汽车模内镶件注塑成型( IMD )技术
IMD模内注塑专业技术应用范围

南京汇康玻璃制品有限公司成立于2009年4月,坐落于南京市溧水区东屏镇工业集中区,旗下分公司滁州汇森玻璃制品有限公司成立于2010年。坐落于滁州市琅琊区城东工业园。本公司拥有先进的印刷设备.自动化硬化设.镀膜线.注塑机等大中型设备,还有一支拥有多年生产制造经验的技术团队,依靠先进的生产设备和技术工艺能够为客户提供:彩晶钢化玻璃面板,模内注塑(IMD)和各类注塑制品以及钢化玻璃电镀。
4、3D复杂形状设计和多样化风格。图案,颜色,字体,LOGO是丝印或网印印刷载频面的片材上,成型为3D形状,可以依客户需求创造金属电镀或天然材质特殊式样。一些效果是电镀喷漆所达不到的。
5、良率高。高压成型只有下模,没有上模。成型过程中不接触片材,不会污染片材。
6、适合做3D产品和高拉伸产品。高压成型可以拉伸的高度有25厘米。
IMD实际上就是将印刷好的薄膜经过成型冲切后,镶嵌在注塑模腔内然后合模注塑而制作的产品。它是融印刷、成型、制模、注塑工艺技术为一体,会塑料片材、油墨、塑料树脂的综合运用。注塑树脂在薄膜的背面与油墨层相结合,面板图文、标识置于薄膜与注塑成型的树脂之间,图文、标识不会因摩擦或时间关系而磨损。
(二)模内镶件注塑成型IMD优势
IMD模内注塑技术应用范围
———————————————————————————————— 作者:
———————————————————————————————— 日期:
ﻩ
IMD模内注塑技术应用范围
模内镶件注塑成型装饰技术即IMD(In-MoldDecoration),IMD是目前国际风行的表面装饰技术。主要用于家电产品的装饰及功能控制面板、汽车仪表盘、空调面板、手机外壳/镜片、洗衣机、冰箱等应用非常广泛。
汽车制造IMD、INS工艺概述

好,外观效果显著,在汽车行业应用范围很广,装饰效果较好,但 是需要投入专用设备及模具,精度较高,成本较高。
由于该技绿色环保、自动化程度高,不会产生飞边披峰等等 特点,现已经在家电,3C、汽车等等产品中广泛应用。
二
IMD工艺流程
1)送膜机送膜到指定位置
2)固定膜片
3)合模注塑
4)开模取件(膜片图案 已转移到塑件表面)
三
INS工艺流程
1)薄膜加热
2)高压空气成型(或者吸 塑成型)
3)刀模裁切
4)已成型薄膜壳片放入 模腔-合模
1.需专用设备及专 用模具; 2.无高拉深; 3.受形状结构限制 比较大等。
六
标杆车IMD应用
宝马X5 2011款
宝马X6 2010款
奥迪Q5 2012款
奥迪A8L 2011款
七
总结及规划
1.XX车型仪表板装饰条及门护板装饰条上已应用IMD表面处理技术 (如上图),后续将进行切换。 2.CH071车型门护板装饰条已确定应用IMD表面处理技术。
汽车制造IMD、INS工艺
一 工艺介绍
IMD全称为IN MOULD DIRECDION,即模内装饰技术的首音 简称。
IMD-TR全称Transfer-Print,即转移印刷术。
INS全称为Film Insert Molding。将带有外观效果的INS薄膜 预先吸塑/高压成型,把多余的膜边冲切,再把冲切好的薄膜壳片放 置在注塑模具内进行注塑。
5)合模注塑
6)开模取件
四
应用范围
由于其特有的工艺特性,此 工艺已经在汽车行业内得到广泛 的应用,如汽车的车标,门板装 饰条,IP板装饰条,迎宾板,空 调出风口,DVD面板,出风口面 板,烟灰箱盖板,排挡面板等等。
IMD(IMR、IML、INS、IMF)技术分析
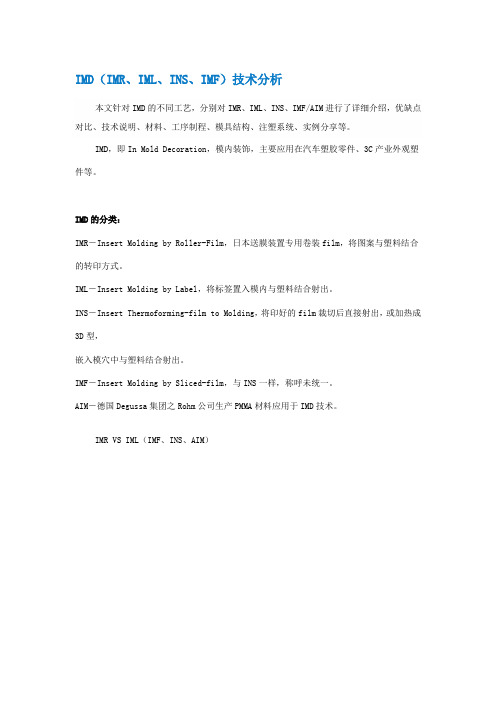
IMD(IMR、IML、INS、IMF)技术分析本文针对IMD的不同工艺,分别对IMR、IML、INS、IMF/AIM进行了详细介绍,优缺点对比、技术说明、材料、工序制程、模具结构、注塑系统、实例分享等。
IMD,即In Mold Decoration,模内装饰,主要应用在汽车塑胶零件、3C产业外观塑件等。
IMD的分类:IMR-Insert Molding by Roller-Film,日本送膜装置专用卷装film,将图案与塑料结合的转印方式。
IML-Insert Molding by Label,将标签置入模内与塑料结合射出。
INS-Insert Thermoforming-film to Molding,将印好的film裁切后直接射出,或加热成3D型,嵌入模穴中与塑料结合射出。
IMF-Insert Molding by Sliced-film,与INS一样,称呼未统一。
AIM-德国Degussa集团之Rohm公司生产PMMA材料应用于IMD技术。
IMR VS IML(IMF、INS、AIM)IMR技术说明:有鉴于当前一些以多层次加工方法生产的作法不良率高,且无法应付多颜色需求,若采人工操作过程繁杂:射出成型→ 包覆保护层→ 电镀→ 喷漆→ 擦拭→上色(曲印) →拆除保护层→ 黏贴贴附层因此有必要寻求可降低生产成本的新工法。
1. 减少原有生产的流程,降低成本。
2. 减少不良率,降低生产成本。
3. 可更加提升外观质感的工法。
4. 可达到更佳耐候条件的工法。
5. 可达到更佳环保的工法。
IMR箔膜:垫片基材依不同的模具表面曲度及扩张比率,需选择不同的基材以配合IMD工序。
IMR模具结构介绍模具两边均需加热,注塑浇口应在定模边安装IMR注塑系统四个重要注塑系统组件:模内转印箔、转印箔定位器、注塑机边料筒及射嘴、注塑模IMR工序实例光阳工厂logo:耐候测试达1000hr → OK(台湾精业开发企业股份有限公司制造)KYMCO电动代步车METER(台湾精业开发企业股份有限公司制造)KYMCO 豪迈奔腾SR G4 125车系 (喷射ENG + 奈米喷漆)KYMCO 豪迈奔腾SR G4 125车系 (陶缸+ 碟煞+ 奈米喷漆) KYMCO V-LINK 125车系 (陶缸+ 碟煞+ 奈米喷漆)KYMCO EASY 4U 100车系 (陶缸+ 碟煞+ 奈米喷漆)IMR工序国外产品实例CD播放器外壳INS 技术说明: 原本INS 是用来辅助一次成型注塑(IMD),但随着3D 立体面装饰的需求,现今的INS 技术以汽车工业来说深受欧洲大厂的亲赖(双B & AUDI)。
汽车IMDINS工艺介绍及模具问题

原因及分析:1)刀口设计不合理, 造成错位和刮削 2)刀口选用材 料及热处理不当,刀刃易损。
成品切口尺寸不准
原因及分析:1)刀口设计强度不够, 造成移位和偏差。 2)横刀设计 配合不好。3)薄膜定位不足。
模内镶嵌(INS) 注塑模
1
定位圈
2
顶板
3
水口板
4
A板
INS注塑模外观
5
前模底板
6
顶针板
7
方铁
8
后模底板
模内镶嵌(INS) 注塑国产常见问题
INS注塑模有别于普通注塑模,除正常 注塑模需注意的一般性问题外,需特别 关注的问题:
外观面不允许任何缩印
设计好薄膜外挂位置,避免 静电和真空吸附
前模用料必须高抛光耐腐蚀
模内镶嵌(INS) & 模内转印(IMR) 对比
模内镶嵌
分型面
分型面
模内转印(IMR)国产常见问题
原因分析:
水口对应点变色
水口对应点变色是由于温度过高和注塑速度 过快压力太大引起的,在模具方面要注意和 检查以下几点:
1. 水口设计是否造成注塑压力太大?
2. 模具设计是否造成水口附件运水不 足,导致温度过高?
3. 注塑机调节参数是否合理?
模内镶嵌(INS) 原理示意图
模内转印
模内镶嵌(INS) & 模内转印(IMR) 成本对比
产品单价
高 中 低 模内镶嵌 模内转印 水转印
产量
汽车IMD国产瓶颈和技术创新
IMD内饰国产化的瓶颈:
1. 汽车内饰设计水平相对滞后 2. 消费者对IMD内饰认识较少 3. IMD模具开发费用昂贵 4. 产品工序复杂、不良率高 5. 成型技术难度大,以致成本高昂
IMD基本知识教程
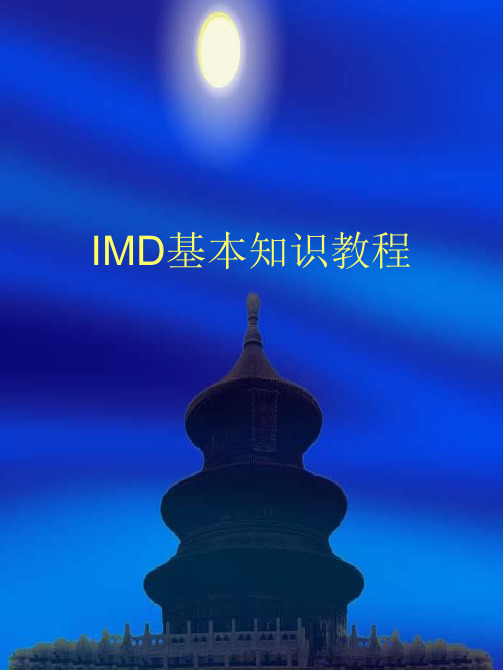
湿度90%
三、IMD的优势及其缺点
优势 1. 产品稳定性:使产品产生一致性与标准化的正确
套色。 2. 产品耐久性:耐划伤、耐磨性好、耐(溶剂)性
强,使用寿命长,不变色、不掉色。透过特殊处 理的COATING薄膜的保护,可提供产品更优良 的表面耐磨与耐化学特性。防尘、防潮性好 。 产品的表面硬度可达到H~3H。 3. 3D复杂形状设计,立体感好:应用薄膜优良的 伸展性,可顺利达成所需的产品复杂性外开设计 需求。功能按键凹凸均匀、手感好、有极长的使 用寿命。 4. 多样化风格:图案清晰:可依客户需求创造金属 电镀或天然材质特殊式样。 5. 制程简化:经由一次注塑成型的工法,将成型与 装饰同时达成,可有效降低成本与工时,可提供 稳定的生产。 6. 降低成本与工时:IMD制程中只需要一套模具, 不像其它老替代制程需开多套治具,可以去除一 次作业程序的人力与工时,降低系统成本与库存 成本。 缺点 1. 温度难控制(丝印部)。 2. 注塑、温度、压力、速度难控制。 3. 油墨的性能和成型模具的结构有难度。
1. A、三段式干燥(第一段为 70 ℃ ,第二段为 70-90 ℃ ,第三段为室温,传送带速度3-7米/分 钟)
2. B、后补干燥:放置在晾架上入烘箱中干燥,烘 箱空气流通及空气交换良好,温度为70-90℃ 15个小时。
IMD的印刷精度可达到±0.05mm。 表面硬度可达到3H。 功能按键的寿命可达到100万次以上。
薄膜使用的材料有:PET、 PC、 PVC、 PE…等,一般为卷料。 基材使用的材料有:PC、PMMA、PBT、 PC+ABS、PS…等。
目前国内一些人士把IMR称之为IMD,把IML/IMF 独立于IMD之外。最根本的区别在于IML/IMF和 IMR在lens表面的不同, IML/IMF表面有PET或PC 等片材,而IMR表面只有油墨。
IMD基础技术介绍

IMD技术介绍工程技术中心目录IMD发展历程IMD/IML/IMR简介IML工艺流程IML产品加工与设备展示IML产品应用展示IML设计注意事项IML未来发展趋势2IMD 发展历程yIMD工艺技朮最早由Bayer公司开发,于1989年第一件产品问世,应用于VM-Golf车型之显示面板.随着消费者对电子产品个性化,高质量等要求,渐延伸到手机,汽车,家电等产品上的运用.其优异的物理与机械性能深受行业的亲睐,在2002年得到业界讯速推广.3IMD/IML/IMR简介IMD :In-Mold Decoration(模内装饰成型)指在公母模间放置一印刷膜片,通过射出成形时将印刷油墨转印或Film披覆到塑件表面。
IML:In-Mold Label指在成型模内放入一片具印刷图案的膜片,射出成形时将该披覆到塑件表Film披覆到塑件表面.IMR: In-Mold Roller指在公母模间有一印刷的膜卷,射出成形时将印刷油墨转印到塑件表面,完成后需对产品表面进行Hard coating处理以达成良好的性能.(因日本Nissha公司专利问题,该工艺未被业界广范推广)4IMD优势1.产品表面抗刮伤,环境适用性高.2.复杂之3D外形,着色定位度高.3.高分辨率之图案线条,永不褪色,使用寿命提高.4.可任意设计图案.5.多彩之颜色.6.简化背光技术,色彩对比高.7.可自动化生产,产量大.8.经济效益 (a)一套模具可生产多种产品.()(b)无窗口区域产品可使用再生塑料.9.易于改变外观设计,适合多样小量式产品.5IML 工艺流程印刷整形冲切成型各工序产出品:印刷后薄膜整形后产品冲切后产品成品6IML技朮已在多个领域进行运用.7A.Film选择1.材质PET,PC目前主要采用英国柯图泰,日本中井,Bayer,GE等公司材料.yPET薄膜,其硬度2H,但热压后返弹较大,尺寸难把握,目前主要用于镜片IML。
PC薄膜硬度1H,其热定型较好,热压薄膜与塑模的配合较好,目前要用于成镜片和机壳目前主要用于成型镜片和机壳。
IMD成型技术
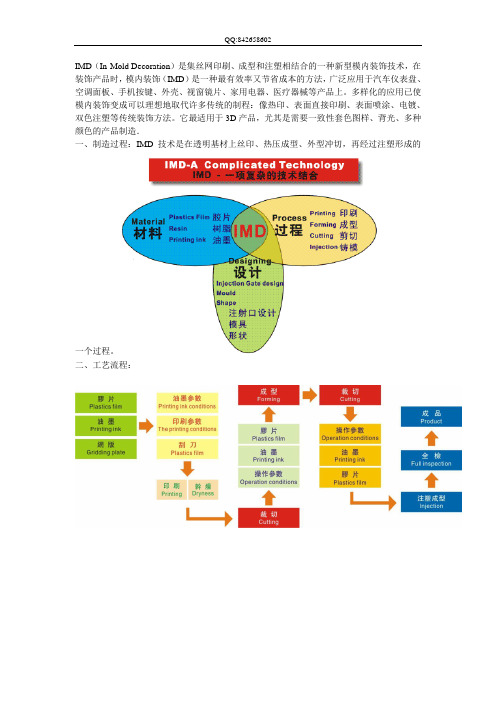
IMD(In-Mold Decoration)是集丝网印刷、成型和注塑相结合的一种新型模内装饰技术,在装饰产品时,模内装饰(IMD)是一种最有效率又节省成本的方法,广泛应用于汽车仪表盘、空调面板、手机按键、外壳、视窗镜片、家用电器、医疗器械等产品上。
多样化的应用已使模内装饰变成可以理想地取代许多传统的制程:像热印、表面直接印刷、表面喷涂、电镀、双色注塑等传统装饰方法。
它最适用于3D产品,尤其是需要一致性套色图样、背光、多种颜色的产品制造.
一、制造过程:IMD技术是在透明基材上丝印、热压成型、外型冲切,再经过注塑形成的
一个过程。
二、工艺流程:
三:IMD设备:
IML工艺的特点:
IMD/IML产品以清晰度高、立体感好、表面耐划伤、可随意更改设计造型图案、增强产品美观外型、体现完美异型结构的优势,广泛的应用于手机镜片、机壳等需3D造型的外观产品上。
解决以往压克力平板所不能达到的异型效果和多种颜色。
IMD/IML技术:是集丝网印刷、成型和注塑相结合的一种新型模内装饰技术,在装饰产品时,模内装饰(IMD/IML)是一种最有效又节省成本的方法,广泛应用于通讯产品(如:手机/小灵通镜片、装饰件、外壳等)、家用电器(视窗面板、按键面板、装饰面板等)、医疗器材(视窗镜片、机壳、装饰件等)和汽车仪表盘。
多样化的应用已使模内装饰变成可以理想的取代许多传统的制程:像热转印、表面直接印刷、表面喷涂、直接电镀、双色注塑等传统装饰方法。
它最适用于3D产品,尤其是需要一致性套色图样、背光、多种颜色并要体现在各种曲面、弧形产品等!。
浅述IMD技术及其在汽车中的应用

MANUFACTURING AND PROCESS | 制造与工艺 时代汽车 浅述IMD技术及其在汽车中的应用黄忠仕 农应斌百色职业学院 广西百色市 533000摘 要: 我国社会经济的蓬勃发展拉动了汽车产业的崛起。
随着市场竞争愈演愈烈,汽车内部装饰也成为了产品销售的独特优势,实用、精良的内饰材料会给消费者造成强烈的视觉冲击,享受到前所未有的舒适体验,从而有效激发消费者的购买欲。
基于此,为了更好地满足市场需求,在汽车开发设计中也开始注重内饰制造工艺的研发,从而提高内饰材料的实用性、精美性、以及环保性。
IMD成型技术是在现代科学技术发展基础下衍生的一种新型表面装饰技术,代表了未来汽车内饰工艺的主流趋势。
本文将通过阐释IMD技术的相关概念及工艺流程,明确IMD技术的优缺点,然后通过对IMD 各技术产品特点进行比较,分析了 IMD技术在汽车中的应用,表明其具有广阔的发展前景。
关键词:IMD 汽车内饰 工艺流程 产品特点早于20世纪90年代初汽车市场上就曾出现过双层胶片层间黏结结构的内饰设计,这是IMD技术的最初雏形。
随着技术的不断更新和发展,截止至今IMD已经逐渐发展成为多元化结构的三维成型产品。
因其较高的实用价值和精巧的制作工艺被越来越多的行业所熟知,IMD作为一种新型环保的塑料装饰技术被广泛应用于多种产品的表明装饰。
目前市场推广的IMD技术打破了传统刻板模式,开辟了新的工艺技术,实现了薄膜与印刷图案、油墨及塑料注塑相融合的突破,提高了产品表面的视觉效果,提供给消费者一种愉悦、舒适、崭新的体验。
近年来,IMD 技术被广泛应用于汽车仪表表盘、内饰件的按键等产品,并深受广大消费者的青睐和好评。
1 IMD计划概念及工艺流程的论述1.1 IMD技术概念IMD技术的全称是IN MOLD DECORATION,即能同时实现部件注塑和表明装饰的新型模内装饰技术,集功能性与美观性为一体,是目前汽车内饰生产工艺中成本最低、效率最高的技术。
- 1、下载文档前请自行甄别文档内容的完整性,平台不提供额外的编辑、内容补充、找答案等附加服务。
- 2、"仅部分预览"的文档,不可在线预览部分如存在完整性等问题,可反馈申请退款(可完整预览的文档不适用该条件!)。
- 3、如文档侵犯您的权益,请联系客服反馈,我们会尽快为您处理(人工客服工作时间:9:00-18:30)。
汽车模内镶件注塑成型(IMD )技术塑料加工商们正在将可成型彩色薄膜视为一个经济、耐用、环境友好的装饰手段,它可使零件在脱模时即已完成装饰。
模内镶件注塑成型(IMD )技术,利用的就是这种可成型薄膜,可替代传统的、在零件脱模后采用的涂漆、印刷、热模锻、镀铬工艺。
该技术的首次成功应用是制成了一些小型的、相对较平的汽车内外饰零部件和手机零件。
今天,IMD技术有了更进一步的发展,可以制成更大的三维零件,例如整个仪表板、汽车保险杠、托板、汽车顶盖,甚至汽车、卡车的发动机罩。
据说,第一个实现商业化的、无需涂漆的水平车身板已经应用在Smart双座敞篷轿车上了。
IMD技术可节省再加工的费用,这对汽车工业极具诱惑力。
GE Plastics的Lexan SLX(一种聚碳酸酯共聚物)车身零件生产经理Venkata-krishnan Umamaheswaran说:“汽车上最贵的就是油漆了,涂漆生产线是汽车装配车间最大的投资,会占据车间一半的地面空间,而且一年内会产生1500多吨VOCs(挥发性有机物)。
”IMD技术的优势还包括:边角料产率低;可在同一地点完成零件的成型和装饰;回收性更好。
IMD技术可获得A级表面,且无流痕,更不会像流痕那样造成“模内驻色”。
但是如果零件本身就有很多孔,必须在脱模后进行装饰,那么IMD技术的经济效益则会大打折扣。
IMD技术的倡导者们宣称:利用最新一代的可成型薄膜制成的车身板,具有与涂漆金属板相媲美的甚至更高的抗划伤性和抗冲击性。
但是,假设汽车制造商们对涂漆生产线仍然施以巨额投资,则IMD在近期内还是无望完全取代涂漆工艺。
不过,工业观察家们相信:在美国,今后即使有投资,也很少会出现建造大型涂漆生产线的情况。
IMD技术首先将一块已经被印刷、涂覆或染色过的塑料薄板经冲切成坯料后,热成型成最终产品的形状。
修正后,把它放入注射腔内,从型腔后面注入一种与其相容的基体材料,最后得到成品。
成品的表面可以是纯色的,也可具有金属外观或木纹效果,还可印有图形符号。
最近,IMD技术的发展已经超越了注射成型。
薄膜嵌入物正在被用在热塑性塑料或聚氨酯复合物基体材料上面。
此外,TSF技术,即厚板成型技术(一种将薄膜装饰复合板直接热成型为成品零件的技术),作为另一种新兴技术,也在制造大型零件,例如卡车保险杠、摇板、座后置物板等。
IMD技术起源于在胶片印刷术和丝网印刷术中所使用的薄膜,这种薄膜可模拟木纹效果,可在仪表盘上标记刻度和图案。
其中,印刷层可以作零件的“第一面”(油墨层-薄膜层-基体材料),也可作“第二面”(薄膜层-油墨层-基体材料)。
后者情况下,薄膜层必须透明,否则会遮住印刷层。
薄膜层的作用是将印刷层密封起来,使其更加耐久。
为了避免后注射时热和剪切对印刷层的破坏,还可以在印刷层的另外一面加上一层薄膜(薄膜层-油墨层-薄膜层-基体材料)。
另外一个保护印刷层的办法是:将薄膜放到模芯上,利用透明树脂对其重叠注塑。
据说,这样可使成品的表面看起来非常光泽,还有一种润湿感。
IMD技术正在逐步应用于大型三维汽车内外饰零部件的制造,其中的一个方向是利用无漆薄膜来获得单纯色、金属抛光效果、亮镀铬效果。
薄膜上涂覆了类油漆层,使其具有了热成型时所需的可拉伸性。
还有一类更新颖的应用于汽车三维零件的薄膜结构,这种结构是通过共挤出得到的,外面是透明层,里面是受保护的有色层。
这种结构的支持者们说:有色层与那些无漆薄膜上的类油漆层比较,可能更适合于热成型复杂的深冲压零件。
IMD产品的耐候性IMD技术发展的前沿领域是制造A级抗寒耐热汽车外饰面,用在汽车、重型卡车上。
目前有6家厂商提供IMD可成型薄膜,其中5家已可提供抗寒耐热的产品,剩下的1家尚在研究之中。
(1 )Avery Dennison公司提供“Avloy Dry Paint”型可成型薄膜,材料为丙烯酸/PVDF(聚偏氟乙烯),是一种有色层/透明层式结构。
薄膜[20~30 mils(1mils=千分之一寸)]复合在厚一点的ABS或TPO(热塑性聚烯烃弹性体)底板上。
厚底板的选择依需热成型的成品零件而定。
Avloy薄膜制成的终饰材,可在高光泽度单纯色和低光泽度单纯色之间任意选择,还可获得金属效果、珍珠效果、金属抛光效果和打印图案。
(2 )Soliant LLC公司提供“Fluorex”无漆膜,也是一种透明层/有色层式结构,这种无漆膜已应用在几款汽车上。
材料结构共包括四层:顶部的透明层(聚丙烯/含氟聚合物的混合物)、有色涂层(材料同透明层)、紧贴层(或粘结层)、底板层(ABS、TPO、PVC或PC )。
底板层的厚度可从0.3到300 mils。
Soliant公司制造的Fluorex T/HR应用于挤出复合技术,Fluorex 2000应用于模内镶件注塑成型技术。
这些薄膜可提供多种印刷样式(包括抛光金属外观),应用于汽车内外装饰。
最新的薄膜是Fluorex Bright,可提供一系列的亮镀铬效果,包括有色铬和黑色铬。
在佛罗里达州和亚利桑那州,Fluorex Bright已完成了一年的户外测试。
(3 )Mayco Plastic公司制造四层“模内着色”(MIC )IMD可成型薄膜。
公司将这种薄膜应用于它自己的IMD项目中,还计划以卷膜、规格板材、预成型外壳等形式对外出售。
此外,Mayco还在研发厚板成型(TSF )薄膜。
该公司的A级亮膜是离聚物和聚丙烯的共挤出薄膜。
该薄膜的上透明涂层和下有色涂层,都基于A. Schulman公司的新型紫外稳定离聚物。
薄膜第三层是粘结层,第四层是底板层。
底板层材料可以选择聚丙烯的均聚物或共聚物、茂金属聚丙烯或TPO。
以前,MIC薄膜曾被用在数量有限的戴姆勒-克莱斯勒2002 Dodge Neon的前托板上。
现在,戴姆勒-克莱斯勒正在安装两台3000吨注射机,准备利用IMD薄膜注射成型Neon 2004和2005车型的前托板和尾托板。
(4 )Senoplast USA制造的共挤出三层薄膜Senotop,厚度为1~2毫米,可应用于IMD 或直接热成型。
顶层是PMMA透明层,紧跟着的是PMMA有色层,底层是ASA/PC共混物。
据报道,底层还可以是ABS、ABS/PC、ASA(丙烯腈-丙烯酸酯-苯乙烯)、ASA/PC,PC和PBT/PC等。
(5 )GE Plastics提供的也是共挤出薄膜。
薄膜上的覆盖层透明光亮,由新型Lexan SLX 聚碳酸酯共聚物制成,这种共聚物的主链上有阻挡紫外线的基团。
覆盖层保护了Lexan PC 制成的有色层。
薄膜可以“后浇铸”PC、PC合金或者大多数聚酯。
GE还为薄膜研发了联结层,可使其他基体材料也能“后浇铸”Lexan SLX薄膜。
例如:带有PC/ASA联结层的薄膜,可以粘结到玻璃纤维增强的聚氨酯基体材料上,制成Smart跑车的车顶组件。
此外,该公司正在研发具有镀铬感的IMD薄膜和耐高温的、基于Ultem PEI材料的UL94-0薄膜。
(6 )拜耳聚合物最近将母公司和子公司(Sheffield Plastics )进行薄膜市场销售的合并,期望将它的IMD技术扩展到汽车外装饰领域。
高级IMD市场拓展专家帕特里克·格里芬说:“IMD技术在汽车外装饰领域的应用将远远大于其在汽车内装饰领域的应用。
”现在,拜耳正在研发一种可成型的涂层体系,其效果将等同于汽车涂漆。
格里芬说他们目前的进度大约达到了60%。
这种涂层体系将被用在拜耳的Makrofol PC、BayfolPC/PBT薄膜上,而这些薄膜与ABS、PC和PC/ABS基体材料是相容的。
不含油漆的A级表面几个可获得A级表面的汽车外饰IMD应用正在开展之中。
Soliant,当前IMD应用最多的公司,正在集中研发整个部件(例如摇板)的装饰,不再强调修整。
在Soliant公司,TPO的IMD应用项目最多。
Fluorex IMD薄膜的应用项目包括Acura 3.2 TL摇板和车身侧模塑件、丰田Avalon摇板、Cadillac Seville和Deville A和B立柱、本田Odyssey车身侧模塑件、Renault Laguna上下装饰网格,还有奥迪、大众、尼桑、Maxima、沃尔沃S80和S60的车顶带。
目前,公司正致力于车顶组件的开发。
此外,市场部主管John Cupstid还看到了薄膜在保险杠托板上的潜在应用。
对于Soliant公司,将厚板直接热成型为零件占公司生意的近50%。
这些零件多数较简单且平展,但也有一些超大型零件,例如用在Hendrickson International制造的Class 5~8型卡车上的新型汽配保险杠。
此外,正在进行生产的零件还有Chevrolet Trailblazer摇板和Chevrolet Impala尾灯。
Mayco Plastics也在集中研发大型汽车零件,如前后托板和车身板。
该公司总裁廷·赫费尔说:“共挤出的MIC薄膜也可应用于卡车、越野车设备、器具、家具等。
共挤出的无漆薄膜,如Soliant的Fluorex和Avery Dennison的Avloy,已在获得轻金属光泽方面取得进展。
但必须承认,共挤出薄膜仍然很难获得金属光泽。
GE的Lexan SLX全球市场经理托德·史威尼说:“我们已获得了一系列具有金属光泽的薄膜,我们正在继续丰富我们的光色板,包括轻金属色和银色”。
GE的Lexan SLX薄膜的IMD 应用包括轮胎罩、重点零部件、车顶板等。
公司现有四个新的机密项目用于制造立式和卧式车身板。
正在应用的零件有:前托板、挡板、门板、反射镜外罩和总导管。
此外,GE正在研发车篷。
Avery Dennison总是更多的专注于一些更小的零件(主要是一些装饰用附饰品)。
例如:2000~2004 本田Civics上的车身侧塑件、2001~2004 福特Mercury Grand Marquis车模上的后门装饰物、GM SSR概念越野车上的轮子装饰物。
公司高级市场经理迈克·科茨比尔说:“我们觉得至少在目前,还无法制造像保险杠和车篷那样的大型零件。
虽然每个人都想做保险杠,但是难题太多,如:如何获得金属光泽,如何伸展薄膜使其边缘恰当地卷曲等。
大零件的边缘装饰很贵,例如1平方英尺的零件可能需要一整块2平方英尺的无漆薄膜,包括修整飞边毛刺。
”Senoplast现有三个项目研发车顶组件,他们使用的是可热成型的、以聚芳酯长纤维为底板的Senotop薄膜。
该公司第一系列的产品是前阻流板和尾板,用在2003 Smart的月形车顶上。
第三个IMD项目是注射成型ABS/PC挡板和保险杠,用在Smart车上。
该公司市场部经理Andreas Hoellebauer说:除此之外,还有一个美国的汽车制造商正在利用我们的Senotop IMD薄膜研发A B立柱盖。