活性焦工艺
活性焦吸附法
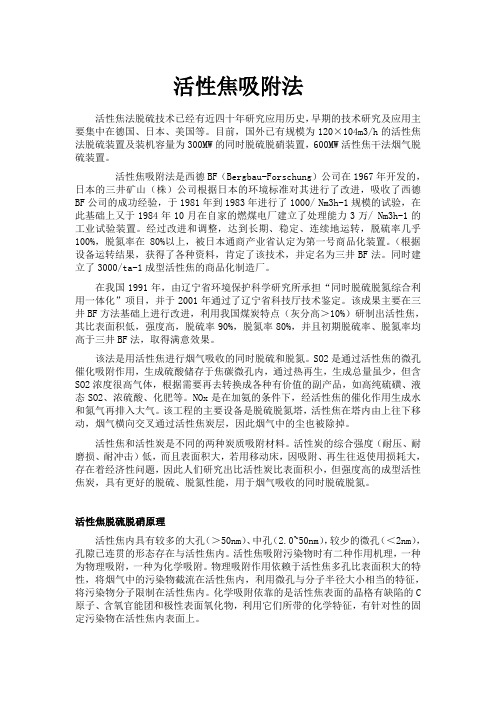
活性焦吸附法活性焦法脱硫技术已经有近四十年研究应用历史,早期的技术研究及应用主要集中在德国、日本、美国等。
目前,国外已有规模为120×104m3/h的活性焦法脱硫装置及装机容量为300MW的同时脱硫脱硝装置,600MW活性焦干法烟气脱硫装置。
活性焦吸附法是西德BF(Bergbau-Forschung)公司在1967年开发的,日本的三井矿山(株)公司根据日本的环境标准对其进行了改进,吸收了西德BF公司的成功经验,于1981年到1983年进行了1000/ Nm3h-1规模的试验,在此基础上又于1984年10月在自家的燃煤电厂建立了处理能力3万/ Nm3h-1的工业试验装置。
经过改进和调整,达到长期、稳定、连续地运转,脱硫率几乎100%,脱氮率在80%以上,被日本通商产业省认定为第一号商品化装置。
(根据设备运转结果,获得了各种资料,肯定了该技术,并定名为三井BF法。
同时建立了3000/ta-1成型活性焦的商品化制造厂。
在我国1991年,由辽宁省环境保护科学研究所承担“同时脱硫脱氮综合利用一体化”项目,并于2001年通过了辽宁省科技厅技术鉴定。
该成果主要在三井BF方法基础上进行改进,利用我国煤炭特点(灰分高>10%)研制出活性焦,其比表面积低,强度高,脱硫率90%,脱氮率80%,并且初期脱硫率、脱氮率均高于三井BF法,取得满意效果。
该法是用活性焦进行烟气吸收的同时脱硫和脱氮。
SO2是通过活性焦的微孔催化吸附作用,生成硫酸储存于焦碳微孔内,通过热再生,生成总量虽少,但含SO2浓度很高气体,根据需要再去转换成各种有价值的副产品,如高纯硫磺、液态SO2、浓硫酸、化肥等。
NOx是在加氨的条件下,经活性焦的催化作用生成水和氮气再排入大气。
该工程的主要设备是脱硫脱氮塔,活性焦在塔内由上往下移动,烟气横向交叉通过活性焦炭层,因此烟气中的尘也被除掉。
活性焦和活性炭是不同的两种炭质吸附材料。
活性炭的综合强度(耐压、耐磨损、耐冲击)低,而且表面积大,若用移动床,因吸附、再生往返使用损耗大,存在着经济性问题,因此人们研究出比活性炭比表面积小,但强度高的成型活性焦炭,具有更好的脱硫、脱氮性能,用于烟气吸收的同时脱硫脱氮。
活性焦相关技术资料

活性焦烟气脱硫技术相关技术资料一、生产工艺生产工艺:活性焦的生产方法是按重量百分比将褐煤与焦煤混合并粉碎制得煤粉,加入煤焦油和水基乳化剂捏合制成煤膏,煤膏经液压挤条制成条状颗粒,在炭化炉中一次完成烘干、炭化,在具有氧化氛围的活化炉中,通入水蒸汽活化制成活化料,活化料经自然氧化形成具有丰富表面官能团结构的活性焦。
用褐煤作为制作活性焦的主原料,不仅价格相对便宜,所制作活性焦的性能除具有强度高,中孔发达和同时脱硫脱硝的特点外,还可在脱硫脱硝的同时应用于烟气除尘。
大约1.5T至2.1T生产一吨活性焦。
二、活性焦烟气脱硫技术成本国内目前已投入连续稳定运行的某工业活性焦干法脱硫装置年运行成本分析见表2。
以此计算,活性焦的消耗占烟气脱硫技术总成本的约65%,是影响活性焦脱硫技术经济性能的关键因素。
由试验研究和实际运行表明,活性焦的消耗主要包括两部分,其一为脱附再生反应时消耗的活性焦,其二为活性焦颗粒在移动床自上而下移动时因为磨损消耗的数量。
一般而言,磨损消耗的活性数量与其质量紧密相连,活性焦质量差则消耗高,使脱硫成本增加。
因此,降低烟气脱硫技术成本的主要途径是提高活性焦性能,尤其是提高其耐压强度和耐磨强度,同时又不降低其脱硫性能,从而降低活性焦的消耗和生产成本。
目前,可以采用的主要工艺方法包括配煤技术,通过配煤技术改善活性焦的原料性能,达到改善孔隙结构和吸附脱附性能的目的;另外,也可以通过工艺参数的改变或采取添加催化剂的方法,以达到提高脱硫用活性焦综合使用性能的目的,以降低活性焦在烟气脱硫过程中的使用成本,从而最终降低烟气脱硫技术成本。
三、活性焦干法烟气脱硫技术应用情况目前活性焦干法烟气脱硫技术在电厂应用中,主要是在一些小型机组上使用,如5万千瓦、10万千瓦,最大的30万千瓦机组。
目前国内尚无投产运行使用此技术的大型机组。
在建的主要是神华在锡林浩特市的胜利电厂,规模是2×660MW空冷超临界机组。
整个活性焦干法烟气脱硫系统招标价8亿元。
针对污水处理厂提标的活性焦应用工艺

针对污水处理厂提标的活性焦应用工艺摘要:经过生化处理后的城市污水,出水水质为《城镇污水处理厂污染物排放标准》(GB18918-2002)中的一级B标准,采用活性焦过滤吸附法进行深度处理,出水水质可以达到《地表水环境质量标准》(GB3838-2002)中III类水质标准,满足再生水要求。
活性焦过滤吸附工艺在技术、经济两方面的可行性,为大量的缺水城市通过将城市污水进行深度处理提标,从而解决水资源严重短缺问题提供了一条有效途径。
截止目前ACAA技术已完成市政、焦化、印染、化工等污水工程应用已突破150个项目,日处理水量达到350万吨以上。
关键词:污水处理厂;活性焦;技术原理;工艺流程;污水提标1技术原理活性焦吸附与活化技术。
(简称“ACAA”技术,Activated Coke Adsorption and Activation),是一种可去除水中常规污染物指标的吸附活化技术。
不仅可去除COD、BOD等成分,对于污水的脱色、除臭等也具有非常良好的效果。
对于常规生化、高级氧化等难以去除的有机污染物,也具有明显的去除效率,是目前比较成熟的污水处理工艺之一,在污水深度处理、提标改造、中水回用及零排放领域得到了充分的认可。
吸附饱和后的活性焦,再通过850℃的活化再生炉进行再生。
吸附的有机物在再生过程中进行高温裂解。
有机污染物转化为甲烷、乙烷、碳氢化合物等成分组成可燃气体作为热能利用,且活性焦的孔道重新打开,性能得以恢复,损失率低,活性焦循环使用。
活性焦再生过程无固废产生,真正意义实现污染物清洁排放。
2活性焦再生活化吸附饱和的活性焦,通过高温裂解活化再生系统将吸附在活性焦孔道内的有机污染物进行分解,此时的有机污染物转化为甲烷、乙烷、碳氢化合物等成分组成可燃气体作为热能利用,且活性焦的孔道重新打开,活性焦循环使用;活性焦的再生性能恢复率为90-110%,再生破碎损耗率小于5%,真正意义实现污染物去除的清洁技术。
图1国清智能多段式再生炉图2活性焦再生活化系统3吸附过程活性焦的吸附过程是:在其颗粒表面形成一层平衡的表面浓度,再把有机物质杂质吸附到活性炭颗粒内,使用初期的吸附效果很高,但时间一长,活性炭的吸附能力会不同程度地减弱,吸附效果也随之下降。
活性焦设备工艺技术概况

烟道气)从炉头进入回转炉内,最后经过炉尾焚烧排入烟囡。整 个过程中,物料与活化气体混合物逆向流动接触活化。回转活化 炉是目前国内外中小企业使用较多的一种活化设备。它的优点主 要是投资小, 建设周期短;机械化程度高,劳动强度较小;更换 原料及调整工艺过程快,开、停炉 方便。
气体活化法所用的原料称为焦化料,焦化料在焦化过程中就形成 了活化所需要的 表面积和初孔结构,不过由于初孔孔隙被焦化过程 中生成的一些无序的无定形碳或焦 油馏出物所堵塞或封闭,因此焦 化料的比表面积很小。气体活化的过程就是通过气化 反应使焦化料
原来闭塞的孔开放、原有孔隙的扩大及孔壁烧失、某些结构经选择 性活 化而产生新孔的过程。在一定的活化烧失率范围内,活化气体 与焦化料的气化反应程 度越深,生产出的活性焦比表面积就越大、 孔隙就越发达、活性焦的吸附性能就越好。
谢谢 观看
2) 筛分工段 经过活化的活性焦分为两部分,一部分直接进入磨粉工段,另一 部分进入筛分工段。作为筛上物的粗颗粒产品,直接作为成品进 行包装;筛下物的细颗粒继续进入到磨粉工段。 4) 包装工段 配备粉料包装机及颗粒包装机,分别用于粉料和筛分后的颗粒成 品料的包装
回转活化炉特点:
回转活化炉主要由加料装置、炉尾、回转筒体、出料装置、炉头 所组成。炉头设有活化气体入口和燃料烧咀。
化反应属于气固 相系统的多相反应,活化过程中包括物理和化学两 个过程,整个过程包括气相中的活 化剂向焦化料外表面的扩散、活 化剂向焦化料内表面进行扩散、活化剂被焦化料表面 所吸附、焦化
料表面发生气化反应生成中间产物(表面络合物)、中间产物分解 成反应 产物、反应产物脱附、脱附下来的反应产物由焦化料内表面 向外表面扩散等过程。
活性焦干法烟气集成净化技术
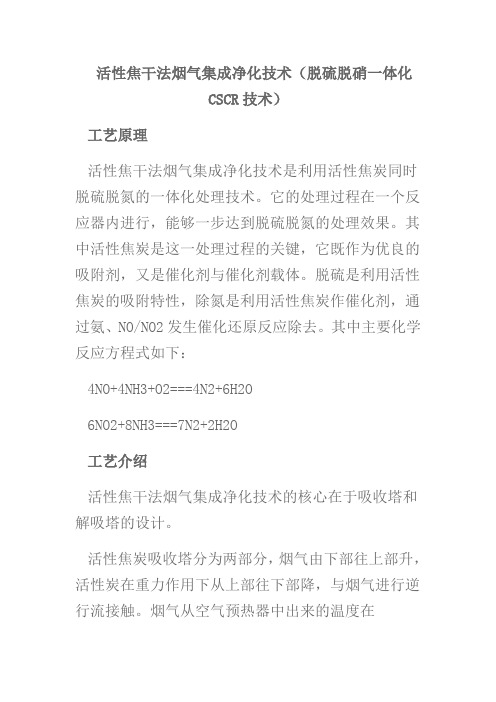
活性焦干法烟气集成净化技术(脱硫脱硝一体化CSCR技术)工艺原理活性焦干法烟气集成净化技术是利用活性焦炭同时脱硫脱氮的一体化处理技术。
它的处理过程在一个反应器内进行,能够一步达到脱硫脱氮的处理效果。
其中活性焦炭是这一处理过程的关键,它既作为优良的吸附剂,又是催化剂与催化剂载体。
脱硫是利用活性焦炭的吸附特性,除氮是利用活性焦炭作催化剂,通过氨、NO/NO2发生催化还原反应除去。
其中主要化学反应方程式如下:4NO+4NH3+O2===4N2+6H2O6NO2+8NH3===7N2+2H2O工艺介绍活性焦干法烟气集成净化技术的核心在于吸收塔和解吸塔的设计。
活性焦炭吸收塔分为两部分,烟气由下部往上部升,活性炭在重力作用下从上部往下部降,与烟气进行逆行流接触。
烟气从空气预热器中出来的温度在(102-160)℃之间,该温度区域是此工艺的最佳温度,能达到最高的脱除率。
烟气首先进入吸收塔下部,在这一段SO2被脱出,然后烟气进入上面部分,喷入氮气与NOX反应脱硝。
饱含SO2的焦炭从吸收塔底部排出来通过震动筛,不合大小的颗粒焦炭催化剂在进入解析塔之前被筛选出来。
经过筛选的活性焦炭再被送到解析塔顶部。
活性焦炭解析塔包括三个主要的区域:上层区域是加热区,中间部分是热解析区,下面是冷却区。
天然气燃烧器用来加热通过换热器间接加热活性焦炭。
在解析塔底部,空气从20℃被加热到250℃,接着天然气燃烧器将空气加热到550℃,这部分空气将在解析塔的上部用于预加热活性焦炭。
排除的富含SO2的气体将会用来生产硫酸或其它高纯度硫系列产品。
工艺流程锅炉烟气通过增压风机加压进入吸附塔,进入塔内的烟气在穿过活性焦层时烟气中的二氧化硫、氮氧化物、汞等重金属以及HF、HCL、二噁英等污染物被活性焦吸附,净化后的烟气经净烟道汇集通过烟囱排出。
吸附饱和的活性焦从吸附塔底部排出,通过输送系统运至解析塔加热解析;再生后的活性焦经筛分再被返回吸附塔内重复。
活性焦设备工艺技术概况

化反应属于气固 相系统的多相反应,活化过程中包括物理和化学两 个过程,整个过程包括气相中的活 化剂向焦化料外表面的扩散、活 化剂向焦化料内表面进行扩散、活化剂被焦化料表面 所吸附、焦化 料表面发生气化反应生成中间产物(表面络合物)、中间产物分解 成反应 产物、反应产物脱附、脱附下来的反应产物由焦化料内表面 向外表面扩散等过程。
谢谢 观看
活性焦工艺技术概况
延河重工
(1) 国内、外工艺技术概况 活性焦生产的核心过程就是活化,按照活化方式的分类, 活性焦的生产方法目前 分为三种,即气体活化法、化学 药品活化法及化学物理活化法。目前国内外以兰炭为原料 生产活性焦的厂商一般都采用气体活化法。以下主要介绍 气体活化法工艺。
2)气体活化法 气体活化法是将原料经过焦化后,采用水蒸汽、烟道气、空气等 含氧气体或水蒸 汽与烟道气、水蒸汽与空气、烟道气与空气等混 合气体作为活化剂,在高温下与焦化 所得的具有一定初孔结构的 焦化料接触进行活化或两种活化剂交替进行活化,从而生 产出比 表面积巨大、孔隙发达的活性焦产品。 气体活化法也称物理活化法,焦一种发展,它是在焦化料生产过 程中加入少量的 催化剂(一种或几种),当焦化料进行活化时, 催化剂催化焦化料与水蒸汽、二氧化碳 (烟道气)等活化剂的气化 反应,生产出具有特殊孔隙结构或高吸附性能的活性焦产品。 气 体活化法基本适合于所有含碳材料用于制造活性焦的生产过程。 目前,国内外气体活化法生产活性焦最常用的活化气体
2) 筛分工段 经过活化的活性焦分为两部分,一部分直接进入磨粉工段,另一 部分进入筛分工段。作为筛上物的粗颗粒产品,直接作为成品进 行包装;筛下物的细颗粒继续进入到磨粉工段。 4) 包装工段 配备粉料包装机及颗粒包装机,分别用于粉料和筛分后的颗粒成 品料的包装
活性焦到底是什么,三分钟告诉你答案

活性炭(焦)到底是什么?三分钟告诉你答案文章导读如今我国使用的焦炉烟气脱硫脱硝技术共有四种,但其传统的半干法脱硫、SCR脱硝工艺已经不能适应日益增长的工业效率和环保需求,不能适应有关方面的国家新规、新政策。
本文主要介绍了利用活性炭(焦)的吸附性和催化性,与烟气在吸附塔内逆向流动的脱硫脱硝工艺,以迎合新时代的工业发展方向,节能降耗,实现效益最大化。
2019年,国家环保产业迈入一个新的元年。
纵观历年来环保产业的发展,无疑2019年将开启截然的局面,水土固废气的大监管格局已形成。
活性炭(焦)脱硫脱硝工艺技术是国家“十三五”863 课题——“可资源化烟气脱硫技术”的引进、研发及工程应用项目,“活性焦干法烟气脱硫技术”被国家工业和信息化部列为清洁生产技术推行方案。
新的格局下,环保产业已从政策播种时代进入到全面的政策深耕时代,加强先进适用环保技术装备推广应用和集成创新刻不容缓。
1、活性炭(焦)性质简介1.1活性炭(焦)是一种什么物质活性炭(焦)是以煤炭为主要原材料,经过磨粉、混捏成型、炭化、活化及洗涤等一系列工序研制而成得到的,特异性吸附能力较强的环保材料。
不但能够当作高分散催化体系,还能够当作还原剂使用。
1.2活性炭(焦)的物理、化学特性活性炭(焦)的主要物理特性是其孔结构和比表面积。
活性炭在结构方面,因为是不规则排列的微晶炭,所以在固定的地方会有一些小间隙,小间隙之间的相互组合产生数量较多的微孔,较大的内比表面积,让活性炭质材料有良好的吸附功能。
另外,这种材料较大的比表面和数量较多的孔结构让分子更加容易进行扩散。
活性炭(焦)的化学特性即在活性炭质材料的表面上,有很多的含氧、含氮官能团。
产生吸附作用的活性中心就是表面官能团,它让活性炭质材料具有弱极性,使吸附剂的催化性能更加强大,让炭对有机物、无机物的吸附选择性发生变化2、活性炭(焦)应用场景2.1活性炭(焦)的好处活性炭(焦)因为自身的吸附特性和催化特性,对于烟气有良好的净化效果,跟传统SCR、SICS等工艺相比,在活性炭(焦)脱硫脱硝工艺的过程中,没有废水、废渣、废气等二次污染产生,能够去除湿法难以去除的三氧化硫,具有运行费用低,维护方便,系统能耗低的优点。
活性焦再生过程原理流程
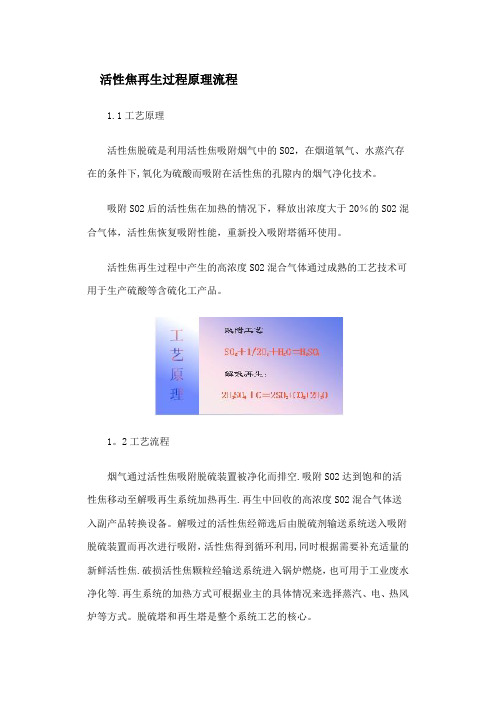
活性焦再生过程原理流程1.1工艺原理活性焦脱硫是利用活性焦吸附烟气中的SO2,在烟道氧气、水蒸汽存在的条件下,氧化为硫酸而吸附在活性焦的孔隙内的烟气净化技术。
吸附SO2后的活性焦在加热的情况下,释放出浓度大于20%的SO2混合气体,活性焦恢复吸附性能,重新投入吸附塔循环使用。
活性焦再生过程中产生的高浓度SO2混合气体通过成熟的工艺技术可用于生产硫酸等含硫化工产品。
1。
2工艺流程烟气通过活性焦吸附脱硫装置被净化而排空.吸附SO2达到饱和的活性焦移动至解吸再生系统加热再生.再生中回收的高浓度SO2混合气体送入副产品转换设备。
解吸过的活性焦经筛选后由脱硫剂输送系统送入吸附脱硫装置而再次进行吸附,活性焦得到循环利用,同时根据需要补充适量的新鲜活性焦.破损活性焦颗粒经输送系统进入锅炉燃烧,也可用于工业废水净化等.再生系统的加热方式可根据业主的具体情况来选择蒸汽、电、热风炉等方式。
脱硫塔和再生塔是整个系统工艺的核心。
1.3模块化设计根据活性焦脱硫技术的特点,脱硫装置采用模块化设计思想,使不同容量的锅炉脱硫时进行较为简单的模块组合,提高了工程效率。
2系统组成及布置活性焦脱硫系统由活性焦吸附脱硫装置、解吸再生系统、脱硫剂输送系统和SO2气体加工系统组成。
活性焦脱硫系统安装于除尘器与烟囱之间。
脱硫装置由吸附反应器、再生反应器构成,根据实际情况以及业主要求可采用一体化布置或分体式布置。
烟气从烟道进入脱硫装置净化以后,返回烟道排空.在装置进出口烟道和装置旁路烟道上设置了关闭挡板风门,通过控制挡板风门,可方便地投入或切除该装置。
脱硫风机用于克服吸附反应器对烟气的阻力,整个脱硫装置与原有烟气并联布置,呈一个相对独立的脱硫岛。
SO2气体加工处理根据情况可以相对独立布置。
3技术特点·环保性能优异的资源化干法脱硫技术,降低建设与运行费用;·脱硫效率>95%,同时具有良好除尘效果(除尘效率>70%),并能同时脱除汞、二恶英、氮氧化物等有害物质,真正实现污染物的集成净化。
- 1、下载文档前请自行甄别文档内容的完整性,平台不提供额外的编辑、内容补充、找答案等附加服务。
- 2、"仅部分预览"的文档,不可在线预览部分如存在完整性等问题,可反馈申请退款(可完整预览的文档不适用该条件!)。
- 3、如文档侵犯您的权益,请联系客服反馈,我们会尽快为您处理(人工客服工作时间:9:00-18:30)。
目录1、活性焦联合脱硫脱硝技术 (1)1.1脱硫用活性焦的制备 (2)1.2活性焦原料配比对活性焦性能的影响 (2)1.3活性焦联合脱硫脱硝技术的工业应用 (2)2、活性焦脱除S02和NO,的机理 (3)2.1活性焦烟气联合脱硫脱硝技术工艺流程 (4)3、影响活性焦性能的因素 (4)3.1温度对脱硫效果的影响 (4)3.2水蒸气及氧气含量对脱硫性能的影响 (4)3.3活性焦改性对脱硫效果的影响 (5)4、联合脱硫脱硝技术的特点 (5)5、活性焦工艺的经济性分析 (5)6、结语 (6)近20年是烟气中S02和N0X同时脱除技术发展最快的时期。
按脱除机理不同,这些技术可分为2大类,即同时脱硫脱硝(Simultaneous S02/ N0x Removal)技术和联合脱硫脱硝(Co mbined S02/NOxRemoval)技术。
同时脱硫脱硝技术是指用一种吸附剂在同一过程内将烟气中的S02和NOx同时脱除的技术,如钙基同时脱硫脱硝技术。
另外,应用电场技术的烟气净化方法也在研究、开发之中,如电子束法、电晕放电法等技术。
目前,同时脱硫脱硝技术的相关研究大都处于试验研究阶段,离大规模工业化应用尚有一定距离。
活性焦脱硫就是一种能实现同时脱硫脱硝除尘的技术。
1、活性焦联合脱硫脱硝技术活性焦是以煤炭为原料生产的一种新型炭材料,其生产过程与活性炭基本相同,但生产条件、原料、配方和主要设备结构与活性炭生产工艺差别很大,均需要根据活性焦的特点进行改进。
近年来,日本、德国、美国等国以及我国的煤炭科学研究总院相继开发出了综合强度高、比表面积较小的活性焦。
活性焦是S02的优良吸附剂,也是NH3还原NO的优良催化剂。
目前,已经开发的脱硫脱硝催化剂及其使用温度见表一表一脱硫脱硝催化剂及其使用温度活性焦能在110?150乞时将NO催化还原成%和1120,此温度范围恰好在工业锅炉烟气排放温度范围内,因此,无需对烟气加热。
活性焦烟气脱硫脱硝技术无二次污染,可循环使用,脱除效率高。
美国政府调査报告为,该技木是最先进的烟气脱硫脱脱硝技术。
然而,活性焦联合脱硫脱硝的机理仍需进一步研究,工艺还需完善。
1.1脱硫用活性焦的制备脱硫用活性焦一般直径为9mm,长度为8-12mm。
脱硫用的活性焦具有活性炭的优点,克服了活性炭的缺点,比活性炭的脱硫脱氮效率高,并且机械强度髙、价格低,比表面积大,耐磨、耐压、耐冲击。
活性焦内具有较多的大孔(>50nm)、中孔(2.0~50nm)及较少的微孔(<2nm),孔隙以连贯的形态存在于活性焦内。
这种孔式的使其具有吸附污染物的作用。
1.2活性焦原料配比对活性焦性能的影响脱硫用活性焦原料由褐煤半焦、焦煤、煤焦油组成。
褐煤是炭化程度很低的煤,是煤中等级最低、形成年代最短的一类。
褐煤的机械强度低,化学反应性强,在空气中易风化变质,容易自燃,不易储存和远距离运输,发热量较低。
由于褐煤的成焦性能较差,因此用其制备活性焦时必须加人一定量的焦煤,才能炼制成焦。
考虑到原料褐煤和焦煤所占比例不仅影响活性焦产品的质量,也影响其价格,因此,应在保证其质量的前提下尽量减少焦煤的用量。
此外,在活性焦的制备过程中,粘结剂的加人既利于其成型也能提高其机械强度,但粘结剂含量过髙会降低其脱硫脱氮效率。
原料配比不同,制成的活性焦性能差异较用碘吸附率[1]反映活性焦的吸附性能,碘吸附率越髙,活性焦吸附性能越好;用转鼓强度[2]反映活性焦的机械强度,转鼓强度越高,活性焦的机械强度越髙。
原料配比对活性焦性能影响试验的结果如表2所示。
表2 原料配比对70 20 10 40.42 80.8865 25 10 49.28 98.6765 25 10 49.28 98.6755 35 10 33.11 98.02由表2可见,褐煤半焦:焦煤:煤焦油为65:25:10时所制备的活性焦的碘吸附率和转鼓强度均较高合于作为脱硫脱硝用的脱硫脱硝剂。
1.3活性焦联合脱硫脱硝技术的工业应用活性焦联合脱硫脱硝技术发展以德国和日本最为先进。
德国BF公司在1976年开发,后经日本三井矿山公司改进建立了实验装置,并于1984年建成烟气处理量为3万m3/h的活性焦脱硫装置。
德国于1987年就已成功地将活性炭(焦)联合脱除S02/N0、工艺用于ArAerf;燃煤电厂第5号和7号机组迸行脱疏脱硝,两台机组的烟气排放量分别为45万mVh和66万m3/h, 吕02的脱除率司达95%以上,NOx地脱除率在60%左右。
日本电力能源公司(EPDC)的350 MW空气流化床燃烧(AFBC)锅炉中安装了活性焦脱除NOxI 艺设备,并于1995年开始运行。
该工艺仅采用了1台移动床吸附塔,处理的烟气量为116. 3万mVh,在140 1下,活性焦循环速率为14 600 kg/h。
经稳定运行2 200 h以上,发现NOx脱除率可达到80%。
由于从AFBC锅炉出来的S02排放浓度很低,所以在S02被活性焦吸附的同时,在第一级吸附塔中NOx&能得到有效的脱除。
2001年,煤炭科学研究总院北京煤化工分院和南京电力自动化设备总厂联合承担国家863项目,研制出高性能、低生产成本的活性焦产品。
该产品用于贵州宏福实业开发有限公司的工业示范装置,运行效果良好。
2005年4月,处理烟气量为20万mVh的工业示范装置投入运行,脱硫效率95.7% ,回收S02 1.7 t/h。
2、活性焦脱除S02和NO,的机理目前各国学者对活性焦脱除S02的机理研究较多,所得出的结论不尽一致,但基本能够达成共识的是:活性焦对S02和NOx的吸附有物理吸附和化学吸附2种方式,当烟气中无水蒸气和氧气存在时,主要发生物理吸附,吸附量非常小; 当烟气中有足够量的氧气和水蒸气时,发生物理吸附的同时也发生化学吸附[M]和表面反应。
活性焦表面的S02被催化氧化为H2S04,其反应式为2S02 +02 +2H20 —2H2S04 (1)对于炭类催化剂的SCR反应文献报道不多,研究表明,以活性焦为催化剂,SCR工艺必须用NH3作吸附剂;Mochida等认为,在活性炭纤维上,NH3吸附反应所需温度为100 ~ 150丈,其反应式为4N0 + 4NH3 + 02 —4N2 + 6H20 (2)2N02 +4NH3 + 02—3N2 +6H20 (3)活性焦再生有水洗和加热2种方法。
水洗活性焦再生需要大量的水,而且产生酸水形成二次污染,故很少使用。
活性焦再生通常是将富含302的活性焦加热到350T以上,发生如下化学反应,释放出S02。
2H2S04 + C --2S02 十C02 + 2H20 (4)再生反灰能够恢复活性焦的活性,国内外的应用实践已经证实了这一点。
活性焦经过再生、循环使用后,其吸附和催化能力不但不会降低, 还会提高。
S02以硫酸态被吸附和再生时,需要消耗活性焦的碳元素。
2.1活性焦烟气联合脱硫脱硝技术工艺流程活性焦联合脱硫脱硝工艺主要由吸附、解吸和硫回收3部分组成,工艺流程如下图所示。
该工艺采用移动床吸附加热再生法。
移动床由上下两段组成,反应温度为100 ~200度。
活性焦在重力作用下,由移动床上段向下段移动,烟气由下而上流过,在逆向移动中烟气中的302先由活性焦吸附脱除。
烟气流经上段时向塔内注入NH3, NH3与N0X在活性焦催化还原作用下生成N2。
吸附饱和的活性焦由吸收塔的底部送人再生反应器进行再生。
再生反应器也是移动床反应器, 用蒸气或热风炉尾气以间接加热的形式把吸附过S02的活性焦加热到300 ~500 T ,使活性焦得到再生。
再生反应器内的活性焦从上往下移动,停留一段时间后排出反应器,经筛分后送回活性焦脱硫反应器循环使用;再次产生的高浓度S02气体用高温离心机抽出,用于生产硫酸或其它化工产品。
在一定工艺条件下,此套装置脱硫效率可达95%以上,脱硝效率达70%以上,硫回收率达90%。
3、影响活性焦性能的因素3.1温度对脱硫效果的影响下图为不同反应温度条件下,太西活性焦脱硫率随时间的变化情况。
随着反应温度的提高,太西活性焦的so2脱除率下降。
从活性焦脱硫反应机理看,活性焦脱除so2首先发生吸附过程,即吸附在活性位上,而温度提高有利于脱附过程,导致吸附在活性位上的so2 等减少,因此最终影响了脱除率。
3.2水蒸气及氧气含量对脱硫性能的影响氧气的存在对活性焦的脱硫性能有较大影响,当氧气含量为3 % ~6 %时,活性焦的性能较佳,而氧气含量过低或过高均能导致脱硫率下降。
在没有水蒸气和氧气的条件下,活性焦的脱硫能力较差,而加人水蒸气后脱硫性能显着提高。
在同时有氧气和水蒸气存在时,活性焦脱硫率明显提高,这可能与〇2与S02反应生成S03, 而S03与H20反应生成H2S04有关。
当然水蒸气含量过高也不利于脱硫。
3.3活性焦改性对脱硫效果的影响为进一步提高活性焦的脱硫性能,许多学者研究了改性活性焦脱硫性能,煤炭科学研究总院北京煤化工分院(以下简称煤科总院煤化分院)对载Cu太西活性焦的研究结果显示,载Cu活性焦脱硫效率明显高于未改性活件焦。
据分析,改性后活性焦表面增加了新的活性位,S〇2在载Cu活性焦表面除发生吸附和与02、H20的表面发生氧化反应之外,还与覆盖在活性焦表面上的CuO反应生成了CuS04。
刘守军等[5]研究了CuO/AC用于烟气脱硫,同样发现在120?250 t范围内显示出高的脱硫活性。
Klinik等[6]的研究结果表明,负载Co、Ni、Mn和V 的化合物后,活性炭的脱硫活性增强。
卜洪忠等[7] 的总结也表明,通过添加金属化合物或硝酸改性,大部分研究者的结论是可提高活性焦(炭)的脱S02 能力,当然也有的研究者得出了不同结论。
4、联合脱硫脱硝技术的特点国内外活性焦烟气脱硫脱硝技术的开发研究和运行实践表明该技术具有多方面的优点。
(1)干法脱硫过程基本不消耗水,避免了废水处理。
反应温度在烟气排放温度范围内,无需对烟气进行加热处理,净化后的烟气也不需要冷却或加热,节约能源。
(2)脱硫塔与再生塔既可一体化设计,减少占地面积,也可分体设计;该技术既适用于老电厂改造,也适用于新建电厂脱硫。
(3)活性焦联合脱硫脱硝工艺不仅脱除烟气中的502和NO,,而且可以脱除汞、碳氢化合物及粉尘,不需要任何除尘装置即可将烟气排向烟囱。
(4)产生可出售的副产品如琉酸,有效实现了硫的资源化,并可获得一定的经济效益。
活性焦烟气联合脱硫脱硝工艺发展的总体趋势是降低净化装置的基本建设投资及运行成本。
活性焦的性能是活性焦联合脱硫脱硝工艺的关键,对所用活性焦强度、抗氧化性和抗毒化性等性能有特殊的要求。
因此,在不降低现有活性焦性能的条件下,提高其耐压强度和耐磨强度可以显着降低整个工艺成本。
加强新设备、新工艺的研究,简化现有的工艺流程,采用多功能设备,解决脱除和再生在一个装置内进行的问题,解决副产品硫酸的浓度和应用市场的问题可以促进活性焦联合脱硫脱硝工艺的大规模应用。