对加工精度的影响要比△1小得多。
由上图2可知若因△2而使刀尖由a下降至b,不难推得工件半径R的变化量。
c)前后导轨存在平行度误差(扭曲)时,刀架运动时会产生摆动,刀尖的运动轨迹是一条空间曲线,使工件产生形状误差。
由右图可见,当前后导轨有了扭曲误差△3之后,由几何关系可求得△y≈(H/B)△3。
一般车床的H/B≈2/3,外圆磨床的H/B≈1,车床和外圆磨床前后导轨的平行度误差对加工精度的影响很大。
d)导轨与主轴回转轴线的平行度误差:若车床与主轴回转轴线在水平面内有平行度误差,车出的内外圆柱面就产生锥度;若车床与主轴回转轴线在垂直面内有平行度误差,则圆柱面成双曲回转体。
因是非误差敏感方向,故可略。
(见P198)除了导轨本身的制造误差外,导轨的不均匀磨损和安装质量,也使造成导轨误差的重要因素。