陶瓷材料热压烧结
纳米batio3陶瓷的超高压烧结
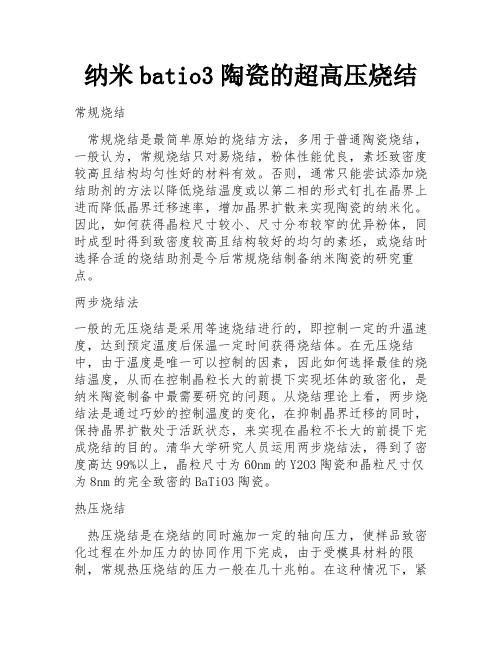
纳米batio3陶瓷的超高压烧结常规烧结常规烧结是最简单原始的烧结方法,多用于普通陶瓷烧结,一般认为,常规烧结只对易烧结,粉体性能优良,素坯致密度较高且结构均匀性好的材料有效。
否则,通常只能尝试添加烧结助剂的方法以降低烧结温度或以第二相的形式钉扎在晶界上进而降低晶界迁移速率,增加晶界扩散来实现陶瓷的纳米化。
因此,如何获得晶粒尺寸较小、尺寸分布较窄的优异粉体,同时成型时得到致密度较高且结构较好的均匀的素坯,或烧结时选择合适的烧结助剂是今后常规烧结制备纳米陶瓷的研究重点。
两步烧结法一般的无压烧结是采用等速烧结进行的,即控制一定的升温速度,达到预定温度后保温一定时间获得烧结体。
在无压烧结中,由于温度是唯一可以控制的因素,因此如何选择最佳的烧结温度,从而在控制晶粒长大的前提下实现坯体的致密化,是纳米陶瓷制备中最需要研究的问题。
从烧结理论上看,两步烧结法是通过巧妙的控制温度的变化,在抑制晶界迁移的同时,保持晶界扩散处于活跃状态,来实现在晶粒不长大的前提下完成烧结的目的。
清华大学研究人员运用两步烧结法,得到了密度高达99%以上,晶粒尺寸为60nm的Y2O3陶瓷和晶粒尺寸仅为8nm的完全致密的BaTiO3陶瓷。
热压烧结热压烧结是在烧结的同时施加一定的轴向压力,使样品致密化过程在外加压力的协同作用下完成,由于受模具材料的限制,常规热压烧结的压力一般在几十兆帕。
在这种情况下,紧紧靠压力的作用还是很难获得纳米陶瓷,通常还需要第二相辅助或其它因素共同作用。
在不考虑塑性变形和蠕变的情况下,轴向压力越大,素坯致密度越高,热压过程中的致密化速率越大,所以纳米陶瓷的热压烧结往往需要很高的压力。
高压力作用使得纳米陶瓷的烧结温度比微米陶瓷低几百度,这对抑制晶粒粗化有很好的效果,这种烧结方式也被称为是超高压烧结。
超高压烧结的特点是不仅能够迅速达到高密度,而且使晶体结构甚至原子、电子状态发生变化,从而材料具有在通常烧结下不能达到的性能。
热压烧结法制造陶瓷技术
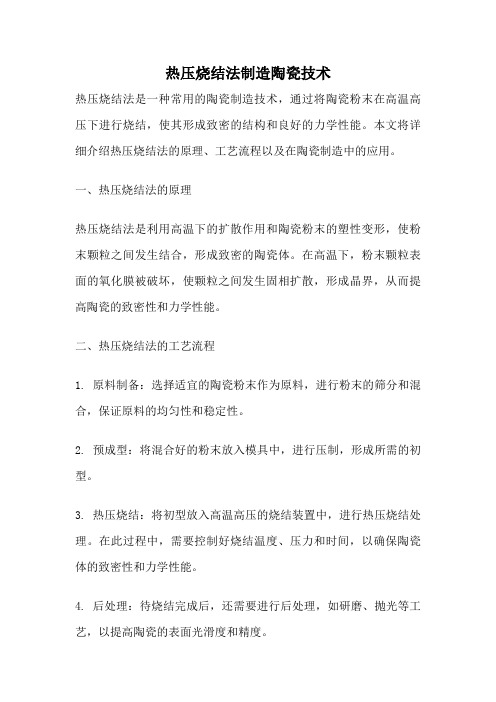
热压烧结法制造陶瓷技术热压烧结法是一种常用的陶瓷制造技术,通过将陶瓷粉末在高温高压下进行烧结,使其形成致密的结构和良好的力学性能。
本文将详细介绍热压烧结法的原理、工艺流程以及在陶瓷制造中的应用。
一、热压烧结法的原理热压烧结法是利用高温下的扩散作用和陶瓷粉末的塑性变形,使粉末颗粒之间发生结合,形成致密的陶瓷体。
在高温下,粉末颗粒表面的氧化膜被破坏,使颗粒之间发生固相扩散,形成晶界,从而提高陶瓷的致密性和力学性能。
二、热压烧结法的工艺流程1. 原料制备:选择适宜的陶瓷粉末作为原料,进行粉末的筛分和混合,保证原料的均匀性和稳定性。
2. 预成型:将混合好的粉末放入模具中,进行压制,形成所需的初型。
3. 热压烧结:将初型放入高温高压的烧结装置中,进行热压烧结处理。
在此过程中,需要控制好烧结温度、压力和时间,以确保陶瓷体的致密性和力学性能。
4. 后处理:待烧结完成后,还需要进行后处理,如研磨、抛光等工艺,以提高陶瓷的表面光滑度和精度。
三、热压烧结法在陶瓷制造中的应用热压烧结法广泛应用于陶瓷制造的各个领域,如电子陶瓷、结构陶瓷、功能陶瓷等。
1. 电子陶瓷:热压烧结法可以制备出具有良好电气性能的陶瓷材料,用于电子元器件的制造,如电容器、压电器件等。
2. 结构陶瓷:热压烧结法可以制备出高硬度、高强度的陶瓷材料,用于制造刀具、轴承等机械零件,具有良好的耐磨性和耐腐蚀性。
3. 功能陶瓷:热压烧结法可以制备出具有特殊功能的陶瓷材料,如氧化铝陶瓷用于高温热障涂层,氧化锆陶瓷用于人工关节等医疗器械。
四、热压烧结法的优势和不足热压烧结法具有以下优势:1. 可以制备出高密度的陶瓷材料,具有良好的力学性能和耐磨性。
2. 工艺稳定,可重复性好,能够生产大批量的陶瓷制品。
3. 可以制备出复杂形状的陶瓷制品,满足不同应用的需求。
然而,热压烧结法也存在一些不足之处:1. 设备成本较高,需要较大的投资。
2. 对原料的要求较高,需要选择适合的粉末和添加剂。
陶瓷烧结PPT课件

未来研究方向与展望
新材料与新工艺的开发
跨学科合作与技术融合
智能化与数字化技术的 应用
未来,研究者们将继续探索新型陶瓷 材料,研究新的烧结工艺和技术,以 满足各种应用需求。同时,如何实现 陶瓷材料的绿色生产和降低成本也是 未来的重要研究方向。
陶瓷烧结技术涉及到材料科学、物理 学、化学等多个学科领域,未来的研 究将更加注重跨学科的合作和技术融 合,以推动陶瓷材料的发展和应用。
还原气氛
可以还原杂质,提高陶瓷的纯度。
压力的影响
常压烧结
是最常见的烧结方式,适用于大多数 陶瓷材料。
加压烧结
在加压条件下,可以促进陶瓷的致密 化,提高其性能。
05
陶瓷烧结的质量控制与检测
质量控制方法
原料质量控制
对原料的化学成分、粒度、含水 率等指标进行严格检测和控制,
确保原料质量稳定。
工艺参数控制
在烧结过程中,对温度、压力、气 氛等工艺参数进行精确控制,以获 得最佳的烧结效果。
设备维护与校准
定期对烧结设备进行维护和校准, 确保设备运行稳定,提高产品的重 复性和可靠性。
性能检测与评价
物理性能检测
检测产品的密度、气孔率、热膨 胀系数等物理性能指标,确保产
品性能符合要求。
力学性能检测
通过抗弯强度、抗压强度等力学 性能试验,评估产品的机械性能
和可靠性。
耐腐蚀性能检测
对产品的耐酸、耐碱、耐热等性 能进行检测,以适应不同环境下
的使用要求。
缺陷分析与改进
缺陷识别
通过外观检查、无损检测等方法,识别产品中的 缺陷和问题。
原因分析
对缺陷产生的原因进行深入分析,找出根本原因 并制定相应的改进措施。
陶瓷材料工艺学--第五章 陶瓷材料的烧结

a. 影响铁和钛的价态; b. 使SiO2和CO还原; c. 形成氮化合物。
结论:气氛的影响有好有坏,关键是看坯体的组成。
(4)升温与降温速度对产品性能的影响
75%Al2O3瓷的升温速率与性能的关系曲线 1―抗折强度;2―温度系数;3―介质损耗角
(4)升温与降温速度对产品性能的影响
全部组元都转变为液相,而烧结是在低于主要组分的熔点下进
行的。
这两个过程均在低于材料熔点或熔融温
度之下进行的。并且在过程的自始至终都至少有一相是固态。
固相烧结一般可分为三个阶段:初始阶段,主要表现为颗粒形状 改变;中间阶段,主要表现为气孔形状改变;最终阶段,主要表现为 气孔尺寸减小。
烧结过程
收缩
降温速率对坯体的白度和性能都有影响。特别是 含玻璃相多的陶瓷,应采取高温快冷和低温慢冷的制 度。
高温快冷可避免泛黄、釉面析晶,提高光泽;低 温慢冷可减少应力,避免开裂等。
影响陶瓷材料烧结的工艺参数:
(1)烧成温度 (2)保温时间 (3)烧成气氛 (4)升温与降温速率
本节小结
1、 烧结的定义和烧结的方法 2、 烧结的类型
接触部位 颈部 颈部 颈部 颈部 颈部 颈部 颈部
相关参数 晶格扩散率,Dl 晶界扩散率,Db
粘度,η 表面扩散率,Ds 晶格扩散率,Dl 蒸汽压差,Δp 气相扩散率,Dg
5.3.2 晶粒过渡生长现象
晶粒的异常长大是指在长大速度较慢的细晶基体内有少部分区域快 速长大形成粗大晶粒的现象。
在烧结过程中发生异常长大与以下主要因素有关: ① 材料中含有杂质或者第二相夹杂物 ② 材料中存在高的各向异性的界面能,例如固/液界面
三、气孔排除
陶瓷烧结方法
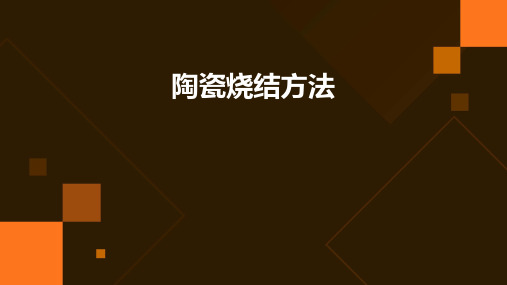
马弗炉是一种传统的陶瓷烧成设备,具有结构简单、操作方便、加 热速度快等优点。
应用范围
适用于各种陶瓷材料的烧成、烧结和熔融等工艺过程,特别适合于 大规模生产。
使用注意事项
使用马弗炉时应注意安全,避免烫伤和火灾事故;同时应注意炉温的 控制和炉内气氛的调节,以保证烧成效果。
真空炉
特点
真空炉是在真空环境下进行加热的设备,具有高温、高真 空的特点,可以有效地去除材料中的气体和杂质,提高产 品的纯度和性能。
02
烧结方法的分类
固相烧结
01
02
03
定义
固相烧结是陶瓷材料在完 全或部分熔融状态下获得 致密化的过程。
特点
固相烧结过程中不出现液 相,致密化主要依靠颗粒 重排、扩散传质和颗粒表 面能的驱动。
应用
适用于制备高熔点、低导 热系数、低塑性的陶瓷材 料,如氧化铝、氮化硅等。
液相烧结
定义
01
液相烧结是通过添加可熔性组分(如金属、玻璃或其它陶瓷材
在复合材料中的应用
树脂基复合材料
通过烧结方法制备树脂基复合材料,提高材料的强度、刚度和耐 腐蚀性。
碳纤维复合材料
通过烧结方法制备碳纤维复合材料,实现材料的轻量化和高性能 化。
玻璃纤维复合材料
通过烧结方法制备玻璃纤维复合材料,提高材料的强度和耐热性。
感谢您的观看
THANKS
瓷材料的致密度和力学性能。
应用
适用于制备形状复杂、细孔结构的陶 瓷制品,如蜂窝陶瓷、多层陶瓷电容
器等。
03
烧结工艺参数
温度
低温烧结
低温烧结通常在1000℃以下进行,适用于对热敏感的材料,如某些玻璃或陶瓷。低温烧结可以减少材料内部的热应力, 降低烧结温度对材料性能的影响。
热压烧结法
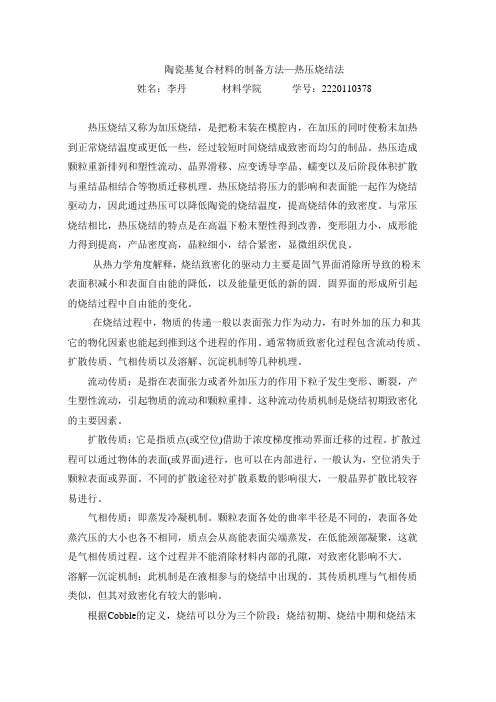
陶瓷基复合材料的制备方法—热压烧结法姓名:李丹材料学院学号:2220110378热压烧结又称为加压烧结,是把粉末装在模腔内,在加压的同时使粉末加热到正常烧结温度或更低一些,经过较短时间烧结成致密而均匀的制品。
热压造成颗粒重新排列和塑性流动、晶界滑移、应变诱导孪晶、蠕变以及后阶段体积扩散与重结晶相结合等物质迁移机理。
热压烧结将压力的影响和表面能一起作为烧结驱动力,因此通过热压可以降低陶瓷的烧结温度,提高烧结体的致密度。
与常压烧结相比,热压烧结的特点是在高温下粉末塑性得到改善,变形阻力小,成形能力得到提高,产品密度高,晶粒细小,结合紧密,显微组织优良。
从热力学角度解释,烧结致密化的驱动力主要是固气界面消除所导致的粉末表面积减小和表面自由能的降低,以及能量更低的新的固.固界面的形成所引起的烧结过程中自由能的变化。
在烧结过程中,物质的传递一般以表面张力作为动力,有时外加的压力和其它的物化因素也能起到推到这个进程的作用。
通常物质致密化过程包含流动传质、扩散传质、气相传质以及溶解、沉淀机制等几种机理。
流动传质:是指在表面张力或者外加压力的作用下粒子发生变形、断裂,产生塑性流动,引起物质的流动和颗粒重排。
这种流动传质机制是烧结初期致密化的主要因素。
扩散传质:它是指质点(或空位)借助于浓度梯度推动界面迁移的过程。
扩散过程可以通过物体的表面(或界面)进行,也可以在内部进行,一般认为,空位消失于颗粒表面或界面。
不同的扩散途径对扩散系数的影响很大,一般晶界扩散比较容易进行。
气相传质:即蒸发冷凝机制。
颗粒表面各处的曲率半径是不同的,表面各处蒸汽压的大小也各不相同,质点会从高能表面尖端蒸发,在低能颈部凝聚,这就是气相传质过程。
这个过程并不能消除材料内部的孔隙,对致密化影响不大。
溶解—沉淀机制:此机制是在液相参与的烧结中出现的。
其传质机理与气相传质类似,但其对致密化有较大的影响。
根据Cobble的定义,烧结可以分为三个阶段:烧结初期、烧结中期和烧结末期。
无压烧结 热压烧结

无压烧结热压烧结
无压烧结和热压烧结是陶瓷材料制备中常用的两种工艺方法。
无压烧结是指在大气条件下,通过加热陶瓷粉末使其颗粒间发生相互扩散、结合并形成致密块体的过程。
而热压烧结则是在高温高压条件下,对陶瓷粉末进行加热和压缩,以实现颗粒间的结合和致密化。
从工艺角度来看,无压烧结相对简单,只需要通过加热来实现颗粒间的扩散和结合,不需要额外的压力。
这种方法适用于一些特殊形状的陶瓷制品,但由于缺乏压力,制品的致密度和强度可能不如热压烧结的高。
而热压烧结则结合了高温和高压的条件,可以更好地实现陶瓷粉末的致密化和结合,因此通常可以获得更高的致密度和强度。
但是,这种方法需要更复杂的设备和工艺控制,成本相对较高。
从材料性能角度来看,热压烧结通常可以获得更高的致密度和强度,因此适用于对材料性能要求较高的场合,例如制备高性能陶瓷刀具、陶瓷复合材料等。
而无压烧结则适用于一些对致密度和强度要求相对较低的场合,例如一些绝缘材料、陶瓷颗粒增强复合材
料等。
综上所述,无压烧结和热压烧结都是陶瓷材料制备中常用的工艺方法,它们各有优势和适用场合。
选择合适的工艺方法需要综合考虑材料性能要求、成本和生产工艺等因素。
陶瓷材料的烧结与晶粒生长
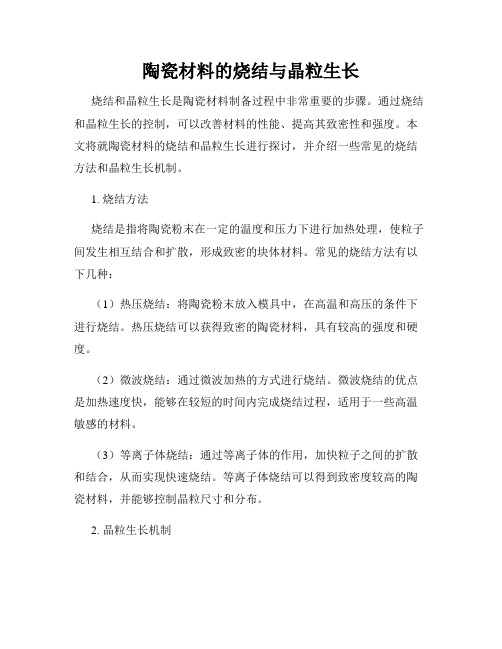
陶瓷材料的烧结与晶粒生长烧结和晶粒生长是陶瓷材料制备过程中非常重要的步骤。
通过烧结和晶粒生长的控制,可以改善材料的性能、提高其致密性和强度。
本文将就陶瓷材料的烧结和晶粒生长进行探讨,并介绍一些常见的烧结方法和晶粒生长机制。
1. 烧结方法烧结是指将陶瓷粉末在一定的温度和压力下进行加热处理,使粒子间发生相互结合和扩散,形成致密的块体材料。
常见的烧结方法有以下几种:(1)热压烧结:将陶瓷粉末放入模具中,在高温和高压的条件下进行烧结。
热压烧结可以获得致密的陶瓷材料,具有较高的强度和硬度。
(2)微波烧结:通过微波加热的方式进行烧结。
微波烧结的优点是加热速度快,能够在较短的时间内完成烧结过程,适用于一些高温敏感的材料。
(3)等离子体烧结:通过等离子体的作用,加快粒子之间的扩散和结合,从而实现快速烧结。
等离子体烧结可以得到致密度较高的陶瓷材料,并能够控制晶粒尺寸和分布。
2. 晶粒生长机制晶粒生长是指陶瓷材料在烧结过程中晶粒尺寸的增大。
晶粒尺寸的大小和分布对陶瓷材料的性能有着重要的影响。
常见的晶粒生长机制包括以下几种:(1)一维生长:晶粒沿着某个方向生长,呈现出棒状或柱状的形态。
一维生长机制适用于一些具有纤维状结构的陶瓷材料。
(2)表面扩散:晶粒表面发生扩散,并与周围的颗粒结合。
表面扩散是晶粒生长的主要机制之一,通过控制晶粒表面的扩散速率,可以调控晶粒尺寸和形态。
(3)体内扩散:晶粒内部的原子通过扩散运动,使晶粒尺寸增大。
体内扩散主要取决于材料的化学成分和温度条件。
3. 影响烧结和晶粒生长的因素烧结和晶粒生长受到多种因素的影响,下面介绍其中几个重要的因素:(1)温度:温度是烧结和晶粒生长的关键因素之一。
适当的温度可以促进晶粒的结合和生长,但过高的温度可能引起过烧,导致晶粒长大过快。
(2)压力:压力可以提高粒子的结合程度和致密性,对烧结效果有重要影响。
不同材料和形状的陶瓷,适宜的压力范围也有所不同。
(3)时间:烧结时间影响烧结程度和晶粒生长的速率。
- 1、下载文档前请自行甄别文档内容的完整性,平台不提供额外的编辑、内容补充、找答案等附加服务。
- 2、"仅部分预览"的文档,不可在线预览部分如存在完整性等问题,可反馈申请退款(可完整预览的文档不适用该条件!)。
- 3、如文档侵犯您的权益,请联系客服反馈,我们会尽快为您处理(人工客服工作时间:9:00-18:30)。
6.65×10-3Pa 气体压力: Max.0.93MPa 加热压压力: Max.4.9×10-4N 热功率: 20KVA
热压烧结工艺是在一定的高温下,对样品施加 一定的压力,使坯体粉体中的质点在受高温作用 的同时还受到外加机械力的作用,促进毛坯中不 同粉粒间的接触与扩散,使得粉粒重排,粒间发 生滑移,大的堆积间隙被填充,气孔被排除,从 而提高其反应速度和样品的致密度
烧结粉体装模,放入烧结炉中
进行热压烧结
关闭烧结炉,清理烧结制品
对结品进行加工
装料前要根据所装粉料的密度、设定厚度、
模具的大小,进行粉料质量的计算 装入模具的粉料需摇平、摇匀、防止烧结体 压扁 料与垫片,垫片与垫片间需垫石墨纸 严格遵守操作程序
在烧结过程中施加一定的外力,使材料 加速流动、重排和致密化,制备致密、坚硬 的烧结体。通过实验使学生掌握陶瓷热压烧 结方法、熟悉高温烧结炉、掌握正确操作规 程
多功能高温烧结炉;石墨片
型号:FVPHP-R-5.FRET-20 主要技术参数:
温度指标: 最高温度2300℃,通常工作温度2200℃ 升温时间:60分钟内从室温升至2200℃ 模具内腔尺寸: Φ120×110mm 真空度: