2000m3高炉内型设计
年产值刚生铁450吨的高炉车间中高炉内型设计

课程设计说明书题目名称:年产值钢生铁450吨的高炉车间中高炉内型设计系部:机械系工程系专业班级:学生:学号:指导教师:完成日期:新疆工程学院课程设计评定意见设计题目系部_________________ 专业班级学生_________________ 学生学号评定意见:评定成绩:指导教师〔签名〕:年月日新疆工程学院____________系(部)课程设计任务书学年学期年月日教研室主任〔签名〕系〔部〕主任〔签名〕目录前言 (1)配料计算方法 (3)配料计算原始条件 (3)吨铁简易配料计算 (5)物料平衡计算方法 (10)物料平衡计算的原始条件 (10)吨铁物料平衡计算 (10)高炉内型设计方法 (15)炉缸 (15)炉腹 (16)炉身 (17)炉腰 (17)炉喉 (17)死铁层厚度 (18)高炉内型计算 (18)高炉内型图 (20)参考资料 (21)一、前言近年来,随着我国经济的快速发展,在基础设施建设,,比上年度增长15.19%,占世界总产量的49.74%,08年全国生铁产量4.7067亿t,炼铁生产能力超过6亿t,09年全国生铁产量达5.4375亿t,但有6000万t/年的生产能力居于淘汰之列〔主要是300m³以下容积小高炉〕。
在产量不断增长的同时,我国的高炉炼铁技术也取得了较大的进步,入炉焦比和炼铁工序能耗不断下降,喷煤比、热风温度和利用系数也不断提高,高炉操作技术也日趋成熟,各项技术经济指标得到进一步改善。
我国现有高炉1300多座,大于1000m3以上容积的高炉有150多座。
近年来,高炉大型化的步伐加快,宝钢建成三座4 000m³级的高炉,另外已建成和在建的7 座4000m³级高炉以及首钢曹妃甸2座5500 m³高炉。
大型高炉均采用了先进的技术装备,一大批成熟高新技术和装备的应用大大降低了生产成本和劳动强度,自动化程度也进一步提升,生产环境有了很大改善,企业生产效率和经济效益得到明显提高。
安钢炼铁厂高炉工艺简介

2、工艺流程
4800m3高炉工艺布置图
3、主要工艺参数
序号 1 2 3 4 5 6 7 8 9 10 12 13 14 15 16 17 18 项目 有效容积 利用系数 焦比 煤比 富氧率 熟料率 烧结矿配比 球团矿配比 块矿配比 入炉矿品位 入炉风量 热风温度 炉顶温度 炉顶压力 渣铁比 日产生铁 年产生铁 单位 m3 t/(m3·d) kg/t铁 kg/t铁 1# 2200 2.36 350 169 5.10% 95% 80% 15% 4.50% 55.91% 4200 1185 150~260 0.21 368 5200 187 3# 4800 2.3 305 200 4% 86% 91% 75% 73.30% 16% 13% 9% 13.60% 59.20% 55.47% 7000 5800 1250 1250 150~260 150~250 0.25 0.22 310 365 10918 6500 382 237
1#、2#高炉,矿、焦槽单独设置,各用一条运 输胶带机(供矿皮带和供焦皮带),共用一条上 料主皮带,构成两个独立、并列的系统。
4.1矿焦槽系统
3#高炉,矿、焦槽呈双排布置,不设中间斗, 矿石、焦炭在槽下筛分称量后共用一条胶带机运 入上料主胶带输送机,然后运至高炉炉顶设备。
4#、5#高炉,矿、焦槽单独设置,矿石筛分 后经皮带机运输到两个矿石集中斗,焦炭由焦槽 直接进入焦炭集中斗,称量后装入料车,然后运 至高炉炉顶设备。
4.5炉体系统
4.5炉体系统
4.5.4炉底、炉缸内衬
2200m3 和2800m3 高炉采用陶瓷杯炭砖水冷炉底炉缸结构。 炉底中心下部立砌两层国产炭砖,其中下层为半石墨炭 砖,上层为微孔炭砖;上部砌两层低导热刚玉莫来石砖,炉 缸内侧砌低导热刚玉莫来石砖,外侧炉缸采用进口微孔炭 砖,在进口微孔炭砖与风口组合砖之间砌筑3层国产微孔炭 砖;在炉缸,炉底交接处采用加厚陶瓷质耐火材料和进口 微孔炭砖砌筑结构。 在风口区采用大块组合砖砌筑,以加强结构的稳定性; 铁口通道采用大块和小块相结合特殊组合砖结构。
高炉本体尺寸设计
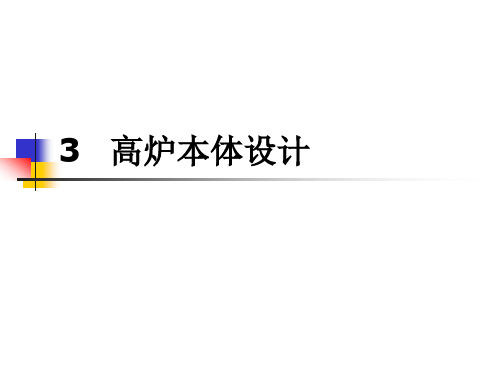
1. 比较法:
由给定的产量确定炉容,根据建厂的冶炼 条件,寻找条件相似,炉容相近,各项生产技 术指标较好的合理炉型作为设计的基础。经过 几次修订参数和计算,确定较为合理的炉型。 目前,设计高炉多采用这种方法。
风口中心线与铁口中心线间距离称 为风口高度(hf)。
风口高度可参照下式计算:
hf
hZ k
式中:
k ——渣口高度与风口高度之比,一般
取0.5~ 0.6,渣量大取低值。
(4)风口数目(n): 主要取决于炉容大小,与炉缸直径
成正比,还与冶炼强度有关。 风口数目可以按下式计算:
中小型高炉:
n 2(d 1)
2. 计算法:
计算法即经验数据的统计法。 计算时可选定某一关系式,算出某一主
要尺寸,再根据炉型中各部位尺寸间的关系 式作炉型计算,最后校核炉容,修定后确定 设计炉型。
经验公式 :
大型高炉:
Hu 6.44Vu0.2
d 0.32Vu 0.45
适应于我国50~70年代1000~2000m3高 炉的基本情况,炉型为瘦长型。
炉腹高度由下式计算 :
h2
D 2
d
tg
炉腹角一般为79º~83º,过大不利于煤气
分布并破坏稳定的渣皮保护层,过小则增
大对炉料下降的阻力,不利于高炉顺行。
4. 炉身: 炉身呈正截圆锥形。
作用:
(1)适应炉料受热后体积的膨胀,有利于 减小炉料下降的摩擦阻力,避免形成料拱。
(2)适应煤气流冷却后体积的收缩,保证 一定的煤气流速。
D
d1 2
tg
新钢高炉基本参数
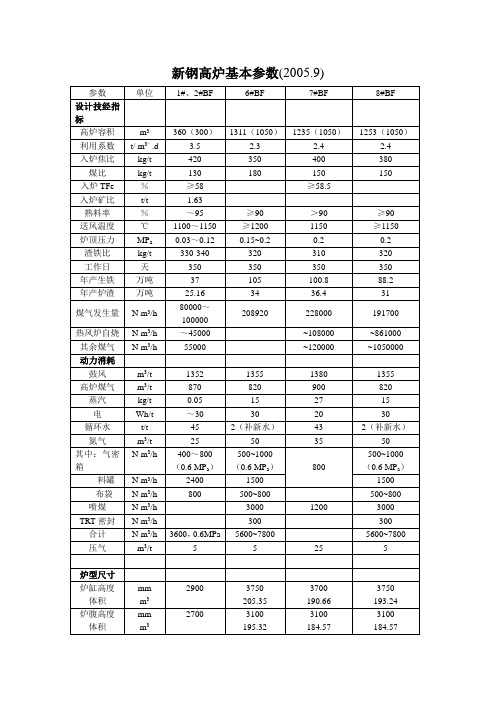
座数
座
3,球式
3,kaluging
3,改进内燃式
3,改进内燃式
全高
m
20.64
43.96
41
41
钢壳内径
(上/下)
mm
8550/7310
9990/8550
8500
8000
蓄热室断面积
m2
30.68
44.6
30.55
25.15
蓄热(球床)高度
m
7.0
24.36
格子砖(装球)量
t/座
390(φ40,φ60)
1311
1235
1253
A
m2
19.6349
54.076
51.51
51.53
Hu/D
3.0221
2.65
2.677
2.73
Vu/A
18.3219
136.1257
炉腹角
°
80.7443
79.0459
78°8′45″
79°2′45″
炉身角
°
84.4142
83.5665
83°30′29″
83°57′5″
工作容积Vw
其他:2440t/h
0.65 MPa
5550
其中:风口及炉顶打水:1250t/h,1.5MPa
炉体:3950t/h,
0.65 MPa
其他:350t/h
0.65 MPa
4320
其中:风口及炉顶打水:680t/h,1.25MPa
2,3段:1200t/h,
0.65 MPa
其他:2440t/h
0.65 MPa
4段光面,单进单出RTCr
高炉炉型设计

4、炉腹高度h2 ;炉腰直径D;炉腹角α
• 选取炉腹角α : 一般取值79o~83o h2 =
1 2 ( D d ) tg
选取 D/d 炉型 D/d 小型高炉 1.25~1.5 中型高炉 1.15~1.25 大型高炉 1.09~1.15
5、选取炉身角β; 炉身高度 h4 ; 炉喉直径 d1
世界高炉之王——沙钢5860立方米炼铁高炉
日本第二大钢铁集团——日本JFE钢铁福山厂 。
(左起)第2高炉、第3高炉、第4高炉、第5高炉,4号高炉 2006年5月扩容到5000立方米,5号高炉扩容到5500立方米
全世界共有9座5500m³ 以上特大型炼铁高炉
• 1、沙钢的5860m³ 高炉;
• 2、日本新日铁大分厂1号、2号高炉(容积均为5775m³ ) • 3、俄罗斯北方钢铁切列波维茨厂5号高炉(容积5580m³ ) 4、日本新日铁君津厂4号高炉(容积5555m³ ) • 5、德国蒂森钢铁斯韦尔根厂2号高炉(容积5513m³ ), • 6、日本JFE福山厂5号高炉(容积5500m³ ) • 7、韩国浦项光阳钢厂4号高炉(容积5500m³ )
h z 1 . 27
0 . 45
bP ' Nc d 铁
2
hf
hz k
― 渣口高度与风口高度之比
k = 0.5~0.6 ; k
炉缸高度: h =h + a ; 1 f
a―风口结构尺寸,一般取值0.35~0.5m
hz― 渣口与铁口中心线的距离称为渣口高度 P ― 生铁日产量,t b ― 生铁产量波动系数,一般取值1.2 N ― 昼夜出铁次数,8~12次/d (大高炉取大值)
• 通过对高炉炉型的大量研究和探索,人们 逐步认识了高炉炉型与原燃料和鼓风制度 的适应关系,即炉型与炉料运动和煤气流 运动规律的适应性。炉型是随着原燃料条 件的改善,操作技术水平的提高,科学技 术的进步而不断发展变化的,逐步形成了 现代的五段式高炉炉型。
攀钢新3号高炉的设计和主要设备简介

攀钢新3号高炉的设计和主要设备简介作者:王含来源:《硅谷》2011年第06期摘要:攀钢新3号高炉的设计在结合攀钢1、2、3、4号高炉生产实践经验的基础上,采用许多新工艺、新材料、新结构、新设备。
高炉的装备水平和自动控制水平达到当前国内高炉冶炼钒钛磁铁矿的先进水平,新3号高炉的有效容积为2000m3,为国内高炉冶炼钒钛磁铁矿的大型化奠定良好的基础。
关键词:设计;设备;高炉;热风炉中图分类号:F42文献标识码:A文章编号:1671-7597(2011)0320074-02攀钢四座高炉,总炉容为5030m3,年产炼钢铁水约420万吨,各高炉有效容积为:#1,1280m3(最初建设有效容积为1000m3,90年大修扩为1200m3,2002年再次大修扩为1280m3);#2、#3,1200m3;#4,1350m3。
根据以上情况,可以看出,攀钢高炉单个有效容积偏小,难以充分发挥出高炉炼铁方面的优势。
为了提高高炉装备水平,攀钢新3号高炉有效容积设计为2000m3,是国内冶炼钒钛磁铁矿最大的高炉,为国内高炉冶炼钒钛磁铁矿的大型化奠定了良好的基础。
1 设计原则遵循长寿、高效、节能、实用的原则,方便生产操作和维护,结合实际采用成熟的先进技术,提高技术装备水平;以高起点、少投入、多产出为原则。
2 高炉主要技术操作指标攀钢新3号高炉主要设计指标的确定,一方面考虑了冶炼钒钛磁铁矿的特点,另一方面考虑了高炉大型化对指标的影响,同时也参考了攀钢其它四座高炉的操作指标,具体设计指标见表1。
3 平面布置新#3高炉布置在四号高炉西侧的弄弄沟内,为原炼铁厂铸铁车间位置。
此位置有铁路和道路与厂区连接;场地地形较平坦,地形标高在1104.00m~1104.50m左右。
四座外燃式热风炉和重力除尘器分别布置在新#3高炉的北面和西面。
原料矿槽布置在新#3高炉东面,与高炉轴线夹角为64°00′;煤粉喷吹塔和焦丁回收场布置在原料矿槽的北面。
高炉炉内大型部件的优化设计

高炉炉内大型部件的优化设计钢铁行业是国民经济的重要支柱之一,高炉是钢铁生产中最为核心的设备之一。
高炉炉内的大型部件是高炉正常生产的关键装备,其优化设计对高炉的性能和效益有着重要的影响。
本文将从高炉炉内大型部件的现状分析、优化设计的方法和效果等方面来探讨该问题。
一、现状分析随着我国钢铁行业的不断发展,高炉设计和制造技术也得到了长足的进步。
目前,国内高炉的建设规模和性能已经达到世界先进水平,但是在炉内大型部件的设计和制造方面还存在一些问题。
首先是材料的选择和质量问题。
炉内大型部件一般要求使用高强度、高耐磨、高温抗氧化等特殊材料,这些材料的生产和加工技术相对较为复杂,并且对原材料的质量要求非常高。
目前国内对这些材料的生产和加工还存在一定的技术瓶颈和质量不稳定的问题。
其次是部件结构和设计存在问题。
炉内大型部件的结构和设计直接关系到高炉的稳定运行和维护保养难度。
对于现有的一些高炉,部件的结构和设计存在一些不合理之处,例如连接方式不合理、零部件不充分等问题,这会导致部件易于损坏、维修难度大,进而影响高炉的连续生产率和稳定性。
二、优化设计方法针对上述问题,我们可以从以下几方面进行优化设计:1、材料的选择和质量管控。
生产高质量的特殊材料需要具备一定的技术实力和标准化的生产制造流程,对于材料的选取,需要考虑其特性、性能和成本等多方面因素。
在材料的生产和加工过程中,还需要保证质量的稳定性和可追溯性,以便对部件的质量进行管控。
2、结构的优化与改进。
对于结构存在不合理之处的部件,需要进行针对性的设计改进,调整其零部件的分布方式、连接方式等,增强其耐用性、抗损性和维修性。
对于结构不确定或者存在预测问题的部件,可以借助现代的工程仿真技术,来对其进行设计和求解,提高设计参数的合理性和优化效益。
3、生产流程的改良与优化。
生产规模的不断扩大和重量的增加,使得大型部件的生产和加工成本不断攀升。
在生产过程中,需要从原材料加工、转炉熔炼、精整吊装、现场焊接等多个方面进行管控和优化,以确保生产流程的高效稳定和部件的质量安全。
高炉炉型选择以及炉容计算

3600高炉本体设计原始数据:高炉有效容积:Vu=3600高炉年工作日:355天高炉利用系数:设计内容:1.高炉炉型的选择;2.高炉内型尺寸的计算(包括风口、铁口、渣口数量,大型高炉一般不设渣口);3.高炉耐火材料的选用;4.高炉冷却方式和冷却器的确定;5.高炉炉壳厚度的确定。
高炉本体包括高炉基础、炉衬、冷却装置、以及高炉炉型设计计算等。
高炉的大小以高炉有效容积()表示,本设计高炉有效容积为3600,按我国规定,属于大型高炉;高炉炉衬用耐火材料,是由陶瓷质和砖质耐火材料构成的综合结构;有些高炉也采用高纯度的刚玉砖和碳化硅砖;高炉冷却设备器件结构也在不断更新,软水冷却、纯水冷却都得到了广泛的应用。
1.高炉炉型选择高炉是竖炉。
高炉内部工作剖面的形状称为高炉炉型或称高炉内型。
高炉冶炼的实质是上升的煤气流和下降的炉料之间所进行的传热传质过程,因此必须提供燃料燃烧的空间,提供高温煤气流与炉料进行传热传质的空间。
炉型要适合原料的条件,保证冶炼过程的顺行。
近代高炉炉型为圆断面五段式,是两头小中间大的准圆筒形。
高炉内型如图1。
高炉有效高度(炉腰直径(D)与有效高度()之比值是表示高炉“细长”或“矮胖”的一个重要指标,在我国大型高炉Hu/D =—,随着有效容积的增加,这一比值在逐渐降低。
在该设计中,。
炉缸高炉炉型下部圆筒部分为炉缸,炉缸的上、中、下部位分别装有风口、渣口、铁口。
炉缸下部容积盛液态渣铁,图1 高炉内型上部空间为风口燃烧带。
铁口位于炉缸下水平面,铁口数目依炉容或产量而定,对于3000的高炉,设置3—4个铁口,以每个铁口日出铁量1500—3000t设置铁口数目。
在该设计中,设置4个铁口。
渣口与铁口中心线的距离称为渣口高度(),它取决于原料条件,即渣量的大小。
渣口高度的确定参照下式计算:= =式中:P——生铁日产量,t;B——生铁产量波动系数,取;N——昼夜出铁次数,取9;——铁水密度,取;C——渣口以下炉缸容积利用系数,一般为,在该设计中,取;d——炉缸直径m。
- 1、下载文档前请自行甄别文档内容的完整性,平台不提供额外的编辑、内容补充、找答案等附加服务。
- 2、"仅部分预览"的文档,不可在线预览部分如存在完整性等问题,可反馈申请退款(可完整预览的文档不适用该条件!)。
- 3、如文档侵犯您的权益,请联系客服反馈,我们会尽快为您处理(人工客服工作时间:9:00-18:30)。
1800炉型设计说明书摘要:本设计要求建1800高炉。
设计主要内容包括高炉炉型设计计算及高炉本体立剖图,同时对所设计高炉的特点进行简述。
设计高炉有效容积为1800径比取2.3,高炉利用系数取值为2.0,据此设计高炉炉型。
设计本着优质、高产、低耗和对环境污染小的宗旨,为日产生铁4000t的高炉提供高炉内型设计。
设计说明书对1800内型进行了的详细的计算,并结合国内外相同炉容高炉的先进生产操作经验及相关的数据,力求设计的高炉达到高度机械化、自动化和大型化,达到最佳的生产效益。
绪论最近二十年来,日本和欧盟区的在役高炉座数由1990年的65座和92座下降到28座和58座,下降幅度分别为56.9%和37%,但是高炉的平均容积却分别由1558m3和1690m3上升到4157m3和2063m3,上升幅度为166.8%和22%,这基本代表了国外高炉大型化的发展状况。
高冶炼强度、高富氧喷煤比和长寿命化作为大型高炉操作的主要优势受到大家越来越高的关注和青睐,但是高炉大型化作为一项系统工程,它在立足自身条件的基础上仍须匹配的炼钢、烧结和炼焦能力。
我国近年推出的《钢铁产业发展政策》中规定高炉炉容在300m3以下归并为淘汰落后产能项目,且仍存在扩大小高炉容积的淘汰范围的趋势。
同时国内钢铁产业的快速发展均加速了世界和我国高炉大型化的发展进程。
由于大型化高炉具备的单位投资省、效能高和成本低等特点,从而有效地增强了其竞争力。
20世纪高炉容积增长非常快。
20世纪初,高炉炉缸直径4-5m,年产铁水约100000吨左右,原料主要是块矿和焦炭。
20世纪末,最大高炉的炉缸直径达到14-15m,年产铁水300-400万吨。
目前,特大型高炉的日产量能够达到甚至超过12000吨。
例如,大分厂2号高炉(日本新日铁)炉缸直径15.6m,生产能力为13500吨铁/天。
蒂森-克虏伯公司施韦尔格恩2号高炉炉缸直径14.9m,生产能力为12000吨铁/天。
70年代末全世界2000立方以上高炉已超过120座,其中日本占1/3,中国有四座。
全世界4000立方以上高炉已超过20座,其中日本15座,中国有1座在建设中。
我国高炉大型化的发展模式与国外基本相近,主要是采取新建大型高炉、以多座旧小高炉合并成大型高炉和高炉大修扩容等形式来推动着高炉的大型化发展。
据不完全统计,我国自2004年以来相继建成投产的3200m3级15座,4000m3级8座,5000m3级3座,且有越来越大的趋势。
目前,河北迁钢和山东济钢等企业也正在建设4000m3级高炉,近来宝钢湛江和武钢防城港项目也在规划筹建5500m3级超大型高炉。
我国高炉大型化的标准主要是依据高炉容积的大小来划分的,且衡量标准也由过去的1000m3提高到2000m3,甚至更大。
虽然大型化高炉相对于小高炉存在着生产率高、生产稳定、指标先进和成本低等显著的优点,但是对于我国高炉大型化的发展状况,我们仍然需要科学客观地看待。
第一章高炉炉型高炉是竖炉,高炉内部工作空间剖面的形状称为高炉炉型或高炉内型。
高炉冶炼的实质是上升的煤气流和下降的炉料之间进行传热传质的过程,因此必须提供燃料燃烧的空间,提供高温煤气流与炉料进行传热传质的空问。
高炉炉型要适应原燃料条件的要求,保证冶炼过程的顺利。
1.1炉型的发展过程炉型的发展过程主要受当时的技术条件和原燃料条件的限制。
随着原燃料条件的改善以及鼓风能力的提高,高炉炉型也在不断地演变和发展,炉型演变过程大体可分为3个阶段。
(1)无型阶段-又称生吹法。
在土坡挖洞,四周砌行块,以木炭冶炼,这是原始的方法。
(2)大腰阶段-炉腰尺寸过大的炉型。
出于当工业不发达,高炉冶炼以人力、蓄力、风力、水力鼓风,鼓风能力很弱,为了保证整个炉缸截面获得高温,炉缸直径很小,冶炼以木炭或无烟煤为燃料,机械强度很低,为了避免高炉下部燃料被压碎,从而影响料柱透气性,故有效高度很低;为了人工装料方便并能够将炉料装到炉喉中心.炉喉直径也很小,而大的炉腰直径减小了烟气流速度,延长了烟气在炉内停留时间,起到焖住炉内热量的作用。
因此,炉缸和炉喉直径小,有效高度低,而炉腰直径很大。
这类高炉生产率很低,一座28m3高炉日产量只有1.5 t左右。
(3)近代高炉-由于鼓风机能力进一步提高.原燃料处理更加精细,高炉炉型向着“大型横向”发展。
高炉内型合理与否对高炉冶炼过程有很大影响。
炉型设计合理是获得良好技术经济指标,保证高炉操作顺行的基础。
1.2五段式高炉①高炉有效客积和有效高度高炉大钟下降位置的下沿到铁口中心线间的距离称为高炉有效高度,对于无钟炉顶为旋转溜槽最低位置的下缘到铁口中心线之间的趴离。
在有效高度范围内,炉型所包括的容积称为高炉有效容积。
高炉的有效高度,对高炉内煤气与炉料之间传热传质过程行很大影响。
在相同炉窖和冶炼强度条件下,增大有效高度,炉料与煤气流接触机会增多,有利于改善传热传质过程、降低燃料消耗;仅过分增加有效高度,料校对煤气的阻力增大.容易形成料供,对炉科下降不利。
高炉有效高度应适应原燃料条件,如原燃料强度、粒度及均匀性等。
生产实践证明,高炉有效高度与有效容积有一定关系,但不是直线关系,当有效容积增加到—定值后,有效高度的增加则不显著。
②炉缸高炉炉型下部的圆筒部分为炉缸,炉缸的上、中、下部位分别没有风口、渣口与铁口,现代大型高炉多不设渣口。
炉缸下部容积盛装液态渣铁,上部空间为风口的燃烧带。
(1)炉缸直径炉缸直径过大和过小都直接影响高炉生产。
直径过大将导致炉腹角过大,边缘气流过分发展,中心气流不活跃而引起炉缸堆积,同时加速对炉衬的侵蚀;炉缸直径过小限制焦炭的燃烧.影响产员的提高。
炉缸截面积应保证一定数量的焦炭和喷吹燃料的燃烧,炉缸截面燃烧强度是高炉冶炼的一个重要指标,它是指每1h每1m3炉缸截面积所烧侥的焦炭的数量,一般为 1.00~1.25t/(m 2·h)。
炉缸截面燃烧强度的选择,应与风机能力和原燃料条件相适应,风机能力大、原料透气性好、燃料可燃性好的燃烧强度可选大些,否则选低值。
(2)炉缸高度炉缸高度的确定,包括渣口高度、风口高度以及风口安装尺寸的确定。
铁口位于炉缸下水平面,铁口数目根据高炉炉容或高炉产量而定,一般1000m3以下高炉设一个铁口,1500~3000m3高炉设2~3个铁口,3000m3以上高炉设3~4个铁口,或以每个铁口日出铁量1500—3000t设铁口数目。
原则上出铁口数目取上限,有利于强化高炉冶炼。
渣口中心线与铁口中心线间距离称为渣口高度,它取决于原料条件,即渣量的大小。
渣口过高,下渣量增加,对铁口的维护不利;渣口过低,易出现渣中带铁事故,从而损坏渣口,大、中型高炉渣口高度多为1.5~1.7m。
(3)炉腹炉腹在炉缸上部,呈倒截圆锥形。
炉腹的形状适应了炉料熔化滴落后体积的收缩,稳定下料速度。
同时,可使高温煤气流离开炉墙,既不烧坏炉墙又有利于渣皮的稳定,对上部料柱而言,使燃烧带处于炉喉边缘的下方,有利于松动炉料,促进冶炼顺行。
燃烧带产生的煤气量为鼓风量的1.4倍左右,理论燃烧温度1800~2000℃,气体体积剧烈膨胀,炉腹的存在适应这一变化。
炉腹的结构尺寸是炉腹高度h和炉腹角α。
炉腹过高,有可能炉料尚未熔融就进2人收缩段,易造成难行和悬料;炉腹过低则减弱炉腹的作用。
(4)炉身炉身呈圆锥台形,其形状炉料受热后体积的膨胀和煤气流冷却后的收缩,有利于减少炉料下降的摩擦阻力,避免形成料拱。
炉身角对高炉煤气流的合理分布和炉料顺行影响较大。
炉身角小,有利于炉料下降,但易于发展边缘煤气流,过小时但只边缘煤气流过分发展。
炉身角大,有利于抑制边缘煤气流发展,但不利于炉料下行,对高炉顺行不利。
设计炉身角时要考虑原料条件,原料条件好时,可取大些,相反,则取小些。
高炉冶炼强度大,喷煤量大,炉身角取小值。
同时要适应高炉容积,一般大高炉由于径向尺寸大,径向膨胀量也大,就要求小些,中小型高炉大些。
(5)炉腰炉腹上部的圆柱形空间为炉腰,是高炉炉型中直径最大的部位。
炉腰处恰是冶炼的软熔带、透气性变差,炉腰的存在扩大了该部位的横向空间,改善了透气条件。
在炉型结构上,炉腰起着承上启下的作用,使炉腹向炉身的过渡变得平缓,减小死角。
炉腰直径与炉缸直径和炉腹角和炉腹高度几何相关,并决定了炉型的下部结构特点。
一般炉腰直径与炉缸直径有一定比例关系,大型高炉D/d取值1.09~1.15,中型高炉1.15~1.25,小型高炉1.25~1.5。
(6)炉喉炉喉吴圆柱形,它的作用是承接炉料,稳定料面,保证炉料合理分布。
炉喉直径与炉腰直径、炉身角、炉身高度几何相关,并决定了高炉炉型的上部结构特点。
根据任务要求,可得出以下条件:Hu/D=2.5~3.1 Vu=1500~3000m 3设置2个铁口 炉腹2.8~3.6炉腰直径D/炉缸直径d=1.10-1.15 炉腹角取78o -83o炉渣口高度1.5~1.7m 炉腰直径高度1-3m炉喉直径d 1/炉腰直径D=0.64~0.73本设计任务:设计1800 m 3高炉一座2.1定容积选定高炉座数为1座,高炉利用系数为ηv =2.0t/(m 3 ·d),高炉容积V u =2000m 32.2确定年工作日和日产量年工作日为355天,日产量P 总=V u ·ηv =4000t2.3炉缸尺寸1炉缸直径它是决定焦炭燃烧量和出铁能力的重要参数,大型高炉一般采用经验公式:炉缸直径 m d V u0.1020004087.04087.04205.04205.0=⨯== 2)炉缸高度要求能储存一次铁水量和下渣量,加上出铁量波动系数。
一般应使炉缸的容积占高炉有效容积的一个比例范围,现代大型高炉一般在17%~18%左右。
A.炉缸高度m V V h u u7.48707.344206.1841.0159.01=-=-B.风口高度 09.355.07.1===k h h z f 取m h f 1.3= C.风口数量262.1==πd n2.4炉腰尺寸(1)炉腰直径决定于炉缸直径,炉腰高度和角度,炉腰直径稍大些好,它有利改善初成渣的透气性 可D/d 来确定,可经验公式炉腰直径 m D V u 3.1120005684.05684.03942.03942.0=⨯==(2) 炉腰高度在炉腹部位炉料下降缓慢,未还原的矿石在此经过充分还原后进入炉缸。
因此,炉腹的高度应与炉容相适应。
炉腹过高,可能是炉料还未熔化就过早的进入炉腹,容易导致悬料:炉腹过低就无法发挥作用炉腰高度m V V h u u 8.13278.63586.07848.02152.03=-=-(3).炉喉尺寸 1)炉喉直径m V d u 6.720004317.04317.03777.03777.01=⨯==2)炉喉高度炉喉起到控制炉料和煤气流分布的作用。